Химия твердого топлива, 2019, № 6, стр. 35-40
КОНЦЕПЦИЯ ТЕХНОЛОГИЧЕСКОГО КОМПЛЕКСА ПЕРЕРАБОТКИ ОТХОДОВ ДОБЫЧИ И ОБОГАЩЕНИЯ УГЛЕЙ С ПОЛУЧЕНИЕМ ШИРОКОГО СПЕКТРА ТОВАРНОЙ ПРОДУКЦИИ
М. Я. Шпирт 1, *, Е. Г. Горлов 1, **, А. В. Шумовский 1, ***
1 ФГУП Институт горючих ископаемых – научно-технический центр по комплексной переработке
твердых горючих ископаемых
119071 Москва, Россия
* E-mail: shpirt@yandex.ru
** E-mail: gorloveg@mail.ru
*** E-mail: a.shumowsky@yandex.ru
Поступила в редакцию 29.04.2019
После доработки 20.05.2019
Принята к публикации 03.06.2019
Аннотация
Рассмотрены технологии переработки отходов добычи и переработки углей для получения товарных продуктов в зависимости от особенностей сырья. Показано, что наиболее востребованным может быть производство из углеотходов материалов для строительства. Изучены процессы получения из углеотходов концентратов редкоземельных элементов (РЗЭ), алюминия, железа, коагулянтов для водоочистки, топливных добавок – энергетических углей и добавок для металлургической промышленности. Впервые предложена концепция технологического комплекса, позволяющего в едином цикле получать широкий ассортимент товарных продуктов из углеотходов. Разработана базовая конфигурация комплексной технологии, подобрано основное оборудование для технологических процессов. Показаны возможные результаты реализации технологии в промышленности.
Образование отходов при добыче и переработке полезных ископаемых приводит к загрязнению окружающей среды: атмосферного воздуха, подземных и поверхностных вод, почв и растительности.
Современной тенденцией в промышленно развитых странах является крупномасштабное внедрение проектов, связанных с уменьшением объемов отходов добычи, переработки и потребления полезных ископаемых и решением экологических проблем, обусловленных их хранением. В России среди всех отраслей промышленности добыча твердых горючих ископаемых, главным образом углей, и их обогащение занимают одно из первых мест в мире по объему образования твердых отходов: на 1 т товарного угля при открытой и шахтной добыче углей образуется около 4–4.5 т и 0.3–0.4 т вскрышных и шахтных пород соответственно; после обогащения – 0.3–0.4 т отходов (породы гравитации и флотохвостов) углеобогащения [1].
С учетом реальных и планируемых объемов добычи и переработки углей в России на период до 2025 г. ежегодный выход вскрышных пород составит более 350 млн т, отходов обогащения – примерно 35–40 млн т.
Основная масса углеотходов направляется на хранение, среди них, преобладают вскрышные породы (около 50% от их ежегодного накопления используется для обратной закладки выработанного пространства, 45–49% составляют так называемые органоминеральные с содержанием органического углерода не менее 5%).
Вскрышные и шахтные породы, а также породы гравитационного обогащения хранятся в отвалах (терриконах и плоских отвалах); отходы флотационного обогащения – в шламоотстойниках (флотационных прудах). Многие предприятия не имеют возможности полностью реализовать шламы, т.е. уголь крупностью менее 1 мм. Не отгруженные потребителям шламы гидравлическим методом направляют в шламоотстойники, и на предприятиях, применяющих флототационное обогащение углей, они хранятся вместе с флотохвостами.
На территории России в отвалах хранится не менее 10–11 млрд т отходов добычи и обогащения углей [2]. Хранение углеотходов обусловливает выведение из хозяйственного оборота значительных площадей земельных территорий нашей страны, а строительство и эксплуатация отвалов требует существенных капитальных вложений и эксплуатационных затрат. Так, например, затраты, необходимые для сбора, транспортировки в отвалы и хранения в них пород гравитации, составляют от 20 до 25% всех расходов на обогащение углей.
