Физика Земли, 2021, № 5, стр. 104-119
Динамика роста трещины гидроразрыва по данным ультразвукового просвечивания в лабораторных экспериментах
С. Б. Турунтаев 1, 2, *, Е. В. Зенченко 1, **, П. Е. Зенченко 1, ***, М. А. Тримонова 1, ****, Н. А. Барышников 1, *****, *, Е. В. Новикова 1, 2, ******
1 Институт динамики геосфер имени академика М.А. Садовского РАН
г. Москва, Россия
2 Московский физико-технический институт
г. Москва, Россия
* E-mail: s.turuntaev@gmail.com
** E-mail: zenchevj@gmail.com
*** E-mail: zenpet22@gmail.com
**** E-mail: trimonova.ma@gmail.com
***** E-mail: nabarysh@gmail.com
* E-mail: s.turuntaev@gmail.com
****** E-mail: helenvn97@gmail.com
Поступила в редакцию 12.03.2021
После доработки 29.03.2021
Принята к публикации 01.04.2021
Аннотация
Данные акустического просвечивания, полученные в лабораторном эксперименте, были использованы для выделения стадий возникновения, роста и заполнения жидкостью трещины гидроразрыва. Лабораторная установка позволяет выполнять эксперименты с пористыми насыщенными образцами искусственных материалов диаметром 430 мм и высотой 70 мм. В качестве модельного материала использовалась смесь гипса с цементом, образец насыщали водным раствором гипса и нагружали вертикальными и двумя горизонтальными независимыми напряжениями. Трещина создавалась закачкой вязкой жидкости с постоянной скоростью через обсаженную скважину в центре образца. Мониторинг гидроразрыва пласта осуществлялся путем регистрации ультразвуковых импульсов, проходящих через образец. Сравнение вариаций амплитуд ультразвуковых импульсов и давления закачки привело к следующим наблюдениям: начало роста трещины гидроразрыва пласта происходит при давлении, меньшем максимального значения; рост трещины происходит быстрее ее заполнения жидкостью; после заполнения трещины жидкостью происходит увеличение раскрытия трещины. Когда закачка прекращается, регистрируется закрытие трещины по мере снижения давления в скважине за счет фильтрации в образец. Показана возможность создания вторичной трещины гидроразрыва в случае изменения ориентации главных сжимающих напряжений при условии, если первичная трещина перпендикулярна оси скважины, а вторичная – параллельна оси.
ВВЕДЕНИЕ
Гидравлический разрыв пласта, осуществляемый путем закачки жидкости в заданный интервал скважины под давлением, превышающим прочность пород и минимальные напряжения, остается основным методом увеличения притока нефти к скважине [Economides, Nolte, 2000]. Несмотря на достаточно большую историю применения этого метода и существование большого количества расчетных пакетов программ, предназначенных для дизайна ГРП (симуляторов ГРП) [Hattori et al., 2017], нефтедобывающие и нефтесервисные компании зачастую сталкиваются с проблемами при проведении гидроразрыва, ряд из которых связан с недостаточной проработанностью физических моделей, заложенных в расчетные программные пакеты. Развитие и усложнение этих моделей требует постановки новых экспериментов в лаборатории, которые позволили бы оценить вклад тех или иных факторов на развитие трещин ГРП.
Существует множество теоретических и экспериментальных исследований возникновения и распространения трещины гидроразрыва [Zoback et al., 1977; Stanchits et al., 2012; Bunger et al., 2013; Baykin, Golovin, 2018; Gladkov, Linkov, 2018; Liu et al., 2008; Berchenko, Detournay, 1997; Smirnov et al., 2020]. Все известные модели имеют ограничения, оценить которые можно только проводя эксперименты. Эксперименты в реальных условиях, на месторождениях, проводить или невозможно, или очень сложно и дорого. Поэтому требуется проводить эксперименты на образцах реальных пород или на искусственных образцах. Для выполнения требования масштабируемости эксперимента к реальным условиям наиболее эффективным является выбор материала образца и условий эксперимента в соответствии с критериями подобия [De Pater et al., 1994]. Эксперименты на больших (от 0.3 до 1 м) образцах горных пород кубической формы, используемых во многих геомеханических лабораториях, обладают рядом недостатков: сложность и дороговизна подготовки и проведения экспериментов, сохраняющиеся вопросы к масштабируемости результатов, полученных на образцах, хотя и больших, но все равно малых по сравнению с реальными ситуациями, неоднородности поля напряжения из-за кубической формы образцов, сложности получения однородных образцов большого размера и т.д.
Для преодоления ряда экспериментальных проблем в ИДГ РАН была создана уникальная установка, позволяющая проводить эксперименты на образцах искусственного пористого материала, подобранного в соответствии с критериями подобия. Образцы имеют форму дисков диаметром 0.43 м и высотой 0.07 м, установка позволяет нагружать образцы по трем независимым осям, создавать градиенты порового давления, измерять поровое давление жидкости в нескольких точках, регистрировать акустическую эмиссию, прозвучивать образец акустическими импульсами. Результаты экспериментов, проводящихся на этой установке, приведены в публикациях [Зенченко и др., 2019; Trimonova et al., 2017; Turuntaev et al., 2017; Borisov et al., 2020].
В настоящей статье представлены результаты экспериментов по изучению распространения трещины гидроразрыва путем сопоставления изменения давления жидкости, закачиваемой в образец с постоянным расходом, и изменения амплитуд ультразвуковых волн, проходящих через образец в процессе образования трещины. Метод применялся в ряде работ [Groenenboom, Fokkema, 1998; Groenenboom et al., 2001; Stanchits et al., 2012] для изучения как распространения трещины, так и повторного открытия трещины гидроразрыва. Отличием настоящей работы, помимо формы и материала образцов, является проведение повторного гидроразрыва после изменения напряженного состояния, создаваемого в образце.
