Коллоидный журнал, 2022, T. 84, № 4, стр. 433-452
Формирование на поверхности трековых мембран гидрофобных и супергидрофобных покрытий с целью создания композиционных мембран для опреснения воды
Л. И. Кравец 1, *, М. А. Ярмоленко 2, А. В. Рогачев 2, Р. В. Гайнутдинов 3, В. А. Алтынов 1, Н. Е. Лизунов 1
1 Объединенный институт ядерных исследований, Лаборатория ядерных реакций
им. Г.Н. Флерова
141980 Московская обл., г. Дубна, ул. Жолио-Кюри, д. 6, Россия
2 Гомельский государственный университет им. Ф. Скорины
246019 Гомель,
ул. Советская, д. 104, Беларусь
3 Федеральный научно-исследовательский центр “Кристаллография
и фотоника” РАН
119333 Москва, Ленинский пр., д. 59, Россия
* E-mail: kravets@jinr.ru
Поступила в редакцию 31.03.2022
После доработки 13.05.2022
Принята к публикации 16.05.2022
- EDN: CPFTVI
- DOI: 10.31857/S0023291222040085
Аннотация
Рассмотрены способы формирования покрытий на поверхности гидрофильной трековой мембраны из полиэтилентерефталата с помощью метода электронно-лучевого диспергирования полимеров в вакууме. Показано, что применение данного метода при использовании в качестве мишени для диспергирования сверхвысокомолекулярного полиэтилена и полипропилена позволяет получать на поверхности мембраны гидрофобные и высокогидрофобные покрытия с морфологически развитой структурой. Осаждение на их поверхности тонкого слоя политетрафторэтилена электронно-лучевым диспергированием приводит к формированию супергидрофобного покрытия. Для получения на поверхности мембраны однослойного супергидрофобного покрытия в качестве мишени использован политетрафторэтилен. Методами атомно-силовой и растровой электронной микроскопии исследованы морфология и структура поверхности полученных композиционных мембран. Химический состав осажденных на поверхности трековой мембраны полимерных покрытий изучен методом рентгеновской фотоэлектронной спектроскопии. Показано, что композиционные мембраны разработанного образца могут быть использованы в процессах опреснения водного раствора хлорида натрия методом мембранной дистилляции. Установлено, что использование тонкого гидрофобного слоя в сочетании с толстой гидрофильной основой позволяет повысить производительность процесса мембранной дистилляции.
ВВЕДЕНИЕ
Для опреснения солeных и солоноватых вод перспективно использование метода мембранной дистилляции (МД), в основе которого лежит проницаемость микропористой мембраны для водяного пара при одновременной непроницаемости для воды [1–3]. Данный метод обладает рядом преимуществ по сравнению с другими процессами разделения (дистилляция, электродиализ, обратный осмос и др.), основным из которых является высокая селективность разделения. Рабочие температуры в процессе мембранной дистилляции значительно ниже (обычно температура разделяемой смеси находится в диапазоне от 50 до 80°С), чем в традиционном процессе дистилляции. Поэтому в этом случае нет необходимости нагревать смесь до температуры кипения. Это делает данный процесс экономически привлекательным. Поскольку движущей силой МД является разность температур, а не давлений, то рабочие давления по сравнению с такими мембранными процессами, как обратный осмос, невелики. Это делает процесс мембранной дистилляции технологически более безопасным. Кроме того, при проведении МД тепловые потери в окружающую среду незначительны по сравнению с другими процессами.
Для проведения процесса мембранной дистилляции применяют мембранно-дистилляционные модули. В настоящее время известны четыре основных варианта конфигураций модуля для реализации данного процесса: мембранный дистиллятор прямого контакта, мембранный дистиллятор с воздушным зазором, мембранный дистиллятор с газовой сдувкой конденсата и вакуумный мембранный дистиллятор [4, 5]. Конфигурация модуля с воздушным зазором является оптимальной, поскольку имеющийся воздушный зазор обеспечивает значительное снижение теплопотерь по сравнению с другими модулями благодаря наличию конденсирующей перегородки и большей разности температур между горячей и охлажденной поверхностями, а также обеспечивает более высокую тепловую энергию для испарения воды [6].
Основным элементом в разделительных модулях, применяемых в процессах мембранной дистилляции, являются мембраны. Как правило, для этих целей используются производимые промышленностью гидрофобные микрофильтрационные мембраны из полипропилена, поливинилиденфторида и политетрафторэтилена в виде пленок, трубок или волокон [7, 8], которые имеют значительное сопротивление массообмену и, вследствие этого, низкую производительность. Для успешной реализации процессов опреснения солeных и солоноватых вод необходимо создание нового поколения высокопроизводительных мембран, эффективных в термоградиентных (протекающих под действием градиента температуры) процессах разделения, к которым относится метод мембранной дистилляции. В литературе имеется незначительное число работ, посвященных вопросам создания мембран, специально предназначенных для мембранной дистилляции. Лишь в последние 5−10 лет появились публикации, посвященные получению специальных мембран для этого процесса и изучению их поверхностных и структурных характеристик. Среди них можно отметить работы, в которых были предприняты попытки с помощью физико-химических методов получить на поверхности гидрофильных микропористых мембран тонкий гидрофобный слой, который определяет функциональные свойства созданных композиционных мембран. Авторами этих работ показано, что использование тонкого гидрофобного слоя в сочетании с толстой гидрофильной основой позволяет увеличить поток пермеата через мембрану [9–13].
В этой связи изучение физико-химических закономерностей и технологических принципов направленного изменения структуры и поверхностных свойств гидрофильных мембран путем нанесения на их поверхность гидрофобных покрытий является актуальной задачей. Для этого возможно использование широкого круга методов модифицирования, которые условно разделяются на растворные и безрастворные методы. Среди растворных способов можно выделить химические и электрохимические методы, метод пропиткой гидрофобизирующими агентами или нанесения тонких пленок Ленгмюра−Блоджетт [14, 15]. Основными преимуществами данных способов являются доступность и технологическая простота. Однако, основная проблема использования композиционных мембран этого типа связана с недостаточной стабильностью их поверхностных свойств и, соответственно, с недостаточной стабильностью разделительных характеристик.
Альтернативой растворных способов нанесения покрытий является применение безрастворных физико-химических методов модифицирования, в результате которых образуются химические связи между покрытиями и макромолекулами поверхностного слоя мембран. Особое место в этой группе методов занимает метод осаждения слоя полимера, синтезированного в плазме [16–18]. Данный метод обладает большими преимуществами: позволяет регулировать толщину осажденного слоя полимера, обеспечивает его высокую адгезию, характеризуется малым временем проведения процесса и возможностью применения в качестве прекурсоров широкого круга органических и элементорганических соединений. Применение этого метода в случае полимеризации органических соединений, содержащих функциональные группы, позволило получить на поверхности трековых мембран полимерные слои гидрофильной природы [19]. Однако, попытка использовать метод плазмохимической полимеризации с целью получения гидрофобного слоя полимера на поверхности мембран не приводит к положительным результатам. Проведенные исследования показали, что на поверхности осажденных покрытий при использовании в качестве прекурсоров соединений, не содержащих функциональные группы, например, ацетилена [20], тетрафторэтана [21] или перфторгексана [22], присутствуют кислородсодержащие функциональные группы, образование которых связано с окислением при выносе образцов на воздух, а также с наличием остаточного кислорода в вакуумной реакционной камере [23]. Именно с образованием кислородсодержащих групп в поверхностном слое осажденных полимерных покрытий связаны недостаточно высокие значения углов смачивания полученных покрытий.
Для осаждения тонких гидрофобных покрытий на поверхности пористых мембран возможно также использование ряда современных методов, таких как химическое осаждение из паровой фазы [24], золь-гель метод [25], фотохимическая прививка [26] и др. Однако, наибольший интерес представляет формирование покрытий из активной газовой фазы, образованной путем диспергирования полимеров в результате воздействия лазерного излучения [27], плазмы высокочастотного разряда [28, 29] или пучка ускоренных электронов [30, 31]. Эти методы являются высокотехнологичными, производительными и позволяют регулировать структуру и состав осаждаемых покрытий в широком диапазоне [32], а также получать супергидрофобные покрытия на поверхности твердых тел [28, 33, 34]. В ряде публикаций последних лет было показано, что использование двухслойных композиционных мембран с тонким микропористым слоем, обладающим супергидрофобными свойствами, для мембранной дистилляции позволяет повысить эффективность этого процесса [35, 36]. В связи с этим поиск новых методов получения двухслойных полимерных мембран, в составе которых один из слоев имеет супергидрофобную природу, является весьма актуальным.
Существует два основных подхода для создания супергидрофобных поверхностей, у которых угол смачивания водой выше 150°: образование микро- или наноструктур с высокой степенью шероховатости на поверхности гидрофобных материалов, к которым в первую очередь относятся соединения на основе кремния и фтора, или нанесение гидрофобных покрытий на поверхности с высокой степенью шероховатости [37]. В данной работе с помощью метода электронно-лучевого диспергирования полимеров в вакууме исследованы способы формирования одно- и двухслойных супергидрофобных покрытий на поверхности гидрофильной трековой мембраны из полиэтилентерефталата, реализующие оба подхода.
Для образования на поверхности мембраны однослойного супергидрофобного покрытия с высокой степенью шероховатости в качестве мишени использовали политетрафторэтилен. При формировании двухслойного супергидрофобного покрытия на первом этапе с целью получения покрытия с высокой степенью шероховатости в качестве мишени применяли полипропилен и сверхвысокомолекулярный полиэтилен, на поверхность которого на втором этапе наносили тонкий слой политетрафторэтилена. Для определения эффективности композиционных мембран разработанного образца использован процесс обессоливания водного раствора хлорида натрия методом мембранной дистилляции с воздушным зазором.
