Химия твердого топлива, 2019, № 1, стр. 48-53
ГИДРОГЕНИЗАЦИЯ НАФТАЛИНОВЫХ ФРАКЦИЙ КАМЕННОУГОЛЬНОЙ СМОЛЫ ИЗ УГЛЯ ШУБАРКУЛЬСКОГО МЕСТОРОЖДЕНИЯ
А. С. Малолетнев 1, *, Н. Т. Смагулова 2, **, Ж. К. Каирбеков 2, ***, А. Ж. Каирбеков 2, ****, Л. К. Кудреева 2, *****
1 Горный институт НИТУ МИСиС
119049 Москва, Россия
2 ДГП НИИ Новых химических технологий и материалов
050012 Алматы, Республика Казахстан
* E-mail: anstanmal@mail.ru
** E-mail: nazym2011@inbox.ru
*** E-mail: us.niinhtm@mail.ru
**** E-mail: nazym2011@inbox.ru
***** E-mail: nazym2011@inbox.ru
Поступила в редакцию 08.06.2018
После доработки 02.08.2018
Принята к публикации 24.10.2018
Аннотация
Приведены результаты исследований по гидрогенизации нафталиновой фракции каменноугольной смолы для получения бессернистого нафталина высшего качества и высокочистого бензола для органических синтезов, а также для увеличения выхода нафталина в результате гидродеметилирования его гомологов, содержащихся в исходном сырье. Установлено, что предварительное озонирование смеси сырого коксохимического бензола и нафталиновой фракции (3:1) в течение 60 мин позволяет при последующей высокотемпературной гидрогенизации получить выход ценных химических продуктов 95–96% от перерабатываемого сырья.
Нафталиновые фракции каменноугольной (коксохимической) смолы и технические сорта нафталина являются объектами исследований, направленных на разработку условий их гидрогенизационной очистки от примесей сернистых соединений, непредельных углеводородов и других, а также на получение тетралина. Однако образующийся тетралин трудно выделить в чистом виде при его невысокой концентрации в гидрогенизате, поэтому параллельно проводятся исследования по разработке условий гидрогенизации, позволяющих очистить нафталин при минимальной глубине его гидрирования.
Исследования по гидрогенизации нафталинсодержащих продуктов (сырые нафталиновые фракции, прессовые оттеки и др.) были направлены на разработку оптимальных условий получения бессернистого нафталина и тетралина, а также на увеличение выхода нафталина в результате гидродеметилирования его гомологов, содержащихся в исходном сырье [1]. Следует отметить, что переработка прессовых оттеков КХЗ представляет определенный самостоятельный интерес, так как они не находят в настоящее время квалифицированного применения.
При высокотемпературной гидрогенизации, осуществляемой при температуре 500°С и выше, наряду с удалением серо-, кислород- и азотсодержащих соединений, интенсивное развитие получают реакции гидрокрекинга насыщенных и гидродеалкилирования ароматических углеводородов. В результате возрастает выход нафталина и его концентрация в гидрогенизатах по сравнению с сырьем, упрощается технология его выделения, в частности появляется возможность применения метода четкой ректификации для получения 99%-ного и более чистого нафталина с высокой степенью отбора от потенциала. При гидрогенизации нафталиновых фракций Запорожского КХЗ и Губахинского КХЗ (400–550°С, 5 МПа, объемная скорость подачи сырья 0.5 кг/л·ч, подача газа, содержащего 50% Н2, 1.5 м3/кг, Al–Co–Mo-катализатор, подача водяного пара 15% на сырье) были получены гидрогенизаты, содержащие 82–85% нафталина, 0.3–0.5% тетралина и 0.0031–0.0017% серы. При гидрогенизационной переработке в аналогичных условиях нафталиновой фракции смолы Новолипецкого металлургического завода выход гидрогенизата, содержащего 90.8% нафталина, 0.4% тетралина и 0.0015% серы, составлял 96.5% [1]. Было показано, что при температуре 550°С нафталин практически не гидрируется, но интенсивно протекают реакции деметилирования метилнафталинов.
