Известия РАН. Энергетика, 2019, № 6, стр. 130-144
Современные программные средства для моделирования и проектирования индукционных нагревателей
В. Б. Демидович 1, *, Ю. Ю. Перевалов 1
1 Санкт-Петербургский электротехнический университет “ЛЭТИ”
Санкт-Петербург, Россия
* E-mail: vbdemidovich@mail.ru
Поступила в редакцию 09.11.2019
После доработки 25.11.2019
Принята к публикации 28.11.2019
Аннотация
В статье излагаются принципы построения электротепловых моделей индукционных нагревателей. Дается краткое описание программного комплекса Индукционный нагрев. Приводятся примеры использования этого пакета при проектировании разнообразных индукционных нагревателей. Дальнейшее развитие этого пакета связано с разработкой цифровых систем управления и цифровых двойников мощных индукционных нагревателей.
ВВЕДЕНИЕ
Электромагнитная обработка материалов, в частности, индукционный нагрев металлов, получает все большее распространение в науке и промышленности. Особенно заметно это в металлургических отраслях [1, 2]. Мощности индукционных установок достигают десятков мегаватт. Учитывая, что индукционные технологии выгодно отличаются от других нагревательных технологий своей энергоэффективностью и низкими выбросами парниковых газов [3, 4], актуально развитие новых и совершенствование традиционных технологий с применением индукционного нагрева.
Индукционные нагревательные системы являются сложными техническими объектами, в которых протекают физические процессы различной природы. Без предварительного моделирования и создания фактически цифровых двойников современные мощные индукционные нагревательные установки не могут вписываться в технологический процесс. В общем случае математическое описание таких объектов представляет собой систему детерминированных нелинейных дифференциальных и интегральных уравнений, записанных для многомерных и многосвязных областей. Если не вводить существенных упрощений в постановку задачи, то решение указанной системы уравнений, а значит и количественное описание изучаемых объектов, может быть получено только с использованием численных методов посредством моделирования на вычислительной технике.
Применение компьютеров при моделировании индукционных электротермических установок позволило существенно продвинуть теорию индукционного нагрева. Это связано с тем, что появилась реальная возможность не только исследовать отдельные аспекты и закономерности проявления электромагнитных, тепловых и других эффектов в устройствах индукционного нагрева, но и создавать комплексные модели, учитывающие неразрывную связь электромагнитных и тепловых процессов в нелинейных и многомерных областях загрузки индукционных электротермических устройств. В известном смысле можно говорить о том, что уровень развития моделирования индукционных нагревателей (ИН) и технологических процессов с использованием индукционного нагрева определяет уровень развития теории индукционного нагрева. Ошибки в проектировании этих установок приводят к чрезвычайно неприятным и дорогостоящим последствиям. Поэтому без точного расчета электромагнитных и температурных полей при индукционном нагреве невозможно проектирование и управление сложными энергоемкими установками индукционного нагрева.
ЭТАПЫ МОДЕЛИРОВАНИЯ СИСТЕМ ИНДУКЦИОННОГО НАГРЕВА
До появления компьютерной техники развивались аналитические методы расчета индукторов [5–7], основанные на схемах замещения. Были проведены металловедческие исследования, позволяющие выявить особенности индукционного метода термообработки [8]. С появлением в 60-х гг. ХХ в. доступной для научной и инженерной деятельности вычислительной техники стали быстро развиваться численные методы расчета и моделирования электромагнитных и температурных полей при индукционном нагреве, которые систематизированы в монографиях [9, 10].
Моделирование индукционных нагревательных систем прошло несколько этапов. Вначале были разработаны пространственно одномерные модели индукционного нагрева цилиндра или пластины в продольном магнитном поле. Весьма эффективным оказался метод связанных контуров при решении двумерных задач индукционного нагрева цилиндрических немагнитных тел [11]. В целом на этом этапе (условно по времени – начало 60-х–середина 70-х гг. ХХ в.) исследователям из разных стран удалось решить некоторые теоретические проблемы индукционного нагрева, такие как краевые эффекты индуктора и заготовки, переноса мощности в соседних магнитосвязанных индукторах и т.д.