МЕТОДЫ ИССЛЕДОВАНИЯ
В экспериментах по модифицированию использовали трековую мембрану (ТМ) из полиэтилентерефталата (ПЭТФ) с эффективным диаметром пор 250 нм, полученную на основе полимерной пленки Лавсан (ГОСТ 24234-80, Россия) плотностью 1.40 г/см3 и номинальной толщиной 10.0 мкм. Для получения мембраны исходную пленку облучали ускоренными на циклотроне У-400 положительно заряженными ионами криптона с энергией ∼3 МэВ/нуклон. Флюенс ионов составлял 2 × 108 см–2. Химическое травление облученной пленки для образования пор проводили при температуре 75°С в водном растворе гидроксида натрия с концентрацией 3 моль/л по методике [38]. До начала травления для увеличения избирательности процесса травления треков облученную пленку подвергали воздействию УФ-излучения с максимальной длиной волны спектра испускания 310–320 нм. При исследовании процесса мембранной дистилляции также использовали образцы трековой мембраны из полипропилена (ПП ТМ) с эффективным диаметром пор 250 нм. Для изготовления мембраны исходную пленку Torayfan T2372 (Toray Co., Japan) толщиной 10.0 мкм облучали ускоренными на циклотроне ионами криптона. Флюенс ионов составлял 2 × 108 см–2. Химическое травление облученной пленки проводили при температуре 80°C в водном растворе оксида хрома(VI) с концентрацией 1000 г/л по методике [39].
Покрытия на поверхность ПЭТФ трековой мембраны размером 20 × 30 см2 наносили осаждением из активной газовой фазы, формируемой электронно-лучевым диспергированием (ЭЛД) полимеров в вакууме. В качестве источника электронов использовали электронно-лучевую пушку с катодом прямого накала, позволяющую получать пучки с энергией 0.8–1.6 кэВ и площадью сечения (5–10) × 10−4 м2. Начальное давление остаточных газов в вакуумной камере составляло 4 × 10−3 Па, температура поверхности подложки ~300 К. Мишенями для нанесения покрытий служили порошки изотактического полипропилена (ПП) со средней молекулярной массой 9.7 × 104 г/моль и плотностью 0.91 г/см3 (Polypropylene Co., Japan), сверхвысокомолекулярного полиэтилена (СВМПЭ) со средней молекулярной массой 5 × × 106 г/моль (Foresight Global FZE, UAE) и политетрафторэтилена (ПТФЭ), плотность которого составляла 2.15 г/см3 (Aldrich Co.). Двухслойные покрытия формировали в едином технологическом цикле без разгерметизации вакуумной камеры, автоматически перемещая мишени в зону воздействия электронного пучка. Контроль толщины осаждаемых покрытий осуществляли с помощью кварцевого измерителя толщины. Схема установки и методика осаждения покрытий подробно описаны в [40].
Характеристики исходных и модифицированных мембран определяли при помощи ряда методик. Количество полимера, осажденного на мембране, находили гравиметрически по привесу массы образца. Газопроницаемость (поток воздуха, прошедший через мембрану) измеряли при определенном перепаде давления (ΔP) при помощи поплавкового расходомера. По величине газопроницаемости, исходя из уравнения Хагена-Пуазейля [41]:
где Q − расход воздуха, η − вязкость воздуха, l − толщина мембраны, S − площадь мембраны, d − диаметр пор, N − плотность пор (число пор на 1 см2), применяя соответствующую программу, рассчитывали газодинамический (эффективный) диаметр пор. Погрешность определения эффективного диаметра пор не превышала 2%. Объемную пористость мембран рассчитывали исходя из соотношения объема пор к общему объему в единице объема мембраны [42]: где П − пористость, d − эффективный диаметр пор, N − плотность пор.Исследование микроструктуры образцов, а также определение диаметра пор на поверхности мембран проводили с помощью растрового электронного микроскопа (РЭМ) высокого разрешения “HITACHI” SU-8020 (Japan). Перед просмотром на образцы напыляли в вакууме тонкий слой золота. Для определения формы каналов пор и контроля толщины осажденных покрытий изучали поперечные сколы мембран. Для получения скола мембраны предварительно подвергали воздействию УФ-излучения с целью разрушения исходной полимерной матрицы. Методика получения поперечного скола мембран подробно описана в [43].
Смачиваемость поверхности мембран характеризовали значениями углов смачивания водой, измеренными с помощью установки “Easy Drop DSA100” (KRUSS, Germany) и программного обеспечения Drop Shape Analysis V.1.90.0.14 (точность измерения ±1°). Для измерений использовали деионизованную воду.
Величину LEP (liquid entry pressure, давление жидкости на входе мембраны) для гидрофобных мембран рассчитывали по уравнению Юнга-Лапласа [44]:
(3)
${\text{LE}}{{{\text{P}}}_{w}} = ~\frac{{ - 2B\gamma {{~}_{{\text{L}}}}\cos {\kern 1pt} {{\Theta }_{w}}}}{{{{r}_{{\max }}}}},$Морфологию поверхности мембран изучали методом атомно-силовой микроскопии (АСМ) [45] с помощью прибора NTEGRA Prima (NT-MDT, Россия). Сканирование проводили в прерывисто-контактном режиме с использованием кремниевых зондов HA_FM (Tipsnano, Estonia). Поле сканирования составляло 2 × 2 мкм2 с разрешением 512 × 512 точек на изображение. Основным определяемым параметром являлась поверхностная шероховатость Rms (среднеквадратичное отклонение профиля поверхности от базовой поверхности), рассчитанная по всем точкам скана [46]. Для того чтобы избежать влияния пор при определении поверхностной шероховатости, исследовали также сканы меньшей площадью, не содержащие пор.
Рентгеновские фотоэлектронные спектры (РФЭС) получали с помощью прибора K-Alpha “Thermo Scientific” (USA), оснащенного полусферическим анализатором. Для возбуждения фотоэлектронов использовали рентгеновское излучение алюминиевого анода (AlKα = 1486.6 эВ) при напряжении на трубке 12 кВ и токе эмиссии 3 мА. Положение пиков калибровали по стандартному пику С1s (284.6 эВ) [47]. Обзорные спектры регистрировали при окне пропускания 100 эВ с шагом по спектру 0.5 эВ, региональные спектры – при окне пропускания 20 эВ с шагом 0.05 эВ. Регистрацию и обработку спектров проводили с помощью программы Avantage совместно с атласами эталонных спектров [47, 48]. Форму пиков аппроксимировали сверткой Гауссовой и Лоренцевой функций.
Экспериментальные исследования по использованию модифицированных мембран для опреснения водного раствора хлорида натрия проводили на лабораторной установке (рис. 1), которая содержала мембранно-дистилляционный модуль (МДМ) с воздушным зазором, устанавливаемый вертикально. Рабочая площадь мембраны составляла 5 × 10−3 м2. МДМ состоял из двух камер, разделенных мембраной и сплошной охлаждаемой перегородкой. Толщина воздушного зазора между мембраной и охлаждаемой перегородкой составляла 4 мм. По одной из камер проходил горячий поток (опресняемая вода), по другой двигался поток холодной воды. Горячий поток циркулировал по замкнутому контуру между МДМ и водяным термостатом марки LOIP LT-100 (Россия), с помощью которого поддерживалась температура 65°С. Холодный поток циркулировал по замкнутому контуру между МДМ и жидкостным криостатом марки LOIP FT-211-25 (Россия), с помощью которого поддерживалась температура 10°С. Температуру горячего и холодного потоков на входе и выходе МДМ контролировали электронными термометрами с ценой деления 0.1°С. Опресняемая вода, концентрация хлорида натрия в которой составляла 15 г/л, и холодная вода термостатировались в специальных емкостях по принципу “водяной бани”. Перемещение горячего и холодного потоков осуществлялось насосами марки LOIP LS-301 (Россия). Скорость потока в камерах горячего раствора и холодной воды составляла 600 ± 5 мл/мин. Расходы горячего и холодного потоков контролировали ротаметрами. Конденсат, образующийся на поверхности охлаждаемой перегородки, стекал самотеком через имеющейся в нижней части штуцер в стеклянный измерительный цилиндр. Использовался объемный метод измерения количества конденсата, получаемого за определенное время. Эффективность процесса мембранной дистилляции оценивали коэффициентом солезадержания, который определяли из соотношения:
где С0 – концентрация хлорида натрия в исходном растворе, Сx – концентрация хлорида натрия в конденсате. Концентрацию соли в исходном растворе и конденсате определяли кондуктометрически с помощью прибора Starter 3100C (OHAUS Co., China). Погрешность измерений составляла ±0.5%.РЕЗУЛЬТАТЫ И ИХ ОБСУЖДЕНИЕ
Результаты измерений характеристик исходной ПЭТФ ТМ с диаметром пор 250 нм и композиционных мембран, полученных путем нанесения на ее поверхность покрытий из ПП и СВМПЭ электронно-лучевым диспергированием исходных полимеров в вакууме, приведены в табл. 1, где каждое экспериментально найденное значение представляет собой результат усреднения трех измерений. Из представленных данных следует, что в процессе модифицирования наблюдается прирост массы образцов мембран, связанный с осаждением покрытий на ее поверхности. Поток воздуха и, как следствие, эффективный диаметр пор композиционных мембран, рассчитываемый из величины газопроницаемости, уменьшается.
Таблица 1.
Изменение характеристик ПЭТФ ТМ при нанесении на ее поверхность покрытий, полученных методом электронно-лучевого диспергирования полимеров
Параметры | Исходная мембрана | Тип и толщина осажденного слоя полимера | |||
---|---|---|---|---|---|
ПП | СВМПЭ | ||||
200 нм | 500 нм | 200 нм | 500 нм | ||
Увеличение массы образца, % | — | 5.6 ± 0.1 | 7.8 ± 0.1 | 5.1 ± 0.1 | 8.7 ± 0.1 |
Поток воздуха при ΔР = 104 Па, мл/мин см2 | 300 ± 10 | 150 ± 3 | 75 ± 2 | 165 ± 4 | 50 ± 1 |
Эффективный диаметр пор, нм | 250 ± 5 | 200 ± 4 | 165 ± 3 | 210 ± 4 | 145 ± 3 |
Угол смачивания водой, град | 65 ± 1 | 104 ±1 | 102 ±1 | 95 ± 1 | 115 ± 1 |
Поверхностная шероховатость, нм (площадь сканирования 2 × 2 мкм2) | 50.0 ± 0.5 | 24.5 ± 0.3 | 20.2 ± 0.3 | 28.1 ± 0.4 | 50.4 ± 0.4 |
Поверхностная шероховатость, нм (область без пор) | 5.4 ± 0.1 | 13.3 ± 0.2 | 10.4 ± 0.2 | 22.1 ± 0.3 | 38.5 ± 0.4 |
Электронно-микроскопическое исследование поверхности композиционных мембран (рис. 2) показало, что по мере увеличения толщины осажденного слоя полимера происходит более значительное уменьшение диаметра пор на поверхности мембран. Так, например, для мембраны с покрытием из ПП толщиной 500 нм (рис. 2в) уменьшение диаметра пор более существенно, в сравнении с мембраной, толщина покрытия у которой составляет 200 нм (рис. 2б). Вместе с этим, экспериментальные данные показали, что диаметр пор на обратной стороне мембран остается неизменным (рис. 2е). Это свидетельствует о том, что осаждение покрытий происходит лишь на стороне мембран, подвергнутых модифицированию. Нанесение на поверхность ПЭТФ ТМ покрытий методом электронно-лучевого диспергирования полимеров в вакууме приводит, таким образом, к формированию композиционных мембран, имеющих асимметричную форму пор – диаметр пор на необработанной стороне мембран не изменяется, а на модифицированной стороне происходит его уменьшение. Аналогичные данные получены нами при исследовании модифицирования трековых мембран методом полимеризации в плазме [19].
