Химическая физика, 2023, T. 42, № 3, стр. 16-22
Конверсия продуктов газификации древесины методом парциального окисления воздухом
В. М. Кислов 1, *, Ю. Ю. Цветкова 1, Е. Н. Пилипенко 1, М. А. Репина 2, М. В. Салганская 1
1 Институт проблем химической физики Российской академии наук
Черноголовка, Россия
2 Сахалинский государственный университет
Южно-Сахалинск, Россия
* E-mail: vmkislov@icp.ac.ru
Поступила в редакцию 19.07.2022
После доработки 13.08.2022
Принята к публикации 20.09.2022
- EDN: LYHAIU
- DOI: 10.31857/S0207401X2303007X
Аннотация
Экспериментально исследованы различные способы получения горючего газа с низким содержанием смолы при газификации древесины в сверхадибатических режимах: посредством добавления катализаторов к газифицируемому топливу, окислительной конверсии продуктов газификации древесины и совместного использования двух вышеназванных способов. Установлено, что при конверсии продуктов каталитической газификации древесины возможно получение бессмольного горючего газа, который может быть использован в энергетике, но он непригоден для химического синтеза.
ВВЕДЕНИЕ
Биомасса является перспективным источником получения энергии и химических продуктов вследствие ее возобновляемости, низкого содержания вредных веществ и климатической нейтральности. Вместе с тем в исходном виде древесина мало пригодна для использования в крупномасштабных энергетических устройствах и химической промышленности. Более перспективным способом использования биомассы является превращение ее в газообразные продукты, например, путем газификации или пиролиза [1–4].
Качество образующихся газообразных продуктов (состав, содержание примесей) зависит от вида и влажности биомассы, а также от выбранного метода и режимных факторов газификации. Тем не менее в образующихся продуктах газификации, наряду с газообразными соединениями (CO2, CO, H2, N2), всегда присутствуют пары́ воды, а также органические продукты пиролиза твердых топлив (смолы). Использовать продукт-газ, содержащий значительное количество смол (до 500 г/м3) [5], без его очистки можно только в топках паровых или водогрейных котлов, имеющих низкую энергетическую эффективность [6–9].
Одним из перспективных способов получения свободных от смол газообразных продуктов при термической переработке биомассы или других топлив (в том числе отходов) является использование катализаторов [10–14]. Другой перспективный способ – конверсия методом парциального окисления газообразных [15, 16] и жидких углеводородов [17, 18], образующихся при термическом разложении различных органических топлив [19–21]. В качестве окислителя, как правило, используют воздух, кислород, водяной пар, а также паровоздушные или парокислородные смеси.
В литературе имеется большое количество различных работ, посвященных получению горючего бессмольного газа путем конверсии методом парциального окисления смол, образующихся при термическом разложении древесины. Приведены различные схемы осуществления конверсии, определены оптимальные температурные режимы и описаны особенности окисления и крекинга различных содержащихся в смолах отдельных компонентов [22–24]. Общим недостатком реализации подобных схем является необходимость использования дополнительных затрат энергии для поддержания достаточно высоких температур, необходимых для осуществления эффективного преобразования смол в горючие газообразные продукты. Вместе с тем термодинамические расчеты показывают возможность конверсии продуктов газификации древесины в бессмольный газ без дополнительных затрат энергии [25].
Наши эксперименты [25–27] показали, что, несмотря на значительное (примерно в 10 раз) снижение содержания смолы в газообразных продуктах, без использования дополнительных источников энергии ни один из этих способов взятый в отдельности не позволяет получить газообразные продукты с содержанием смолы менее 0.1 об.%. В связи с этим для получения бессмольного горючего газа представляется целесообразным использовать комбинацию указанных методов. Цель настоящей работы – исследование способов получения бессмольного газа путем окислительной конверсии продуктов газификации древесины без добавок и древесины, пропитанной катализатором (K2СО3).
