Физика и химия стекла, 2022, T. 48, № 1, стр. 75-84
Влияние содержания волокон SiC в карбидокремниевом материале на его механические свойства
С. Н. Перевислов 1, *, Т. Л. Апухтина 2, А. С. Лысенков 3, М. Г. Фролова 3, М. В. Томкович 4
1 Институт химии силикатов им. И.В. Гребенщикова РАН
199034 Санкт-Петербург, наб. Макарова, 2, Россия
2 Научно-исследовательский институт химии и технологии элементоорганических соединений
105118 Москва, ш. Энтузиастов, 38, Россия
3 Институт металлургии и материаловедения им. А.А. Байкова РАН
119334 Москва, Ленинский пр., 49, Россия
4 Физико-технический институт им. А.Ф. Иоффе РАН
194021 Санкт-Петербург, Политехническая ул., 26, Россия
* E-mail: perevislov@mail.ru
Поступила в редакцию 26.07.2021
После доработки 22.09.2021
Принята к публикации 08.10.2021
- EDN: AUIQOS
- DOI: 10.31857/S0132665122010103
Аннотация
Получены SiC-материалы методом пропитки жидким кремнием пористой заготовки, состоящей из карбида кремния и углерода. В состав материала, на стадии подготовки шихтовых композиций, вводили до 18 об. % SiCf, армирующих материал и придающих ему высокий уровень механических характеристик. При увеличении содержания волокон (>10 об. % SiCf) снижается плотность и уменьшается прочность материала, тем не менее трещиностойкость его повышается. Максимальное значение критического коэффициента интенсивности напряжений зафиксировано у материала, содержащего 15 об. % SiCf – K1С = 6.0 ± 0.2 MПа ⋅ м1/2.
ВВЕДЕНИЕ
Карбид кремния обладает уникальными свойствами: низкой плотностью (ρ = 3.21 г/см3) и коэффициентом термического расширения (а = 4.5 × 10–6 К–1), высокой твердостью (Hμ = 31 ГПа) и высокотемпературной стойкостью, а также устойчивостью к действию многих кислот и щелочей, что позволяет использовать материалы на основе SiC при работе в экстремальных условиях высоких температур, динамических нагрузок и агрессивных сред. Широкое распространение в промышленности SiC получил при изготовлении на его основе узлов трения, абразивных материалов и элементов брони [1].
Высокий уровень свойств достигается на материалах, полученных методами: горячего прессования (σизг = 700 ± 50 МПа; HV = 25 ± 1 ГПа; K1С = 6.5 ± 0.5 МПа ⋅ м1/2); горячего изостатического прессования (σизг = 800 ± 30 МПа; HV = 26.0 ± 0.5 ГПа; K1С = 8.0 ± 0.4 МПа ⋅ м1/2); плазменного спекания (σизг = 730 ± 10 МПа; HV = 26.0 ± ± 0.3 ГПа; K1С = 7.5 ± 0.2 МПа ⋅ м1/2); твердофазного спекания (σизг = 400 ± 20 МПа; HV = 26.0 ± 0.3 ГПа; K1С = 4.5 ± 0.2 МПа ⋅ м1/2) и жидкофазного спекания (σизг = 550 ± ± 20 МПа; HV = 21.0 ± 0.3 ГПа; K1С = 5.2 ± 0.2 МПа ⋅ м1/2) [2], однако низкая производительность методов, высокая трудоемкость и большая усадка при спекании приводят к поиску альтернативных технологий и повышению локальных свойств реакционно-спеченных карбидокремниевых материалов (SiSiC).
Реакционно-спеченный карбид кремния широко распространен в промышленности благодаря практически безусадочной технологии производства и низкой температуре спекания. SiSiC-материалы получают пропиткой жидким кремнием пористых заготовок, включающих первичный карбид кремния SiCI (исходные частицы SiC) и углерод, за счет транспорта углерода через расплав кремния и образования на поверхности первичных частиц вторичного карбида SiCII [3, 4].
