Известия РАН. Механика твердого тела, 2023, № 2, стр. 3-29
МЕХАНИКА ДЕФЕКТОВ В БЕЗДИСЛОКАЦИОННЫХ МОНОКРИСТАЛЛАХ КРЕМНИЯ
Н. А. Верезуб a, *, А. И. Простомолотов a, **
a Институт проблем механики им. А.Ю. Ишлинского РАН
Москва, Россия
* E-mail: verezub@ipmnet.ru
** E-mail: aprosto@inbox.ru
Поступила в редакцию 03.08.2022
После доработки 16.08.2022
Принята к публикации 22.08.2022
- EDN: DHFWUC
- DOI: 10.31857/S057232992260061X
Аннотация
Задачи механики дефектов в бездислокационных монокристаллах кремния являются актуальными и технически значимыми в связи с интенсивным развитием микроэлектроники, которая предъявляет все более высокие требования по минимизации уровня микро- и нанодефектов в пластинах кремния, используемых для изготовления микроэлектронных чипов. Решение этих задач связано с изучением закономерностей термомеханических процессов как на стадии выращивания монокристаллов кремния, так и на последующих термообработках вырезаемых из них пластин. В статье дается обзор теоретических и экспериментальных работ, направленных на разработку способов управления этими процессами. Это включает развитие физических представлений о дефектообразовании в бездислокационном монокристаллическом кремнии и разработку математических моделей, соответствующих различным температурным диапазонам, реализуемым как при выращивании монокристалла, так и при термообработке, вырезаемых их него пластин. Так, вблизи температуры кристаллизации моделируются процессы быстрой рекомбинации и диффузионного переноса собственных точечных дефектов (вакансий и межузельных атомов кремния), а при более низких температурах моделируются процессы их агломерации в микродефекты (поры и кластеры межузельных атомов кремния). Иллюстрируется верификация таких моделей для двух экспериментальных процессов выращивания монокристаллов кремния диаметром 150 мм методом Чохральского, а также для процесса быстрой высокотемпературной термообработки вырезанных на их основе пластин кремния.
1. Развитие представлений о дефектообразовании в бездислокационнных монокристаллах кремния. К началу 1980-х годов накопилось достаточно много экспериментальных данных о дефектах, названных D-дефектами, образующимися из избыточных вакансий при выращивании кристаллов методом зонной плавки (ЗП) с большими скоростями вытягивания [1]. Они нашли отражение в фундаментальной статье Воронкова [2], в которой предложена физическая концепция взаимодействия собственных точечных дефектов (СТД): вакансий и межузельных атомов кремния применительно к выращиванию монокристаллического бездислокационного кремния.
Согласно этой концепции, вблизи фронта кристаллизации (ФК) происходит “быстрая” рекомбинация вакансий (i) и собственных межузельных атомов (v), в результате которой монокристалл растет с преобладанием вакансий или межузельных атомов кремния (или по принятой терминологии: в вакансионном или межузельном режимах). Впервые было предложено количественно это оценивать по некоторой критической величине ξcrit, которая определяется как отношение скорости вытягивания Vp к осевому градиенту температур G на ФК. Так, при ξ = Vp/G < ξcrit доминируют межузельные атомы, а при ξ > ξcrit – вакансии. Если осевой градиент температуры меняется значительно в радиальном сечении растущего монокристалла кремния, то величина ξ может становиться больше ξcrit в центральной части слитка и там преобладают вакансии, а при ξ меньшей ξcrit на периферии поперечного сечения слитка преобладают межузельные атомы. Однако математическая модель этой концепции была представлена только в одномерной (по оси слитка) формулировке.
Расчеты в [2] проведены на основе одномерной стационарной модели v‑i‑рекомбинации. Данные о тепловом поле в кристалле считаются известными и задаются как аналитически, так и из эксперимента или других расчетных работ [3]. Результаты таких расчетов в [4] позволили оценить тип и распределения остаточных СТД-концентраций в растущем кристалле в зависимости от величины ξ. Показано, что значительная остаточная концентрация вакансий возникает, если скорость роста превышает критическую скорость (Vp)crit = ξcrit ⋅ G и она увеличивается при возрастании Vp/(Vp)crit. Также показано, что концентрация ростовых межузельных атомов при Vp < (Vp)crit является убывающей функцией от Vp/(Vp)crit. Концентрации ростовых дефектов, т.е. вакансий при Vp ≫ (Vp)crit и межузельных атомов при Vp ≪ (Vp)crit, оцениваются величиной ~1014 см–3.
В начале 1990-х годов эта концепция была экспериментально подтверждена после обнаружения частиц кристаллического происхождения, являющихся результатом образования дефектов в монокристаллах, выращенных по методу Чохральского (МЧ). Эксперименты выявили образование в монокристаллах OSF (Oxidation-induced Stacking Fault nuclei) – кольца. Доминирующими типами СТД снаружи и внутри OSF-кольца являются межузельные атомы и вакансии соответственно.
В последующие годы был систематизирован обширный экспериментальный материал по свойствам кислорода в МЧ- и ЗП-выращиваемых монокристаллах кремния, а также проанализировано поведение электрически активных кислородных комплексов в термообработанном кремнии и механизмы преципитации кислорода в нем [5]. Сложилось мнение, что образование кислородных преципитатов SiO2 связано с эмиссией межузельных атомов кремния и абсорбцией вакансий по следующей реакции:
Дальнейшее охлаждение приводит к сильному стоку вакансий в поры. Он будет практически полным, если вакансии не связаны кислородом в комплексы vO2 ниже некоторой характеристической температуры Tb (~1020°С). Вакансии, оставшиеся после поглощения порами, участвуют в зарождении оксидных частиц при дальнейшем охлаждении (ниже 950°С). Величина остаточной концентрации вакансий определяет зарождение кислородных кластеров при более низких температурах (650–700°С).
Сопутствующие работы позволили получить необходимые экспериментальные данные. Так, в [7] обсуждается величина равновесного коэффициента распределения (k0) кислорода в расплаве кремния на основе ростовых процессов по МЧ и исследования распределений кислорода в кристаллах. При этом сделан неожиданный вывод о том, что этот коэффициент соответствует оттеснению кислорода от ФК и его величина изменяется в узком диапазоне, меньшем 1: k0 = 0.2–0.3. В [8] дается обзор методов измерения термофизических свойств СТД в кремнии (самодиффузия кремния, в том числе в неравновесных условиях), а также приводятся температурные зависимости коэффициента диффузии. В [9] описана методика теста пластин кремния после химической обработки и полировки на выявление OSF-кольца для осуществления качественного контроля в производственных условиях, реализуемых на заводе ЭЛМА (г. Зеленоград).
Большой объем ростовых экспериментов проведен в [10]. Анализ ростовых микродефектов выполнен для монокристаллов кремния, выращенных в условиях вакансионного пересыщения. Анализируются высокочистые ЗП-кристаллы кремния диаметром 2, 3 и 4 дюйма. Скорость роста была 3 мм/мин, ξ = 0.210 мм2/K ⋅ мин и Vp/(Vp)crit = 1.4. Плотность ростовых микродефектов была малой: 101–102 см–2, основными дефектами считаются скользящие 60°-дислокации, плотность которых достигает 106–106 см–2, их размер 50–100 нм. Показано, что генерация скользящих дислокаций связана с образованием пор, которые являются следствием агломерации вакансий при очень больших скоростях роста.
Интересна связь напряженного состояния монокристалла кремния с наличием микродефектов. Так, в [11] обсуждаются причины большого разброса значений критического напряжения для монокристаллов кремния: 60–150 Гс/мм2. Данные получены при статическом нагружении образцов при высоких температурах и экстраполяции значений к Тm. Такой разброс свидетельствует о том, что в кристаллах кремния присутствуют источники дислокаций различной природы и разных размеров. Такими источниками могут служить микроскопические дислокационные петли, возникающие в охлаждающемся кристалле в результате трансформации кластеров точечных дефектов. Дислокации могут зарождаться и на преципитатах примеси. В промышленных условиях нарушение бездислокационного роста чаще всего обусловлено попаданием в расплав инородных частиц. В этом случае величины термоупругих напряжений являются несущественными и оптимизация тепловых режимов должна проводиться с учетом условий образования и осаждения моноокиси кремния.
Для ЗП-выращивания математические модели v‑i-рекомбинации и образования вакансионных кластеров типа vO2 рассмотрены в целом ряде работ. В [12] приведены совместно математическая модель v-i-взаимодействия и термоупругие напряжения при выращивании кристаллов кремния диаметром 200 мм. В [13] выполнено численное моделирование и проанализировано радиальное распределение электропроводимости в монокристаллах кремния, выращенных ЗП-методом. Численное моделирование проведено на основе “глобальной” тепловой ЗП-модели, в которой учитываются тепловая конвекция и вращение кристалла с определением формы расплавленной зоны и расчетом индукционного энерговыделения. Также в [14] численно изучено влияние высокочастотного нагрева на изменения электропроводимости, а в [15] проведено численное моделирование взаимодействия СТД при ЗП-выращивании монокристаллов кремния малого диаметра (0.8 дюйма) для различных коэффициентов диффузии и энергетических порогов процесса v-i-рекомбинации, позволившее дать сравнение с данными расчетов по модели В.В. Воронкова [2] и измерениями распределений микродефектов DLTS (Deep Layer Transition metal Spectroscopy) [16].
Для МЧ-выращивания в [3, 17, 18] образование вакансионных кластеров рассматривается на основе двумерной стационарной модели v-i-рекомбинации и двумерного теплового поля в кристалле, которое предварительно рассчитывается в рамках “глобальной” тепловой МЧ-модели. В [19, 20] тепловое поле полагается известным из эксперимента и рассматривается нестационарную двумерную модель v-i-рекомбинации совместно с моделью образования вакансионных кластеров. В [21] для расчета равновесных конфигураций и коэффициентов диффузии использовался межатомный потенциал Штиллингера–Вебера и показано хорошее согласие расчетного распределения межузельных атомов с экспериментальным.
