Химия твердого топлива, 2020, № 1, стр. 30-37
ПРОЦЕСС ПОЛУЧЕНИЯ МЕТАЛЛУРГИЧЕСКОГО КОКСА ПИРОЛИЗОМ СМЕСЕЙ ТОРФА, БИОМАССЫ И ГУДРОНА
А. В. Шумовский 1, *, Е. Г. Горлов 1, **, М. А. Ношин 2, ***
1 ФГУП Институт горючих ископаемых – научно-технический центр по комплексной переработке
твердых горючих ископаемых (ФГУП ИГИ)
119071 Москва, Россия
2 ООО “ИЛМиТЭ
119049 Москва, Россия
* E-mail: a.shumowsky@yandex.ru
** E-mail: gorloveg@mail.ru
*** E-mail: mary_cool@mail.ru
Поступила в редакцию 29.04.2019
После доработки 20.06.2019
Принята к публикации 04.10.2019
Аннотация
Исследована возможность получения металлургического кокса низкотемпературным пиролизом смесей торфа, биомассы и гудрона. Приводятся данные о влиянии на характеристики получаемых продуктов предварительной подготовки сырьевых смесей, содержания в смесях гудрона, температуры процесса. Экспериментально установлено, что максимальный выход полукокса достигается при содержании гудрона 20–40%, причем добавление гудрона в смеси способствует повышению механической прочности получаемого полукокса.
ВВЕДЕНИЕ
Постоянно растущая потребность в стали, которая стала основным конструкционным материалом современного мира, требует пропорционального увеличения объемов получения кокса. Известно, что в сырьевой составляющей себестоимости чугуна 40–50% приходится на кокс. Балансовые запасы коксующихся углей в России оцениваются в 42.3 млрд т, из них 77% приходится на Кузнецкий угольный бассейн, а прогнозные ресурсы составляют около 390 млрд т. При этом годовая потребность крупнейших металлургических комбинатов России в коксующемся угле оценивается в 20.8 млн т. Однако добыча коксующихся углей – дорогостоящий процесс: их месторождения залегают очень глубоко, а потому добываются они шахтовым способом, что серьезно увеличивает себестоимость и конечную стоимость коксующегося угля на рынке. Помимо экономических причин стремление металлургов избавиться от “угольной” зависимости связано и с задачей повышения качества конечной продукции сталелитейных производств. Каменноугольный кокс вносит в чугун большое количество различных примесей, негативно сказывающихся на качестве металла, например серу. По этой причине металлургические комбинаты вынуждены дополнительно обрабатывать металл, что значительно удорожает технологический процесс. Кроме того, некоторым высокотехнологичным отраслям, таким, как атомная энергетика, самолето- и судостроение, в основном требуется высококачественная и чистая сталь, поэтому одним из направлений совершенствования технологических процессов в металлургическом производстве первого передела стал поиск альтернативного коксующимся углям сырья для производства кокса. Один из таких заменителей достаточно известен – это нефтяной кокс – побочный продукт нефтепереработки. Однако широкого применения в черной металлургии он не получил.
Поскольку для производства кокса может быть использовано практически любое природное углеродсодержащее сырье, появилась идея использовать для этих целей торф и другое растительное сырье [1, 2].
Преимущества торфяного кокса по сравнению с каменноугольным следующие: так как в торфе почти нет серы и фосфора, в получаемом из него коксе эти вредные для металлургии элементы практически полностью отсутствуют, так содержание серы не превышает 0.2%, что примерно в 10–20 раз меньше, чем у каменноугольного кокса. Зольность торфяного кокса ниже, чем каменноугольного: не более 8–10% по сравнению с более 12% каменноугольного кокса. Содержание летучих веществ в торфяном коксе зависит от способа коксования и колеблется от 6 до 8 [3]. Аналогичный показатель каменноугольного кокса составляет около 1.5%. По механической прочности торфяной кокс уступает каменноугольному и находится на уровне хороших сортов древесного угля.
