Химическая физика, 2020, T. 39, № 5, стр. 16-22
Изучение горения газогенераторных составов с добавками углеродных порошков
С. Турсынбек 1, 2, В. Е. Зарко 3, *, О. Г. Глотов 3, А. Б. Кискин 3, М. А. Корчагин 4, З. А. Мансуров 1, 2, Г. С. Суродин 3, К. А. Умбеткалиев 1, 2
1 Казахский национальный университет им. ал-Фараби
Алматы, Казахстан
2 Институт проблем горения
Алматы, Казахстан
3 Институт химической кинетики и горения им. В.В. Воеводского Сибирского отделения
Российской академии наук
Новосибирск, Россия
4 Институт химии твердого тела и механохимии Сибирского отделения
Российской академии наук
Новосибирск, Россия
* E-mail: vez41@mail.ru
Поступила в редакцию 01.03.2019
После доработки 31.05.2019
Принята к публикации 20.09.2019
Аннотация
При проведении взрывных работ в условиях плотной городской застройки и в процессе добычи штучного камня возникает вопрос об организации щадящих режимов разрушения, что требует использования пиротехнических составов, работающих в режиме дефлаграции. В таких составах в качестве окислителя применяются перхлорат аммония, аммиачная селитра и другие нитраты. В качестве горючего часто используется магний. В настоящей работе изучено горение трехкомпонентной смеси нитрата натрия, магния и углерода. Последний получали путем карбонизации скорлупы грецкого ореха либо при измельчении углеродного адсорбента из фильтра противогаза. Проведены термодинамические расчеты горения и измерены характеристики горения смеси NaNO3/Mg/C с соотношением компонентов (60/20/20).
ВВЕДЕНИЕ
В процессе добычи штучного камня и при разрушении бетонных и кирпичных строений в условиях плотной городской застройки очень важным является вопрос безопасности и эффективности проведения работ. Повышение эффективности разрушения строений для получения транспортабельных кусков сопровождается увеличением количества и дальности разлета мелких осколков. Также наблюдается рост интенсивности сейсмовзрывных (СВ) и ударных воздушных (УВ) волн.
Для того чтобы снизить бризантное воздействие при взрывных работах, используют различные методы и средства. В настоящее время при извлечении блочного камня используются вещества, способные создавать давление в шпуре за счет реакции горения в дефлаграционном режиме [1].
В последние годы наблюдается увеличение мощности взрывов на горнодобывающих предприятиях. По данным инструментальных наблюдений и ощущениям жителей городов, расположенных вблизи карьеров, взрывы по своему эффекту сравнимы с землетрясением. Последствия таких взрывов проявляются в падении дымовых труб, балок перекрытий зданий и сооружений, отслоении штукатурки, расслоении фундаментов, появлении новых и раскрытии существующих трещин.
Вопросы эффективности и безопасности проведения таких работ зачастую находятся в противоречии между собой. Так, повышение эффективности разрушения (получение кусков нужных размеров), как правило, сопровождается ростом количества трещин и мелких осколков, увеличением дальности их разлета и интенсивности УВ и СВ волн. Для снижения вредного действия взрыва при щадящем взрывании используются различные методы и средства, например заряды рыхления с пониженными удельными расходами взрывчатых веществ (ВВ), а также конструкции зарядов мягкого нагружения с воздушными радиальными зазорами и зазорами, заполненными инертными средами.
Известны [2] газогенераторные патроны NoneX, используемые в качестве недетонационных пиротехнических средств для разрушения горных пород и искусственных преград. В этих составах в качестве окислителя применяется аммиачная селитра в смеси с бездымным порохом. Такие заряды работают в режиме дефлаграции, не создают ударных волн и дробления. Пиротехнические составы, работающие в режиме дефлаграции, применяются для разрушения различных конструкций без создания УВ и СВ волн, не образуют пыли и являются безопасными по сравнению с обычными ВВ, работающими в режиме взрыва или детонации.