Полученные экспериментальные результаты могут служить основой для усложнения теоретических моделей, описывающих образование и распространение трещин ГРП, возможности повторного ГРП, использование кривых изменения давления закачки для оценки свойств породного массива и его напряженного состояния в призабойной зоне.
ОПИСАНИЕ ЭКСПЕРИМЕНТАЛЬНОЙ УСТАНОВКИ
Эксперименты проводились на установке трехосного нагружения, разработанной в ИДГ РАН и подробно описанной в ряде публикаций [Trimonova et al., 2017; Turuntaev et al., 2017; Зенченко и др., 2019]. Конструктивно установка состоит из двух горизонтальных дисков диаметром 0.75 м, между которыми расположено кольцо высотой 0.07 м с внутренним диаметром 0.43 м. Диски между собой стягиваются шпильками, образуя рабочую камеру диаметром 0.43 м при высоте 0.07 м. В дисках и кольце имеется ряд отверстий, которые могут использоваться для монтажа пьезоэлектрических преобразователей акустической эмиссии, датчиков давления, а также для закачки и откачки жидкостей. В качестве модельного материала использовалась смесь гипса с добавлением портландцемента, которая заливалась в рабочий объем установки при снятом верхнем диске. Затем материал затвердевал и высушивался, формируя образец с пористостью 40–45% и проницаемостью 1–3 мД (1–3 × 10–15 м2). Вопросы подобия и адекватности используемого модельного материала и параметров эксперимента применительно к гидроразрыву в полевых условиях были рассмотрены в работе [Trimonova et al., 2017; Turuntaev et al., 2017]. Схема экспериментальной установки приведена на рис. 1.
При сборке установки перед проведением эксперимента поверхность образца накрывалась резиновой мембраной, поверх которой устанавливался верхний диск. Между мембраной и диском сохранялся небольшой зазор толщиной около 2 мм, который был заполнен водой под заданным давлением, создаваемым буферным объемом сжатого азота, что обеспечивало необходимое вертикальное напряжение в образце. Для задания горизонтальных напряжений на внутренней поверхности кольца были смонтированы четыре герметичные камеры из тонкой листовой меди со штуцерами, выведенными наружу. Угловая длина каждой камеры составляла 80°. Штуцеры диаметрально противоположных камер соединялись между собой. Необходимые давления в парных камерах создавались при помощи насоса. Все четыре камеры можно соединить между собой, чтобы создать равнокомпонентное поле горизонтальных напряжений.
При подготовке экспериментов по созданию горизонтальной трещины ГРП перед заливкой образца в центральное отверстие нижнего основания вставлялась латунная трубка диаметром 12 мм с заглушенным концом, имитирующая обсаженную скважину. Трубка содержала затравку из двух слоев латунной сетки с размером ячейки 0.3 мм в виде диска диаметром 25 мм, расположенного на глухом конце трубки на середине высоты образца. Для формирования вспомогательных скважин, расположенных на периферии образца, в нижнем основании устанавливалась вставки из фторопласта, имеющие небольшую конусность, которые после затвердевания гипса вынимались. Образованные отверстия использовались для насыщения порового пространства образца. В качестве порового флюида использовался насыщенный раствор гипса, что предотвращало частичное растворение высушенного образца.
Для создания трещины гидроразрыва в центральную скважину подавалась жидкость (минеральное масло с вязкостью ≈0.1 Па · с) с постоянным расходом ≈0.2 см3/с. Давление в скважине, а также вертикальное давление и давление в боковых камерах измерялось при помощи преобразователей NAT 8252 производства Trafag AG с нормированным токовым выходом. Сигналы с датчиков давления регистрировались с помощью АЦП Е14-440 производства L-Card с частотой дискретизации 100 Гц с записью на жесткий диск персонального компьютера.
Мониторинг трещины гидроразрыва осуществлялся путем регистрации ультразвуковых импульсов, проходящих через образец. Акустические импульсы регистрировались пьезопреобразователями, расположенными в нижнем диске (рис. 2), излучателями служили пьезопреобразователи, расположенные в верхнем диске. Ультразвуковой импульс возбуждался путем подачи на пьезопреобразователи электрического импульса амплитудой ≈200 В. Резонансная частота пьезопреобразователей составляла примерно 250 кГц. Период повторения импульсов составлял 100 или 200 мс. Сигналы с преобразователей подавались на предусилители, после чего регистрировались скоростным АЦП Е20-10 производства L-Card с частотой дискретизации 2.5 МГц на канал с непрерывной записью на жесткий диск компьютера.
Рис. 2.
Схема расположения акустических датчиков и камер бокового нагружения в экспериментальной установке. Светлые кружки Ах – пьезопреобразователи в верхнем основании, черные – в нижнем. Кружки Рх – точки измерения порового давления.
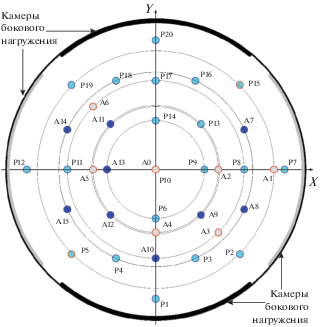
Процедура проведения экспериментов и обработки экспериментальных данных
После сборки установки с образцом пространство между мембраной и верхним диском заполнялось водой. Для уменьшения влияния трения между нижним диском и образцом вначале проводилось нагружение боковыми камерами, после чего осуществлялось вертикальное нагружение. Регистрация давления запускалась до начала нагружения образца. После завершения нагружения включалась нагнетательная установка. После проведения каждого этапа эксперимента верхний диск и резиновая мембрана снимались и образец фотографировался. Если требовалось провести следующий этап эксперимента, установка вновь собиралась. После завершения всех этапов эксперимента образец извлекался из установки. При необходимости образец разделяли на части для визуального исследования образовавшихся трещин ГРП.
