Мембраны и мембранные технологии, 2023, T. 13, № 2, стр. 83-95
Паровая конверсия этана и его смесей с метаном в мембранном реакторе с фольгой из Pd–Ru сплава
Л. П. Диденко a, *, В. Н. Бабак a, Л. А. Семенцова a, Т. В. Дорофеева a, П. Е. Чижов a, С. В. Горбунов b
a Институт проблем химической физики РАН
Черноголовка, Россия
b Институт металлургии и материаловедения им. А.А. Байкова РАН
Москва, Россия
* E-mail: ludi@icp.ac.ru
Поступила в редакцию 12.08.2022
После доработки 13.11.2022
Принята к публикации 07.12.2022
- EDN: HYVKWL
- DOI: 10.31857/S2218117223020037
Аннотация
Исследованы закономерности паровой конверсии этана и метан-этановых смесей, содержащих 5, 10 и 15% этана, в реакторе с мембраной в виде фольги толщиной 30 мкм из сплава Pd–6% Ru и никелевым катализатором марки НИАП-03-01. Реакцию изучали при следующих условиях: температуры 773 и 823 К, объемные скорости сырья 1800 и 3600 ч–1, соотношения пар/сырье 3 и 5. Паровую конверсию этана исследовали в температурном интервале 773–853 К. Сравнительные эксперименты в традиционном реакторе показали, что в мембранном реакторе увеличивается превращение сырья по реакции паровой конверсии с образованием Н2 и СО2 и снижается его гидрокрекинг. Вакуумирование пермеата приводит к возрастанию выхода Н2 и СО2. При снижении соотношения пар/сырье от 5 до 3 увеличивается гидрокрекинг сырья и скорость образования углеродных отложений. Оптимальными условиями паровой конверсии метан-этановых смесей являются Т = 773 К (этана – температурный интервал 773–853 К), 1800 ч–1 и пар/сырье 5. Установленные закономерности сходны с полученными ранее для других видов сырья (смесей метана с пропаном, пропана, н-бутана, смеси, моделирующей средний состав попутного нефтяного газа) в данном мембранном реакторе.
1. ВВЕДЕНИЕ
Водородная энергетика является перспективной и быстро развивающейся отраслью энергетики, основанной на использовании экологически чистого энергоносителя – водорода [1]. В связи с этим потребность в водороде постоянно возрастает. Важным практическим применением водорода является использование в топливных элементах. Для низкотемпературных топливных элементов с полимерными протонообменными мембранами, где концентрация СО не должна превышать 10 ppm, требуется водород высокой чистоты (99.999 об. %). В настоящее время около 48% Н2 получается паровой конверсией природного газа [2]. Паровую конверсию метана проводят при температурах более 973 К, поскольку выход продуктов ограничен термодинамическим равновесием. Природный газ, помимо метана, содержит 3–7 об. % С2+ углеводородов. При высоких температурах из С2+ углеводородов с высокой скоростью образуются углеродные отложения (УО), дезактивирующие катализатор. Чтобы этого избежать, С2+ алканы необходимо удалять из природного газа. С этой целью в промышленном процессе паровой конверсии природного газа проводят стадию предриформинга при температурах 673–773 К, в которой в результате паровой конверсии гомологов метана на никелевых катализаторах образуется смесь метана, водорода и оксидов углерода. Необходимость использования стадии предриформинга приводит к увеличению капитало- и энергозатрат процесса.
Мембранная технология, в которой объединены реакционный процесс и отвод Н2 через мембрану, не требует использования стадии предриформинга. Отвод водорода из реакционной смеси через мембрану приводит к смещению равновесия протекающих в смеси реакций, в результате чего можно достичь высокой конверсии сырья при более низких температурах. В мембранном процессе не требуются дополнительные стадии доокисления СО по реакции водяного газа и очистки получаемого Н2, что позволяет снизить капитало- и энергоемкость паровой конверсии. Идея каталитического мембранного процесса сформулирована академиком В.М. Грязновым и реализована в последующих работах [3–6]. В обзорах [7, 8] представлен накопленный в настоящее время большой экспериментальный и теоретический материал, касающийся свойств водородселективных мембран из палладиевых сплавов, конструкций мембранных реакторов и их использования для получения водорода из углеводородного сырья. Эффективное использование мембранного реактора для получения Н2 из природного газа, содержащего, помимо СН4, около 10% С2Н6, 5% С3Н8 и 2% С4Н10, паровой конверсией при относительно невысоких температурах (673–823 К) описано в [9, 10]. Показано, что в мембранном реакторе с композиционной Pd–Au мембраной и Ni катализатором в оптимальных условиях конверсия сырья составляет 80%, степень извлечения Н2 более 80% и не наблюдается образования УО. В работе [11] предложен мембранный риформер паровой конверсии сетевого природного газа, содержащего 88.5% СН4, 4.6% С2Н6, 5.4% С3Н8 и 1.5% С4Н10. Производительность риформера составляет 40 нм3/ч Н2 (99.99%) и он стабильно работает в течение 3000 ч. В мембранном реакторе с композитной палладиевой мембраной на подложке из пористой нержавеющей стали и промышленным катализатором Ru/Al2O3 конверсия метана при 823 К и трансмембранном давлении 912 кПа составила 82%, а производительность по водороду при объемной скорости сырья 2000 ч–1 составила 0.18 нм3/ч [12]. Хотя природный газ содержит преимущественно метан, его состав может меняться в зависимости от месторождения. Кроме того, существует такое сырье, как попутные газы нефтяных и газонефтяных месторождений с более высоким содержанием С2+ алканов. Это ценное сырье используется недостаточно эффективно и частично сжигается в факелах, что наносит ущерб окружающей среде. Ранее мы показали, что в мембранном реакторе с Pd–Ru мембраной и промышленным никелевым катализатором возможно получать водород паровой конверсией смеси, моделирующей усредненный состав попутных нефтяных газов [13]. Поскольку скорость образования УО возрастает с увеличением количества атомов углерода в алкане, контролировать протекание этой побочной реакции проще, используя в качестве сырья углеводородные смеси более узкого состава, например, метан-этановые. На большинстве газоперерабатывающих заводов с целью более рационального использования сырья попутный нефтяной газ разделяют на газовый бензин, пропан-бутан и сухой газ. Сухой газ представляет собой смесь метана с этаном. Его используют как в качестве топлива, так и для получения ацетилена, водорода и т.