МЕТОДИКА ЭКСПЕРИМЕНТА
Эксперименты проводили в кварцевом реакторе периодического действия, принципиальная схема которого показана на рис. 1. В реактор загружали сухие кубики сосновой древесины с длиной ребра 5–10 мм в одних экспериментах в исходном виде (без добавок), в других – c катализатором K2CO3, внесенным в древесину путем пропитки с последующей сушкой.
Рис. 1.
Принципиальная схема экспериментальной установки: 1 – реактор, 2–12 – термопары, 13 – инициатор с нагревающей спиралью, 14 – конвертор продукт-газа, 15 – воздухопровод конвертора, 16 – электроспираль воспламенения продуктов газификации, 17, 18 – расходомеры, 19 – теплоотражающий экран, 20 – нижний фланец, 21 – ампула для отбора проб.
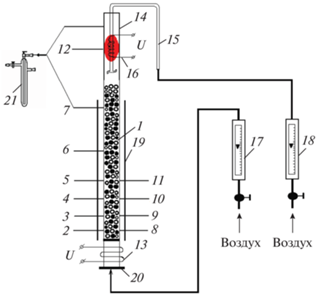
Конверсию продуктов газификации исследуемых образцов проводили методом парциального окисления. В качестве окислителя использовали воздух. Конвертором служила верхняя часть кварцевой трубы газификатора, для чего туда подавали необходимое количество воздуха. В ходе эксперимента с помощью хромель-алюмелевых термопар регистрировали профили температур в пяти сечениях реактора и измеряли температуру в конверторе, отбирали пробы газообразных продуктов из реактора и конвертора, измеряли расходы воздуха в реактор и конвертор. Расход подаваемого воздуха в реактор был постоянным и составлял 0.24 л/с, расход воздуха в конвертор варьировали от 0.30 до 0.65 л/с. После эксперимента твердые продукты сгорания выгружали, взвешивали и определяли содержание в них недогоревшего углерода путем прокаливания. Более подробно методика проведения экспериментов по газификации твердых топлив в режиме фильтрационного горения описана в работе [28], методика пропитки катализатором и определение содержания К2СО3 в древесине представлены в работе [25].
В ходе эксперимента расходы воздуха в газификатор и конвертор контролировали с точностью до 0.01 л/с с помощью электронных расходомеров Mass-View модели MV-306. Показания стандартных хромель-алюмелевых термопар (ГОСТ 3044-84) регистрировали с помощью АЦП и компьютера. Пробы исходных продуктов газификации и продуктов конверсии одновременно отбирали в специальные пробоотборники, и после эксперимента состав отобранных проб анализировали с помощью газового хроматографа Кристалл-5000. Относительная погрешность определения концентраций газов составляла не более 2%.
Определение содержания пиролизных смол, как в продуктах газификации, так и продуктах конверсии, непосредственно в процессе эксперимента затруднительно. Результаты предыдущих работ [25, 29] показали, что для точного определения содержания смол в продуктах газификации их следует полностью осадить и разделить полученные жидкие продукты пиролиза на отстойные смолы и водный раствор. Чем больше смолы будет осаждено, тем полученный результат будет точнее. Стадия конверсии в этом случае становится невозможна.
Остаточное содержание смол в продуктах конверсии невелико. После их охлаждения значительная часть оставшихся в них жидких компонентов (смол и воды) продуктов оседает на стенках соединительных трубок и пробоотборников, что существенно искажает полученный результат. Более надежным способом определения среднего количество смол и их элементного состава является расчет материального баланса процесса, составленного на основе полученных экспериментальных данных.
