Российские нанотехнологии, 2022, T. 17, № 4, стр. 503-508
НАНОСТРУКТУРИРОВАНИЕ АЛЮМИНИЕВОГО СПЛАВА И ИССЛЕДОВАНИЕ МЕХАНИЧЕСКИХ СВОЙСТВ ПОЛУЧЕННОГО НАНОКОМПОЗИТА Al/C60
В. М. Прохоров 1, *, И. А. Евдокимов 1, А. И. Коробов 2, А. И. Кокшайский 2, Н. И. Одина 2, Н. В. Ширгина 2
1 Технологический институт сверхтвердых и новых углеродных материалов
Москва, Россия
2 Московский государственный университет им. М.В. Ломоносова
Москва, Россия
* E-mail: pvm@tisnum.ru
Поступила в редакцию 05.12.2021
После доработки 05.12.2021
Принята к публикации 10.12.2021
Аннотация
Проведено наноструктурирование алюминиевого сплава AMg6 методом интенсивной пластической деформации путем горячей экструзии заготовки из опрессованного нанокомпозитного порошка, полученного диспергированием в планетарной шаровой мельнице смеси стружки сплава и порошка фуллерита С60. Исследованы структурные особенности полученного нанокомпозита n‑AMg6/С60. Представлены экспериментальные исследования механических характеристик нанокомпозита n-AMg6/С60. Для наноструктурированных композитных образцов измерены кривые напряжения–деформации σ = σ(ε) при циклическом изменении напряжения, приложенного к образцам. В ходе экспериментов в композитных образцах n-AMg6/C60 почти не было обнаружено остаточных деформаций, а кривые напряжения–деформации не содержали зон, соответствующих пластической деформации. Установлено, что обратимая механическая нагрузка–разгрузка образцов n-AMg6/C60 вызывает их упрочнение. Эти данные дополнены измерениями микротвердости и изменений скорости продольных упругих волн при циклическом изменении нагрузки на образце.
ВВЕДЕНИЕ
Одним из современных методов, используемых для улучшения механических физических свойств металлов и сплавов, является наноструктурирование, т.е. формирование наноструктуры во всем объеме материала [1, 2]. В частности, наноструктурирование – известный способ повышения прочностных свойств материалов [3, 4]. В последние несколько лет наблюдается значительный прогресс в разработке методов наноструктурирования, которые приводят к новым сочетаниям свойств, таким как высокая прочность, более высокая твердость, рекордный усталостный ресурс и т.д. [5, 6]. Основными методами наноструктурирования металлов и сплавов являются различные варианты метода интенсивной пластической деформации (ИПД) и метод высокоэнергетической обработки (измельчения до наноразмерного состояния) в шаровой мельнице с последующем горячим прессованием. Эти методы часто сочетаются с методом горячей экструзии [7, 8].
Прочность на растяжение нанокристаллических металлов в 1.5–8 раз выше, чем крупнозернистых металлов [9, 10]. Микротвердость наноструктурированных материалов в 2–7 раз выше, чем у крупнозернистых материалов, причем рост микротвердости подчиняется известному закону Холла–Петча. В частности, изучение микротвердости нанокристаллического сплава Al9.85Mg1.5 [11] показало, что отжиг сплава с размером зерен ~150 нм при 400 К приводит к релаксации границ зерен и их постепенному переходу в равновесное состояние, хотя размер зерен не менялся. Релаксация границ зерен вследствие отжига сопровождалась уменьшением микротвердости от 1.7 до 1.4 ГПа.
В [12, 15] были отмечены необычные упругие свойства нанокристаллических металлов, обусловленные не только малым размером зерен, но и состоянием границ раздела.
Исследования повышения механических характеристик алюминиевых сплавов путем наноструктурирования проводились во многих работах [16–21], в которых отмечались различные аномалии механического поведения.
При изготовлении промышленных изделий используется более 150 алюминиевых сплавов. Значительный объем среди них занимает сплав AMg6, относящийся к системе Al–Mg–Mn. Сплав содержит 93.68% алюминия, 5.8–6.8% магния и 0.5–0.8% марганца и других примесей [3].
