Кинетика и катализ, 2022, T. 63, № 3, стр. 333-348
Cоздание и исследование модельного кобальтсодержащего катализатора на основе непористого углеродного волокна для высокопроизводительного процесса синтеза Фишера–Тропша
И. Г. Соломоник a, *, К. О. Грязнов a, Е. А. Пушина a, Д. Д. Приходько a, В. З. Мордкович a
a ФГБНУ Технологический институт сверхтвердых и новых углеродных материалов
108840 Москва, Троицк, ул. Центральная, 7а, Россия
* E-mail: igsol@bk.ru
Поступила в редакцию 12.03.2021
После доработки 13.12.2021
Принята к публикации 23.01.2022
- EDN: KDJMQZ
- DOI: 10.31857/S0453881122030133
Аннотация
Созданный на базе графитизированного ПАН-волокна нанесением тонкого слоя оксида алюминия носитель и модельный кобальтсодержащий катализатор синтеза Фишера–Тропша на его основе изучены рядом физико-химических методов, таких как физическая сорбция азота, ТПВ-Н2, ДТА-ДТГ (в варианте дериватографии), хроматография, электронная микроскопия (ПЭМ и СЭМ-ВР), 4-х контактный метод для определения теплопроводности. Обсуждены полученные структурные, адсорбционные, электронно-микроскопические, дериватографические данные и значение коэффициента теплопроводности наряду с активностью катализатора в синтезе Фишера–Тропша. Найдено, что катализатор после проведения синтеза значимо отличается от исходного, основной причиной дезактивации является отложение и накопление высокомолекулярных продуктов синтеза. В установившемся режиме его каталитические показатели, в том числе удельная производительность на массу металлического кобальта, соответствуют таковым для высокопроизводительного гранулированного катализатора на базе графита. Это позволяет использовать полученные результаты как модельные для идентификации отсутствия диффузионных сопротивлений, наличия высокой теплопроводности и необходимых поверхностных состояний разрабатываемого катализатора процесса GTL нового поколения.
ВВЕДЕНИЕ
Создание эффективных, селективных и высокопроизводительных катализаторов синтеза Фишера–Тропша на базе носителей с повышенной теплопроводностью за счет создания перколяционной сети из чешуйчатого алюминия или графита [1, 2] не отменяет вопрос дальнейшего их усовершенствования с оптимизацией массообмена при сохранении или увеличении съема тепла, генерируемого сильноэкзотермичной реакцией получения углеводородов. Очевидным потенциальным решением для снижения диффузионных ограничений является использование систем, в которых активный компонент катализатора располагается не на внутренней поверхности поры, а на внешней поверхности пористого структурированного монолита, микроканального реактора или углеродного волокна (нановолокна), наноуглеродного войлока [3, 4]. В многочисленных публикациях, которые рассмотрены в обзорах [5–7], основным способом получения такого рода катализаторов служит генерация наноуглеродных волокон на развитой поверхности неорганического носителя с последующей пропиткой активными в синтезе металлами.
Металлический компонент располагается на внутренней и внешней поверхности нанотрубок, причем наибольший вклад в каталитическую активность вносят именно внешние частицы металла при реализации их оптимальных размеров. Для кристаллитов кобальта эти величины составляют 6–8 нм [8, 9]. Каталитические параметры данных систем обусловлены также происходящим взаимодействием металлического прекурсора с углеродным носителем, возникновением дефектов, образованием карбидов, высокой поверхностной подвижностью частиц, обусловливающих их спекание и дезактивацию катализатора. Для снижения нежелательных эффектов используют декорирование поверхности наноуглеродного волокна оксидами алюминия или кремния.
Один из принципиально возможных вариантов применения углеродного носителя без создания таблетированных катализаторов стационарного слоя – генерация активных центров на внешней поверхности изолированных углеродных нитей из ПАН-волокна, между которыми протекают реактанты. При этом практически полностью отсутствуют диффузионные затруднения, сама углеродная нить обладает высокой теплопроводностью, и реализуется эффективный теплоотвод в газовый поток.
Таким образом, потенциально можно создать реактор из протяженных волокон, каждое из которых играет роль стенки поры с нанесенным катализатором, а их локальная совокупность является аналогом единичной реакционной трубы с суммарной реализацией многотрубного вертикального реактора. В отличие от классического блочного катализатора, представляющего собой монолит с пористой системой, т.е. пронизанный каналами, внутри которых расположен активный компонент, в рассматриваемом случае этот компонент находится (аналогично корочковым системам) на внешней поверхности. Такую систему можно определить как катализатор на непористом углеродном волокне (КНУВ).
Целью настоящей работы было приготовление и сравнительное исследование физико-химическими методами исходного и извлеченного из реактора после проведения в течение ряда дней синтеза Фишера–Тропша (СФТ) катализатора на основе непористого углеродного волокна (НУВ). На это волокно последовательно были нанесены сначала слой оксида алюминия, а затем оксид кобальта разложением нитрата кобальта. Каталитические свойства синтезированной системы сопоставлены с характеристиками высокопроизводительного катализатора СФТ на основе экструдированного носителя с перколяционной сетью из терморасширенного графита (ТРГ) [2].
Созданный на базе графитизированного ПАН-волокна носитель обладает высокой теплопроводностью, обусловленной собственным значением этого показателя для единичного углеродного волокна, однако реальная ее величина для жгута (связки волокон) неизвестна. Была отработана методика измерения коэффициента теплопроводности синтезированного катализатора на непористом углеродном волокне. Показано, что теплопроводность получаемого КНУВ сравнима с таковой для катализатора [2] на базе ТРГ или выше ее. Даже для заполненного продуктами синтеза КНУВ в стационарном режиме этот показатель остается весьма высоким.
При приготовлении катализатора КНУВ на непористом волокне априорно предполагалось, что активный компонент будет располагаться на поверхности и внутри пор предварительно нанесенного оксида алюминия с соответствующим уменьшением доступной поверхности и объема пор. Однако существенный, по сравнению с носителем, рост величины удельной поверхности катализатора, определенной по методу БЭТ, указывает на более сложную картину происходящих процессов, которые получили объяснение в ходе изучения систем. Были получены структурные, адсорбционные, электронно-микроскопические, дериватографические данные, найдены значения теплопроводности, выполнено исследование КНУВ методом термопрограммированного восстановления и определена его активность в синтезе Фишера–Тропша. Обнаружено, что катализатор после проведения синтеза значимо отличается от исходного, основной причиной его дезактивации является отложение и накопление высокомолекулярных продуктов синтеза.