Для выделения зондирующих ультразвуковых импульсов при активном акустическом мониторинге использовалась периодичность их посылки. С помощью преобразования Гильберта строились огибающие фрагментов записи, содержащих зондирующие импульсы, и находились их максимальные значения.
РЕЗУЛЬТАТЫ ЭКСПЕРИМЕНТОВ
Эксперимент 1. Создание горизонтальной трещины
Для образования горизонтальной трещины ГРП необходимо, чтобы горизонтальные сжимающие напряжения превышали вертикальное. В описываемом эксперименте вертикальное давление было задано 0.95 МПа. Давление в камерах горизонтального нагружения поддерживалось в диапазоне 1.4–1.6 МПа. На рис. 3 представлена фотография образца после проведения эксперимента. Видно, что образовавшаяся трещина вышла на поверхность в пределах сектора немногим более 90°. Последующее изучение образца показало, что образовавшаяся трещина имеет плоскую горизонтальную часть радиусом приблизительно 10 см, переходящую в коническую поверхность, часть которой доходит до поверхности образца. Схематический разрез трещины и траектории УЗ лучей показаны на рис. 4. Выход трещины на поверхность, видимо, обусловлен различием граничных условий на нижней и верхней плоскостях образца. Аналогичное поведение трещин ГРП наблюдалось в работе [Bunger et al., 2013].
Рис. 3.
Фото образца с горизонтальной трещиной после эксперимента. Темные кружки показывают расположение акустических датчиков в нижнем диске, светлые – в верхнем.
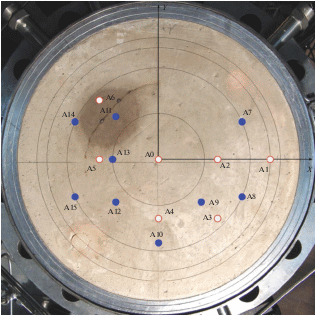
На рис. 5 представлена зависимость давления от времени в центральной скважине, синхронизированная с зависимостями амплитуды огибающей ультразвуковых импульсов от времени. Можно отметить, что спад амплитуды ультразвуковых импульсов на приемниках начинается до достижения максимального давления, что свидетельствует о начале роста трещины гидроразрыва при давлении, меньшем максимального. После спада следует подъем амплитуд, который обусловлен выходом фронта жидкости, заполняющей трещину ГРП, на линию “источник–приемник”. В той части трещины, которая не вышла на поверхность, масло практически не достигло этих линий, в результате чего амплитуда не выросла. В отличие от спада, начало роста амплитуды четко локализовано во времени. Учитывая пространственное расположение источника ультразвуковых импульсов, приемников и геометрию трещины, можно оценить скорость распространения фронта жидкости ГРП, которая составила ≈35 мм/с, скорость роста трещины при этом оценивается в 100–130 мм/с.
Рис. 5.
Слева – полная запись зависимости давления в центральной скважине и синхронных с ней зависимостей изменения амплитуды огибающей ультразвуковых импульсов от времени. Справа – начальный фрагмент этой записи: вертикальной линией обозначен момент времени достижения максимума давления.

После подъема амплитуды ультразвуковых импульсов регистрируется значительный спад, который обусловлен, по-видимому, постепенным расширением образовавшейся трещины. На приемниках, расположенных ближе к центральной скважине, этот спад максимальный. Отмечается более чем трехкратное падение амплитуды по сравнению с исходной величиной (до образования трещины).
Эксперимент 1. Создание вертикальной трещины
Во второй части эксперимента исследовалась возможность образования новой вертикальной трещины ГРП из той же скважины. Эта часть эксперимента была проведена в три этапа. После каждого этапа установка открывалась и оценивалась длина образовавшейся трещины. Для получения трещины, расположенной в вертикальной плоскости экспериментальной установки, необходимо, чтобы вертикальное напряжение превышало максимальное горизонтальное. На первом этапе были заданы следующие значения давлений в камерах нагружения:
– вертикальное давление – 6.8 МПа;
– давление в камере по оси Х – 3.2 МПа;
– давление в камере по оси Y – 1 МПа.
Существенный контраст горизонтальных напряжений был необходим, чтобы обеспечить рост трещины ГРП в направлении оси Х установки. В качестве излучателей и приемников ультразвука использовались следующие пары преобразователей: для излучателя А3 приемниками были А7 и А8, а для излучателя А6 – приемники А12, А13 и А15. Взаимное расположение излучателей и приемников, а также положение трещины гидроразрыва после первого этапа эксперимента показано на рис. 6. На приемнике А8 амплитуда УЗ импульсов практически не менялась, а на приемнике А7 наблюдался незначительный спад. Трасса А3–А8 находится в стороне от трещины ГРП, а А3–А7 проходит вблизи ее кончика. На трассах А6–А12, А6–А13 и А6–А15 наблюдалось заметное уменьшение амплитуды УЗ импульсов по мере распространения трещины, эти трассы пересекаются трещиной ГРП.
Рис. 6.
Фото образца после проведения первого этапа эксперимента по образованию вертикальной трещины ГРП.