Сплав хорошо сваривается при комнатных и более высоких температурах, он сочетает в себе хорошие прочностные и пластические характеристики. Этот набор свойств способствовал широкому применению данного сплава в аэрокосмической промышленности, строительстве и автомобилестроении, коррозионная стойкость в различных средах, включая морскую воду, объясняет его успешное применение в судостроении. Для улучшения механических свойств алюминиевых сплавов их предварительно подвергают механической деформации и термической обработке. Однако трудно повысить прочностные характеристики магнийсодержащего AMg6 путем закалки, так как этот сплав не поддается термическому упрочнению.
Более высокие значения механических характеристик в нанокомпозитном углеродисто-упрочненном сплаве AMg6, полученном путем измельчения в шаровой мельнице с последующим прессованием, были получены в [20–22]. Относительное удлинение при разрыве нанокомпозита AMg6 увеличено до 10.5–14.1% при более высокой твердости 1.5–1.7 ГПа.
В данной работе описана процедура наноструктурирования алюминиевого сплава AMg6 и представлены результаты сравнительных экспериментальных исследований механических характеристик сплава и нанокомпозита на его основе n-AMg6/С60 при испытаниях на растяжение, а также влияние деформационного упрочнения на эти характеристики при многоцикловых процессах нагружения–разгрузки вплоть до разрушения образца.
МЕТОДЫ
Наноструктурирование сплава. В качестве матричного материала для получения наноструктурного композиционного материала, модифицированного углеродными наноструктурами, применяли деформационно-упрочняемый алюминиевый сплав AMg6. Сплав имеет следующий химический состав: Mg – 6.124, Mn – 0.5977, Fe – 0.351, Si – 0.310, Zn – 0.203, Ti – 0.0843, Cu – 0.086%, Al – баланс.
Наноструктурный композит n-AMg6/C60 получен методом совместного механолегирования исходных компонентов в высокоэнергетической планетарной шаровой мельнице. Смесь стружки сплава AMg6 с добавлением 0.3 мас. % фуллерита С60 обрабатывали в предварительно футерованных матричным сплавом размольных контейнерах в течение 60 мин. Для поддержания требуемого теплового режима процесса механолегирования размол проводили циклами по 5 мин с перерывом 3 мин. По данным рентгенофазового анализа и сканирующей электронной микроскопии полученные порошковые смеси состоят из наночастиц композита n-AMg6/C60 размером 40–60 нм, объединенных в агломераты размером 200–500 мк.
Наноструктурный композит n-AMg6/C60 предварительно компактировали в цилиндрические брикеты диаметром 180 мм при температуре 250°С и давлении 200–300 МПа. Полученный компакт подвергали прямой горячей экструзии при температуре 290°С и степени деформации 5.2. Высокая степень деформации и низкая температура экструзии обеспечивают сохранение наноструктурного состояния композита при термобарической обработке. Фуллерен С60, располагаясь по границам зерен алюминия, также обеспечивает замедление процессов рекристаллизации и межзеренной диффузии.
На рис. 1 представлены изображения, полученные с помощью растрового электронного микроскопа (РЭМ)), частиц нанокомпозитного порошка n-AMg6/C60 после измельчения, а также микроструктура образцов исходного сплава AMg6 (рис. 1б) и наноструктурного n-AMg6/С60 после экструзии (рис. 1в).
Рис. 1.
РЭМ-изображение частиц нанокомпозитного порошка n-AMg6/C60 после механолегирования (а); микроструктура образцов исходного сплава AMg6 (б) и наноструктурного n-AMg6/С60 после экструзии (в).
