Российские нанотехнологии, 2020, T. 15, № 6, стр. 811-819
ИССЛЕДОВАНИЕ КИСЛОРОДНОГО КОНЦЕНТРАТОРА С ТВЕРДЫМ ПОЛИМЕРНЫМ ЭЛЕКТРОЛИТОМ С НАНОСТРУКТУРНЫМИ КАТАЛИЗАТОРАМИ НА ОСНОВЕ ГИДРОФОБИЗИРОВАННОГО НОСИТЕЛЯ
А. С. Пушкарев 1, 2, 3, *, И. В. Пушкарева 1, 2, М. А. Соловьев 1, 2, С. И. Бутрим 2, С. А. Григорьев 1
1 Национальный исследовательский центр “Курчатовский институт”
Москва, Россия
2 Национальный исследовательский университет “МЭИ”
Москва, Россия
3 Московский физико-технический институт (Национальный исследовательский университет)
Долгопрудный, Россия
* E-mail: pushkarev_as@nrcki.ru
Поступила в редакцию 11.06.2020
После доработки 11.06.2020
Принята к публикации 03.07.2020
Аннотация
В настоящее время важной задачей является эффективное производство газообразного кислорода, использующегося во многих отраслях промышленности, для обеспечения жизнедеятельности человека в анаэробных средах, а также в медицине (например, при острой респираторной недостаточности, которая является одним из осложнений при COVID-19). Электрохимический насос (концентратор) кислорода с твердым полимерным электролитом (ТПЭ) – электролизер с деполяризацией катода воздухом – является многообещающим устройством, позволяющим портативно, безопасно и эффективно производить высокочистый кислород непосредственно на месте его использования с меньшими вдвое энергозатратами по сравнению с электролизером с ТПЭ. Рассмотрено влияние гидрофобизации наноструктурного катализатора реакции восстановления кислорода на характеристики кислородного насоса и стойкость катодного каталитического слоя к затоплению. Модификация углеродного носителя частицами политетрафторэтилена позволяет улучшить отвод избыточной воды из каталитического слоя на его основе и повысить предельный ток, характеризующий возникновение транспортных ограничений. Рабочие параметры (температура, расход и давление воздуха) также оказывают существенное влияние на характеристики кислородного насоса, они должны быть оптимизированы для улучшения транспорта воды в каталитических слоях, повышения рабочих плотностей тока и снижения энергозатрат на получение кислорода.
ВВЕДЕНИЕ
Среди электрохимических систем с твердым полимерным электролитом (ТПЭ) наибольшее распространение получили топливные элементы (ТЭ) и электролизеры воды, которые благодаря таким качествам, как высокая эффективность и маневренность, компактность, высокая удельная мощность, уже выходят на рынок. В частности, ТЭ рассматриваются в качестве основы силовых установок и источников тока для небольших генераторов энергии (в том числе резервных), транспорта (от небольших беспилотных летательных аппаратов до автомобилей, автобусов и т.д.) и портативных электронных устройств [1], а электролизер – в качестве источника водорода и кислорода (который чаще рассматривается в качестве побочного продукта) [2].
Однако можно выделить ряд электрохимических устройств на основе ТПЭ, которые могут претендовать на свои рыночные ниши. К таким устройствам, в частности, относятся концентратор кислорода [3, 4], концентратор водорода [5], осушитель воздуха [6], генератор озона [7, 8] и конвертеры спиртов (метанола, этанола и др.) [9, 10].
На данный момент кислород в основном получают методами разделения компонентов воздуха (криогенные, мембранные и сорбционные технологии [11]), а также электролизом воды, который используется главным образом для получения водорода. Ввиду все более широкого распространения электролизеров воды кислород является важным продуктом водородной энергетики, который используется в различных отраслях промышленности, для обеспечения жизнедеятельности человека в анаэробных средах, а также в медицине (например, при острой респираторной недостаточности, которая является одним из осложнений при COVID-19) [12]. Кроме того, он не только не загрязняет окружающую среду, а наоборот, оказывает положительное влияние на экологическую обстановку. С другой стороны, энергозатраты на его получение таким путем достаточно велики (по крайней мере вдвое выше, чем энергозатраты на получение водорода: 7–10 кВт ч/нм3 [3, 13]). К другим недостаткам электролизеров с ТПЭ с точки зрения получения кислорода как основного продукта можно отнести необходимость в безопасной утилизации образующегося водорода, а также кроссовере водорода через мембрану и загрязнении целевого продукта, что выражается в достаточно высоких концентрациях водорода в образующемся на аноде кислороде (до 1.5 об. % в зависимости от плотности тока, давления и других параметров процесса [14, 15]).