К середине 70-х гг. были разработаны первые двумерные электротепловые модели для расчета индукционного нагрева цилиндрических и плоских тел [13, 14]. Уже тогда удалось внедрить или отдельные разработанные численные модели или в целом автоматизированные системы научных исследований (АСНИ) индукционных нагревателей [9, 14] на ЭВМ типа ЕС и БЭСМ-6 при решении научных и практических задач. Часто это приводило к удорожанию исследовательских и проектных работ, поскольку требовало высокой квалификации пользователя и значительных затрат времени на подготовку данных, проведение расчетов и верификацию результатов. Но, как показал опыт, объем информации, доступный при численном моделировании, позволял в конечном итоге получать оптимальные проектные решения за приемлемое время и окупался.
Ситуация существенно изменилась с появлением персональных компьютеров (ПК) в конце 80-х гг. XX в. Доступность ПК, широкое распространение и новые функциональные возможности привели к разработке моделей с “дружественным” интерфейсом, которые позволили значительно расширить круг пользователей и давали возможность пользователю, не знакомому с численными методами, на основе только физической постановки задачи легко вводить базовые исходные данные и анализировать результаты расчетов [9, 10].
В середине 90-x гг. XX в. рост производительности вычислений компьютеров, созданных на платформе Intel, и широкое распространение операционной системы Windows привели к новым возможностям при моделировании. Расширился объем оперативной памяти, что позволило использовать более сложные математические методы, программы стали работать быстрее, повысился уровень информативности при обработке и выводе результатов.
Исследователям стали доступны коммерческих пакеты общего назначения для расчета электромагнитных полей, разработанных такими корпорациями, как ANSYS, ANSOFT, INFOLITICA, Cedrat, VECTOR FIELDS и др. В практику проектирования начало входить использование пространственно трехмерных моделей.
Следует отметить, что все время повышаются требования к точности расчетов ИН, и в связи с этим повышаются требования к программному обеспечению, используемому при исследовании и проектировании. С другой стороны, появление 64-битных персональных компьютеров в начале ХХI в. характеризует очередной скачок в развитии вычислительной техники. Новые доступные объемы оперативной памяти позволяют решать сложные сопряженные нелинейные трехмерные задачи, а применение параллельных вычислений в разы уменьшает время, необходимое для расчетов. Появляется возможность перехода от моделирования отдельных устройств к моделированию сложных комплексов и собственно технологических процессов с применением индукционного нагрева.
Чрезвычайно важно в настоящее время и в будущем использование моделей в системах управления ИН. Очевидно, они должны обладать высокой точностью и быстродействием, обеспечивающим работу в реальном масштабе времени. Системы управления ИН по “модели” становятся превалирующими в современных нагревательных комплексах и превращают их в “интеллектуальные” устройства. Реализация таких систем возможна только с использованием прикладных программных комплексов и невозможна с применением коммерческих пакетов типа ASYS и ему подобных.
ПРОГРАММНЫЙ КОМПЛЕКС INDUCTION HEATING (IndHeat)
Принцип построения современных специализированных программ для ИН [9, 10, 16] показан на рис. 1. Препроцессор, как правило, оснащенный дружественным интерфейсом, служит для ввода данных о структуре нагревателя и режимах его работы. Блок расчета (реализует математическую модель) в современных программах согласован с модулем визуализации, что позволяет исследователю делать выводы и принимать решения в течение вычислительного эксперимента. Очень важный блок управления отвечает за изменения режима работы во времени и дает возможность реализовывать нестационарные процессы, управляя моделью (загрузка, выгрузка деталей и т.д.). Этот блок позволяет использовать одну и ту же модель для различных технологических задач. Постпроцессор служит для визуализации результатов и максимального удобства работы с ними.
В случае необходимости оптимизации конструкции или режима работы индукционной системы используются различные блоки оптимизации. В настоящее время их реализуют как внешние управляющие программы, а не встраивают в основную модель. Это вызвано большим многообразием задач оптимизации, которые трудно учесть при создании программы, а также тем, что желательно применять параллельные и распределенные вычисления, для которых такой подход наиболее эффективен.