Хорошее смачивание углерода расплавом Si с низкой вязкостью и экзотермический характер реакции взаимодействия расплава кремния с твердым углеродом позволяют быстро пропитать пористую заготовку и заполнить все поры. Этот метод приводит к получению плотных SiC/SiC композитов при температурах выше температуры плавления Si (1414°C), при условии формирования исходных заготовок с определенными размером, формой и объемным содержанием пор [5–7]. Чем больше объемное содержание и размер пор в заготовке, тем выше количество свободного кремния в спеченном изделии и тем больше хрупкость материала. Свободный кремний в спеченном материале (выше 15 об. %) снижает вязкость разрушения (ниже 2 MПа ⋅ м1/2) и уменьшает механические характеристики как при комнатной, так и при высоких температурах [8–11]. Для снижения количества свободного кремния и повышения жесткости материала в его состав вводят Mo, Nb, Ni и др., а также волокна углерода, которые при взаимодействии с кремнием образуют SiC [11, 12]. Введение волокон углерода, карбида кремния и других материалов, армирующих структуру, повышает механические характеристики материала и в частности трещиностойкость. Сложность измельчения исходных углеродных волокон и их гомогенного перемешивания, а также высокая вероятность разрушения их целостности при пропитке расплавом кремния, приводят к поиску новых подходов при получении армированных углеродными волокнами композиционных SiSiC-материалов. В работе [13] методом горячего шликерного литья с последующим высокотемпературным спеканием получены материалы на основе карбида кремния с добавлением в качестве армирующих компонентов 20 об. % волокон SiCf с высокой относительной плотностью (ρотн = 97–98%). Введение в состав оксида алюминия волокон SiCf позволяет, методом горячего прессования, получить материал с высоким уровнем свойств: Е = 421 ГПа; K1С = 7.1 МПа ⋅ м1/2; σизг = 480 МПа [14–16]. В работе [17] получены армированные (до 16 об. % SiCf) реакционно-спеченные карбидокремниевые материалы. В качестве волокон использовали керновые SiCf диаметром до 140 мкм, что привело к их неравномерному распределению в структуре материала, худшей пропитке жидким кремнием и уменьшению уровня механических характеристик керамики. Введение 16 об. % SiCf приводит к увеличению пористости материала до 12.3% и уменьшению уровня основных механических характеристик (прочности на изгиб, твердости и модуля упругости). Трещиностойкость композита возрастает до 5.2 МПа ⋅ м1/2 при увеличении содержания волокон до 8 об. %, а затем уменьшается. Представляет интерес исследование структуры и механических характеристик реакционно-спеченного карбидокремниевого материала, армированного бескерновыми волокнами SiCf.
Целью работы является получение армированных бескерновыми волокнами SiCf реакционно-спеченных карбидокремниевых материалов, исследование фазового состава и микроструктуры, а также влияния введения волокон в материал на его механические характеристики.
ЭКСПЕРИМЕНТАЛЬНАЯ ЧАСТЬ
Как показано в работе [18] для максимальной упаковки частиц при формовании заготовок изделий необходимо использовать порошки разного гранулометрического состава. Составы материалов, исследуемых в работе представлены в табл. 1.
Размер частиц порошка карбида кремния определяли на лазерном анализаторе дисперсности MasterSizer 3000: марки М40 – d0.5 = 28.8 мкм; марки М5 – d0.5 = 3.7 мкм (“Волжский абразивный завод”, Россия). В работе использовали углерод марки К-354. Волокна SiCf в виде непрерывных нитей получены методом карбонизации поликарбосиланового волокна [18]. Волокна диаметром d = 44 ± 3 мкм (рис. 1) измельчали в планетарной мельнице до размера d = 44 ± 3 мкм, l = 0.5–1.0 мм. Плотность волокон ρ = 2.708 г/см3, прочность на растяжение разных партий волокон σраст = 1242.7–2112.5 МПа [19]. Элементный состав волокна (табл. 2) подтверждает его однородность во всем объеме SiCf.
Рис. 1.
Микрофотография поверхности волокна (1), центр волокна (2) и элементный рентгенофлуоресцентный анализ волокна SiCf.