Известно, что характеристики торфяного полукокса в значительной мере зависят от происхождения и свойств исходного материала, а также от способа получения. Первый фактор оказывает большое влияние на зольность и механическую прочность кокса, второй – на количество летучих продуктов и, отчасти, на механическую прочность. Для получения высококачественного металлургического кокса должен применяться малозольный сфагновый торф, средне или хорошо разложившийся и хорошо переработанный. Полукокс и кокс повышенной механической прочности можно получать из верхового торфа средней степени разложения и низинного гипнового торфа. По мере увеличения степени разложения исходного торфа выход твердых продуктов пиролиза и смолы увеличивается, а выход пирогенетической воды и газа снижается. При увеличении скорости нагревания выход твердых продуктов пиролиза падает, а летучих продуктов и дегтя – возрастает. Переход от малой скорости нагревания торфа (несколько градусов в минуту) к высокоскоростному нагреву (тысячи градусов в секунду) удваивает выход смолы. Пиролизом торфа получают полукокс (температура процесса 500–600°С), а прокалкой полукокса при 900–1000°С – прочный кокс. Из сельскохозяйственных отходов ранее полукокс не производили и таких закономерностей не наблюдали.
Специфическая особенность торфяного кокса – его высокая реакционная способность, существенно превышающая этот показатель у минерального кокса, что очень важно для доменного процесса и производства высококачественных специальных сплавов: углекислота, образующаяся из окиси углерода за счет раскисления окислов железа, восстанавливается быстрее, в результате чего процесс восстановления руды идет интенсивнее, чем при применении каменноугольного кокса. Недостатком является низкая механическая прочность и невысокий выход целевого продукта, поэтому современные западные технологии ориентированы в основном на получение из торфа жидкого продукта и пиролизного масла [4].
ЭКСПЕРИМЕНТАЛЬНАЯ ЧАСТЬ
Изучена возможность получения полукокса из смесей органоминерального сырья и тяжелого нефтяного остатка – гудрона, в процессе пиролиза для увеличения выхода полукокса и повышения его механической прочности.
В качестве тяжелого нефтяного остатка использовали гудрон производства АО “КНПЗ-КЭН” (Краснодар), характеристики которого представлены в табл. 1.
Таблица 1.
Физико-химические свойства гудрона
Показатель | Гудрон |
---|---|
Плотность при 20°С | 1008.6 |
Вязкость структурная при 100°С, Па · с | 510 |
Содержание, мас. %: | |
асфальтены | 6.2 |
вода | 2.5 |
механопримеси | 0.6 |
Начало кипения, °С | 368 |
Содержание серы, мас. % | 2.2 |
Коксуемость, % | 8.6 |
В качестве органоминерального сырья использовали торф и биомассу: отходы агропромышленного комплекса – лузгу подсолнечника и стержни початков кукурузы. Такой выбор обусловлен тем, что, согласно [5], именно эти материалы можно рассматривать как высокореакционное топливо с большим (до 60%) выходом летучих веществ при их переработке. Характеристики представительных проб органоминерального сырья представлены в табл. 2, а химический состав золы (минеральной части) – в табл. 3.
Таблица 2.
Физико-химические свойства органоминерального сырья
Добавка | Технический анализ, мас. % | Элементный анализ, мас. % | ||||||
---|---|---|---|---|---|---|---|---|
W a | Ad | V daf | Сdaf | Hdaf | Sdaf | Ndaf | O (пo разности) | |
Лузга подсолнечника | 8.1 | 2.5 | 60.8 | 50.3 | 6.3 | 0.15 | 1.8 | 41.45 |
Стержни початков кукурузы | 6.7 | 8.1 | 56.8 | 48.9 | 6.65 | 0.22 | 1.45 | 42.78 |
Торф | 42.6 | 6.8 | 57.8 | 57.8 | 6.2 | 0.3 | 2.2 | – |
Таблица 3.
Химический состав золы органоминерального сырья
Состав золы, мас. % стержней початков кукурузы | |||||||||
---|---|---|---|---|---|---|---|---|---|
SiO2 | А12О3 | Fe2O3 | TiO2 | CaO | MgO | SO3 | K2O | Na2O | P2O5 |
70.5 | – | – | – | 5.8 | 7.8 | – | 10.2 | 5.7 | – |
Состав золы, мас. % лузги подсолнечника | |||||||||
SiO2 | А12О3 | Fe2O3 | TiO2 | CaO | MgO | SO3 | K2O | Na2O | P2O5 |
74.8 | 2.8 | 1.5 | – | – | – | – | 20.1 | 0.7 | 0.1 |
Состав золы, мас. % торфа | |||||||||
SiO2 | А12О3 | Fe2O3 | TiO2 | CaO | MgO | SO3 | K2O | Na2O | P2O5 |
40.8 | 15.8 | 4.5 | – | 20.6 | 4.0 | 8.7 | 1.7 | 2.1 |
Органоминеральное сырье сушили в термостате при температуре 40–50°С, затем предварительно измельчали на щековой мельнице, а далее – в измельчителе твердых тел. Полученное измельченное сырье рассеивали на приборе РОТАПП и отбирали фракцию с размером частиц не более 0.2 мм. Гранулометрический состав измельченного органоминерального сырья класса –0.2 мм представлен в табл. 4.