д. В данной работе исследована паровая конверсия метан-этановых смесей в мембранном реакторе с целью получения водорода высокой чистоты. Кроме того, в качестве сырья исследован 100%-ный этан. Это ценное химическое сырье, наряду с пропаном и бутаном, извлекается из попутного и нефтяных газов. В настоящее время его используют преимущественно для получения этилена, являющегося одним из самых востребованных органических соединений. Основной областью использования этилена является производство полиэтиленов высокого и низкого давления и других полимерных материалов. Производство указанных материалов имеет высокий экономический эффект, поскольку стоимость конечного товара, например, полиэтиленовых труб, в десятки раз выше, чем этана. В литературе представлено большое количество исследований, имеющих целью разработку новых катализаторов и улучшение показателей реакции. Большое количество работ посвящено изучению окислительного дегидрирования этана, которое термодинамически более предпочтительно и протекает при более низких температурах. Вместе с тем, этан может быть использован и как сырье для паровой конверсии с получением водорода. Из одного моля этана можно получить 7 молей Н2, в то время как из метана только 4 моля. Паровая конверсия этана исследована мало. В основном описаны различные катализаторы паровой конверсия смесей, содержащих, наряду с этаном, метан и более высокие гомологи. Поскольку при паровой конверсии таких смесей наблюдается высокая скорость образования УО, большое внимание исследователей уделено поиску устойчивых к дезактивации катализаторов. В работе [14] исследовано влияние присутствующих в природном газе С2, С3 алканов на образование УО в реакции паровой конверсии на Ni- и Rh-катализаторах, нанесенных на смешанный оксид церия-циркония, легированный лантаном. Оба катализатора показали высокую устойчивость к образованию УО, особенно катализатор Rh/La/CeO2–ZrO2. Авторы [15] показали, что СеО2 может быть использован и в качестве катализатора. Исследование паровой конверсии этана при температурах 1073–1171 К показало, что введение в цериевый катализатор 0.15% Gd увеличивает его активность в основой реакции и снижает образование УО. Несмотря на наличие более активных и устойчивых к образованию УО катализаторов, в промышленном процессе используется нанесенный Ni катализатор, поскольку он доступен и имеет низкую цену. Поэтому важное значение имеют исследования, направленные на улучшение свойств никелевых катализаторов. В работе [16] показано, что высокую каталитическую активность и устойчивость к образованию УО обеспечивает высокая дисперсность Ni на носителе. Для сохранения дисперсности, то есть предотвращения спекания Ni на носителе, в катализатор необходимо вводить небольшие количества Pt, Pd или Ru.
В мембранном реакторе паровая конверсия этана практически не исследована. Можно сослаться на работу [17], где на основании теоретического описания реакции с использованием палладиевых мембран различной водородоселективности и проницаемости в температурном интервале 923–1023 К представлены модель, экономический анализ процесса и проектные рекомендации для его промышленной реализации.
Целью данной работы является исследование закономерностей протекания паровой конверсии этана и метан-этановых смесей в мембранном реакторе с получением водорода высокой чистоты.
2. МЕТОДИКА ЭКСПЕРИМЕНТА
2.1. Мембранный реактор
Фольга толщиной 30 мкм из сплава Pd–6% Ru, которую использовали в качестве водородселективной мембраны, предоставлена сотрудниками лаборатории 12 Института металлургии и материаловедения РАН (ИМЕТ РАН, МОСКВА) [18]. Заготовки под фольгу получали плавкой в электродуговой печи в инертной атмосфере. Фольгу заданной толщины получали холодным прокатом с промежуточными вакуумными отжигами. Мембрана из фольги имела форму диска диаметром 56 мм (эффективная площадь поверхности 15.2 см2). Для поддержания механической прочности ее помещали между сетками тонкого плетения из нержавеющей стали. Мембранный реактор включал отделения подвода сырья (ретентат) и отвода Н2 (пермеат), между которыми помещали мембрану [20]. На рис. 1 представлены конструкция реактора и схема экспериментальной установки [19].
Рис. 1.
Экспериментальная установка. (а) Вертикальное сечение: 1 – отверстие для трубки с термопарой, 2 – внешняя стенка, 3 – мембранный модуль, 4 – электоронагреватель, (5–7) – стальные трубки для подачи сырья и выхода продуктов из отделений ретентата и пермеата, 8 – холодильник, 9 – смеситель, (10–13) – ротаметры, 14 – вакуумный насос. (б) Мембранный модуль: 1 – отделение пермеата, 2 – мембрана, 3 – отделение ретентата, 4 – трубки для подачи сырья и выхода продуктов реакции. (в) Схема реакционной ячейки: 1 – вакуумируемое отделение пермеата, 2 – отделение ретентата с катализатором, 3 – мембрана.
