Физика и химия стекла, 2022, T. 48, № 3, стр. 334-342
Пористый железо-калиевооксидный композит
А. Ю. Бугаева 1, *, Л. Ю. Назарова 1, Е. М. Тропников 2, В. А. Белый 1, Ю. И. Рябков 1
1 Институт химии ФИЦ Коми НЦ УрО РАН
167982 Сыктывкар, ул. Первомайская, 48, Россия
2 Институт геологии ФИЦ Коми НЦ УрО РАН
167982 Сыктывкар, ул. Первомайская, 54, Россия
* E-mail: bugaeva-ay@chemi.komisc.ru
Поступила в редакцию 28.06.21
После доработки 26.07.21
Принята к публикации 06.08.21
- EDN: KRVSOV
- DOI: 10.31857/S0132665121060056
Аннотация
Способ получения пористого железо-калиевооксидного композита с бидисперсной структурой включает импрегнирование выгорающей микродобавки диоксанлигнина березы продуктами гидролиза солей, полученных с использованием способов соосаждения и золь-гель. Методами синхронного термического, рентгенофазового, рентгеноспектрального анализов и сканирующей электронной микроскопии изучено влияние количества диоксанлигнина березы и способов получения шихты на процессы фазообразования в многокомпонентном железо-калиевооксидном композите. Методом низкотемпературной физической сорбции азота определены текстурные характеристики композита. Композит предназначен для применения в качестве сорбентов, носителей катализаторов, фильтрующих и теплозащитных материалов, пламегасителей и звукопоглотителей.
ВВЕДЕНИЕ
Пористые материалы находят свое применение в медицинской, химической и нефтехимической промышленности в качестве сорбентов, носителей катализаторов, фильтрующих и теплозащитных материалов, пламегасителей и звукопоглотителей. Одним из способов получения пористых материалов является введение в шихту выгорающих добавок.
Синтез композитов осуществляется при высоких температурах, стимулирующих рост и агрегацию кристаллов. Эти процессы компенсируются действием промотирующих добавок [1–3]. Формирование композитов на основе железо-калиевооксидных систем с бидисперсной пористой структурой является принципиальной проблемой их синтеза [4]. Преимущества такой структуры по сравнению с монодисперсной заключаются в наибольшей степени использования внутренней поверхности материала [5]. Увеличение площади удельной поверхности, размера и объема пор [6] ведет к повышению гигроскопичности и хрупкости материала [7]. Введение промотирующих и выгорающих добавок способствует получению пористого композита при высоких температурах.
Пористую керамику с полидисперсной структурой на основе диоксида кремния [8], с мезопорами диаметром до 30 нм, макропорами диаметром 10 мкм и ультрамакропорами диаметром 50 мкм, можно назвать наиболее близким аналогом композита с бидисперсной структурой. Композит получен с использованием в качестве выгорающих добавок: муки (длиной частиц 10–20 мкм и их диаметром 2 мкм), крахмала (диаметром частиц 5–70 мкм), микроцеллюлозы (длиной волокон 10–30 мкм, диаметром ~2–5 мкм), технической сажи (диаметром частиц 50 нм). Значительное количество (2−25 мас. %) указанных выгорающих добавок повышает риск разрушения материала за счет большого количества и размера макропор и ультрамакропор.
В работе [9] показано применение порошковой целлюлозы (ПЦ) в качестве выгорающей добавки (1−3 мас. %) для получения пористого композита на основе железо-калиевооксидных систем, обладающего гомогенностью состава и содержащего незначительное количество моноферрита калия. ПЦ обладает следующими характеристиками: молярное соотношение С/О 1.2, удельная поверхность 6.00 м2/г, общий объем пор 0.007 см3/г, средний диаметр пор 4.8 нм, средний диаметр частиц ∼2.5 мкм. Низкое значение молярного соотношения С/О и текстурные характеристики ПЦ являются недостатками использованной выгорающей добавки.