Рис. 2.
Микрофотографии поверхностного слоя исходной ПЭТФ ТМ (а), мембран с покрытием из ПП толщиной 200 (б) и 500 нм (в); мембран с покрытием из СВМПЭ толщиной 200 (г) и 500 нм (д); обратная сторона модифицированной мембраны (е).
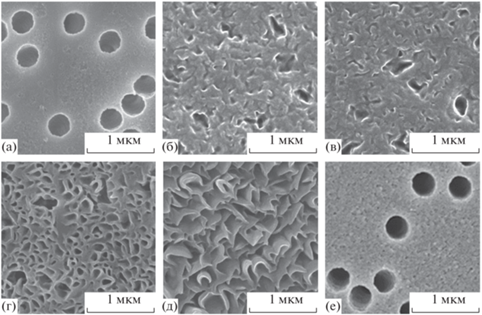
Исследование морфологии поверхности композиционных мембран методом АСМ показывает некоторое различие процессов осаждения покрытий из ПП и СВМПЭ. Так, для исходной мембраны с диаметром пор 250 нм величина среднеквадратичного отклонения профиля поверхности от базовой плоскости Rms, рассчитанная по всем точкам скана площадью 2 × 2 мкм2, составляет 50.0 нм (табл. 1). Относительно высокое значение этой величины обусловлено как наличием пор на поверхности мембраны, так и способом изготовления трековой мембраны, включающим химическое травление. Наличие пор оказывает более заметное влияние на величину шероховатости. На это указывает определение таких параметров, как средняя высота пика шероховатости Rpm и средняя глубина впадины шероховатости Rvm профиля поверхности. Оценка этих параметров для исходной мембраны показывает, что величина Rvm составляет 389.5 нм, в то время как значение Rpm = = 62.2 нм, что значительно ниже. Чтобы избежать влияния пор при определении поверхностной шероховатости, для исследований были также обработаны участки поверхности, не содержащие пор. Для исходной ПЭТФ ТМ величина Rms в этом случае составляет 5.4 нм, что на порядок меньше, чем при выборе поля сканирования большей величины.
При осаждении на поверхности ПЭТФ ТМ покрытий из ПП и СВМПЭ толщиной 200 нм в случае сканирования образца площадью 2 × 2 мкм2 наблюдается сглаживание поверхности − шероховатость образующихся композиционных мембран уменьшается (табл. 1). Этот результат объясняется формированием слоя полимера в каналах пор на некоторой глубине от входа и частичным перекрытием пор на поверхности мембраны. Однако, при выборе участка для сканирования, не содержащего пор, Rms для мембраны с покрытием из ПП равна 13.3 нм, а для мембраны с покрытием из СВМПЭ − 22.1 нм. Эти значения выше, чем у исходной мембраны, что указывает на развитие шероховатости поверхностного слоя при нанесении покрытий. Увеличение толщины осажденного слоя ПП до 500 нм вызывает незначительное снижение поверхностной шероховатости. Величина Rms для модифицированных образцов мембран, рассчитанная по всем точкам скана площадью 2 × 2 мкм2, уменьшается.
Аналогичная зависимость наблюдается на поверхности мембран, не содержащей пор, при выборе площади сканирования меньшего размера (табл. 1). В противоположность этому, при возрастании толщины покрытия из СВМПЭ мы наблюдаем существенный рост шероховатости поверхностного слоя. Так, при толщине осажденного слоя 200 нм, величина среднеквадратичного отклонения профиля поверхности поверхностного слоя композиционной мембраны, не содержащей поры, составляет 22.1 нм. Увеличение толщины осажденного слоя СВМПЭ до 500 нм вызывает рост поверхностной шероховатости до 38.5 нм. Такая же зависимость наблюдается при выборе площади сканирования большего размера (табл. 1). Возрастание величины Rms на поверхности без пор в процессе осаждения свидетельствует о том, что пленка СВМПЭ имеет более развитую поверхность по сравнению с поверхностью покрытий из ПП. Наблюдаемые различия в морфологии поверхностного слоя композиционных мембран, образующихся в процессе нанесения покрытий из ПП и СВМПЭ на поверхность исходной трековой мембраны, может быть связано, прежде всего, с размерами осаждающихся полимерных наноструктур. Наноструктуры, образующиеся на поверхности трековых мембран, при диспергировании СВМПЭ под действием электронного пучка, имеют, как правило, существенно большие размеры, чем наноструктуры, формирующиеся при диспергировании ПП.
Исследование поверхностных свойств композиционных мембран показывает, что осаждение покрытий из ПП и СВМПЭ, полученных электронно-лучевым диспергированием исходных полимеров в вакууме, приводит к существенной гидрофобизации поверхности ПЭТФ ТМ. Если исходная мембрана характеризуется величиной угла смачивания водой (Θ), равной 65°, то для ПЭТФ ТМ со слоем ПП толщиной 200 нм значение Θ составляет 104°. Для мембраны со слоем ПП толщиной 500 нм угол смачивания водой равен 102°. Снижение угла смачивания при возрастании толщины покрытия обусловлено уменьшением шероховатости осажденного слоя полимера [49, 50]. Для ПЭТФ ТМ со слоем СВМПЭ толщиной 200 нм значение Θ = 95°. Увеличение толщины нанесенного слоя полимера до 500 нм приводит к повышению угла смачивания до 115°. Такое изменение смачиваемости поверхности композиционных мембран обусловлено ростом шероховатости осажденного слоя СВМПЭ, обладающего гидрофобными свойствами, при увеличении его толщины [49, 50].
Таким образом, нанесение на поверхность ПЭТФ ТМ покрытий из ПП и СВМПЭ электронно-лучевым диспергированием исходных полимеров в вакууме, приводит к образованию композиционных мембран, состоящих из двух слоев, одним из которых является исходная трековая мембрана, характеризующаяся средним уровнем гидрофильности. Второй слой имеет гидрофобную природу. Величина угла смачивания этого слоя, в зависимости от природы осажденного полимерного покрытия и его толщины, изменяется.
Для выявления изменений в химическом составе поверхностного слоя мембран, происходящих в процессе осаждения покрытий на поверхности исходной ПЭТФ ТМ, были проведены измерения спектров РФЭС. Анализ спектра РФЭС поверхностного слоя исходной ПЭТФ ТМ показало присутствие линий, связанных с атомами углерода и кислорода, атомные концентрации которых составляют 74.5 и 25.5%, соответственно. Для установления природы функциональных групп на поверхности мембраны был подробно исследован спектр атома углерода. Разложение линии спектра C1s ПЭТФ ТМ на компоненты показывает, что он имеет сложный характер (рис. 3а). Наиболее интенсивный компонент спектра с максимумом энергии связи при 284.6 эВ, относительный вклад которого составляет 66.0%, соответствует углероду в составе связей С−С и С−Н [47, 48]. Компоненты с максимумами энергий связи при 286.3 и 288.7 эВ отвечают углероду в составе кислородсодержащих функциональных групп: C−О с концентрацией 18.3% и O=C−О, концентрация которых составляет 15.7% [51, 52]. Значительная концентрация кислородсодержащих функциональных групп в поверхностном слое исходной ПЭТФ ТМ определяет гидрофильность ее поверхности.
Рис. 3.
Спектры РФЭС атомов С1s исходной ПЭТФ ТМ (а) и порошка СВМПЭ (б); покрытий из ПП (в) и СВМПЭ (г), осажденных методом электронно-лучевого диспергирования.
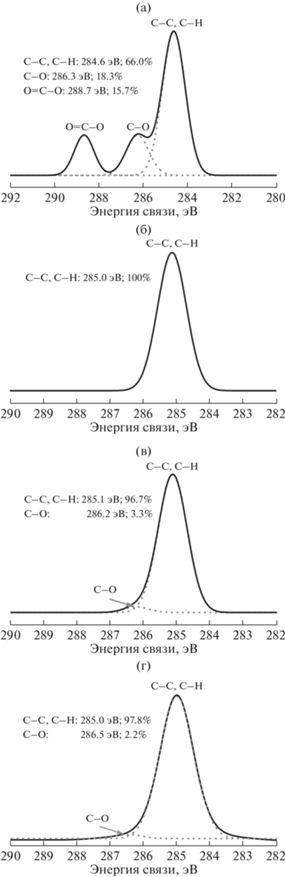
Исследование методом РФЭС химической структуры покрытий из ПП и СВМПЭ толщиной 300 нм, осажденных методом ЭЛД, показало присутствие пиков, связанных с атомами углерода и кислорода, атомные концентрации которых составляют соответственно 98.5 и 1.5% для покрытия из ПП и 98.7 и 1.3% для покрытия из СВМПЭ. Детальный анализ спектров атомов C1s свидетельствует о некотором различии электронной структуры и химического состояния углерода в исходных полимерах (рис. 3б) и осажденных покрытиях (рис. 3в, 3г). В спектрах исходных полимеров (на рис. 3б в виду тождественности спектров ПП и СВМПЭ приведен лишь спектр атома C1s СВМПЭ) присутствует один интенсивный пик с максимумом при 285.0 эВ, отвечающий химическому состоянию углерода в составе связей C–C и C–H [47, 48]. В спектрах покрытий из ПП и СВМПЭ, присутствуют два компонента: интенсивный с максимумом энергии связи 285.0 эВ, отвечающий химическому состоянию углерода в составе групп C–C и C–H, и компонент малой интенсивности с максимумом при 286.5 эВ, который соответствует углероду в составе кислородсодержащих функциональных групп C−ОH и C−OR [53, 54]. Парциальные концентрации этих состояний для покрытия из ПП соответственно равны 96.7 и 3.3%, а для покрытия из СВМПЭ − 97.8 и 2.2%. Эти данные свидетельствуют о появлении на поверхности полимерных покрытий кислородсодержащих групп, т.е. часть атомов углерода находится в окисленном состоянии. Большая концентрация кислородсодержащих групп на поверхности покрытия из ПП свидетельствует о том, что данный полимер в большей степени подвержен окислению в процессе диспергирования. Отношение числа атомов кислорода к числу атомов углерода в осажденных покрытиях из ПП и СВМПЭ в среднем составляет 1.4 × 10–2, что на порядок ниже, чем на поверхности исходной ПЭТФ ТМ. Это свидетельствует о том, что концентрация ионогенных функциональных групп, в частности кислородсодержащих групп, на поверхности значительно ниже в сравнении с исходной мембраной, для которой отношение числа атомов кислорода к числу атомов углерода составляет 3.4 × 10–1.