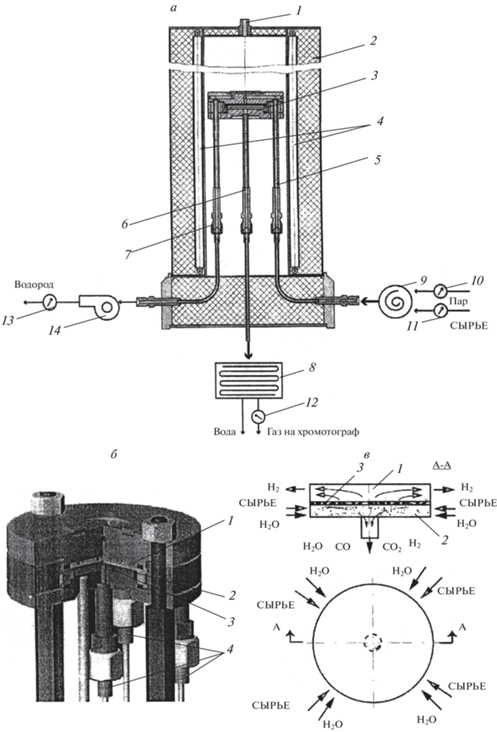
В отделении ретентата поддерживали атмосферное давление. Для отвода Н2 из реакционной смеси через мембрану в отделении пермеата снижали парциальное давление Н2. Для этого противотоком сырью подавали отводящий газ (N2) со скоростью 150 см3/мин. Кроме отводящего газа, для отвода Н2 применяли вакуумирование отделения пермеата с использованием безмасляного диафрагменного (мембранного) вакуумного насоса MZ 2C NT (Германия).
Конверсию сырья (α, %), селективность образования продуктов паровой конверсии этана (Sпрод, %) и отвод Н2 через мембрану (φ, %) рассчитывали по формулам [20]:
(1)
$\alpha = \frac{{{{V}^{{{\text{вх}}}}}X_{{{\text{С}}{{{\text{Н}}}_{{\text{4}}}}}}^{{{\text{вх}}}} - {{V}^{{{\text{рет}}}}}Х_{{{\text{С}}{{{\text{Н}}}_{{\text{4}}}}}}^{{{\text{рет}}}}}}{{{{V}^{{{\text{вх}}}}}X_{{{\text{С}}{{{\text{Н}}}_{{\text{4}}}}}}^{{{\text{вх}}}}}} \times 100\% ,$(2)
${{S}_{{{\text{прод}}}}} = \frac{{{{V}^{{{\text{рет}}}}}{{X}_{{{\text{прод}}}}}}}{{2\left( {{{V}^{{{\text{вх}}}}}X_{{{{{\text{C}}}_{{\text{2}}}}{{{\text{H}}}_{{\text{6}}}}}}^{{{\text{вх}}}} - {{V}^{{{\text{рет}}}}}X_{{{{{\text{C}}}_{{\text{2}}}}{{{\text{H}}}_{{\text{6}}}}}}^{{{\text{рет}}}}} \right)}} \times 100\% ,$(3)
$\varphi = \frac{{{{V}^{{{\text{перм}}}}}X_{{{{{\text{H}}}_{{\text{2}}}}}}^{{{\text{перм}}}}}}{{{{V}^{{{\text{перм}}}}}X_{{{{{\text{H}}}_{{\text{2}}}}}}^{{{\text{перм}}}} + {{V}^{{{\text{рет}}}}}X_{{{{{\text{H}}}_{{\text{2}}}}}}^{{{\text{рет}}}}}} \times 100\% ,$$Х_{{{\text{С}}{{{\text{Н}}}_{{\text{4}}}}{\text{(}}{{{\text{С}}}_{{\text{2}}}}{{{\text{Н}}}_{{\text{6}}}}{\text{)}}}}^{{{\text{вх}}}}$ – объемная концентрация СН4 (или С2Н6) в газовом потоке на входе в реактор, об. %;
$Х_{{{\text{С}}{{{\text{Н}}}_{{\text{4}}}}{\text{(}}{{{\text{С}}}_{{\text{2}}}}{{{\text{Н}}}_{{\text{6}}}}{\text{)}}}}^{{{\text{рет}}}}$ – объемная концентрация СН4 (или С2Н6) в продуктах реакции на выходе из отделения ретентата, об. %;
${{V}^{{{\text{перм}}}}}$ – скорость газового потока на выходе из отделения пермеата, см3/мин;
$Х_{{{{{\text{Н}}}_{{\text{2}}}}}}^{{{\text{перм}}}}$ – объемная концентрация Н2 в пермеате, об. %;
${{V}^{{{\text{рет}}}}}$ – скорость газового потока на выходе из отделения ретентата, см3/мин;
$Х_{{{{{\text{Н}}}_{{\text{2}}}}}}^{{{\text{рет}}}}$ – объемная концентрация Н2 в ретентате, об. %.
Скорость образования углеродных отложений из этана рассчитывали из материального баланса по углероду. Количество поступающего в реактор углерода (ммоль/мин гкат) рассчитывали на основании скорости подачи сырья в реактор и содержания в нем этана:
(4)
${{С}^{{{\text{вх}}}}} = \frac{{2{{V}^{{{\text{вх}}}}}X_{{{{{\text{С}}}_{{\text{2}}}}{{{\text{Н}}}_{{\text{6}}}}}}^{{{\text{вх}}}}}}{{22.4 \times 100}}.$Для расчета количества образующегося углерода (ммоль/мин гкат) использовали скорость газового потока, выходящего из отделения ретентата и содержание в нем углеродсодержащих компонентов.