Лигнин березы − представитель лигнинов лиственных пород древесины хорошо изучен. В работе [10] были исследованы макромолекулярные характеристики диоксанлигнина березы и его химическая структура. Компактные гидродинамические размеры макромолекул лигнина березы и их разветвленность предопределяют потенциальные области его применения – в качестве наполнителей, сорбентов, носителей катализаторов и выгорающих добавок. Ранее диоксанлигнин березы (ДЛБ) не был использован для получения железо-калиевооксидного композита с бидисперсной структурой. В данном исследовании на примере ДЛБ подобраны условия для использования лигнинов лиственных пород древесины, выделенных органосольвентными методами, в качестве выгорающих добавок. ДЛБ имеет следующие характеристики: молярное соотношение С/О 2.4, удельная поверхность 30.00 м2/г, общий объем пор 0.055 см3/г, средний диаметр пор 1.8 нм, средний диаметр частиц 3 мкм и использован в качестве выгорающей добавки в количестве 0.125−0.250 мас. %. Учитывая различия химического строения и термической устойчивости ПЦ и ДЛБ, уменьшено количество используемой микродобавки ДЛБ в 8−12 раз от количества добавки ПЦ.
Цель данной работы – синтез пористого многокомпонентного композита с применением диоксанлигнина березы, исследование процессов фазообразования, изучение микроструктуры и характеристик полученного композита.
ЭКСПЕРИМЕНТАЛЬНАЯ ЧАСТЬ
В качестве исходных реагентов использованы кристаллогидрат нитрата железа (III) марки “хч”, кристаллогидрат нитратa церия (III) марки “хч”, нитрат калия марки “хч”, оксид молибдена (VI) марки “хч”, оксид титана (IV) марки “осч”, карбонат кальция марки “ч”, тетраэтоксисилан (ТУ6-09-11 053-94) и ДЛБ, взятые в стехиометрическом соотношении. ДЛБ выделен и очищен по методике [11].
Приготовление шихты композита включает импрегнирование выгорающей микродобавки диоксанлигнина березы продуктами гидролиза солей, полученных с использованием способов соосаждения и золь-гель, высушивание и дальнейшую термообработку на воздухе. Образцы композита в виде таблеток сформованы методом полусухого прессования и обожжены ступенчато на воздухе в интервале температур 20−700°С, со скоростью нагрева (Vнагр) 10°С/мин и изотермической выдержкой в течение 3 ч.
Объектом исследования представлен композит, полученный из шихты с соотношением компонентов, мас. %: [Fe2O3 : K2O : MоO3 : CeO2 : CaO : TiO2 : MgO : SiO2] : ДЛБ = = (100 − х)[56.71 : 20.88 : 11.55 : 6.38 : 3.68 : 0.58 : 0.11 : 0.11] : x, где х – 0−0.250.
Приводимые значения Т1/Т2, содержания фаз, среднего размера области когерентного рассеяния (ОКР), отвечали значениям, полученным способами соосаждения и золь-гель соответственно.
Изучение термических превращений ДЛБ и ксерогелей композита проведено методом синхронного термического анализа (ТГ-ДСК) на приборе NETZSCHSTA 409 PC. Измерения осуществлены в динамическом режиме в интервале температур 25−200°С со скоростью нагрева Vнагр 1°С/мин и 200−800°С с Vнагр 10°С/мин для образца ДЛБ и в интервале температур 25−200°С с Vнагр 1°С/мин и 200−1200°С с Vнагр 10°С/мин для образцов композита в алундовых тиглях на воздухе. Ошибка измерений составила ±1%.
Оценка вклада значения энтальпии термодеструкции ДЛБ в общее значение энтальпии, выделяющейся при протекании процессов в результате термообработки композита, проведена на основании расчета энтальпии в характерных для них температурных интервалах с использованием программы NETZSCH Proteus®.