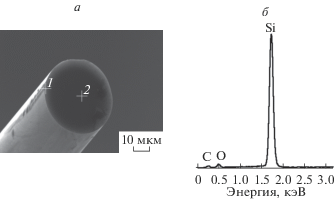
Таблица 2.
Элементный состав волокна SiCf
№ участка | Содержание элементов в составе волокон SiCf, мас. % | ||
---|---|---|---|
SiK | CK | OK | |
1 | 44.01 | 47.52 | 8.47 |
2 | 56.81 | 36.92 | 6.27 |
Исходные порошки карбида кремния в необходимом соотношении (табл. 1) смешивали в барабанном смесителе с углеродом в течении 20 ч, затем в шихту добавляли волокна карбида кремния. Общее время перемешивания шихтовых компонентов 40 ч. Перемешанные порошки пластифицировали 2% раствором органического связующего и гранулировали. Методом полусухого формования при давлении 100 МПа прессовали образцы размером 6 × 6 × 45 мм, которые сушили при температуре 100–110°С в течение 5 ч и укладывали в графитовые контейнеры, обмазанные гексагональным нитридом бора, во избежание прилипания жидкого кремния к стенкам контейнера, затем засыпали кусковым кремнием d = 3.0–5.0 мм из расчета 0.7 массы кремния от массы заготовки. Пропитку кремнием (реакционное спекание) осуществляли при температуре 1600°С в течение 10 мин в вакууме. Спеченные образцы поступали на пескоструйную обработку.
Фазовый состав изучали методом рентгенофазового анализа на установке Rigaku Smartlab 3. Плотность и пористость спеченных образцов определяли методом гидростатического взвешивания. Прочность на изгиб измеряли на разрывной машине Shimadzu AG-300kNX. Модуль упругости определяли на установке ЗВУК-130. Микротвердость определяли на микротвердомере ПМТ-3М; критический коэффициент интенсивности напряжений материалов – по длине трещин, исходящих из диагоналей отпечатка Виккерса. Исследование микроструктуры образцов проводили на оптическом микроскопе Techno Meiji IM 7200 и сканирующем электронном микроскопе TESCAN VEGA 3 SBH. Оборудование частично предоставлено “Инжиниринговым центром” СПбГТИ(ТУ).
РЕЗУЛЬТАТЫ ИССЛЕДОВАНИЙ И ИХ ОБСУЖДЕНИЕ
Для реакционно-спеченных изделий характерна структура практически беспористого (П ≤ 0.5%) материала (рис. 2), в которой основной фазой являются зерна первичного карбида кремния SiCI, фаза между ними – вторичный карбид SiCII (образованный по реакции взаимодействия углерода с кремнием), занимающий 20–30% объема всего материала и напрямую зависящий от количества вводимого в исходную шихту углерода. В составе готового изделия также присутствует непрореагировавший (свободный) кремний, частично растворенный в SiCII (рис. 2).
При изучении результатов РФА видно, что интенсивность пиков Si возрастает при увеличении объемного содержания введенных в состав материала волокон SiCf. Большое содержание SiCf приводит к худшей уплотняемости, высокой пористости, большему содержанию свободного кремния и, как следствие, снижению уровня механических характеристик. Увеличение объема свободного кремния происходит за счет снижения содержания фазы карбида кремния (рис. 3). РФА образца, содержащего 5 об. % SiCf, зафиксировал наличие небольшого количества фазы 15R-SiC, которая при увеличении содержания SiCf в составе материала более 10 об. % частично переходит в более стабильную фазу 6Н-SiC (рис. 3).
Рис. 3.
Рентгеновские дифрактограммы реакционно-спеченных SiC-материалов, содержащих 5 об. % SiCf (a); 10 об. % SiCf (б); 15 об. % SiCf (в); 18 об. % SiCf (г).