При разработке моделей для ИН целесообразно использовать модульный или объектно-ориентированный принцип. Это предполагает создание специализированной библиотеки стандартных подпрограмм для решения задач индукционного нагрева. На базе такой библиотеки можно легко и, самое главное, быстро конструировать новые модели, учитывающие различные режимы нагрева, а также те или иные особенности технологического процесса.
В СПбГЭТУ “ЛЭТИ” разработаны, теоретически обоснованы и экспериментально проверены численные модели совместного расчета электромагнитных и температурных полей в индукционных нагревателях, составляющие иерархическую структуру из пространственно одно-, двух- и трехмерных моделей [9, 10, 16], образующих специализированный комплекс программ IndHeat.
Программы, входящие в пакет Induction Heating (IndHeat):
• CP1D – пространственно одномерная модель для расчетов индукционного нагрева цилиндрической загрузки, слябов, пластин, лент;
• SS2D – пространственно двухмерная модель для расчетов индукционного нагрева слябов, пластин, лент;
• Universal2D – пространственно двухмерная модель для расчета индукционного нагрева цилиндрических тел;
• Universal3D – пространственно трехмерная модель для расчета индукционного нагрева слябов, блюмсов.
Использование двумерной постановки задачи для расчета нагрева осесимметричных заготовок в цилиндрических индукторах в большинстве случаев позволяет получать исчерпывающую информацию о процессе нагрева. Учет конечной длины индуктора и загрузки дает возможность оценить влияние важнейших конструктивных параметров индукторов и режимов нагрева на электромагнитные и тепловые характеристики индукционного нагревателя.
Программа UNIVERSAL 2D применяет комбинированный метод расчета, используя метод интегральных уравнений (МИУ) для решения внешней электрической (воздух и область индуктора) и метод конечных разностей (МКР) для решения внутренней электротепловой (область заготовки) задач, которые связаны с помощью импедансных граничных условий [9]. В результате внешнего электрического расчета при заданном напряжении питания, токе или мощности цепи определяются полная активная мощность, полная реактивная мощность, активная мощность, выделяющаяся в загрузке, мощность потерь в индукторах, токи в индукторах, электрический КПД нагревателя, распределение напряженности магнитного поля на поверхности загрузки. Внутренний электротепловой расчет заключается в нахождении распределения температуры по длине и в поперечном сечении выходной заготовки при определенных граничных условиях на поверхности загрузки, которые задаются или из условия свободного теплообмена с окружающей средой, или с учетом футеровки. Одновременно рассчитываются общие тепловые потери и распределение температуры внутренней поверхности футеровки по длине нагревателя.
С помощью UNIVERSAL 2D пользователь без больших временны́х затрат и с достаточной расчетной точностью может получить все требуемые параметры индукционной системы. Расчет может производиться при любой степени выраженности поверхностного эффекта, встречающегося в практике сквозного индукционного нагрева заготовок из меди, алюминия, титана, их сплавов, магнитной и немагнитной стали и т.д. Предусматривается расчет нагревателей с секционированными многофазными индукторами, с обычным и автотрансформаторным включением обмоток.
Модель UNIVERSAL 3D основана на комбинации трех численных методов: МКЭ, МКР и МИУ. Структурная схема модели такая же, как и для системы с осесимметричной магнитной загрузкой (рис. 2.1). Задача разбивается на внешнюю, решаемую МИУ (2D) и внутреннюю трехмерную (область загрузки), решаемую МКЭ и МКР. Сшивание задач происходит также с помощью импедансных граничных условий.
Квазитрехмерная программа UNIVERSAL 3D предназначена для расчета электромагнитных и тепловых параметров индукционного нагрева ферромагнитных и немагнитных заготовок. Программа позволяет моделировать индукционный нагрев тел прямоугольного сечения и прямоугольного сечения со скруглением углов перед пластической деформацией, прокаткой, термообработкой и т.д.