Для идентификации фазового состава исходного ДЛБ и образцов композита использован метод рентгеновской порошковой дифрактометрии (XRD-6000 Shimadzu, излучение CuKα, λ = 1.54184 Å). Полнопрофильный анализ рентгенодифракционных картин и уточнение структур методом Ритвельда проведены с помощью программы PowderCell v.2.4 [12] и базы данных ICSD [13]. Оценка размера ОКР в полученных образцах композита осуществлена по уширению дифракционных линий с использованием формулы Селякова–Шеррера [14]. Ошибка измерений составила ±1%.
Морфология, структура образцов композита и их элементный состав исследованы с помощью сканирующей электронной микроскопии (СЭМ) на приборе VEGA3 TESСAN 3 LMH с энергодисперсионным спектрометром X-Max 50 Oxford Instruments.
Измерение площади удельной поверхности, объема пор, диаметра пор ДЛБ и образцов композита проведено методом низкотемпературной физической сорбции азота на приборе Quantachrome Nova 1200a. Ошибка измерений составила ±3%.
Оценка размера частиц (dср) в порошках выполнена по результатам определения величины их удельной поверхности [15]. Определение пикнометрической плотности (ρпикн) ДЛБ и образцов композита проведено согласно ГОСТ 31992.1-2012 (ISO 2811-1:2011).
РЕЗУЛЬТАТЫ И ИХ ОБСУЖДЕНИЕ
Химический состав изучаемого композита сопоставим с химическим составом композита, полученного с использованием ПЦ в качестве выгорающей добавки [9].
Подобно окислительной термодеструкции древесины всех пород [16], по результатам исследования исходного ДЛБ методом ТГ-ДСК, десорбция физически связанной воды происходит в интервале температур 33−180°С (эндоэффекты, минимумы 50, 109 и 148°С). Процессы термодеструкции ДЛБ (дегидратация, деполимеризация и окисление) протекали последовательно в интервале температур 230−730°С. Процессам термодеструкции отвечают эффекты: максимумы 298°С (экзо), 424°С (экзо), 550°С (экзо), минимум 557°С (эндо) и максимум 652°С (экзо) соответственно.
По результатам изменения температурных интервалов термических процессов, протекающих в шихте композита, установлено, что увеличение количества ДЛБ в составе шихты понизило температуру протекания эндотермических (термодеструкция ДЛБ, разложение NH4NO3, образование KFe11O17) и экзотермических (окисление оксидов железа до γ-Fe2O3 и α-Fe2O3 и первичная рекристаллизация α-Fe2O3) процессов и сузило их температурные интервалы при обоих способах получения композита. В то же время увеличение количества ДЛБ в составе шихты привело к расширению температурных интервалов протекания эндо- (образование К2MoO4 и испарение ферритов) и экзотермических (образование К2MoO4 и собирательная рекристаллизация α-Fe2O3) процессов при обоих способах получения композита. Определено, что с увеличением количества ДЛБ в составе шихты остальные эндо- и экзотермические процессы протекают разнонаправленно в зависимости от способа получения композита (табл. 1).
Таблица 1.