При составлении материального баланса используются результаты анализа влажности и элементного состава сухой древесины и образующейся из нее смолы, а также данные, полученные в ходе эксперимента: массовая скорость газификации, расходы воздуха в газификатор и конвертор, выход и состав газообразных компонентов (на каждой из стадий). Считается, что поступающий с воздухом азот в реакциях не участвует. Схематично материальный баланс газификации записывали следующим образом:
A[C1H1.52O0.65]древесина + X[H2O]влага + B([O2] + + 3.76[N2])воздух 1 = (3.76B[N2] + [CdOeHf])газ 1 + + Y[H2O]пар 1 + [CnHmOk]смола 1.
Схему материального баланса конверсии выражали в виде
(3.76B[N2] + [CdOeHf])газ + Y[H2O]пар 1 + + [CnHmOk]смола + Z([O2] + 3.76[N2])воздух 2 = = (3.76(B + Z)[N2] + [Cd2Oe2Hf2])газ 2 + + Y2[H2O]пар 2 + [Cn2Hm2Ok2]смола 2,
где A, X, B, Y, Z, Y2 – стехиометрические коэффициенты брутто-реакции конверсии; d, e, f, n, m, k, d 2, e 2, n 2, m 2, k 2 – стехиометрические индексы брутто-формул компонентов конверсии.
Составляли поэлементные уравнения баланса углерода, водорода, кислорода и азота, входящих в реактор в виде древесины и воздуха, и выходящих из него в виде газообразных продуктов, смолы и воды. Массовый суммарный выход жидких продуктов (смолы и воды) рассчитывали из баланса компонентов по разности; определение содержания в них смолы и воды проводили исходя из известного их состава. Содержание компонентов в газообразных продуктах определяли по данным газового анализа.
Согласно результатам, представленным в работах [25, 29], расхождение между результатами расчета выхода смол при газификации различных твердых топлив и экспериментальными данными их прямого определения не превышает 10%. Результаты расчета материального баланса данных экспериментов также подтверждают эти оценки.
В качестве основного параметра, управляющего конверсией, использовали количество воздуха, подаваемого в конвертор. Под коэффициентом избытка воздуха, подаваемого для конверсии, понимается безразмерный параметр J, рассчитываемый как отношение расхода воздуха, подаваемого в конвертор, к расходу воздуха, необходимому для полного сгорания продуктов газификации. Для исходных продуктов газификации J = 0, при их полном сгорании J = 1. Степень конверсии смол определяли как отношение массы смолы, конвертируемой в газообразные продукты, к массе смолы, поступающей в конвертор с продуктами газификации.
РЕЗУЛЬТАТЫ И ИХ ОБСУЖДЕНИЕ
При конверсии продуктов некаталитической газификации древесины максимальная концентрация горючих компонентов (CO и H2) достигается при коэффициенте J = 0.63 (рис. 2). Теплота сгорания газообразных продуктов увеличивается от 2.5 МДж/м3 (J = 0) до 4.2 МДж/м3 (J = 0.63). Максимальная степень конверсии смол при J = = 0.63 составляет примерно 85%, а общий энергетический КПД газификации по газообразным продуктам – до 60%.
Рис. 2.
Зависимость содержания газообразных соединений, образующихся при конверсии продуктов некаталитической газификации древесины (об.%), от коэффициента избытка воздуха: 1 – CO2, 2 – CO, 3 – H2, 4 – CH4.
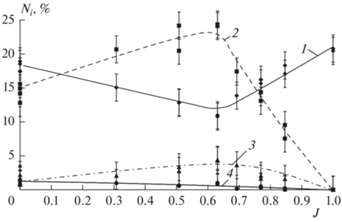
В процессе конверсии меняется не только состав и объем газообразных продуктов, но и содержание в них смолы и паров воды. Полные сведения о выходе образующихся при конверсии продуктов определены из расчетов материальных балансов процессов газификации и конверсии. На рис. 3 представлены зависимости количества образующихся в единицу времени продуктов конверсии: CO2, CO, H2, CH4, смолы (в пересчете на условную брутто-формулу С1Н1.2О0.3) и H2O при различном расходе подаваемого в конвертор воздуха. Подача в конвертор воздуха до значений коэффициента избытка воздуха, соответствующих J = 0.63, приводит к окислению значительного количества смолы (примерно 85%), увеличению выхода CO2 и значительному росту выхода CO (рис. 3). Выход H2 также несколько увеличивается. При большем расходе воздуха содержание смолы в аэрозоле уже невелико, поэтому наряду с окислением смолы также начинается окисление газообразных продуктов, что приводит к резкому снижению выхода CO и H2 и увеличению выхода CO2 и H2O.