(5)
${{С}^{{{\text{рет}}}}} = \frac{{{{V}^{{{\text{рет}}}}}\left( {Х_{{{\text{СО}}}}^{{{\text{рет}}}} + Х_{{{\text{С}}{{{\text{О}}}_{{\text{2}}}}}}^{{{\text{рет}}}} + Х_{{{\text{С}}{{{\text{Н}}}_{{\text{4}}}}}}^{{{\text{рет}}}} + 2Х_{{{{{\text{С}}}_{{\text{2}}}}{{{\text{Н}}}_{{\text{6}}}}}}^{{{\text{рет}}}}} \right)}}{{22.4 \times 100}}.$Количество УО (ммоль/мин гкат) представляет собой разность между количеством поступающего и образующегося углерода:
2.2. Исследование паровой конверсии [13]
В качестве сырья использовали как этан (99.95%), так и смеси метана (99.95%), содержащие 5, 10 и 15 об. % С2Н6. В отделение ретентата помещали 2 см3 (3.35 г) промышленного никелевого катализатора паровой конверсии природного газа марки НИАП–03-01 (производитель ООО “НИАП-КАТАЛИЗАТОР”, г. Новомосковск), содержащего 11.2 мас. % Ni в пересчете на NiO. Сырье смешивали с водяным паром в требуемом соотношении и подавали с заданной скоростью на катализатор через отверстия, расположенные по периферии отделения ретентата, а образующиеся продукты отводили через центральное отверстие и пропускали через холодильник для конденсирования непрореагировавшей воды. Объемную скорость “сухих” газов, выходящих из реактора, измеряли, используя пенный расходомер, и подавали в хроматограф. Состав продуктов анализировали в режиме реального времени с использованием хроматографа “Кристалл-5000” с ПИД и детектором по теплопроводности. Содержание Н2 в продуктах реакции определяли на колонке с молекулярными ситами 13Х (2 мм × 2 м, 50°С, газ-носитель – аргон). Углеводородный состав продуктов определяли на колонке НР-Al/KCl (0.5 мм × 30 м, 80°С, газ-носитель – гелий). Содержание СО и СО2 определяли на колонке с активированным углем (2 мм × 2 м, 100°С, газ-носитель-гелий). Для расчета содержания продуктов использовали метод абсолютной калибровки.
Расходы газовых потоков контролировали регуляторами расхода газа РРГ-12 (“Элточприбор”, г. Зеленоград). Нагрев реактора осуществляли электрической печью. Для контроля за температурой в реакторе и в печи использовали хромель-алюмелевые термопары.
Катализатор обрабатывали непосредственно в реакторе смесью (60% Н2–40% Ar) – пар в течение 60 мин при температуре эксперимента (предварительные эксперименты показали, что изменение температуры предварительной обработки катализатора в интервале 773–973 К не влияет на его активность). Время реакции 90 мин.
Холостые эксперименты показали, что при выбранных условиях в отсутствие катализатора в мембранном реакторе паровая конверсия не протекает.
3. РЕЗУЛЬТАТЫ И ИХ ОБСУЖДЕНИЕ
Паровую конверсию этана исследовали при температурах 773–853 К (метан-этановые смеси – при 773 и 823 К), объемных скоростях сырья 1800 и 3600 ч–1 и соотношении пар/сырье 5. Объемная скорость 1800 ч–1 соответствует подаче в реактор этана (или метан-этановой смеси) со скоростью 10 см3/мин и пара со скоростью 50 см3/мин. При объемной скорости 3600 ч–1 соответствующие скорости составляют 20 и 100 см3/мин. Выполненные ранее исследования показали, что при выбранных условиях наблюдается высокое превращение сырья по реакции паровой конверсии и низкая скорость образования УО, т.е. эти условия являются оптимальными для изучения в данном мембранном реакторе [13, 20]. Продуктами реакции являются Н2, СО2, СО (менее 5%) и СН4. Согласно расчету материального баланса по углероду, реакция также сопровождается образованием УО.
3.1. Исследование паровой конверсии этана
Паровая конверсия этана происходит по реакциям:
(7)
$\begin{gathered} {{{\text{С}}}_{{\text{2}}}}{{{\text{Н}}}_{{\text{6}}}} + {\text{2}}{{{\text{H}}}_{{\text{2}}}}{\text{O}} \to {\text{2CO}} + 5{{{\text{H}}}_{{{\text{2\;}}}}} \\ \Delta Н_{{298}}^{0} = 346{\text{ кДж/моль}}, \\ \end{gathered} $(8)
$\begin{gathered} {{{\text{C}}}_{{\text{2}}}}{{{\text{H}}}_{{\text{6}}}} + {\text{4}}{{{\text{H}}}_{{\text{2}}}}{\text{O}} \to 2{\text{C}}{{{\text{O}}}_{{\text{2}}}} + 7{{{\text{H}}}_{2}} \\ \Delta Н_{{298}}^{0} = 264{\text{ кДж/моль}}. \\ \end{gathered} $Кроме того, возможно протекание гидрокрекинга этана:
(9)
${{{\text{С}}}_{{\text{2}}}}{{{\text{Н}}}_{{\text{6}}}} + {{{\text{Н}}}_{{\text{2}}}} \leftrightarrow {\text{2С}}{{{\text{Н}}}_{4}}\,\,\,\Delta Н_{{298}}^{0} = - 66{\text{ кДж/моль}}.$Высокие температуры реакции благоприятны для протекания крекинга этана:
(10)
${{{\text{С}}}_{{\text{2}}}}{{{\text{Н}}}_{{\text{6}}}} \to 2{\text{C}} + 3{{{\text{H}}}_{{\text{2}}}}.$При выбранных условиях конверсия этана в мембранном реакторе близка к 100%. Для сравнения проведены эксперименты в традиционном реакторе (без отвода Н2), в которых вместо мембраны устанавливали газонепроницаемую перегородку из нержавеющей стали. На рис. 2а, 2б показаны селективности образования СО2 и СН4 в мембранном и традиционном процессах. Селективность образования СО не представлена, она составляет 1–3%. Поскольку целевой продукт Н2 получается наряду с СО2 по реакции (8), по изменению содержания СО2 в реакционной смеси можно судить об образовании Н2. Из представленных на рис. 2а, 2б зависимостей видно, что при всех условиях селективность образования СО2 в мембранном реакторе выше, чем в традиционном. При вакуумировании пермеата она возрастает и приближается к 100%. В то же время побочная реакция гидрокрекинга этана с образованием СН4 в мембранном реакторе ниже, чем в традиционном. Это может быть обусловлено более низким содержанием Н2 в мембранном реакторе вследствие его извлечения из реакционной смеси. Как показано на рис. 2а, селективность образования СН4 в мембранном реакторе при 1800 ч–1 составляет 6% и снижается с температурой до 2%. При этих условиях в традиционном реакторе селективность образования СН4 составляет 9–11%, т.е. гидрокрекинг этана выше, чем в мембранном реакторе. При объемной скорости 3600 ч–1 в мембранном реакторе в начале исследуемого температурного интервала наблюдается высокая селективность образования СН4, составляющая около 35%, при вакуумировании пермеата она снижается до 12% (рис. 2б). Аналогичную закономерность мы установили ранее при исследовании паровой конверсии другого углеводородного сырья в данном мембранном реакторе [13, 20]. Предположено, что при указанных условиях СН4 образуется не по реакции гидрокрекинга, а в результате смещения равновесия эндотермической реакции 11 влево, т.е. в строну СН4 и Н2О, происходящего при уменьшении времени контакта сырья с катализатором и снижении температуры. При вакуумировании пермеата увеличивается конверсия СО по реакции водяного газа, что приводит к смещению равновесия реакции 11 вправо, в результате чего содержание СН4 в реакционной смеси снижается. В то же время в традиционном реакторе при указанных условиях селективность образования СН4 составляет 37–40%, что указывает на высокое превращение этана в побочной реакции гидрокрекинга (рис. 2б). В целом, полученные результаты показывают, что проведение паровой конверсии этана в мембранном реакторе имеет существенные преимущества по сравнению с традиционным реактором, поскольку приводит к увеличению превращения этана по реакции паровой конверсии и снижению его гидрокрекинга. При вакуумировании пермеата наблюдается почти 100%-ное превращение этана в СО2 и, следовательно, в целевой продукт Н2.
