Известия РАН. Серия физическая, 2020, T. 84, № 6, стр. 824-828
Новые применения лазерной виброметрии
А. В. Стуленков 1, *, П. И. Коротин 1, А. С. Суворов 1
1 Федеральное государственное бюджетное учреждение науки
“Федеральный исследовательский центр Институт прикладной физики Российской академии наук”
Нижний Новгород, Россия
* E-mail: stulenkov@ipfran.ru
Поступила в редакцию 16.12.2019
После доработки 20.01.2020
Принята к публикации 26.02.2020
Аннотация
О возможности использования лазеров для бесконтактного измерения вибраций известно с середины 1960-х годов. Данная работа демонстрирует развитие некоторых прикладных направлений: использование лазерной виброметрии в акустической голографии ближнего поля, верификация численных моделей колебаний сложных конструкций, вибрационная дефектоскопия.
ВВЕДЕНИЕ
О возможности определять параметры вибрации тела по модуляции отраженного лазерного луча известно достаточно давно [1]. Сравнительно недавно стали появляться приборы, которые не только надежно измеряют параметры вибрации, но, даже при их высокой цене, конкурентоспособны с измерителями на основе пьезокерамики. Оставаясь существенно более сложными приборами, лазерные виброметры имеют целый ряд преимуществ, которые существенно расширяют область применения [2].
Традиционно для измерения распределения вибраций на поверхности тела, используются схемы, которые предполагают установку фиксированного количества датчиков. Однако существует целый ряд ситуаций и задач, когда контактный подход невозможен или не в состоянии обеспечить измерения с необходимой точностью. Приведем некоторые примеры подобных ситуаций: контроль вибраций на поверхностях с малым импедансом, когда вес датчика искажает показания [3]; измерения колебаний поверхности жидкости [4]; контроль вибрации тел, охлажденных до сверхнизких температур [5]; измерения в помещениях с высоким уровнем радиации или другой вредной для человека средой; необходимость высокого пространственного разрешения [6]; измерения на неровных поверхностях; измерения на сверхвысоких частотах вплоть до гиперзвуковых [7]. Перечень задач можно и продолжить, но ясно, что новый тип измерительных приборов влечет за собой и появление новых методов измерений, которые ранее были невозможны.
Лазерная доплеровская (ЛД) виброметрия (ЛДВ, LDV) использует то, что изменение частоты света, отраженного от тела, пропорционально скорости колебаний в точке отражения луча. Изменение угла падения луча на поверхность дает возможность измерять все три составляющие вектора скорости. Сканирование лазерного луча возможно с очень большой частотой, что позволяет для низкочастотных колебаний строить мгновенные распределения вибрационной скорости по телу. Сканирование можно синхронизовать с частотой вращения объекта контроля, например, лопаток турбины. Все эти возможности используются в различных конструкциях ЛД- виброметров. В данной работе представлены методы лазерной виброметрии в областях, где возможно заметное продвижение при использовании указанной альтернативы контактным измерениям: ближнепольная акустическая голография, верификация численных моделей сложных конструкций и связанная с ней неразрушающая дефектоскопия.
АКУСТИЧЕСКАЯ ГОЛОГРАФИЯ БЛИЖНЕГО ПОЛЯ
Акустическая голография ближнего поля – метод, позволяющий определять поле в дальней зоне объекта и восстанавливать распределение акустической интенсивности на поверхности объекта [8–10]. Для получения исходных данных – распределения поля вблизи исследуемого тела, необходимого для реализации метода, – изначально применялись планарные микрофонные решетки или перемещаемые цепочки приемников. Основным недостатком такого подхода является ограничение частотного диапазона и пространственного разрешения. В работе [11] был предложен способ регистрации скорости частиц среды с помощью тонкого невесомого экрана, на котором измерялась скорость колебаний для использования в акустической голографии. Появление сканирующих лазерных виброметров позволило произвести первые подобные измерения в воздухе [12, 13] с помощью экрана из полиэстера в деревянной рамке. Результаты сравнивались со скоростью, определенной с использованием градиента давления, измеренного двумя микрофонами.