В работе [2] установлено, что при каталитической гидрогенизации смеси сырого бензола и нафталиновой фракции коксохимической смолы под давлением 5 МПа (водородсодержащий газ содержал 50–55% Н2) и температуре 560–580°С над Al–Co–Mo-катализатором получают гидрогенизат для полного выделения ароматических углеводородов методом четкой ректификации.
Аналогичные результаты были получены при применении цеолитсодержащего катализатора МоНNaУ, но при более низкой температуре – 475°С [3].
В данной статье приведены результаты исследований по гидрогенизации нафталиновых фракций каменноугольной смолы полукоксования угля Шубаркульского месторождения для получения бессернистого нафталина высшего качества и высокочистого бензола для органических синтезов, а также для увеличения выхода нафталина в результате гидродеметилирования его гомологов, содержащихся в каменноугольной смоле.
В качестве сырья применяли дистиллятные фракции с т. кип. 180–230°С, выделенные из необезвоженной смолы АО “Сары Арка Спецкокс” (г. Караганда, Республика Казахстан) полукоксования угля Шубаркульского месторождения. Характеристика смолы приведена в табл. 1, нафталиновых фракций – в табл. 2.
Таблица 1.
Характеристика смолы полукоксования угля месторождения Шубаркуль
Показатель | Значение показателя |
---|---|
Плотность при 20°С, г/см3 | 1.071 |
Содержание воды, мас. % | 3.4 |
Фракционный состав, мас. %: | |
н.кип. | 130 |
выкипает до 180°С | 2.4 |
180–330°С | 19.0 |
выше 330°С+потери | 78.6 |
Зольность, мас. % | 0.11 |
Содержание, мас. %: | |
полиароматические углеводороды | 60.0 |
вещества, нерастворимые в толуоле | 1.3 |
Элементный состав, мас. %: | |
C | 91.11 |
H | 5.50 |
S | 0.35 |
N | 1.46 |
О (по разности) | 1.58 |
Таблица 2.
Химический состав (мас. %) гидрогенизатов, полученных гидрогенизацией нафталиновых фракций с т. кип. 180–230°С (4 МПа, 15 мин, промышленный Al–Co–Mo-катализатор, лабораторная установка высокого давления)
Показатель | Сырье | Температура процесса, °С | ||
---|---|---|---|---|
400 | 450 | 525 | ||
Плотность, $\rho _{4}^{{20}}$ | 0.9358 | 0.9198 | 0.9292 | 0.9194 |
Йодное число, г J2/ на 100 г продукта | 13.4 | 12.6 | 12.0 | 11.4 |
Содержание серы | 0.32 | 0.14 | 0.08 | 0.10 |
Моноциклические ароматические углеводороды, в том числе | 31.3 | 29.5 | 23.0 | 24.8 |
этилбензол | 0.7 | 3.2 | 2.5 | 0.9 |
тетралин | 0.6 | 25.5 | 21.3 | 5.7 |
метилтетралины | 0.5 | 3.8 | 1.6 | – |
нафталин | 41.5 | 21.5 | 34.1 | 50.5 |
2-метилнафталин | 12.4 | 10.7 | 11.1 | 10.5 |
1-метилнафталин | 9.2 | 8.7 | 8.6 | 7.9 |
бензтиофен | 3.7 | – | – | – |
дифенил | 0.8 | 0.3 | 0.3 | 0.6 |
Гидрогенизацию проводили в проточной лабораторной установке высокого давления с пустотелым реактором объемом 0.25 дм3 с перемешивающим устройством (рис. 1). Смесь сырья с измельченным промышленным Al–Co–Мо-катализатором загружали в реактор, который предварительно продували аргоном при начальном давлении 4 МПа. Включали обогрев реактора, а при достижении 150°С – перемешивающее устройство. Температуру замеряли термопарой и автоматически поддерживали с точностью ±2°C. Рабочее давление водорода составляло 4.0 МПа, температура 400–525°С, время реакции 15 мин.
Рис. 1.