Рис. 2.
Изменение селективности образования СН4 и СО2 при паровой конверсии этана в мембранном и традиционном реакторах. Объемная скорость сырья (ч–1): 1800 (а) и 3600 (б). Н2 отводили как с использованием отводящего газа, так и вакуумированием пермеата.
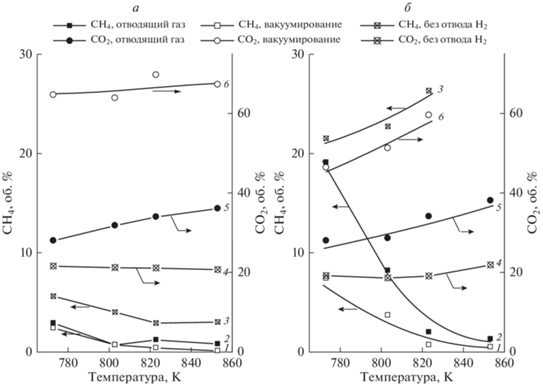
Помимо гидрокрекинга в исследуемой системе протекает побочная реакция крекинга этана с образованием УО и Н2 (реакция (10)). При объемной скорости 1800 ч–1 ее скорость невелика и во всем исследуемом температурном интервале составляет 0.01–0.02 ммоль/мин гкат (рис. 3а). При объемной скорости 3600 ч–1 скорость образования УО возрастает, к ее увеличению также приводит возрастание температуры (рис. 3а).
Рис. 3.
Изменение скорости образования УО** (а), Н2 общ* (б) и отвода Н2 (б) с температурой и объемной скоростью сырья. Соотношение пар/этан 5. Для отвода Н2 использовали отводящий газ. * Общий Н2 представлен в виде общей скорости потока Н2, выходящего из отделений ретентата и пермеата. ** Скорость образования углеродных отложений рассчитана из материального баланса по углероду.
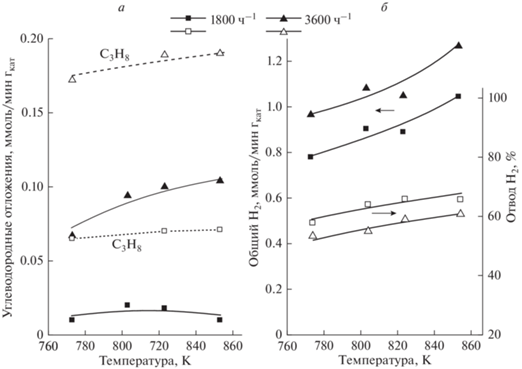
На рис. 3а для сравнения показаны зависимости, соответствующие скорости образования УО при паровой конверсии пропана в тех же условиях. Пропан может быть использован в качестве сырья в исследуемой реакции и поэтому представляет сравнить скорости образования УО из этана и пропана. Можно видеть, что из пропана образуется значительно больше УО, чем из этана.
Целевой продукт реакции Н2 содержится в газовых потоках, выходящих из отделений ретентата и пермеата мембранного реактора. Его общее количество (Н2 общ) представлено в виде общей скорости потоков на рис. 4б. Видно, что Н2 общ возрастает как с температурой, так и с увеличением объемной скорости сырья. Поскольку указанные условия благоприятны для протекания крекинга этана (рис. 4а), увеличение Н2 общ может происходить за счет образующегося при крекинге Н2. С точки зрения стабилизации каталитической системы реакцию необходимо проводить при условиях минимального образования УО. Такими условиями являются температурный интервал 773–853 К, объемная скорость 1800 ч–1 и соотношение пар/сырье 5. Помимо низкого образования УО, при указанных условиях наблюдается высокая селективность образования СО2 (следовательно, и Н2) и низкое превращение этана в реакции гидрокрекинга (рис. 2а). Кроме того, при объемной скорости 1800 ч–1 через мембрану отводится больше Н2, чем при 3600 ч–1 (рис. 3б). Отвод Н2 через мембрану при 1800 ч–1 и использовании отводящего газа составляет более 60%, а при вакуумировании пермеата он возрастает до 80%.