Кроме того, в породах добычи и обогащения содержатся значительные количества органических веществ, что приводит к их самовозгоранию. В результате самовозгорания в атмосферу поступают экологически опасные вещества (CO, H2S, бензопирены, токсичные соединения азота и др.). По ориентировочным данным, в России около 25% горящих отвалов отходов добычи и обогащения углей. Особенную экологическую опасность представляют отвалы углеотходов, содержащие соединения серы, которые частично окисляются с образованием высокотоксичной серной кислоты, поэтому необходимо решать экологические проблемы, связанные с загрязнением земельных территорий, атмосферы, а также грунтовых и подземных вод соединениями различных металлов (Al, Fe, Zn, Ni и др.) в результате их выщелачивания водными потоками (дожди, тающий снег), просачивающимися в почву.
В России объем утилизации отходов добычи и обогащения углей составляет менее 5% от общего объема образующихся углеотходов,что приводит к затратам на сбор, хранение и снижение неблагоприятных экологических последствий.
Экспериментальные исследования и промышленный опыт показывают, что углеотходы – эффективное сырье для утилизации, используемое в строительстве, металлургии, сельском хозяйстве, водоочистке и других областях [2–5].
На сегодняшний день актуален поиск эффективных технологических решений по переработке углеотходов. Как правило, разрабатываемые и внедряемые технологии переработки имеют монопрофильную направленность. Так, в работе [6] рекомендована технология сжигания со сбором образующихся зольных уносов и шлаков для производства товарных соединений микроэлементов. В работах [7, 8] предложены варианты использования топливосодержащих отходов в качестве сырья для производства портландцементного клинкера и цемента, а авторами работы [9] предложена технология получения коагулянтов для очистки воды из углеотходов Подмосковного бассейна. Возможности автоклавной экстракции металлов из отходов добычи и переработки металлоносных углей Восточного Донбасса рассмотрены в [10]. Физико-химические основы переработки германиевого сырья, в том числе углеотходов, изложены в монографии [11]. Отходы угледобычи и углеобогащения применяются в качестве сырья для петрургической промышленности (каменного литья) [12].
Известно, что состав углеотходов в терриконах непостоянен и изменяется в широких пределах в зависимости от горно-геологических условий местности, в которой происходила добыча угля, а также по высоте и объему отвала, поэтому перед переработкой углеотходов необходимо их предварительное усреднение.
Состав и свойства горелых и негорелых пород терриконов также имеют большие различия. Негорелые породы состоят в основном из глин, сланцев, аргиллитов, алевролитов, песчаников и песков. Глины и сланцы, представленные в горных породах терриконов, в значительной степени подверглись литификации, и для проявления типичных глинистых свойств должны быть подвержены измельчению и рыхлению. Алевролиты довольно устойчивы в воде, часто содержат углистые включения и по минеральному составу близки к тонкозернистым песчаникам, сцементированным глинистым и реже карбонатным веществом. В песчаниках преобладает кварц, присутствуют полевые шпаты и слюды.
Самовозгорание терриконов приводит к существенной потере органического вещества и дегидратации вмещающих пород. Состав и свойства горелых пород зависят от степени обжига. Низкую гидравлическую активность, как правило, проявляют сильно обожженные породы, а для среднеобожженных характерна наибольшая гидравлическая активность. Слабообожженные породы отличаются более низкой прочностью и представлены мелкой фракцией. Установлено, что негорелые отходы угледобычи – это высокоэффективные выгорающие добавки, а горелые – отощители и интенсификаторы спекания в составе сырьевой шихты для производства строительной керамики.