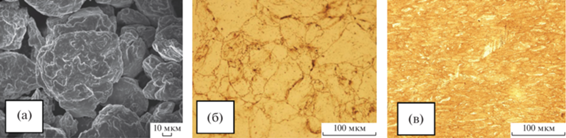
Как видно из рис. 1в, зерна алюминия после экструзионного деформирования ориентированы вдоль оси экструзии и между зернами нет пор. Отметим, что микроструктура экструдированных наноструктурных композитов n-AMg6/C60 наследует морфологию порошков после их механолегирования. Также из рис. 1б и 1в видно, что размер зерен в экструдированном материале соответствует размерам агрегатов и агломератов в порошке нанокомпозита. Данное свойство за счет изменения структуры порошков на стадии их подготовки позволяет управлять свойствами конечного продукта (прочность, пластичность) [23, 24].
Наноструктурированные образцы для исследования были изготовлены из экструдированной заготовки, вид и размеры которой представлены на рис. 2а. Образцы по форме и размерам соответствовали ГОСТу для каждого вида испытаний и были вырезаны из разных областей экструдированного стержня.
Рис. 2.
Общий вид заготовки наноструктурого сплава n-AMg6/С60 после экструзии (а) и образцы для механических испытаний (б).
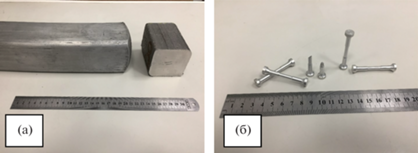
Согласно исследованию методом гидростатического взвешивания плотность наностируктурированных образцов составляет 2.63 ± 0.02 г/см3, что соответствует 99% удельной плотности сплава AMg6. Плотность образцов измеряли на весах KERN-770-60, оснащенных консолью Sartorius YDK 01 LP.
Испытания на растяжение проводили с использованием многоцелевой напольной системы электромеханических испытаний Instron 5982 (Германия). Когда образцы, полученные методом экструзии, подвергались испытанию на растяжение, направление нагрузки совпадало с осью экструзии. Скорость растяжения составляла 0.2 мм/мин.
Свойства при растяжении (предел прочности) оценивали для образцов стандартной формы (диаметр шейки 4 мм и длина 50 мм), полученных из предшественника AMg6 и экструдированного композита n-AMg6/C60 (рис. 2б).
Испытания на циклические растяжения с ультразвуковыми измерениями. Механическое устройство, создающее обратимые циклические деформации растяжения в исследуемых образцах, было сконструировано нами на базе 20-тонного пресса (производства компании MATRIX); схема и описание устройства приведены в [25]. В устройстве реализованы статический метод измерения кривой напряжение–деформация (σ–ε) при обратимом изменении напряжения в исследуемом образце и импульсный метод измерения скорости и поглощения объемных акустических волн. Измерительная система включала в себя автоматизированную ультразвуковую систему Ritec RAM-5000, четырехканальный цифровой осциллограф DS09104A и механическое устройство, создающее контролируемые обратимые деформации растяжения в исследуемом материале. Ультразвуковая система позволяла измерять зависимость скоростей ультразвуковых волн от деформации образца. В работе зависимость скорости продольных упругих волн V от деформации образца измеряли импульсным методом “отражения” с использованием формулы V = 2L/τ, где L – длина образца, а τ – время двойного прохождения акустического импульса через образец.
Микротвердость образцов n-AMg6/C60, подвергнутых циклическим деформациям растяжения, измеряли в соответствии с ГОСТ 2999-75 с помощью твердомера DuraScan20 путем приложения нагрузки 50 г на индентор Виккерса в течение 12 с. Измерения микротвердости были выполнены на металлографических срезах, вырезанных из разных частей образца n-AMg6/C60, подвергнутого циклической деформации вплоть до разрушения (рис. 3): из центральной части гантелеобразного образца, которая испытывала значительную пластическую деформацию при нагружении вплоть до разрушения (обозначена цифрой 2 на рис. 3) и из части 1, которая была почти ненапряженной при циклическом нагружении–разгрузке. Микротвердость измеряли в пяти точках образца, вырезанного из части 2, которые были расположены по диаметру (8 мм) через 2 мм друг от друга, и в пяти точках, которые были расположены на поверхности головки гантели диаметром 25 мм через 6 мм друг от друга (часть 1 на рис. 3). Значения микротвердости были усреднены по результатам пяти измерений.