Процессы, протекающие в шихте композита, в зависимости от количества микродобавки ДЛБ и способа получения
Протекающий процесс | Тепловой эффект | Интервалы термических эффектов, °С | |||||
---|---|---|---|---|---|---|---|
x, мас. % | |||||||
0 | 0.125 | 0.250 | |||||
Способы получения шихты | |||||||
соосаждение | золь-гель | соосаждение | золь-гель | соосаждение | золь-гель | ||
Удаление адсорбированной H2O [17] | эндо | 25−170 | 25−147 | 25−150 | 25−172 | 25−133 | 25−172 |
Окисление ДЛБ Термодеструкция ДЛБ |
эндо экзо эндо |
25−150 230−698 550−648 |
25−172 172−730 550−648 |
25−133 196−698 553−642 |
25−172 172−600 553−642 |
||
Разложение NH4NO3, Mg(OH)2, Ce(OH)4, Fe (OH)3 [18] | эндо эндо |
170−335 335−671 |
147−342 342−720 |
255−300 326−698 |
151−304 304−740 |
263−326 326−698 |
146−307 304−630 |
4Fe3O4 + O2 → 6 γ-Fe2O3 [3] γ-Fe2O3 → α-Fe2O3 [3] |
экзо экзо |
305−418 418−671 |
311−406 406−710 |
314−402 401−506 |
304−400 400−579 |
312−412 412−511 |
304−393 520−571 |
Образование К2MoO4 | |||||||
(240−360) [19] (360−500) [20] (360–500) [21] |
эндо экзо экзо |
298−323 426−507 − |
300−323 411−483 − |
298−326 405−513 519−579 |
285−355 400−524 524−555 |
296−336 415−512 519−579 |
287−342 416−497 530−562 |
Образование | |||||||
KFeO2 [22, 23] KFe11O17 [22, 24] |
эндо эндо |
614−671 817−961 |
657−721 846−949 |
550−640 647−712 |
658−743 788−928 |
552−657 648−730 |
547−601 749−807 |
Испарение ферритов [24] Плавление K2MoO4 [24] |
эндо эндо |
1137−1200 961−965 |
830−937 949−999 |
1141−1200 903−910 |
830−946 859−932 |
1135−1200 878−930 |
798−946 825−870 |
Рекристаллизация α-Fe2O3 [24] | |||||||
первичная собирательная |
экзо экзо |
888−1060 1060−1200 |
983−1108 1070−1200 |
980−1013 1086−1200 |
920−996 1059−1200 |
987−1002 1002−1200 |
861−877 950−1113 |
Завершение потери массы (по Маршу) | 25−600 | 25−779 | 25−710 | 25−742 | 25−710 | 25−600 |
По результатам расчета определено значение энтальпии термодеструкции исходного ДЛБ, равное 11295 Дж/г. С введением выгорающей микродобавки 0.125 и 0.250 мас. % ДЛБ в состав шихты композита вклад энтальпии термодеструкции ДЛБ в общее значение энтальпии экзотермических процессов составил, %, 5.40/4.00 и 8.20/4.80 соответственно.
При повышении температуры одновременно прошли процессы термодеструкции ДЛБ, катализируемые присутствующими оксидами [9], и фазообразования сложных оксидов, стимулированные тепловыми эффектами термодеструкции ДЛБ. Следует учесть, что введение оксида церия CeO2 в железо-калиевооксидную систему привело к смещению эндоэффектов образования моноферритов калия KFeO2 в сторону бóльших, а полиферритов калия KFe11O17 − меньших температур, вследствие чего произошло перераспределение ферритных фаз [2]. При обоих способах получения сместилось начало температур образования KFeO2 в область низких температур на 64°С/1°С и на 62°С/110°С, а KFe11O17 − на 170°С/58°С и 169°С/97°С при использовании 0.125 и 0.250 мас. % ДЛБ соответственно (табл. 1). Показано, что снижение температур начала образования KFeO2 и KFe11O17 зависит от количества микродобавки ДЛБ при использовании золь-гель способа для приготовления шихты, но не зависит в случае применения способа соосаждения солей.
Температуры завершения процессов, идущих с изменением массы, с применением 0.125 и 0.250 мас. % ДЛБ и использованием способа соосаждения повысились на 110°С, а с использованием золь-гель способа эти температуры снизились на 37 и 179°С соответственно (табл. 1).
Таким образом, методом ТГ-ДСК определено комплексное влияние как количества микродобавки ДЛБ, так и способа получения на температуры завершения процессов фазообразования.