Поэтому необходимо отказаться от реакции выделения водорода на катоде и обеспечить потребление протонов, образующихся в ходе анодного процесса окисления воды, в другом процессе, например в реакции восстановлении кислорода (РВК) [16], которая является катодной реакцией для ТЭ с ТПЭ [17]. Такой подход также позволит существенно снизить энергозатраты на получение кислорода, так как равновесное напряжение такого элемента близко к нулю [4].
Предлагаемая электрохимическая система – кислородный насос (КН) (концентратор) с ТПЭ – в которой анодным процессом является выделение кислорода, а катодным – восстановление кислорода с образованием воды, является перспективной для эффективного получения кислорода высокой чистоты, в том числе компримированного (до 25 МПа) [18]. К его достоинствам можно отнести бесшумность работы, отсутствие в рабочей зоне веществ, загрязняющих конечный продукт, высокую маневренность по нагрузке и возможность использования в качестве реагента воздух из окружающей среды без предварительного нагрева [4]. Результаты предварительных исследований [4, 16] показали, что при достаточно высоких значениях напряжения (1.7–1.8 В) образование водорода остается незначительным, что гарантирует безопасность такого концентратора в сочетании с высокой производительностью. Отметим, что традиционные способы концентрирования кислорода из воздуха обеспечивают чистоту кислорода более 99 об. % [19], в то время как концентратор кислорода с ТПЭ способен обеспечить чистоту кислорода до 99.9 об. % и выше [16].
Важнейшим аспектом работы электрохимических систем с ТПЭ является водный баланс элемента. В частности, в ТЭ с ТПЭ замедленный отвод влаги из катодного электрокаталитического слоя приводит к его затоплению и снижению активной поверхности и, напротив, слишком быстрый отвод воды, прибывающей в результате электроосмотического переноса с анода и образующейся дополнительно в результате протекания РВК, приводит к локальному осушению ТПЭ, увеличению сопротивления и соответствующему ухудшению характеристик элемента [20]. Более того, воздушный катод КН с ТПЭ при практически значимых плотностях тока (0.5–1 А/см2) вынужден функционировать в условиях значительного электроосмотического и диффузионного потоков воды со стороны анода, характерных для заполненного водой электролизера воды с ТПЭ (число переносимых молекул воды на один протон достигает 2.5–4 молекул H2O на 1 H+ [21]). В этой связи для создания высокоэффективного концентратора кислорода с ТПЭ необходима оптимизация его режимов работы, а также состава катодного и анодного электрокаталитических слоев с точки зрения их активности и водного баланса мембранно-электродного блока (МЭБ).
В представленном исследовании рассмотрено влияние гидрофобизации наноструктурного углеродного носителя на стойкость катодного каталитического слоя КН с ТПЭ к затоплению. В качестве критерия использовалось значение предельной плотности тока (или предельного тока), которое характеризует транспортные ограничения, возникающие в каталитическом слое при его затоплении избыточным количеством воды. Кроме того, исследовано влияние различных рабочих параметров (температуры, расхода и давления воздуха в катодной камере) на характеристики КН с ТПЭ на основе катода с оптимальным содержанием политетрафторэтилена (ПТФЭ) и даны рекомендации по дальнейшей оптимизации режимов работы КН с ТПЭ.
МЕТОДИКА ЭКСПЕРИМЕНТА
Гидрофобизацию углеродного носителя частицами ПТФЭ проводили путем обработки сажи Vulcan XC-72 (Cabot, США) в водной суспензии фторопласта марки DISP 30–250 (FuelCellStore, США) с размером частиц 0.1–0.15 мкм на водяной бане при температуре 100°С с постоянным перемешиванием до полной коагуляции последнего, которая выражалась в обесцвечивании суспензии. После осаждения гидрофобизатора носитель подвергали трехкратной декантации в бидистиллированной воде, высушивали, а затем отжигали при температуре 360°С в течениe 1 ч. После охлаждения носитель измельчали в шаровой мельнице Retsch PM-100 (Retsch, Германия). Согласно приведенной методике получены носители с содержанием ПТФЭ 5, 10 и 15 мас. % (C5, C10 и C15 соответственно).
Синтез катодных электрокатализаторов на различных углеродных носителях проводили методом восстановления прекурсора наночастиц Pt H2PtCl6 ⋅ 6H2O в среде этиленгликоля (метод “полиол”), подробно описанным в [22, 23].
Для определения удельной поверхности модифицированных наноструктурных углеродных носителей применяли метод БЭТ с использованием анализатора TriStar 3000 (Micromeritics, США). Площадь удельной электрохимически активной поверхности (ЭАП) катализаторов определяли из циклических вольтамперограмм, измеренных в стандартной трехэлектродной ячейке в деаэрированном 0.5 М растворе H2SO4 [10, 24].