Таким образом, как показывают наши экспериментальные результаты, осаждение на поверхность ПЭТФ ТМ покрытий из СВМПЭ электронно-лучевым диспергированием приводит к формированию полимерного слоя с более развитой поверхностью в сравнении с покрытиями из ПП. Обусловлено это размерами осаждающихся полимерных наноструктур. Наноструктуры из СВМПЭ имеют существенно большие размеры, что обусловливает значительное повышение поверхностной шероховатости данного покрытия. Это, в свою очередь, вызывает более существенное повышение угла смачивания. Для решения вопроса о возможности получения покрытий с супергидрофобными свойствами мы предприняли более детальное изучение процесса формирования покрытий из СВМПЭ на поверхности трековой мембраны из полиэтилентерефталата. Результаты электронно-микроскопического исследования поверхностного слоя композиционных мембран, образующихся после нанесения покрытий из СВМПЭ толщиной от 100 до 1200 нм показывают следующее. Для мембраны с осажденным слоем СВМПЭ толщиной 100 нм наблюдается незначительное уменьшение диаметра пор на поверхности. Поверхность осажденного слоя полимера имеет слабо выраженную шероховатость. По мере увеличения толщины покрытия диаметр пор на поверхности мембраны уменьшается. Так, для мембраны с толщиной покрытия 200 нм (рис. 2г) уменьшение диаметра пор более существенно. Осажденный слой полимера при этом приобретает сетчатую форму и становится более шероховатым. При увеличении толщины нанесенного слоя полимера на поверхности мембраны образуются упорядоченные морфологические наноструктуры, размеры которых возрастают с ростом толщины покрытия (рис. 2д и 4). Такое изменение приводит к росту поверхностной шероховатости композиционных мембран. Так, при толщине покрытия 1200 нм величина Rms составляет 63.8 нм. Это вызывает повышение угла смачивания до 125°, т.е. в этом случае происходит образование высокогидрофобного слоя полимера.
Рис. 4.
Микрофотографии поверхностного слоя ПЭТФ ТМ (а, в, д) и трехмерные изображения (б, г, е) с покрытием из СВМПЭ толщиной 700 (а, б), 900 (в, г) и 1200 нм (д, е).
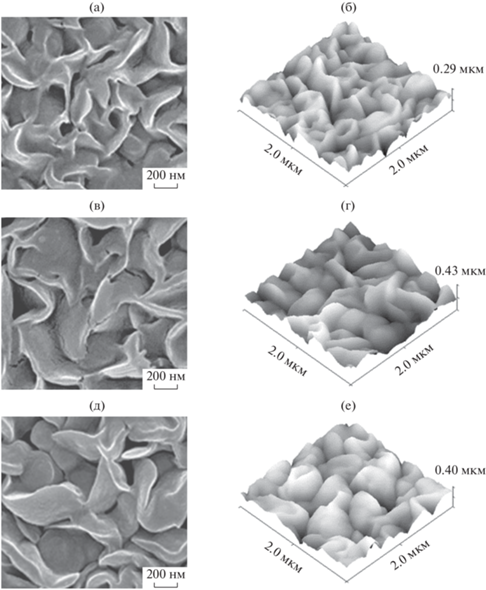
Как показали наши исследования, осаждение на поверхности ПЭТФ ТМ покрытия из СВМПЭ толщиной более 1200 нм не приводит к росту величины поверхностной шероховатости (рис. 5а), а, следовательно, и к повышению угла смачивания (рис. 5б). В то же время известно, что ПТФЭ обладает более низкой поверхностной энергией в сравнении с СВМПЭ. Так, для ПТФЭ поверхностная энергия составляет 18.3 мДж/м2, а для СВМПЭ эта величина равна 33.0 мДж/м2. В этой связи для получения супергидрофобного слоя полимера на поверхности трековых мембран нами применена методика формирования двухслойного покрытия.
Рис. 5.
Изменение поверхностной шероховатости (а) при различной площади сканирования (S) и угла смачивания (б) покрытия из СВМПЭ в зависимости от его толщины.
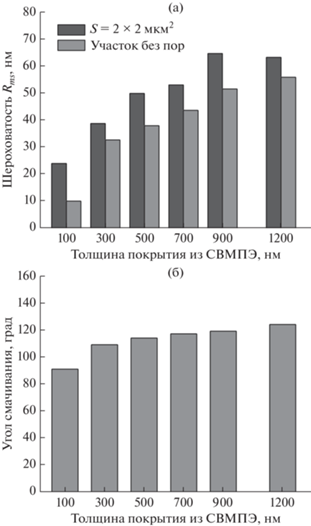
На первом этапе для образования покрытия с морфологически развитой структурой на поверхности мембраны с помощью метода ЭЛД осаждали слой СВМПЭ. Этот слой, в зависимости от его толщины, обладал гидрофобными или высокогидрофобными свойствами. На втором этапе для формирования супергидрофобного покрытия на поверхности слоя СВМПЭ осаждали тонкую пленку ПТФЭ. Осаждение на поверхности мембраны второго слоя толщиной 100 нм, полученного методом электронно-лучевого диспергирования ПТФЭ, приводит к образованию супергидрофобного покрытия. Значения углов смачивания водой для этого типа композиционных мембран, как показывают экспериментальные данные, в зависимости от общей толщины двухслойного покрытия изменяются от 150° до 160°. Формирование на поверхности мембран супергидрофобного покрытия объясняется более низкой поверхностной энергией пленки из фторопласта, а также более значительным развитием шероховатости ее поверхности (рис. 6а–6в) в сравнении с покрытием из СВМПЭ (рис. 4). Кроме того, в этом случае мы наблюдаем образование полимера с иерархической структурой, наиболее выраженной для покрытия, полученного электронно-лучевым диспергированием полимеров с общей толщиной 1300 нм: слой СВМПЭ толщиной 1200 нм и слой ПТФЭ толщиной 100 нм (рис. 6в). Для покрытия с общей толщиной 1000 нм: СВМПЭ толщиной 900 нм и слой ПТФЭ толщиной 100 нм (рис. 6б), иерархическая структура слабо выражена. Мы не наблюдаем формирования полимера с иерархической структурой для покрытия с общей толщиной 800 нм: СВМПЭ толщиной 700 нм и слой П-ТФЭ толщиной 100 нм (рис. 6а).
Рис. 6.
Трехмерные изображения (полученные с помощью АСМ) поверхности ПЭТФ ТМ после нанесения двухслойного покрытия: первого слоя СВМПЭ толщиной 700 (а), 900 (б), 1200 нм (в) и второго слоя ПТФЭ толщиной 100 нм; первого слоя СВМПЭ толщиной 1200 нм и второго слоя ПТФЭ толщиной 200 (г), 300 (д) и 400 нм (е).
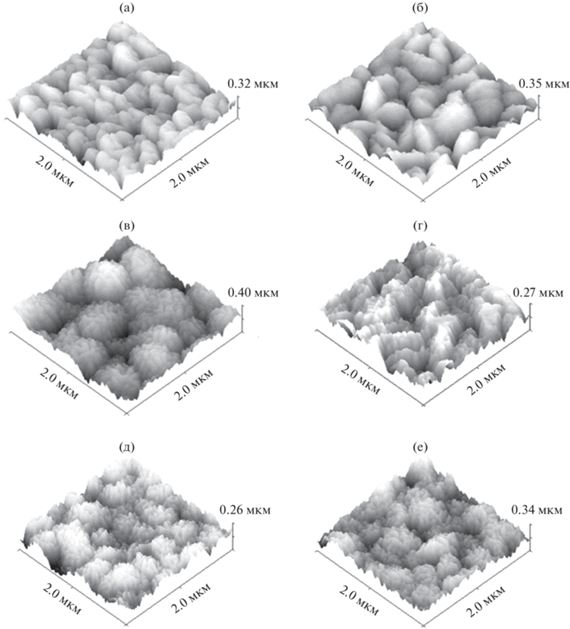
Увеличение толщины слоя ПТФЭ до 400 нм, осаждаемого на поверхности покрытия СВМПЭ толщиной 1200 нм (рис. 6г–6е), также приводит к образованию полимеров с иерархической структурой. Однако, в этом случае сформированные на поверхности ПЭТФ ТМ полимеры не обладают супергидрофобными свойствами. Значения углов смачивания для композиционных мембран этого типа, в зависимости от общей толщины двухслойного покрытия, изменяются от 134° до 140° (рис. 7а). Понижение величины угла смачивания объясняется уменьшением шероховатости поверхностного слоя за счет сглаживания микрорельефа поверхности (рис. 7б).
Рис. 7.
Изменение угла смачивания (а) и поверхностной шероховатости (б) покрытия из ПТФЭ в зависимости от его толщины, осажденного на поверхности слоя СВМПЭ толщиной 1200 нм; площадь сканирования 2 × 2 мкм2.