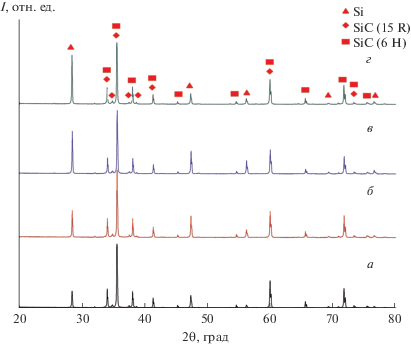
С возрастанием объемного содержания SiCf в составе SiSiC-материалов их плотность уменьшается, достигая значений ρ = 3.01 ± 0.01 г/см3 (материал состава 5), что определяется высокой пористостью (П = 3.5 ± 0.2%) (рис. 4). Хаотичная упаковка SiCf не позволяет получать заготовки с высокой плотностью при формовании, что приводит к возрастанию пористости спеченной армированной керамики, увеличению содержания свободного кремния в материале и, как следствие, уменьшению уровня механических характеристик (рис. 5).
Рис. 4.
Зависимости плотности и пористости SiSiC-материалов от объемного содержания SiCf (⚫ – плотность; ◼ – пористость).
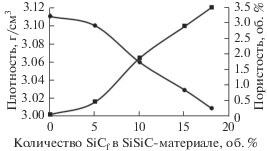
Рис. 5.
Зависимости модуля упругости и прочности при поперечном изгибе SiSiC-материалов от объемного содержания SiCf (⚫ – модуль упругости; ◼ – прочность при изгибе).

Прочность при изгибе армированного материала увеличивается с возрастанием содержания волокон (рис. 5), до максимального значения σизг = 720 ± 10 МПа при 10 об. % SiCf. Снижение прочности (при введении >10 об. % SiCf) объясняется повышением объемной пористости материала более 1.8%, высоким содержанием свободного кремния и, как следствие, хрупкостью керамики.
Модуль упругости зависит от дефектов структуры материала, т.е. микротрещин, объемной пористости и примесных фаз (свободный кремний). При введении в SiSiC-материал волокон (18 об. % SiCf) его модуль упругости уменьшается до значений Е = = 320 ± 10 ГПа (материал состава 5) (рис. 5).
Для керамики, спеченной из порошковых компонентов, критический коэффициент интенсивности напряжений (K1С) зависит от пористости и при ее повышении K1С уменьшается до 5.5 МПа ⋅ м1/2. Армирование структуры волокнами SiCf повышает трещиностойкость керамики. Скорость распространения зародившейся трещины в SiSiC-материале (Vзвука = 10500 м/с) примерно равна 1/3 Vзвука – 3500 м/с. При соударении трещины с волокном ее энергии может быть недостаточно для разрушения волокна, поэтому трещина огибает волокна разрушая бóльший объем материала и уменьшая свою энергию, такой эффект называется “отклонение трещины” [20, 21]. Поэтому трещиностойкость армированных материалов, при увеличении объемного содержания SiCf, увеличивается – K1С = 6.0 ± 0.2 МПа ⋅ м1/2 (материал состава 4). При значительном содержании волокон (18 об. % SiCf) увеличивается пористость материала и количество свободного кремния, из-за чего снижается его трещиностойкость (рис. 6). Введение до 15 об. % SiCf повышает K1С, т.е. трещиностойкость материала на 80% (по сравнению со стандартным SiSiC-материалом [9]).
Рис. 6.
Зависимости критического коэффициента интенсивности напряжений и микротвердости SiSiC-материалов от объемного содержания SiCf (⚫ – критический коэффициент интенсивности напряжений; ◼ – Микротвердость).
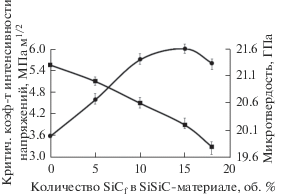
Для составов с высокой пористостью и большим объемным содержанием волокон твердость уменьшается HV = 19.8 ± 0.2 ГПа (материал состава 5) (рис. 6).
Микроструктура SiSiC-материала, армированного SiCf, представлена на рис. 7.
Кремний, пропитывая пористую заготовку, частично по поверхности растворяет волокна SiCf (рис. 7а). Частичное растворение волокон и насыщение фазой SiC пористой заготовки способствует более прочному сцеплению SiCf с матрицей, что при небольшом объемном содержании волокон (≤10 об. % SiCf) способствует повышению уровня механических характеристик керамики. Однако в местах малого контакта жидкого кремния с волокном прочность сцепления последнего с матрицей слабая и волокна могут вырываться из матрицы при небольшом механическом нагружении (рис. 7б).