Рис. 3.
Выход веществ, образующихся при конверсии продуктов некаталитической газификации древесины (ci, ммоль/с), при различных расходах подаваемого в конвертор воздуха: 1 – CO2, 2 – CO, 3 – H2, 4 – CH4, 5 – H2O, 6 – смола.
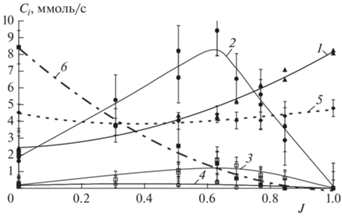
Добавка катализатора существенно влияет на состав образующихся продуктов. Ранее [25] было показано, что газификация древесины, пропитанной K2СО3, приводит к изменению состава газообразных продуктов: с увеличением содержания карбоната калия концентрация диоксида углерода и водорода растет, а моноксида углерода – снижается. Выход газообразных продуктов при этом увеличивается примерно на 30%, а выход смол значительно снижается. При газификации древесины с содержанием K2СО3 5% и выше твердые продукты сгорания, состоящие из золы и карбоната калия, начинают вспениваться, затрудняя доступ окислителя к частицам древесного угля, т.е. при увеличении содержания в древесине K2СО3 наблюдается рост доли недогоревшего углерода в твердых продуктах сгорания.
В работе [25] использовалась экспериментальная установка со смолоотделителем, при работе которой в реакторе поддерживали избыточное давление (~0.5 атм). Снижение в реакторе давления на 0.5 атм при каталитической газификации наших экспериментах привело к заметному изменению состава газообразных продуктов. Ранее при некаталитической газификации древесины, торфа, угля и других твердых топлив изменение давления на 0.5 атм практически не влияло на состав газообразных продуктов [29]. Сопоставление полученных нами в данной работе характеристик газификации и приведенных в работе [25] представлено на рис. 4 и в табл. 1. При каталитической газификации при атмосферном давлении выход газообразных продуктов ниже, а содержание в них горючих компонентов (CO и H2) выше, чем при повышенном давлении. Выход смол в обоих случаях примерно одинаков, а содержание углерода в твердых продуктах сгорания при газификации при атмосферном давлении примерно на 20% выше, чем при повышенном давлении.
Рис. 4.
Состав газообразных продуктов газификации пропитанной катализатором древесины в зависимости от содержания в ней K2СО3 (ω, %): 1 и 2 – CO2, 3 и 4 – CO, 5 и 6 – H2; сплошные линии – p = 1 атм, пунктирные – p = 1.5 атм.
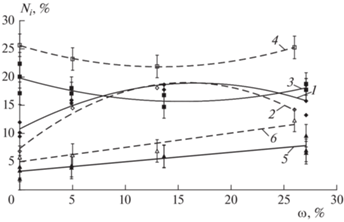
Таблица 1.
