Геология рудных месторождений, 2023, T. 65, № 5, стр. 450-462
Минеральные ресурсы атомной отрасли России и изоляция радиоактивных отходов
В. А. Петров a, *, С. В. Юдинцев a, **
a Институт геологии рудных месторождений, петрографии, минералогии и геохимии РАН
119017 Москва, Старомонетный пер., 35, Россия
* E-mail: vlad243@igem.ru
** E-mail: yudintsevsv@gmail.com
Поступила в редакцию 30.05.2023
После доработки 05.06.2023
Принята к публикации 10.06.2023
- EDN: WCNXEV
- DOI: 10.31857/S0016777023050076
Аннотация
Рассмотрены задачи по обеспечению устойчивого развития атомной отрасли России, которые направлены на решение проблем начальных и завершающих стадий ядерного топливного цикла от воспроизводства минерально-сырьевой базы урана до обращения с жидкими высокоактивными отходами переработки отработавшего ядерного топлива. Проведен анализ тенденций развития минерально-сырьевого комплекса в связи с прогнозируемым ростом выработки электроэнергии на атомных станциях. На примере территории юго-восточного Забайкалья в рамках актуальных прогнозно-минерагенических исследований предложены новые подходы к выделению и обоснованию поисковых площадей на основе моделей минералообразующих систем урановых месторождений с использованием данных дистанционного зондирования Земли, ГИС-моделирования и нейросетевых технологий. Проведен детальный анализ тенденций в решении задач завершающих стадий ядерного топливного цикла. Для изоляции и последующего захоронения РЗЭ-актинидной фракции высокоактивных отходов предлагается использовать фосфатные стеклокерамики с монацитом.
ВВЕДЕНИЕ
В материалах МАГАТЭ отмечено, что “по мере того как вводятся в эксплуатацию новые АЭС, все больше стран рассматривает ядерную энергетику как возможное средство достижения целей в области борьбы с изменением климата и обеспечения энергетической безопасности. В условиях развивающегося глобального кризиса и на фоне восстановления мира после пандемии COVID-19 ядерная отрасль достигла второго за последнее десятилетие результата по годовому объему производства” (Energy…, 2022). Ядерный топливный цикл (ЯТЦ) включает добычу и обогащение урана, изготовление топлива и его использование в реакторах на АЭС, затем отработавшее ядерное топливо (ОЯТ) направляется на переработку, хранение или окончательное захоронение в геологических формациях. В ходе переработки до 95 мас. % ОЯТ может быть регенерировано и снова направлено на АЭС. Если рассматривать отдельные схемы ЯТЦ, то все они начинаются с добычи урана, а завершаются изоляцией радиоактивных отходов в геологических формациях.
Выдающийся советский и российский ученый и государственный деятель академик Н.П. Лаверов, чтения памяти которого прошли в Президиуме РАН 02.02.2023 года в преддверии Дня российской науки, внес неоценимый вклад в развитие атомной отрасли в России – от воспроизводства минерально-сырьевой базы (МСБ) урана до геологической изоляции отработавших ядерных материалов. Николай Павлович начал научно-организационную деятельность в ИГЕМ РАН, в 1958–1966 гг. он работал младшим научным сотрудником и ученым секретарем (фактически руководителем) на геологической станции Экспедиции №1 в поселке Табошар, Таджикистан. Круглогодичная станция имела филиалы практически на всех эксплуатируемых урановых месторождениях. Основное внимание Николая Павловича привлекли месторождения уран-молибденовой рудной формации в вулканотектонических структурах, в 1972 г. он защитил докторскую диссертацию “Геологические условия формирования урановых месторождений в областях континентального вулканизма (на примере Срединного Тянь-Шаня)” (Лаверов, 1972). Этот объемный труд остается источником идей о генезисе урановых месторождений в вулканотектонических структурах, условиях мобилизации и миграции рудных компонентов, и положении полей разгрузки продуктивных ураноносных гидротермальных растворов.
По производству атомной электроэнергии Россия занимает 4-е место в мире, а по доле атомной энергетики в общем объеме производства электроэнергии мы находимся на 16-ом месте (Energy…, 2022). Два года назад это было 18-е место. Сохранение этой тенденции требует разработки новых подходов к сочетанию методов и средств воспроизводства МСБ урана и обращения с отходами разного уровня радиоактивности в едином контексте функционирования и развития ЯТЦ России.
МИНЕРАЛЬНЫЕ РЕСУРСЫ АТОМНОЙ ОТРАСЛИ РОССИИ
В соответствии с докладом (Государственный…, 2022), который готовился под общим руководством ФГБУ “ВИМС”, балансовые запасы урана России на 01.01.2022 г. составляли 707.7 тыс. т (53 месторождения, на 8 объектах учтены и забалансовые запасы). По ряду ключевых показателей мы имеем одну из крупнейших минерально-сырьевых баз урана в мире (Бортников и др., 2021). Однако анализ распределения запасов урана по основным геолого-промышленным типам месторождений (фиг. 1) показывает, что из этого объема в работе находится около четверти. Те запасы, которые находятся в резерве, либо имеют высокую себестоимость добычи, например, Эльконские месторождения Алдана (130–260 долларов за кг), либо уран является попутным элементом в комплексных редкоземельных рудах (месторождения Улуг-Танзегское, Катугинское, Степное, Шаргадыкское и др.).
Фиг. 1.
Распределение запасов урана по основным геолого-промышленным типам, в тыс. тонн (Машковцев и др., 2021).
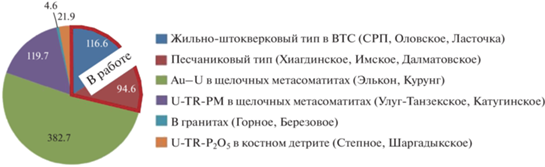
Если рассматривать проблему воспроизводства МСБ урана через прогноз мировой выработки электроэнергии (Energy…, 2022) на атомных станциях по сценариям МАГАТЭ (от 6.9% до 14% к 2050 г.), то увидим следующее. Во-первых, в мире из примерно 56 тыс. т добываемого в год урана около 65% приходится на страны, тяготеющие в своем политико-экономическом развитии к России, а около 35% на страны, которые ориентируются на США. Во-вторых, по имеющимся оценкам (Бойцов, 2021; Тарханов, Бугриева, 2021; Uranium…, 2023), в период 2010–2020 гг. потребность в природном уране покрывалась добычей, с 2020 г. наметился дефицит уран-добывающих мощностей, и к 2025 году прогнозируется снижение добычи урана и появление дефицита мощностей из-за вывода из эксплуатации рудников в связи с истощением запасов. Тенденция к увеличению выработки электроэнергии на АЭС сохранится даже в случае широкой имплементации технологий “зеленой энергетики”.
Каким образом специалисты урановой геологии могут реагировать на эти тенденции? Например, с помощью определения рудовмещающих комплексов и ураноносных структур методами ГИС-моделирования с использованием минерально-системного подхода. В его основе лежит парадигма “источник рудоносных флюидов–пути перемещения–физико-химические обстановки рудоотложения в структурных ловушках” (Wyborn et al., 1994; Skirrow et al., 2009). Примером совмещения в пространстве и во времени минеральных систем, связанных с гранитами и вулканитами, служат месторождения Стрельцовского рудного поля в Забайкалье (Андреева и др., 2020; Пэк и др., 2020; Петров и др., 2022).
Расчетные и полученные in situ данные показывают, что активные и проницаемые для флюидов разломы имеют определенную ориентировку в поле действующих напряжений и деформаций (Jaeger, Cook, 1979; Fuchs, Müller, 2001; Zoback et al., 2002). Нами предложено применять алгоритм, включающий: выделение разломно-трещинных структур, проницаемых для рудоносных растворов в период рудообразования; установление мультиспектральных характеристик предрудных, рудосопровождающих и пострудных метасоматитов по данным дистанционного зондирования Земли (ДЗЗ, спутники LANSAT-8 и WorlView-2); приложение нейросетевых технологий для анализа ключевых факторов уранового рудогенеза. Использование этого подхода показано на примере юго-восточного Забайкалья (фиг. 2), где имеется крупнейший в стране комплекс по добыче и переработке урана – ПАО “Приаргунское производственное горно-химическое объединение”, а также другие предприятия по добыче руд стратегических металлов.