Для SiSiC-материалов характерно хрупкое разрушение, трещина распространяется вдоль зерен SiCI. Однако, упрочненные волокнами материалы испытывают частично транскристаллитное разрушение (разрушение зерен (рис. 8а) и волокон (рис. 8б)), что значительно снижает энергию разрушения керамики и повышает K1С (рис. 6).
Рис. 8.
Фрактограмма армированного SiSiC-материала (а), область материала, включающая волокно SiCf (б).

Сравнивая свойства реакционно-спеченных нитрида кремния [22], карбида кремния [23] и карбида бора [24] со свойствами, полученных в работе армированных SiSiC-материалов (табл. 3), можно отметить высокую прочность и критический коэффициент интенсивности напряжений армированных карбидокремниевых материалов при достаточно низкой плотности, что определяет широкий спектр применения армированной керамики в качестве конструкционных материалов.
Таблица 3.
Физико-механические свойства реакционно-спеченных материалов на основе нитрида кремния, карбида кремния, карбида бора
Материал | ρ, г/см3 | П, % | Еупр, ГПа | σизг, МПа | К1С, МПа·м1/2 | Hμ, ГПа |
---|---|---|---|---|---|---|
Реакционно-спеченный Si3N4 [22] | 2.85 | 10.0 | 230 | 280 | 3.0 | 14.0 |
Реакционно-спеченный SiC [23] | 3.11 | 0.2 | 390 | 400 | 3.6 | 21.2 |
Реакционно-спеченный В4С [24] | 2.65 | 1.5 | 400 | 350 | 3.0 | 34.0 |
Реакционно-спеченный SiC + 10 об. % SiCf | 3.06 | 1.9 | 360 | 710 | 5.6 | 20.6 |
ЗАКЛЮЧЕНИЕ
Получены SiSiC-материалы методом пропитки жидким кремнием пористой заготовки, состоящей из карбида кремния и углерода. В состав материала, на стадии подготовки шихтовых композиций, вводили до 18 об. % волокон карбида кремния. Плотность материалов, при введении 18 об. % SiCf, снижается с ρ = 3.11 ± 0.01 г/см3 до ρ = = 3.01 ± 0.01 г/см3, а пористость повышается до 3.5 ± 0.2%. Уровень механических характеристик снижается при возрастании пористости и свободного кремния в материале, однако значение К1С увеличивается. Максимальное значение критического коэффициента интенсивности напряжений зафиксировано у материала, содержащего 15 об. % SiCf – K1С = 5.2 ± 0.2 МПа ⋅ м1/2. Введение более 15 об. % SiCf приводит к снижению уровня механических характеристик.
Список литературы
Briggs J. Engineering ceramics in Europe and the USA. UK–Worcester. 2011. 331 p.
Riedel R., Chen I.-W., Schmalzried C., Schwetz K.A. Silicon carbide – and boron carbide-based hard materials (Chapter 4) // Ceram. Sci. Techn. Mater. Proper. 2010. V. 2. P. 131–227.
Wilhelm M., Kornfeld M., Wruss W. Development of SiC–Si composites with fine-grained SiC microstructures // J. Eur. Ceram. Soc. 1999. V. 19. P. 2155–2163.
Wilhelm M., Werdenich S., Wruss W. Influence of resin content and compaction pressure on the mechanical properties of SiC–Si composites with sub-micron SiC microstructures // J. Eur. Ceram. Soc. 2001. V. 21. P. 981–990.
Yanxiang B., ShouHong T., Dongliang J. The fabrication of reaction-formed silicon carbide with controlled microstructure by infiltrating a pure carbon preform with molten Si // Ceram. Intern. 2004. V. 30. P. 435–439.
Suyama S., Kameda T., Itoh Y. Development of high-strength reaction-sintered silicon carbide // Diam. Relat. Mater. 2003. V. 12. P. 1201–1204.