Таблица 4.
Гранулометрический состав сырья класса –0.2 мм
Содержание, мас. % измельченных стержней початков кукурузы | |||
---|---|---|---|
0.2–0.1 | 0.1–0.063 | 0.063–0.05 | Менее 0.05 |
7.5 | 43.1 | 22.7 | 26.7 |
Содержание, мас. % измельченной лузги подсолнечника | |||
0.2–0.1 | 0.1–0.063 | 0.063–0.05 | Менее 0.05 |
2.7 | 12.7 | 48.9 | 35.7 |
Содержание, мас. % измельченного торфа | |||
0.2–0.1 | 0.1–0.063 | 0.063–0.05 | Менее 0.05 |
12.7 | 15.7 | 38.9 |
При приготовлении сырьевых смесей – суспензий, в нагретый до 90–95°С гудрон при перемешивании постепенно засыпали заданное количество измельченного органоминерального сырья. Полученные грубые суспензии гомогенизировали и механоактивировали путем 2–3-кратного пропускания через диспергатор. После каждого опыта анализировали размер частиц твердой фазы. На приборе Г.С. Ходакова были определены размеры частиц твердой фазы в суспензии.
Стабильность полученных гомогенных суспензий определяли по методике ИГИ, сущность которой заключается в определении концентрации дисперсной фазы в верхнем слое через заданное время отстоя.
Опыты проводили на установке пиролиза ГУ-01 (рис. 1). Пиролизер 1 подключен к линиям охлаждающей воды 2, к линии сжатого воздуха 3, к источнику питания через автоматы 4, 5. Автомат 4 подключен к верхнему муфелю 6 пиролизера, автомат 5 – к нижнему муфелю 7 пиролизера. Для контроля температуры предусмотрены термометры 8 и вторичные приборы 9. Количество подаваемого воздуха контролируется ротаметром 10. Газы окисления проходят змеевик холодильника и поступают на фильтр 11.
Пиролизер (рис. 2) состоит из корпуса 1 с внутренней изоляцией 2 и наружной изоляцией 3. По высоте корпуса 1 расположены три датчика температуры 4, выступающие на 3 мм от поверхности канала внутренней изоляции. В нижней части корпуса при помощи шпилек 5 с гайками 6 смонтирован золоприемник, в верхней части которого расположена золотниковая решетка 7. Подача воздуха на окисление проводится при помощи воздухо-охлаждающего ввода 8.
Пиролизер оборудован загрузочными и выгрузочными устройствами, а также системой охлаждения и конденсации парогазовой смеси. Торф загружается в аппарат через верхний фланец, который после загрузки закрывают. Подача нагретого газа-теплоносителя в пиролизер осуществляется через кольцевой канал, находящийся выше середины аппарата.
Для предварительного розжига сырья служат два муфеля 9, 10, расположенные в верхней и нижней частях корпуса. Вывод газов окисления осуществляется через наружный холодильник 11, оборудованный змеевиком 12. Для загрузки сырья предусмотрена воронка 13 с герметичной крышкой 14. Подвод электроэнергии к муфелю осуществляется через сальниковые уплотнения 15.
Анализ состава образующихся газов проводили на хроматографе ЛХМ-80 в потоке газа-носителя гелия на 3-метровых колонках, заполненных цеолитом марки 13Х и силикагелем марки АСК. На колонках с цеолитом при комнатной температуре определяли Н2, О2, N2, CH4, СО, С2Н6, а на колонке с силикагелем при программировании температуры до 200°С – СО2, углеводороды С3–С4. Анализ получаемого полукокса на реакционную способность проводили по методу, основанному на реакции кокса с СО2 (по ГОСТ 10089-89). Теплотворную способность (теплоту сгорания) получаемого полукокса определяли в калориметрической бомбе по ГОСТ 147-2013. Содержание серы определяли по методу Эшка (по ГОСТ 8606-2015), содержание фосфора – по ГОСТ 27894.5-88, содержание зольных примесей – по ГОСТ 11306-2013.