Для пород-оснований угленосных карьеров или почвенных пород угольных пластов, для районов залегания угля на высокоглиноземистых породах или на закарстованных известняках, для склонов поднятий и платформенных угленосных формаций характерно высокое содержание алюминия. Высокоглиноземистые породы, залегающие в угольных пластах, добываемые попутно с углем и попадающие в терриконы, представлены в большинстве случаев каолинитом. Все эти особенности следует учитывать при разработке методов переработки углеотходов. Идеей предлагаемого технологического комплекса переработки отходов добычи и обогащения углей является совмещение в едином цикле основных процессов переработки для получения широкого ассортимента товарной продукции.
Технологический комплекс переработки углеотходов разрабатывался с учетом возможности вовлечения в промышленное использование практически всех видов углеотходов: как было показано ранее [2], для обеспечения требуемого количества тепла, которое может быть получено при сжигании углеотходов, требования к твердым отходам добычи и обогащения углей при их использовании как топлива для сжигания следующие: содержание серы 1–2%, зольность 50–65%, влажность 12–25%, низшая теплота сгорания 7–10 МДж/кг. В производстве вяжущих материалов предпочтительно использовать отходы высокометаморфизированных углей, а общее содержание углерода в них ограничить. Для производства аглопорита предпочтительно использовать углеотходы с зольностью 50–82% и коэффициентом плавкости Кпл, равным 4–12, для производства керамзита – вспучивающиеся или сильно вспучивающиеся углеотходы с содержанием органического углерода менее 4%, в качестве шихты для производства цемента – углеотходы с зольностью 50–82%.
Как показали исследования, проводимые в ИГИ, для получения сульфата алюминия (коагулянта для очистки питьевых и промышленных сточных вод) наиболее пригодны глинистые углеотходы, содержащие алюминий в виде каолинита с содержанием Al2O3 выше 25%.
Для получения концентрата редкоземельных элементов, иттрия и скандия использована сернокислотная схема переработки, включающая операции осаждения малорастворимых двойных сульфатов редкоземельных металлов с натрием, последующий гидролиз осадков гидроокисью натрия, растворение образующихся гидроокисей редкоземельных металлов азотной кислотой и очистку их экстракцией. Схема технологического комплекса (рисунок) разработана на основании данных исследовательских работ ИГИ и накопленного опыта внедрения их результатов в опытно промышленных масштабах, преимущественно на установках Жилевской ОПОФ. В основу схемы легли технологии, разработанные в ИГИ и описанные в [1, 6, 9, 11, 13], а также системы идентификации и классификации углеотходов по промышленному использованию, предложенные в [14, 15].
Это модульная система, составные технологические части которой могут функционировать автономно в зависимости от особенностей перерабатываемого сырья, производя или весь возможный ассортимент продуктов, или отдельные продукты, выбранные по каким-то причинам (коньюнктурным, технологическим, сырьевым и др.). При разработке исходили из условия использования во всех составляющих его модулях в основном стандартного технологического оборудования. Режимы и параметры процессов описаны в [1, 6, 9, 11, 12]. В табл. 1 представлен состав базовой конфигурации технологического комплекса.
Таблица 1.