Согласно результатам рентгенофазового анализа, в образцах, обожженных при идентичных условиях, найдено сходство влияния способов получения на фазовый состав образцов композита. В конечных продуктах отсутствуют оксигидроксидные фазы железа. Следовательно, при обоих способах процессы дегидратации оксигидроксидных фаз и их фазовые переходы в оксид железа α-Fe2O3 [3] ускорялись, о чем свидетельствует снижение температуры получения α-Fe2O3 (табл. 1).
В образцах, обожженных при температуре 700°С, в отсутствии ДЛБ, идентифицированы фазы оксида железа α-Fe2O3 (76/68 об. %), оксида церия CeO2 (11/18 об. %) и молибдата калия K2MoO4 (13/14 об. %). Введение в шихту 0.250 мас. % ДЛБ повлияло на изменение фазового состава образцов, обожженных при той же температуре. Количество фазы K2MoO4 увеличилось до 43/25 об. %. С использованием обоих способов образовалась фаза KFeO2 (10 об. %). В отсутствии ДЛБ ферриты калия в композите формируются до 800°С. С введением в шихту ДЛБ температура образования ферритов калия снижена на 100°С. Аналогичное понижение температуры образования ферритов калия определено для композита с введением в шихту выгорающей добавки ПЦ [9].
В отсутствии промоторов средний размер ОКР α-Fe2O3 (650°С) равен 58 нм. В присутствии промоторов CeO2 и К2O [2] размер ОКР α-Fe2O3 уменьшился до 35 нм. В изучаемом нами композите, имеющем в своем составе набор промоторов K2O, MоO3, CeO2, CaO, TiO2, MgO и SiO2, средний размер ОКР α-Fe2O3 уменьшился до 27/28 нм. С введением ДЛБ в шихту средний размер ОКР уменьшился до 23 нм с использованием способа соосаждения и практически не изменился с использованием золь-гель способа (30 нм). Снижение среднего размера ОКР α-Fe2O3 в полученном композите объясняется формированием фазы KFeO2, подобно формированию фазы KFeO2 на поверхности частиц α-Fe2O3 в системе α-Fe2O3–K2O [2]. Комбинированное влияние набора промоторов и выгорающей микродобавки с использованием способа соосаждения способствовало уменьшению агломерации α-Fe2O3.
Средние размеры ОКР CeO2 и K2MoO4 в отсутствии ДЛБ были равны 27/25 и 49/73 нм соответственно. С введением 0.250 мас. % ДЛБ в шихту, средние размеры ОКР CeO2 и K2MoO4 изменились до значений 15/37 и 14/85 нм соответственно. Уменьшение среднего размера ОКР CeO2 на 55% с использованием способа соосаждения происходит вследствие сегрегации CeO2 по границам агломератов. Увеличение среднего размера ОКР CeO2 на 40% с использованием золь-гель способа позволяет судить об образовании агрегатов CeO2 в объеме композита. В зависимости от способа получения шихты, оксид церия локализован не только в матрице α-Fe2O3, но и на поверхности агломератов, что подтверждено результатами исследований методом СЭМ (рис. 1). С использованием способа соосаждения в композите образовались агломераты, содержащие в своем объеме кристаллиты K2MoO4 меньших размеров, по сравнению с размерами кристаллитов K2MoO4, полученных при использовании золь-гель способа (рис. 1в, е). С введением микродобавки ДЛБ в шихту идентифицирована фаза KFeO2, средний размер ОКР которой составил 114/200 нм. В композите, полученном с использованием способа соосаждения, средний размер ОКР KFe11O17 составил 160 нм, а в композите, полученном с использованием золь-гель способа, отмечено полное отсутствие данной фазы.
Рис. 1.
Электронно-микроскопические изображения образцов, полученных с использованием способа соосаждения с импрегнированием микродобавки ДЛБ в мас. %: 0 (а), 0.125 (б), 0.250 (в); с использованием способа золь-гель с импрегнированием микродобавки ДЛБ в мас. %: 0 (г), 0.125 (д), 0.250 (е).