Низкотемпературный пиролиз проводили в периодическом режиме со скоростью подъема температуры ∼10 град/мин в интервале температур 250–550°С. Предварительно установка продувалась аргоном. Загрузка сырья составляла 200 г. Твердый продукт пиролиза – полукокс, отбирали из приемной емкости снизу аппарата, жидкие продукты собирали в охлаждаемые льдом скруббера, а газ – в газометре (через газовые часы).
Первоначально провели пиролиз исходного органоминерального сырья при температурах 350–550°С с целью оценки возможности получения из него полукокса. В табл. 5 представлен баланс процесса пиролиза исходного органоминерального сырья при 350–550°С.
Таблица 5.
Баланс процесса пиролиза органоминерального сырья при 350–550°С
Выход, мас. % | Торф | Стержни початков кукурузы | Лузга подсолнечника | ||||||||||||
---|---|---|---|---|---|---|---|---|---|---|---|---|---|---|---|
Температура, °С | Температура, °С | Температура, °С | |||||||||||||
350 | 400 | 450 | 500 | 550 | 350 | 400 | 450 | 500 | 550 | 350 | 400 | 450 | 500 | 550 | |
Полукокс | 70.3 | 54.0 | 46.3 | 41.30 | 36.5 | 66.0 | 52.1 | 42.4 | 39.4 | 34.4 | 63.5 | 50.4 | 41.1 | 36.9 | 29.7 |
Жидкая фаза | 14.9 | 31.5 | 36.6 | 36.8 | 33.8 | 17.2 | 30.8 | 33.5 | 34.0 | 32.1 | 17.6 | 28.2 | 32.0 | 31.5 | 30.6 |
Газ (по разности) | 8.8 | 14.5 | 17.1 | 21.9 | 29.7 | 16.8 | 17.1 | 24.1 | 26.6 | 33.5 | 18.9 | 21.4 | 26.9 | 31.6 | 39.7 |
Как следует из полученных данных, с повышением температуры процесса закономерно уменьшается выход полукокса, причем наибольший выход наблюдается при пиролизе торфа, а более низкие – при пиролизе стержней початков кукурузы и лузги подсолнечника. Так как количество полукокса, образующегося из стержней початков кукурузы и лузги подсолнечника достаточно большое, то эти материалы можно рассматривать как дополнительное органоминеральное сырье для производства металлургического кокса.
В табл. 6 представлены результаты исследований зависимости содержания углерода в полукоксе от температуры. Образующийся при пиролизе стержней початков кукурузы и лузги подсолнечника полукокс обладает низкой механической прочностью (предел прочности при сжатии не выше 10–12 МПа) и недостаточным содержанием углерода (ниже 90%). Для выявления возможности увеличения механической прочности получаемого полукокса был изучен процесс пиролиза при 550°C смесей биомассы с гудроном. Содержание гудрона в смесях варьировалось в интервале 10–50 мас. %.
Таблица 6.
Зависимость содержания углерода в полукоксе от температуры пиролиза
Сырье | Температура пиролиза, °С | Содержание углерода в полу-коксе, мас. % |
---|---|---|
Стержни початков кукурузы | 400 | 75.2 |
То же | 450 | 81.1 |
» | 500 | 86.2 |
» | 550 | 89.7 |
Лузга подсолнечника | 400 | 76.3 |
То же | 450 | 80.9 |
» | 500 | 86.9 |
» | 550 | 89.3 |
Установлено, что, если смеси готовили механическим смешением компонентов, то выход полукокса увеличивается на 3–10% по сравнению с выходом полукокса при пиролизе биомассы без добавления гудрона. При содержании 10–30% гудрона в смесях наблюдалось образование полукокса, содержащего неоднородные твердые частицы, которые, очевидно, образуются из-за неравномерности перемешивания компонентов сырья и формирования неоднородных по составу смесей. Дальнейшее увеличение количества гудрона в сырьевой смеси приводит к образованию неоднородного остатка, который уже включает часть жидкого крекинг-остатка, образующегося при пиролизе гудрона. Этот неоднородный остаток пиролиза необходимо подвергать дополнительному коксованию для получения твердого остатка.