В [17] представлена стационарная модель СТД-взаимодействия, которая включает все возможные процессы: движение при вытягивании кристалла, СТД-диффузию и термодиффузию, а также v-i-рекомбинацию. Показано хорошее соответствие критерию Воронкова при значении ξcrit = 0.134 мм2/мин ⋅ К. Обсуждается ситуация, когда осевой температурный градиент на ФК постепенно снижается при постоянной скорости выращивания монокристалла. В этом случае область, образованная дефектами А‑ и В-типа, ограничивается узкими полосами различного типа (с В-дефектами, без дефектов и с нарушениями кристаллической структуры). После отжига в окислительной атмосфере в области этих полос проявляется OSF-кольцо. Подтверждается гипотеза, что ростовыми дефектами в монокристаллах кремния вакансионного типа, выращенных по МЧ, являются поры и оксидные частицы. Они гетерогенно зарождаются в узком температурном диапазоне (1100–1000°C), в зависимости от начальной концентрации вакансий. Доминирующим типом ростовых дефектов обычно являются поры. Их плотность приблизительно равна 3 × 106 см–3, радиус – 55 нм. Снижение начальной концентрации вакансий приводит к смене доминирующего типа микродефектов с пор на оксидные частицы. Их плотность и радиус оцениваются в 3 × 108 см–3 и 5 нм. Поскольку снижение начальной концентрации вакансий происходит от центра кристалла к его боковой поверхности (или по направлению к границе между вакансиями и межузельными атомами), то вакансионная область состоит из внутренней части, образованной порами, и узкой внешней полосы из оксидных частиц.
Существует альтернативный подход к пониманию дефектообразования в кремнии [22], где представлена иная (чем модель Воронкова [2]) физическая модель образования микродефектов в бездислокационных монокристаллах кремния на основе экспериментального материала (для небольших диаметров кристаллов по данным Запорожского титаномагниевого комбината). Обсуждаются процессы дефектообразования при широком варьировании условий выращивания монокристаллов. Анализируется влияние условий изготовления приборных композиций и имитационных термических обработок на образование, трансформацию и электрическую активность микродефектов. Рассматривается механизм образования ростовых микродефектов с учетом полученных результатов. Отметим, что в [22] развивается подход на основе предположений о гетерогенной природе образования и трансформации ростовых микродефектов. В обоснование этого подхода авторы отмечают, что динамика СТД в физической модели В.В. Воронкова определяется процессом рекомбинации СТД и не учитывает влияние фоновых примесей (кислорода и углерода). Их экспериментальные данные дали основания для предположения о высоком барьере для СТД-рекомбинации и преобладании диффузии примесей и их комплексов. Однако известно, что В.В. Воронков использовал данные для монокристаллов с малой концентрацией фоновых примесей, поэтому в его тестах достаточно точно выполнялось условие “быстрой” СТД-рекомбинации. Авторы [22] использовали монокристаллы с высоким содержанием примесей, которые препятствуют “быстрой” рекомбинации СТД, что отразилось в их оценках, показавших существенное повышение энергетического порога СТД-рекомбинации.
В целом можно отметить наиболее важные температурные диапазоны, определяющие математические модели дефектообразования. Температурная зона, прилегающая к ФК (от 1683 до ~1450 K), соответствует рекомбинации собственных точечных дефектов (вакансий и межузельных атомов кремния) и образованию первичных микродефектов, связанных с распадом пересыщенного твердого раствора СТД. Далее по мере понижения температуры в зоне 1450–1100 K происходит другой физический процесс с участием кислорода, поэтому важно регулировать тепловые условия как непосредственно вблизи ФК, так и на удалении от него, где образуются микродефекты (вакансионно-кислородные комплексы). Управление дефектообразованием в этих температурных зонах является важной задачей, актуальность которой стимулировала разработку двумерных математических моделей дефектообразования в сопряжении с сопряженной тепловой моделью выращивания монокристалла для учета особенностей конкретной МЧ-установки.
2. Верификация моделей дефектообразования на основе данных технологических экспериментов по МЧ-выращиванию монокристаллов кремния. Ввиду большой практической значимости малодефектного бездислокационного монокристаллического кремния упомянутые выше модели дефектообразования тестировались в ряде ведущих индустриальных фирм и университетов применительно к самому распространенному промышленному выращиванию монокристаллов кремния – МЧ-процессу. Для расчета дефектообразования в конкретных ростовых процессах применяется двухмерное математическое моделирование на основе “глобальной” тепловой МЧ-модели.
Авторами из Massachusetts Institute of Technology [3, 18] сопряженное тепловое моделирование выполнено по программе IHTCM применительно к МЧ-выращиванию кристалла диаметром 150 мм из тигля диаметром 440 мм при вращении кристалла и тигля со скоростями 15 и 9 об/мин, соответственно. Результаты такого теплового моделирования использованы в модели “быстрой” v-i-рекомбинации [17, 23], где изучается СТД-взаимодействие как в процессе МЧ-выращивания монокристаллов кремния, так и при отжиге вырезаемых из них пластин. При этом отмечается, что в большинстве работ используются недостаточно точные коэффициенты диффузии, равновесной концентрации и кинетических параметров, а также анализируются различные методики их определения. Например, в [17] величина ξcrit для OSF-кольца была равна 0.134 мм2/мин ⋅ K, хотя в [24] авторы предлагают более высокое ее значение 0.22 мм2/мин ⋅ K. Можно отметить, что такое отличие может быть вызвано различием методик и программ для сопряженного теплового моделирования: в первом случае использовалась программа FEMAG, а во втором – ABAQUS.
В целом отметим, что критерий В.В. Воронкова ξcrit, определяемый как отношение скорости вытягивания монокристалла кремния к осевому температурному градиенту Vp/G [мм2/мин ⋅ К], не является автомодельной безразмерной величиной, поэтому его значения могут варьироваться для разных процессов МЧ- и ЗП-выращивания монокристаллов кремния. На значение ξcrit влияет как диаметр выращиваемого монокристалла, так и величина радиальной неоднородности осевого температурного градиента G на ФК. Однако значительные отличия ξcrit в [24] могут объясняться неточностью расчета температурных градиентов в МЧ-процессе, т.к. по результатам многих других МЧ-процессов выращивания для фиксированного диаметра монокристалла и близких тепловых условий выращивания (на схожих тепловых МЧ-установках) значения ξcrit являются близкими к 0.13. Это свидетельствует о достоверности этой величины и объясняет ее широкое использование в технологической практике. Для единообразия мы поправили в тексте значения ξcrit до двух значащих цифр.
Авторами из Samsung Electronics Co. [25] экспериментально исследовано влияние ростовых микродефектов на качество пластин кремния, DRAM-память и другие приборные элементы, изготавливаемые на их основе. Обсуждаются механизмы возникновения различных типов микродефектов в монокристаллах кремния при МЧ-выращивании, а также применимость критерия В.В. Воронкова для обоснования способов получения совершенных кристаллов.
Авторами из Mitsubishi Materials Silicon Co. [26] обсуждается роль СТД в образовании центров преципитации кислорода в бездислокационном кремнии. В рамках модели В.В. Воронкова объясняется преципитация кислорода – формирование центров преципитации в растущем кристалле. Выполнено математическое моделирование распределений микродефектов на основе данных теплового моделирования МЧ, проведенного по программе FEMAG. Дано сравнение распределений осевого градиента температуры G на ФК без и с учетом конвекции в расплаве, рассчитанной по двум моделям турбулентности. Обсуждается сравнение формы OSF-кольца c данными расчетов СТД-концентраций.
Авторами из Shin-Etsu Handotai Co. [27–29] экспериментально изучено влияние диаметра кристалла и скорости его вытягивания из расплава на образование ростовых микродефектов в МЧ-кремнии. Проведены измерения температур в кристалле вблизи ФК с помощью термопар и обсуждается механизм образования ростовых микродефектов. Исследовано 6 слитков кремния разного диаметра (200, 150, 125, 100, 75, 50 мм) и длиной 30 см, выращенных из загрузки 70 кг в одинаковых условиях. Все кристаллы были ориентации 〈100〉, р-типа с удельным сопротивлением 10–20 Ом ⋅ см. Для анализа микродефектов использован метод определения времени жизни электрических носителей. В работе критикуется величина критерия В.В. Воронкова ξcrit и его использование в других работах, где проведены расчеты по программе FEMAG.
Авторами из Kotmatsu Electronic Metals Co. [19, 20] рассмотрена количественная модель образования ростовых дефектов в монокристаллах МЧ-кремния. В [19] численно исследована зависимость распределений СТД от ростовых условий и дано ее сравнение с экспериментальными данными. В [20] определяются равновесные концентрации (Cve, Cie) и коэффициенты диффузии (Dv, Di) межузельных атомов и вакансий в кристаллах кремния на основе анализа поведения ростовых микродефектов. При значениях ξcrit возникают условия для образования совершенной структуры кристалла, что проверено по расчетным распределениям микродефектов в кристаллах. Утверждается, что определяющими для величины ξcrit являются значения температурного градиента на кромке ФК.
Авторы из Osaka University [30] теоретически обосновывают значения равновесных СТД-концентраций в различных условиях МЧ-выращивания кристаллов кремния. Рассматриваются равновесные концентрации на поверхности кристалла, в его объеме и во время образования вторичных дефектов, т.е. дислокационных петель и пор. Утверждается, что формула для расчета равновесной СТД-концентрации не может быть одной и той же во время всего ростового процесса. В целом, сделанные оценки согласуются с выводами В.В. Воронкова в [4].