Эта программа является расширением UNIVERSAL 2D для тел с прямоугольным сечением и предоставляет пользователю те же самые возможности. В UNIVERSAL 3D также можно моделировать различные типы нагревателей (периодический, методический и непрерывный), нестационарные режимы их работы (пуск, разгрузка) и моделировать всю технологическую линию термообработки металлов, включая газовые печи и зоны транспортировки.
Все они позволяют моделировать электромагнитные и температурные поля в нагревателях периодического действия, непрерывных нагревателях, непрерывных с дискретным и с возвратно-поступательным движением загрузки.
ПРИЛОЖЕНИЯ ПРОГРАММНОГО КОМПЛЕКСА IndHeat ПРИ РАЗРАБОТКЕ ИНДУКЦИОННЫХ НАГРЕВАТЕЛЕЙ
Нагрев титановых слитков перед прессованием с помощью комбинированного метода нагрева в индукционном нагревателе и печи сопротивления
Исходные данные для моделирования и разработки технологической линии: нагрев слитков из титановых сплавов диаметром до 275 мм перед прессованием с требуемой конечной температурой перед прессованием 1000°C с теплоперепадом не более 20°C.
С помощью программы Universal 2D моделировался полностью весь технологический процесс – нагрев до определенной температуры (900°C) в индукционном нагревателе, затем транспортировка нагретой в индукторе заготовки к печи сопротивления и нагрев в печи сопротивления до температуры прессования с выравниванием температуры по объему заготовки.
На рис. 2 представлено изменение температуры поверхности и центра заготовки (красная и синяя линии соответственно) и температурное поле по длине заготовки на всех стадиях технологической линии нагрева. Как видно из рисунка, на выходе из индуктора температурное поле сильно неравномерное – разница между центром и поверхностью достигает 250°C. Во время транспортировки температура несколько выравнивается за счет теплопроводности. Дальнейший нагрев в печи сопротивления позволяет достичь требуемого распределения температуры по объему слитка. Использование индукционного нагрева в такой линии позволяет уменьшить общее время нагрева, а, следовательно, увеличить производительность и уменьшить энергозатраты на тонну нагреваемого металла.
Моделирование прецизионного нагрева длинномерных титановых заготовок в системе индукторов с организацией возвратно-поступательных движений заготовки
Для моделирования прецизионного нагрева длинномерных титановых заготовок диаметром от 50 до 120 мм, длиной от 2000 до 5800 мм, в системе из 8 индукторов использовалась программа Universal 2D. При этом моделировалось возвратно-поступательное движение заготовок внутри индукционной системы. Конечная температура нагрева 750 ± 20°С. Такая система движения заготовок необходима для “размывания” температуры по длине нагреваемой заготовки и получения требуемого температурного распределения.
В ходе анализа системы и по результатам численного моделирования было выявлено, что для равномерного нагрева длинномерных цилиндрических заготовок из сплавов титана необходимо выполнение следующих условий: одинаковые геометрические параметры всех индукторов (длина, диаметр, кол-во витков, футеровка), одинаковое расстояние между индукторами, равенство величины амплитуды покачивания сумме длины индуктора и расстоянию между индукторами, одинаковое значение тока в индукторах в процессе нагрева, отключение нагрева только после полного числа циклов “качения” заготовки.
На рис. 3 изображено распределение температуры по длине на поверхности заготовки в течение одного цикла “качения”: в момент начала “качения”, в конце “качения” и в процессе перемещения заготовки между крайними положениями, полученное по результатам численного моделирования.
Моделирование нагрева циркониевых слитков в периодическом индукционном нагревателе специальной конструкции
На рис. 4 изображено конечное распределение температуры по длине заготовки из циркония диаметром 220 мм и длиной 475 мм. Требуемая конечная температура нагрева 1000°C, с теплоперепадом по объему заготовки не более 20°C. Такой прецизионный нагрев стал возможным с применением оптимальных режимов нагрева и специальной конструкции индуктора, имеющего двухслойную обмотку и специальные торцевые футеровочные крышки. Второй слой индуктора предназначен для компенсирования краевого эффекта индуктора и располагается симметрично по краям. Футеровочные крышки предназначены для уменьшения теплопотерь с торцов заготовки.