Наноструктурную Ir-чернь, которая использовалась в качестве анодного электрокатализатора, получали методом химического восстановления прекурсора H2IrCl6 ⋅ 6H2O с использованием NaBH4 в качестве восстанавливающего агента [25].
Для исследования характеристик кислородного насоса с ТПЭ изготавливали МЭБ, в которых в качестве ТПЭ использовали мембрану Nafion® 117 (Chemours Company, США), МЭБ имели круглую форму с рабочей поверхностью 7 см2. В качестве анодного газодиффузионного электрода (ГДЭ) использовали пористый титан (марки ВТ-1-0 толщиной 900 мкм, пористостью 28% [4, 26]), а в качестве катодного – углеродную ткань ELAT LT1400W (NuVant Systems Inc., США) с гидрофобным микропористым подслоем и пористостью 62–64%.
Формирование электрокаталитичских слоев на поверхности ГДЭ осуществляли путем распыления “каталитических чернил” в потоке воздуха, применяя промежуточную сушку нанесенных слоев, на поверхность ГДЭ [23, 27]. “Каталитические чернила” включают в себя электрокатализатор и раствор протонообменного полимера Nafion® (Ion Power, США) (содержание полимера по сухому остатку составило 15 мас. % в случае наночастиц Pt на носителях и 5 мас. % в случае Ir-черни), готовили их путем гомогенизации составляющих в среде изопропилового спирта в ультразвуковой ванне при частоте 22–25 кГц в течение 20 мин. Плотность нанесения катодного электрокатализатора составляла 1.5 мг/см2, анодного – 2 мг/см2. МЭБ формировали, используя мембрану Nafion® 117 в качестве ТПЭ и приготовленные электроды. Анод, катод и мембрану, разделяющую их, зажимали в титановой лабораторной ячейке, состоящей из двух термостатируемых полуячеек [28]. Формирование МЭБ осуществляли непосредственно в тестовой лабораторной ячейке после сборки и выдерживали при 90°С без нагрузки в течение 2 ч [27].
При тестировании МЭБ в лабораторной ячейке на аноде подачу реагента – деионизированной воды – и отвод продукта реакции – кислорода –осуществляли методом “газ-лифт” (схема экспериментального стенда приведена на рис. 1). Реагент катодной реакции – воздух с относительной влажностью 50% – продувается через катодную камеру с расходом 0.1–0.5 л/мин и уносит воду, которая является продуктом РВК, а также ту, которая электроосмотически переносится с заполненной водой анодной камеры. Вольтамперные характеристики (ВАХ) КН регистрировали в потенциостатическом ступенчатом режиме в диапазоне напряжений от 0.45 до 1.4 В. Переход к следующему значению напряжения осуществлялся только после установления стационарного значения тока при данном значении напряжения (обычно в течение 15–20 мин).
Экспериментальные ВАХ КН обрабатывали с помощью простой модели, которая позволяет разделить поляризационные, омические и диффузионные потери и часто используется для анализа ВАХ ТЭ и электролизеров воды с ТПЭ [29–31], которая для КН выражается уравнением
где UТЭ – напряжение ячейки, В; E0 – равновесный потенциал, В; ηact – электрохимические потери напряжения в МЭБ, В; ηconc – концентрационные потери, В; i – плотность тока, А/см2; Rtot – полное сопротивление КН, Ом см2. Значение равновесного потенциала (E0) рассчитывали согласно уравнению Нернста [32]. Анод и катод объединены в один эффективный электрод, а расчет электрохимических потерь (ηact) элемента осуществляли с помощью уравнения Тафеля [30]:РЕЗУЛЬТАТЫ И ИХ ОБСУЖДЕНИЕ
Результаты исследований влияния рабочих параметров КН с ТПЭ (температуры, расхода и давления воздуха на катоде) приведены для МЭБ на основе катодного катализатора наиболее удачного состава – Pt40/C10. Анализ влияния содержания ПТФЭ в составе носителя катодного катализатора приведен в конце статьи.
На рис. 2 представлены ВАХ КН с ТПЭ, полученные при различных температурах. Как и в электролизерах воды с ТПЭ [13], в КН следует использовать более толстые протонообменные мембраны (например, такие как Nafion® 117 толщиной ~180 мкм), чем применяемые в ТЭ (толщиной 50 мкм и менее). Это обусловлено возможностью использовать более высокие рабочие температуры (до 80°С) [34], а также снизить скорость диффузии азота воздуха и замедлить перенос воды с анода на катод.
Рис. 2.
Вольтамперные характеристики КН при различных температурах: 1 – 40, 2 – 60, 3 – 80°С. Катодный катализатор – Pt40/C10, расход воздуха – 0.5 л/мин.