РЕЗУЛЬТАТЫ
Предел прочности. На рис. 4 представлены типичные диаграммы деформации образцов исходного сплава AMg6 и нанокомпозита n-AMg6/С60. Из приведенных на рисунке данных видно, что условный предел текучести (σ0.2) при растяжении наноструктурных сплавов n-AMg6/С60 увеличился от значения 210 МПа (для исходного AMg6) до 640 МПа. Отметим, что наряду с увеличением прочности наблюдается резкое падение пластичности наноструктурного n-AMg6/С60. Такое поведение характерно для наноструктурных материалов и связано с затруднением осуществления механизмов межзеренного проскальзывания и миграции дислокаций в объеме материала.
Рис. 4.
Графики напряжение–деформация образцов наноструктурного композита n-AMg6/С60 (1) и исходного сплава AMg6 (2).
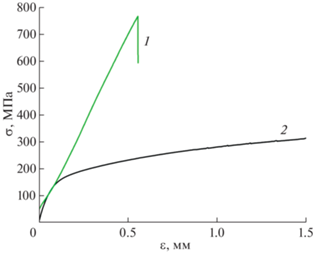
Исследования механических характеристик образцов исходного AMg6 были проведены в [26]. Измеренные механические свойства образцов материалов, исследуемых в настоящей работе, такие как предел текучести, прочность при растяжении, предельная деформация, совпали с данными [26] в пределах статистической погрешности.
Влияние статических обратимых механических деформаций. Исследовали два гантелеобразных образца (рис. 3): AMg6 (образец 1) и n-AMg6/С60 (образец 2). Каждый образец циклически растягивали на устройстве, создающем обратимые деформации растяжения вплоть до разрыва в течение более трех часов. Протоколы испытаний приведены на рис. 5.
Рис. 5.
Временные характеристики процесса нагружения–разгрузки (а, б) и соответствующие результаты измерения кривых напряжение–деформация, σ = σ(ε) (в, г), для двух образцов при циклическом изменении напряжения.
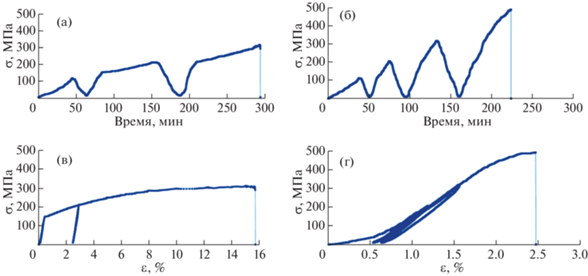
На рис. 5а и 5б представлены временные характеристики процесса нагружения–разгрузки, а на рис. 5в и 5г – соответствующие результаты измерения кривых напряжение–деформация, σ = σ(ε), для двух образцов при циклическом изменении напряжения. В процессе обратимой нагрузки–разгрузки остаточные деформации, наблюдаемые при нулевом растягивающем напряжении (σ = 0), практически отсутствовали для обоих образцов.
Для образца 1 разрушение произошло после двух циклов нагрузки–разгрузки при σ ~ 300 МПа и ε ~ 15.5%. Образец 2 подвергся разрушению после трех циклов нагрузки–разгрузки при σ ~ 470 МПа и ε ~ 2.5%.
Разница в значениях напряжений и деформаций, соответствующих разрушению образцов 1 и 2, указывает на значительное упрочнение материала в образце 2 по сравнению с образцом 1. Для обоих образцов не наблюдалось образования характерной “шейки” в области, близкой к перелому. Этот факт свидетельствует о хрупком разрушении образцов. Видно, что наноструктурированный образец является более прочным и хрупким, чем исходный.