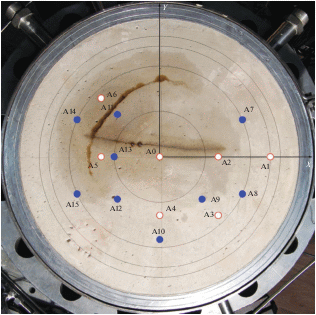
Этапы 2 и 3 эксперимента по образованию вертикальной трещины гидроразрыва были проведены с целью дальнейшего проращивания трещины ГРП, образованной на первом этапе. Эти этапы проведены друг за другом без разборки установки при следующих давлениях:
– вертикальное давление – 5.8–6.8 МПа;
– давление в камере по оси Х – 3 МПа;
– давление в камере по оси Y – 0.1 МПа.
В качестве излучателей и приемников ультразвука использовались следующие пары преобразователей: для излучателя А2 приемниками были А7 и А9, а для излучателя А5 – приемники А11 и А14. Фото образца после проведения этапов 2 и 3 представлено на рис. 7. Зависимость давления от времени для обоих этапов показана на рис. 8. Максимальное давление в рабочей скважине на втором этапе составило ≈9 МПа, а на третьем этапе было около 7 МПа.
Рис. 7.
Фотография образца в экспериментальной установке после проведения этапов 2 и 3 эксперимента по образованию вертикальной трещины ГРП. Стрелками указано положение трещины после первого повторного эксперимента.
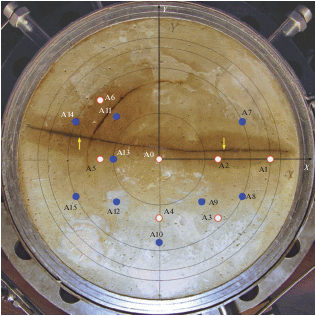
Рис. 8.
Зависимость давления в центральной скважине и нагружающих давлений от времени на этапах 2 и 3 эксперимента по образованию вертикальной трещины ГРП.
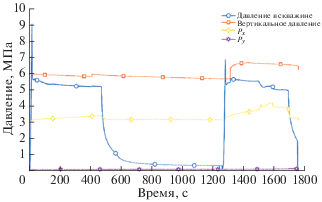
На рис. 9 представлены начальные участки и полные зависимости от времени давлений на этапе 2 синхронно с зависимостями амплитуд принятых УЗ импульсов. По этим зависимостям с учетом геометрии расположения излучателей и приемников в этом эксперименте можно оценить скорость распространения фронта жидкости по трещине ГРП между трассами А5–А11 и А5–А14 как ≈22 мм/с.
Рис. 9.
Начальный участок (слева) и полные записи (справа) зависимостей давления в центральной скважине и нагружающих давлений от времени – верхний график; амплитуды УЗ импульсов для разных приемников – нижний.
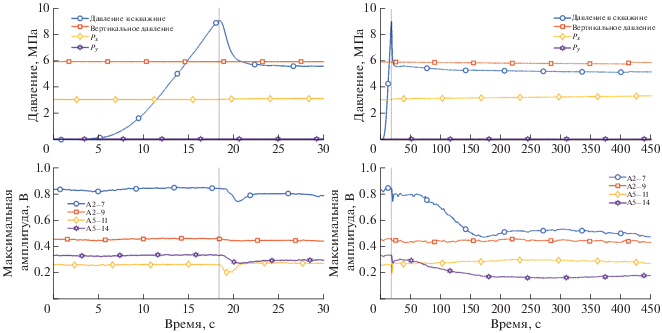
При рассмотрении полных записей следует отметить существенный спад амплитуды УЗ импульсов, особенно отчетливо наблюдающийся на приемнике А7. Этот спад обусловлен, скорее всего, продолжением расширения трещины ГРП по мере поступления в нее рабочей жидкости. При остановке нагнетания амплитуда УЗ импульсов снова начинает расти, что свидетельствует о смыкании трещины по мере спада давления в ней.
После проведения всех этапов эксперимента образец был разделен на две части и извлечен из установки. На фотографиях (рис. 10) видно, что трещина вблизи верхней плоскости образца дошла до его краев, в то время как вблизи нижней их не достигла. Это обусловлено влиянием трения между нижним основанием установки и поверхностью образца. Также на нижнем фото хорошо видна первичная трещина ГРП, особенно ее часть, выходящая на свободную поверхность. Именно в соответствии с этим фото на рис. 4 показано схематическое положение трещины.
Эксперимент 2
Учитывая результаты проведения первого эксперимента, в постановку второго эксперимента были внесены изменения. Для создания близких граничных условий на верхней и нижней плоскостях образца, на поверхность нижнего основания был нанесен тонкий (0.5–1 мм) слой силиконового компаунда. В этом эксперименте, как и в предыдущем, наряду с изучением динамики роста трещины ГРП проводилось исследование возможности получения новой трещины при повторном ГРП в измененном напряженном состоянии. Эксперимент проводился в несколько этапов. На этапах 1 и 2 была образована первичная горизонтальная трещина. Давления в боковых камерах превышали вертикальное. На этапе 3 вертикальное давление было задано бо́льшим, чем горизонтальные. После третьего этапа было проведено две серии экспериментов (3a1–3a5 и 3b1–3b3), в которых сразу после достижения максимального давления в рабочей скважине выключалась подача масла в рабочую скважину. Наконец, целью четвертого и пятого этапов эксперимента было увеличение длины вертикальной трещины. Параметры проведения всех экспериментов приведены в таблице.