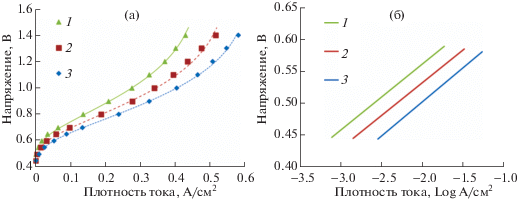
Влияние температуры на характер ВАХ как в случае электролизера воды, так и в случае КН связано прежде всего со снижением перенапряжения катодной и анодной реакций (что заметно в области малых значений плотности тока – до 0.1 А/см2), а также уменьшением омического сопротивления МЭБ (зависящего главным образом от протонной проводимости мембраны [35], электронной и протонной проводимости каталитических слоев [36], и контактных сопротивлений между компонентами МЭБ [37]), которое проявляется в уменьшении наклона линейного участка ВАХ в области значений плотности тока 0.1–0.3 А/см2.
Напряжение КН, при котором процесс концентрирования кислорода начинает протекать с заметной скоростью, составляет ~0.45–0.5 В, что близко к значению, представленному в литературе – 0.53 В [16].
ВАХ КН (рис. 2а) характеризуется несколькими характерными областями. В области низких плотностей тока (обычно до 0.07–0.1 А/см2 [27, 34, 38]) в величине напряжения доминируют кинетические потери, связанные с поляризацией анода и катода. При росте плотности тока наблюдается переход к линейной области ВАХ, где доминируют омические потери напряжения. Дальнейший нелинейный рост напряжения при значениях плотности тока более 0.3 А/см2, по-видимому, связан с ограничениями транспорта кислорода и падением его концентрации (парциального давления) в активной зоне катода.
Тафелевский наклон характеристики МЭБ на основе Pt/Vulcan XC-72 и Ir-черни (рис. 2б) в области низких плотностей тока (до 0.1 А/см2) включает в себя как вклад со стороны РВК, так и со стороны реакции выделения кислорода [34, 38] и составил ~102–107 мВ/дек. Полученные значения являются вполне обоснованными. Согласно литературным данным реакция выделения кислорода на аморфных оксидах Ir (которые формируются в активном слое анода на основе черни Ir [39] при окислении металлического Ir) протекает с высокой скоростью при участии активированных атомов кислорода кристаллической решетки [40, 41], в этом случае значение тафелевского наклона для реакции составляет ~38–45 мВ/дек [42–44]. Тафелевский наклон РВК для малых плотностей тока при протекании реакции по типичному для Pt механизму, включающему в себя перенос первого электрона в качестве лимитирующей стадии, составляет ~60–70 мВ/дек [45]. Из результатов, приведенных на рис. 2а, видно, что увеличение температуры практически не влияет на механизм реакции, но позволяет повысить скорость электрохимических реакций [46] и снизить сопротивление ячейки главным образом за счет повышения протонной проводимости мембраны [47]. В частности, при увеличении температуры КН с 40 до 80°С сопротивление ячейки падает с 0.3 до 0.23 Ом см2.
Повышение рабочей температуры приводит к смещению предельной плотности тока в сторону более высоких значений – с 0.487 А/см2 при 40°С до 0.63 А/см2, что хорошо согласуется с данными [4]. Это происходит, по-видимому, за счет ускорения диффузии кислорода в активном слое и смещения водного баланса ячейки в сторону меньшего влагосодержания активного слоя катода за счет увеличения влагоемкости отходящего воздуха.
На рис. 3 приведены результаты исследований влияния расхода воздуха (коэффициента избытка) на ВАХ КН.
Рис. 3.
Вольтамперные характеристики КН при различном расходе воздуха: 1 – 0.3, 2 – 0.4, 3 – 0.5 л/мин. Катодный катализатор – Pt40/C10, температура – 80°С.
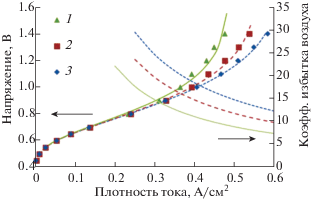
Увеличение расхода воздуха (коэффициента избытка), подаваемого на катод (рис. 3), способствует более быстрому удалению избыточной влаги из пор газодиффузионного и электрокаталитического слоев катода, предотвращая его затопление. Из результатов, приведенных на рис. 3, видно, что увеличение скорости потока воздуха существенно влияет на ВАХ КН: при расходах воздуха в диапазоне 0.3–0.5 л/мин ВАХ претерпевает изменения только в области высоких плотностей тока, где доминируют потери, связанные с транспортом кислорода к активным центрам катода и его затоплением водой, а предельный ток увеличивается с 0.488 до 0.63 А/см2. Можно предположить, что дальнейшее увеличение расхода воздуха позволит повысить значение предельной плотности тока и продлить линейную область ВАХ КН (фактически – рабочий диапазон плотностей тока) до более высоких значений, характерных для электролизеров с ТПЭ – до 1 А/см2 и выше [4, 16]. С другой стороны, увеличение расхода воздуха будет ограничено некоторым предельным значением для данного состава катодного электрокаталитического слоя, при котором наступит локальное пересыхание слоя и резкий рост сопротивления. Таким образом, необходима дальнейшая оптимизация режима работы КН с ТПЭ с заданным составом МЭБ в более широком диапазоне значений расхода воздуха, что оказалось технологически невозможным в данном исследовании.