Состав базовой конфигурации технологического комплекса
№ | Модуль | Основное оборудование модуля |
---|---|---|
1 | Прием и хранение сырья термообработки | Бункеры для приема и хранения сырья, реагентов, емкости для приема и хранения серной кислоты, воды |
2 | Подготовка сырья к переработке | Бункер с дозатором-питателем, дробилка-измельчитель |
3 | Получени энергетического угля и добавок к стройматериалам | Сепаратор-классификатор, бункеры приема энергетического угля и добавок к стройматериалам |
4 | Термообработка | Бункер с дозатором, аппарат для термообработки холодильник, бункер для сбора продуктов после термообработки, бункер для сбора мелких фракций после термообработки, смеситель, воздуходувка, емкость для сбора горячей воды. |
5 | Получение сульфата алюминия | Емкость с мешалкой для обработки серной кислотой, емкость-дозатор для подачи серной кислоты, фильтр, емкость для раствора серной кислоты, емкости для коагулянтов |
6 | Получение концентратов РЗЭ, иттрия и скандия | Емкость с мешалкой, фильтр, сушилка, емкости для концентрата РЗЭ, иттрия и скандия. |
7 | Получение добавок к стройматериалам | Емкость для приема твердого остатка, сушилка, бункер для хранения добавок к стройматериалам |
8 | Получение концентратов алюминия и железа | Магнитный сепаратор, бункеры для приема концентратов алюминия и железа |
9 | Получение серной кислоты | Узел синтеза серной кислоты, емкость для раствора серной кислоты, емкость для разбавления серной кислоты |
10 | Прием и хранение готовой продукции | Бункеры с дозаторами, емкости |
В схеме используется серокислотный метод с предварительной аморфизацией структуры каолинита для перевода его в реакционноспособное состояние (метакаолин) термообработкой при 550–600°С в течение 1–2 ч. При обработке полученного материала 20%-ным раствором серной кислоты 82–86% алюминия переходит в раствор в виде сульфата. Раствор сульфата алюминия можно использовать в качестве коагулянта для водоочистки или в качестве сырья в производстве алюмосиликатных катализаторов и цеолитов. Возможно также получение сухого товарного сульфата алюминия с содержанием Al2O3 более 14% упариванием раствора в многокорпусных выпарных установках.
Подготовка отходов угледобычи к переработке заключается в их предварительной сушке с последующим дроблением и измельчением до фракции не более 1мм. Предварительная сушка отходов угледобычи необходима для повышения эффективности работы дробильно-помольного оборудования.
Особенности предлагаемой схемы заключаются в следующем:
возможность переработки углеотходов с получением широкой гаммы ценных продуктов в едином комплексе по безотходной технологии;
возможность адаптации комплекса к переработке углеотходов различного происхождения, расширение спектра вовлекаемых в оборот углеотходов.
Реализация предлагаемой комплексной схемы в виде промышленной установки позволяет организовать производство продуктов, представленных в табл. 2.
Таблица 2.
Продукты и их характеристики
№ | Продукт | Характеристика продукта |
---|---|---|
1 | Топливно-минеральная добавка для производства керамического кирпича, аглопорита, керамической эффективной строительной керамики и дренажных труб, а также других строительныхматериалов | Углерод (органический) от 5 до 25 мас. %; сера ≤2 мас. %; (СаО + MgO) ≤ 12 мас. % |
2 | Энергетическое топливо | Зольность (на сухую массу) ≤ 20 мас. %; серы ≤ 1.5 мас. %. |
3 | Добавка в сырьевую шихту при производстве цемента | Углерод (органический) ≤ 40 мас. %; сера ≤ 2.5 мас. % |
4 | Коагулянт (сульфат алюминия) для очистки питьевых или сбросных производственных вод | По ГОСТ 1296-85 |
5 | Коагулянт (смешанный сульфат алюминия и железа) для очистки питьевых или сбросных производственных вод | Железо ≤ 12 мас. % |
6 | Концентрат редкоземельных металлов, иттрий. | Оксиды РЗМ до 95 мас. %, в том числе: Y2O3 ≤ 35 мас. %; La2O3 ≤ 85 мас. % |
7 | Концентрат скандия (на схеме отсутствует) | Sc2O3 ≤ 80 мас. % |
8 | Концентрат железа для доменной или внедоменной переработки | Железа ≥ 50%; серы ≤ 0.15 %; влажность ≤ 10% |
Наиболее целесообразно создавать производства указанных продуктов по предлагаемой комплексной схеме в виде специализированных предприятий, расположенных вблизи крупнотоннажных источников сырья, т.е. вблизи угольных терриконов и угольных отвалов. Возможно и создание участков по переработке углеотходов в составе предприятий угледобычи и углеобогащения с инфраструктурой, необходимой для размещения установок.