3.2. Паровая конверсия смесей метана, содержащих 5, 10 и 15% этана
Паровая конверсия метана происходит по реакциям:
(11)
$\begin{gathered} {\text{С}}{{{\text{Н}}}_{4}} + {{{\text{Н}}}_{{\text{2}}}}{\text{О}} \leftrightarrow {\text{СО}} + 3{{{\text{Н}}}_{2}} \\ \Delta Н_{{298}}^{0} = 206{\text{ кДж/моль}}, \\ \end{gathered} $(12)
$\begin{gathered} {\text{СО}} + {{{\text{Н}}}_{{\text{2}}}}{\text{О}} \leftrightarrow {\text{С}}{{{\text{О}}}_{{\text{2}}}} + {{{\text{Н}}}_{2}} \\ \Delta Н_{{298}}^{0} = - 41{\text{ кДж/моль,}} \\ \end{gathered} $(13)
$\begin{gathered} {\text{C}}{{{\text{H}}}_{4}} + 2{{{\text{H}}}_{{\text{2}}}}{\text{O}} \leftrightarrow {\text{C}}{{{\text{O}}}_{2}} + 4{{{\text{H}}}_{{\text{2}}}}, \\ \Delta Н_{{298}}^{0} = 164.7{\text{ кДж/моль}}{\text{.}} \\ \end{gathered} $Присутствующий в смеси С2Н6 превращается по представленным выше реакциям (7)–(10). Гидрокрекинг этана (реакция (9)) является “нежелательной” реакцией, так как приводит к увеличению содержания метана в реакционной смеси, что снижает показатель его конверсии.
Кроме того, в исследуемой системе возможно образование УО по реакциям:
Из этана также может образовываться УО по представленной выше реакции (10).
В результате накопления УО катализатор может дезактивироваться. Для снижения этого процесса используют соотношение пар/сырье, превышающее стехиометрическое.
В этом случае избыток пара переводит углеродные отложения в газообразные продукты по реакции:
На рис. 4а, 4б показан состав реакционной смеси при 1800 и 3600 ч–1 и двух способах отвода Н2 через мембрану – с использованием отводящего газа и путем вакуумирования пермеата. Можно видеть, что при 1800 ч–1 содержание СО2 выше, чем при 3600 ч–1, что может быть обусловлено более высоким временем контакта сырья с катализатором. При вакуумировании пермеата содержание СО2 увеличивается. Содержание СО в реакционной смеси мало и не превышает 0.5%. При объемной скорости 1800 ч–1 увеличение содержания С2Н6 приводит к возрастанию СО2 в реакционной смеси, а содержание СН4 при этом не изменяется. Эти данные показывают, что в результате паровой конверсии присутствующего в смеси этана образуется дополнительное количество СО2 (следовательно, и Н2), а его гидрокрекинг не происходит. При 3600 ч–1 увеличение содержания этана в сырье не приводит к возрастанию содержания СО2 в продуктах. При этом содержание СН4 сохраняется постоянным, но возрастает по абсолютной величине. Отсюда следует, что при объемной скорости 3600 ч–1 по-прежнему гидрокрекинг содержащегося в смеси этана не происходит, содержание СН4 соответствует количеству непрореагировавшего сырья, а его увеличение обусловлено снижением превращения из-за уменьшения времени контакта. Тот результат, что при возрастании содержания этана в сырье содержание СО2 не увеличивается показывает, что этан превращается не по реакции паровой конверсии. Его превращение может происходить в результате крекинга с образованием УО и Н2. Это находится в согласии с результатами, представленными в разделе 3.1, где показано, что при объемной скорости до 3600 ч–1 скорость образования УО из этана возрастает. Поскольку зависимости для СН4 на рис. 4а, 4б соответствуют количеству непрореагировавшего метана, возможно рассчитать его конверсию по уравнению (1). При 1800 ч–1 она составляет 88% для 100%-ного СН4 и 76% для смеси, содержащей 15% С2Н6. При 3600 ч–1 конверсия снижается до соответствующих значений 80 и 68%. Этан в продуктах отсутствует, то есть превращается полностью.
Для сравнения на рис. 4а, 4б показано содержание СН4 в продуктах паровой конверсии смеси метана с пропаном. Пропан, наряду с этаном, содержится в природном и попутном нефтяном газах, которые могут являться сырьем для паровой конверсии с получением водорода. Поэтому представляет интерес исследовать его влияние на протекание побочных реакций гидрокрекинга и образования УО. Можно видеть, что при 1800 ч–1 содержание СН4 не изменяется при увеличении содержания пропана в смеси и практически не отличается от метан-этановой смеси. То есть, при указанных условиях гидрокрекинг пропана не происходит. При 3600 ч–1 содержание СН4 возрастает с увеличением содержания С3Н8, что указывает на протекание гидрокрекинга. Таким образом, в отличие от метан-этановой смеси, паровая конверсия смеси метана с пропаном при объемной скорости 3600 ч–1 сопровождается протеканием нежелательной реакции гидрокрекинга пропана.
При температуре 823 К с увеличением содержания этана в смеси содержание СО2 изменяется незначительно (рис. 5а, 5б). При вакуумировании пермеата оно возрастает, что указывает на увеличение превращения сырья по реакции паровой конверсии. Этан в продуктах отсутствует, т.е. превращается полностью. На содержание СН4 увеличение содержания С2Н6 практически не влияет. Таким образом, гидрокрекинг содержащегося в смеси этана при 823 К не происходит, а содержание метана в реакционной смеси соответствует его непрореагировавшему количеству. Это позволяет рассчитать конверсию СН4 по уравнению (1), которая при объемной скорости 1800 ч–1 составляет 92% для 100%-ного СН4 и 96% для смеси, содержащей 15% С2Н6. При объемной скорости 3600 ч–1 конверсия СН4 снижается до соответствующих значений 73 и 89%.
Рис. 5.
Изменение содержания СО, СН4 и СО2 в реакционной смеси при различном содержании С2Н6 в метане. Т = = 823 К; пар/сырье 5. Объемная скорость сырья (ч–1): 1800 (а) и 3600 (б). Пустые значки соответствуют экспериментам с вакуумированием пермеата.