На рис. 4 представлены результаты исследования влияния давления воздуха, подаваемого на катод, на ВАХ КН с ТПЭ. Из приведенных результатов видно, что влияние давления воздуха на ВАХ КН носит ограниченный характер и главным образом выражается в ускорении кинетики катодной реакции за счет повышения концентрации и облегчения доступа кислорода к активным центрам катализатора, а также снижения перепада парциального давления кислорода между входом и выходом (который возникает вследствие протекания реакции), что приводит к некоторому снижению напряжения ячейки во всем диапазоне плотностей тока [48, 49]. Однако при повышении давления с 0.2 до 0.3 МПа влияние давления оказывается незначительным.
Рис. 4.
Вольтамперные характеристики КН при различном давлении воздуха на катоде: 1 – 0.1, 2 – 0.2, 3 – 0.3 МПа. Катодный катализатор – Pt40/C10, расход воздуха – 0.5 л/мин, температура – 80°С.
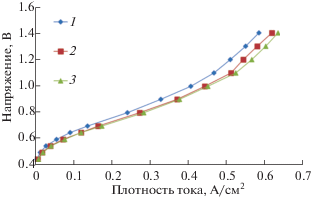
Повысить предельный ток и расширить рабочий диапазон КН с ТПЭ можно с помощью улучшения транспортных свойств катодного электрокаталитического слоя в сторону более быстрого отвода влаги. Введение в катодный каталитический слой частиц ПТФЭ способствует формированию системы каналов, по которым возможен эффективный отвод избыточной влаги из слоя [31, 50], а также более эффективному транспорту кислорода к активным центрам катализатора [51, 52]. В представленной работе синтезированы катодные электрокатализаторы на основе сажи, модифицированной частицами ПТФЭ, в качестве носителя.
На рис. 5 приведены фрагменты циклических вольтамперограмм синтезированных электрокатализаторов Pt40/C, Pt40/C5 и Pt40/C10, которые использовались для определения их ЭАП [10, 24]. Приведенные кривые демонстрируют выраженные пики адсорбции/десорбции водорода в области потенциалов ~0.05–0.40 В относительно стандартного водородного электрода (СВЭ), характерные для катализаторов на основе наночастиц Pt [53], которые представляют собой заряд, затраченный на адсорбцию/десорбцию монослоя H2 и используются для определения ЭАП электрокатализаторов. Форма кривых свидетельствует о том, что внедрение в носитель частиц ПТФЭ не оказывает влияния на поликристаллическую структуру наночастиц Pt [53].
Рис. 5.
Фрагменты циклических вольтамперограмм различных катализаторов: 1 – Pt40/C, 2 – Pt40/C5, 3 – Pt40/C10, которые измерены в 0.5 М растворе H2SO4 при температуре 25°С и скорости развертки потенциала 20 мВ/с.
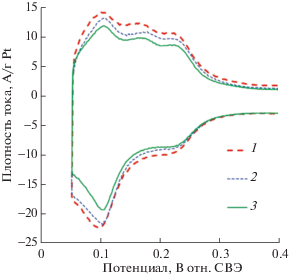
В табл. 1 представлены значения удельной площади поверхности носителей и значения ЭАП синтезированных катализаторов с различным содержанием ПТФЭ.
Таблица 1.
Характеристики углеродного носителя и катализаторов на их основе с разным содержанием ПТФЭ
Катализатор | Удельная площадь поверхности носителя, измеренная методом адсорбции азота, м2/г | Удельная электрохимически активная площадь поверхности катализатора, м2/г Pt |
---|---|---|
Pt40/С | 230 | 52.5 |
Pt40/С5 | 208 | 48.7 |
Pt40/С10 | 171 | 43.3 |
Pt40/С15 | 138 | 37.4 |
Предварительное осаждение на поверхности сажи частиц ПТФЭ приводит к заметному снижению его удельной поверхности (по БЭТ), а ЭАП электрокатализатора на основе указанных носителей с ростом содержания ПТФЭ снижается не так быстро (табл. 1). Это может объясняться тем, что при умеренной концентрации ПТФЭ (до 5–10 мас. %) число центров нуклеации наночастиц Pt на поверхности носителя остается достаточным для формирования частиц с оптимальной морфологией, а степень использования Pt несколько увеличивается за счет ускорения диффузии в каталитическом слое [54].