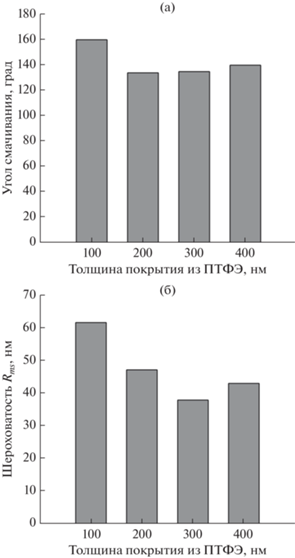
Изучение методом РФЭС химического состава слоя ПТФЭ, осажденного методом ЭЛД, показало присутствие пиков, связанных с атомами углерода и фтора. Теоретически отношение числа атомов фтора к углероду для ПТФЭ составляет 2, для слоя полимера, полученного методом ЭЛД ПТФЭ, это отношение несколько ниже. Снижение соотношения числа атомов фтора к углероду при длительном проведении процесса свидетельствует об отрыве некоторого количества атомов фтора. Детальный анализ спектров C1s показывает значительное различие электронной структуры и химического состояния углерода в исходном ПТФЭ (рис. 8а) и осажденных методом ЭЛД пленках полимера (рис. 8б). В спектре исходного полимера присутствуют два компонента: интенсивный с максимумом энергии связи при 292.1 эВ, отвечающий химическому состоянию углерода в составе групп CF2 [47, 48], и компонент малой интенсивности с максимумом энергии связи, равным 284.5 эВ, который соответствует углероду в составе связей C−C [47, 48]. Парциальные концентрации этих состояний составляют 98.5 и 1.5%, соответственно. Согласно литературным данным, спектр C1s ПТФЭ содержит один компонент, отвечающий группе CF2 с максимумом энергии связи 292.1 эВ [55, 56]. По-видимому, присутствие в спектре слабоинтенсивного пика может быть связано с наличием в составе полимера незначительного количества углеводородных примесей.
Рис. 8.
Спектры РФЭС атомов С1s исходного ПТФЭ (а) и покрытия из ПТФЭ толщиной 100 нм, осажденного методом электронно-лучевого диспергирования (б).
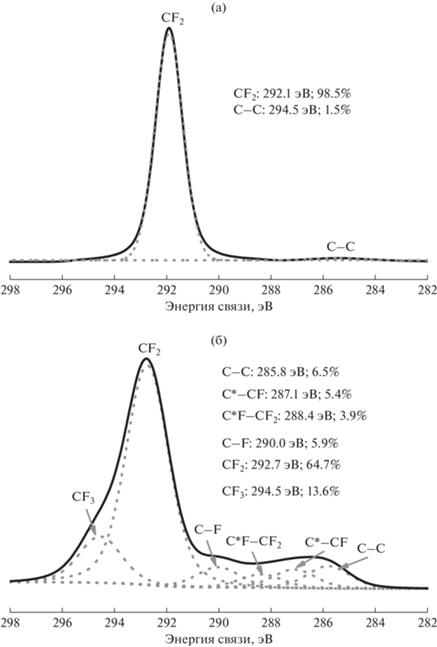
Для ПТФЭ, полученного методом ЭЛД, наблюдается уширение спектра, что свидетельствует о суперпозиции нескольких линий, соответствующих различным химическим состояниям атома углерода. Разложение линии спектра С1s выявило четыре дополнительных пика с энергией связи 287.1, 288.4, 294.5 и 290.0 эВ, отвечающие химическому состоянию углерода в составе групп C*−CF, C*F−CF2, CF3 и связи C−F [28, 29, 34]. Это свидетельствует о протекании процессов деструкции ПТФЭ, происходящих под воздействием электронного пучка, а присутствие групп CF3 указывает на наличие макромолекул с короткими цепями [57]. Следует заметить, что полимеры, формируемые под воздействием электронного пучка, не содержат атомов кислорода и азота, с присутствием которых связана более низкая величина угла смачивания покрытий, осажденных методом магнетронного распыления. Кроме того, полимеры, осажденные методом ЭЛД, по химическому составу более близки к исходному ПТФЭ. Для них наблюдается более высокая концентрация химических групп CF2 и значительно меньшие концентрации групп C*−CF, CF3 по сравнению с покрытиями, осажденными методом магнетронного распыления [58].
Осаждение слоя ПТФЭ для образования двухслойного покрытия на поверхности ПЭТФ ТМ, таким образом, приводит к формированию композиционных мембран, состоящих из трех слоев, одним из которых является исходная мембрана, характеризующаяся наличием концевых карбоксильных групп на поверхности и имеющая средний уровень гидрофильности. Два других слоя, образующих двухслойное покрытие, нанесенных последовательным диспергированием СВМПЭ и ПТФЭ, в зависимости от толщины, имеют высокогидрофобную или супергидрофобную природу. Это покрытие не содержит ионогенных функциональных групп на внешней поверхности.
Исследование процесса нанесения на поверхность ПЭТФ ТМ однослойного покрытия ПТФЭ методом ЭЛД показывает, что с ростом толщины осажденного слоя наблюдается уменьшение диаметра пор на поверхности образующихся композиционных мембран (рис. 9). Эффективный диаметр пор мембран при этом также уменьшается (табл. 2). Так, осаждение пленки полимера толщиной 100 нм вызывает уменьшение эффективного диаметра пор до 225 нм. Осаждение пленки полимера толщиной 300 нм приводит к более значительному уменьшению диаметра пор на поверхности мембраны (рис. 9в), эффективный диаметр пор уменьшается при этом до 195 нм. При осаждении пленки ПТФЭ толщиной 500 нм поры на поверхности исходной мембраны практически полностью закрываются слоем полимера (рис. 9г), эффективный диаметр пор композиционной мембраны в этом случае составляет 180 нм.
Рис. 9.
Трехмерные изображения (полученные с помощью АСМ) поверхности исходной ПЭТФ ТМ (а) и мембран с покрытием из ПТФЭ толщиной 100 (б), 300 (в) и 500 нм (г), осажденным методом ЭЛД.
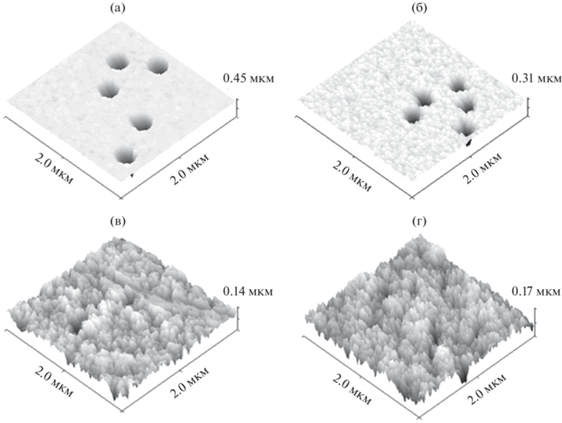
Таблица 2.
Изменение характеристик ПЭТФ ТМ при нанесении на ее поверхность покрытий, полученных методом электронно-лучевого диспергирования ПТФЭ
Параметры | Исходная мембрана |
Толщина осажденного покрытия из ПТФЭ, нм | ||
---|---|---|---|---|
100 | 300 | 500 | ||
Увеличение массы образца, % | — | 4.2 ± 0.1 | 10.2 ± 0.2 | 13.7 ± 0.2 |
Поток воздуха при ΔР = 104 Па, мл/мин см2 | 300 ± 10 | 215 ± 5 | 130 ± 3 | 100 ± 2 |
Эффективный диаметр пор, нм | 250 ± 5 | 225 ± 5 | 195 ± 4 | 180 ± 4 |
Угол смачивания водой, град | 65 ± 1 | 130 ± 1 | 150 ± 1 | 155 ± 1 |
Поверхностная шероховатость, нм (площадь сканирования 2 × 2 мкм2) | 50.0 ± 0.5 | 28.3 ± 0.4 | 16.3 ± 0.3 | 20.1 ± 0.4 |
Поверхностная шероховатость, нм (область без пор) | 5.4 ± 0.5 | 10.2 ± 0.2 | 14.2 ± 0.3 | 17.2 ± 0.4 |
Для практических целей при использовании мембран в процессах мембранной дистилляции при опреснении воды важно, чтобы осаждаемое покрытие не образовывало сплошного непористого слоя на поверхности исходной мембраны, так как это может привести к существенному снижению газопроницаемости композиционных мембран. Иными словами, композиционные мембраны должны обладать достаточной проницаемостью, сопоставимой с проницаемостью гидрофобных мембран из ПВДФ, ПТФЭ и ПП, традиционно применяемыми в процессах мембранной дистилляции. Анализ экспериментальных данных показывает, что при осаждении на поверхности ПЭТФ ТМ с эффективным диаметром пор 250 нм покрытия из ПТФЭ толщиной 100 нм, полученного электронно-лучевым диспергированием исходного полимера, образующаяся композиционная мембрана обладает более высокой проницаемостью в сравнении с мембраной из ПВДФ с диаметром пор 0.22 мкм толщиной 50 мкм (Millipore, Germany), величина газопроницаемости которой при ΔР = 104 Па составляет 190 мл/мин см2 [59]. Осаждение на поверхности ПЭТФ ТМ покрытий из ПТФЭ большей толщины вызывает заметное снижение проницаемости композиционных мембран (табл. 2). Данный факт следует учитывать при выборе длительности модифицирования ПЭТФ-мембраны с целью гидрофобизации ее поверхности. Вопрос выбора режимов обработки в разряде, таким образом, имеет два аспекта: с одной стороны, он связан с установлением длительности его воздействия, при котором изменения в поверхностном слое мембран приводили бы к заметному повышению угла смачиваемости, т.е. композиционные мембраны обладали бы высокогидрофобными свойствами. Толщина осажденного покрытия при этом должна быть достаточной для равномерного распределения по поверхности исходной мембраны. С другой стороны, необходимо выбирать длительность воздействия разряда, при которой в процессе обработки не происходило бы образования сплошного непористого слоя на поверхности исходной мембраны, значительно снижающего газопроницаемость композиционных мембран. Выбор оптимальных режимов обработки позволяет получать композиционные мембраны с гидрофобной поверхностью, обладающие достаточной проницаемостью. Это делает возможным использование их в процессах мембранной дистилляции при опреснении морской воды.
Изучение морфологии поверхности модифицированных мембран с помощью метода АСМ показывает, что осаждение пленки полимера, полученной диспергированием ПТФЭ под действием электронного пучка, приводит к изменению ее поверхностной шероховатости. Так, для исходной мембраны величина Rms, рассчитанная по всем точкам скана площадью 2 × 2 мкм2, составляет 50.0 нм. Осаждение на поверхности ПЭТФ ТМ покрытия из ПТФЭ вследствие формирования полимера в каналах пор на некоторой глубине от входа и частичного перекрытия пор приводит к сглаживанию поверхностной неоднородности − величина среднеквадратичного отклонения профиля поверхности для модифицированных мембран уменьшается. Однако, при выборе меньшей площади сканирования, не содержащей пор, величина Rms выше, чем у исходной мембраны (табл. 2). Возрастание величины Rms на участке поверхности без пор в процессе осаждения свидетельствует о том, что покрытие из ПТФЭ имеет более развитую поверхность по сравнению с поверхностью исходной ТМ и величина его шероховатости в значительной степени зависит от продолжительности процесса осаждения.