Таблица 1
№ этапа | Давление в камере Х, МПа | Давление в камере Y, МПа | Вертикальное давление, МПа | Давление гидроразрыва, МПа |
---|---|---|---|---|
1 | 2.0 | 2.0 | 1.0 | 6.6 |
2 | 2.0 | 2.0 | 1.0 | 5.0 |
3 | 1.15 | 0.5 | 3.1 | 7.7 |
3a1 | 0.53 | 0.53 | 1.5 | 4.4 |
3a2 | 0.52 | 0.52 | 1.5 | 3.7 |
3a3 | 0.52 | 0.52 | 1.5 | 3.4 |
3а4 | 0.52 | 0.52 | 1.5 | 3.2 |
3а5 | 0.52 | 0.52 | 1.5 | 3.0 |
3b1 | 0.54 | 0.54 | 2.0 | 3. 5 |
3b2 | 0.54 | 0.54 | 2.0 | 3.3 |
3b3 | 0.54 | 0.54 | 2.0 | 3.2 |
4 | 2.0 | 1.0 | 4.4 | 7.6 |
5.1 | 1.5 | 0.5 | 4.5 | 7.0 |
5.2 | 1.5 | 0.5 | 4.4 | 6.0 |
5.3 | 1.5 | 0.5 | 4.4 | 5.6 |
Этап 1
Для акустического мониторинга трещины ГРП на этом этапе использовался излучатель А0 и две группы приемников А9, А10, А12 и А13, А14, А15, подключенные к двум разным АЦП. Конфигурация расположения пьезопреобразователей показана на рис. 15. На рис. 11 представлены зависимости давления в рабочей скважине и синхронизированные с ней зависимости амплитуды принятых УЗ импульсов. После проведения первого этапа экспериментальная установка была открыта, каких-либо изменений на поверхности образца обнаружено не было.
Этап 2
На этапе 2 была изменена схема подключения излучателей и приемников ультразвука. В паре с излучателем А0 использовались приемники А8, А13, А14 и А15, а совместно с излучателем А9 – приемники А2, А3 и А4. Расширение зоны зондирования было проведено в предположении дальнейшего распространения трещины ГРП на этом этапе. Зависимости давления в рабочей скважине и синхронные с ней зависимости амплитуды принятых УЗ импульсов для излучателей А0 и А9 представлены на рис. 12. Изменение амплитуды УЗ импульсов происходит раньше по отношению к моменту времени достижения максимума давления в рабочей скважине, чем это наблюдалось на первом этапе. Это может говорить о том, что уже имеющаяся трещина начинает расширяться раньше, чем продолжится ее дальнейший рост, отмечаемый по максимальному давлению. На графиках амплитуды УЗ импульсов для излучателя А9 величина амплитуды не изменяется на протяжении всего эксперимента, что говорит о том, что трещина не пересекла соответствующие трассы излучатель–приемник. После проведения второго этапа эксперимента внешних изменений образца также не произошло.
Этапы 3–5
Целью этапа 3 было исследование возможности создания вертикальной трещины ГРП (вдоль скважины) при изменении напряженно-деформированного состояния коллектора. Параметры проведения эксперимента на этапе 3 следующие:
– вертикальное давление – 3.1 МПа;
– давление в камере по оси Х – 1.15 МПа;
– давление в камере по оси Y – 0.5 МПа.
На рис. 13 приведены зависимости давления в центральной скважине и нагружающих давлений от времени. Величина максимального давления составила 7.7 МПа. На третьем этапе трещина ГРП не пересекла предполагаемые трассы “излучатель–приемник” и не оказала влияния на прохождение ультразвукового сигнала по этим трассам. После проведения третьего этапа эксперимента экспериментальная установка была открыта. Внешних изменений образца замечено не было.
Рис. 13.
Эксперимент 2, этап 3. Зависимости давления в центральной скважине и нагружающих давлений от времени.
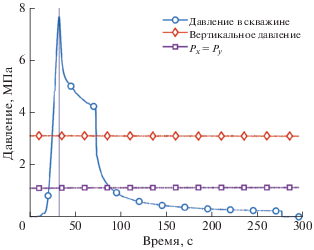
После этапа 3 было проведено две серии экспериментов, в которых сразу после достижения максимального давления в рабочей скважине выключалась подача масла в рабочую скважину. Параметры проведения этих серий приведены в табл. 1 под №№ 3a1–3a5 и 3b1–3b3, зависимости давления в скважине и изменения амплитуд УЗ импульсов приведены на рис. 14. Можно отметить снижение давления гидроразрыва в каждом последующем эксперименте в серии. С увеличением вертикального давления с 1.5 до 2.0 МПа давление гидроразрыва снова возрастает и затем вновь последовательно снижается. Спад амплитуды УЗ сигналов начинается заметно раньше момента достижения максимального давления уже в эксперименте этапа 3а1. На трассах А0–А9 этот спад четко выражен для всех экспериментов серий при различных вертикальных давлениях и при этом практически не сдвигается относительно максимума давления. На трассе А0–А13 выраженное начало изменения амплитуды наблюдается в первых трех экспериментах при вертикальном давлении 1.5 МПа с тенденцией более раннего начала для последующих экспериментов. Во всех остальных экспериментах на этой трассе наблюдается плавное уменьшение амплитуды УЗ сигналов с такой же тенденцией начала спада максимальной амплитуды при меньшем давлении в скважине. Для трассы А0–А12 во всех экспериментах обеих серий выраженного начала спада максимальной амплитуды не наблюдается, а происходит плавное уменьшение амплитуды. Вместе с тем, для трасс А0–А12 и А0–А13 в большинстве экспериментов на зависимостях максимальной амплитуды от времени в момент достижения максимального давления наблюдается небольшой излом. Следует обратить внимание на поведение максимальной амплитуды для трассы А0–А11, которая практически перестает реагировать на изменение давления в скважине, начиная с четвертого эксперимента первой серии с вертикальным давлением 1.5 МПа.