В установившемся режиме каталитические показатели КНУВ в расчете на нанесенный металл соответствуют характеристикам высокопроизводительного гранулированного катализатора на базе терморасширенного графита, что позволяет использовать полученные результаты как модельные для идентификации отсутствия диффузионного сопротивления, наличия высокой теплопроводности и необходимых поверхностных состояний пористого катализатора процесса GTL нового поколения.
ЭКСПЕРИМЕНТАЛЬНАЯ ЧАСТЬ
Структурные параметры пористой системы образцов изучали методом физической сорбции азота на приборе Autosorb-1С (“Quantachrome”, США) с использованием фирменного программного обеспечения. Все образцы перед измерением сорбции–десорбции азота подвергали термовакуумной обработке при 300°С в течение 10 ч, а катализатор после синтеза – предварительному механическому удалению воскообразных продуктов и двукратной промывке внешней поверхности волокон в диэтиловом эфире. Термопрограммированное восстановление водородом (ТПВ-Н2) проводили в токе газа (10% Н2/Ar) также с помощью Autosorb-1.
Электронно-микроскопические снимки получали на сканирующем электронном микроскопе JSM-7600F (“JEOL”, Япония), оснащенном энерго-дисперсионным и волновым спектрометрами. Ток зонда до 200 нА позволял выполнять качественный и количественный микроанализ с пределом обнаружения для элементов: B – 0.0063%; C – 0.0068%; N – 0.0495%; O – 0.014% (EDX, Energy-dispersive X-ray spectroscopy). При изучении структурных параметров использовали представительные образцы исходных носителя и катализатора после проведенной в ходе их сорбционных исследований термовакуумной обработки и хранения в негерметичных условиях. Катализатор после синтеза изучали электронно-микроскопическим методом без дополнительной обработки вне спектрометра.
Для оценки поведения катализаторов в ходе термолиза и изменения их фазового и поверхностного состава применяли термический анализ в варианте дериватографии на приборе STA-449 F1 Jupiter (“NETZSCH”, Германия). Использование в составе газа-носителя (кроме инертного газа) синтетического воздуха (с содержанием 21.4 об. % кислорода и менее 0.0002 об. % метана по ТУ 2114-002-00153318-02) позволило изучить поведение каталитических систем в динамической окислительной атмосфере. Калибровку прибора по тепловым эффектам проводили на основе стандартных данных о температурах и энтальпиях фазовых переходов ряда веществ в широком диапазоне параметров. Исследования в динамической окислительной атмосфере (соотношение синтетический воздух : Не = 2.5) осуществляли в корундовых тиглях с крышкой, газ диффузионно поступал сверху, в качестве стандартов температур и энтальпий фазовых переходов использовали калибровку по In, KClO4, CsCl, K2CrO4, BaCO3, Au.
Измерения коэффициента теплопроводности углеродного волокна, образцов катализаторов на его основе и модельных образцов выполняли [10] на комплексном физическом анализаторе PPM System EverCool-II (“Quantum Design”, США). Коэффициент теплопроводности таблетированных образцов сравнения определяли аналогично [2], используя прибор LFA 457/2/G MicroFlash (“NETZSCH”, Германия), с учетом измерения реальной теплоемкости систем на приборе DSC8000 (“PerkinElmer”, США). Истинную плотность находили с помощью гелиевого пикнометра ULTRAPYK 1200e (“Quantachrome Instruments”, США).
Каталитическую активность изученных систем (КНУВ и гранулированных катализаторов сравнения) исследовали аналогично [2] в лабораторном проточном реакторе в режиме “stop&go” ежедневных рабочих смен при давлении 2 МПа и составе исходной смеси 95% синтез-газа с соотношением Н2/СО = 2 и 5% азота. Азот использовали в качестве внутреннего стандарта для хроматографического анализа; контроль температур осуществляли непосредственно в слое катализатора.
Для проведения каталитических испытаний образец КНУВ формовали специальным образом. Синтезированный катализатор представляет собой сложенные и плотноупакованные фрагменты первоначального жгута из исходного углеродного волокна длиной 35 мм со строго линейным и параллельным друг другу начальным расположением углеродных нитей. Некоторые нити в ходе обработок смешались, слегка изменяя длину фрагмента до ~40 мм. Дополнительным распрямлением и укладыванием в кварцевой лодочке формировали пакет длиной 35–40 мм, который затем заливали разогретыми мягкими восками (продуктами синтеза Фишера–Тропша). Пропитанный образец плотно окатывали в виде цилиндра под диаметр трубки 1/2 дюйма и в нем формировали ложбинку под карман для термопары. Это позволяло при расположении КНУВ внутри реактора полностью обходить карманы термопар без изменения геометрии образца. Дальнейшим поджатием образца к нижнему держателю катализатора из пористой керамики создавали плотную ровную упаковку на длину стандартной реакционной зоны.
Полученный КНУВ до проведения синтеза Фишера–Тропша активировали в токе водорода с объемной скоростью подачи газа (GHSV) 3000 ч–1 при 400°С и атмосферном давлении в течение 1 ч с одновременным удалением формовочных восков. Исходный синтез-газ и газообразные продукты СФТ анализировали аналогично [2] на хроматографе Кристалл-Люкс 4000М (“Мета-хром”, Россия). Для определения СО, СН4 и N2 применяли колонку (3 м × 3 мм) с молекулярными ситами СаА, а СО2 и углеводородов С2–С4 – HayeSep (также 3 м × 3 мм). Режим – температурно-программированный (60–200°С, скорость нагрева – 10°С/мин, детектор – катарометр, газ-носитель – гелий). Жидкие углеводороды С5+ анализировали с помощью газожидкостной хроматографии на капиллярной колонке с фазой DB-Petro в температурно-программированном (50–270°С) режиме. Детектор – ПИД, газ-носитель – гелий. Постепенный подъем расхода синтез-газа в лабораторном реакторе параллельно с повышением температуры осуществляли в ходе разработки катализаторов в течение 2–3 нед. вплоть до выхода на стационарный режим или достижения максимальных показателей.