Экономическая эффективность использования углеотходов (текущих твердых отходов добычи и обогащения углей и складированных в отвалах или флотошламоотстойниках) при их переработке по предлагаемой схеме во многом зависит от (транспортных расходов, цен на заменяемое минеральное сырье, топливо и других условий). Преимуществом использования углеотходов вместо традиционного минерального сырья и топлива является значительная более низкая их стоимость.
По предварительным расчетам, экономический эффект от переработки 1 т углеотходов в зависимости от направления их переработки будет изменяться от 200 до 600 руб, а суммарный объем переработки углеотходовможет составить 30–40 млн т/г.
Потребность в продуктах, произведенных из отходов добычи и обогащения углей, для производства стройматериалов для среднестатистической области центрального региона РФ может составлять 3–4 млн т/г (без учета использования в строительстве искусственных земляных сооружений и автомобильных дорог), что может дать снижение стоимости 1 м2 жилья (без учета инфраструктурных затрат) приблизительно на 10%.
Для среднестатистической области, при годовом вводе в строй ~500 000 м2 жилья, экономический эффект может составить до 0.5 млрд руб/г.
Производство из отходов добычи и обогащения углей топливной добавки позволит обеспечить топливом цементные заводы. Средний цементный завод, использующий в качестве основного топлива уголь, потребляет 200–250 тыс. т/г несортового угля, привозимого, как правило, с разрезов Кузбасса. Хотя бы частичный перевод завода на местное топливо из углеотходов чувствительно скажется на себестоимости производимого им цемента, так как около 60% цены цемента – это топливная составляющая. Только в регионе Москвы (радиус 500 км) работает 8 цементных заводов с общим объемом производства цемента 12–15 млн т/г, 150 бетонных и ЖБИ заводов с объемом производства 5 млн т/г, 15 кирпичных завода с с объемом производства 2.6 млн т/г. Эти предприятия в состоянии потреблять около 8–10 млн т/г отходов переработки и обогащения углей.
В процессе производства цемента в составе сырьевой шихты на отходы добычи и обогащения углей может быть заменено 12–20% алюмосиликатной и железосодержащей частей (или 0.3–0.6 т на 1 т клинкера). При средней мощности цементного завода в РФ 1 млн т клинкера количество замещаемых минеральных ресурсов может составлять 0.3–0.6 млн т на один завод. При замене части сырьевой смеси на данный вид отхода экономия может составить 13–20 млн руб/г.
Предприятия по производству железобетонных изделий различного назначения являются основой строительной индустрии. В РФ производство бетона составляет около 25–30 млн м3/г (около 60 млн т/г). Объемы потребления добавок в бетоны сопоставимы спотребностям цементных заводов.
Средний завод железобетонных изделий производительностью 400 000 м3/г требует для своего производства 560 000 т минерального заполнителя. Экономия от замещения всего объема может составить около 112 млн руб/г для одного завода.
Таким образом, предварительная оценка эффекта от внедрения предложенной технологии показала ее актуальность и перспективность как с точки зрения экономики, так и с позиции снижения техногенного воздействия на окружающую среду. Углеотходы – практически неисчерпаемый источник дешевого сырья, использование которого для получения широкого ассортимента товарных продуктов приводит к экономии капитальных вложений, повышению уровня рентабельности промышленных предприятий, высвобождению значительных площадей земельных угодий и снижению степени загрязнения окружающей среды.
Рис. 1.