Принципиальная схема лабораторной установки: 1 – реактор; 2 – стакан-вкладыш; 3 – электропечь; 4 – амперметр; 5 – лабораторный трансформатор; 6 – термопара; 7 – реле; 8 – КСП-4; 9 – манометр; 10 – вентиль тонкой регулировки; 11 – газовый баллон; 12 – газометр; 13 – перемешивающее устройство; 14, 16 – уплотнительные болты; 15 – заглушка.
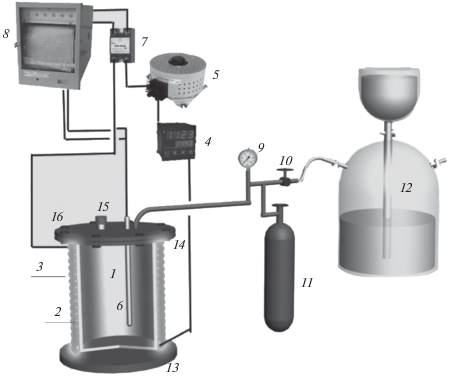
Групповой углеводородный состав исходной нафталиновой фракции и полученных гидрогенизатов определяли на хроматографе “ХРОМАТЭК” (Германия), содержание серы – с помощью прибора “POST LEKI P1437” (Германия).
Результаты гидрогенизации нафталиновых фракций с т. кип. 180–230°С коксохимической смолы приведены в табл. 2, из которой следует, что с увеличением температуры процесса с 400 до 525°С содержание нафталина в гидрогенизатах возрастает, а этилбензола, тетралина и ароматических углеводородов С8–С9 – уменьшается.
Характерной особенностью химического состава гидрогенизатов, полученных при температуре 500°С и выше, является незначительное содержание насыщенных углеводородов (0.3–0.4%), т.е. практически столько же или даже меньше, чем в сырье. Это свидетельствует о развитии при 500°С и выше в присутствии Al–Co–Mo-катализатора реакций гидрокрекинга насыщенных углеводородов и возможности получения гидрогенизатов, практически полностью состоящих из ароматических углеводородов.
Следует отметить, что алкилнафталины подвергаются гидродеалкилированию с относительно более высокими скоростями (примерно в 2–5 раз) по сравнению с соответствующими алкилбензолами. Однако концентрация алкилнафталинов, главным образом метилнафталинов, во фракциях с т. кип. 180–230°С коксохимической смолы, полученных на промышленных дистилляционных установках КХЗ, незначительна и не превышает 10–15%, причем основной компонент – 2-метилнафталин, который наименее реакционноспособен. Поэтому глубокое деметилирование гомологов нафталина сопровождается аналогичными трудностями, имеющими место при переработке бензольных углеводородов, в частности содержащих значительное количество толуола, для глубокого превращения которого в бензол необходимо применять “жесткие” условия и повышенную температуру процесса. Следовательно, бензольные углеводороды и нафталиновые фракции целесообразно перерабатывать совместно методом высокотемпературной гидрогенизации. Кроме того, совместная гидрогенизационная переработка такой смеси позволит сохранить в первой ступени процесса при гидростабилизации часть сырья в жидкой фазе, которая растворит основную массу полимерных продуктов, образующихся при нагреве сырого бензола, что предотвратит отложение их на теплообменной поверхности аппаратуры.
При высокотемпературной гидрогенизации под давлением до 4–5.0 МПа с катализаторами (550–600°С) или без катализаторов – термический процесс (650–700°С), протекают две основные реакции превращения углеводородов – деструкция парафиновых и нафтеновых углеводородов в газы С1–С4 и деалкилирование ароматических углеводородов [4]. В результате в составе жидких продуктов сохраняются в основном бензол, нафталин и их гомологи, выделение которых методом четкой ректификации не вызывает затруднений. Кроме того, за счет деалкилирования выход их значительно возрастает в зависимости от потенциального содержания в сырье.