Исследуемые системы (как исходный носитель, так и катализатор на его основе), а также извлеченный после СФТ из середины реактора сухой образец представляли собой пучки волокон, близкие к исходной ленте углеродного волокна (нить УКН-М-12К-1-760-ЭД производства ООО “Аргон”) с номинальной линейной плотностью 760 мг/м и плотностью нити 1.75 г/см3. Из таких нитей изготавливалось углеродное волокно УКН-12 000, являвшееся исходным сырьем при синтезе катализатора КНУВ.
Была отработана методика получения тонкого равномерного слоя оксида алюминия на поверхности волокна с термогравиметрическим контролем сдвига начала окисления углерода вследствие нанесения этого покрытия более чем на 100°С.
Катализатор КНУВ готовили путем последовательного (в два приема с промежуточной сушкой) нанесения из спиртового раствора нитрата кобальта на модифицированное НУВ и следующей за этим ступенчатой прокалки в сопоставимом с экструзионными катализаторами Фишера–Тропша режиме в токе воздуха с максимальной температурой 250°С. По изменению массы была определена концентрация активного компонента, которая составила, в расчете на металл, 1.1% Со. Благодаря многостадийному формированию оксидно-алюминиевого защитного слоя и пропитке каталитически активным кобальтом в растворе с “распушенной” лентой углеродного волокна при абсолютной доступности отдельных нитей для реактантов было реализовано равномерное нанесение компонентов, которое также сохранялось по длине и сечению полученного жгута катализатора.
РЕЗУЛЬТАТЫ И ИХ ОБСУЖДЕНИЕ
Схематично отличие обычного экструдированного блочного катализатора и катализатора из жгута волокон представлено на рис. 1.
Теплопроводность катализатора СФТ является одной из базовых характеристик, позволяющая сохранять высокую селективность процесса по С5+ до тех пор, пока генерируемое при синтезе тепло успевает отводиться из зоны реакции.
Исследование теплопроводности систем показало (табл. 1), что и носитель, и катализаторы имеют повышенный коэффициент теплопроводности по сравнению с обычными для пористых керамических катализаторов величинами, составляющими порядка 0.2–0.3 Вт м–1 К–1.
Таблица 1.
Коэффициенты теплопроводности модельных систем и катализатора КНУВ
Образец | λ*, Вт м–1 К–1 | Масса исследованного образца, г |
---|---|---|
Фехраль | 13 | 0.0755 |
УКН-12000, исх. волокно 1 | 42 | 0.0140 |
УКН-12000, исх. волокно 2 | 40 | 0.0127 |
УКН-12000, исх. волокно 3 | 19 | 0.0828 |
КНУВ, носитель | 63 | 0.0126 |
КНУВ, носитель | 53 | 0.0034 |
КНУВ, кат. исходный 1 | 186 | 0.0032 |
КНУВ, кат. исходный 2 | 140 | 0.0028 |
КНУВ, кат. после синтеза | 23 | 0.0159 |
КНУВ, кат. после синтеза, отмыта от углеводородов | 67 | 0.0120 |
Для измерения коэффициента теплопроводности, из-за гибкости углеродного волокна и невозможности качественно закрепить его на плоскости измерительной ячейки прибора, была реализована специальная сборка. С целью создания эффективного стока тепла на датчики исходное или обработанное углеродное волокно, сложенное в максимально плотно упакованную связку, обрабатывали серебряной пастой в местах крепления контактов в соответствии со схемой, представленной на рис. 2.
Рис. 2.
Пучок исследуемого на теплопроводность образца с контакными точками серебряной пасты (а) и контактами датчика (б); держатель образца в сборке (в).
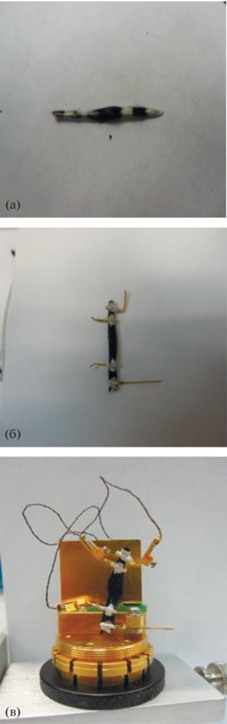
После нанесения серебряной пасты по сечению пучка волокон для равномерного смачивания каждого волокна (рис. 2а) образец сушили до воздушно-сухого состояния. Затем образец погружали в ложбинку на плоскости держателя и плотно зажимали сверху (сборка на рис. 2б) наконечниками датчиков ровно по положению линий от высохшей серебряной пасты. После этого полученные контакты вновь закрепляли, нанося поверх дополнительный тонкий слой серебряной пасты (рис. 2в).
Необходимую для определения коэффициента теплопроводности величину площади сечения пучка волокон находили из экспериментальных данных расчетным путем по одинаковому для всех изученных систем алгоритму.
Например, масса катализатора, извлеченного из зоны равномерного нагрева реактора после синтеза Фишера–Тропша, составляет mобр = = 0.0159 г. При паспортном значении плотности нити его объем равен:
Длина образца lобр = 2.2490 см. Принимая, что все углеродное волокно представлено фибриллами цилиндрической формы, получаем площадь сечения образца:
Корректность полученных результатов подтверждается поверочным расчетом. По паспортным данным исходное углеродное волокно УКН-12 000 содержит около 12000 фибрилл в ленте. Согласно данным растровой электронной микроскопии исходного углеродного волокна радиус фибриллы (rфибр) равен 3 мкм (3 × 10–6 м). Отсюда площадь сечения одной фибриллы
Принимая во внимание, что в извлеченном из реактора образце может содержаться больше, чем одна целая лента исходного НУВ, наблюдается хорошая сходимость расчетных величин. Кроме того, наличие на катализаторе после синтеза некоторого количества продуктов завышает массу образца, и, соответственно, расчетные значения объема и площади сечения образца.
При измерении в качестве стандартной пробы коэффициента теплопроводности для расположенной строго линейно фехралевой проволоки диаметром 0.8 мм (расстояние между точками l2, 3 = = 12.6 мм) было получено значение λ = 13 Вт м–1 К–1. Согласно данным [11] для импортных фехралей λ = 13–16.5 Вт м–1 К–1. Для проволоки российского производства Н23Ю5Т значение коэффициента теплопроводности не гостируется, однако по [12] ее температуропроводность равна 0.34 × × 10–5 м2/с, удельная теплоемкость – 0.48 кДж кг–1 К–1, а плотность – 7.21 г/см3. Отсюда расчетное значение λ = 11.76 Вт м–1 К–1, что очень близко к экспериментально определенной величине и подтверждает корректность используемой методики. Хорошая сходимость экспериментально определенного коэффициента теплопроводности для фехраля с табличными данными доказывает достоверность получаемых значений.