Авторами из Nippon Steel Co. [31] экспериментально изучалось влияние легирования азотом на образование ростовых микродефектов. Это относится к образованию пор и оксидных преципитатов, содержащих азот. Характеристики этих дефектов зависят от концентрации азота. Обычно концентрация пор уменьшается при увеличении концентрации азота и лишь небольшое количество пор наблюдается в кристалле, легированном азотом до концентрации выше 1015 см–3. В таких кристаллах оксидные преципитаты, содержащие азот и кислород, стабильно растут при большой температуре ~ 1100°С. Из ростовых экспериментов следует, что азот подавляет рост пор, в результате чего остается большее число свободных вакансий, которые становятся центрами роста оксидных преципитатов.
Авторами из Sumitomo Metal Industries Ltd. [24] обсуждаются измерения микродефектов в монокристалле кремния диаметром 150 мм, легированного бором (15.5–100 Ом ⋅ см), выращенного в направлении 〈100〉. Концентрация кислорода составляет 1.5 × 1017 см–3, скорость вытягивания Vp = 1.2–0.7 мм/мин, длина L = 50 см.
Авторами из Tokyo Institute of Technology [32] рассматривается модель для расчета распределений и размеров пор. При использовании расчетной концентрации точечных дефектов эта модель позволяет вычислять образование пор и их рост при T < < 1150°C. По этой модели можно также рассчитывать толщину окисной пленки, которая образуется на внутренней стенке поры. Считается, что эта модель может быть адаптирована к высокой концентрации примесей (B, P, As, Sb). В [33] рассматривается модель оксидной преципитации при отжиге пластин кремния. Морфология преципитата определяется из условия минимума свободной энергии. Моделирование начинается при 1000°С с входной концентрацией остаточных точечных дефектов после COP-образования. Плотность и скорость роста преципитатов согласуется с экспериментом. В [34] исследовано влияние осевых температурных градиентов на образование ростовых дефектов при выращивании кристалла при Ga > Ge (Ga – градиент на оси, Ge – на боковой поверхности кристалла), что необычно для МЧ-выращивания. Установлено, что при изменении скорости вытягивания Vp форма OSF-кольца преобразуется в W-образный профиль, который не обнаруживался ранее. W-образная форма OSF-кольца приводит к инверсии распределения ростовых микродефектов внутри и вне кольца: пластины включали дислокационные кластеры внутри кольца, а поры были вне этого кольца.
Авторами из Zhejiang University (Hangzhou, China) [35] дано сравнение поведения OSF-дефектов в легированных и нелегированных азотом монокристаллах кремния. Образцы подвергались одной и двум стадиям термоотжига. Размер и плотность OSF-дефектов изучались с помощью оптического и электронного микроскопов. Обнаружено, что при быстрой низкотемпературной термообработке (~750°С) OSF-дефекты лучше проявляются в кристаллах кремния, легированных азотом (АМЧ). Однако с увеличением времени термообработки плотность OSF-дефектов не изменяется в АМЧ-кремнии, но значительно увеличивается в МЧ-кремнии, при этом размер OSF-дефектов становится больше.
3. Математическая модель быстрой СТД-рекомбинации и переноса. Данную статью следует рассматривать в комплексе с предшествующей статьей [36], посвященной разработке сопряженной термомеханичекой модели МЧ-выращивания монокристаллов кремния. Отметим, что упомянутые в п. 2 программы IHTCM и FEMAG также предназначены для решения задач сопряженного теплопереноса (с учетом сложной геометрии установки, расчетом кондуктивного теплообмена и теплового излучения, гидродинамики расплава, процесса кристаллизации) при выращивании монокристаллов МЧ-кремния. В этих программах применяется конечно-элементная аппроксимация, гидродинамика расплава в МЧ-модели рассчитывается с использованием турбулентных моделей. В целом методические основы этих программ соответствуют функциональным возможностям компьютерной программы, применяемой авторами статьи [36].
Такое комплексное исследование проводилось авторами статьи в течение ряда лет в кооперации с ведущими отечественными и зарубежными технологическими организациями (ГИРЕДМЕТ, ЭЛМА, MEMC Inc.).
Физическая суть модели дефектообразования В.В. Воронкова состоит в том, что аннигиляция вакансий и междоузельных атомов вблизи ФК в значительной степени определяет их последующую миграцию и распределение в кристалле. Скорость аннигиляции равна разности между скоростями прямой реакции рекомбинации и обратной реакции термической генерации пар СТД. Скорость прямой (бинарной) реакции рекомбинации пропорциональна произведению концентраций взаимодействующих СТД. Скорость обратной реакции связана со скоростью прямой реакции законом действующих масс. Таким образом, скорость аннигиляции записывается в виде:
В выращиваемом МЧ-кристалле кремния перенос вакансий и межузельных атомов осуществляется в основном конвективной диффузией, процессом термодиффузии мы пренебрегаем. Концентрации Cv(r, z, t) – вакансий и Ci(r, z, t) – межузельных атомов удовлетворяют диффузионно-рекомбинационным уравнениям [37]:
(3.1)
$\frac{{\partial {{C}_{{\text{i}}}}}}{{\partial t}} = {\text{div}}\left( {{{D}_{{\text{i}}}}\nabla {{C}_{{\text{i}}}}} \right) - {{V}_{P}}\frac{{\partial {{C}_{{\text{i}}}}}}{{\partial z}} - {{K}_{{{\text{iv}}}}}\left( {{{C}_{{\text{v}}}}{{C}_{{\text{i}}}} - {{C}_{{{\text{v}}e}}}{{C}_{{{\text{i}}e}}}} \right)$Коэффициенты диффузии (Dv, Di) и равновесные концентрации вакансий и межузельных атомов (Cve, Cie) удобно задавать с использованием их значений в точке плавления (Tm) следующим образом:
Индекс m соответствует значению данной величины при температуре плавления (кристаллизации) Tm. Коэффициент рекомбинации записывается в виде:
Хотя полный набор констант в точности неизвестен, они связаны между собой определенными соотношениями.
Во-первых, известные данные по коэффициенту самодиффузии кремния и по диффузии в нем ряда примесей (Au, Zn и др.) позволяют оценить величину произведений DiCie, т.е. сумму энергий EiD + Ei = 4.8 эВ и Dim×Cim ≈ 2.6 × 1011 с–1см–1.
Во-вторых, значение ξcrit для перехода от межузельного к вакансионному режиму роста (в рамках одномерной диффузионной задачи для малых значений EiD и EvD) приближенно оценивается следующей формулой (см. [4]):
В-третьих, константа Dim может рассматриваться как подгоночный параметр, который логично выбирать в интервале значений (2.0–5.5) × 10–4 см2/с и нужно изменять значения Cvm и Cim в соответствии с величиной ξcrit. Значению ξcrit = 0.13 мм2/K ⋅ мин соответствуют параметры из табл. 1.
Таблица 1.
Параметры СТД-модели
Коэффициент диффузии вакансий | Dvm | см2/с | 4.0 ×10–5 |
Коэффициент диффузии межузельных атомов кремния | Dim | см2/с | 5.25 × 10–4 |
Диффузионный порог вакансий | EvD | эВ | 0.35 |
Диффузионный порог межузельных атомов кремния | EiD | эВ | 0.20 |
Равновесная концентрация вакансий | Cvm | см–3 | 7.2 × 1014 |
Равновесная концентрация межузельных атомов кремния | Cim | см–3 | 5.2 × 1014 |
Равновесный порог образования вакансий | Ev | эВ | 4.5 |
Равновесный порог образования межузельных атомов кремния | Ei | эВ | 4.6 |
Можно отметить, что по результатам процессов выращивания монокристаллов кремния диаметром 100 и 150 мм критерий В.В. Воронкова ξcrit остается близким к значению 0.13 мм2/мин ⋅ К. Небольшая 9%-я его вариация в разных процессах может быть вызвана различиями в расчетных программах и реальных тепловых условиях выращивания монокристаллов кремния. Этот критерий широко используется в технологической практике, хотя не является автомодельной и безразмерной величиной.
Значение параметра Erec неизвестно. При его выборе требуется выполнение условия “быстрой” рекомбинации, в результате которой “выживающий” СТД должен быть абсолютно преобладающим. Это условие выполняется, если Erec не превышает 1.5 эВ. Нами использована величина Erec = 1.5 эВ. Радиус рекомбинации rcap принят равным 3.0 × 10–8 см.
На рис. 1 показана расчетная схема v-i -взаимодействия в кристалле кремния. Здесь справа от оси симметрии Г1: ФК – Г2 и z = H0 – его вогнутость, боковая поверхность кристалла Г3, верхняя граница Г4 при z = H области v-i-взаимодействия. Слева от оси показана расчетная сетка треугольных конечных элементов. В проведенных расчетах: H = 11.5 см. Задаются граничные условия:
Рис. 1.
Расчетная схема v-i -взаимодействия в кристалле кремния. Здесь справа от оси симметрии Г1: ФК Г2 (z = H0 – его вогнутость), боковая поверхность кристалла Г3, верхняя граница Г4 области v-i-взаимодействия. Слева от оси показана сетка треугольных конечных элементов.
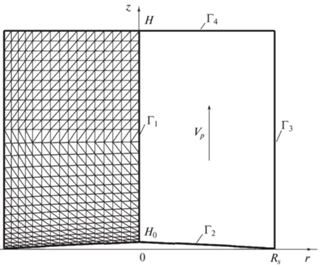
Рис. 2.
Процесс ТУ-6-18: распределение изотерм [K] в кристалле и других компонентах ростового узла на различных стадиях роста в зависимости от объема цилиндрической части выращенного кристалла: a – 10, b – 50, c – 80%.
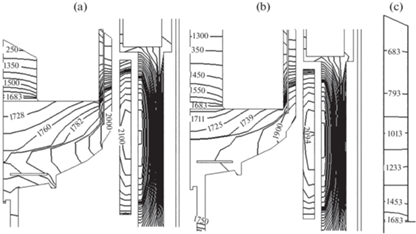
Здесь C соответствует текущим значениям Cv или Ci, а $C_{e}^{{}}$ – отвечающим им значениям равновесной концентрации.