Скорости продольных упругих волн. Одновременно с измерением кривой напряжения–деформации в ходе обратимых циклов нагружения–разгрузки импульсным методом для образцов 1 и 2 измеряли зависимости скорости V продольных упругих волн от изменения растягивающего напряжения σ (рис. 6а, 6б) и от деформации ε (рис. 6в, 6г). После двух циклов нагрузки–разгрузки скорость увеличилась на 0.2%, а после 12 – она увеличилась почти на 0.5% по сравнению с ненагруженным образцом. В момент разрушения скорость продольных упругих волн в образце уменьшилась примерно на 16% по сравнению с ненагруженным образцом.
Рис. 6.
Зависимости скорости V продольных объемных акустических волн от изменения растягивающего напряжения σ (а, б) и деформации (в, г).
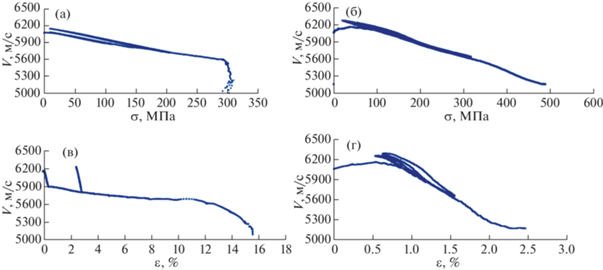
Микротвердость. Для ненапряженной части 1 n-AMg6/C60 измеренные значения микротвердости Н составили 1.29 ± 0.03 ГПа. Для части 2 n‑AMg6/C60 среднее значение составляло Hср = = 1.74 ± 0.04 ГПа. Было измерено распределение микротвердости по диаметру, перпендикулярному оси образца 1 (табл. 1). Можно видеть, что по краям диаметра микротвердость больше по сравнению с внутренней областью напряженной части 2. Это связано с тем, что при обработке образца на токарном станке внешняя сторона деформированной части образца подвергается дополнительной механической нагрузке, что вызывает дополнительное упрочнение цилиндрической поверхности образца.
Таблица 1.
Зависимость микротвердости H образца n‑AMg6/C60 от координаты для деформированной части 2
Координата измерения по диаметру, мм (рис. 4) | H, ГПа |
---|---|
0.5 | 1.75 ± 0.07 |
2.0 | 1.72 ± 0.03 |
4.0 | 1.75 ± 0.04 |
6.0 | 1.69 ± 0.03 |
7.5 | 1.78 ± 0.05 |
ЗАКЛЮЧЕНИЕ
Проведено наноструктурирование алюминиевого сплава AMg6 и представлены результаты сравнительных экспериментальных исследований сплава и нанокомпозита на его основе n‑AMg6/С60, микротвердости, упругих характеристик, механических характеристик при испытаниях на растяжение, а также влияние деформационного упрочнения на эти характеристики при многоцикловых процессах нагружения–разгрузки вплоть до разрушения образца. Для наноструктурных композитных образцов n-AMg6/C60 были измерены кривые напряжения–деформации σ = σ(ε) при циклическом изменении напряжения, приложенного к образцам. В ходе экспериментов в композитных образцах n-AMg6/C60 почти не было обнаружено остаточных деформаций, а кривые напряжения–деформации не содержали зон, соответствующих пластической деформации. Установлено, что обратимая механическая нагрузка–разгрузка образцов n-AMg6/C60 вызывает их упрочнение.
Работа выполнена с использованием оборудования ЦКП ФГБНУ ТИСНУМ “Исследования наноструктурных, углеродных и сверхтвердых материалов”.
Список литературы
Валиев Р.З., Александров И.В. Объемные наноструктурные металлические материалы: получение, структура и свойства. М.: ИКЦ “Академкнига”, 2007. 398 с.
Valiev R.Z., Zhilyaev A.P., Langdon T.G. Bulk Nanostructured Materials: Fundamentals and Applications. John Wiley & Sons, Inc., 2014. 456 p.
Конструкционные материалы: Справочник / Под общ. ред. Б.Н. Арзамасова. М.: Машиностроение, 1990. 688 с.
Langdon T.G. // Rev. Adv. Mater. Sci. 2012. V. 31. P. 1.