Результаты измерений (табл. 1) для исходного волокна УКН-12 000 свидетельствуют (при общей воспроизводимости эксперимента) о влиянии массы взятой пробы на фиксируемые величины. Для образца с большей массой найденное значение коэффициента теплопроводности было меньше. В случае носителя и катализатора КНУВ такой зависимости не наблюдается, причем величина, определенная для исходного катализатора, много больше, чем для носителя.
Значение коэффициента теплопроводности исходного катализатора приближается к величине такового для графитов (100–350 Вт м–1 К–1) при отсутствии существенных видимых отличий, которые могли бы приводить к значимой разнице теплопроводности катализатора и носителя.
Известно, что методически корректное определение [13] коэффициента теплопроводности с точностью (±5%) на используемом нами приборе зависит от сечения образца и для высоких значений (10–250 Вт м–1 К–1) проводится на системах сечением 1 мм2 и менее. При коэффициенте теплопроводности, по данным производителя [14], углеволокна на основе ПАН до 70 Вт м–1 К–1 обычно наблюдаемый коэффициент теплопроводности волокон составляет около 7–8 Вт м–1 К–1, что подтверждает разумность зафиксированных значений (табл. 1).
Это позволяет предположить, что основную роль в получаемом значении величины (кроме собственно теплопроводящих свойств материала) играет полнота смачивания каждого филамента серебряной пастой, которая для малого количества волокон существенно выше. Если же в эксперименте используется более толстый пучок волокон, то не все его составляющие могут быть достаточно хорошо зафиксированы серебряной пастой и не участвуют в процессе теплопередачи, хотя входят в расчетную величину сечения. Этот же эффект может играть свою отрицательную роль в значимом снижении теплопроводности отработанного катализатора после проведения синтеза Фишера–Тропша в связи с присутствием углеводородов на поверхности и ухудшением контакта пасты с филаментами. Контрольный эксперимент (табл. 1) с тщательно отмытым от сорбированных углеводородов (многократной последовательной экстракцией гептаном, гексаном и диэтиловым эфиром) катализатором показал, что значение коэффициента теплопроводности возрастает до уровня исходного носителя, однако остается существенно меньше такового для исходного катализатора. Это может указывать на значимую роль в образовании контактов между филаментами губчатых кобальтоксидных структур, которые наблюдаются методом электронной микроскопии. Они могут заполняться серебряной пастой и обеспечивать столь высокую теплопроводность. В случае катализатора после синтеза при простой экстракции без термовакуумной обработки, очевидно, не происходит удаления продуктов из этих структур. Соответственно, они не заполняются серебряной пастой и даже при физическом контакте (через них) филаментов друг с другом коэффициент теплопроводности отработанного образца не увеличивается до величины, характерной для исходного катализатора.
Таким образом, реальная теплопроводность КНУВ существеннейшим образом зависит как от плотности упаковки волокон внутри реактора, так и от накопления тяжелых продуктов синтеза. При этом она все равно остается намного выше, чем у традиционно используемых каталитических систем. Также следует иметь в виду, что основной теплосъем в реакторе в целом реализуется потоком газа, для которого в случае катализатора такого типа практически отсутствуют диффузионные сопротивления.
Совокупность данных ряда физико-химических аппаратурных методов, рассмотренных ниже, убедительно показывает, что нанесение переходного оксидно-алюминиевого слоя и введение кобальта существенным образом меняют структуру катализатора по сравнению с исходным волокном и обуславливают отложение на поверхности КНУВ высокомолекулярных продуктов, ведущих в дальнейшем к его дезактивации.
Необходимое для создания эффективно работающих центров СФТ предварительное нанесение оксида алюминия на поверхность углеродного волокна уменьшает его дефектность и создает защитное покрытие, качество которого возможно контролировать [15] по сдвигу начала окисления на воздухе в режиме термогравиметрического анализа (ТГА). Была разработана отличающаяся от [15] методика нанесения защитного оксидно-алюминиевого слоя на НУВ из раствора оксихлорида алюминия такого же состава, который позволял [16] получать прочные нити оксида алюминия. Используемый при синтезе непрерывных поликристаллических волокон оксида алюминия формовочный органический полимер (поливиниловый спирт) обладает высокой сорбционной способностью к НУВ. Данное обстоятельство способствует созданию на внешней поверхности НУВ протяженного, практически бездефектного, очень тонкого защитного слоя оксида алюминия, который будет далее служить для фиксации каталитически активного металла и, вместе с тем, не препятствовать передаче тепла высокоэкзотермичной реакции к углеродному волокну и стоку по нему. Отметим, что при взаимодействии полимерного золя и ионов соли, оксидов металлов с выдержкой в гидротермальных условиях при 350°С происходит структурирование с образованием тубуленов, содержащих металлы со средним размером 50 нм, а при 200°С возникают слоистые нанопленки толщиной до 5 нм и металлсодержащими нанокристаллами между слоями.
Отработанная с помощью ТГА для модельного образца (200 мм) жгута НУВ методика нанесения оксидно-алюминиевого покрытия позволила защитить поверхность и сдвинуть температуру начала окисления более чем на 100°С относительно исходного волокна (рис. 3).
Отметим, что для корректного определения свойств защитного слоя в режиме ТГА согласно предложенной методике недопустимо обрезать образец и необходимо исследовать только полностью обработанные волокна, иначе происходит окисление через открытые торцы волокна. Поскольку по предварительным данным [15] на поверхности НУВ может осаждаться не более 1–1.5 мас. % Al2O3, то при приготовлении пропиточных растворов (с учетом неполноты протекания реакций) брали 10-кратный избыток алюминия относительно этих величин. Расчетные количества веществ корректировали пропорционально содержанию волокна в жгуте исходя из плотного заполнения реакционной зоны по всему диаметру лабораторного реактора при толщине ленты НУВ равной 0.25 мм.