На рис. 6 приведены результаты исследования характеристик КН с ТПЭ с катодными катализаторами на основе углеродного носителя, модифицированного ПТФЭ. Представленные результаты показывают, что применение модифицированного носителя оказывает существенное влияние на ВАХ КН. В частности, модификация носителя 5 и 10 мас. % ПТФЭ позволила повысить предельный ток с 0.58 до 0.605 и 0.63 А/см2 соответственно. При этом тафелевский наклон всех исследованных МЭБ лежит в узком диапазоне от 104 до 109 мВ/дек, что свидетельствует о незначительном влиянии содержания ПТФЭ в носителе на механизм РВК. На рис. 6б приведена зависимость предельного тока от содержания ПТФЭ в составе носителя катодного катализатора, которая проходит через максимум, соответствующий оптимальному значению – 10 мас. %. Модификация углеродного носителя оптимальным количеством ПТФЭ позволяет существенно улучшить транспорт воды в катодном электрокаталитическом слое, предотвратить его преждевременное затопление, облегчить доступ кислорода к активным центрам катализатора и повысить степень использования Pt [31, 50, 51]. Дальнейшее повышение содержания ПТФЭ приводит к росту размера наночастиц Pt, снижению ЭАП катализатора и значительному падению протонной проводимости каталитического слоя (вследствие снижения содержания протонпроводящего полимера [55]), что, по-видимому, обусловливает ухудшение ВАХ КН.
ЗАКЛЮЧЕНИЕ
Рассмотрено влияние гидрофобизации углеродного носителя на стойкость катодного каталитического слоя к затоплению, а также влияние рабочей температуры, расхода и давления воздуха на характеристики кислородного насоса с ТПЭ. Показано, что расход воздуха (коэффициент избытка) существенно влияет на значение предельного тока (который характеризует возникновение ограничений массопереноса в каталитическом слое при его затоплении), позволяя увеличить рабочий диапазон плотностей тока и существенно снизить энергозатраты на получение кислорода. При этом необходима оптимизация расхода воздуха (коэффициента избытка) в более широком диапазоне величин. Давление подаваемого воздуха, напротив, оказывает ограниченное влияние на характеристики КН с ТПЭ. Введение ПТФЭ в углеродный носитель является эффективным способом борьбы с преждевременным затоплением катодного каталитического слоя, позволяет повысить предельный ток и расширить рабочую область плотностей тока КН с ТПЭ, хотя приводит к существенному сокращению удельной поверхности носителя, доступной для формирования активных наночастиц, и активной поверхности катализатора на его основе. В целом энергозатраты на получение кислорода составляют 3.4–4.7 кВт ч/нм3 О2 при плотности тока 0.15–0.4 А/см2, что в 1.5–2 раза ниже по сравнению с электролизером с ТПЭ.
Исследование выполнено при финансовой поддержке стипендии Президента Российской Федерации № СП-1764.2019.1 и НИЦ “Курчатовский институт” (в рамках приказа № 1919 от 25.09.2020, подпрограмма 6).
Список литературы
Sharaf O.Z., Orhan M.F. // Renew. Sustain. Energy Rev. 2014. V. 32. P. 810. https://doi.org/10.1016/j.rser.2014.01.012
Ayers K. // Curr. Opin. Electrochem. 2019. V. 18. P. 9. https://doi.org/10.1016/j.coelec.2019.08.008
Eladeb B., Bonnet C., Favre E., Lapicque F. // J. Electrochem. Sci. Eng. 2012. V. 2. P. 211. https://doi.org/10.5599/jese.2012.0016
Калинников А.А., Островский С.В., Порембский В.И. и др. // Журн. прикл. химии. 2018. Т. 91. С. 798.
Grigoriev S.A., Shtatniy I.G., Millet P. et al. // Int. J. Hydrogen Energy. 2011. V. 36. № 6. P. 4148. https://doi.org/10.1016/j.ijhydene.2010.07.012
Li D., Qi R., Zhang L.-Z. // Int. J. Hydrogen Energy. 2019. V. 44. № 36. P. 19533. https://doi.org/10.1016/j.ijhydene.2019.06.011
Okada F., Nagashima K., Kobayashi T. // Electrochim. Acta. 2019. V. 294. P. 391. https://doi.org/10.1016/j.electacta.2018.10.055
Пушкарев А.С., Пушкарева И.В., Григорьев С.А. // Журн. прикл. химии. 2016. Т. 89. С. 857.