Цель данной работы – определить достижимую точность измерений. После проверки различных материалов был выбран экрана из полиэтилена с алюминиевым покрытием толщиной 12 мкм. Данный материал тонкий и легкий (плотность ~1800 кг ⋅ м–3) и выгодно отличается за счет алюминиевого покрытия, которое хорошо отражает луч лазерного виброметра. Кроме того, потери в материале достаточно высоки, чтобы подавлять собственные резонансные формы колебаний экрана по сравнению с вынужденными колебаниями от воздействия звукового поля. Сложностью при измерениях оказалась чувствительность к воздушным потокам, возбуждающим маятниковые колебания всей конструкции. Для изучения возможностей метода использован экран прямоугольной формы (высота – 1.2 м, ширина – 0.9 м). Верхняя часть экрана приклеивалась к деревянной рамке, и экран растягивался под собственным весом.
В измерениях использован динамик, установленный на расстоянии 16 см от экрана, возбуждаемый шумовым сигналом в полосе 500–5000 Гц (рис. 1а). Сканирующий лазерный виброметр располагался с противоположной стороны на удалении 4 м от экрана. Все измерения проводились в акустической безэховой камере для исключения отражений от стен.
Рис. 1.
а – Схема измерительной установки; б – распределение нормальной компоненты скорости на поверхности экрана на частоте 1800 Гц.
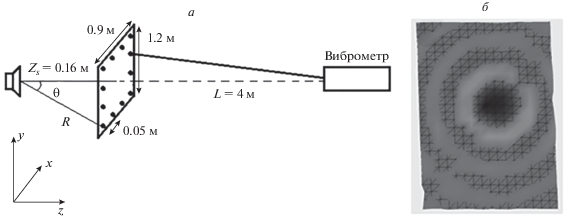
Экспериментальная схема позволяла наблюдать на поверхности экрана расходящиеся волны от точки напротив источника звука. Для регистрации мы использовали сканирование по 425 точкам с шагом 5.5 см. Сетка и мгновенное распределение скорости показаны на рис. 1б.
Скорость, измеренная лазерным виброметром на экране, была сопоставлена со скоростью колебаний среды, определенной в отсутствие экрана. Для этого микрофон помещался в точки сканирования в отсутствие экрана. Звуковое давление, определенное в точке, пересчитывалось в нормальную компоненту колебательной скорости (z-компонента скорости, рис. 1а). Нормальная к плоскости экрана компонента скорости определялась по формуле:
(1)
${{V}_{z}} = \frac{i}{{2\pi f\rho }}\frac{{\partial p}}{{\partial z}} = \frac{i}{{2\pi f\rho }}\frac{{{{z}_{s}}{{e}^{{ikR}}}(ikR - 1)}}{{{{R}^{3}}}},$Здесь ${{p}_{0}}$ – амплитуда звукового давления источника, приведенная к 1 метру, $F(f,\theta )$ – множитель, характеризующий частотную зависимость динамика.
Таким образом, для описанных условий эксперимента отличие амплитуды скоростей, определенных в свободном пространстве и с помощью лазерной виброметрии на экране в диапазоне частот ниже 4 кГц, не превышает 3–4 дБ. На графике (рис. 2б) в диапазоне частот 1500–2500 Гц заметно превышение уровня колебаний на экране. Это превышение (до 5 дБ) обусловлено влиянием собственных колебаний экрана. Характерная фазовая картина и полученная точность измерений по амплитуде указывают на пригодность данных, полученных с помощью лазерной виброметрии, для реализации метода акустической голографии в ближнем поле.
ВЕРИФИКАЦИЯ ЧИСЛЕННЫХ МОДЕЛЕЙ
Обеспечение требований к измерениям акустических характеристик сложных механоакустических систем невозможно без численного моделирования на этапе проектирования. Использование численной конечно-элементной модели (КЭМ), созданной по чертежам конструкции, возможно после подтверждения ее достоверности – верификации на физическом эксперименте.
Корректировка параметров КЭМ в ручном режиме по измеренным на прототипе или модели конструкции вибрационным или акустическим полям в общем случае является нерешаемой задачей, так как количество степеней свободы КЭМ может достигать нескольких миллионов. Известно несколько автоматических способов доводки параметров численных моделей [14–16]. Одним из эффективных методов, позволяющим учитывать и различные производственные дефекты, и геометрические отклонения формы и размеров без глубокой детализации корректируемой численной модели, является метод, описанный в работе [17].
В [17] предполагается, что для корректного расчета акустического и вибрационного полей необходимо выполнение двух условий: совпадение собственных резонансных частот и форм колебаний объекта и его КЭМ. Алгоритм, описанный в работе, позволяет изменять значения параметров КЭМ для приведения вычисленных значений частот в соответствие с экспериментом при сохранении форм собственных колебаний за счет изменения параметров жесткости элементов КЭМ.