Нагрев состоит из двух этапов: на первом этапе нагрев производится при максимальной мощности на частоте 60 Гц до достижения температуры на поверхности, близкой к конечной, второй этап нагрева заключается в термостатировании. Таким образом, по окончании нагрева достигается требуемое равномерное распределение температуры с минимальным перепадом 20°C.
Кроме температурных полей в продольном и поперечном сечении заготовки в процессе моделирования были получены значения виткового сопротивления индуктора, которые приведены на рис. 3. Как видно из рисунка, сопротивление внешнего слоя меньше, чем внутреннего, что объясняется эффектом близости. Сопротивление витков внутреннего слоя, расположенного под витками внешнего слоя, выше, чем в средней части, что объясняется перераспределением тока по сечению витка.
Моделирование индукционного нагрева мерных цилиндрических заготовок в кузнечном индукционном нагревателе (КИН) методического действия с дискретным переталкиванием заготовок
Кузнечные индукционные нагреватели используются для объемного нагрева заготовок перед пластической деформацией. Нагреву подвергаются заготовки большой номенклатуры как по диаметру, так и по длине, при этом довольно часто возникает потребность нагревать широкую гамму заготовок в одном индукторе. В таком случае неизбежно влияние на надежность режимов работы и производительность установки в целом, и особенно на ее энергетические показатели. Применение математического моделирования позволяет определить оптимальную конструкцию индукционного нагревателя, характеристики источника питания установки, составить технологические карты нагрева для всей гаммы нагреваемых заготовок.
Исходные данные для моделирования: диаметр нагреваемых стальных заготовок 30–110 мм, производительность установки 2 т/ч, температура штамповки 1230 ± 20°С с температурным перепадом не более 100°С по радиусу.
По результатам моделирования были определены характеристики типоразмеров индукторов и их назначение – в одном индукторе нагреваются заготовки диаметром от 30 до 60 мм, в другом индукторе диаметром от 65 до 110 мм. Частота тока 1000 Гц.
На рис. 5 показано расчетное окно программы Universal 2D при моделировании нагрева заготовок диметром 60 мм.
С помощью пакета программ IndHeat, кроме моделирования стационарных режимов работы кузнечных индукционных нагревателей, возможно моделирование и нестационарных режимов: пуска и разгрузки нагревателя, режим термостатирования. Например, анализ результатов моделирования пуска нагревателя позволяет дать рекомендации по количеству холодных заготовок при пуске для уменьшения брака.
Индукционный нагреватель с дискретным переталкиванием мерных заготовок является одним из самых распространенных типов нагревателей, используемых в кузнечном производстве. При проектировании индукционного нагревателя в основу проектного решения обычно принимается анализ его работы в установившемся режиме. Однако, как показывает опыт, в работе индукционного нагревателя значительную долю времени занимают различного рода неустановившиеся, переходные процессы. Поэтому анализ нестационарных режимов работы нагревателей должен входить при их проектировании как необходимый этап.
В качестве примера рассмотрим нагрев партии из 18 штук стальных заготовок диаметром 8 см и длиной 40 см каждая. Заготовки перемещаются в индукционном нагревателе, состоящем из двух индукционных катушек с числом витков 100, внутренним диаметром 13 см и длиной 125 см, включенных параллельно к источнику питания с частотой 1000 Гц. Темп переталкивания – 40 с. Все расчеты и оптимизация индукционных нагревателей проводилась в среде UNIVERSAL2D. На рис. 6 показано распределение температуры в заготовках в стационарном режиме.
Рис. 6.
Зависимости распределение температуры в заготовках в стационарном режиме: 1 – поверхности; 2 – средней; 3 – центра.