Фиг. 2.
Прогнозная схема распределения комплексов и структур, перспективных на гидротермальную рудную минерализацию в юго-восточном Забайкалье, созданная на основе обработки и интерпретации спектральных характеристик оптических данных ДЗЗ (аппарат Landsat-8) в сочетании с ГИС-проектированием, геолого-геофизическим и металлогеническим моделированием с использованием алгоритмов нечеткой логики (Nafigin et al., 2022).
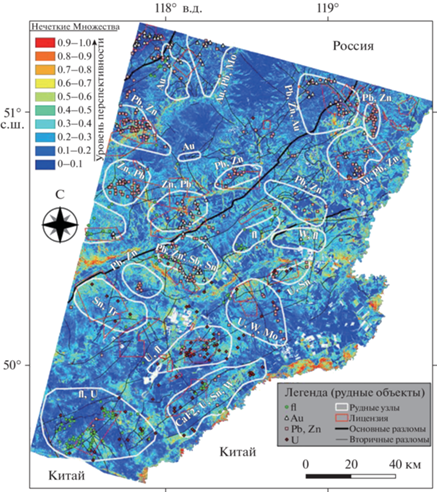
Необходимо также учитывать, что вне зависимости от способа добычи (карьер, шахта, подземное выщелачивание), срок от открытия месторождений до начала освоения неуклонно растет. Если в 1950–1960-х гг. он составлял 5–10 лет, то сейчас уже 20–40 лет. Поэтому для ликвидации дефицита уранодобывающих мощностей потребуется все больше времени и ресурсов, а также внедрение новых технологий поисков, оценки и разведки глубокозалегающих “скрытых” рудных тел (Машковцев, Петров, 2023). Наметившиеся в настоящее время изменения в алгоритме обоснования поисково-разведочных работ на уран от описательной структурно-формационной классификации МАГАТЭ на основе 15 типов, 37 подтипов и 14 классов урановых месторождений (Geological…, 2018), к геолого-генетическим моделям месторождений (моделям урановых минеральных систем) с акцентом на состав и свойства рудоносных флюидов (Descriptive…, 2020) открывают важную новую страницу в урановой геологии и создают хорошие перспективы при поисках и разведке минеральных ресурсов для устойчивого развития ядерной энергетики России.
ИЗОЛЯЦИЯ РАДИОАКТИВНЫХ ОТХОДОВ
К 2021 г. в 31 стране мира имелось 442 действующих ядерных реактора и еще 52 находились в стадии строительства. Для их работы необходимо около 8000 т топлива в год, что соответствует 60 000 т природного урана (Uranium…, 2023). Подавляющая часть блоков относится к реакторам на медленных (тепловых) нейтронах – ВВЭР, РБМК, PWR, BWR и др., где используется оксидное урановое топливо, содержащее до 4 мас. % 235U. Тепловая, а значит и электрическая, энергия, вырабатываемая реактором, примерно на 2/3 обусловлена делением 235U и на 1/3 – делением 239Pu, образующегося при захвате нейтронов ядрами 238U. Поэтому лишь небольшая часть (менее 1%) энергетического потенциала природного урана реализуется в текущем ядерном топливном цикле. Оставшиеся после изготовления топлива миллионы тонн обедненного урана, содержащие до 0.2 мас. % 235U, хранятся в виде летучего выше 50°С гексафторида (UF6) и полученного в результате его конверсии диоксида урана.
Добыча урана в мире в 2020–2021 годах составляла 47 000 т, остальное получали из складских запасов и от переработки отработавшего топлива, ОЯТ. К 2040 г. потребность АЭС в природном уране оценивается в 60–110 тыс. т (Uranium…, 2023). Существенное увеличение ресурсов ядерной энергетики связано с переходом к двухкомпонентной системе с реакторами на медленных (тепловых) и быстрых нейтронах и замкнутым топливным циклом, то есть с переработкой ОЯТ. Это позволит использовать для выработки электроэнергии не только 235U и 239Pu, но также и 238U, с долей 99.3% в природной смеси изотопов.
Из реакторов гражданской ядерной энергетики с 1954 по 2016 год выгружено около 390 000 т ОЯТ, а треть его уже переработана (Status…, 2022). В настоящее время, с учетом объемов наработки, масса ОЯТ в мире приближается к 300 000 т, в России хранится почти 25 000 т ОЯТ реакторов ВВЭР и РБМК (Шестой…, 2020). Переработка ОЯТ ведет к появлению больших объемов радиоактивных отходов (РАО), включая высокоактивные (ВАО), которые содержат долгоживущие продукты деления (79Se, 99Tc, 129I, 135Cs), актиниды (Np, Am, Cm) и др. Объем твердых ВАО в 2016 г. оценивался как 29 000 м3 (Status…, 2022) или около 70 000 т (не считая ОЯТ). Проблемой обращения с ВАО в мире занимаются более 70 лет, их предлагается включать в устойчивые стеклообразные или минералоподобные матрицы для захоронения. В нашей стране эта работа началась позже, ее активизация связана с созданием нового направления “радиогеоэкология”, инициированного академиком Н.П. Лаверовым. В статье (Лаверов и др., 1991) отмечено, что захоронение РАО в геологические формации – это крупная междисциплинарная проблема. Основная задача радиогеоэкологии определена как обоснование безопасного захоронения таких отходов в геологической среде. Она решается созданием мультибарьерной системы, и первым из таких барьеров является консервирующая матрица отходов. Главные результаты первых двадцати лет изучения этой проблемы в ИГЕМ РАН обобщены в работе (Лаверов и др., 2008), которая до сих пор сохраняет актуальность.
История и современное состояние обращения с высокоактивными отходами в России
Проблема изоляции отходов ядерной энергетики уже почти 70 лет находится в центре внимания специалистов многих стран. Такие отходы в больших объемах возникают в ходе переработки ОЯТ при извлечении U и Pu для последующего использования (Глаголенко и др., 1997; Копырин и др., 2006; Лаверов и др., 2008). В мире промышленная иммобилизация ВАО в B–Si стекла ведется с 1978 г. (Donald, 2010; Jantzen, 2011), в России для этого с 1987 г. применяется Na–Al–P стекломатрица (Поляков и др., 1994; Глаголенко и др., 1997; Ремизов и др., 2018; Богатов и др., 2021). В мире имеется 35 000–40 000 т высокоактивного стекла при массовом соотношении количеств B–Si и Al–P стекломатриц, равном 4 : 1. Остеклованные ВАО (отходы 1-го и 2-го классов по Российской классификации) планируется размещать в кристаллических породах на глубинах 0.5–1 км в глубоком шахтном хранилище (ПГЗРО). В нашей стране реализуется проект “Енисейский” в Красноярском крае, нацеленный на сооружение ПГЗРО в гранитогнейсах (Laverov et al., 2016).
При регенерации ОЯТ происходит перераспределение радионуклидов относительно состава ОЯТ (Копырин и др., 2006; Богатов и др., 2021). В первом цикле экстракционной переработки из ВАО извлекается 99.9% U, 99.5% Pu и 98% Np (Глаголенко и др., 1997). Остекловывание жидких ВАО ведется на ПО “Маяк” в одну стадию в керамических печах ЭП-500 (Поляков и др., 1994; Вашман и др., 1997; Полуэктов и др., 2005; Ремизов и др., 2018). Температура варки Na–Al–P стекла 910–1135°С, его состав лежит в пределах, мас. %: 23–26 Na2O, 14–19 Аl2O3, 52–54 Р2O5. Доля отходов в матрице, с учетом Аl2O3, равна 21–26 мас. %, а на продукты деления и актиниды приходится 3–5 мас. %. Начиная с 1987 года на ПО “Маяк” работали 5 печей, на 4-х первых установках получено 6200 т остеклованных ВАО с активностью 640 млн Ки. Печь ЭП-500/5 производительностью до 800 т стекла/год запущена в декабре 2016 г., после окончания ее эксплуатации для остекловывания отходов будут применяться малогабаритные демонтируемые плавители (Баторшин и др., 2013).