Рис. 14.
Эксперимент 2, этапы 3а1–3b3. Зависимости давления в центральной скважине и нагружающих напряжений – верхние графики; амплитуды УЗ импульсов на разных приемниках для экспериментов 3a1, 3a2, 3b1, 3b3 – нижние графики.
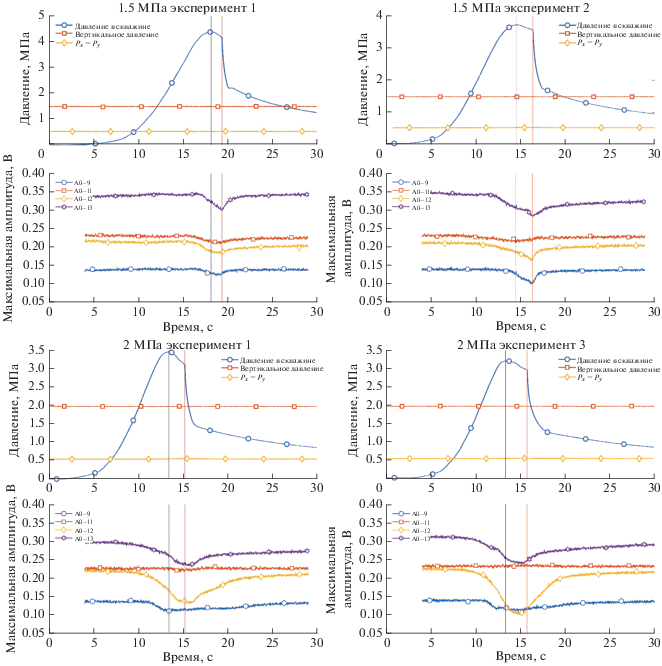
После остановки закачки в скважину амплитуда принятых УЗ импульсов начинает увеличиваться, причем восстановление амплитуды имеет в большинстве случаев ярко выраженное начало, совпадающее с началом спада давления в скважине. Для трасс А0–А9 и А0–А13 изменение максимальной амплитуды слабо меняется от эксперимента к эксперименту. В отличие от этого, изменение амплитуды на трассе А0–А12 заметно увеличивается в следующих друг за другом экспериментах. Этот рост наиболее заметен, начиная с четвертого эксперимента первой серии. Такое поведение максимальной амплитуды принятого УЗ сигнала может свидетельствовать об образовании и дальнейшем росте и расширении вертикальной трещины ГРП, пересекающей трассу А0–А12, что приводит к ослаблению проходящего через нее УЗ импульса. По этой же причине преимущественный рост новой вертикальной трещины приводит к перераспределению потока жидкости, поступающей из скважины, и ослаблению питания первоначальной горизонтальной трещины в направлении А0–А11 и невозможности ее дальнейшего раскрытия и роста.
После проведения этих серий экспериментальная установка была открыта и было обнаружено, что на поверхность образца вышла трещина. Внешний вид образца после проведения этих этапов эксперимента показан на фото рис. 15.
Этапы 4 и 5 были выполнены с целью прорастить образовавшуюся трещину. Фото образца после проведения этих этапов приведено на рис. 16. На фотографии образца видно, что трещина, образовавшаяся после дополнительных экспериментов третьего этапа, удлинилась лишь незначительно. Наряду с ней, из центральной области образца проросла новая трещина, общая длина которой вдвое превышает длину первой вертикальной трещины. При этом на фотографии нижней плоскости образца на рис. 16 видна только трещина, образовавшаяся после проведения 4 и 5 этапов эксперимента. Также хорошо заметна область проникновения масла из трещины в окружающий массив.
Рис. 16.
Фото верхней (слева) и нижней (справа) плоскостей образца после проведения этапов 4 и 5. Фото справа зеркально отражено относительно горизонтальной оси, чтобы совпадали контуры трещин в верней и нижней плоскостях.
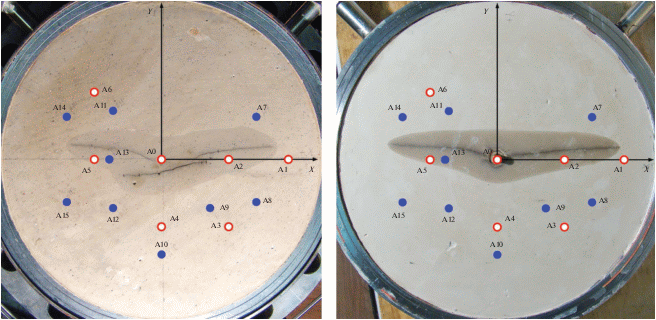
После того как образец был извлечен из экспериментальной установки, он был разделен по трещине на две части. Фото одной из частей образца приведено на рис. 17. В дальнейшем каждая часть образца также была разделена на две части, так что получилось четыре примерно равных сектора. На границах разломов можно проследить траектории распространения горизонтальной трещины ГРП в направлениях X и Y. Фотографии плоскостей разломов приведены на рис. 18.
Рис. 17.
Образец после проведения эксперимента 2, разделенный по трещине ГРП. Ориентация образца сохранена.
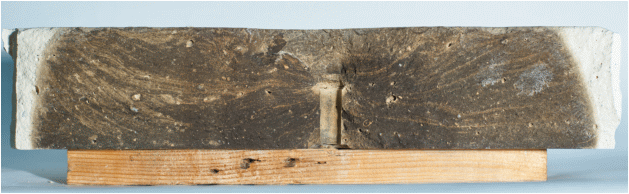
Рис. 18.