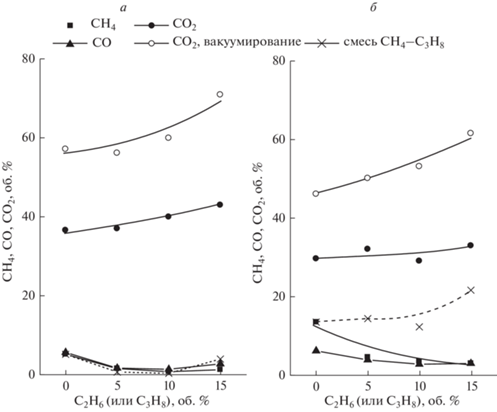
По-прежнему паровая конверсия смеси метана с пропаном при объемной скорости 3600 ч–1 приводит к увеличению содержания СН4, что указывает на протекание гидрокрекинга пропана. Например, при паровой конверсии метановой смеси, содержащей 15% пропана, в реакционной смеси содержится более 20% СН4 (рис. 5б).
Соотношение пар/алкан, используемое обычно при паровой конверсии углеводородного сырья превышает стехиометрическое, что требуется как для увеличения конверсии сырья, так и для снижения образования УО. С практической точки зрения необходим оптимум по соотношению пар/сырье, поскольку большой избыток водяного пара увеличивает капитало- и энергоемкость процесса. Кроме того, водяной пар негативно влияет на скорость отвода Н2 из реакционной смеси из-за его адсорбции на поверхности палладиевой мембраны. Представленные выше экспериментальные результаты получены при соотношении пар/сырье 5. Интересно исследовать влияние на реакцию более низкого соотношения, например, (3). Соответствующие данные для паровой конверсии метановой смеси, содержащей 15% этана, приведены в табл. 1. Там же для сравнения представлены данные для соотношения пар/сырье 5.
Таблица 1.
Влияние соотношения пар/сырье на показатели паровой конверсии метановой смеси, содержащей 15% этана. Н2 отводили с использованием отводящего газа
Объемная скорость сырья, ч–1 | Т, К | Углеродсодержащие продукты в смеси, об. % | *Н2 общ, ммоль/мин гкат |
**УО, ммоль/мин гкат |
||
---|---|---|---|---|---|---|
СН4 | СО | СО2 | ||||
Пар/сырье 3 | ||||||
1800 | 773/823 | 7.3/1.5 | 1.7/2.1 | 35.9/32.2 | 0.86/0.95 | 0.04/0.09 |
3600 | 30.5/5.4 | 3.2/3.9 | 28.6/28.0 | 0.96/1.14 | 0.06/0.12 | |
Пар/сырье 5 | ||||||
1800 | 773/823 | 7.3/1.3 | 2.3/3.1 | 45.1/43.8 | 0.59/0.62 | 0.02/0.04 |
3600 | 9.8/3.7 | 2.1/3.0 | 29.4/31.4 | 0.88/0.97 | 0.04/0.05 |
Можно видеть, что при пар/сырье 3, температуре 773 К и объемной скорости сырья 3600 ч–1 в реакционной смеси содержится более 30% СН4. Высокое содержание СН4 при указанных условиях наблюдается также при паровой конверсии другого углеводородного сырья (пропана, бутана, углеводородной смеси, моделирующей состав попутного нефтяного газа) в данном мембранном реакторе [13, 20]. Оно обусловлено не протеканием гидрокрекинга, а уменьшением конверсии СО по реакции водяного газа (реакция (12)) и смещением, вследствие этого, равновесия эндотермической реакции (11) влево. Аналогичным образом, к увеличению содержания СН4 приводит снижение температуры и возрастание объемной скорости до 3600 ч–1 при паровой конверсии этана (рис. 2б). Но основным эффектом от снижения избытка пара является увеличение скорости образования УО в результате крекинга сырья. Как видно из табл. 1, при соотношении пар/сырье 3 наблюдается более высокая скорость образования УО, чем при соотношении (5). Там же показано, что к увеличению образования УО приводит возрастание температуры и объемной скорости сырья. Образующийся при этом водород вносит вклад в скорость образования Н2 общ. Это демонстрирует рис. 6а, 6б, где показана скорость образования Н2 общ из метан-этановых смесей при 1800 и 3600 ч–1 и соотношениях пар/сырье 3 и 5. Можно видеть, что Н2 общ увеличивается как при снижении избытка пара, так и при возрастании объемной скорости сырья. Поскольку при указанных условиях увеличивается крекинг сырья с образованием УО и Н2, увеличение Н2 общ обусловлено дополнительным образованием Н2 при крекинге сырья. Поэтому, с точки зрения стабилизации каталитической системы паровую конверсию метан-этановых смесей следует выполнять при условиях минимального образования УО: Т = 773 К, 1800 ч–1 и пар/сырье 5.
ЗАКЛЮЧЕНИЕ
Исследована паровая конверсия этана и метан-этановых смесей, содержащих 5, 10 и 15% этана в мембранном реакторе с промышленным никелевым катализатором при атмосферном давлении, температурах 773 и 823 К, объемных скоростях сырья 1800 и 3600 ч–1 и соотношениях пар/сырье 3 и 5 (паровую конверсию этана исследовали в температурном интервале 773–853 К). В качестве мембраны использовали фольгу толщиной 30 мкм из Pd–Ru сплава. Сравнительные эксперименты в мембранном и традиционном реакторах показывают преимущество мембранного процесса – в результате отвода Н2 из реакционной смеси увеличивается превращение сырья по реакции паровой конверсии и снижается протекание побочной реакции гидрокрекинга этана. Увеличение скорости отвода Н2 через мембрану вакуумированием пермеата приводит к значительному увеличению селективности образования СО2, а, следовательно, и целевого продукта Н2. Конверсия сырья в углеродные отложения возрастает при увеличении объемной скорости сырья, температуры и снижении соотношения пар/сырье.