К настоящему времени в печи ЭП-500-5 получено 1600 т стекла (Богатов и др., 2021), а общая масса остеклованных отходов, хранящихся на ПО “Маяк”, приближается к 8000 т. Отверждение 15 тыс. м3 жидких ВАО и шламов добавит еще 5000–6000 т высокоактивного стекла (Баторшин и др., 2013, 2015). Для этого предполагается использовать индукционный плавитель с “холодным” тиглем, ИПХТ (Баторшин и др., 2015). В итоге общее количество стекла приблизится к 14 000 т, что на 30% превысит проектную вместимость будущего подземного хранилища “Енисейский” (Laverov et al., 2016).
Из-за ограничений по радиационному разогреву и термостойкости стекломатрицы ВАО на 1 т ОЯТ образуется 1.2–1.8 т стекла (Власова и др., 2017; Ремизов и др., 2018), что в 4–5 раз выше значений, чем при использовании B–Si матрицы, содержащей 18–20 мас. % ВАО. Недостаток технологии заключается в малом ресурсе работы печей ЭП-500 (3–5 лет). При больших габаритах (9.5 × 4 × 3 м) производительность печи всего 85 кг стекла/час. После вывода из эксплуатации ее демонтаж представляет очень сложную задачу, так как в печи остается высокоактивное стекло. Проблемы, связанные с остекловыванием жидких ВАО, и пути их решения, отражены во многих статьях (Глаголенко и др., 1997; Баторшин и др., 2013, 2015; Ремизов и др., 2018).
Особенность Na–Al–P-стекол – их низкая термостойкость, что ограничивает содержание в матрице теплогенерирующих компонентов ВАО (90Sr, 137Cs). Фазы AlPO4 и Na3Al2(PO4)3 образуются из расплава при остывании со скоростью менее 30°С в час (Вашман и др., 1997). Нагрев при 500°С неактивного стекла вызвал его частичную кристаллизацию с образованием фаз Na3(Al,Fe)2(PO4)3 и фосфата РЗЭ. После выдержки 150 ч при 450°С в стекле найдены Na3Al2(PO4)3, Na3PO4, AlPO4, NaPO3, (Fe,Cr)2O3. Центры их кристаллизации – металлические и оксидные фазы низкорастворимых элементов ВАО (Ru, Rh, Pd, Fe, Cr и Ni).
После кристаллизации стекла скорость выщелачивания элементов вырастет в десятки и сотни раз (Вашман и др., 1997; Юдинцев и др., 2020). На поведение РЗЭ это не оказывает заметного влияния из-за их вхождения в монацит. В документах (ГОСТ Р 50926-96; НП-093-14; НП-019-15) определены требования к остеклованным отходам, однако стекло неизбежно раскристаллизуется со временем, чему способствует его нагрев из-за распада радионуклидов.
Перспективные направления в области обращения с высокоактивными отходами
Сооружение современного высокопроизводительного комплекса переработки ОЯТ и отверждения ВАО – ключевое условие перехода к двухкомпонентной ядерной энергетике, функционирующей в режиме замкнутого топливного цикла. Его задача – сокращение объема высокоактивных отходов, подлежащих глубинному захоронению. Прогресс в решении этой проблемы связан с сепарацией ВАО на группы сходных по свойствам элементов. Одна из таких групп представлена фракцией трехвалентных редких земель (РЗЭ) и малых актинидов (МА – Am, Cm). Редкие земли представлены, в основном, стабильными изотопами, актиниды определяют долгосрочную опасность и вносят существенный вклад в тепловыделение ВАО. Приемы выделения РЗЭ – МА фракции испытаны на реальных жидких отходах переработки ОЯТ и уже готовы к практическому использованию (Копырин и др., 2006; Юдинцев, 2021).
На единственной в мире промышленной установке фракционирования жидких ВАО на ПО “Маяк” с 1996 по 2003 год переработано 1620 м3 жидких ВАО с активностью 55 млн Кюри. Нуклиды 90Sr и 137Cs извлекали хлорированным дикарболлидом кобальта и включали в стекло, РЗЭ и трансплутониевые элементы (ТПЭ) осаждали в виде оксалатов (Копырин и др., 2006; Логунов и др., 2013). Стоимость переработки ВАО выросла на 5%, издержки на остекловывание снизились на 60%. Для иммобилизации концентрата РЗЭ – ТПЭ предложен монацит (Rovnyi et al., 2004) с высокой стойкостью при выщелачивании. После выделения 90Sr и 137Cs на ПО “Маяк” образовалось 117 м3 раствора состава (г/л): Nd – 0.5, Sm – 0.3, La – 0.2, Pr – 0.15, Gd – 0.03, Y – 0.05, U – 0.5, Pu – 0.005, Al – 5.0, Fe – 2.5, Si – 2.0, Mn – 0.7, Cr – 0.5, Ni – 0.4, Ca – 0.2, Mg – 0.1, ТПЭ представлены 241Am и 244Cm. Добавлением к раствору щавелевой кислоты осаждались оксалаты РЗЭ и ТПЭ с удалением до 90% Ce и La, 95% Pr, Pm, Nd и Sm, 98% Y, Gd, Ee, Am и Cm, 88% Pu. Осадок переводили в порошок ортофосфата РЗЭ и спекали с получением монацитовой керамики. Монацит, как матрица актинидов, изучен в большом числе публикаций (Boatner, 2002; Омельяненко и др., 2007; Dacheux et al., 2013). Его образование при кристаллизации фосфатных стекол с РЗЭ позволяет использовать для изоляции отходов РЗЭ–МА фракции монацитовые стеклокерамики.
Образование монацита в алюмофосфатном стекле с имитаторами ВАО (РЗЭ, U)
Образцы получены плавлением двух оксидно-фосфатных смесей в алундовых тиглях в электропечи при 1000°С (далее АФ-1) или 1200°С (АФ-2). Расчетный состав образца АФ-1: 21.0% Na2O, 17.0% Al2O3, 50.0% P2O5, 10.0% Ln2O3 (Ln = La + + Ce + Nd), 5.0% продукты деления (MoO3, ZrO2, BaO) и коррозии (Cr2O3, Fe2O3, NiO, MnO); образца АФ-2: 17.0% Na2O, 15.0% Al2O3, 6.0% Fe2O3, 50.0% P2O5, 1.0% NiO, 3.0% Cs2O, 2.0% SrO, 5.0% Ln2O3 (Ln = Ce + Nd) и 3.0% UO2. Имитаторами элементов ВАО служили Cs, Sr, Ce, Nd, Ni, Мо, а также U. Затем стекла нагревали 4 ч на воздухе при 500°С (АФ-1) или сутки при 300°С на воздухе либо в автоклаве в парах воды с влажностью 70% (АФ-2). Образцы изучали рентгенофазовым анализом (РФА), в оптическом и сканирующем электронном микроскопах (СЭМ/ЭДС). Образец АФ-1 сложен стеклом и фосфатом РЗЭ, монацитом (фиг. 3), который образуется из-за превышения содержания РЗЭ над растворимостью в расплаве, оцениваемой в 2–3 мас. % (Вашман и др., 1997; Матюнин, 2000). Зерна монацита имеют размеры до 20 микрон и часто образуют сростки. Фракционирование РЗЭ резко смещено в пользу монацита (табл. 1), коэффициент распределения, Кр = Срзэ монацит/Срзэ стекло, составляет 30. Нагрев 4 ч при 500°С ведет к появлению фаз алюмофосфатов вокруг кристаллов монацита, которые служат центрами кристаллизации (фиг. 3а–б). В составе этих сферолитов РЗЭ отсутствуют.