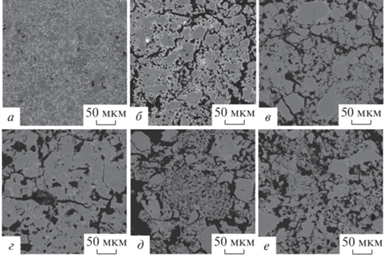
Установлено, что в образцах, полученных в отсутствии ДЛБ, средний размер ОКР образовавшихся фаз не зависит от способов получения, за исключением K2MoO4. Введение ДЛБ в шихту способствовало уменьшению средних размеров ОКР образовавшихся фаз композита с использованием способа соосаждения и увеличению с использованием золь-гель способа. Вероятно, с введением микродобавки ДЛБ в состав композита процессы спекания, сопровождающиеся агломерацией вторичных частиц, ускоряются с использованием золь-гель способа.
Изучено формирование микроструктуры композита в зависимости от способов получения и количества введенного ДЛБ. В микроструктуре образцов композитов, синтезированных с использованием способов соосаждения (рис. 1а–в) и золь-гель (рис. 1г–е), наблюдается высокая однородность распределения всех компонентов материала. В матрице α-Fe2O3 (фазы серого цвета) равномерно распределены включения всех использованных промоторов (фазы светлого и белого цвета) либо в виде индивидуальных кристаллов, либо небольших кластеров.
С использованием обоих способов получения композита образовалась так называемая “сетка”, состоящая из кристаллитов размером 1 × 2 мкм, и сформировались агрегаты 20 × 40 и 60 × 70 мкм, что соответствует введению 0.125 и 0.250 мас. % ДЛБ. Размеры агломератов образцов, полученных с использованием золь-гель способа, в два раза меньше по сравнению с размерами агломератов образцов, полученных с использованием способа соосаждения, того же химического состава. Вероятно, речь идет о замедлении агломерации с использованием золь-гель способа.
Таким образом, установлена зависимость влияния способов получения композита на агломерацию кристаллитов при термообработке. Образцы, полученные в отсутствии ДЛБ, отличались большей пористостью (рис. 1г) с использованием золь-гель способа, чем с использованием способа соосаждения. Пористость образцов зависит от количества введенной выгорающей добавки в состав шихты (рис. 1б, в, д, е). С введением микродобавки ДЛБ в состав шихты получена структура мелкозернистой керамики с сетчато-ячеистым каркасом, аналогичной структуре пенокерамики [25].
Результаты рентгенофазового анализа и сканирующей электронной микроскопии подтвердили результаты измерения текстурных характеристик и расчета среднего размера частиц образцов, полученных с применением ДЛБ (табл. 2). Размер кристаллитов, определенный по уширению линии рентгеновской дифракции в пределах погрешности методов, соответствовал размеру частиц по результатам исследований методами СЭМ и низкотемпературной физической сорбции азота.
Таблица 2.
Характеристики образцов пористого железо-калиевооксидного композита
№ образца композита | Способ получения | Количество ДЛБ, мас. % | Удельная поверхность, Sуд, м2/г | Общий объем пор, Vпор, см3/г | Средний диаметр мезопор, dпор, нм | Средний диаметр макропор, dпор, нм | Средний диаметр частиц, dср, мкм |
---|---|---|---|---|---|---|---|
1 | Соосаждение | 0 | 5.29 ± 0.04 | 0.008 ± 0.001 | 38 ± 1 | 52 ± 1 | 1.2 ± 0.1 |
2 | Соосаждение | 0.125 | 1.89 ± 0.04 | 0.007 ± 0.001 | 40 ± 1 | 100 ± 1 | 1.4 ± 0.1 |
3 | Соосаждение | 0.250 | 2.86 ± 0.04 | 0.006 ± 0.001 | 16 ± 1 | 130 ± 1 | 2.2 ± 0.1 |
4 | Золь-гель | 0 | 7.86 ± 0.04 | 0.011 ± 0.001 | 32 ± 1 | 58 ± 1 | 0.8 ± 0.1 |
5 | Золь-гель | 0.125 | 5.22 ± 0.04 | 0.013 ± 0.001 | 36 ± 1 | 75 ± 1 | 1.2 ± 0.1 |
Удельная поверхность (Sуд) и общий объем пор (Vпор) образцов с применением ДЛБ, полученных с использованием золь-гель способа, выше в два раза значений Sуд и Vпор образцов, полученных с использованием способа соосаждения, что объясняется дисперсностью частиц. В образцах, полученных обоими способами, обнаружено наличие мезопор диаметром до 40 нм и макропор диаметром до 130 нм, что соответствует бидисперсной структуре композита. Если средний диаметр мезопор в образцах, полученных обоими способами, одинаков, то средний диаметр макропор выше у образцов композита, полученного с применением ДЛБ и использованием способа соосаждения (табл. 2).