Характеристики газификации древесины, пропитанной K2СО3, при атмосферном (p = 1 атм) и повышенном (p = 1.5 атм) давлении
Содержание К2СО3, мас.% | Параметры | |||||
---|---|---|---|---|---|---|
выход газа, м3/кг древесины |
выход смол, мас.% | недогоревший углерод, мас.% | ||||
p = 1.5 атм [17] | p = 1 атм | p = 1.5 атм [17] | p = 1 атм (расчет) | p = 1.5 атм [17] | p = 1 атм | |
0 | 1.35 | 1.26 | 42.3 | 42.3 | 0 | 0 |
5 | 1.64 | 1.50 | 20.4 | 20.0–22.3 | 2.3 | 2.7 |
13 | 1.74 | 1.54 | 10.1 | 9.30–10.7 | 6.4 | 8.0 |
26.5 | 1.78 | 1.56 | 2.9 | 2.50–4.7 | 12.6 | 15.7 |
Ранее экспериментально установлено, что состав полученной смолы как при газификации древесины без катализатора, так и при использовании K2СО3 практически одинаков и (в пересчете на сухую массу) составляет: C = 67.0–67.5, H = = 6.8–7.8, O = 24.7–26.2 мас.% [25]. В данных экспериментах состав и выход образующейся смолы, рассчитанный из материального баланса газификации древесины, близок к результатам, полученным в работе [25], и соответствует приведенной ранее брутто-формуле смолы – С1H1.2O0.3.
Конверсию продуктов каталитической газификации древесины проводили аналогично конверсии продуктов некаталитической газификации древесины. Перед началом каждого эксперимента по приведенным в табл. 1 данным были рассчитаны диапазоны расходов воздуха, необходимых для парциального окисления и полного сгорания смолы, содержащейся в газообразных продуктах. На начальном этапе эксперимента расход подаваемого воздуха в конвертор был минимально необходим, а затем его постепенно увеличивали до полного исчезновения следов смол в газообразных продуктах.
Во всех экспериментах с конверсией продуктов каталитической газификации древесины расход подаваемого для конверсии воздуха, при котором в продуктах конверсии исчезали следы смолы, был выше, чем расход воздуха, необходимый для полного сжигания содержащихся в газообразных продуктах смол, и примерно соответствовал коэффициенту избытка воздуха J = 0.50.
Для достижения высокой теплоты сгорания газообразных продуктов конверсии необходимо обеспечить достаточно высокие температуры (от 700 °С и выше) и строго определенное соотношение поступающих потоков окислителя на стадиях конверсии и газификации. При газификации древесины, пропитанной K2СО3, содержание смол в продукт-газе ниже, чем при некаталитической газификации (см. табл. 1), поэтому тепла, выделяющегося при их окислении, оказывается недостаточно для нагрева и воспламенения реакционной смеси, и возникновения самоподдерживающегося процесса конверсии. Следует также учитывать отсутствие теплоизоляции конвертора, которое обуславливает высокий уровень потерь тепла через боковую стенку, поэтому на осуществление процесса требуется повышенный расход энергии.
Для повышения температуры необходимо подавать в конвертор повышенный расход воздуха для окисления не только смолы, но и частично газообразных горючих компонентов продукт-газа. При конверсии продуктов каталитической газификации в первую очередь (наряду со смолой) окисляется содержащийся в них водород (рис. 5). Содержание СО при этом также снижается.
Рис. 5.
Состав газообразных продуктов, образующихся при конверсии продуктов каталитической газификации древесины, пропитанной K2CO3 (ω, %): 1 – СО; 2 – СО2; 3 – Н2.
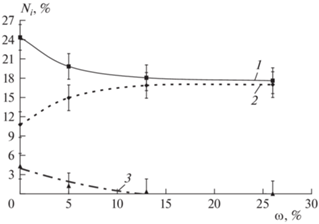
Таким образом, при конверсии продуктов каталитической газификации древесины можно получить низкокалорийный бессмольный горючий газ с теплотой сгорания примерно 2.2–2.5 МДж/м3, в котором из горючих газов имеется один CO. Подобный газ можно использовать только для получения энергии, а для использования в химической промышленности он непригоден.
ВЫВОДЫ
1. Исследована некаталитическая и каталитическая конверсия предварительно перемешанных продуктов газификации сосновой древесины и воздуха в спутном потоке.