Разлом образца в плоскости Х, образованный вертикальной трещиной ГРП (слева), и в плоскости Y, образованный раскалыванием (справа). Эллипсами указана область, в которой расположена субгоризонтальная трещина первичного ГРП.
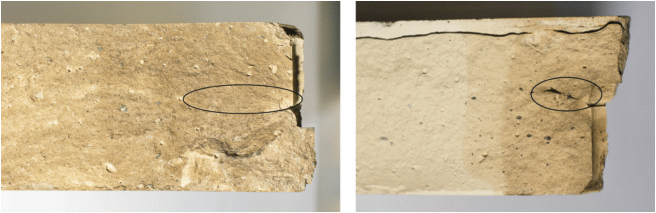
На каждом разломе можно обнаружить первичную субгоризонтальную трещину ГРП. В направлении Х ее полудлину можно оценить как 40–50 мм, в направлении Y ее полудлина составляет 18 мм. Для локации первичной трещины ГРП было проведено дополнительное ультразвуковое просвечивание всех четырех фрагментов образца и построены контуры равных амплитуд УЗ сигнала, которые изображены на рис. 19 с наложением на фото образца. Размеры области с уровнем сигнала 0.2, после которого начинается быстрый рост амплитуды, равны примерно 55 мм по оси Y и 140 мм по оси Х, что близко к измеренному размеру трещины по оси Y плюс диаметр центральной трубки с затравкой (15 мм), но заметно превышает видимый размер трещины в направлении оси Х. Если учесть параметры проведения эксперимента на этапе 3, то можно сделать вывод, что мог произойти поворот плоскости трещины, причем контраст напряжений в горизонтальной плоскости способствовал росту трещины в направлении оси Х.
ОБСУЖДЕНИЕ
Использование методов акустического просвечивания трещины гидроразрыва в лабораторных экспериментах позволило выявить важные особенности ее распространения. В эксперименте по образованию горизонтальной трещины гидроразрыва (перпендикулярной оси скважины) было подтверждено наличие сухого носика трещины и оценено среднее значение скорости фронта жидкости в трещине ГРП. Величина этой скорости (22–35 мм/с) сопоставима со средней скоростью распространения фронта жидкости, непосредственно измеренной в эксперименте по образованию горизонтальной трещины гидроразрыва в образце диаметром 110 мм, описанном в работе [Зенченко и др., 2019], и составившей 70 мм/с. Отклонение горизонтальной трещины ГРП в сторону свободной поверхности, обусловленное различием граничных условий на плоских поверхностях образца, является недостатком первого из описанных экспериментов, при том, что в пробном эксперименте, проведенном в цитируемой выше работе, где обе плоские поверхности цилиндрического образца были свободными, такого отклонения не наблюдалось. Изменение условий проведения экспериментов (добавление упругого слоя на нижней стороне образца) позволило получить горизонтальную трещину, не выходящую на поверхность.
Результаты выполненных экспериментов подтвердили данные работы [Stanchits et al., 2015] о том, что образование трещины гидроразрыва начинается раньше, чем давление в скважине достигнет максимума. По мере распространения трещины формируется ее сухой кончик, расход жидкости через трещину на этом этапе меньше, чем задаваемый поток жидкости закачки. По мере расширения трещины (что проявляется в снижении амплитуды проходящих импульсов УЗ) поток жидкости в трещину возрастает и начинает превышать расход закачки; это, вместе с упругим расширением жидкости, приводит к падению давления. Продвижение фронта жидкости в трещине проявляется в росте амплитуд импульсов УЗ, однако продолжающееся расширение трещины через некоторое время вновь приводит к снижению амплитуды проходящих импульсов. После остановки закачки трещина начинает смыкаться, что увеличивает амплитуду импульсов.
Проведенные эксперименты подтвердили возможность образования новой трещины, ориентированной вертикально (вдоль скважины), при наличии первоначальной горизонтальной трещины и проведении повторного ГРП в той же скважине. Вторичная трещина была создана только в результате изменения напряженного состояния модели коллектора. Следует отметить отсутствие каких-либо других специальных мер, таких как затравки, перфорация скважины, направленных на стимулирование образования новой трещины в заданном направлении (как это было сделано, например, в работе [Liu et al., 2008]).
Серия повторных экспериментов с увеличением компоненты напряжений, перпендикулярной плоскости первичной трещины, показала перераспределение потоков жидкости при образовании вторичной трещины, что проявилось в изменении вариаций амплитуд зондирующих УЗ импульсов.
ЗАКЛЮЧЕНИЕ И ВЫВОДЫ
Выполнена серия лабораторных экспериментов на пористых материалах по изучению закономерностей возникновения и распространения трещин гидроразрыва пласта с одновременной регистрацией изменений давления жидкости в нагнетательной скважине и амплитуд проходящих упругих волн. Найдено, что образование трещин ГРП можно разделить на этапы: возникновение сухой трещины, заполнение трещины жидкостью, раскрытие трещины, рост трещины с практически постоянной апертурой, закрытие трещины при прекращении закачки. Получено, что возникновение трещины происходит раньше, чем давление закачки достигает своего максимума. Использование метода ультразвукового просвечивания позволило экспериментально оценить скорости распространения трещины ГРП (100–130 мм/с) и продвижения фронта жидкости в ней (22–35 мм/с), сопоставимые с результатами непосредственных измерений этих величин в специальных экспериментах. Давление раскрытия и закрытия трещины в первом приближении линейно зависят от минимального главного напряжения. Изменение напряженно-деформированного состояния среды при повторном ГРП позволило получить вторичную трещину, ориентированную по направлению максимального горизонтального сжимающего напряжения и расположенную вдоль скважины при условии, что первичная трещина была расположена перпендикулярно скважине.