Результаты исследования показывают, что этан, как в смеси с метаном, так и в индивидуальном виде может быть использован как сырье для паровой конверсии. По сравнению с другими С2+алканами при выбранных условиях из этана образуется меньше углеродных отложений и СН4. Оптимальными условиями паровой конверсии этана в данном мембранном реакторе являются температурный интервал 773–853 К, объемная скорость сырья 1800 ч–1 и соотношение пар/сырье 5. Для паровой конверсии метан-этановых смесей оптимальной является температура 773 К. При указанных условиях наблюдается близкая к 100% конверсия этана, а в метан- этановых смесях полное превращение этана и высокие показатели конверсии СН4. При этом наблюдается низкая конверсия сырья в углеродные отложения и незначительно превращение по реакции гидрокрекинга. При вакуумировании пермеата из реакционной смеси извлекается более 80% образующегося водорода. Увеличение как температуры, так и объемной скорости сырья приводит к более высокому выходу целевого продукта. Однако при этом часть водорода получается в результате крекинга сырья с образованием углеродных отложений, которые могут дезактивировать катализатор. Установленные закономерности сходны с полученными ранее для другого углеводородного сырья (смесей метана с пропаном, пропана, н-бутана, модельной смеси с усредненным составом попутного нефтяного газа). Таким образом, в данном реакторе возможно получать водород высокой чистоты из различных видов углеводородного сырья.
Список литературы
Филиппов С.П., Ярославцев А.Б. // Успехи химии. 2021. Т. 90. № 6. С. 627. (Filippov S.P., Yaroslavtsev A.B. // Russian Chemical Reviews. 2021. V. 90. № 6. P. 627).
Dincer I., Acar C. // Int. J. Hydrogen Energy. 2015. V. 40. P. 11094.
Грязнов В.М. // Докл. АН СССР. 1969. Т. 189. С. 794.
Gryaznov V.M. // Platinum Met. Rev. 1986. V. 30. P. 68.
Грязнов В.М., Ермилова М.М., Орехова Н.В., Скакунова Е.В. // Изв. АН СССР. Сер. Хим. 1988. № 4. С. 750. (Gryaznov V.M., Ermilova M.M., Orekhova N.V., Skakunova E.V. // Russ.Chem. Bull., International Edition. 1988. V. 37. P. 637).
Gryaznov V.M. // Sep. Purif. Rev. 2000. V. 29. P. 171.
Habib M.A., Harale A., Paglieri S., Alrashed F.S., Alsayoud A., Rao M.V., Nemitallah M.A., Hossain S., Hussien M., Ali A., Haque M.A., Abuelyamen A., Shakeel M.R., Mokheimer E.M.A., Ben-Mansour R. // Energy Fuels. 2021. V. 35. № 7. P. 5558.
Jokar S.M., Farokhnia A., Tavakolian M., Pejman M., Parvasi P., Javanmardi J., Zare F., Clara Gonçalves M., Basile A. // Int. J. Hydrogen Energy. 2022. https://doi.org/10.1016/
Anzelmo B., Wilcox J., Liguori S. // J. Membr. Sci. 2018. V. 565. P. 25.
Anzelmo B., Wilcox J., Liguori S. // J. Membr. Sci. 2018. V. 568. P. 113–120.
Shirasaki Y., Tsuneki T., Ota Y., Yasuda I., Tachibana S., Nakajima H., Kobayashi K. // Int. J. Hydrogen Energy. 2009. V. 34. P. 4482.
Kim C.-H., Han J.-Y., Kim S., Lee B., Lim H., Lee K.-Y., Ryi S.-K. // Int. J. Hydrogen Energy. 2018. V. 43. № 15. P. 7684.
Диденко Л.П., Бабак В.Н., Семенцова Л.А., Дорофеева Т.В., Чижов П.Е., Горбунов С.В. // Мембраны и мембранные технологии. 2021. Т. 11. № 5. С. 336. (Didenko L.P., Babak V.N., Sementsova L.A., Dorofeeva T.V., Chizhov P.E., and Gorbunov S.V. // Membranes and Membrane Technologies. 2021. V. 3. № 5. P. 302).
Angeli S.D., Pilitsis F.G., Lemonidou A.A. // Catalysis Today. 2015. V. 242. P. 119.
Veranitisagul C., Koonsaeng N., Laosiripojana N., Laobuthee A. // J. Ind. Eng. Chem. 2012. V. 18. P. 898.
Li S., Gong J. // Chem. Soc. Rev. 2014. V. 43. P. 7245.
Jeong S., Kim S., Lee B., Ryi S.-K., Lim H. // Int. J. Hydrogen Energy. 2018. V. 43. P. 7693.
Бурханов Г.С., Рошан Н.Р., Горбунов С.В., Касьянов В.С., Кутербеков К.А., Бекмырза К.Ж., Мерзадинова Г.Т. // Металлы. 2021. № 2. С. 71.
Бабак В.Н., Диденко Л.П., Семенцова Л.А., Квурт Ю.П. // Теоретические основы химической технологии. 2022. Т.56. № 3. С. 282. (Babak V.N., Didenko L.P., Sementsova L.A., Kvurt J.P. // Theoretical foundations of chemical engineering. 2022. V. 56. № 3. P. 279).
Диденко Л.П., Семенцова Л.А., Бабак В.Н., Чижов П.Е., Дорофеева Т.В., Квурт Ю.П. // Мембраны и мембранные технологии. 2020. Т. 10. № 2. С. 99. (Didenko L.P., Babak V.N., Sementsova L.A., Chizhov P.E., Dorofeeva T.V., Kvurt J.P. // Membranes and Membrane Technologies. 2020. V. 2. № 2. P. 85.)
Дополнительные материалы отсутствуют.
Инструменты
Мембраны и мембранные технологии