ЗАКЛЮЧЕНИЕ
В результате изучения процессов фазообразования в многокомпонентном композите в условиях термического нагрева, вследствие введения в шихту диоксанлигнина березы (0.125−0.250 мас. %), имеющего повышенное содержание углерода в структуре и более высокую термическую устойчивость по сравнению с порошковой целлюлозой, установлено, что как способ получения, так и количество выгорающей микродобавки оказали существенное влияние на температурные интервалы эндо- и экзотермических процессов, протекающих при формировании фазового состава, морфологии и структуры композита. Для изготовления пористого железо-калиевооксидного композита со средним диаметром мезопор 16 нм и макропор 130 нм, отвечающим бидисперсной структуре, предложен способ, включающий импрегнирование выгорающей микродобавки диоксанлигнина березы продуктами гидролиза солей, полученных с использованием способа соосаждения.
Работа выполнена при финансовой поддержке РФФИ и Республики Коми в рамках научного проекта № 20-43-110001 с использованием оборудования Центров Коллективного Пользования “Химия” ИХ и “Геонаука” ИГ ФИЦ Коми НЦ УрО РАН.
Список литературы
Аниканова Л.Г., Дворецкий Н.В. Стабилизация щелочных промоторов в структуре железооксидных катализаторов дегидрирования // Катализ в промышленности. 2016. Т. 16. № 1. С. 29−36.
Lamberov A.A., Dementeva E.V., Kuzmina O.V., Gilmanov K.K. Investigating the mechanism of the effect of cerium additives on the properties of the iron-potassium the active system component of dehydrogenation catalysts of hydrocarbons report 2 // Catalysis in Industry. 2013. V. 5. № 1. P. 50−60.
Cornell R.M., Schwertmann U. The Iron Oxides: Structure, Properties, Reactions, Occurrences, and Uses // Weinheim, Germany: Wiley, 2003. 703 p.
Комаров В.С., Бесараб С.В. Синтез бипористых металлосиликатных адсорбентов и катализаторов // Весцi нацыянальнай акадэмii навук Беларусi. Серыя хiмiчных навук. 2013. № 1. С. 36−39.
Комаров В.С., Бесараб С.В. Адсорбенты и носители катализаторов. Научные основы регулирования пористой структуры: 2014. М.: ООО “Научно-издательский центр ИНФРА-М”. 203 с.
Пат. RU2470704 Катализатор дегидрогенизации. Опубл. 27.12.2012. Бюл. № 36.
Гаршин А.П. Материаловедение. Техническая керамика в машиностроение. Учебник. Москва, 2018. Сер. 63. 296 с.
Ратько А.И., Иванец А.И., Азаров С.М. Влияние добавок на пористую структуру керамики на основе кристаллического SiO2 // Неорг. матер. 2008. Т. 44. № 7. С. 883−889.
Бугаева А.Ю., Лоухина И.В., Казакова Е.Г., Назарова Л.Ю., Рябков Ю.И. Влияние порошковой целлюлозы и способа получения шихты на фазовый состав и характеристики железо-калиевооксидного материала // ЖПХ. 2019. Т. 92. Вып. 10. С. 1271−1282.