Рост шероховатости осажденного покрытия из ПТФЭ при возрастании его толщины обусловливает повышение угла смачивания поверхностного слоя мембраны. Так, для композиционной мембраны с толщиной осажденного покрытия из ПТФЭ 100 нм Θ = 130°. Значение Rms на ее беспоровой поверхности составляет 10.2 нм. Осаждение слоя ПТФЭ толщиной 300 нм приводит к росту Rms до 14.2 нм, что вызывает повышение Θ до 150°, т.е. в этом случае мы наблюдаем формирование супергидрофобной поверхности. При осаждении покрытия из ПТФЭ толщиной 500 нм также происходит образование супергидрофобной поверхности, угол смачивания которой равен 155° при ее шероховатости 17.2 нм (табл. 2). Значительное повышение угла смачивания (более 150°) объясняется ростом шероховатости поверхностного слоя осажденного слоя полимера, обладающего гидрофобными свойствами [49, 50].
Осаждение на поверхности ПЭТФ ТМ покрытий из активной газовой фазы, получаемой методом электронно-лучевого диспергирования ПТФЭ, таким образом, приводит к существенной гидрофобизации поверхностного слоя мембраны, степень которой зависит от толщины покрытия. При осаждении полимерного слоя толщиной 100 нм происходит формирование покрытия, обладающего высокогидрофобными свойствами, угол смачивания водой поверхности которого составляет 130°. Возрастание толщины осажденного слоя до 500 нм за счет существенного увеличения поверхностной шероховатости приводит к формированию покрытия, обладающего супергидрофобными свойствами, для которого угол смачивания составляет 155°.
Краевой угол воды с поверхностью является ключевым параметром, указывающим, является ли мембрана более гидрофобной по отношению к другой. Однако, при использовании мембран в процессах мембранной дистилляции для опреснения воды, помимо угла смачивания, важным параметром является также величина LEP − это минимально необходимое давление жидкости для проникновения в поры мембраны. Чтобы предотвратить возникновение смачивания пор, значение LEP должно быть как можно выше. Согласно уравнению (3), применяемому для расчета LEP, эта величина зависит от максимального размера пор и гидрофобности мембраны. Это означает, что для получения высокого LEP следует использовать материалы для мембран, обладающие высокой гидрофобностью, низким уровнем энергии и малым размером пор [60]. Заметим, выбор мембран с незначительным размером пор может привести к снижению производительности процесса мембранной дистилляции вследствие низкой проницаемости мембран. Иными словами, для достижения высокой производительности процесса применяемые мембраны должны обладать высокой проницаемостью и высоким значением LEP.
Значения LEP для исходной ПП ТМ и композиционных мембран, сформированных осаждением покрытия из ПТФЭ различной толщины на поверхность ПЭТФ ТМ приведены в табл. 3 (в расчетах в качестве максимального радиуса пор использованы значения, определенные из величины газопроницаемости мембран). Из представленных данных следует, что по сравнению с исходной ПП ТМ, для которой значение LEP составляло 2.95 ± 0.05 бар, композиционные мембраны показали увеличение LEP с 4.15 ± 0.05 до 7.35 ± ± 0.05 бар. Эти результаты указывают на то, что для композиционных мембран требуется более высокое давление, чтобы пропускать воду через поры, а слой покрытия из ПТФЭ эффективно улучшает сопротивление смачиванию. Наилучшими характеристиками при этом обладает мембрана с толщиной покрытия 500 нм, угол смачивания для которой равен 155°, для которой эффективный диаметр пор наименьший.
Таблица 3.
Сравнение исходных и композиционных мембран по производительности и селективности разделения в процессе мембранной дистилляции
Параметры | ПЭТФ ТМ | ПП ТМ | Толщина осажденного покрытия из ПТФЭ, нм | ||
---|---|---|---|---|---|
100 | 300 | 500 | |||
Эффективный диаметр пор, нм | 250 ± 5 | 250 ± 5 | 225 ± 4 | 195 ± 4 | 180 ± 3 |
Диаметр пор на поверхности, нм | 295 ± 5 | 300 ± 5 | 215 ± 4 | — | — |
Пористость, % | 9.8 ± 0.2 | 9.8 ± 0.2 | 7.9 ± 0.1 | 6.0 ± 0.1 | 5.1 ± 0.1 |
Угол смачивания водой, град | 65 ± 1 | 120 ± 1 | 130 ± 1 | 150 ± 1 | 155 ± 1 |
LEPw, бар | — | 2.95 ± 0.05 | 4.15 ± 0.05 | 6.45 ± 0.05 | 7.35 ± 0.05 |
Максимальный поток конденсата, г/м2 ч | 1815 ± 10 | 630 ± 4 | 980 ± 5 | 960 ± 5 | 945 ± 5 |
Удельная электропроводность конденсата, мкСм/см | 12 800 ± 10 | 3.2 ± 0.3 | 6.0 ± 0.5 | 5.3 ± 0.4 | 5.8 ± 0.5 |
Концентрация соли в конденсате, мг/л | 6980 ± 5 | 1.50 ± 0.02 | 3.40 ± 0.05 | 2.45 ± 0.04 | 2.80 ± 0.05 |
Коэффициент солезадержания, % | 53.45 | 99.99 | 99.97 | 99.98 | 99.99 |
Для определения эффективности разделения солевого раствора модифицированными мембранами был использован метод мембранной дистилляции с воздушным зазором. На рис. 10а приведены данные по изменению производительности исследуемых мембран во времени. Можно видеть, в процессе эксплуатации для всех композиционных мембран на начальном этапе наблюдается возрастание потока конденсата до определенного максимального значения. При этом композиционная мембрана с толщиной осажденного слоя ПТФЭ, равной 100 нм, показала наибольшее максимальное значение потока конденсата − 980 ± 5 г/м2 ч. По мере увеличения толщины слоя ПТФЭ, осажденного на поверхности ПЭТФ ТМ, величина максимального потока конденсата уменьшается. Так, максимальный поток конденсата через мембрану с толщиной слоя ПТФЭ, равной 300 нм, составляет 960 ± 5 г/м2 ч, а для мембраны с толщиной осажденного слоя 500 нм эта величина равна 945 ± 5 г/м2 ч. Из исследуемых мембран наибольшей газопроницаемостью обладает композиционная мембрана с толщиной осажденного слоя 100 нм, а наименьшей − с толщиной слоя ПТФЭ, равной 500 нм. Это позволяет сделать заключение о том, что эффективность работы мембран в процессе мембранной дистилляции, в первую очередь, определяется величиной их газопроницаемости, т.е. пористостью.
Рис. 10.
Изменение потока конденсата во времени в процессе МД при использовании ПЭТФ ТМ с покрытием из ПТФЭ толщиной 100 (1), 300 (2) и 500 нм (3), осажденным методом электронно-лучевого диспергирования (а), и исходных трековых мембран из ПЭТФ и ПП (б).

Сравнение полученных нами экспериментальных данных по производительности композиционных мембран с коммерческими мембранами, применяемыми для обессоливания воды методом мембранной дистилляции, показывает, что при проведении процесса в сходных режимах мембраны разработанного образца практически не уступают производимым промышленностью гидрофобным микрофильтрационным мембранам. Так, авторами работы [61] при исследовании процесса мембранной дистилляции с использованием мембранно-дистилляционного модуля с воздушным зазором шириной 8.5 мм при разделении водного раствора хлорида натрия с концентрацией 15 г/л при температуре 50°С (температура охлаждающего раствора 10°С) показано, что поток конденсата через мембрану из поливинилиденфторида (Millipore) с диаметром пор 450 нм и толщиной 125 мкм составляет 1200 г/м2 час. Авторы также показали, что величина потока конденсата зависит от многих факторов: температуры исходного и охлаждающего растворов, концентрации соли в разделяемой смеси, ширины воздушного зазора, скорости циркуляции потоков в камерах горячего исходного раствора и холодной воды. Производительность процесса мембранной дистилляции также определяется конструкцией мембранно-дистилляционного модуля и диаметром пор используемой мембраны. Поэтому трудно было ожидать, что полученные нами данные будут идентичными. Кроме того, для формирования композиционных мембран в качестве пористой подложки были использованы трековые мембраны с меньшим диаметром пор.
Через два часа после начала испытаний композиционные мембраны показали идентичную тенденцию к снижению потока конденсата. Потоки конденсата начинают постепенно снижаться до окончания эксперимента. Уменьшение потока конденсата на 0.6% регистрируется через 6 ч для композиционной мембраны с покрытием из ПТФЭ толщиной 100 нм. Для мембраны с осажденным слоем ПТФЭ толщиной 300 нм это значение составляет 1.5%, а для мембраны с покрытием из ПТФЭ толщиной 500 нм – 1.7%. Т.е., для композиционных мембран с толщиной нанесенного полимерного слоя 300 и 500 нм происходит более резкое падение потока конденсата во времени по сравнению с мембраной, содержащей слой ПТФЭ толщиной 100 нм. Вместе с этим, для последней наблюдается лишь уменьшение диаметра пор на поверхности (рис. 9б). В то же время, для двух других композиционных мембран осаждение слоя ПТФЭ приводит к закрытию пор на их поверхности (рис. 9в, 9г), свидетельствующему о существенном уменьшении диаметра пор в осажденном слое полимера. Это сравнение показывает, что эффективность мембран в процессе мембранной дистилляции определяется не только величиной их пористости, но и состоянием пор на их поверхности. Следует также отметить, что смачиваемости исследуемых мембран несколько отличались друг от друга. Возможно, что эффективность мембран в процессе мембранной дистилляции также определяется величиной смачиваемости их поверхности.
Причиной уменьшения потока конденсата во времени может также являться осаждение соли на рабочей поверхности мембраны, т.е. загрязнение мембраны. Кроме этого, модифицированные мембраны имели шероховатость поверхности. Композиционная мембрана с толщиной нанесенного слоя ПТФЭ 500 нм имела самую высокую поверхностную шероховатость, за которой следовали мембраны с осажденным слоем ПТФЭ толщиной 300 и 100 нм. Очевидно, шероховатость мембраны влияет на площадь поверхности, на которой испаряется вода. Это должно существенно повлиять на эффективность мембран в процессе мембранной дистилляции. К сожалению, наши экспериментальные данные не позволяют нам сделать вывод о влиянии шероховатости осажденного слоя ПТФЭ на производительность данного процесса, поскольку композиционные мембраны имели различную пористость.