Для теста по данным одномерной рекомбинационной модели температурное поле в кристалле задавалось зависящим только от z:
В этом случае результаты расчетов по двумерной модели должны соответствовать результатам решения задачи в одномерной постановке. Сравнение величины ξ при изменении осевого температурного градиента GS в диапазоне 30–300 K/см и вариациях скорости вытягивания Vp вблизи порога v-i-перехода показывает, что переход имеет место при постоянном значении ξcrit = 0.13 мм2/K · мин, что отвечает критерию выбора коэффициентов в данной модели. В случае двумерной модели при Kiv ∼ 2 × 10–19 см3/с достаточно точно выполняется условие “быстрой” рекомбинации: CveCie = CvCi. Определенная по двумерной модели величина остаточной концентрации “выживающих” дефектов (для вакансионного режима, реализуемого при GS = 120 K/см, Vp = 1.61 и 1.58 мм/мин) составила Cvres = 3.9 × 1012 см–3. По оценке [4] эта величина несколько ниже: Cvres = 2.8 × 1012 см–3. Небольшое расхождение вызвано различной аппроксимацией уравнений. Можно считать, что для одномерного температурного поля решения, полученные по данной двумерной модели, достаточно хорошо соответствуют результатам одномерной модели и аналитическим оценкам В.В. Воронкова.
Диффузионно-рекомбинационные уравнения (3.1–3.2) можно свести к одному уравнению. Для этого предполагается, что скорость рекомбинации очень высокая и произведение двух концентраций CvCi близко к произведению их равновесных величин. Тогда величины Cv и Ci не являются независимыми и могут быть выражены одна через другую следующим соотношением:
Диффузионная задача сводится к одной независимой переменной, причем удобно выбрать разность Civ. Тогда концентрации выражаются в виде:
Величина Civ определяется как разность концентраций межузельных атомов кремния Ci и вакансий Cv. Если значения Civ > 0, то в области монокристалла, где это выполняется, существует межузельный режим выращивания монокристалла кремния, а при Civ < 0 в области преобладают вакансии, что означает вакансионную область в монокристалле. Обсуждение знака и значений величины Civ приводится далее при анализе результатов (рис. 4, 5, 7).
Рис. 3.
Зависимость параметров тепловой истории выращивания слитка (Ga, Ge [K/см] и ξa, ξe [мм2/K ⋅ мин]) от % объема цилиндрической части: a – кристалл процесса ТУ-6-18, штрихпунктирная линия соответствует v-i-переходу при ξcrit = 0.136 мм2/K ⋅ мин; b – кристалл процесса ТУ-6-20, штрихпунктирная линия соответствует “взвешенной” зависимости параметров ξa и ξe с коэффициентом 0.6.

Рис. 4.
Картины распределения разности концентраций Civ [см–3] в вакансионном (a), смешанном (b) и межузельном (c) режимах, возникающие в результате v-i-рекомбинации для различных стадий роста и скоростей выращивания кристалла из тигля диаметром 18 дюймов в процессе ТУ-6-18: a – 40%; Vp = 0.46 мм/мин; b – 42%, 0.44 мм/мин; c – 80%, 0.52 мм/мин.
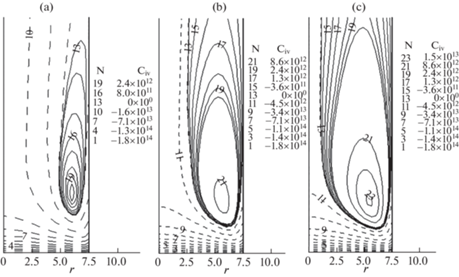
Рис. 5.
Кристалл процесса ТУ-6-18: a – профиль скорости вытягивания Vp [мм/мин]; b – расчетные изолинии Civ [см–3] после v‑i-рекомбинации; c – экспериментальная картина микродефектов (карта времени жизни, визуализирующая распределение микродефектов в слитке после декорирования медью и цикла оксидной преципитации). Масштаб длины слитка LS [%] соответствуют данным (b, c).
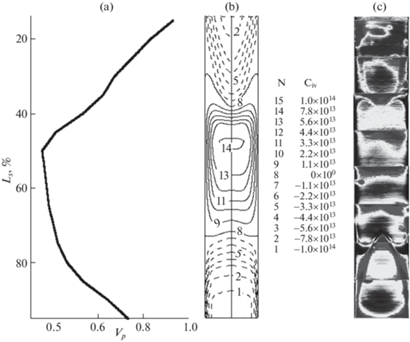
Рис. 6.
Осевые распределения микродефектов (на оси r = 0) для процесса ТУ-6-18-2: a – концентрация Nv [см–3] и радиус Rv [нм] пор, b – концентрация Np [см–3] и радиус Rp [нм] кислородных комплексов.
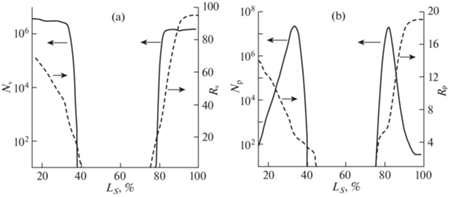
Рис. 7.
Кристалл процесса ТУ-6-20: a – профиль скорости вытягивания Vp [мм/мин], b – расчетные изолинии Civ [см–3] после v-i-рекомбинации, c – экспериментальная картина микродефектов (карта времени жизни: A, B – контрольные сечения распределений микродефектов).
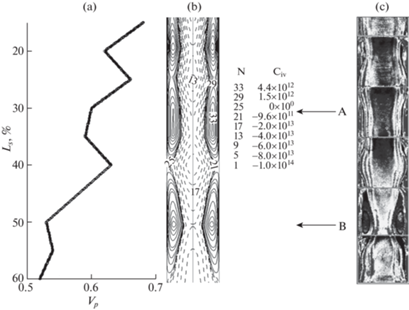
Уравнение для Civ(r, z, t) получается подстановкой в исходные уравнения:
Задаются значения энергетических порогов для равновесных концентраций и коэффициентов диффузии: Ev = 4.5 эВ, Ei = 4.6 эВ, EvD = 0.35 эВ, EiD = 0.20 эВ. С учетом экспериментального значения: D × Cim = 3 × 1011 см–1 ⋅ с–1 выбираются следующие значения коэффициентов диффузии при температуре кристаллизации: Dim = 6.23 × 10–4 см2/с, Dvm = 4.0 × 10–5 см2/с. По формуле: ${{C}_{{{\text{i}}m}}} = D{\text{/}}{{D}_{{{\text{i}}m}}} \times {{C}_{{{\text{i}}m}}}$ вычисляется величина Cim = 6.05 × × 1014 см–3, а далее с учетом критического значения критерия Воронкова: вычисляется величина Cvm = 8.48 × 1014 см–3. Далее проверка выполнения соотношения: Dvm ⋅ Cvm ≪ ≪ Dim ⋅ Cim показывает его выполнение.
4. Математическая модель образования микродефектов. По предложению В.В. Воронкова авторы статьи реализовали в виде компьютерной программы следующую математическую модель образования вакансионных микродефектов. Предполагается, что вакансия в решетке кремния является дефектом с четырьмя свободными связями, каждая пара из которых может акцептировать один кислородный атом. Эта реакция приводит к восстановлению Si–Si-связи, которая была занята кислородным атомом. При высокой температуре занятость каждой пары связей мала, в результате чего большинство вакансий свободно. При низких температурах занятость близка к 1, так что большинство вакансий существуют в виде vO2-комплексов, являющихся связанными вакансиями. При промежуточных температурах имеет место смешанная популяция свободных вакансий: двойных vO2- и одинарных vO-кислородных комплексов. Для упрощения вкладом одинарных комплексов пренебрегается. Это справедливо при условии, что энергия связи второго кислородного атома выше, чем первого.
Для определения свободной и связанной фракций вакансий удобно вначале рассмотреть равновесную концентрацию Cbe комплекса vO2, которая пропорциональна квадрату концентрации кислорода CO:
Если скорость образования vO2 определяется вакансионной диффузией, то равновесие достигается очень быстро. Тогда Сb/Cv = Cbe/Cve и температура Tb, при которой вакансии связываются, определяется из выражения: Cb = Cv (или Cbе = Cve).
С учетом того, что: Cve = Cvm ⋅ exp(– E/kT + E/kTm), получаем:
Температура Tb связана с ΔE уравнением:
В приближении стационарной скорости можно использовать классическую теорию зародышеобразования, согласно которой скорость образования пор есть:
σv = 930 эрг/см2 – поверхностная энергия кремния,
${{F}_{{\text{v}}}} = \frac{{16\sqrt {3~} {{\sigma }}_{{\text{v}}}^{3}}}{{{{{{\rho }}}^{2}}f_{{\text{v}}}^{2}}}$ – энергия барьера нуклеации,
${{f}_{{\text{v}}}} = kT\log \left( {\frac{{{{C}_{{\text{v}}}}}}{{{{C}_{{{\text{v}}e}}}}}} \right){\text{\;}}$ – движущая сила образования пор, причем множитель соответствует октаэдрической форме пор (для сферической формы он равен 16π/3),
σv относится к (111)‑направлению роста.
Соответственно для частиц имеем:
Здесь: σp = 790 эрг/см2, ρp/ρ = 2, γ = 0.5, Eo = 1.5 эВ, а CO задается из эксперимента или данных расчета конвективной диффузии в расплаве. Например, концентрация кислорода в объеме слитка задается постоянной: CO = 8.0 × 1017 см–3.
В любой момент времени концентрация пор и частиц может быть получена интегрированием:
Тогда для оценки радиуса поры применяется следующее уравнение:
Наконец, радиус поры, которая образовалась в момент времени t' и затем росла до момента t, равен:
Аналогично оценивается радиус оксидной частицы:
Модель образования кластеров межузельных атомов кремния аналогична образованию вакансионных пор при замене вакансионной диффузии к зародышу на диффузию межузельных атомов.