Источником Al2O3 является оксихлорид, который одновременно модифицирует поверхность углеродного волокна, создавая дополнительные центры фиксации. В зависимости от рН равновесное содержание мономерных и полимерных форм в растворе оксихлорида существенно различается. При рН 3.7–3.8 количество полимеров составляет 35–40%, поэтому значение рН в процессе получения поддерживали в диапазоне 3.7–4.4. Пропиточный 0.4 М раствор оксихлорида алюминия готовили при непрерывном длительном перемешивании на магнитной мешалке смеси AlCl3 ⋅ 6H2O и металлического алюминия (порошок АСД6) при нагреве до 80–90°С и приборном контроле заданного рН.
Раствор кристаллического поливинилового спирта (ПВС) в воде также готовили длительным перемешиванием при 90°С до полного растворения и медленно остужали до комнатной температуры с визуальным контролем отсутствия коагуляции. Перед нанесением оксихлорида на углеродное волокно с него предварительно удаляли аппрет (за несколько итераций смесью с объемным соотношением этанол : ацетон = 50 : 50). Далее в пропиточный раствор, содержащий приготовленный ПВС, оксихлорид и избыточный AlCl3 помещали отмытое от аппрета и высушенное НУВ. Систему перемешивали при 70–80°С в течение 1 ч в ультразвуковой бане, извлекали на следующий день, сушили и прокаливали на воздухе при ступенчатом нагреве до 300°С. Затем с этим же образцом повторно проводили такую же обработку, но с последующим прокаливанием при нагреве до 590°С в токе инертного газа, а после этого осуществляли третье нанесение с аналогичным прокаливанием и окончательным термолизом при 900°С с образованием γ-Al2O3. Изменение массы модифицированного образца по сравнению с исходным указывает на суммарное введение в состав носителя 2.84 мас. % γ-Al2O3. С учетом возможной динамики веса образца при промежуточных прокалках можно принять, что содержание оксида алюминия составляет порядка 3 мас. %.
Кобальт наносили из спиртового раствора нитрата в несколько приемов по максимальной сорбции на предварительно полученный и прокаленный модифицированный носитель. Первоначальную пропитку (исходя из вводимого расчетного количества 1% Со) производили в герметичной колбе при полном покрытии волокон раствором (50°С, 6 ч) и дополнительно выдерживали в течение 50 ч при комнатной температуре до практически полного обесцвечивания раствора нитрата кобальта. Контрольный эксперимент со второй порцией такого же раствора при комнатной температуре за 18 ч показал отсутствие значимого обесцвечивания раствора. Извлеченное волокно нагревали до 250°С в токе воздуха в стандартном режиме прокалки катализатора для разложения нитрата и формирования поверхностных структур. Изменение массы полученного образца по сравнению с исходным носителем дало концентрацию нанесенного металла 1.1% Со в расчете на весь катализатор и, соответственно, около 30% на его оксидно-алюминиевый компонент.
Катализатор после синтеза (рис. 4а) теряет существенно бóльшую массу, чем исходный. Соответственно, после окисления в токе воздуха масса зольного остатка для отработанного катализатора составляет 3% против 10.7%. Одновременно наблюдается рост величины экзоэффекта окисления в области температур 300–650°С (рис. 4б) при практически неизменном положении основного максимума ДТГ (рис. 4в), обусловленного окислением собственно углеродного волокна и возникающих обуглероженных смолообразных продуктов деструкции из полученных при СФТ углеводородов. Эти данные свидетельствуют о наличии на поверхности извлеченного из реактора катализатора КНУВ высокомолекулярных углеводородов и восков, которые окисляются в токе воздуха или частично улетучиваются в процессе термовакуумной обработки (табл. 2).
Рис. 4.
ТГА в токе кислородсодержащего газа для исходного КНУВ (–) и после проведения СФТ (–): а – потери массы; б – термоэффекты; в – кривые ДТГ.
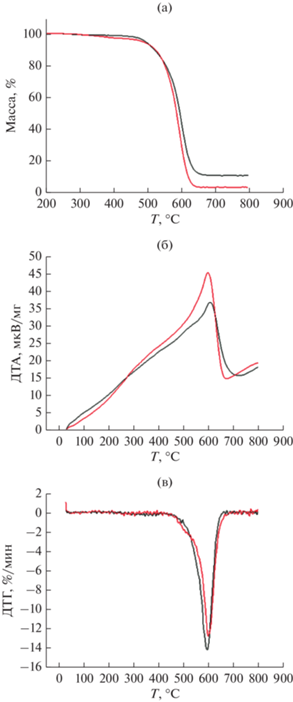
Наблюдаемые потери массы при пробоподготовке для исследования структурных параметров и величин удельной поверхности систем представлены в табл. 2.
Обычно в связи с проникновением в поры носителя пропиточного раствора и закрытия части устьев пор солевым компонентом поверхность катализатора меньше, чем поверхность носителя. В нашем случае динамика изменения удельной поверхности образцов контрастирует с той, что характерна для катализаторов на носителях с развитой пористой поверхностью. Однако с полученными результатами согласуются все остальные данные по исследованию структурных характеристик систем (рис. 5–8).
Рис. 5.
Распределение удельной поверхности пор по радиусам, найденное из адсорбционной ветви изотермы адсорбции–десорбции по модели BJH для носителя КНУВ (–) и катализатора (–).
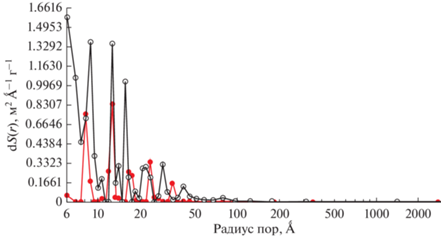
Рис. 6.
Изменение удельной поверхности в зависимости от радиуса пор по модели BJH для носителя КНУВ (–), исходного катализатора (–) и катализатора после СФТ (–).
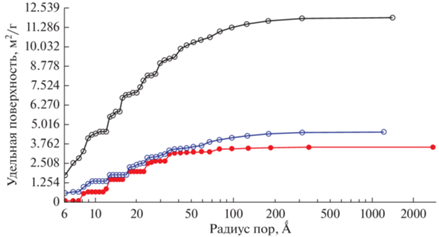
Рис. 7.
Изменение объема пор в зависимости от радиуса пор по модели BJH для носителя КНУВ (–), исходного катализатора (–) и катализатора после СФТ (–).