Фиг. 3.
Стекло АФ-1 после нагрева 4 ч при 500°С: фотографии в оптическом микроскопе, николи скрещены, увеличение в 60 (а) и 200 (б) раз (стекло – темное, сферолиты Na–Al–P фаз – светлое, монацит – желтое). СЭМ-изображение (в, г) сферолитов фосфатов (темно-серое) вокруг кристаллов монацита (белое) в остаточном стекле (светло-серое). Черное – поры.

Таблица 1.
Составы (мас. %) стекла (1), монацита (2) и сферолитов (3) в образце АФ-1
Фаза | Na2O | Al2O3 | P2O5 | MeО2 – х | SrO | ZrO2 | MoO3 | Cs2O | BaO | Ln2O3 |
---|---|---|---|---|---|---|---|---|---|---|
1 | 24.0 | 17.2 | 47.8 | 0.8 | 0.8 | 2.9 | 1.4 | 0.9 | 0.8 | 2.4 |
2 | <по | <по | 27.9 | <по | 0.5 | <по | <по | 0.6 | 0.3 | 72.1 |
3 | 25.5 | 19.1 | 51.3 | 1.4 | <по | <по | 0.4 | 0.5 | 0.6 | 0.6 |
Стекло АФ-2 однородно (табл. 2), суточный нагрев при 300°С в “сухих” условиях не привел к каким-либо его изменениям. Для ускорения кристаллизации стекло обработали в автоклаве нагретым паром с влажностью 70%. Жидкая фаза в опыте отсутствует, а поэтому состав образца не меняется, а происходит кристаллизация стекла с образованием монацита и двух Na–Al–Fe фосфатов несколько различного состава (фиг. 4, табл. 2). Монацит образует сферические выделения диаметром от 1–2 до 20 микрон, в нем имеются высокие количества Sr и U (табл. 2). Вхождение урана происходит по реакции 2РЗЭ3+ = Sr2+ + U4+. Для монацита типичны обмены с участием двух- и четырехвалентных катионов, такая разность монацита с высоким содержанием двух- и четырехзарядных катионов известна как минерал чералит.
Таблица 2.
Составы исходного стекла AФ-2 и фаз, образованных после его обработки паром
Фаза | Na2O | Al2O3 | P2O5 | Fe2O3 | NiO | SrO | Cs2O | Ce2O3 | Nd2O3 | UO2 |
---|---|---|---|---|---|---|---|---|---|---|
Стекло1 | 17.4 | 14.4 | 50.4 | 5.5 | 1.1 | 2.0 | 2.5 | 2.3 | 1.9 | 2.5 |
Фосфат-1 | 22.9 | 19.2 | 53.1 | 4.8 | н.о. | н.о. | н.о. | н.о. | н.о. | н.о. |
Фосфат-2 | 14.2 | 14.4 | 50.4 | 10.1 | 7.0 | 2.8 | 1.1 | н.о. | н.о. | н.о. |
Монацит | н.о.2 | 2.03 | 32.1 | н.о. | н.о. | 11.5 | н.о. | 20.6 | 17.9 | 15.9 |
О фосфатных стеклах с РЗЭ и монацитовых стеклокерамиках
Изучалась растворимость РЗЭ (Матюнин, 2000; Stefanovsky et al., 2019a, 2019b; Frolova et al., 2022) и актинидов (Вашман и др., 1997; Данилов и др., 2018) в Na–Al–Fe–P–расплавах. Так как кристаллохимическим аналогом трехвалентных актинидов (Am, Cm) и РЗЭ–МА фракции в целом служат легкие РЗЭ (Юдинцев, 2021), то наибольший интерес представляют данные о поведении La, Nd, Sm. Их растворимость в алюмо-(железо)-фосфатном расплаве при 1000°С составляет, в мас. %: 1.5–1.7 (La2O3), 2.5–2.6 (Nd2O3) или 3.7–3.8 (Sm2O3) (Матюнин, 2000).
В работах (Данилов и др., 2018; Стефановский и др., 2018; Stefanovsky et al., 2017, 2018, 2019a, 2019b) исследованы алюмофосфатное (SAP) и алюмо-железофосфатное (SAIP) стекла с РЗЭ и актинидами (U, Np, Pu, Am). Их составы (мол. %/мас. %): 40/24.3 Na2O, 20/20.0 Al2O3, 40/55.7 P2O5 (SAP); 40/23.0 Na2O, 10/9.5 Al2O3, 10/14.8 Fe2O3, 40/52.7 P2O5 (SAIP). Содержание РЗЭ менялось от 1 до 20 мас. %, актинидов – от долей процента (Np, Pu, Am) до 50% (U). Стекла получали плавлением в течение 0.5–6 ч при 1000–1300°С и сливом на плиту для закалки либо охлаждением по режиму, аналогичному остыванию блока в 200-литровом контейнере на ПО “Маяк”. При содержании в стекле до 5 мас. % РЗЭ монацит не образуется. При медленном охлаждении в стекле образуются фосфаты Na, Al (или Fe–Al) и РЗЭ (монацита), скорость выщелачивания элементов возрастает в 5–10 раз и составляет 10–6 г/(см2 сут) (Stefanovsky et al., 2017). РЗЭ-имитаторы актинидов при кристаллизации концентрируются в монаците, коэффициент их распределения между монацитом и стеклом составляет 45–70. Определены (Стефановский и др., 2018) фазовый состав стекломатриц с РЗЭ (La, Ce, Eu, Gd), их структура и устойчивость в воде. Введение в стекла до 5 мас. % оксидов лантанидов (Ln) не вызывает кристаллизации фаз при закалке (кроме La-содержащего стекла) и не оказывает заметного влияния на их структуру и гидролитическую устойчивость. После медленного отжига стекла SAP кристаллизуются с выделением Al–P, Na–Al–P, Ln–P (монацит) и Na–Ln–P фаз, в случае Gd – еще и оксида Gd2O3. Плавлением от 1 до 6 ч при 1000 или 1200°C получены алюмо-фосфатное (SAP) и алюмо-железо-фосфатное (SAIP) стекла с 9 мас. % оксидов РЗЭ. Часть расплава закаливали, остальной объем остывал в печи. Закаленные стекла гомогенны, остывавшие в печи, кроме стекла, содержат фосфаты Al, Na–Al и РЗЭ (монацит). Изучение устойчивости образцов (вода, фракция 0.071–0.125 мм, 90°С, 7 суток) выявило увеличение скорости выщелачивания из частично закристаллизованных стекол в 5–10 раз по сравнению с закаленным. Включение 9 мас. % РЗЭ не ухудшает устойчивость в воде закаленных стекол в отношении Na, Al и P. Для отожженных стекол скорости выщелачивания растут в 2–40 раз, что обусловлено образованием фосфатов и алюмо-фосфатов натрия. Выщелачивание РЗЭ остается на низком уровне из-за образования монацита. В случае кристаллизации стекла он будет удерживать РЗЭ и не допустит ухудшения свойств матрицы при хранении. Скорости выщелачивания на 30-е сутки равны, г/(см2 сут): 3.5 × 10–8, 3.4 × 10–9 и 6.3 × 10–9 для Np, Pu и Am соответственно, что ниже нормативных значений – не более 10–7 г/(см2 сут) для 239Pu. Более высокие скорости выщелачивания Np, чем Pu и Am связаны, вероятно, с его присутствием, по крайней мере частично, в виде иона ${\text{NpO}}_{2}^{ + }$ (Данилов и др., 2018).