Модули базовой конфигурации технологического комплекса (нумерация соответствует нумерации в табл. 1): 1 – прием и хранение сырья (бункера для приема и хранения сырья, реагентов, емкости для приема и хранения серной кислоты, воды); 2 – подготовка сырья к переработке (бункер с дозатором-питателем, дробилка-измельчитель); 3 – получение энергетического угля и добавок к стройматериалам (сепаратор-классификатор, бункеры приема энергетического угля и добавок к стройматериалам); 4 – термообработка ( бункер с дозатором, аппарат для термообработки, холодильник, бункер для сбора продуктов после термообработки, бункер для сбора мелких фракций после термообработки, смеситель, воздуходувка, емкость для сбора горячей воды); 5 – получение сульфата алюминия (емкость с мешалкой для обработки серной кислотой, емкость-дозатор для подачи серной кислоты, фильтр, емкость для раствора серной кислоты, емкости для коагулянтов); 6 – получение концентратов РЗЭ, иттрия и скандия (емкость с мешалкой, фильтр, сушилка, емкости для концентрата РЗЭ, иттрия и скандия); 7 – получение добавок к стройматериалам (емкость для приема твердого остатка, сушилка, бункер хранения добавок к стройматериалам); 8 – получение концентратов алюминия и железа (магнитный сепаратор, приемные бункеры для концентратов алюминия и железа); 9 – получение серной кислоты (узел синтеза серной кислоты, емкость для раствора серной кислоты, емкость для разбавления серной кислоты); 10 – прием и хранение готовой продукции (бункеры с дозаторами, емкости).
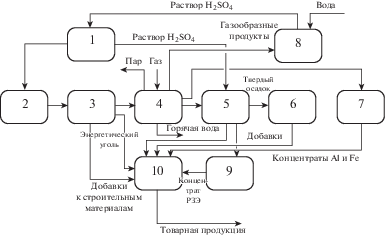
Список литературы
Шпирт М.Я., Артемьев В.Б., Силютин С.А. Использование твердых отходов добычи и переработки углей. М.: Горное дело, 2013. 432 с.
Володарский И.Х., Игнатова Н.Н., Шпирт М.Я. Основные принципы создания экологически безопасных процессов добычи и переработки твердых горючих ископаемых. // Юбил. сб. тр. ИГИ. Состояние и перспективы комплексного использования твердых горючих ископаемых. М.: НТК “Трек”, 2011. С.237.
Починков И.В., Мясков А.В. Анализ существующих методов использования и переработки отходов угледобычи // Научн. вестн. Моск. гос. горного ин-та. 2013. № 5. С. 76.
Гайдай М.Ф. Геоэкологические аспекты рационального использования ресурсного потенциала терриконов угледобывающих предприятий (на примере Кизеловского угольного бассейна). Дисс. … канд. техн. наук. Пермь: Пермский национальный исследовательский политехнический университет, 2016. 160 с.
Худякова Л.И. // XXI век. Техносферная безопасность. 2017. Т. 2. № 2. С. 45.
Шпирт М.Я. // Горный инф.-анал. бюл. 2015. № 4. С. 172.
Пьячев В.А. Углеотходы ценное сырье для производства цемента // Изв. вузов. Горный журн. 1998. № 3–4. С. 64.
Уфимцев В.М., Капустин Ф.Л., Пьячев В.А. // Цемент и его применение. 2009. № 6. С. 20.
Малолетнев А.С., Зекель Л.А., Шпирт М.Я. // ХТТ. 2010. № 3. С. 37.
Левченко С.В. Геологические особенности формирования и комплексное использование металлоносных углей Восточного Донбасса. Дисс. … канд. геолого-минерал. наук Ростов-на-Дону: ФГОАУ ВПО Южный федеральный университет, 2012. 146 с.
Шпирт М.Я. Безотходная технология: Утилизация отходов добычи и переработки твердых горючих ископаемых. М.: Недра. 1986, 254 с.
Умнов В.А. // Горный инф.-анал. бюл. 1995. № 5. С. 99–106.
Шпирт М.Я., Рубан В.А., Иткин Ю.В. Рациональное использование отходов добычи и обогащения углей. М.: Недра, 1990. 223 с.
Силютин С.А., Шпирт М.Я., Лавриненко А.А. // ХТТ. 2016. № 3. С. 20.
Шпирт М.Я., Иткин Ю.В. // ХТТ. 1980. № 2. С. 73.
Дополнительные материалы отсутствуют.
Инструменты
Химия твердого топлива