С целью выявления возможности улучшения физико-механических свойств полукокса была изучена возможность использования механоактивации исходных смесей в диспергаторе ИГИ конструкции Хотунцева–Пушкина с применением 2–3-кратного диспергирования.
Механоактивация позволила не только получить гомогенные по своему составу смеси, но и повысить выход полукокса и его механическую прочность. Этот эффект можно объяснить тем, что при механоактивации частицы гудрона не только равномерно распределяются во всем объеме исходной смеси и подвергаются механодеструкции, но и частично локализуются в порах частиц органоминеральных компонентов смесей, а затем высокомолекулярные углеводородные молекулы гудрона в процессе пиролиза сополимеризуются, что способствует упрочнению структуры образующегося полукокса.
Из результатов опытов по пиролизу механоактивированного сырья, представленных на рис. 3, следует, что максимальный выход полукокса для всех сочетаний компонентов смесей достигается в интервале содержания гудрона 20–40%. Для определения реального выхода полукокса при содержании в исходной смеси 40–50% гудрона и отделения крекинг-остатка от полукокса применяли экстракцию кипящим толуолом в аппарате Грефе. Показатели качества кокса, полученного пиролизом механоактивированных смесей, приведены в табл. 7, из которой видно, что полученные продукты по всем основным показателям соответствуют требованиям, предъявляемым к металлургическому коксу.
Рис. 3.
Результаты опытов по пиролизу механоактивированного сырья (смесей гудрона, торфа и биомасс).
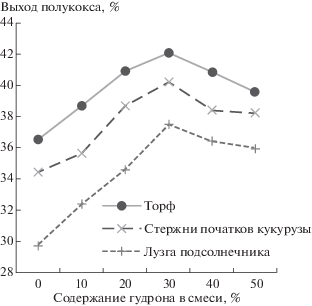
Таблица 7.
Характеристики кокса, полученного пиролизом механоактивированных смесей
Показатель | Требование | Смесь из 70% торфа и 30% гудрона | Смесь из 70% стержней початков кукурузы и 30% гудрона | Смесь из 70% лузги подсолнечника и 30% гудрона |
---|---|---|---|---|
Калорийность, Ккал/кг | 4000–4200 | 5800 | 5700 | 5700 |
Углерод, % | Не ниже 95 | 96 | 96 | 96 |
Фосфор, % | Не выше 0.02 | 0.02 | 0.01 | 0.01 |
Сера, % | Не выше 0.2 | 0.15 | 0.12 | 0.10 |
Зольность, % | Не более 3 | 2.8 | 2.0 | 1.3 |
Предел прочности при сжатии, МПа | Не ниже 15 | 19 | 17 | 17 |
ЗАКЛЮЧЕНИЕ
Впервые показана возможность получения кокса, соответствующего по своим характеристикам требованиям, предъявляемым к коксу для металлургии, пиролизом смесей гудрона, торфа и биомассы (отходов агропромышленного комплекса – стержней початков кукурузы и лузги подсолнечника).
Показано, что механоактивация сырьевых смесей способствует увеличению выхода полукокса и существенному повышению его механической прочности.
Установлено, что максимальный выход полукокса для всех сочетаний компонентов смесей достигается при содержании гудрона 20–40%, с повышением температуры процесса пиролиза увеличивается содержание углерода в полукоксе, но выход полукокса закономерно уменьшается. Наибольший выход полукокса наблюдается при пиролизе торфа, а более низкие – при пиролизе стержней початков кукурузы и лузги подсолнечника.
Список литературы
Журавлев А.В., Савина Е.С., Мальцева А.В. // Тр. Междунар. научн.-практ. конф. “Уральская горная школа – регионам”. 2012. С. 597.
Бессмертных А.В., Зайченко В.М., Коростина М.А., Кузьмина Ю.С. // Промышленная энергетика. 2013. № 2. С. 54.
Раковский В.Е., Пигулевская Л.В. Химия и генезис торфа. М.: Недра, 1978. 178 с.
Sutcu H. // Korean J. Chem. Eng. 2007. V. 24(5). P. 736.
Осьмак А.А., Серёгин А.А. // Восточно-Европейский журнал передовых технологий. ISSN 1729-3774 2/8 (68) 2014.
Дополнительные материалы отсутствуют.
Инструменты
Химия твердого топлива