Ju H., Badwal S., Giddey S. // Appl. Energy. 2018. V. 231. P. 502. https://doi.org/10.1016/j.apenergy.2018.09.125
Pushkarev A., Pushkareva I., Ivanova N. et al. // Catalysts. 2019. V. 9. № 3. P. 271. https://doi.org/10.3390/catal9030271
Smith A., Klosek J. // Fuel Process. Technol. 2001. V. 70. № 2. P. 115. https://doi.org/10.1016/S0378-3820(01)00131-X
Lai C.C., Shih T.P., Ko W.C. et al. // Int. J. Antimicrob. Agents. 2020. V. 55. P. 105924. https://doi.org/10.1016/j.ijantimicag.2020.105924
Carmo M., Fritz D.L., Mergel J., Stolten D. // Int. J. Hydrogen Energy. 2013. V. 38. № 12. P. 4901. https://doi.org/10.1016/j.ijhydene.2013.01.151
Ito H., Maeda T., Nakano A., Takenaka H. // Int. J. Hydrogen Energy. 2011. V. 36. № 17. P. 10527. https://doi.org/10.1016/j.ijhydene.2011.05.127
Grigoriev S.A., Porembskiy V.I., Korobtsev S.V. et al. // Int. J. Hydrogen Energy. 2011. V. 36. № 3. P. 2721. https://doi.org/10.1016/j.ijhydene.2010.03.058
Giddey S., Ciacchi F.T., Badwal S.P.S. // J. Memb. Sci. 2010. V. 346. № 1. P. 227. https://doi.org/10.1016/j.memsci.2009.09.042
Wang Y., Ruiz Diaz D.F., Chen K.S. et al. // Mater. Today. 2020. V. 32. P. 178. https://doi.org/10.1016/j.mattod.2019.06.005
Пат. США. High-differential-pressure water electrolysis cell and method of operation / Cipollini N.E., Roy R.J., Eldridge C. заявитель и патентообладатель Hamilton Sundstrand Space System International Inc. № 20110198232A1; заявл. 19.03.2010; опубл. 18.08.2011.
Banaszkiewicz T., Chorowski M., Gizicki W. // Energy Procedia. 2014. V. 51. P. 127. https://doi.org/10.1016/j.egypro.2014.07.014
Schmittinger W., Vahidi A. // J. Power Sources. 2008. V. 180. № 1. P. 1. https://doi.org/10.1016/j.jpowsour.2008.01.070
Xie G., Okada T. // J. Electrochem. Soc. 1995. V. 142. № 9. P. 3057. https://doi.org/10.1149/1.2048686
Baranov I.E., Porembskii V.I., Lyutikova E.K. et al. // Chemical Problems. 2019. V. 17. № 4. P. 489. https://doi.org/10.32737/2221-8688-2019-4-489-499
Grigoriev S., Fateev V., Pushkarev A. et al. // Materials. 2018. V. 11. № 8. P. 1405. https://doi.org/10.3390/ma11081405
Spasov D.D., Ivanova N.A., Pushkarev A.S. et al. // Catalysts. 2019. V. 9. № 10. P. 803. https://doi.org/10.3390/catal9100803
Пушкарева И.В., Пушкарев А.С., Григорьев С.А. и др. // Журн. прикл. химии. 2016. Т. 89. С. 1586.
Fateev V., Alekseeva O., Lutikova E. et al. // Int. J. Hydrogen Energy. 2016. V. 41. № 25. P. 10515. https://doi.org/10.1016/j.ijhydene.2016.04.192
Pushkarev A.S., Solovyev M.A., Grigoriev S.A. et al. // Int. J. Hydrogen Energy. 2020. V. 45. № 49. P. 26206. https://doi.org/10.1016/j.ijhydene.2020.02.098
Valiollahi R., Vagin M., Gueskine V. et al. // Sustain. Energy Fuels. 2019. V. 3. № 12. P. 3387. https://doi.org/10.1039/C9SE00687G
Rakousky C., Reimer U., Wippermann K. et al. // J. Power Sources. 2016. V. 326. P. 120. https://doi.org/10.1016/j.jpowsour.2016.06.082
Bezmalinovic D., Simic B., Barbir F. // J. Power Sources. 2015. V. 294. P. 82. https://doi.org/10.1016/j.jpowsour.2015.06.047
Avcioglu G.S., Ficicilar B., Bayrakceken A., Eroglu I. // Int. J. Hydrogen Energy. 2015. V. 40. № 24. P. 7720. https://doi.org/10.1016/j.ijhydene.2015.02.004
Аваков В.Б., Богдановская В.А., Капустин А.В. и др. // Электрохимия. 2015. Т. 51. С. 650.