Согласно (Stefanovsky et al., 2019b), стекла SAP (Тпл. = 1000°C) и SAIP (Тпл. = 1200°C) с 10 мас. % РЗЭ не содержат кристаллических фаз, и только в образце с La имеются следы монацита (LaPO4). При обжиге не содержащее РЗЭ стекло SAP частично кристаллизуется с выделением AlPO4 и β-Na6Al3(P2O7)3. В стекле с La2O3 главные фазы – AlPO4 и монацит. В образце с Се2О3 кристаллических фаз, кроме AlPO4, не обнаружено. Введение CeO2 приводит к появлению церианита, монацита и Na3Al2(PO4)3. В отожженных образцах с оксидами Pr и Nd содержатся AlPO4, монацит и следы Na3Al2(PO4)3. В образцах с Sm, Eu, Gd обнаружен ортофосфат Na3РЗЭ(PO4)2. Введение до ~10 мас. % оксидов РЗЭ в стекла не влияет на выщелачивание Na, Al, Fe, P. Скорости выщелачивания РЗЭ равны 10–7–10–6 г/(см2 сут). Закаленные стекла SAIP менее растворимы, чем SAP, отожженные образцы более устойчивы, чем закаленные за счет включения РЗЭ в монацит. После отжига выход Na и P из стекла SAP увеличивается в 2–15 раз, скорости выщелачивания Al, Fe и РЗЭ не меняются.
Стеклокерамика, содержащая до 20 мас. % оксидов (РЗЭ), получена путем плавки при 1250°С и последующей закалкой или медленным охлаждением до комнатной температуры (Stefanovsky et al., 2018). Безжелезистая стеклокерамика сложена стеклом и небольшим количеством AlPO4 и монацита. Железосодержащая стеклокерамика при низком содержании РЗЭ (5–10 маc. %) состояла из стекла, небольших количеств монацита и фосфата Na–Al–Fe, при высоком (15–20 мас. %) – из ортофосфата Na–Al–Fe, монацита и стекла. Медленно охлажденные образцы содержат больше фаз, чем закаленные. Скорости выщелачивания Na, Al, Fe и P составляют 10−5 –10−7 г см−2 сут−1, для РЗЭ их величины меньше 10−5 г см−2 сут−1.
Свойства Na–Al–(Fe)–P стекол с 10 мас. % смеси оксидов состава (La0.57Ce0.36Nd0.93)О3 изучены в статье (Frolova et al., 2022). Образцы готовили плавлением 1 ч при 1200°С и быстрой закалкой. В них имеется монацит, растворимость РЗЭ в стеклах в пределах точности анализа одинакова, мас. %: 0.8–0.9 La2O3, 0.7–0.8 CeO2, 1.9–2.0 Nd2O3, в сумме 3.5 мас. %. Основная часть РЗЭ находится в монаците, который образует зерна размером до 10 микрон. Значения Кр между монацитом и стеклом равны: 17–20 (Ce), 17–21 (La) и 13–17 (Nd).
При обращении с ВАО важное значение имеет технология иммобилизации в матрицу. Существуют ограничения при использовании керамических печей для отверждения ВАО. Этих недостатков лишена технология высокочастотной индукционной плавки в холодном тигле (ИПХТ) при нагреве электромагнитным полем от высокочастотного генератора. Ее достоинства: отсутствие электродов, огнеупоров и контакта расплава со стенками тигля из-за не расплавившегося слоя шихты, а перемешивание расплава вихревыми токами позволяет достичь высоких температур, удельной производительности и качества конечного продукта. Поэтому ИПХТ является эффективным приемом получения стекол, керамик и стеклокерамик для изоляции ВАО, в том числе с монацитом. Работы по ИПХТ ведутся во Франции, в России, США, Великобритании, Южной Корее, Индии. Подходы различаются выбором рабочих частот, размером и возможностью опорожнения тигля и рядом других особенностей. Французский вариант предусматривает низкие частоты (200–300 кГц) и тигли диаметром до 1 м, в российском – частота составляет 1760 кГц при диаметре тигля до 0.5 м. На заводе во Франции с 2011 года для остекловывания ВАО используется тигель диаметром 650 мм, генератор с частотой 200 кГц и мощностью 600 кВт. ИПХТ считается перспективной технологией для синтеза матриц отходов высокого и среднего (САО) уровня активности, в том числе актинидной фракции (Vlasov et al., 1987; Kushnikov et al., 1997; Smelova et al., 1997; Sobolev et al., 1997; Demine et al., 2001), САО от работы АЭС, очистки урана и др. Пионером изготовления матриц методом ИПХТ в нашей стране был В.И. Власов (ВНИИНМ, МосНПО “Радон”). ИПХТ используется во ФГУП “Радон” для остекловывания жидких САО на установке с частотой 1760 кГц и мощностью 160 кВт. При загрузке шихты в виде пасты с влажностью 22 мас. % производительность по стеклу равна 25 кг/ч. С 1998 г. переработано 15000 м3 жидких САО, получено 50 т стекла. ИПХТ активно развивается в Госкорпорации Росатом (ВНИИНМ, ВНИИХТ, Радиевый Институт, ПО “Маяк”) Российской академии наук (ИФХЭ), Санкт-Петербургском государственном электротехническом университете (ЛЭТИ). Использование ИПХТ позволяет увеличить температуру расплава с 1000°С до 1200–1300°С и растворимость РЗЭ в нем. Конвективное перемешивание расплава препятствует осаждению из расплава кристаллических фаз (монацита) и нарушению однородности матрицы. Поэтому содержание фракции РЗЭ-актинидов может быть выше растворимости элементов в расплаве и достигать 10–20 мас. % (Kushnikov et al., 1997). Результаты исследований показали перспективность использования ИПХТ для остекловывания жидких и твердых отходов с высокой производительностью и надежностью (Лопух и др., 2022). Методом ИПХТ получены стекла, керамики на основе пирохлора и муратаита, стеклокерамики с фазами цирконолита, граната или бритолита, содержащие имитаторы РЗЭ-актинидной и актинидной фракций ВАО (Смелова и др., 2000; Лаверов и др., 2011, 2013; Юдинцев и др., 2015; Стефановский, Юдинцев, 2016; Stefanovsky et al., 2016, 2019; Юдинцев и др., 2021). Во ВНИИНМ создан малогабаритный плавитель с холодным тиглем с рабочей температурой в 1500°С, достаточной для синтеза различных типов матриц, в том числе на фосфатной основе с монацитом. С 2003 года работает установка с тиглем диаметром 380 мм, высотой 800 мм и с производительностью 25 кг матрицы в час. В ней учтены требования по дистанционным условиям эксплуатации, замене и ремонту оборудования, а также демонтажу установки.
Иммобилизация ВАО, совмещающая получение гранулированного прекурсора и его плавку в ИПХТ с образованием компактной формы, рассмотрена в работе (Мельникова и др., 2023). Этот метод позволяет снизить уносы, уменьшить коррозионное воздействие из-за образования гарнисажа, повысить эффективность получения матрицы. Прекурсор получали на демонстрационном грануляторе (фиг. 5а), в который загружалась смесь, отвечающая составу матрицы. Затем на поверхность подавался имитатор жидких ВАО с формированием окатышей. Их размер и прочность зависели от состава матричной смеси и температуры, задаваемой в пределах 200–270°С. Скорость вращения борта тарели 1.54 м/с, угол наклона к вертикали 40°. Гранулят (фиг. 5б, в) порциями загружали в тигель (фиг. 5г, д), после гомогенизации расплава установку отключали и происходила кристаллизация матрицы (фиг. 5е, ж). Плавлением гранулированной шихты в ИПХТ при 1600оС получены 2 образца массой каждый 2 кг. Параметры изготовления образцов выбраны максимально близкими к реальным технологическим условиям, что обеспечивает их соответствие промышленному продукту.
Фиг. 5.
Установка для грануляции (а); гранулы шихты (б, в); “холодный” тигель (г) и вся установка ИПХТ (д); подготовленные для изучения образцы керамических матриц (е, ж).