Для последующих оценок плотности кислородных преципитатов SiOx важной является доля оставшихся свободных вакансий, а также величина убыли концентрации кислорода. В результате образования вакансионных микродефектов уменьшается доля свободных вакансий, которые поглощаются порами и взаимодействуют с атомами кислорода, образуя комплексы vO2.
5. Тепловые истории выращивания монокристаллов кремния диаметром 150 мм: процессы ТУ-6-18 и ТУ-6-20. Название “тепловая история” используется для обозначения набора тепловых параметров, включающих значения осевого температурного градиента на ФК в центре (на оси) – Ga и на кромке выращиваемого монокристалла – Ge для дискретных моментов времени выращивания монокристалла. Этот набор параметров и соответствующие значения скорости вытягивания монокристалла являются исходными данными для моделей дефектообразования, которые позволяют адекватно учесть тепловые условия выращивания монокристалла кремния на конкретной тепловой МЧ-установке.
В тепловом узле (ТУ) для тигля диаметром 18 дюймов был проведен процесс ТУ-6-18 для выращивания кристаллов кремния диаметром ~6 дюймов (150 мм) в тепловом узле МЧ-установки EKZ 2700™. Теплоперенос рассчитывался для 10 последовательных стадий роста LS (от начала до конца цилиндрической части кристалла – 0–100% объема), причем на каждой стадии предполагалась его стационарность. Анализировалось продольное распределение осевого температурного градиента и его радиальная неоднородность на ФК. Помимо изменения геометрии в период роста учитывалось изменение Vp. Форма мениска и поверхности расплава задавались. Положение и форма ФК рассчитывались при заданном положении его кромки на боковой поверхности кристалла и автоматическом изменении мощности нагревателя. Уровень расплава по мере вытягивания кристалла соответственно уменьшался. На рис. 2 показано распределение изотерм в кристалле и других компонентах теплового узла на различных стадиях процесса роста в зависимости от % объема цилиндрической части выращенного слитка LS: а – 10, b – 50, c – 80%. Можно отметить, что G уменьшался от 35 K/см при 20% объема до 25 K/см при 100%, Vp уменьшалась от 0.9 до 0.35 мм/мин.
При переходе от 18- к 20-дюймовому тиглю для процесса ТУ-6-20 сделана существенная модификация расчетного макета: увеличение диаметра тигля до 20 дюймов, увеличение загрузочной массы расплава до 80 кг c последующим учетом изменения уровня расплава в тигле на промежуточных стадиях выращивания кристалла, а также модификация боковых экранов и нагревателя. Длина кристалла была увеличена со 120 до 160 см. Моделировались 11 ростовых стадий, соответствующих 0, 10, 20, …, 100% выращенного объема цилиндрической части монокристалла. Температурные поля в кристалле на промежуточных стадиях (5, 15, 25, …, 95) определялись интерполяцией. Максимальная длина цилиндрической части кристалла составляла 154 см при LS = = 100%.
Анализ распределений изотерм в тигельной части показывает, что при увеличении длины кристалла осевые градиенты несколько уменьшаются. На верхнем торце температура уменьшается от 980 (20%) до 640 (60%) и до 500 K (100%). В верхней части кристалла при его длине большей 95 см (на стадиях роста больших 60%) величина осевого градиента существенно уменьшается на последующих стадиях.
Процесс образования вакансионных микродефектов и межузельных кластеров рассматривается в диапазоне температур 1450–1250 K. Характерный диапазон температур для образования вакансионных комплексов 1293–1343 K.
По данным расчета теплового поля рассчитывались градиенты температуры в кристалле и по известной величине Vp оценивалась характерная скорость охлаждения слитка.
Для процессов выращивания слитков ТУ-6-18 и ТУ-6-20 профили осевых температурных градиентов Ga(T) и Ge(T) проанализированы в зависимости от температуры для 40%‑й стадии выращивания, а также представлены профили скорости вытягивания Vp (в % от LS). Из сравнения профилей Ga(T) и Ge(T) следует, что при высоких температурах (T > 1450 K) скорость охлаждения поверхности кристалла выше, чем в его центра. При T = 1450–1170 K наблюдается обратная ситуация, а при T < 1170 K обе эти величины одинаковые.
При T = 1400–1300 K градиент на оси выше, чем на поверхности кристалла. Например, Ge примерно равен 22 K/см, Ga изменяется от 33 до 27 K/см. Поэтому при Vp = = 0.61 мм/мин скорость охлаждения поверхности слитка равна 1.34 K/мин, а в его центре изменяется в диапазоне 2.01–1.64 K/мин. Изменения скорости вытягивания для слитков ТУ-6-18 и ТУ-6-20 различаются: в 1-м случае имеет место монотонное уменьшение Vp до стадии 50% и затем ее монотонное увеличение до конца процесса, а во 2-м Vp изменяется немонотонно через 5% длины слитка.
Для процессов ТУ-6-18 и ТУ-6-20 на рис. 3 показаны зависимости параметров тепловой истории выращивания слитка (Ga, Ge, ξa, ξe) от % объема цилиндрической части LS: a – кристалл ТУ-6-18, штрихпунктирная линия соответствует v-i-переходу при ξcrit = 0.136 мм2/K ⋅ мин; b – кристалл ТУ-6-20, штрихпунктирная линия соответствует “взвешенной” зависимости параметров ξa и ξe с коэффициентом 0.6. Максимальная длина кристалла ТУ-6-18 при 100%-й стадии – 155 см, кристалла ТУ-6-20 при 60%-й стадии – 96 см (соответственно, при 100%-й стадии – 160 см).
Значение ξcrit = 0.136 мм2/мин · К рассчитано с использованием усредненной по радиусу величине осевого температурного градиента на ФК. Это значение согласуется с упомянутым выше универсальным значением ξcrit = 0.13 мм2/мин · К.
Можно сказать, что зависимости изменения осевых температурных градиентов на ФК Ga и Ge для обоих кристаллов примерно одинаковые, хотя при более внимательном рассмотрении можно заметить разницу в их значениях, вносимую различием в режимах скоростей вытягивания. Эти зависимости характеризуются большими значениями градиентов на начальных стадиях роста (при 20%: Ga = 48 и Ge = 85 K/см) и их монотонным уменьшением к концу процесса до Ga = 35 и Ge = 48 K/см.
Для предварительной оценки распределений концентраций остаточных СТД после рекомбинации наибольшее значение имеют зависимости величин Vp/Ga и Vp/Ge от стадии роста. Величина критерия ξcrit выбирается на основе сравнения с экспериментальными картами времени жизни для конкретных кристаллов. Представление тепловой истории выращиваемого кристалла в аналитической форме позволяет запомнить и хранить температурные поля для всего процесса выращивания, что необходимо на этапах реализации нестационарной модели СТД-переноса и рекомбинации. Сущность этой методики состоит в представлении температурных распределений вдоль оси и кромки кристалла в виде полиномов 6–8-й степеней. Они рассчитываются по температурным полям в кристалле для каждой расчетной ростовой стадии.
Расчет концентрации микродефектов в кристаллах выполняется за три этапа. На первом рассчитываются тепловые поля в установке, необходимые для определения распределения температуры в монокристаллах кремния. На втором этапе рассчитываются остаточные концентрации СТД после v‑i-рекомбинации. Третий этап заключается в расчете концентрации и размеров микродефектов вакансионного типа (пор, оксидных частиц) и кластеров, образующихся в результате агломерации межузельных атомов кремния. При двумерной аппроксимации v‑i‑граница во всем объеме слитка получается непосредственно из решения задачи. Однако расположение этой границы вдоль слитка, получаемое расчетным путем, зависит от входных параметров математической модели и нуждается в экспериментальной апробации. С этой целью использованы карты времени жизни для слитков.
6. Результаты расчета СТД-распределений в процессе ТУ-6-18. Вначале для процесса выращивания монокристаллов кремния диаметром 150 мм из тигля диаметром 18 дюймов рассмотрим результаты расчета процесса v-i-рекомбинации [38]. На рис. 4 показаны картины распределения разности концентраций Civ в вакансионном (a), смешанном (b) и межузельном (c) ростовых режимах, возникающие в результате v-i-рекомбинации для различных стадий роста и скоростей выращивания кристалла из тигля в процессе ТУ-6-18: a – 40%; Vp = 0.46 мм/мин; b – 42%, Vp = 0.44 мм/мин; c – 80%, Vp = 0.52 мм/мин.
Результатом расчета на каждом временном шаге считается радиальное распределение концентрации Civ на достаточном удалении от ФК. В данном случае это удаление составляет 20 см. Полагается, что суммарная картина изолиний переменной Civ, построенная для всех временных шагов, соответствует ее двумерному распределению после v-i-рекомбинации. Анализ результатов показывает, что в начале выращивания кристалл находится в вакансионном режиме. Затем в связи с уменьшением Vp на участке 40–43% объема возникает и начинает расширяться межузельная область, которая существует до 70% объема и затем за счет увеличения Vp опять сменяется вакансионной.
На рис. 5 представлены результаты расчетов для сравнения с данными выращенного экспериментального кристалла ТУ-6-18: профиль скорости вытягивания (a), расчетные изолинии Civ после v-i-рекомбинации (b) и экспериментальная картина микродефектов (c), визуализированная по времени жизни электрических носителей заряда.
Сравнение показывает, что конфигурация переходов от вакансионной к межузельной моде по данным карты времени жизни соответствует аналогичным переходам на расчетной картине изолиний. Эти переходы вызваны значительным уменьшением Vp от начала процесса до 50%-й стадии и, соответственно, уменьшением параметра ξa до значений, меньших ξcrit, соответствующих переходу от вакансионного к межузельному ростовому режиму.