Причиной уменьшения потока конденсата во времени в процессе мембранной дистилляции может также являться разрушение осажденного на поверхности трековой мембраны гидрофобного покрытия и проникновения в поры продуктов деструкции. Исследование смачиваемости композиционных мембран по завершению процесса показало, что угол смачивания водой поверхности мембран, в зависимости от толщины покрытия, уменьшается на 8°−10°. Это может указывать на частичное разрушение слоя полимера. Однако, для исходных трековых мембран из ПЭТФ и ПП наблюдается аналогичная зависимость изменения потока конденсата во времени (рис. 10б). Для них также на начальном этапе происходит увеличение потока конденсата до определенного максимального значения, а затем величина потока начинает постепенно снижаться. При этом исходная ПЭТФ ТМ показала максимальное значение потока конденсата, равное 1815 ± 10 г/м2 ч. Высокое значение этой величины обусловлено гидрофильными свойствами матрицы мембраны. Для мембраны из полипропилена вследствие ее гидрофобности значение максимального потока равно 630 ± 4 г/м2 ч, что значительно ниже, чем для двухслойных композиционных мембран. Причиной низкого значения потока для ПП трековой мембраны является более значительная толщина по сравнению с толщиной нанесенного гидрофобного покрытия из ПТФЭ для композиционных мембран. Уменьшение потока конденсата во времени для исходных ТМ дает основание полагать, что основной причиной снижения производительности композиционных мембран является, скорее всего, конструкция мембранно-разделительного модуля, а не разрушение покрытия из ПТФЭ. Вопрос о стабильности осажденного на поверхности трековых мембран полимерного слоя является серьезной задачей и требует отдельного рассмотрения. Здесь же мы хотели бы заметить, поверхность композиционных мембран по окончании процесса мембранной дистилляции остается достаточно гидрофобной, и можно надеяться на то, что мембраны разработанного образца смогут найти применение для опреснения воды.
Таким образом, двухслойные композиционные мембраны, состоящие из тонкого высоко- или супергидрофобного слоя и толстой гидрофильной основы, показали более высокие значения потока конденсата, чем трековая мембрана из полипропилена. Модифицированные мембраны обеспечивают более короткий путь прохождения пара через гидрофобный слой по сравнению с трековой мембраной из полипропилена. Другая основная часть мембраны, которая является гидрофильной по природе, обеспечивает меньшее сопротивление массопереносу. Именно сочетание в составе композиционных мембран тонкого гидрофобного слоя с толстой гидрофильной основой приводит к повышению производительности процесса мембранной дистилляции при опреснении соленых вод.
Сравнение композиционных мембран по селективности разделения при опреснении водного раствора хлорида натрия с концентрацией 15.0 г/л (удельная электропроводность 26.85 мСм/см) методом мембранной дистилляции приведено в табл. 3. В таблице также представлены данные по селективности разделения для исходных трековых мембран из полиэтилентерефталата и полипропилена с одинаковой пористостью. Можно видеть, что исследованные композиционные мембраны обеспечивают высокую селективность разделения. В результате проведения процесса МД содержание соли в воде снижается в среднем более, чем в 5000 раз. Значение коэффициента солезадержания (R) в исследованном режиме составляет 99.97−99.98%. Для исходной ПЭТФ ТМ коэффициент солезадержания равен 53.45%, а для мембраны из ПП − 99.99%. Низкое значение R для трековой мембраны из ПЭТФ указывает на недостаточную селективность разделения в процессе мембранной дистилляции.
ВЫВОДЫ
На основании полученных результатов можно сделать следующие выводы. Формирование покрытий из ПП и СВМПЭ на поверхности ПЭТФ ТМ методом электронно-лучевого диспергирования приводит к образованию композиционных мембран, состоящих из гидрофильного и гидрофобного слоев. Одним из этих слоев является исходная ПЭТФ ТМ, характеризующаяся средним уровнем гидрофильности. Угол смачивания водой этого слоя составляет 65°. Другой нанесенный слой имеет гидрофобную природу. Величина угла смачивания этого слоя, в зависимости от природы осажденного полимерного покрытия и его толщины, изменяется.
Осаждение на поверхности ПЭТФ ТМ покрытий из СВМПЭ электронно-лучевым диспергированием приводит к формированию полимерного слоя с более развитой поверхностью в сравнении с покрытиями из ПП. Обусловлено это размерами осаждающихся полимерных наноструктур. Размеры наноструктур из СВМПЭ, как правило, имеют существенно большие размеры, чем наноструктуры из ПП. Значительный рост шероховатости осажденного покрытия из СВМПЭ при увеличении его толщины обусловливает более существенное повышение угла смачивания, величина которого изменяется от 92° до 125°.
Осаждение на поверхности композиционных мембран, содержащих покрытие из СВМПЭ, слоя ПТФЭ толщиной 100 нм электронно-лучевым диспергированием, приводит к образованию супергидрофобного покрытия. Величина угла смачивания для этого типа мембран в зависимости от общей толщины двухслойного покрытия изменяется от 150° до 160°. Значительное повышение угла смачивания объясняется меньшей свободной поверхностной энергией ПТФЭ и существенным развитием шероховатости этого слоя, по сравнению с покрытием из СВМПЭ, а также образованием полимерного покрытия, имеющего иерархическую структуру.
Осаждение на поверхности ПЭТФ ТМ однослойных покрытий из активной газовой фазы, получаемой методом электронно-лучевого диспергирования ПТФЭ, приводит к существенной гидрофобизации поверхностного слоя мембраны, степень которой зависит от толщины покрытия. При осаждении полимерного слоя толщиной 100 нм происходит формирование покрытия, обладающего высокогидрофобными свойствами, угол смачивания водой поверхности которого составляет 130°. Возрастание толщины осажденного слоя до 500 нм за счет существенного увеличения поверхностной шероховатости приводит к формированию покрытия, обладающего супергидрофобными свойствами, для которого угол смачивания составляет 155°.
Композиционные мембраны, состоящие из гидрофильной микропористой основы, в качестве которой использована трековая мембран из ПЭТФ, и осажденных на ее поверхности покрытий из ПТФЭ, полученных электронно-лучевым диспергированием, по сравнению с исходной мембраной, обеспечивают более высокую селективность разделения при обессоливании водного раствора хлорида натрия методом мембранной дистилляции. Кроме того, производительность двухслойных композиционных мембран в процессе мембранной дистилляции вследствие низкого сопротивления массопереносу (за счет уменьшения длины пути переноса водяного пара через гидрофобный слой покрытия из ПТФЭ) выше в сравнении с исходной ПП трековой мембраной. Получаемый в результате мембранной дистилляции дистиллят соответствует требованиям к питьевой воде и к технологической воде во многих производствах. Таким образом, композиционные мембраны разработанного образца могут быть применены для опреснения воды методом мембранной дистилляции.
Список литературы
Брык М.Т., Нигматуллин Р.Р. Мембранная дистилляция // Успехи химии. 1994. Т. 63. № 12. С. 1114−1129.
Drioli E., Ali A., Macedonio F. Membrane distillation: recent developments and perspectives // Desalination. 2015. V. 356. P. 56−84.
Eykens L., DeSitter K., Dotremont C., Pinoy L., Van der Bruggen B. Coating techniques for membrane distillation: an experimental assessment // Sep. Purif. Technol. 2018. V. 193. P. 38−48.
Alkhudhiri A., Darwish N., Hilal N. Experimental and theoretical investigation on water desalination using air gap membrane distillation // Desalination. 2012. V. 287. P. 55−60.
Khalifa A., Lawal D., Antar M., Khayet M. Experimental and theoretical investigation on water desalination using air gap membrane distillation // Desalination. 2015. V. 376. P. 94−108.
Woo Yu.Ch., Tijing L.D., Park M.J., Yao M., Choi J.-S., Lee S., Kim S.-H., An K.-J., Shon H.K. Electrospun dual-layer nonwoven membrane for desalination by air gap membrane distillation // Desalination. 2017. V. 404. P. 187−198.
Alklaibi A.M., Lior N. Membrane-distillation desalination: status and potential // Desalination. 2004. V. 171. P. 111−131.
El-Bourawi M.S., Ding Z., Ma R., Khayet M. A framework for better understanding membrane distillation separation process // J. Membr. Sci. 2006. V. 285. P. 4−29.
Qtaishat M., Khayet M., Matsuura T. Guidelines for preparation of higher flux hydrophobic/hydrophilic composite membranes for membrane distillation // J. Membr. Sci. 2009. V. 329. P. 193−200.
Essalhi M., Khayet M. Surface segregation of fluorinated modifying macromolecule for hydrophobic/hydrophilic membrane preparation and application in air gap and direct contact membrane distillation // J. Membr. Sci. 2012. V. 417–418. P. 163−173.
Gancarz I., Bryjak M., Kujawski J., Wolska J., Kujawa J., Kujawski W. Plasma deposited fluorinated films on porous membranes // Mater. Chem. Phys. 2015. V. 151. P. 233−242.
Agbaje T.A., Al-Gharabli S., Mavukkandy M.O., Kujawa J., Arafar H.A. PVDF/magnetite blend membranes for enhanced flux and salt rejection in membrane distillation // Desalination. 2018. V. 436. P. 69−80.
Korolkov I.V., Gorin Y.G., Yeszhanov A.B., Kozlovskiy A.L., Zdorovets M.V. Preparation of PET track-etched membranes for membrane distillation by photo-induced graft polymerization // Mater. Chem. Phys. 2018. V. 205. P. 55−63.
Mehta A., Zydnel A.L. Effect of spacer arm length on the performance of charge-modified ultrafiltration membranes // J. Membr. Sci. 2008. V. 313. P. 304−314.
Мельникова Г.Б., Жавнерко Г.К, Чижик С.А., Бильдюкевич А.В. Структура и механические свойства ультрафильтрационных мембран, модифицированных пленками Ленгмюра–Блоджетт // Мембраны и мембранные технологии. 2016. Т. 6. № 2. С. 144−151.
Bryjak M., Gancarz I. // Membrane prepared via plasma modification. In: Membranes for membrane reactors: preparation, optimization and selection / Eds. A. Basile and F. Gallucci. Chichester (UK): John Wiley & Sons. 2011. P. 549−568.
Kravets L.I., Gilman A.B., Dinescu G. Modification of polymer membrane properties by low-temperature plasma // Rus. J. Gener. Chem. 2015. V. 85. P. 1284−1301.