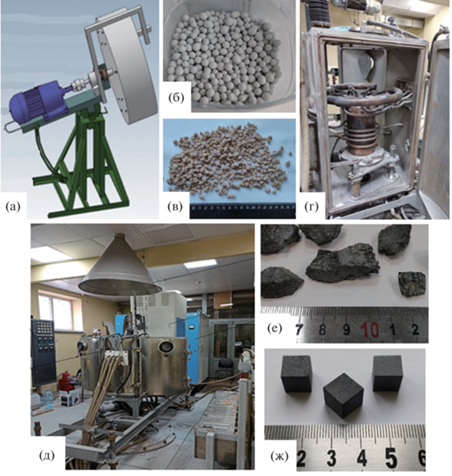
Реализация стратегии многократной переработки ОЯТ, извлечения Pu, Np, Am и Cm для трансмутации потребует строительства и эксплуатации крупных заводов по переработке ОЯТ, для фракционирвания ВАО, дистанционного изготовления топлива и реакторов для трансмутации. Для использования ресурсов урана и сокращения опасности малых актинидов необходимы сооружение и эксплуатация ряда сложных и дорогих технологий (реакторы, установки по переработке и изготовлению топлива). Быстрое внедрение такой программы в настоящее время маловероятно, поскольку это требует огромных затрат и решения ряда технологических проблем. Она представляет интерес на горизонте в столетие (Merits…, 2023), тогда как с учетом готовности имеющихся технологий задачи выделения РЗЭ-МА фракции и ее иммобилизации в матрицу можно осуществить в короткие сроки (до 10 лет).
ЗАКЛЮЧЕНИЕ
Расширение минерально-сырьевой базы урана требует новых подходов к совершенствованию прогнозно-поискового комплекса, особенно в связи с исчерпанием легко открываемых приповерхностных объектов и необходимостью направления геологоразведочных работ на выявление скрытых, слепых месторождений, а также с оценкой минерально-сырьевого потенциала территорий Дальнего Востока и Арктического региона с весьма сложными ландшафтно-геоморфологическими и климатическими условиями. Для выделения и обоснования поисковых площадей требуются разномасштабные прогнозно-минерагенические исследования, которые направлены на выявление определенного геолого-промышленного типа месторождений (Машковцев, Петров, 2023). Эти исследования целесообразно проводить с использованием минерально-системного подхода, который ориентирован на создание генетических моделей месторождений (моделей урановых минеральных систем) с акцентом на состав и свойства рудоносных флюидов, что открывает новую страницу в поисках и разведке минеральных ресурсов для ядерной энергетики России и создает хорошие перспективы для устойчивого развития начальной стадии ядерного топливного цикла.
Ядерная энергетика – это единственная низко-углеродная технология для постоянной генерации больших объемов электрической и тепловой энергии (Energy…, 2022; Meeting…, 2022), что определяет ее огромную роль в снижении выбросов парниковых газов и борьбе с изменениями климата. Атомная генерация электроэнергии в нашей стране позволяет снизить годовые выбросы СО2 более чем на 100 млн т (при использовании углеводородного топлива на 1 кВт ч генерируется около 500 г СО2). Однако в ядерном топливном цикле образуются радиоактивные материалы – ОЯТ и отходы его переработки, в том числе наиболее опасные ВАО с долгоживущими трансурановыми актинидами. Использование делящихся материалов в реакторах на быстрых нейтронах более чем на 2 порядка увеличивает ресурсы атомной энергетики и позволяет вовлечь в топливный цикл накопленные запасы урана, обедненного по 235U. Образующиеся ВАО отверждаются в B–Si или Al–P стекла, что не вполне отвечает требованиям безопасности и эффективности. В частности, низкое содержание отходов (3–20 мас. %) ухудшает использование пространства глубинного хранилища. Со временем стекла кристаллизуются с увеличением растворимости и образованием коллоидов с высокой способностью к миграции. Решение проблемы ВАО связано с разделением их на группы радионуклидов, многие из этих приемов испытаны на реальных отходах переработки ОЯТ. Полученные фракции, включая группу РЗЭ-актинидов, можно включать в стекла, керамики или стеклокристаллическую матрицу с монацитом. Использование для ее изготовления ИПХТ позволит повысить загрузку отходами за счет увеличения температуры процесса и растворимости этих элементов в фосфатных расплавах. В отличие от керамических печей-плавителей, где образование в расплаве монацита может привести к нежелательным последствиям из-за его осаждения и аккумуляции в донной части, вихревые конвективные токи установки ИПХТ будут обеспечивать перемешивание расплава. Это делает ИПХТ перспективным способом изготовления стеклокерамик с фазой монацита. Кристаллизация стекла с образованием монацита происходит на 100–150°С выше температуры стеклования. Последняя, в зависимости от состава стекла, оценивается как 450–500°С, что определяет оптимальный интервал нагрева стекла в 500–700°С. Лимитирующим фактором для загрузки матриц отходами выступает тепловыделение в связи с распадом РЗЭ (Eu, Sm), а затем малых актинидов (Am, Cm). Оценки нагрева блока в зависимости от содержания отходов, габаритов матрицы и времени выдержки до захоронения имеются в работах (Юдинцев и др., 2021; Ojovan, Yudintsev, 2023). Эти значения необходимо будет в дальнейшем проверить в опытах по раскристаллизации при термической обработке стекол, содержащих РЗЭ.
В силу ограниченного объема в статье затронуты лишь некоторые важные аспекты воспроизводства минерально-сырьевой базы урана и обращения с высокоактивными отходами. Интересующемуся этой темой читателю можно рекомендовать обзоры и статьи, приведенные в списке литературы.
Список литературы
Андреева О.В., Петров В.А., Полуэктов В.В. Мезозойские кислые магматиты Юго-Восточного Забайкалья: петрогеохимия, связь с метасоматизмом и рудообразованием // Геология рудн. месторождений. 2020. Т. 62. № 1. С. 76–104.
Баторшин Г.Ш., Иванов И.А., Козлов П.В., Мокров Ю.Г. Основные стратегические решения по модернизации системы обращения с РАО на ФГУП “ПО "Маяк” // Вопросы радиационной безопасности. 2013. № 3. С. 3–11.
Баторшин Г.Ш., Ремизов М.Б., Козлов П.В., Логунов М.В., Кустов С.В. Технология переработки ядерного наследия ФГУП “ПО "Маяк” – накопленных высокоактивных гетерогенных отходов // Вопросы радиационной безопасности. 2015. № 1. С. 3–10.
Богатов С.А., Блохин П.А., Уткин С.С., Дорофеев А.Н., Киселёв А.И., Козлов П.В., Лукин С.А., Ремизов М.Б., Семёнов М.А. Усредненные оценки удельной активности и тепловыделения остеклованных высокоактивных отходов, накопленных на ФГУП “ПО "Маяк” // Вопросы радиационной безопасности. 2021. № 3. С. 1–12.
Бортников Н.С., Петров В.А., Машковцев Г.А., Печенкин И.Г. Создание минерально-сырьевой базы атомной отрасли // Минеральное сырье. Серия геолого-экономическая. № 39. М.: ФГБУ “ВИМС”, 2021. 23 с.
Бойцов А.В. Развитие мировой урановой промышленности – вызовы времени // Сборник докладов пятого международного симпозиума “Уран: геология, ресурсы, производство”. 23-24.11.2021. М.: ФГБУ “ВИМС”, 2021. С. 11–22.
Вашман А.А., Демин А.В., Крылова Н.В., Кушников В.В., Матюнин Ю.И., Полуэктов П.П., Поляков А.С., Тетерин Э.Г. Фосфатные стекла с радиоактивными отходами. М.: ЦНИИатоминформ, 1997. 172 с.
Власова Н.В., Ремизов М.Б., Козлов П.В., Беланова Е.А. Исследование химической устойчивости алюмофосфатных стекол, имитирующих отвержденные ВАО, подлежащие возврату зарубежным поставщикам ОЯТ // Вопросы радиационной безопасности. 2017. № 3. С. 32–37.