Вблизи оси вакансионная область исчезает и кристалл переходит в межузельный режим примерно при 44%-й стадии, который существует на некотором участке кристалла (на оси до 73%-й стадии), затем сменяется опять вакансионным режимом ввиду возрастания Vp к концу процесса. Относительно ростовой стадии, соответствующей минимальному значению Vp, картина изолиний является несимметричной ввиду разной скорости изменения Vp на участках уменьшения и увеличения: Vp уменьшается примерно в 2 раза быстрее, чем возрастает. Характерные значения разности концентраций Civ в начале и конце роста в вакансионной моде: – 7.8 × 1013 и – 1.0 × 1014 см–3. В центральной межузельной области максимальное значение равно 7.8 × 1013 см–3. Области с малой концентрацией (до 1.1 × 1013) наблюдаются в межузельной моде между изолиниями 8 и 9 на достаточно малых участках кристалла.
7. Результаты расчета распределения микродефектов в кристалле для процесса ТУ-6-18. Сравнение расчетных и экспериментальных данных показывает пространственное соответствие в расположении дефектов вакансионного и межузельного типа. Это подтверждает достаточность анализа поведения v‑i‑границы по двумерным СТД-распределениям, полученным в результате расчета v‑i‑рекомбинации.
Теория утверждает, что монокристалл кремния растет в вакансионном или межузельном режимах в зависимости от величины параметра В.В. Воронкова ξ по отношению к критическому значению. При ξcrit = 0.13 мм2/K ⋅ мин вакансионный режим соответствует ξ > ξcrit. Концентрация вакансий Cv увеличивается при увеличении ξ и уменьшается в радиальном направлении до нуля на v‑i‑границе. Концентрация и тип микродефектов, образующихся за счет агрегации вакансий при последующем охлаждении, сильно зависит от Cv. При больших значениях Cv преобладают микродефекты в виде пор, а при меньших Cv – в виде оксидных частиц, образующихся после агрегации вакансий и атомов кислорода. В результате вакансионная зона разделяется на главную внутреннюю часть, содержащую поры (которые идентифицируются как D‑дефекты), и краевую полосу, содержащую частицы. Эта полоса (P‑лента) локализована вдоль v‑i‑границы.
Для процесса ТУ-6-18 следует отметить, что при уменьшении скорости вытягивания концентрация вакансий снижается со значения Cv = 9.7 × 1013 см–3 в начальной части слитка до 0 при переходе к i‑моде (на стадии роста 40%). В интервале 40–77% возрастает концентрация межузельных атомов до значения Ci = 8.0 × 1013 см–3 (на стадии 50%) и затем с увеличением Vp ее значение снижается до 0 при переходе к v‑моде. На стадии 77% значение Cv возрастает до 1.1 × 1014 см-3.
Для процесса ТУ-6-18 [39] на рис. 6 приведены осевые распределения микродефектов на оси: концентрация Nv и радиус Rv пор (a), концентрация Np и радиус Rp кислородных комплексов (b). В начальной и конечной части слитка концентрация и радиус пор максимальные (Nv = 5 × 106 см–3, Rv = 95 нм), вблизи v‑i‑перехода значения Nv, Rv резко уменьшаются. Для типичных значений Cv поры являются доминирующим типом микродефектов при значениях Nv = 3 × 106 см–3, Rv = 55 нм. Соответственно, в начале и конце слитка концентрация оксидных частиц мала (Np = 100–50 см–3) при радиусе, равном 15–19 нм. Однако вблизи v‑i‑границы их концентрация резко возрастает до значения 4 × 107 см–3, а радиус уменьшается до 4–5 нм. Типичные значения Np и Rp равны 3 × 108 см–3и 5 нм соответственно.
8. Результаты расчета СТД-распределений в кристалле процесса ТУ-6-20. В отличие от процесса ТУ-6-18, в данном случае колебания Vp были не такими значительными. Колебательное понижение Vp во время процесса происходило таким образом, что значения критерия ξ колебались около их средней величины, равной 0.13 мм2/K · мин, которую можно принять за ξcrit. Экспериментальные кристаллы были продольно разрезаны и распределения дефектов визуализированы посредством декорирования медью и карт времени жизни после цикла оксидной преципитации.
Для процесса ТУ-6-20 расчетные (b) и экспериментальные (c) результаты показаны на рис. 7: a – профиль скорости вытягивания, b – расчетные изолинии Civ после v-i-рекомбинации, c – экспериментальная картина микродефектов (карта времени жизни: A, B – контрольные сечения распределений микродефектов).
В этом случае также можно сказать, что конфигурация переходов от v- к i-режиму по данным карты времени жизни (c) соответствует аналогичным переходам на расчетной картине изолиний (b). Более того, эти переходы отчетливо соответствуют расположению по длине кристалла колебательных минимумов и максимумов Vp. Радиальные и осевые размеры областей переходов от v- к i-моде также достаточно точно воспроизводятся на расчетной картине изолиний. Кроме этого, можно отметить особенность в распределении СТД, обусловленную ростом кристалла при колебаниях параметра ξ вблизи ξcrit. Она связана с тем, что вблизи боковой поверхности кристалла возникают области с малой СТД-концентрацией. Например, на вакансионных участках кристалла между изолиниями 21–25 концентрация не превышает 9.6 × 1011 см–3, а в межузельных областях ее величины равны 1.5 × 1012 и 4.4 × 1012 см–3 для изолиний 29 и 33 соответственно.
Дополнительно расчетный макет был рассмотрен для ростовых стадий более 60% объема слитка (при длинах слитка более 100 см). Соответствующие ему тепловые параметры приведены на рис. 3,b в виде распределений осевых температурных градиентов Ga и Ge и соответствующих им критериев ξа и ξе в центре и на кромке ФК в зависимости от % объема выращиваемого слитка LS. Значения Vp берутся по данным процесса выращивания, значения Ga и Ge рассчитываются для каждой стадии роста (всего их 19). Отношение градиентов на крае и в центре достаточно большое (Ge/Ga = 1.78). В начале выращивания значения Ga, Ge существенно больше по сравнению с концом процесса и градиенты монотонно уменьшаются по мере роста объема слитка. Изменение Vp не монотонное, это определяет немонотонность критериев ξа и ξе. Можно заметить, что критерий Воронкова предсказывает при ξа > ξcrit = 0.13 мм2/K · мин вакансионный, а при ξе < 0.085 мм2/K ⋅ мин – межузельный режим выращивания слитка. Поэтому в выборе ξcrit есть некоторый произвол и при сравнении с экспериментальными данными значение ξcrit обычно корректируется в сторону увеличения. Например, чтобы удовлетворить экспериментальным данным можно выбрать некоторое “взвешенное” значение ξcrit с коэффициентом 0.6: ξcrit = 0.6 ⋅ (ξa + ξe) и его распределение будет достаточно хорошо описывать поведение v-i границы по длине слитка.
9. Результаты расчета распределений микродефектов в кристалле для процесса ТУ-6-20. Согласно расчетным и экспериментальным данным на рис. 7,b,c видно, что слиток имеет центральную вакансионную и периферийную межузельную области. Положение v‑i‑границы вдоль слитка (отвечающее сужению и расширению вакансионного центра) соответствует немонотонному профилю скорости вытягивания. Сравнение этих карт также показывает пространственное соответствие в расположении дефектов v- и i-типа.
На рис. 8 показаны радиальные распределения микродефектов для 30 и 50% стадий и CO = 8.0 × 1017 см–3: a – концентрация Np и радиус Rp кислородных комплексов, b – концентрация Ns и радиус Rs межузельных кластеров (30% – сплошная и 50% – пунктир, без меток – концентрация, с метками – радиус). Максимальная концентрация пор для 30%-й стадии достигает величины Nv = 8 × 106 см–3, а их радиус – Rv = 23 нм в центральной области слитка радиусом 3 см. Максимальная концентрация оксидных частиц для 30%-й стадии достигает Np = 107 см–3, радиус – Rp = 4.2 нм в пределах центрального кольца радиусом 4 см (b). На стадии 50% максимальная концентрация оксидных частиц существенно меньше (Np = 103 см–3) при радиусе Rp = 4 нм в пределах более узкого центрального кольца радиусом 2.2 см. Межузельные кластеры расположены вблизи боковой поверхности слитка и значения их максимальной концентрации при стадиях 30 и 50% меняются незначительно (Ns = 8 × 104 см–3 и немного меньше для стадии 50%), а радиусы Rs составляют 54 и 67 нм соответственно.
Рис. 8.
Радиальные распределения микродефектов для 30- и 50%-x ростовых стадий кристалла в процессе ТУ-6-20 при постоянном объемном распределении концентрации кислорода (CO = 8.0 × 1017 см–3): a – концентрация Np [см–3] и радиус Rp [нм] кислородных комплексов, b – концентрация Ns [см–3] и радиус Rs [нм] межузельных кластеров (30% – сплошная и 50% – пунктир, без меток – концентрация, с метками – радиус)).
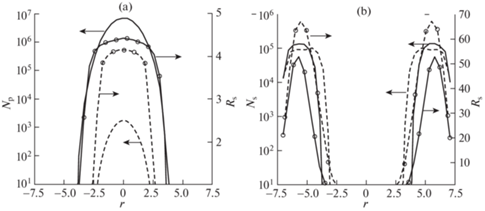
Согласно модели вакансионной агломерации, концентрация кислорода является основным параметром, влияющим на агломерацию оксидных комплексов vO2. Исследованию переноса кислорода в расплаве и определению его значений на ФК посвящено много работ. Считается важным снижение концентрации кислорода в кристалле до уровня (8–2) × 1017 см–3.
10. Процесс быстрой температурной обработки пластин кремния. Актуальными являются вопросы математического моделирования термонапряженного состояния и дефектообразования в пластинах кремния, вырезаемых из выращенных монокристаллических слитков [40, 41]. Для процесса быстрой температурной обработки (БТО) применяется специальное термическое оборудование и подбираются оптимальные условия проведения процесса термообработки. Важную роль играют способы крепления пластин кремния большого диаметра (150, 200 мм и более). В [42] сравниваются экономические параметры при производстве пластин кремния диаметром от 100 до 400 мм. Дан обзор различных методов термообработки пластин кремния и обсуждаются особенности напряженного состояния в пластинах большого диаметра (200 и 300 мм). В [43] предложена математическая модель для описания термонапряженного состояния Si-пластин большого диаметра (200 и 300 мм) в резистивной печи для термического отжига. В печи устанавливается вертикальная кассета пластин таким образом, что каждая из пластин поддерживается на 4-игольчатых опорах. Кроме термонапряжений в радиально-неоднородном тепловом поле, сильное влияние оказывают напряжения, вызванные гравитационной силой, распределение которых в пластине зависит от позиционирования опор.