С целью исключения бризантного действия взрыва при разрушении массива горных пород были созданы устройства (газогенераторы) на основе композиций хлората натрия с полиэтиленом. Физико-химическое превращение в этих устройствах происходит не в детонационном режиме, как у обычных ВВ, а в дефлаграционном [3]. Такой режим горения резко снижает бризантное (дробящее) действие и практически исключает создание УВ и СВ волн. Применение газогенераторов накладывает определенные ограничения на их использование: обязательное наличие плотной забойки шпура песком (гранитным отсевом) и обеспечение при бурении такой глубины шпура, при которой продукты горения удерживаются в его полости. Первое связано с тем, что давление, развиваемое при горении композиции газогенератора, может формироваться только в замкнутом объеме. Величина этого давления зависит в основном от состава и массы заряда газогенератора, а также от прочности разрушаемого материала. Второе условие связано как с величиной давления, развиваемого при горении, так и с темпом его роста, и определяется величиной сил трения забойки о стенки шпура. Для оценки границ использования газогенераторов проведены исследования полноты процесса горения композиций в зависимости от состава заряда.
Один из основных способов сделать пиротехнику более экологичной – исключение компонентов тяжелых металлов, присутствующих в традиционных пиротехнических композициях. Считается, что “зеленая” пиротехника для военного или гражданского использования должна избегать использования тяжелых металлов и перхлоратов [4]. Достаточно часто для генерации газов используют нитроцеллюлозные пороха, а также взрывчатые вещества с высоким содержанием азота, такие как нитрат аммония, нитрат гуанидиния и нитрогуанидин. Преимущественное применение нитрата аммония в газогенераторных составах обусловлено, в частности, тем, что он является дешевым и недефицитным продуктом и при сгорании не дает твердых веществ [5].
Альтернативой нитрату аммония служит нитрат натрия в качестве наиболее доступного и безопасного окислителя. При этом горючим компонентом в газогенерирующих композициях может служить углерод, дешевизна которого обусловлена применением для его получения вторичного растительного сырья либо использованием продуктов утилизации противогазных адсорбентов.
Углеродные материалы, полученные на основе вторичного растительного сырья, находят широкое применение в различных отраслях промышленности, где они используются как катализаторы и адсорбенты. Эти материалы могут найти применение и в пиротехнике при создании газообразующих систем. Для получения углерода из скорлупы грецкого ореха ее измельчают и просеивают через сита, получая дробленые фракции диаметром 2–4 мм. Для химической активации образцы скорлупы грецкого ореха пропитывали 80%-ной фосфорной кислотой в различных пропорциях и высушивали при 160 °С в течение 12 ч в муфельной печи. Полученную смесь подвергают пиролизу в химическом стакане, помещенном в муфельную печь при 500 °С. Обугленные скорлупы затем промывают при кипячении в дистиллированной воде до нейтрального рН. На стадии карбонизации формируется каркас активированного угля с высокой пористостью и прочностью. Технология приготовления углерода из скорлупы грецкого ореха подробно описана в работе [6].
Дополнительно в данной работе использовался активированный уголь в виде продукта утилизации противогазных адсорбентов. Методика активации древесного угля разработана в 1916 г. русским ученым Т.Е. Ловицем. В том же году был разработан противогаз на основе активированного угля. Высокая адсорбционная способность активированного угля объясняется сильно развитой поверхностью последнего. Суммарная поверхность пор, имеющихся в 1 г такого угля, составляет от 300 до 1000 м2. Такая огромная удельная площадь обуславливает возникновение большого избытка поверхностной энергии на границе уголь–газ [7].