Для верификации КЭМ необходимо иметь возможность сравнивать численные и экспериментальные данные в большом количестве точек для определения соответствия расчетных и экспериментальных форм колебаний. Размещение измерительной схемы с большим количеством датчиков неизбежно повлияет на результат измерений, особенно если для верификации используется масштабная модель конструкции. Лазерный доплеровский виброметр решит задачу получения неискаженных экспериментальных данных практически для всего диапазона практических потребностей.
Продемонстрируем использование лазерного виброметра на примере макета стальной цилиндрической оболочки, диаметром около 1 м и длиной немногим более 1 м. На начальном этапе работ исходная КЭМ объекта (рис. 3а) разработана по чертежам макета. Для нее выполнен модальный анализ и определены собственные частоты конструкции с соответствующими им формами колебаний в полосе от 50 до 3000 Гц. Измерения заключались в определении собственных форм колебаний при возбуждении макета вибратором с полосовым шумом. Вибрации регистрировались с помощью трехкомпонентного сканирующего виброметра с системой зеркал, управляемой сервоприводом. Все три компоненты вибрации определялись в 600 точках, что соответствует 1800 однокомпонентным измерительным элементам.
Рис. 3.
Иллюстрации к процессу корректировки численной модели: а – исходная численная модель, б – откорректированная численная модель, в – расчетная форма колебаний на частоте 211 Гц, г – экспериментальная форма колебаний на частоте 197 Гц.
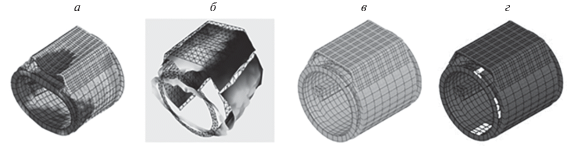
Алгоритм корректировки [17] подразумевает сравнение расчетных и экспериментальных результатов. На рис. 4 представлены амплитудно-частотные характеристики входного импеданса в точке возбуждения вибратором: экспериментальная и расчетная до и после доводки КЭМ. На рис. 3в показана экспериментально измеренная форма колебаний на частоте 197 Гц и на рис. 3г – соответствующая ей расчетная форма, для которой значение резонансной частоты по исходной КЭМ составило 211 Гц.
Рис. 4.
Результат корректировки численной модели. Сплошная кривая – экспериментальный результат, точки – расчет по исходной КЭМ, пунктир – расчет по откорректированной КЭМ.
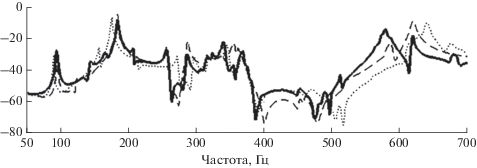
Алгоритм [17] автоматически определяет, у каких элементов КЭМ и насколько надо изменить модуль упругости, чтобы расчетная собственная частота совпала с экспериментальным значением. На рис. 3б элементы КЭМ, у которых была изменена жесткость по результатам работы алгоритма, отмечены.
Таким образом, лазерная виброметрия позволяет реализовать создание и верификацию КЭМ с использованием масштабных моделей конструкций, на которых невозможно разместить достаточное количество датчиков, и кардинально (на порядки) сокращает время проведения измерений.
ДЕФЕКТОСКОПИЯ
Лазерная доплеровская виброметрия активно используется как средство неразрушающего контроля для поиска дефектов в различных конструкциях, чему уделено немалое количество работ, например [18, 19]. В этих работах исследуется поведение относительно простых конструкций при внесении в них искусственных дефектов с помощью разных методов: модального анализа или анализа передаточных функций. Использование лазерного виброметра для этих методов, как правило, не является принципиальным моментом, без которого метод невозможно реализовать. Приведем пример способа локализации дефекта, который без лазерного виброметра не реализуем. В лопатку турбины массой около 0.8 кг внесен искусственный дефект – пропил на электроэрозионном станке длиной около 10 мм и шириной в микроны (рис. 5а). Цель диагностики – локализовать дефект.
Рис. 5.
Поиск дефектов лопатки турбины: а – лопатка с дефектом, б – форма колебаний неповрежденной лопатки на частоте 6524 Гц, в – форма колебаний поврежденной лопатки на частоте 6086 Гц, г – результат работы алгоритма корректировки (темным выделены элементы, у которых была уменьшена жесткость).