Yanxiang W., Shouhong T., Dongliang J. The effect of porous carbon preform and the infiltration process on the properties of reaction-formed SiC // Carbon. 2004. V. 42. P. 1833–1839.
Munoz A., Martinez-Fernandez J., Singh M. High-temperature compressive strength of reaction-formed silicon carbide ceramics // J. Eur. Ceram. Soc. 1998. V. 18. P. 65–68.
Lim C.B., Iseki T. Transport of fine-grained b-SiC in SiC liquid Si system // Adv. Ceram. Mater. 1988. V. 3. P. 291–293.
Herrmanna M., Sempfa K., Kremmera K., Schneidera M., Michaelis A. Electrochemical corrosion of silicon-infiltrated silicon carbide ceramics in aqueous solutions // Ceram. Intern. 2015. V. 41. P. 4422–4429.
Zollfrank C., Sieber H. Microstructure evolution and reaction mechanism of biomorphic SiSiC ceramics // J. Amer. Ceram. Soc. 2005. V. 88. P. 51–58.
Fu Z, Schlier L., Travitzky N., Greil P. Three-dimensional printing of SiSiC lattice truss structures // Mater. Sci. Eng. A. 2013. V. 560. P. 851–856.
Lenk R., Kriwoschepov A.F., Grosse K. Heissgiessen von drucklos gesintertem siliziumcarbid: herstellung der heissgiess schlicker. Hot-casting of pressureless-sintered silicon carbide: preparation of the casting slip // Sprechsaal. 1995. V. 128. P. 17–20.
Chou Y.S., Green D.J. Silicon carbide platelet/alumina composites (I): Effect of forming technique on platelet orientation // J. Amer. Ceram. Soc. 1992. V. 75. P. 3346–3352.
Chou Y.S., Green D.J. Silicon carbide platelet/alumina composites (II): Mechanical properties // J. Amer. Ceram. Soc. 1993. V. 76. P. 1452–1458.
Chou Y.S., Green D.J. Silicon carbide platelet/alumina composites (III): Toughening mechanisms // J. Amer. Ceram. Soc. 1993. V. 76. P. 1985–1992.
Perevislov S.N., Afanas’eva L.E., Baklanova N.I. Mechanical properties of SiC-fiber-reinforced reaction-bonded silicon carbide // Inorg. Mater. 2020. V. 56. № 4. P. 425–429.
Aroati S., Cafri M., Dilman H., Dariel M.P., Frage N. Preparation of reaction bonded silicon carbide (RBSC) using boron carbide as an alternative source of carbon // J. Eur. Ceram. Soc. 2011. V. 31. P. 841–845.
Apukhtina T.L., Shcherbakova G.I., Sidorov D.V., Varfolomeev M.S., Sidorov D.G., Drachev A.I. Reinforcing silicon carbide fibers with protective glass-ceramic coatings // Inorg. Mater. 2015. V. 51. P. 806–810.
Hayun S., Paris V., Mitrani R., Kalabukhov S., Dariel M.P., Zaretsky E., Frage N. Microstructure and mechanical properties of silicon carbide processed by Spark Plasma Sintering (SPS) // Ceram. Intern. 2012. V. 38. P. 6335–6340.
Kim S.H., Kim Y.W., Mitomo M. Microstructure and fracture toughness of liquid-phase-sintered β-SiC containing β-SiC whiskers as seeds // J. Mater. Sci. 2003. V. 38. P. 1117–1121.
Perevislov S.N. Sintering behavior and properties of reaction-bonded silicon nitride // Russ. J. Appl. Chem. 2021. V. 94. № 2. P. 143–151.
Nesmelov D.D., Perevislov S.N. Reaction sintered materials based on boron carbide and silicon carbide // Glass Ceram. 2015. V. 71. № 9–10. P. 313–319.
Perevislov S.N., Shcherbak V., Tomkovich M.V. Phase composition and microstructure of reaction-bonded boron-carbide materials // Refract. Ind. Ceram. 2018. V. 59. № 2. P. 179–183.
Дополнительные материалы отсутствуют.
Инструменты
Физика и химия стекла