В настоящей работе поставлена цель исследовать влияние углеродных порошков различной природы на горение газогенераторных составов на основе нитрата натрия и магния. Предварительно был проведен термодинамический анализ процессов газификации многокомпонентных составов с использованием программной системы TERRA для моделирования фазовых и химических равновесий [8]. Методическую основу расчета составляют фундаментальные законы термодинамики совместно с законами сохранения массы, энергии и заряда. Программа TERRA сопряжена с базой данных по свойствам индивидуальных веществ (около 3500 веществ в газообразном, ионизированном и конденсированном состояниях), что позволяет рассматривать системы, содержащие одновременно до 25 химических элементов. Учитываемые в расчетах конденсированные соединения и компоненты газовой фазы автоматически выбираются из базы данных, и программа позволяет проводить вычисления, рассматривая одновременно до 200 конденсированных и до 500 газообразных веществ в качестве возможных компонентов задаваемого равновесного состояния [9]. Для нахождения оптимального соотношения между окислителем (NaNO3) и горючим (Mg + С) были проведены систематические расчеты равновесных термодинамических характеристик при вариации состава смеси.
Для того чтобы более полно оценить характеристики исследуемых смесей, проведены экспериментальные измерения скорости горения, температуры пламени и состава продуктов горения для двух типов углеродов. Измерения проведены на воздухе с целью получения предварительной информации о возможности осуществления режима послойного горения на выбранных составах. Планируется проведение аналогичных измерений при повышенных давлениях.
ЭКСПЕРИМЕНТАЛЬНАЯ ЧАСТЬ
Для приготовления исходных смесей состава NaNO3 + Mg + C использовались порошок нитрата натрия технического (ГОСТ 19906-74), а также порошок магния марки МПФ-3 и частицы углерода, полученные из противогаза или скорлупы грецкого ореха.
Гранулометрический анализ фракций проводили с использованием проекционного микроскопа и полуавтоматического 24-канального счетного устройства. В качестве препарата использовали либо всю фракцию, либо выборку, взятую квартованием.
Образцы углерода были размельчены и рассеяны на ситах; в опытах в основном использовалась фракция размером 100–200 мкм. Готовые для сжигания смеси помещали в бумажные гильзы диаметром 1.3 см. Масса образца составляла 4.0 г, насыпная плотность образцов – 0.8–0.9 г/см3. Процесс горения регистрировался видеокамерой с частотой 300 кадр/с. Для обработки видеозаписи использовали программу VirtualDub.
Из порошкообразных компонентов готовили образцы для сжигания на воздухе. Компоненты взвешивали на электронных весах “Сартогосм” МВ 210-А и перемешивали вручную в фарфоровой ступке. Результаты обработки измерений для частиц магния, нитрата натрия и углерода из противогаза приведены на рис. 1.
Скорость горения составов измеряли методом перегорающих проволок. Для ее измерений были приготовлены образцы диаметром 13 мм и высотой 25 мм. Компоненты тщательно перемешивали и засыпали в бумажную гильзу. Минимальное уплотнение обеспечивалось постукиванием гильзы, при этом достигалась относительная плотность смеси, равная 0.55. Опыты проводили при атмосферном давлении на открытом воздухе.
Горение инициировалось пламенем газовой горелки с верхнего открытого торца бумажной гильзы, на который помещали пиротехническую намазку, состоящую из перхлората аммония и полимера HTPB (hydroxyl terminated polybutadiene). Для измерения температуры в волне горения использовали вольфрам-рениевые термопары (ВР5/ВР20) диаметром 100 мкм, закрепленные в образце на фиксированном расстоянии друг от друга, что давало дополнительную информацию о скорости горения. Сигналы термопар подавались на аналого-цифровой преобразователь ЛА-2USB-14 и далее – на компьютер. Блок-схема установки для измерения скорости горения представлена на рис. 2.
Рис. 2.
Блок-схема установки для измерения скорости горения методом перегорающих проволок: 1 – образец в бумажной оболочке, 2 – резистор, 3 – светодиодные лампочки.
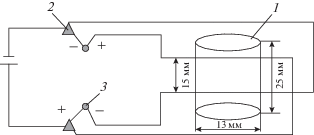
Состав исходных реакционных смесей и продуктов их горения исследовали с помощью рентгенофазового анализа (РФА). Рентгенограммы снимали на дифрактометре ДРОН-4,0 в Cu(Kα)-излучении.