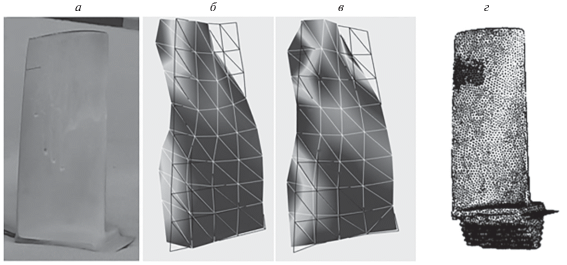
Измерения проводились для поврежденной и неповрежденной лопатки. Вибрации лопатки возбуждались электродинамическим возбудителем с полосовым шумом в диапазоне от 100 Гц до 10 кГц. Колебания лопатки измерялись в наборе из 45 точек – рис. 5б и 5в.
Значения собственных частот поврежденной лопатки уменьшились по сравнению с неповрежденной лопаткой: с ростом частоты заметны и изменения форм колебаний, особенно в районе поврежденной кромки (сравните рис. 5б, 5в измеренные для частоты 6 кГц). Однако в явном виде размеры дефекта и его расположение по формам колебаний определить невозможно.
Для поиска дефекта была построена КЭМ лопатки, состоящая из примерно 80 тысяч элементов. В процессе корректировки КЭМ по алгоритму [17] расчетным значениям собственных частот ставились в соответствие экспериментальные данные для лопатки с дефектом. Без прямого измерения форм колебаний такое сопоставление невозможно. В результате работы алгоритм определил элементы КЭМ, у которых должна быть понижена жесткость для того, чтобы результаты расчета совпали с экспериментом на поврежденной лопатке (рис. 5г). Расположение этих элементов хорошо совпадают с местом и размером дефекта (сравните рис. 5а и 5г). Обеспечить необходимую точность и повторяемость эксперимента контактными измерениями практически невозможно.
Список литературы
Yeh Y., Cummins H.Z. // Appl. Phys. Lett. 1964. V. 4. № 10. P. 176.
Rothberg S.J., Allen M.S., Castellini P. et al. // Opt. Lasers Engin. 2017. V. 99. P. 11.
Huber A.M., Ball G.R., Veraguth et al. // Otology Neurotology. 2006. V. 27. № 8. P. 1104.
Vanlanduit S., Prezniak F., Longo R. et al. // AIP Conf. Proc. 2010. V. 1253. № 1. P. 123.
Chijioke A., Lawall J. // Cryogenics. 2010. V. 50. № 4. P. 266.
Martarelli M., Santolini C., Sassaroli A. // Proc. IMAC-XXVII. V. 2. (Orlando, 2009). P. 840.
Leirset E., Engan H.E., Aksnes A. // Opt. Expr. 2013. V. 21. № 17. P. 19900.
Maynard J.D., Williams E.G., Lee Y. // J. Acoust. Soc. Am. 1985. V. 78. № 4. P. 1395.
Shah P., Vold H., Yang M. // Proc. 17th AIAA/CEAS Aeroacoust. Conf. (Portland, 2011). Art. № 2011–2772.
Salin M.B., Kosteev D.A. // ArXiv: 1812.03826. 2018.
Todoroff D.G., Trivett D.H. // J. Acoust. Soc. Am. 1986. V. 79. № 1. P. 85.
Leclère Q., Laulagnet B. // Appl. Acoust. 2008. V. 69. № 4. P. 302.
Leclère Q., Laulagnet B. // J. Acoust. Soc. Am. 2009. V. 126. № 3. P. 1245.
Ranjbar M., Marburg S. // Int. J. Mech. Sci. 2013. V. 1. № 3. P. 64.
Kim S.Y. Topology design optimization for vibration reduction: reducible design variable method. PhD thesis. Kingston: Queen’s University. 2011.
Carletti E., Miccoli G. // Proc. of ICSV21. V. 1 (Beijing, 2014). P. 425.
Суворов А.С., Соков Е.М., Вьюшкина И.А. // Акуст. журн. 2016. Т. 62. № 5. С. 592; Suvorov A.S., Sokov E.M., V’yushkina I.A. // Acoust. Phys. 2016. V. 62. № 5. P. 592.
Waldron K., Ghoshal A., Schulz M.J. et al. // Finite Elem. Analys. Design. 2002. V. 38. № 3. P. 193.
Khan A.Z., Stanbridge A.B., Ewins D.J. // Proc. SPIE. 1998. V. 3411. Art. № 449.
Дополнительные материалы отсутствуют.
Инструменты
Известия РАН. Серия физическая