Список литературы
Зенченко Е.В., Зенченко П.Е., Лукина А.А., Турунтаев С.Б. Исследование динамики распространения и раскрытия трещин гидроразрыва в лабораторном эксперименте акустическими методами. Динамические процессы в геосферах. Выпуск 11. Сб. научных трудов ИДГ РАН. М.: Графитекс. 2019. С. 26–34. https://doi.org/10.26006/IDG.2019.11.38613
Зенченко Е.В., Тримонова М.А., Турунтаев С.Б. Лабораторное моделирование гидроразрыва пласта и сопутствующих процессов // Нефтяное хозяйство. 2019. Октябрь. С. 68–71. https://doi.org/10.24887/0028-2448-2019-10-68-71
Baykin A.N., Golovin S.V. Application of the Fully Coupled Planar 3D Poroelastic Hydraulic Fracturing Model to the Analysis of the Permeability Contrast Impact on Fracture Propagation // Rock Mechanics and Rock Engineering. 2018. V. 51. P. 3205–3217 https://doi.org/10.1007/s00603-018-1575-1
Berchenko I., Detournay E. Deviation of hydraulic fractures through poroelastic stress changes induced by injection and pumping // J. Rock Mechanics and Mining Sciences. 1997. V. 34. № 6. P. 1009–1019.
Borisov V.E., Zenchenko E.V., Kritsky B.V., Savenkov E.B., Trimonova M.A., Turuntaev S.B. Numerical simulation of laboratory experiments on the analysis of filtration flows in poroelastic media // Herald of the Bauman Moscow State Technical University, Series Natural Sciences. 2020. V. 88. P. 16–31. https://doi.org/10.18698/1812-3368-2020-1-16-31
Bunger A.P., Gordeliy E., Detournay E. Comparison between laboratory experiments and coupled simulations of saucer-shaped hydraulic fractures in homogeneous brittle-elastic solids // J. Mechanics and Physics of Solids. 2013. V. 61. P. 1636–1654.
De Pater C.J., Cleary M.P., Quinn T.S., Barr D.T., Johnson D.E., Weijers L. Experimental Verification of Dimensional Analysis for Hydraulic Fracturing // SPE Production & Facilities. 1994. November. P. 230–238. https://doi.org/10.2118/24994-PA
Economides M.J., Nolte K.G. Reservoir stimulations. N.Y.: Wiley. 2000. 750 p.
Gladkov I.O., Linkov A.M. Solution of Plane Hydrofracture Problem with Stress Contrast // J. Applied Mechanics and Technical Physics. 2018. V. 59. P. 341–351. https://doi.org/10.1134/S0021894418020189
Groenenboom J., van Dam D.B, de Pater C.J. Time-Lapse Ultrasonic Measurements of Laboratory Hydraulic-Fracture Growth: Tip Behavior and Width Profile // SPE J. 2001. March. P. 14–24.
Groenenboom J., Fokkema J.T. Monitoring the width of hydraulic fractures // Geophysics. 1998. V. 63. № 1. P. 139–140.
Hattori, G., Trevelyan, J., Augarde, C.E., Coombs W.M., Aplin A.C. Numerical Simulation of Fracking in Shale Rocks: Current State and Future Approaches // Arch. Computat. Methods Eng. 2017. V. 24. P. 281–317. https://doi.org/10.1007/s11831-016-9169-0
Liu H., Lan Z., Zhang G., Hou F., He X., Liu X. Evaluation of refracture reorientation in both laboratory and field scales // SPE. 2008. V.1. https://doi.org/10.2118/112445-MS
Smirnov V.B., Ponomarev A.V., Isaeva A.V., Bondarenko N.B., Patonin A.V., Kaznacheev P.A., Stroganova S.M., Potanina M.G., R Chadha K., Arora K. Fluid Initiation of Fracture in Dry and Water Saturated Rocks // Izv., Phys. Solid Earth. 2020. V. 56. № 6. P. 808–826.
Stanchits S., Surdi A., Edelman E., Suarez-Rivera R. Acoustic Emission and Ultrasonic Transmission Monitoring of Hydraulic Fracture Initiation and Growth in Rock Samples. 30th European Conference on Acoustic Emission Testing & 7th International Conference on Acoustic Emission. University of Granada. 12–15 September, 2012.
Stanchits S., Burghardt J., Surdi A. Hydraulic Fracturing of Heterogeneous Rock Monitored by Acoustic Emission // Rock Mechanics and Rock Engineering. 2015. V. 48. P. 2513–2527. https://doi.org/10.1007/s00603-015-0848-1
Trimonova M., Baryshnikov N., Zenchenko E., Zenchenko P., Turuntaev S. The Study of the Unstable Fracture Propagation in the Injection Well: Numerical and Laboratory Mode-ling // SPE-187822-MS. 2017. https://doi.org/10.2118/187822-MS
Turuntaev S.B., Zenchenko E.V., Zenchenko P.E., Triminova M.A., Baryshnikov N.A., Aigozhieva A.K. An influence of pore pressure gradient on hydraulic fracture propagation. In: 9th Australasian Congress on Applied Mechanics (ACAM9). Sydney: Engineers Australia. 2017. P. 712–723.
Zoback M., Rummel F., Jung R., Raleigh C. Laboratory hydraulic fracturing experiments in intact and pre-fractured rock // Int. J. Rock. Mech. Min. Sci. Geomech. Abstr. 1977. V. 14. P. 49–58.
Дополнительные материалы отсутствуют.