РЕЗУЛЬТАТЫ И ИХ ОБСУЖДЕНИЕ
Результаты термодинамического расчета параметров различных составов приведены в табл. 1. Предварительные эксперименты показали, что при малом содержании углерода горение смеси происходит с высокой скоростью в конвективном пульсирующем режиме. Равномерное распространение пламени зарегистрировано в волне горения смеси NaNO3/Mg/C состава 60/20/20, который был выбран в качестве рабочего. Этот состав имеет достаточно высокие значения газопроизводительности и параметра RgT, характеризующего работоспособность смеси.
Таблица 1.
Основные параметры термодинамического расчета различных составов при разных соотношениях компонентов NaNO3/Mg/C
Состав | P, МПа | T, K | V, м3/кг ∙ K | Rg, Дж/кг | Z | RgT, Дж/кг |
---|---|---|---|---|---|---|
90/10 (без углерода) | 0.1 | 1634 | 2.27 | 268.59 | 0.48 | 438 874 |
85/10/5 | 0.1 | 2033 | 3.62 | 276.55 | 0.36 | 562 232 |
80/10/10 | 0.1 | 2254 | 4.9 | 260.8 | 0.16 | 587 843 |
75/10/15 | 0.1 | 2682 | 5.96 | 256.6 | 0.16 | 712 339 |
70/15/15 | 0.1 | 2857 | 6.22 | 281.07 | 0.26 | 803 020 |
65/20/15 | 0.1 | 2924 | 6.3 | 294.04 | 0.27 | 859 987 |
60/20/20 | 0.1 | 1954 | 4.8 | 314.43 | 0.22 | 614 705 |
Исследованные составы:
состав № 1: | 60% – NaNO3 технический, |
20% – Mg марки МПФ-3, | |
20% – C из противогаза; | |
состав № 2: | 60% – NaNO3 технический, |
20% – Mg марки МПФ-3, | |
20% – C из скорлупы грецкого ореха. |
Для определения зависимости скорости горения от размера частиц углерода были приготовлены образцы с разной дисперсностью углеродных частиц. Результаты приведены в табл. 2.
Таблица 2.
Зависимость скорости горения смеси состава 60/20/20 от дисперсности частиц углерода
Размер частиц углерода, мкм | u, мм/с | |
---|---|---|
состав № 1 | состав № 2 | |
Ниже 70 | не горит | не горит |
70–100 | 0.5–1 | 0.7–1.5 |
100–200 | 1.7–2.1 | 4.5–5.0 |
Выше 200 | >10 | >15 |
Обработка экспериментальных данных позволила определить диапазон устойчивости процесса горения изучаемой системы и определить максимальные значения линейных скоростей горения в зависимости от размера частиц углерода. Как видно из табл. 2, при малых размерах частиц углерода смесь не удается устойчиво воспламенить, а с увеличением их размера скорость горения смеси возрастает. Такое поведение скорости горения может быть следствием того, что при заданном соотношении компонентов (содержание углерода – 20%) и малых размерах частиц углерода смесь трудногорючая, а при увеличении размеров последних эффективная поверхность контакта уменьшается, и смесь превращается в горючую. Вместе с тем наличие зависимости скорости горения от размера частиц углерода обеспечивает возможности целенаправленного регулирования величины последней для удовлетворения требований конкретных технических заданий.
Измерения температуры в газовой фазе над поверхностью образца проводили с помощью вольфрам-рениевой термопары, установленной на высоте 1 см от образца; эксперимент повторяли 3–4 раза. На рис. 3 и 4 показаны записи температуры в пламени смеси составов № 1 и № 2 соответственно. Начальный отрезок на термограммах соответствует зажиганию и горению воспламенительного состава. В случае смесей состава № 1 температура в пламени достигает ~1400 К. Это приблизительно на 500 К ниже ее значения, полученного в результате термодинамического расчета. В случае смесей состава № 2 температура в пламени близка к термодинамически рассчитанной. Можно полагать, что в последнем случае полнота горения в газовой фазе более высокая, что обусловлено большей удельной поверхностью и более высокой реакционной способностью углерода, полученного из скорлупы грецкого ореха. Неравномерность хода температурной кривой объясняется тем, что смесь была крупнозернистой и насыпной плотности.