В [44] пластины кремния, выращенные в направлении (001), были подвергнуты предварительной термообработке (при 650°С – 16 часов несколько раз и при 1000°С – от 1 до 16 часов), затем отжиг был произведен при 585°С на 3-х опорах несколько раз от 1 до 35 мин. Обнаружено образование дислокационных петель вблизи опор в разных плоскостях скольжения. Измерением сдвиговых напряжений установлена их минимальная (критическая) величина, необходимая для образования одной отдельной дислокационной петли. Показаны картины дефектов для трех пластин, каждая из которых была выдержана при 1000°С разное время (1, 4 и 16 часов). Приведены зависимости критического сдвигового напряжения от времени термообработки для дефектов разного размера (<50, 100 и 250–500 нм). Рассмотрена полуаналитическая модель для интерпретации экспериментальных результатов.
Однако для пластин большого диаметра (200 и 300 мм) возникают существенные трудности в обеспечении малых перепадов температуры по их площади при термообработке. Считается, что процесс термической обработки пластин лучше осуществлять в установках не с резистивным нагревом, а с галогенными лампами накаливания (БТО-процесс). С помощью таких ламп нагрев осуществляется быстро, при этом пластины располагаются горизонтально на трех- или четырехигольчатых опорах. Схема БТО-процесса с креплением пластины кремния на 3-игольчатых опорах представлена на рис. 9,а, где показаны галогенные лампы нагрева 1 и 3, пластина 2, лежащая на 3‑игольчатых опорах 4, которые являются причиной напряжений в их окрестности (см. изолинии на пластине). Временные режимы БТО-процесса с различной выдержкой при максимальной температуре показаны на рис. 9,b, где сплошная линия соответствует меньшей (15 с), а пунктирная – большей (35 с) выдержке.
Рис. 9.
Процесс БТО: a – схема процесса: галогенные лампы нагрева 1, 3 пластины кремния 2, лежащей на 3-игольчатых опорах 4, которые являются причиной напряжений в их окрестности (см. изолинии на пластине); b – временные режимы с различной выдержкой t [с] при максимальной температуре Tmax [°C] (сплошная линия – t = 15 с, пунктирная – 35 с).
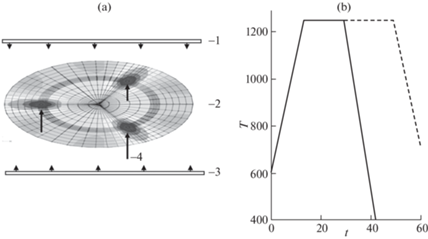
Применение БТО-процесса позволяет эффективно воздействовать на распределение плотности кислородных преципитатов по толщине пластины путем управления распределениями вакансий и межузельных атомов. В частности, управление диффузией вакансий позволяет создавать MDZ-зону (“Magic Denuded Zone”), обедненную кислородными преципитатами глубиной до 100 мк. Механизм такого воздействия объясняется корреляцией между плотностью кислородных преципитатов и концентрацией вакансий Cv, так как кислородный преципитат имеет больший размер по сравнению с атомом кремния и его образование сопровождается абсорбцией вакансий на кислородных зародышах. При Cv > Cve свободная энергия такого процесса увеличивается, а при Cv < Cve уменьшается или подавляется в соответствии с зависимостью: γkTln(Cv/Cve), где Cve – растворимость вакансий при температуре T, γ = 0.5 – количество вакансий, абсорбированных на кислородном атоме, связывающем зародыш.
В данной работе для БТО-процесса рассмотрены нестационарные процессы диффузии и рекомбинации СТД в пластинах кремния при быстром их нагреве от 600 до 1250°С (в течение 13 с), кратковременной выдержке при 1250°С (в течение 15 или 35 с), а затем быстром охлаждении до 600°С (за 13 с). Расчет осуществляется по рассмотренной выше двумерной модели вакансионно-межузельной кинетики в пластине кремния диаметром 150 мм и толщиной 0.67 мм, при этом задаются начальные концентрации дефектов в соответствии с данными предварительного расчета остаточных концентраций Cv и Ci в выращенном слитке. Исходные параметры: радиус пластины R = = 7.5 см, толщина H = 0.67 мм. Распределение концентраций остаточных межузельных атомов и вакансий полагается равномерным по толщине пластины. На границах расчетной области задаются равновесные условия для концентраций: Cv = Cve, Ci = Cie. Параметры приведены в таблице 1. Начальные концентрации вакансий и межузельных атомов взяты по расчетным данным для сечения A слитка ТУ-6-20, в котором реализуется смешанный v-i-режим c OSF-кольцом. Максимальные концентрации вакансий и межузельных атомов в этом сечении пластины были следующими: Cvres = 6.8 × × 1012 см–3, Cires = 1.2 × 1011 см–3. Концентрации вторичных фракций в этих областях были существенно меньше, чем основных.
Результаты расчетов для БТО-процесса представлены на рис. 10 для временных режимов с различной выдержкой (35 с – сплошные линии и 15 с – пунктиры при максимальной температуре Tmax = 1250°C): (a) профили Cv и Ci от толщины пластины; (b) расчетные вакансионные профили от толщины пластины и экспериментальные данные [45] (черные треугольники – с выдержкой 35 с при Tmax = 1250°C). В результате БТО-процесса происходит выравнивание концентраций Cv и Ci в объеме и понижение их максимальных значений: Cvmax = 2.72 × 1012 см–3, Cimax = 1.46 × 108 см–3 (рис. 10,a), причем увеличение времени выдержки при температуре 1250°C приводит к некоторому снижению концентраций СТД (рис. 10,b).
Рис. 10.
Высокотемпературная обработка пластин кремния: a – профили Cv, Ci [см–3] по толщине пластины z [мм] (сплошные линии – 35 с, пунктиры – 15 с); b – сравнение с экспериментальными данными: расчетные вакансионные профили Cv [см–3] по толщине пластины (пунктир – 15 с, сплошная линия – 35 с при Tmax = 1250°C) и экспериментальные данные (черные треугольники – t = 35 с при Tmax = 1250°C).
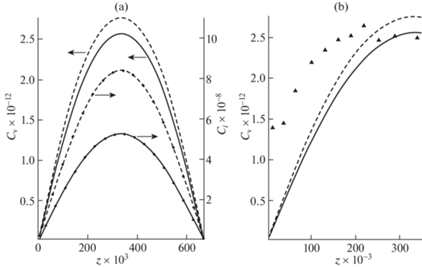
Экспериментальная концентрация вакансий Cv была получена в результате измерения плотности кислородных преципитатов NO и установлению ее корреляции с Cv в виде: NO = 1.28 × 10–36 ⋅ $C_{{\text{v}}}^{{3.71}}$, который после инверсии был получен в более удобном для анализа виде: Cv = 8.09 × 109 ⋅ $N_{{\text{O}}}^{{0.241}}$. Таком образом, после подстановки измеренных значений NO был рассчитан экспериментальный вакансионный профиль Cv по толщине пластины. Сравнение расчетных и экспериментальных данных на рис. 10,b показывает, что имеется некоторое завышение экспериментальных значений Cv(z). Это объясняется тем, что при измерениях NO возникают погрешности в определении Cv из-за атомов платины, введение которых обусловлено условиями эксперимента, но которые индуцируют побочный выталкивающий эффект, в зоне их наибольшей концентрации вблизи поверхностей пластины.
Заключение. Успешное решение рассмотренной проблемы дефектоообразования в бездислокационном монокристаллическом кремнии было обусловлено сочетанием правильного выбора физической модели “быстрой” СТД-рекомбинации, предложенной В.В. Воронковым для одномерного случая с возможностями ее применения в двумерном случае, который был сопряжен с термомеханической моделью. В отличие от физических моделей СТД-взаимодействия других авторов, данный подход стал определяющим в мире и был подтвержден целым рядом технологических экспериментов.
Представленные в статье данные получены в результате многолетнего сотрудничества авторов статьи c основоположником этого научного направления – д.ф.-м.н. В.В. Воронковым. Представленное комплексное термомеханическое исследование проводилось в кооперации с ведущими отечественными и зарубежными технологическими организациями (ГИРЕДМЕТ, ЭЛМА, MEMC Inc.). Разработка и применение сопряженных тепловых моделей МЧ-выращивания монокристаллов кремния и БТО-процесса для вырезаемых из них пластин позволило рассчитать основные тепловые характеристики в монокристаллах и пластинах бездислокационного кремния и затем их применить в моделях дефектообразования, адекватность которых продемонстрирована сравнениями с данными технологических экспериментов.
Благодарность. Авторы благодарят Лауреата международной премии им. Франка в области роста кристаллов, д.ф.-м.н. В.В. Воронкова за многолетнее научное сотрудничество и полезные обсуждения представленных в статье результатов. Представленная работа поддержана темой государственного задания ИПМех РАН (№ АААА-А20-120011690136-2).
Список литературы
Мильвидский М.Г., Освенский В.Б. Структурные дефекты в монокристаллах полупроводников. М.: Металлургия, 1984. 256 с.
Voronkov V.V. The mechanism of swirl defects formation in silicon // J. Crystal Growth. 1982. V. 59. P. 625–643. https://doi.org/10.1016/0022-0248(82)90386-4
Mori T., Wang Z., Brown R. Transient simulation of grown-in defect dynamics in Czochralski crystal growth of silicon // Electrochem. Soc. Proc. 2000. V. 17. P. 118–127.