2. Установлено, что конверсия продуктов некаталитической газификации древесины, содержащих газообразные продукты с теплотой сгорания примерно 2.5 МДж/м3 с высоким содержанием смол (более 0.3 кг/м3), позволяет за счет энергии парциального окисления смол эффективно преобразовать в горючий газ ~85% смол и увеличить теплоту сгорания газообразных продуктов до 4.2 МДж/м3.
3. Добавка к древесине до 26.5% K2CO3 в качестве катализатора существенно снижает температуру и меняет состав продуктов газификации: выход смолы снижается примерно на 90%, выход газообразных продуктов увеличивается и меняется их состав (содержание CO несколько снижается, H2 – линейно увеличивается), а в твердых продуктах сгорания появляется недогоревший углерод. Теплота сгорания газообразных продуктов при этом практически не меняется. Процесс чувствителен к изменению давления: увеличение давления примерно на 0.5 атм (50 кПа) приводит к увеличению выхода газообразных продуктов и снижению содержания в них горючих компонентов.
4. Воздушная конверсия продуктов каталитической газификации древесины с содержанием смолы 0.125 кг/м3 и менее показала, что энергии парциального окисления смол недостаточно для достижения температуры, обеспечивающей высокие скорости реакции конверсии, поэтому необходимо подавать избыточное количество воздуха, частично сжигая содержащиеся в газообразных продуктах H2 (в первую очередь) и CO.
5. Поскольку практически единственным горючим компонентом в образующемся при конверсии низкокалорийном горючем газе (2.2–2.5 МДж/м3) является CO, то такой газ может быть использован только в энергетике, и абсолютно не пригоден для химического синтеза.
Исследование выполнено в рамках госзадания № 0089-2019-0018, номер государственной регистрации АААА-А19-119-022690098-3.
Список литературы
Heidenreich S., Foscolo P.U. // Prog. Energy Combust. Sci. 2015. V. 46. P. 72; https://doi.org/10.1016/j.pecs.2014.06.002
Sansaniwal S.K., Pal K., Rosen M.A., Tyagi S.K. // Renewable Sustainable Energy Rev. 2017. V. 72. P. 363; https://doi.org/10.1016/j.rser.2017.01.038
Watson J., Zhang Y., Si B., Chen W. T., Souza R. // Ibid. 2018. V. 83. P. 1; https://doi.org/10.1016/j.rser.2017.10.003
Orihuela M.P., Espinoza L., Ripoll N., Chacartegui R., Toledo M. // Energy Convers. Manage. 2021. V. 233. P. 113 901; https://doi.org/10.1016/j.enconman.2021.113901
Кислов В.М., Цветков М.В., Зайченко А.Ю., Подлесный Д.Н., Салганский Е.А. // Хим. физика. 2021. Т. 40. № 9. С. 27; https://doi.org/10.31857/S0207401X21090053
Woolcock P.J., Brown R.C. // Biomass Bioenergy. 2013. V. 52. P. 54; https://doi.org/10.1016/j.biombioe.2013.02.036
Asadullah M. // Renewable Sustainable Energy Rev. 2014. V. 40. P. 118; https://doi.org/10.1016/j.rser.2014.07.132
David E., Kopač J. // Renewable Energy. 2021. T. 171. P. 1290; https://doi.org/10.1016/j.renene.2021.02.110