Для получения образцов высококачественного бензола и бессернистого нафталина высшего качества оценочно были проведены опыты по высокотемпературной гидрогенизации (гидродеалкилированию) гидроочищенной и затем подвергнутой озонолизу смеси (3:1) сырого коксохимического бензола и нафталиновой фракции с т. кип. 180–230°С смолы со следующей характеристикой (мас. %): насыщенные углеводороды 2.9; бензол 48.0; толуол 12.9; ксилолы 3.9; этилбензол 0.8; ароматические углеводороды С9 3.5; тетралин+метилтетралины 16.9; нафталин 6.0; 2-метилнафталин 0.9; 1-метил-нафталин 0.1; другие соединения 4.1; содержание серы < 0.001.
Озонирование осуществляли на лабораторном озонаторе ПВ-5 при 20°С и атмосферном давлении в реакторе барботажного типа с непрерывной подачей озоновоздушной смеси (2.16 мол. % озона) со скоростями 0.25 и 2.0 мл/мин. В озонаторе использовался традиционный способ получения озона в газовом разряде барьерного типа. Синтез озона осуществлялся из осушенного воздуха методом короткоцикловой безнагревной адсорбции воздуха. Озонатор охлаждался окружающим воздухом.
При озонировании 30 мл исходной смеси заливали в стеклянный реактор-барботер. Затем соединяли насос подачи воздуха с озонатором и проверяли образование озона. Для определения скорости подачи озона озонатор присоединяли к счетчику газа и регулировали скорость выхода воздуха из насоса до достижения необходимой скорости. После этого озоновоздушную смесь пропускали через сырье.
Учитывая результаты исследований [5] по определению влияния озонирования на процесс гидрогенизации смолы полукоксования Шубаркульского угля, продолжительность озонирования была выбрана 60 мин. Результаты высокотемпературной гидрогенизации смеси сырого коксохимического бензола и нафталиновой фракции смолы приведены в табл. 3, из которой следует, что отложение кокса на катализаторе при осуществлении процесса при 450°С на 1.2% меньше, чем при 525°С. Однако при гидрогенизации сырья при 525°С отмечено увеличение выхода нафталина на 1.6% при выходе гидрогенизата 96.6% против 93.8% при 450°С.
Таблица 3.
Результаты высокотемпературной гидрогенизации предварительно озонированного сырья (4.0 МПа, время озонирования 60 мин, бензол:нафталиновая фракция = 3:1, Н2:сырье =12:1 (моль), Мо-содержащий катализатор на цеолите HNaY)
Показатель, мас. % | Температура, оС | |
---|---|---|
450 | 525 | |
Выход жидких продуктов | 93.8 | 96.6 |
Выход газа (С1–С4) | 5.2 | 3.1 |
Расход водорода | 1.0 | 0.8 |
Содержание кокса на катализаторе | 2.4 | 3.6 |
Выход чистых продуктов при четкой ректификации: | ||
бензол | 56.0 | 51.2 |
нафталин | 22.3 | 23.9 |
Для выделения из гидрогенизата, полученного при 525°С, товарных продуктов был применен метод четкой ректификации. Из гидрогенизата отгонялась головная фракция, а затем выделялся бензол, толуол, фракции 120–150 и 150–180°С (растворители) и нафталин. Материальный баланс переработки смеси сырого коксохимического бензола и нафталиновой фракции приведен в табл. 4.
Таблица 4.
Материальный баланс переработки смеси сырого коксохимического бензола и нафталиновой фракции с т. кип. 180–230°С
Приход | Мас. % | Расход | Мас. % |
---|---|---|---|
I. Гидрогенизация | |||
1. Сырой коксохимический бензол | 75.0 | 1. Гидрогенизат | 105.8 |
2. Нафталиновая фракция | 25.0 | 2. Газ | 3.1 |
3. Добензольная и другие фракции | 8.9 | ||
Итого | 108.9 | Итого | 108.9 |
II. Ректификация | |||
1. Гидрогенизат* | 105.3 | 1. Бензол | 51.2 |
2. Толуол | 11.9 | ||
3. Фракция с т.кип. 120–150°С (растворитель I) | 3.7 | ||
4. Фракция с т.кип. 150–185°С (растворитель II) | 2.4 | ||
5. Нафталин | 23.9 | ||
6. Добензольная фракция | 6.2 | ||
7. Донафталиновая фракция | 0.6 | ||
8. Остаток | 2.9 | ||
9. Потери | 2.5 | ||
Итого | 105.3 | Итого | 105.3 |
Полученный при ректификации кристаллический нафталин высшего качества имеет температуру кристаллизации +78.6°С и содержание серы менее 0.0002%. Температура кристаллизации бензола равна +5.41°С, плотность $\rho _{4}^{{20}}$ 0.8783, йодное число – менее 0.05 г J2/на 100 г продукта, содержание серы 0.00014%, что соответствует требованиям ГОСТ 9572-93 на высокочистый бензол для органического синтеза.