Belyy V.A., Karmanov A.P., Kocheva L.S., Nekrasova P.S., Kaneva M.V., Lobov A.N., Spirikhin L.V. Comparative study of chemical and topological structure of macromolecules of lignins of birch (Betula verrucosa) and apple (Malus domestica) wood. International Journal of Biological Macromolecules // 2019. V. 128. P. 40–48.
Pepper J.M., Siddiqueullah M. The effect of initial acid concentration on the lignin isolated by the acidolysis of aspen wood // Canad. J. Chem. 1961. V. 39. № 7. P. 1454–1461.
Kraus W., Nolze G. Powder cell – a program for the representation and manipulation of crystal structures and calculation of the X-ray powder patterns // J. Appl. Cryst. 1996. V. 29. P. 301−303.
Belsky A., Hellenbrandt M., Karen V.L., Luksch P. New developments in the inorganic crystal structure database (ICSD): accessibility in support of materials research and design // Acta Cryst. B. 2002. V. 58. № 3. P. 364–369.
Егоров-Тисменко Ю.К. Кристаллография / Под ред. Урусова В.С. М.: КДУ, 2005. 592 с.
Гаврилова Н.Н. Анализ пористой структуры на основе адсорбционных данных. М.: РХТУ им. Д. И. Менделеева, 2015. 132 с.
Лоскутов С.Р., Шапченкова О.А., Анискина А.А. Термический анализ древесины основных лесообразующих пород средней Сибири // Сибирский лесной журн. 2015. № 6. С. 17–30.
Михайлов В.И., Кривошапкина Е.Ф., Кривошапкин П.В., Рябков Ю.И. Влияние электрокинетических свойств целлюлозы на морфологию оксида железа (III) при темплатном синтезе // Физика и химия стекла. 2016. Т. 42. № 6. С.752–763.
Лидин Р.А., Молочко В.А., Андреева Л.Л. Химические свойства неорганических веществ. М.: Химия, 2000. 480 с.
Muan A., Gee C.L. Phase Equilibrium Studies in the System Iron Oxide-Al2O3 in Air and at 1 Atm. O2 Pressure // J. Am. Ceram. Soc. 1956. V. 39. № 6. P. 207−214.
Гудкова И.А., Солодовникова З.А., Солодовников С.Ф., Золотова Е.С., Куратьева Н.В. Фазообразование в системах Li2MoO4–K2MoO4–MMoO4 (M = Ca, Pb, Ba) и кристаллическая структура α-KLiMoO4 // Журн. неорг. химии. 2011. Т. 56. № 9. С. 1517–1526.
Пат. РФ 2187364 Катализатор для дегидрирования алкилароматических углеводородов. Опубл. 20.08.2002. Бюл. № 23.
Гильманов Х.Х., Ламберов А.А., Дементьева Е.В., Щатохина Е.В., Иванова А.В., Губайдуллина А.М. Влияние условий термообработки железооксидного катализатора дегидрирования на образование полиферритных фаз // Неорг. матер. 2008. Т.44. № 1. С. 95−101.
Kotarba A., Rozek W., Serafin I., Sojka Z. Reverse effect of doping on stability of principal components of styrene catalyst: KFeO2 and K2Fe22O34 // J. Catalysis. 2007. V. 247. № 2. P. 238−244.
Киселев А.Е., Кудин Л.С., Ильин А.П. Исследование железооксидного катализатора К2О ⋅ nFe2O3. II. Термодинамика сублимации К2О // Изв. вузов. Сер. хим. и хим. технол. 2014. Т. 57. № 3. С. 12−15.
Gibson L.J., Ashby M.F. Cellular solids: structure and properties. Cambridge University Press. 1997. 510 p.
Дополнительные материалы отсутствуют.
Инструменты
Физика и химия стекла