Langdon T.G. // Acta Mater. 2013. V. 61. P. 7035. https://doi.org/10.1016/j.actamat.2013.08.018
Neiman G.W., Weertman J.R., Siegel R.W. // J. Mater. Res. 1991. V. 6. № 5. P. 1012. https://doi.org/10.1557/JMR.1991.1012
Рыжонков Д.И., Лёвина В.В., Дзидзигурди Э.Л. // Наноматериалы. М: БИНОМ, 2008. С. 18.
Glezer A.M. // Phys.-Usp. 2012. V. 55. № 5. P. 522. https://doi.org/10.3367/UFNr.0182.201205h.0559
Andrievski R.A., Glezer A.M. // Phys.-Usp. 2009. V. 52. № 4. P. 315. https://doi.org/10.3367/UFNr.0179.200904a.0337
Bezruchko G.S., Razorenov S.V., Popov M.Yu. // Tech. Phys. 2014. V. 84. № 3. P. 378. https://doi.org/10.1134/S1063784214030062
Valiev R.Z., Chmelik R., Bordenux F. et al. // Scripta Metall. Mater. 1992. V. 27. № 7. P. 855.
Agnew S.R., Weertman O.K. // Mater. Sci. Eng. A. 1998. V. 242. № 1–2. P. 174.
Vinogradov A., Nagasaki S., Patlan V. et al. // Nanostructured Materials. 1999. V. 11 (7). P. 925. https://doi.org/10.1016/S0965-9773(99)00392-X
Клевцов Г.В., Валиев Р.З., Исламгалиев Р.К. и др. // Фундаментальные исследования. 2012. № 2–3. С. 391.
Голубовский Е.Р., Исламгалиев Р.К., Волков М.Е. и др. // Технология легких сплавов. 2013. № 4. С. 92.
Prokhorov V.M., Blank V.D., Bagramov R.H. et al. // AIP Conf. Proc. 2013. V. 1569. P. 389. https://doi.org/10.1063/1.4934461
Prokhorov V.M., Gromnitskaja E.L. // Phys. Solid State. 2018. V. 60. № 4. P. 769. https://doi.org/10.1134/S106378341804025X
Khalikova G.R., Korznikova G., Nazarov K.S. et al. // Lett. Mater. 2020. V. 10 (4). P. 475. https://doi.org/10.22226/2410-3535-2020-4-475-480
Bobruk E.V., Lábár J.L., Gubicza J. et al. // Mater. Res. Lett. 2021. V. 9 (11). P. 475. https://doi.org/10.1080/21663831.2021.1976293
Lvova N.A., Evdokimov I.A., Perfilov S.A. // Adv. Mater. Res. 2015. V. 1119. P. 9. https://doi.org/10.4028/www.scientific.net/AMR.1119.9
Evdokimov I.A., Perfilov S.A., Pozdnyakov A.A. et al. // Inorg. Mater.: Appl. Res. 2018. V. 9 (3). P. 472. https://doi.org/10.1134/S2075113318030139
Евдокимов И.А., Хайруллин Р.Р., Баграмов Р.Х. и др. // Изв. вузов. Порошковая металлургия и функциональные покрытия. 2020. № 3. С. 76. https://doi.org/10.17073/1997-308X-2020-3-76-84
Volkov A.D., Kokshaiskii A.I., Korobov A.I. et al. // Acoustical Physics. 2015. V. 61. P. 651. https://doi.org/10.1134/S1063771016050067
Korobov A.I., Kokshaiskii A.I., Prokhorov V.M. et al. // Phys. Solid State. 2016. V. 58. P. 2472. https://doi.org/10.1134/S106378341612012X
Korobov A.I., Shirgina N.V., Kokshaiskii A.I. et al. // Acoustical Physics. 2019. V. 65. P. 151. https://doi.org/10.1134/S1063771019020064
Korobov A.I., Shirgina N.V., Kokshaiskii A.I. et al. // Acoustical Physics. 2018. V. 64. № 4. P. 415. https://doi.org/10.1134/S1063771018030119
Дополнительные материалы отсутствуют.
Инструменты
Российские нанотехнологии