Глаголенко Ю.В., Дзекун Е.Г., Ровный С.И., Сажнов В.К., Уфимцев В.П., Брощевицкий В.С., Лаптев Г.А., Основин В.И., Захаркин Б.С., Смелов В.С., Ненарокомов Э.А., Никипелов Б.В. Переработка отработавшего ядерного топлива на комплексе РТ-1: история, проблемы, перспективы // Вопросы радиационной безопасности. 1997. № 2. С. 3–12.
ГОСТ Р 50926-96. Отходы высокоактивные отвержденные. Общие технические требования. М.: ИПК Изд-во стандартов, 1996. 6 с.
Государственный доклад “О состоянии и использовании минерально-сырьевых ресурсов Российской Федерации в 2021 году”. М.: ФГБУ “ВИМС”, 2022. 626 с.
Данилов С.С., Стефановский С.В., Стефановская О.И., Винокуров С.Е., Мясоедов Б.Ф., Тетерин Ю.А. Алюмо(железо)фосфатные стекла, содержащие редкоземельные и трансурановые элементы: фазовый состав, состояние окисления Np и Pu, гидролитическая устойчивость // Радиохимия. 2018. Т. 60. № 4. С. 371–375.
Копырин А.А., Карелин А.И., Карелин В.А. Технология производства и радиохимической переработки ядерного топлива. М.: Атомиздат, 2006. 576 с.
Лаверов Н.П. Геологические условия формирования урановых месторождений в областях континентального вулканизма (на примере Срединного Тянь-Шаня). Дис. … докт. г.-м.н. М.: ИГЕМ РАН, 1972.
Лаверов Н.П., Канцель А.В., Лисицин А.К., Омельяненко Б.И., Пэк А.А., Сельцов Б.М., Филоненко Ю.Д. Основные задачи радиогеоэкологии в связи с захоронением радиоактивных отходов // Атомная энергия. 1991. Т. 71. Вып. 6. С. 523–534.
Лаверов Н.П., Величкин В.И., Омельяненко Б.И., Юдинцев С.В., Петров В.А., Бычков А.В. Изоляция отработавших ядерных материалов: геолого-геохимические основы. М.: ИФЗ РАН, 2008. 280 с.
Лаверов Н.П., Юдинцев С.В., Стефановский С.В., Омельяненко Б., Никонов Б.С. Муратаитовые матрицы актинидных отходов // Радиохимия. 2011. Т. 53. № 3. С. 196–207.
Лаверов Н.П., Омельяненко Б.И., Юдинцев С.В., Стефановский С.В., Никонов Б.С. Стекла для иммобилизации отходов низкого и среднего уровней радиоактивности // Геология рудных месторождений. 2013. Т. 55. № 2. С. 87–113.
Логунов М.В., Тананаев И.Г., Мясоедов Б.Ф. Фракционирование ВАО: основные подходы и современное состояние // Труды Российской конференции “Фундаментальные аспекты безопасного захоронения РАО в геологических формациях”. Москва, 15–16 октября 2013. М.: Граница, 2013. С. 94–96.
Лопух Д.Б., Вавилов А.В., Хоршев А.А., Скриган И.Н., Мартынов А.П. Экспериментальные и теоретические исследования индукционных печей с холодными тиглями и донным нагревом для остекловывания радиоактивных отходов // Радиоактивные отходы. 2022. № 4 (21). С. 13–23.
Матюнин Ю.И. Локализация компонентов жидких высокоактивных отходов (РЗЭ, U и Pu) в фосфатных и боросиликатных стеклоподобных материалах. Автореферат диссертации на соискание ученой степени кандидата химических наук. М.: ВНИИНМ, 2000. 25 с.
Машковцев Г.А., Гребенкин Н.А., Петрин А.В., Прохоров Д.А. Основные направления геологоразведочных работ на уран // Сборник докладов. Пятый международный симпозиум “Уран: геология, ресурсы, производство”. 23–24.11.2021. М.: ФГБУ “ВИМС”, 2021. С. 71–90.
Машковцев Г.А., Петров В.А. Пути совершенствования научно-методических основ поисковых работ на твердые полезные ископаемые // Сборник докладов научно-практической конференции “Актуальные проблемы поисковой геологии”. 22–24.11.2022. М.: ФГБУ “ВИМС”, 2023. С. 195–208.
Мельникова И.М., Каленова М.Ю., Щепин А.С., Юдинцев С.В. Устойчивость в воде матриц редкоземельно-актинидной фракции высокорадиоактивных отходов // Докл. РАН. 2023. Т. 508. № 2. С. 275–282.
НП-093-14. Критерии приемлемости радиоактивных отходов для захоронения // Ядерная и радиационная безопасность. 2015. № 3 (77). С. 59–82.
НП-019-15. Сбор, переработка, хранение и кондиционирование жидких радиоактивных отходов. Требования безопасности. Приказ Ростехнадзора от 13.09.2021 года № 299.
Омельяненко Б.И., Лившиц Т.С., Юдинцев С.В., Никонов Б.С. Природные и искусственные минералы – матрицы для иммобилизации актинидов // Геология рудн. месторождений. 2007. Т. 49. № 3. С. 173–193.
Петров В.А., Андреева О.В., Полуэктов В.В., Коваленко Д.В. Ураноносные вулканогенные структуры: Стрельцовская (РФ), Сианшань (КНР) и МакДермитт (США). Сравнительный анализ петрологии кислых вулканитов и состава околорудных метасоматитов // Геология рудн. месторождений. 2022. Т. 64. № 1. С. 7–36.
Полуэктов П.П., Суханов Л.П., Матюнин Ю.И. Научные подходы и технические решения в области обращения с жидкими высокоактивными отходами // Российский химический журнал. 2005. Т. XLIX. № 4. С. 29–41.
Поляков А.С., Борисов Г.Б., Моисеенко Н.И., Основин В.И., Дзекун Е.Г., Медведев Г.М., Бельтюков В.А., Дубков С.А., Филиппов С.Н. Опыт эксплуатации керамического плавителя ЭП-500/1p по остекловыванию жидких высокоактивных отходов // Атомная энергия. 1994. Т. 76. Вып. 3. С. 183–188.
Пэк А.А., Мальковский В.И., Петров В.А. Минеральная система урановых месторождений Стрельцовской кальдеры (Восточное Забайкалье) // Геология рудн. месторождений. 2020. Т. 62. № 1. С. 36–54.
Ремизов М.Б., Козлов П.В., Борисенко В.П., Дементьева И.И., Блохин П.А., Самойлов А.А. Разработка алгоритма оценки радионуклидного состава остеклованных ВАО ФГУП “ПО “МАЯК” для цели их безопасного захоронения // Радиоактивные отходы. 2018. № 3 (4). С. 102–110.
Смелова Т.В., Крылова Н.В., Юдинцев С.В., Никонов Б.С. Силикатная матрица актинид-содержащих отходов // Докл. РАН. 2000. Т. 374. № 2. С. 242–246.
Стефановский С.В., Юдинцев С.В. Титанаты, цирконаты, алюминаты и ферриты – матрицы для иммобилизации актинидов // Успехи химии. 2016. Т. 85. № 9. С. 962–994.
Стефановский С.В., Стефановская О.И., Семенова Д.В. Фазовый состав и структура стекломатериалов на натрий-алюмофосфатной основе, содержащих оксиды редкоземельных элементов // Радиоактивные отходы. 2018. № 1 (2). С. 97–101.
Тарханов А.В., Бугриева Е.П. Современное состояние мировой и российской урановой промышленности // Сборник докладов пятого международного симпозиума “Уран: геология, ресурсы, производство”. 23–24.11.2021. М.: ФГБУ “ВИМС”, 2021. С. 32–40.
Шестой национальный доклад Российской Федерации о выполнении обязательств, вытекающих из Объединенной конвенции о безопасности обращения с отработавшим топливом и о безопасности обращения с радиоактивными отходами. Москва, 2020. 167 с.