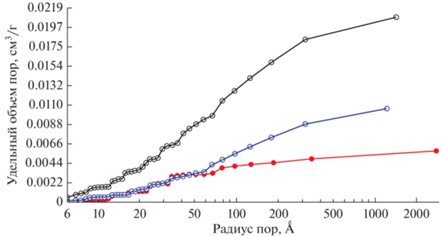
Рис. 8.
Распределение объема пор по радиусам, найденное из адсорбционной ветви изотермы адсорбции–десорбции по модели BJH для исходного катализатора КНУВ (–) и катализатора после СФТ (–).
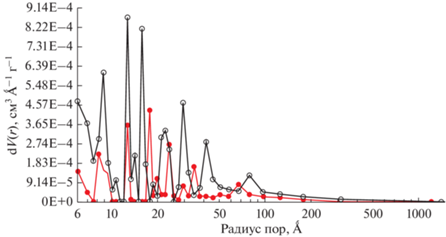
Введение кобальтсодержащего компонента приводит к росту количества пор в катализаторе по сравнению с носителем и практически неизменному в диапазоне микропор их распределению по радиусам. Поскольку непористое углеродное волокно обладает только небольшой собственной внешней поверхностью, очевидно, что эти поры образованы контактирующими частицами нанесенных оксидов или находятся внутри них. Это обуславливает возрастание (рис. 6, 7) как величины удельной поверхности, так и объема пор при нанесении каталитически активной фазы. Отложение продуктов на поверхности и в порах системы приводит к тому, что для катализатора после синтеза эти показатели существенно снижаются (рис. 6, 7). Распределение пор по размерам изменяется при этом незначительно (рис. 8).
Столь необычное поведение находит подтверждение при рассмотрении данных электронной микроскопии, которые объясняют происходящие в ходе формирования носителя и катализатора изменения.
Носитель (рис. 9) представляет собой в основном параллельно расположенные модифицированные филаменты (рис. 9а) исходного углеродного волокна. Причем однородность поверхности волокон весьма высока, и лишь незначительная часть (черные пятна, рис. 9б, 9в) отличается от основной поверхности. По данным локального рентгеновского анализа в точках (рис. 10, табл. 3) найдено, что серый цвет (рис. 9, 10) относится к поверхностному алюминию (оксиду алюминия), а черные пятна – остатки незакрытой поверхности углеродных филаментов. Как следует из рис. 9в, при очень большом увеличении (×150 000) на тонкой поверхностной пленке оксида алюминия видны редкие объемные кластеры малого размера (островок в центре снимка).
Рис. 10.
Микрофотография СЭМ единичного волокна носителя КНУВ с обозначением точек анализа поверхности методом EDS.
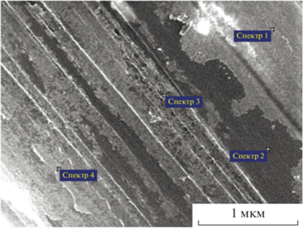
Таблица 3.
Содержание элементов в анализируемых точках поверхности по данным EDS
Точка анализа поверхности | Содержание элементов, ат. % | ||
---|---|---|---|
C | O | Al | |
Точка 1 | 96.60 | 3.21 | 0.19 |
Точка 2 | 97.97 | 1.98 | 0.05 |
Точка 3 | 97.90 | 2.03 | 0.06 |
Точка 4 | 97.92 | 1.95 | 0.13 |
Среднее | 97.60 | 2.29 | 0.11 |
Станд. отклонение | 0.67 | 0.61 | 0.07 |
Таким образом, практически вся поверхность отдельных филаментов при модифицировании покрывается наноразмерным однородным слоем оксида алюминия. Носитель КНУВ представляет собой волокна из углерода с корочковым покрытием тонким слоем Al2O3. Очевидно, что в каталитической системе будет эффективная передача тепла от активного центра через поверхностный оксид алюминия к углеродному волокну, с одной стороны, и в омывающий нить поток синтез-газа – с другой.
Введение кобальтсодержащего компонента при формировании катализатора (рис. 11а) приводит к появлению объемных кластеров оксида кобальта размером до 0.6–0.7 мкм, расположенных островками на оксидноалюминиевой пленке (рис. 11б). Каждый из этих кобальтсодержащих островков обладает развитой губчатой пористой структурой (рис. 11в, 11г), хорошо видимой при большом увеличении (рис. 11г). Последнее однозначно объясняет резкое возрастание (табл. 2) поверхности катализатора по сравнению с носителем.
Рис. 11.
Микрофотографии СЭМ исходного катализатора КНУВ; а – общий вид волокон КНУВ; б – кластеры оксида кобальта на оксидноалюминиевом покрытии УВ; в, г – губчатая структура кластеров оксида кобальта.
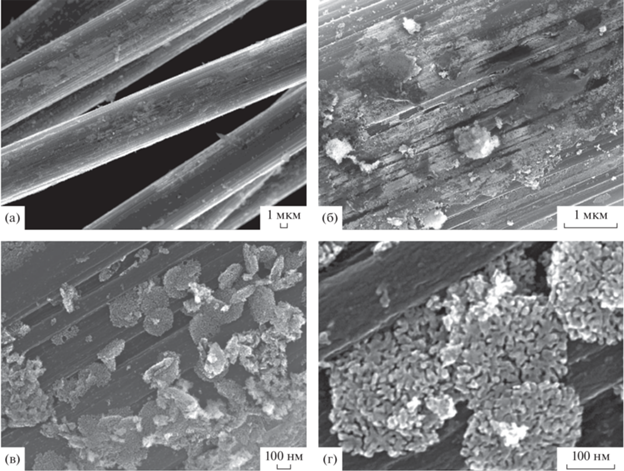
Следует отметить, что в противоположность экструдированному катализатору с терморасширенным графитом, для которого было зафиксировано [2] присутствие в исходном невосстановленном образце металлического кобальта, в изучаемой в настоящей работе системе кобальт по приготовлению содержится только в оксидной форме. Это хорошо видно в электронном микроскопе при картографировании распределения элементов на наблюдаемой поверхности. По-видимому, такое отличие обусловлено отсутствием прямого контакта термолизуемой соли кобальта с углеродным волокном, которое покрыто практически сплошной переходной пленкой оксида алюминия.