Chen Y., Wang Y., Pezzola L., Mussi R., Bromberg L. et al. // Biomass Bioenergy. 2021. V. 149. P. 106085; https://doi.org/10.1016/j.biombioe.2021.106085
Yu J., Guo Q., Gong Y. et al. // Fuel Process. Technol. 2021. V. 214. P. 106723; https://doi.org/10.1016/j.fuproc.2021.106723
Xie Q., Kong S., Liu Y., Zeng H. // Bioresour. Technol. 2012. V. 110. P. 603; https://doi.org/10.1016/j.biortech.2012.01.028
Ren J., Cao J.P., Zhao X.Y., Yang F.L., Wei X.Y. // Renewable Sustainable Energy Rev. 2019. V. 116. P. 109 426; https://doi.org/10.1016/j.rser.2019.109426
Ren J., Liu Y.L., Zhao X.Y., Cao J.P. // J. Energy Inst. 2020. V. 93. P. 1083. https://doi.org/10.1016/j.joei.2019.10.003
Kan T., Strezov V., Evans T. et al. // Renewable Sustainable Energy Rev. 2020. V. 134. P. 110 305. https://doi.org/10.1016/j.rser.2020.110305
Салганский Е.А., Цветков М.В., Зайченко А.Ю., Подлесный Д.Н., Седов И.В. // Хим. физика. 2021. Т. 40. № 11. С. 14; https://doi.org/10.31857/S0207401X2111008X
Цветков М.В., Кислов В.М., Цветкова Ю.Ю. и др. // Хим. физика. 2022. Т. 41. № 8. С. 93; https://doi.org/10.31857/S0207401X22080143
Podlesniy D., Zaichenko A., Tsvetkov M., Salganskaya M., Chub A., Salgansky E. // Fuel. 2021. V. 298. P. 120 862; https://doi.org/10.1016/j.fuel.2021.120862
Зайченко А.Ю., Подлесный Д.Н., Цветков М.В., Салганская М.В., Чуб А.В. // ЖПХ. 2019. Т. 92. № 2. С. 245; https://doi.org/10.1134/S0044461819020166
Тереза А.М., Агафонов Г.Л., Андержанов Э.К. и др. // Хим. физика. 2020. Т. 39. № 8. С. 58; https://doi.org/10.31857/S0207401X20080129
Тереза А.М., Агафонов Г.Л., Андержанов Э.К., Медведев С.П. // Хим. физика. 2021. Т. 40. № 8. С. 56; https://doi.org/10.31857/S0207401X21080136
Тереза А.М., Агафонов Г.Л., Андержанов Э.К. и др. // Хим. физика. 2021. Т. 40. № 12. С. 29; https://doi.org/10.31857/S0207401X21120141
Su Y., Luo Y., Chen Y., Wu W., Zhang Y. // Fuel Process. Technol. 2011. V. 92. P. 1513. https://doi.org/10.1016/j.fuproc.2011.03.013
Ahrenfeldt J., Egsgaard H., Stelte W., Thomsen T., Henriksen U.B. // Fuel. 2013. V. 112. P. 662; https://doi.org/10.1016/j.fuel.2012.09.048
Zhao S., Luo Y., Zhang Y., Long Y. // J. Anal. Appl. Pyrolysis. 2015. V. 112. P. 262; https://doi.org/10.1016/j.jaap.2015.01.016
Кислов В.М., Салганский Е.А., Цветков М.В., Цветкова Ю.Ю. // ЖПХ. 2017. Т. 90. № 5. С. 579.
Глазов С.В., Кислов В.М., Размыслов А.В., Салганская М.В. // ЖПХ. 2019. Т. 92. № 7. С. 927; https://doi.org/10.1134/S0044461819070156
Кислов В.М., Глазов С.В., Салганская М.В., Пилипенко Е.Н., Цветкова Ю.Ю. // ЖПХ. 2021. Т. 94. № 3. С. 363; https://doi.org/10.31857/S0044461821030117
Кислов В.М., Глазов С.В., Салганский Е.А., Колесникова Ю.Ю., Салганская М.В. // Физика горения и взрыва. 2016. Т. 52. № 3. С.72; https://doi.org/10.15372/FGV20160310
Salgansky E.A., Kislov V.M., Glazov S.V., Salganskaya M.V. // J. Combust. 2016. V. 2016. P. 9637082; https://doi.org/10.1155/2016/9637082
Дополнительные материалы отсутствуют.
Инструменты
Химическая физика