Pegalajar-Jurado A., Mann M.N., Maynard M.R., Fisher E.R. Hydrophilic modification of polysulfone ultrafiltration membranes by low temperature water vapor plasma treatment to enhance performance // Plasma Process. Polym. 2016. V. 13. № 6. P. 598−610.
Кравец Л.И., Гильман А.Б., Satulu V., Mitu B., Dinescu G. Формирование “diode-like” композитных мембран методом полимеризации в плазме // Перспективные материалы. 2017. № 9. С. 5−21.
Kravets L.I., Dmitriev S.N., Satulu V., Mitu B., Dinescu G. Structure and electrochemical properties of track membranes with a polymer layer obtained by plasma polymerization of acetylene // J. Phys. Confer. Ser. 2014. V. 516. Article 012006. 6 p.
Kravets L.I., Dmitriev S.N., Satulu V., Mitu B., Dinescu G. Fabrication and electrochemical properties of polymer bilayered membranes // Surf. Coat. Technol. 2011. V. 205. Suppl. 2. P. S455−461.
Chapman Ch.I., Bhattacharyya D., Eberhart R.C., Timmons R.B., Chuong Ch.-J. plasma polymer thin film depositions to regulate gas permeability through nanoporous track etched membranes // J. Membr. Sci. 2008. V. 318. P. 137−144.
Ясуда Х. Полимеризация в плазме. М.: Мир, 1988. 376 с.
Wang J., Song X., Li R., Shen J., Yang G., Huang. Fluorocarbon thin film with superhydrophobic property prepared by pyrolysis of hexafluoropropylene oxide // Appl. Sur. Sci. 2012. V. 258. P. 9782−9785.
Cai S., Zhang Y., Zhang H., Yan H., Lv H., Jiang B. Sol-gel preparation of hydrophobic silica antireflective coatings with low refractive index by base/acid two-step catalysis // ACS Appl. Mater. Interfaces. 2014. V. 6. P. 11470−11475.
Barsbay M., Güven O. Grafting in confined spaces: functionalization of nanochannels of track-etched membranes // Radiat. Phys. Chem. 2014. V. 105. P. 26−30.
Daoud W.A., Xin J.H., Zhang Y.H., Mak C.L. Pulsed laser deposition of superhydrophobic thin teflon films on cellulosic fibers // Thin Solid Films. 2006. V. 515. P. 835−837.
Drabik M., Polonskaya O., Kylian O., Cechvala J., Artemenko A., Gordeev I., Choukourov A., Slavinska D., Matolinova I., Biederman H. Super-hydrophobic coatings prepared by RF magnetron sputtering of PTFE // Plasma Process. Polym. 2010. V. 7. P. 544–551.
Satulu V., Mitu B., Pandele A.M., Voicu S.I., Kravets L., Dinescu G. Composite polyethylene terephthalate track membranes with thin teflon-like layers: preparation and surface properties // Appl. Surf. Sci. 2019. V. 476. P. 452–459.
Henda R., Wilson G., Gray-Munro J., Alshekhli O., McDonald A.M. Henda R., Wilson G., Gray-Munro J., Alshekhli O., McDonald A.M. Preparation of polytetrafluoroethylene by pulsed electron ablation: Deposition and wettability aspects // Thin Solid Films. 2012. V. 520. P.1885–1889.
Kravets L.I., Gilman A.B., Yablokov M.Yu., Shchegolikhin A.N., Mitu B., Dinescu G. Properties of poly(ethylene terephthalate) track membrane with a polymer layer obtained by electron beam dispersion of polytetrafluoroethylene in vacuum // High Temp. Mat. Proc. 2015. V. 19. P. 121–139.
Ярмоленко М.А., Рогачев А.А., Лучников П.А., Рогачев А.В., Джанг Сянь Хун // Микро- и нанокомпозиционные полимерные покрытия, осаждаемые из активной газовой фазы. / Под ред. А.В. Рогачева. М.: Радиотехника, 2016. 424 с.
Rogachev A.A., Tamulevicius S., Rogachev A.V., Yarmolenko M.A., Prosycevas I. The structure and molecular orientation of polytetrafluoroethylene coatings deposited from active gas phase // Appl. Surf. Sci. 2009. V. 255. P. 6851−6856.
Chen Q., Rogachev A.V., Yarmolenko M.A., Rogachev A.A., Jiang X., Gorbachev D.I. Peculiarities of electron-beam formation of hydrophobic and superhydrophobic coatings based on hydrocarbons of various molecular weights and PTFE // J. Coat. Sci. Technol. 2017. V. 4. P. 21−30.
Yang Ch., Li X.-M., Gilron J., Kong D.-F., Yin Y., Oren Y., Linder Ch., He T. CF4 Plasma-modified superhydrophobic PVDF membranes for direct contact membrane distillation // J. Membr. Sci. 2014. V. 456. P. 155−161.
Yan H., Lu X., Wu Ch., Sun X., Tang W. Fabrication of a super-hydrophobic polyvinylidene fluoride hollow fiber membrane using a particle coating process // J. Membr. Sci. 2017. V. 533. P. 130−140.
Butt H.-J., Ilia V. Roisman I.V., Brinkmann M., Papadopoulos P., Vollmer D., Semprebon C. Characterization of super liquid-repellent surfaces // Curr. Opin. Colloid Interface Sci. 2014. V. 19. P. 343−354.
Apel P.Yu., Dmitriev S.N. Micro- and nanoporous materials produced using accelerated heavy ion beams // Adv. Natur. Sci.: Nanosci. Nanotechnol. 2011. V. 2. Article 013002. 9 p.
Kravets L.I., Dmitriev S.N., Apel P.Yu. Production and properties of polypropylene track membranes // Collect. Czech. Commun. 1997. V. 62. P. 752−760.
Xiao J., Rogachev A.V., Yarmolenko V.A., Rogachev A.A., Liu Y., Jiang X., Sun D., Yarmolenko M.A. Formation features, structure and properties of bioactive coatings based on phosphate‑calcium layers, deposited by a low energy electron beam // Surf. Coat. Technol. 2019. V. 359. P. 6−15.
Мулдер М. Введение в мембранную технологию. М.: Мир. 1999. 514 с.
Апель П.Ю., Дмитриев С.Н. Оптимизация формы пор трековых мембран // Критические технологии. Мембраны. 2004. № 3. С. 32−37.
Орелович О.Л., Апель П.Ю. Приемы препарирования образцов трековых мембран для растровой электронной микроскопии // Приборы и техника эксперимента. 2001. Т. 44. № 1. С. 133−136.
Rezaei M., Warsinger D.M., Lienhard J.H., Duke M.C., Matsuura T., Samhaber W.M. Wetting phenomena in membrane distillation: mechanisms, reversal, and prevention // Water Research. 2018. V. 139. P. 329−352.
Scanning probe microscopy and spectroscopy: theory, techniques, and applications. Ed. by Dawn Bonnell. Cambridge: Wiley, 2001.516 p.
Миронов В.Л. Основы сканирующей зондовой микроскопии. Нижний Новгород: ИФМ РАН, 2004. 114 с.
Surface Analysis by auger and X-Ray photoelectron spectroscopy / Eds by Briggs D., Grant J.T. Chichester: IM Publ., 2003. 505 p.
Beamson G., Briggs D. High Resolution XPS of Organic Polymers: The Scienta ESCA300 Database. Chichester: John Wiley, 1992. 295 p.
Quere D. Wetting and roughness // Ann. Rev. Mater. Res. 2008. V. 38. P. 71−99.
Бойнович Л.Б., Емельяненко А.М. Гидрофобные материалы и покрытия: принципы создания, свойства и применение // Усп. хим. 2008. Т. 77. № 7. С. 619−638.
Vesel A., Mozetic M., Zalar A. XPS study of oxygen plasma activated PET // Vacuum. 2008. V. 82. P. 248–251.
Vesel A., Mozetic M. Modification of PET surface by nitrogen plasma treatment // J. Phys. Confer. Ser. 2008. V. 100. Article 012027. 4 p.
Nishime T.M.C., Toth A., Hein L.R.O., Kostov K.G. Surface characteristics analysis of polypropylene treated by dielectric barrier discharge at atmospheric pressure // J. Phys. Confer. Ser. 2012. V. 370. Article 012025. 6 p.
Kostov K.G., Ueda M., Tan I.H., Leite N.F., Beloto A.F., Gomes G.F. Structural effect of nitrogen plasma-based ion implantation on ultra-high molecular weight polyethylene // Surf. Coat. Technol. 2004. V. 186. P. 287−290.
Kolska Z., Reznickova A., Hnatowicz V. Svorcik V. PTFE surface modification by Ar plasma and its characterization // Vacuum. 2012. V. 86. P. 643−647.
Hubert J., Mertens J., Dufour T., Vandencasteele N., Reniers F., Viville P., Lazzaroni R., Raes M., Terryn H. Synthesis and texturization processes of (super)-hydrophobic fluorinated surfaces by atmospheric plasma // J. Mater. Res. 2015. V. 30. P. 3177–3191.
Bismark A., Schulz A., Zell H., Springer J., Tahhan R., Klapotke T.M., Michaeli W. Influence of Fluorination on the Properties of Carbon Fibres // J. Fluor. Chem. 1997. V. 84. P. 127−134.
Кравец Л.И., Алтынов В.А., Яблоков М.Ю., Гильман А.Б., Satulu V., Mitu B., Dinescu G. Исследование морфологии и химической структуры наноразмерных пленок политетрафторэтилена, осажденных на поверхности трековых мембран плазмохимическими методами // Химия высоких энергий. 2018. Т. 52. № 4. С. 318−325.
Dmitriev S.N., Kravets L.I., Sleptsov V.V., Elinson V.M., Potryasai V.V. Hydrophilization of the surface of polyvinylidene fluoride membranes in non-polymerizing gas plasma // Heavy Ion Physics, FLNR Scientific Report 1999−2000. JINR Dubna, Russia. 2001. P. 225−226.
Khayet M., Matsuura T. Preparation and characterization of polyvinylidene fluoride membranes for membrane distillation // Ind. & Eng. Chem. Res. 2001. V. 40. P. 5710−5718.
Hawlader M.N.A., Bahar R., Ng K.Ch., Stanley L.J.W. Transport analysis of an air gap membrane distillation (AGMD) process // Desalination and Water Treatment. 2012. V. 42. P. 333−346.
Дополнительные материалы отсутствуют.
Инструменты
Коллоидный журнал