На катализаторе после проведения синтеза по данным СЭМ фиксируются (рис. 12) хорошо различимые белые аморфные отложения восков. Соотношение кислорода и кобальта в точках под этими отложениями по данным EDS существенно (в 8–10 раз) меньше обычного. Это однозначно указывает на то, что значительная часть кобальта присутствует в восстановленной форме под слоем восков, защитивших его от окисления после извлечения из реактора.
Рис. 12.
Отложения восков после синтеза на катализаторе КНУВ: а – единичная фибрилла; б – поверхность катализатора.
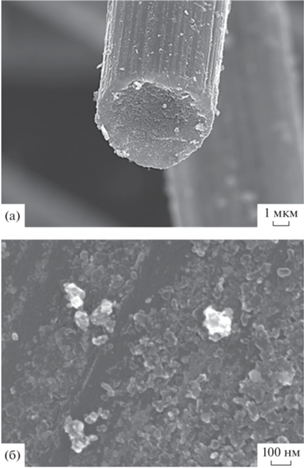
Наличие найденных на поверхности методом электронной микроскопии высокомолекулярных углеводородов, блокирующих кристаллиты кобальта и тормозящих реакцию, однозначно коррелирует с рассмотренными выше термогравиметрическими данными (рис. 4). Эти же высокомолекулярные продукты синтеза Фишера–Тропша закрывают губчатую структуру кластеров кобальтсодержащего компонента, что обусловливает уменьшение фиксируемой по методу БЭТ поверхности катализатора после синтеза (табл. 2) и изменение структурных характеристик (рис. 5–8).
Если на поверхности углеродного носителя (терморасширенный графит, ТРГ) кобальтсодержащий компонент находится в основном в агломерированном виде, то в случае КНУВ картина несколько отличается. Для катализатора 33Со/ТРГ главные эффекты на кривой ТПВ-Н2 (рис. 13) наблюдаются в виде плеча при 384°С, максимума при 426°С с точкой перегиба при 413°С и протяженного максимума выше 600°С, относящегося к восстановлению иммобилизованного на поверхности оксида кобальта [17]. Несмотря на большое количество окисленных центров поверхности исходного ТРГ, получаемого взрывным разложением интеркалята с азотной кислотой, удельный вклад иммобилизованных восстанавливаемых структур в КНУВ существенно выше. При этом последовательно (265, 368, 425, 456 и >550°С) фиксируются низкотемпературные эффекты кобальтсодержащих стейнеритных фаз на поверхности оксида алюминия, агломерированных и иммобилизованных структур с существенно меньшим удельным вкладом в профиль восстановления до массивного металла (основной острый максимум). Небольшое смещение положения максимумов в случае КНУВ, по-видимому, обусловлено лучшим теплоотводом по волокну и необходимостью (по сравнению с терморасширенным графитом) более высокой температуры для протекания реакции восстановления.
Рис. 13.
Кривые ТПВ-Н2 кобальтсодержащих систем КНУВ (1.1% Со) и 33Со/ТРГ. Интенсивность 33Со/ТРГ пересчитана на концентрацию кобальта 1.1%.
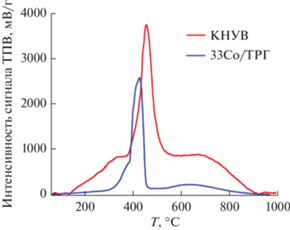
Исследование каталитической активности в синтезе Фишера–Тропша восстановленных систем в установившемся режиме (табл. 4) показало, что основные показатели для кобальтового катализатора на модифицированном углеродном волокне и на носителе с большим содержанием терморасширенного графита со связующим (дисперал) практически идентичны. При термолизе носителя дисперал переходит в оксид алюминия, и образуется композиция, аналогично КНУВ, в значительной мере состоящая из покрытого оксидом алюминия графита. Остальная часть связующего дает оксид алюминия, частично реагирующий с вводимым кобальтом. Отметим, что находящийся непосредственно на поверхности ТРГ каталитически активный металл создает агломерированные [2] и слабо связанные с углеродом образования. Таким образом, очень близкие значения активности катализатора на покрытом защитным оксидным слоем НУВ (в расчете на грамм кобальта) и формованного катализатора указывают на идентичность работающих в СФТ структур и отсутствие диффузионных сопротивлений в случае экструдированной системы, а также на ее достаточную теплопроводность. Максимальная производительность для КНУВ, равная 240.2 мольСО${\text{г}}_{{{\text{Со}}}}^{{ - 1}}$ с–1, достигается при объемной скорости 1000 ч–1 и температуре 280°С, однако селективность по С5+ при этом снижается до 36%.
Таблица 4.
Активность катализаторов СФТ
Катализатор | Т, °С | GHSV, ч–1 |
KСО, % | SC5+, % | ${{S}_{{{\text{C}}{{{\text{H}}}_{4}}}}},$ % | A × 106, мольСО${\text{г}}_{{{\text{Со}}}}^{{ - 1}}$ с–1 |
Производи-тельность, гС5+ кг–1 ч–1 |
---|---|---|---|---|---|---|---|
КНУВ, 1.1% Со |
250 | 400 | 35 | 51 | 26 | 88.77 | 25 |
20% Со/(20% DP2 + + 80% ТРГ)* | 250 | 5000 | 54 | 50 | 28 | 86.63 | 435 |
20% Со/(20% DP2 + + 30% Hβ + 50% ТРГ)** | 229 | 5000 | 79 | 58 | 23 | 86.26 | 503 |
* Пропиточный катализатор. Коэффициент теплопроводности таблетированного носителя составляет 7.3 Вт м–1 К–1 в нормальном направлении и 29.83 Вт м–1 К–1 в тангенциальном. ** Пропиточный катализатор. Коэффициент теплопроводности таблетированного носителя составляет 2.2 Вт м–1 К–1 в нормальном направлении и 15.23 Вт м–1 К–1 в тангенциальном.
Ранее [18] в условиях синтеза Фишера–Тропша наблюдалось образование центров с эффективным зарядом (δ+), представляющих собой кобальт на оксидной подложке – кластеры восстановленного металла, находящиеся на окисленной поверхности кобальтсодержащей поверхностной структуры протошпинельного типа в катализаторах на базе носителей, включающих в себя оксид алюминия, цеолит и другие оксиды. Такие иммобилизованные поверхностные кобальтоксидные структуры, для которых характерен максимум на кривой ТПВ-Н2 (для исходного или предварительного восстановленного в условиях активации СФТ образца) в диапазоне температур 500–800°С, остаются в составе восстановленного катализатора. И именно на них за счет частичного переноса заряда с металла (наличие которого установлено корректными данными по работе выхода электрона), возникают активные и селективные [19] в образовании жидких углеводородов центры Соδ+.