Поскольку за один пропуск сырья полного превращения его в бензол, нафталин и газ не происходит, то ароматические углеводороды С7–С9 и С11 должны после выделения бензола и нафталина возвращаться в процесс в количестве ~25–30% в виде рециркулята. Химический состав продуктов высокотемпературной гидрогенизации с рециркуляцией остатка после выделения нафталина приведен на рис. 2. Видно, что в составе продуктов с рециркуляцией остатка увеличивается выход бензола на 1.4 и нафталина на 1.9%, соответственно, за счет гидродеалкилирования и гидрокрекинга ароматических углеводородов.
Рис. 2.
Химический состав продуктов высокотемпературной гидрогенизации смеси сырого бензола и нафталиновой фракции после рециркуляции остатка (мас. %): ряд 1 – гидроочищенное сырье; ряд 2 – смесь (75:25) гидроочищенного сырья и остатка после выделения нафталина.
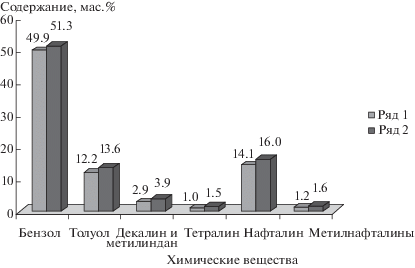
Таким образом, на основании выполненных исследований установлено следующее.
1. При каталитической гидрогенизации сырой нафталиновой фракции коксохимической смолы КХЗ Республики Казахстан для увеличения выхода нафталина рекомендуется температура процесса 525°С, давление 4 МПа, объемная скорость подачи сырья 0.5 кг/л ч.
2. При гидрогенизационной переработке смеси сырого коксохимического бензола и нафталиновой фракции смолы полукоксования Шубаркульского угля под давлением 4 МПа над Al–Co–Mo-катализатором получается гидрогенизат, пригодный для полного выделения ароматических углеводородов методом четкой ректификации.
3. Предварительное озонирование в течение 60 мин смеси сырого бензола и нафталиновой фракции (3 : 1) позволяет при последующей высокотемпературной гидрогенизации получить выход химических продуктов 95–96% от перерабатываемого сырья.
Список литературы
Кричко А.А., Скворцов Д.В., Советова Л.С. // Тр. ИГИ. Т. XXIII. М.: Изд-во ИОТТ. 1968. С. 172.
Кричко А.А., Скворцов Д.В., Советова Л.С., Титова Т.А., Филиппов Б.С. // Тр. ИГИ. Т. 25. Вып. 1. М.: Изд-во ИОТТ. 1970. С. 169.
Кричко А.А., Скворцов Д.В., Филиппов Б.С., Догадина Н.Е. // Тр. ИГИ. Т. 24. Вып. 4. М.: Изд-во ИОТТ. 1969. С. 171.
Баландин А.A. Современное состояние мультиплетной теории гетерогенного катализа. M.: Наука, 1968. 202 с.
Каирбеков Ж.К., Малолетнев А.С., Смагулова Н.Т., Сабитова А.Н. // ХТТ. 2018. № 5. С. 46. [Solid Fuel Chemistry, 2018, vol. 52, no. 5, p. 320. doi 10.3103/S0361521918030047] doi 10.1134/S002311771804014X
Дополнительные материалы отсутствуют.
Инструменты
Химия твердого топлива