Результаты рентгенофазового анализа конденсированных продуктов горения смесей составов № 1 и № 2 показаны на рис. 5 и 6 соответственно. По данным РФА основными фазами в продуктах горения исследуемой смеси являются оксид магния и карбонат натрия. Однако регистрируется также непрореагировавший исходный окислитель – нитрат натрия, причем на качественном уровне его содержание в продуктах горения состава № 1 более высокое, чем в случае состава № 2. Это объясняется тем, что в процессе горения за счет выделеления газовых продуктов происходит частичное диспергирование исходных компонентов в волне горения, наиболее выраженное в случае углерода из противогаза.
ВЫВОДЫ
1. Проведены тесты на воспламеняемость и способность к послойному горению смесей и термодинамические расчеты параметров горения для определения оптимального соотношения исходных компонентов. Установлено, что высокая работоспособность и равномерность горения наблюдаются при соотношении исходных компонентов NaNO3/Mg/C 60/20/20.
2. Измерены скорости горения на воздухе для смесей с различным типом и разными размерами частиц углерода (из противогаза и из скорлупы грецкого ореха). Установлено, что скорость горения составляет 2–5 мм/с. При этом скорость горения состава на основе углерода из скорлупы грецкого ореха приблизительно вдвое выше, чем в случае углерода из противогаза, а температура пламени при горении этого состава выше приблизительно на 500 К.
3. Определена дисперсность частиц углерода, обеспечивающая послойное горение заряда. Она соответствует размерам частиц в интервале 100–200 мкм.
4. Проведен рентгенофазовый анализ твердых продуктов горения. Показано, что основными продуктами являются оксид магния и карбонат натрия.
5. Разработанные газогенераторные составы на основе нитрата натрия, магния и углерода планируются для дальнейшего исследования с целью применения их в зарядах дефлаграционного горения, предназначенных для раскалывания в щадящем режиме блочного камня или разрушения твердых минеральных пород. Для этого подготовлены устройства и регистрирующая аппаратура для измерения динамики роста давления в шпуре при горении газогенераторного состава.
Список литературы
Кирсанов О.Н., Островский В.И., Румянцев В.Н., Парамонов Г.П., Виноградов Ю.И. // Технология орган. и неорган. веществ. 2005. Т. 82. № 6. С. 278.
Парамонов Г.П. // Физические проблемы разрушения горных пород. Сб. тр. Третьей междунар. научн. конф. М.: Ин-т проблем компл. освоения недр РАН, 2003. С. 265.
Парамонов Г.П., Ковалевский В.Н. // Горный журн. Казахстана. 2013. №1. С. 39.
Березуев Ю.А., Евграфов Л.В., Кундышев М.В. // Вестн. КДПУ им. М. Остроградского. 2007. № 5. С. 101.
Andrew W.C. Dissertation Master of Engineering. Pretoria: University of Pretoria, 2017.
Azat S., Rosa Busquets, Pavlenko V.V. et al. // Appl. Mech. and Mater. 2014. V. 467. P. 49.
Габрук Н.Г., Олейникова И.И., Шутеева Т.А., Смальченко Д.Е. // Научные ведомости. БелГУ. Серия: Естественные науки. 2013. № 7(160). С. 114.
Трусов Б.Г. // Матер. III междунар. симпоз. “Горение и плазмохимия”. Алматы: Казахский нац. ун-т им. аль-Фараби, 2005. С. 52.
Трусов Б.Г. // Инженерный журн.: наука и инновации. 2012. № 1(1). С. 21.
Дополнительные материалы отсутствуют.
Инструменты
Химическая физика