Voronkov V.V., Falster R. Grown-in microdefects, residual vacancies and oxygen precipitation bands in Czochralski silicon // J. Crystal Growth. 1999. V. 204. № 4. P. 462–474. https://doi.org/10.1016/S0022-0248(99)00202-X
Бабич В.М., Блецкан Н.И., Венгер Е.Ф. Кислород в монокристаллах кремния. Киев: ИНТЕРПРЕС ЛТД, 1997. 223 с.
Voronkov V.V. Formation of voids and oxide particles in silicon crystals // Mater. Sci. Eng. 2000. V. B73. P. 69–76. https://doi.org/10.1016/S0921-5107(99)00436-5
Lin W. Oxygen segregation and microscopic inhomogeneity in Cz silicon // Proc. 2nd Int. Symp. on Advanced Science and Technology of Silicon Materials. Kona-Hawaii, USA, 1996. P. 288–293.
Bracht H. Native point defects in silicon // Electrochem. Soc. Proc. 1997. V. 22. P. 357–371.
Litvinov Yu. M., Makarov A.S., Petrov S.V. et al. Oxidation test application for chemical-mechanical polished (CMP) silicon wafers quality control // Proc. of 4th Int. Conf. ICSC. Obninsk: IphPE, 2001. P. 605–612.
Федина Л.И., Дрофа А.Т., Ободников В.И. и др. Анализ ростовых микродефектов в кристаллах FZ-Si, выращенных в условиях вакансионного пересыщения // Совещ. по росту кристаллов, пленок и дефектам структуры кремния (Кремний-2002). Новосибирск: ИФП СО РАН, 2002. С. 16.
Эйдензон А.М. Условия возникновения дислокаций в первоначально бездислокационных монокристаллах кремния, выращенных из расплава // Изв. АН СССР. Сер. Физическая. 1980. Т. 44. № 2. С. 312–319.
Wijaranakula W. A real-time simulation of point defect reactions near the solid and melt interface of a 200 mm diameter Czochralski silicon crystal // J. Electrochem. Soc. 1993. V. 140. № 11. P. 3306–3315. https://doi.org/10.1149/1.2221028
Togawa S., Nishi Y., Kobayashi M. Estimation of radial resistivity profile of FZ-Si crystals by numerical simulation // Electrochem. Soc. Proc. 1998. V. 98 (13). P. 67–79.
Ratnieks G., Muiznieks A., Buligins L. et al. Influence of the three dimensionality of the HF electromagnetic field on resistivity variations in Si single crystals during FZ growth // J. Crystal Growth. 2000. V. 216. P. 204–219. https://doi.org/10.1016/S0022-0248(00)00354-7
Larsen T.L., Jensen L., Ludge A. et al. Numerical simulation of point defect transport in floating-zone silicon single crystal growth // J. Crystal Growth. 2001. V. 230. P. 300–304. https://doi.org/10.1016/S0022-0248(01)01320-3
Ciszek T.F., Wang T.H. Silicon defect and impurity studies using float-zone crystal growth as tool // J. Crystal Growth. 2002. V. 237–239. P. 1685–1691. https://doi.org/10.1016/S0022-0248(01)02325-9
Sinno T., Brown R.A., Ammon W.A. et al. Point defect dynamics and the oxidation-induced stacking – fault ring in Czochralski-grown silicon crystals // J. Electrochem. Soc. 1998. V. 145. № 1. P. 302–318. https://doi.org/10.1149/1.1838251
Wang Z., Brown R.A. Simulation of almost defect-free silicon crystal growth // J. Crystal Growth. 2001. V. 231. P. 442–447. https://doi.org/10.1016/S0022-0248(01)01433-6
Nakamura K., Saishoji T., Tomioka J. Diffusion model of point defects in silicon crystals during melt-growth // Electrochem. Soc. Proc. 1998. V. 13. P. 41–53.
Nakamura K., Saishoij T., Tomioka J. Grown-in defects in silicon crystals // J. Crystal Growth. 2002. V. 237–239. P. 1678–1684. https://doi.org/10.1016/S0022-0248(01)02323-5
Sinno T., Jiang Z.K., Brown R.A. Atomistic simulation of point defects in silicon at high temperature // Appl. Phys. Lett. 1996. V. 68. № 21. P. 3026–3030.
Talanin V.I., Talanin I.E., Levinson D.I. Physics of the formation of microdefects in dislocation-free monocrystals of float-zone silicon // Semicond. Sci. Technol. 2002. V. 17. P. 104–113.
Sinno T. Thermophysical properties of intrinsic point defect crystalline silicon // Electrochem. Soc. Proc. 2002. V. 2. № 1. P. 212–226.
Hourai M., Kely G.P.,Tanaka T. et al. Control of grown-in defects in Czochralski silicon crystals // Electrochem. Soc. Proc. 1997. V. 22. P. 372–385.
Furuya H., Harada K., Park J.G. CZ single-crystal silicon without grown-in defects // Solid State Technology. 2000. V. 11. P. 525–528.
Kitamura K., Furukawa J., Nakada Y. et al. Radial distribution of temperature gradients in growing CZ-Si crystals and its application to the prediction of microdefect distribution // J. Crystal Growth. 2002. V. 242. P. 293–301.
Abe T. Thermal gradients measured by thermocouples near growth interfaces in CZ-silicon crystals // Electrochem. Soc. Proc. 1999. V. 99 (1). P. 414–424.
Abe T. The formation mechanism of grown-in defects in CZ silicon crystals based on thermal gradients measured by thermocouples near growth interfaces // Silicon-99, Japan. 1999. P. 55–69.
Nakabayashi Y., Osman H.I., Toyonaga K. et al. Fractional contribution in Si self-diffusion: dopant concentration and temperature dependence on Si self-diffusion mechanism // Electrochem. Soc. Proc. 2002. V. 2. № 1. P. 241–247.
Inoue N., Tanahashi K., Kikuchi M. Point defect behavior in a growing silicon crystal // Proc. 3rd Symp. on Atomic-Scale Surface and Interface Dynamics. Japan: Fukuoka, 1999. P. 215–219.
Nakai K., Inoue Y., Yokota H. et al. Formation of grown-in defects in nitrogen doped Cz-Si crystals // Proc. 3rd Int. Symp. on Advanced Science and Technology of Silicon Materials. 2000. P. 88–95.
Akatsuka M., Okui M., Umeno S., Sucoka K. Calculation of size distribution of void defect in Czochralski silicon // Electrochem. Soc. Proc. 2002. V. 2. № 1. P. 517–527.
Sucoka K., Akatsuka M., Okui M., Kata H. Computer simulation for morfology, size and dependence of oxide precipitates in Czochralski silicon // Electrochem. Soc. Proc. 2002. V. 2. № 1. P. 540–553.
Okui M., Nishimoto M. Effect of the axial temperature gradient on the formation of grown-in defect regions in Czochralski silicon crystals; reversion of the defect regions between the inside and outside of the Ring-OSF // J. Crystal Growth. 2002. V. 237–239. P. 1651–1656.
Yang D., Chu J., Ma X. et al. Oxidation-induced stacking faults in nitrogen doped Czochralski silicon // Electrochem. Soc. Proc. 2002. V. 2. № 1. P. 273–279.
Верезуб Н.А., Простомолотов А.И. Механика процессов выращивания и термообработки монокристаллического кремния // Изв. РАН. МТТ. 2020. № 5. С. 51–63. https://doi.org/10.31857/S0572329920040157
Верезуб Н.А., Воронков В.В., Мильвидский М.Г., Простомолотов А.И. Взаимодействие собственных точечных дефектов при выращивании монокристаллов кремния методом Чох-ральского // Поверхность. Рентгеновские, синхронные и нейтронные исследования. 2001. № 10. С. 15–20.
Verezub N.A., Prostomolotov A.I., Mezhennyi M.V., Mil’vidskii M.G., Reznik V.Ya. Theoretical and experimental study of the formation of grown-in and as-grown microdefects in dislocation-free silicon single crystals grown by Czochralski method //Crystallography reports. 2005. V. 50. Suppl. 1. P. S159–S167.
Prostomolotov A.I., Verezub N.A. Integrated approach for modeling of heat transfer and microdefect formation during CZ silicon single crystal growth // Solid State Phenomena. 2007. V. 131–133. P. 283–288.
Prostomolotov A., Verezub N., Mezhennyi M., Resnik V. Thermal optimization of CZ bulk growth and wafer annealing for crystalline dislocation-free silicon // J. Crystal Growth. 2011. V. 318. P. 187–192. https://doi.org/10.1016/j.jcrysgro.2010.11.080
Vasiliev Yu.B., Verezub N.A., Mezhenniy M.V., Prosolovitch V.S., Prostomolotov A.I., Reznik V.Ya. Peculiarities of a defect generation during a heat treatment of large diameter dislocation–free silicon wafers with specified distribution of oxygen–containing gettering centres // Russian Microelectronics. 2013. V. 42. № 8. P. 467–476.
Huff H.R., Goodall R.K. Silicon wafer thermal processing: 300 mm // Proc. 2nd Int. Symp. on Advanced Science and Technology of Silicon Materials. USA: Kona-Hawaii, 1996. P. 322–343.
Fischer A., Richter H., Kumer W., Kucher P. Slip-free processing of 300 mm silicon batch wafers // J. Appl. Phys. 2000. V. 87. № 3. P. 1543–1549. https://doi.org/10.1063/1.372047
Giannattasio A., Senkader S., Falster R.J., Wilshaw P.W. The generation of slip in CZ-silicon // Int. Conf. on Extended Defects in Semiconductors. Abstracts. Italy: Bologna, 2002. P. 23.
Falster R. Intrinsic point defects and reactions in silicon. Advances in defect engineering // First Int. School on Crystal Growth Technology (ISCGT-1): Book of lecture notes. Switzerland: Beatenberg, 1998. P. 258–274.
Дополнительные материалы отсутствуют.
Инструменты
Известия РАН. Механика твердого тела