При меньшей концентрации образующего перколяционную теплопроводящую сеть графита (табл. 4) в составе носителя активность катализатора, близкая к величинам для двух других систем, наблюдается при значительном температурном сдвиге, что однозначно указывает на реализующиеся в этом случае относительные перегревы внутри зерна. Таким образом, катализатор КНУВ может являться реперной точкой констатации отсутствия локальных перегревов и диффузионных сопротивлений для реальных высокопроизводительных катализаторов синтеза Фишера–Тропша. При этом в целом производительность синтеза для КНУВ, определяемая концентрацией активного компонента, остается низкой, и создание промышленного катализатора СФТ на базе протяженного компактированного жгута (сборки) углеродных волокон представляется нецелесообразным.
ЗАКЛЮЧЕНИЕ
В процессе исследования рядом физико-химических методов носителя, исходного и отработавшего в синтезе Фишера–Тропша катализатора КНУВ, представляющего собой углеродные нити, на поверхность которых последовательно нанесен оксид алюминия и оксид кобальта, установлено:
1) при формировании носителя на поверхности углеродных нитей образуется чрезвычайно тонкая и равномерная пленка из оксида алюминия, покрывающая почти всю цилиндрическую поверхность филаментов;
2) при синтезе катализатора путем введения в его состав оксида кобальта на сформированной оксидноалюминиевой пленке возникают губчатые островковые кластеры размером до 700 нм. В отличие от обычных нанесенных систем, в которых поверхность первоначального носителя существенно больше, это обуславливает возрастание удельной поверхности (по БЭТ) по сравнению с носителем почти в 6 раз;
3) наличие практически сплошной пленки оксида алюминия на поверхности углеродных нитей препятствует прямому контакту углерода с оксидом кобальта и, в отличие от катализатора на базе экструдатов носителя с чешуйчатым графитом, при формировании такой системы не обнаруживается металлический кобальт, возникающий при термолизе за счет восстановления углеродом;
4) катализатор обладает очень высокой теплопроводностью, величина которой может быть сопоставима с теплопроводностью графита;
5) благодаря высокой теплопроводностью системы в ходе синтеза Фишера–Тропша эффективно формируются высокомолекулярные продукты, которые остаются на поверхности катализатора и блокируют реакционные центры. При этом образующиеся воски заполняют пористую систему кластеров кобальта, что обуславливает изменение структуры катализатора и снижение величины поверхности катализатора во время и после синтеза;
6) синтезированный на базе углеродных волокон кобальтовый катализатор является модельным и может служить реперной точкой для констатации отсутствия локальных перегревов и диффузионных сопротивлений в реальных высокопроизводительных катализаторах синтеза Фишера–Тропша.
Список литературы
Mordkovich V.Z., Sineva L.V., Solomonik I.G., Ermolaev V.S., Mitberg E.B. Patent WO2011016759, 2011.
Asalieva E., Sineva L., Sinichkina S., Solomonik I., Gryaznov K., Pushina E., Kulchakovskaya E., Kulnitskiy B., Ovsyannikov D., Mordkovich V. // Appl. Catal. A: General. 2020. V. 601. P. 117639. https://doi.org/10.1016/j.apcata.2020.11763
Holmen A., Venvik H.J., Myrstad R., Zhu J., Chen D. // Catal. Today. 2013. V. 216. P. 150. https://doi.org/10.1016/j.cattod.2013.06.006
Zarubova S., Rane S., Yang J., Yu Y., Zhu Y., Chen D., Holmen A. // ChemSusChem. 2011. V. 4. P. 935. https://doi.org/10.1002/cssc.201100046
Gerber I.C., Serp P. // Chem. Rev. 2020. V. 120. № 2. P. 1250. https://doi.org/10.1021/acs.chemrev.9b00209
Ghogia A.C., Nzihou A., Serp P., Soulantica K., Pham Minh D. // Appl. Catal. A: General. 2021 V. 609. P. 117906.
Chen Y., Wei J., Duyar M.S., Ordomsky V.V., Khodakov A.Y., Liu J. // Chem. Soc. Rev. 2021. V. 50. P. 2337. https://doi.org/10.1039/d0cs00905a
Chernyak S.A., Suslova E.V., Egorov A.V., Lu L., Savilov S.V., Lunin V.V. // Fuel Process. Technol. 2015. V. 140. P. 267. https://doi.org/10.1016/j.fuproc.2015.09.012
Chernyak S., Burtsev A., Egorov A., Maslakov K., Savilov S., Lunin V. // Funct. Mater. Lett. 2020. V. 13. № 04. P. 2050021. https://doi.org/10.1142/S1793604720500216
PPMS thermal-transport application note. http://www.qdusa.com
http://specsplav-vdm.ru/fehral-marka-h23yu5t
ГOCT 12766.1 90.
PPMS TTO manual B0.pdf
Технический бюллетень компании “Kureha Corporation”, https://www.kureha.co.jp/en/business/material/pdf/KRECA_eng.pdf
Урванов С.А. Модифицирование поверхности углеродного волокна углеродными наноструктурами. Дис. … к. х. н. М.: МГУ им. М.В. Ломоносова, 2016.
Балинова Ю.А. Непрерывные поликристаллические волокна оксида алюминия для композиционных материалов. Дис. …к. т. н. М.: ФГУП “ВИАМ”, 2012.
Solomonik I.G., Gryaznov K.O., Skok V.F., Mordkovich V.Z. // RSC Adv. 2015. V. 5. P. 78586. https://doi.org/10.1039/C5RA11853K
Lapidus A.L., Krylova A.Yu., Kazanskii V.B., Borovkov A.Yu., Zaitsev A.V., Rathouslj J., Zukal A., Jan Edlkovi M. // Appl. Catal. 1991. V. 73. P. 65.
Solomonik I.G., Sineva L.V., Mordkovich V.Z. // Abstracts, IX International Conference “Mechanisms of catalytic reactions”. October 22–25, St. Peterburg, 2012. P. 267.
Дополнительные материалы отсутствуют.
Инструменты
Кинетика и катализ