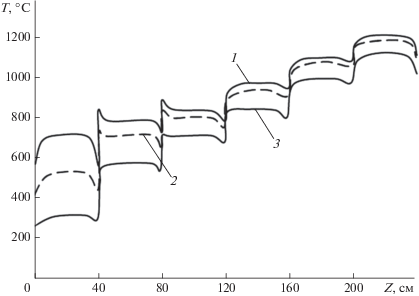
На рис. 7 и 8 показано, как изменяются параметры нагревателя в течение всего цикла нагрева. Нагрев начинается после подачи первой холодной заготовки в первый индуктор. Далее с периодичностью 40 с подаются новые заготовки до полного заполнения двух индукторов (шесть заготовок). Последующая подача холодных заготовок приводит к выталкиванию уже нагретых заготовок с выходом на стационарный режим. Колебания параметров нагревателя в стационарном режиме для второго индуктора меньше, так как заготовки в него поступают почти полностью прогретые выше температуры точки Кюри. На рис. 9 приведены температурные поля первой вышедшей заготовки, 12-й заготовки (стационарный режим) и 18-й (последней) заготовки.
Рис. 7.
Изменение активной мощности и токов в индукторах в процессе нагрева, где индексы 1 и 2 – номера индукторов.
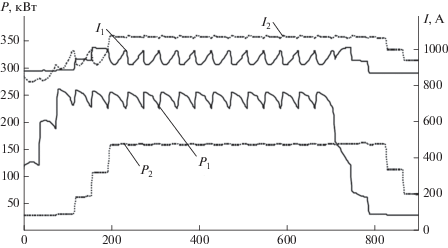
Моделирование технологии индукционной термообработки валков прокатных станов
Валки прокатных станов проходят сложную термическую обработку, включающую многостадийную нормализацию и отжиг, а на заключительной стадии – поверхностную индукционную закалку с отпуском. Разработка оборудования и технологии индукционной термообработки представляет серьезную проблему, от решения которой зависит качество и экономические показатели получения валков прокатных станов и, в конечном счете, проката [17, 18].
Проектирование оборудования и технологии индукционной термообработки валков прокатных станов необходимо осуществлять в первую очередь для обеспечения качества термообработки. Необходимые условия при этом: минимальные отклонения требуемой твердости по длине бочки и глубине закаленного слоя, отсутствие опасных термических и структурных напряжений, приводящих к разрушению валка, как в процессе термообработки, так и после. Без компьютерного моделирования невозможно решение этих задач.
В силу значительных габаритов валков (длина – до нескольких метров) проведение одновременной закалки по всей длине бочки невозможно из-за требуемой значительной мощности и трудностей с одновременным охлаждением. При индукционной термообработке валков прокатных станов целесообразно использовать непрерывно-последовательный метод закалки. Деталь устанавливают в станок и зажимают в центрах, для обеспечения равномерности нагрева по периметру валок вращают с постоянной скоростью. За индуктором на некотором расстоянии расположен спрейер, который жестко связан с индуктором. Таким образом, нагревается и охлаждается вся поверхность бочки валка.
На рис. 10 представлены графики поличастотной (многопроходной) закалки и закалки за один проход, в обоих режимах поставлены одинаковые условия: базовая частота 100 Гц, температура на поверхности валка за индуктором 950°С, а на глубине 100 мм за индуктором 750°С. На рис. 10 представлены следующие графики: 1, 2, 3 – температура на поверхности; на глубине 50 мм, на глубине 100 мм при поличастотной закалке соответственно; 4, 5, 6 – температура на поверхности; на глубине 50 мм, на глубине 100 мм при закалке за один проход соответственно. При использовании непрерывно-последовательного метода закалки сложно достичь большой глубины закаленного слоя. Для того чтобы увеличить глубину, необходимо увеличивать время нахождения нагреваемой зоны под индуктором, чтобы за счет теплопроводности увеличить глубину прогрева.
Это можно сделать либо за счет снижения скорости перемещения детали или за счет увеличения длины индуктора, при этом необходимо помнить, что нельзя допускать перегрева поверхности валка. На рис. 12 показано распределение температуры вдоль валка в процессе нагрева под закалку. Снижение скорости перемещения может привести к появлению тепловой волны перед индуктором (что ведет к нестационарному режиму нагрева) или к проблеме подсуживания стали в месте перехода от индуктора к спрейеру.
Рис. 12.
Распределение температуры вдоль валка в процессе нагрева под закалку: 1 – температура на поверхности; 2 – распределение температуры на глубине 100 мм.