Юдинцев С.В., Стефановский С.В., Каленова М.Ю., Никонов Б.С., Никольский М.С., Кощеев А.М., Щепин А.С. Матрицы для иммобилизации отходов редкоземельно-актинидной фракции, полученные методом индукционного плавления в холодном тигле // Радиохимия. 2015. Т. 57. № 3. С. 272–282.
Юдинцев С.В., Мальковский В.И. Первичные коллоиды при гидротермальном изменении алюмофосфатного стекла с имитаторами радионуклидов // Радиохимия. 2020. Т. 62. № 3. С. 258–270.
Юдинцев С.В. Изоляция фракционированных отходов ядерной энергетики // Радиохимия. 2021. Т. 63. № 5. С. 403–430.
Юдинцев С.В., Мальковский В.И., Каленова М.Ю. Тепловое поле скважинного хранилища радиоактивных отходов // Докл. РАН. 2021. Т. 498. № 2. С. 92–100.
Boatner L.A. Synthesis, structure, and properties of monazite, pretulite, and xenotime // Rev. Mineral. Geochem. 2002. V. 48 (1). P. 87–121.
Dacheux N., Clavier N., Podor R. Versatile monazite: Resolving geological records and solving challenges in materials science. Monazite as a promising long-term radioactive waste matrix: Benefits of high-structural flexibility and chemical durability // Amer. Mineral. 2013. V. 98. P. 833–847.
Demine A.V., Krylova N.V., Polyektov P.P., Shestoperov I.N., Smelova T.V., Gorn V.F., Medvedev G.M. High level liquid waste solidification using a “cold” crucible induction melter // MRS Symp. Proc. V. 663. 2001. https://doi.org/10.1557/PROC-663-27.
Descriptive uranium deposit and mineral system models. Vienna: IAEA, 2020. 328 p.
Donald I.W. Waste immobilization in glass and ceramic based hosts: radioactive, toxic, and hazardous wastes. Chichester, UK: John Wiley & Sons Ltd, 2010. 507 p.
Energy, electricity and nuclear power estimates for the period up to 2050. Vienna: IAEA, 2022. 148 p.
Frolova A.V., Danilov S.S., Vinokurov S.E. Corrosion behavior of some glasses immobilized with REE in simulated mineralized solutions // Ceram. International. 2022. V. 48. P. 19644–19654.
Fuchs K., Müller B. World stress map of the Earth: a key to tectonic processes and technological applications // Naturwissenschaften. 2001. №. 88. P. 357–371.
Geological Classification of Uranium Deposits and Description of Selected Examples. Vienna: IAEA, 2018. 417 p.
Jaeger J.C., Cook N.G.W. Fundamentals of Rock Mechanics. 3rd edition. London: Chapman and Hall, 1979. 593 p.
Jantzen C.M. Development of glass matrices for high level radioactive waste // In: Handbook of advanced radioactive waste conditioning technologies. M.I. Ojovan (Ed.). Cambridge, UK: Woodhead Publishing Limited, 2011. P. 230–292.
Kushnikov V.V., Matyunin Yu.I., Smelova T.V., Demin A.V. Use of induction melter with a cold crucible (CCIM) for HLLW and plutonium immobilization // MRS Symp. Proc. V. 465. 1997. P. 55–64.
Laverov N.P., Yudintsev S.V., Kochkin B.T., Malkovsky V.I. The Russian strategy of using crystalline rock as a repository for nuclear waste // Elements. 2016. V. 12. № 4. P. 253–256.
Meeting climate change targets. The role of nuclear energy. Paris: NEA Publishing, 2022. 49 p.
Merits and Viability of Different Nuclear Fuel Cycles and Technology Options and the Waste Aspects of Advanced Nuclear Reactors. Washington, DC: National Acad. Press. 2023. 314 p.
Nafigin I.O., Ishmukhametova V.T., Ustinov S.A., Minaev V.A., Petrov V.A. Geological and mineralogical mapping based on statistical methods of remote sensing data processing of Landsat-8: a case study in the Southeastern Transbaikalia, Russia // Sustainability. 2022. V. 14. 9242. 25 p.
Ojovan M.I., Yudintsev S.V. Glass, ceramic, and glass-crystalline matrices for HLW immobilisation // Open Ceramics. 2023. V. 14. 100355.
Rovnyi S.I., Medvedev G.M., Aloy A.S., Koltsova T.I., Samoylov S.E. REE and TRU incorporation into monazite structure ceramics // MRS Symp. Proc. V. 824. 2004. P. 208–212.
Skirrow R.G., Jaireth S., Huston D.L., Bastrakov E.N., Schofield A., van der Wielen S.E., Barnicoat A.C. Uranium mineral systems: Processes, exploration criteria and a new deposit framework // Geoscience Australia Record. 2009/20. 2009. 44 p.
Smelova T.V., Krylova N.V., Shestoperov I.N. Synthetic mineral-like matrices for HLLW solidification: preparation by induction melter with a cold crucible (CCIM) // MRS Symp. Proc. V. 465. 1997. P. 425–431.
Sobolev I.A., Stefanovsky S.V., Omelianenko B.I., Ioudintsev S.V., Vance E.R., Jostsons A. Comparative study of synroc-c ceramics produced by hot-pressing and inductive melting // MRS Symp. Proc. V. 465. 1997. P. 371–378.
Status and trends in spent fuel and radioactive waste management. Vienna: IAEA, 2022. 88 p.
Stefanovsky S.V., Yudintsev S.V., Vinokurov S.E., Myasoedov B.F. Chemical-technological and mineralogical-geochemical aspects of the radioactive waste management // Geochemistry International. 2016. V. 54. № 13. P. 1136–1156.
Stefanovsky S.V., Stefanovsky O.I., Myasoedov B.F., Vinikurov S.E., Danilov S.S., Nikonov B.S., Maslakov K.I., Teterind Yu.A. The phase composition, structure, and hydrolytic durability of sodium-aluminum-(iron)-phosphate glassy materials doped with lanthanum, cerium, europium, and gadolinium oxides // J. of Non-Cryst. Solids. 2017. V. 471. P. 421–428.
Stefanovskii S.V., Stefanovskaya O.I., Semenova D.V., Kadyko M.I., Danilov S.S. Phase composition, structure, and hydrolytic stability of sodium-aluminum(iron) phosphate glass containing rare-earth oxides // Glass and Ceramics. 2018. V. 75. № 3–4. P. 89–94.
Stefanovsky S., Ptashkin A., Knyazev O., Stefanovsky O., Yudintsev S., Nikonov B., Myasoedov B.F. Cold crucible melting and characterization of titanate-zirconate pyrochlore as potential rare earth / actinide waste form // Ceram. International. 2019a. V. 45. P. 3518–3521.
Stefanovsky S.V., Stefanovsky O.I., Danilov S.S., Kadyko M.I. Phosphate-based glasses and glass ceramics for immobilization of lanthanides and actinides // Ceram. International. 2019b. V. 45. P. 9331–9338.
Uranium 2022: Resources, Production and Demand. OECD NEA, Rep. №. 7634. 2023. 561 p.
Vlasov V.I., Kedrovsky O.L., Nikiforov A.S., Polyakov A.S. Shishtchitz I.Y. Handling of liquid radioactive waste in the concept of closed nuclear fuel // in the “Back End of the Nuclear Fuel Cycle: Strategies and Options”. Vienna, Austria: IAEA, 1987. P. 109–117.
Wyborn L.A.I., Heinrich C.A., Jaques A.L. Australian Proterozoic mineral systems: essential ingredients and mappable criteria // AusIMM Publication Series 4/94. 1994. P. 109–115.
Zoback M.D., Townend J., Rollimund B.G. Steady-state failure equilibrium and deformation of intraplate lithosphere // International Geology Review. 2002. V. 44. P. 383–401.
Дополнительные материалы отсутствуют.
Инструменты
Геология рудных месторождений