Haji S. // Renew. Energy. 2011. V. 36. № 2. P. 451. https://doi.org/10.1016/j.renene.2010.07.007
Ito H., Maeda T., Nakano A. et al. // Electrochim. Acta. 2013. V. 100. P. 242. https://doi.org/10.1016/j.electacta.2012.05.068
Mališ J., Mazúr P., Paidar M. et al. // Int. J. Hydrogen Energy. 2016. V. 41. № 4. P. 2177. https://doi.org/10.1016/j.ijhydene.2015.11.102
Babic U., Schmidt T.J., Gubler L. // J. Electrochem. Soc. 2018. V. 165. № 15. P. J3016. https://doi.org/10.1149/2.0031815jes
Lettenmeier P., Kolb S., Burggraf F. et al. // J. Power Sources. 2016. V. 311. P. 153. https://doi.org/10.1016/j.jpowsour.2016.01.100
Siracusano S., Baglio V., Di Blasi A. et al. // Int. J. Hydrogen Energy. 2010. V. 35. № 11. P. 5558. https://doi.org/10.1016/j.ijhydene.2010.03.102
Siracusano S., Baglio V., Grigoriev S.A. et al. // J. Power Sources. 2017. V. 366. P. 105. https://doi.org/10.1016/j.jpowsour.2017.09.020
Fierro S., Nagel T., Baltruschat H., Comninellis C. // Electrochem. Commun. 2007. V. 9. № 8. P. 1969. https://doi.org/10.1016/j.elecom.2007.05.008
Geiger S., Kasian O., Ledendecker M. et al. // Nat. Catal. 2018. V. 1. № 7. P. 508. https://doi.org/10.1038/s41929-018-0085-6
Lettenmeier P., Wang L., Golla-Schindler U. et al. // Angew. Chemie Int. Ed. 2016. V. 55. № 2. P. 742. https://doi.org/10.1002/anie.201507626
Pushkarev A.S., Pushkareva I.V., Du Preez S.P. et al. // Chemical Problems. 2019. V. 17. № 1. P. 9. https://doi.org/10.32737/2221-8688-2019-1-9-15
Abbott D.F., Lebedev D., Waltar K. et al. // Chem. Mater. 2016. V. 28. № 18. P. 6591. https://doi.org/10.1021/acs.chemmater.6b02625
Богдановская В.А., Тарасевич М.Р., Лозовая О.В. // Электрохимия. 2011. Т. 47. С. 902.
Parthasarathy A., Srinivasan S., Appleby J.A., Martin C.R. // J. Electrochem. Soc. 1992. V. 139. № 9. P. 2530. https://doi.org/10.1149/1.2221258
van der Merwe J., Uren K., van Schoor G., Bessarabov D. // Int. J. Hydrogen Energy. 2014. V. 39. № 26. P. 14212. https://doi.org/10.1016/j.ijhydene.2014.02.096
Amirinejad M., Rowshanzamir S., Eikani M.H. // J. Power Sources. 2006. V. 161. № 2. P. 872. https://doi.org/10.1016/j.jpowsour.2006.04.144
Kadjo A.J.-J., Brault P., Caillard A. et al. // J. Power Sources. 2007. V. 172. № 2. P. 613. https://doi.org/10.1016/j.jpowsour.2007.05.019
Avcioglu G.S., Ficicilar B., Eroglu I. // Int. J. Hydrogen Energy. 2018. https://doi.org/10.1016/j.ijhydene.2018.03.045
Wan Z., Liu S., Zhong Q. et al. // Int. J. Hydrogen Energy. 2018. V. 43. № 15. P. 7456. https://doi.org/10.1016/j.ijhydene.2018.01.091
Wang M., Chen M., Yang Z. et al. // Energy Convers. Manag. 2019. V. 191. P. 132. https://doi.org/10.1016/j.enconman.2019.04.014
Gasteiger H.A., Kocha S.S., Sompalli B., Wagner F.T. // Appl. Catal. B Environ. 2005. V. 56. № 1–2. P. 9. https://doi.org/10.1016/j.apcatb.2004.06.021
Song W., Yu H., Hao L. et al. // Solid State Ionics. 2010. V. 181. № 8–10. P. 453. https://doi.org/10.1016/j.ssi.2010.01.022
Baranov I.E., Nikolaev I.I., Pushkarev A.S. et al. // Int. J. Electrochem. Sci. 2018. V. 13. P. 8673. https://doi.org/10.20964/2018.09.48
Дополнительные материалы отсутствуют.
Инструменты
Российские нанотехнологии