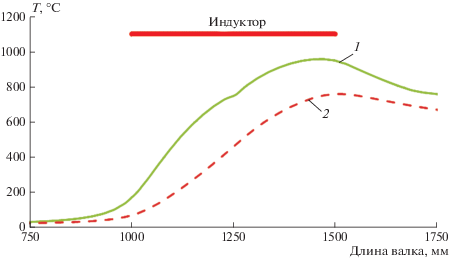
Индукционный подогрев валков большого диаметра целесообразно осуществлять на частоте тока 100 Гц, а частота тока на закалочном проходе определяется требуемой глубиной закалки.
Комплексные модели термообработки валков позволяют не только осуществлять расчетное проектирование, но и разрабатывать технологическую карту термообработки и вводить ее в систему управления, что гарантированно обеспечивает высокое качество термообработки валков.
ЗАКЛЮЧЕНИЕ
Разработанный специализированный пакет программ IndHeat позволяет моделировать и проектировать широкий круг технологических процессов с использованием индукционного нагрева. Это программное обеспечение служит основой при построении цифровых двойников и систем управления индукционными нагревателями.
Список литературы
Rudnev V., Loveless D., Cook R. Handbook of Induction Heating. – 2nd Edition, CRC Press, 2017.
Vasilev A.S., Demidovich V.B. Inductive heating in the metallurgical industry Russian Electrical Engineering. 2003. V. 74. № 5. P. 61–64.
Muehlbauer A. History of Induction Heating and Melting. – Vulkan Verlag, 2008.
Бааке Э., Йорн У., Мюльбауэр А. Энергопотребление и эмиссия СО2 при промышленном технологическом нагреве / Перевод с немецкого под редакцией В.Б. Демидовича – V-ULKAN-VERLAG ESSEN, 1997. 173 с.
Слухоцкий А.Е., Рыскин С.Е. Индукторы для индукционного нагрева. Л.: Энергия, 1974. 264 с.
Кувалдин А.Б. Низкотемпературный индукционный нагрев стали. М.: Энергия, 1976.
Davis J., Simpson P. Induction Heating Handbook. – McGraw-Hill, 1979.
Головин Г.Ф., Замятнин М.М. Высокочастотная термическая обработка. Вопросы металловедения и технологии / 3-е изд., перераб. и доп. Л.: Машиностроение. Ленигр. отд., 1990. 239 с.
Немков В.С., Демидович В.Б. Теория и расчет устройств индукционного нагрева. Л.: Энергоатомиздат, 1988.
Демидович В.Б., Чмиленко Ф.В. Компьютерное моделирование устройств индукционного нагрева. СПб: Изд-во СПбГЭТУ “ЛЭТИ”, 2013. 160 с.
Kolbe E., Reiss W. Eine Methode zur numerischen Bestimmung der Stromdichteverteilung // Wiss. Z. Hochschule Elektrotechnik. Ilmenau. 1963. Bd. 9. № 3. P. 311–317.
Reichert K. A numerical method to calculate induction heating installations, J. Elektrowaerme Int. 1968. Bd. 26. № 4.
Демидович В.Б., Немков В.С., Полеводов Б.С. Электротепловая модель индукционного нагревателя немагнитных цилиндрических слитков // Изв. ЛЭТИ, 1976. Вып. 203. С. 7–14.
Демидович В.Б. Проектирование электротермических установок. Л.: ЛЭТИ, 1988.
Демидович В.Б., Растворова И.И. Метод совместного моделирования электрических цепных и полевых задач // Электротехника. 2014. № 8. С. 63–67.
Демидович В.Б. Компьютерное моделирование и оптимальное проектирование энергосберегающих технологий индукционного нагрева металлов // Изв. РАН. Энергетика. 2012. № 6. С. 48–63.
Демидович В.Б., Перевалов Ю.Ю. Индукторы для закалки валков прокатных станов // Электричество. 2019. № 3. С. 65–70.
Demidovich V.B., Perevalov Yu.Yu. Increase of efficiency of heat treatment of large-sized mill rolls by means of modeling of thermal conditions of hardening // Metallurgist, 2019.
Дополнительные материалы отсутствуют.
Инструменты
Известия РАН. Энергетика