Нефтехимия, 2019, T. 59, № 1, стр. 76-82
КАТАЛИТИЧЕСКИЕ СИСТЕМЫ НА ОСНОВЕ ГАЛОГЕНИДА МЕТАЛЛА И ЧЕТВЕРТИЧНОЙ АММОНИЕВОЙ СОЛИ В РЕАКЦИИ КАРБОКСИЛИРОВАНИЯ 1,2-ЭПОКСИЦИКЛОПЕНТАНА
Г. Ю. Тараненко 1, Г. В. Рыбина 1, *, С. С. Среднев 1, А. Е. Мешечкина 1, А. В. Тарасов 1
1 Ярославский государственный технический университет
Ярославль, Россия
* E-mail: rybinagv@ystu.ru
Поступила в редакцию 18.01.2018
После доработки 26.07.2018
Принята к публикации 18.03.2018
Аннотация
Представлены результаты исследования реакции карбоксилирования 1,2-эпоксициклопентана в циклопентенкарбонат (ЦПК) на различных каталитических системах. Установлено, что наиболее эффективно реакция протекает в присутствии кристаллогидрата хлорида (бромида) кобальта или никеля и четвертичной аммониевой соли – ТЭАБ, ТБАБ. Синтез ЦПК рекомендуется проводить под давлением СО2 не ниже 3.5 МПа и температуре 140–150°С, без растворителя или в среде растворителя, в качестве которого можно использовать целевой ЦПК, ДМФА или N-МП, при массовой доле 1-эпоксициклопентана в исходной смеси не ниже 25%. Эти условия позволяют в течение 2–4 ч получить ЦПК с селективностью 97–99% при практически полной конверсии эпоксида. Показана возможность повторного использования найденной каталитической системы.
Циклические органические карбонаты (ЦК) являются перспективными продуктами промышленного органического синтеза. Несмотря на широкие области их практического использования, сейчас преимущественно производятся низкомолекулярные ЦК, такие как этилен- и пропиленкарбонат [1].
В последние десятилетия исследователи все большее внимание уделяют синтезу алициклических ЦК, в частности циклопентенкарбонату (ЦПК). Возрастающий интерес к ЦПК вызван возможностью его применения как в качестве высокоэффективного безхлорного растворителя [2], так и мономера в синтезе ряда уретансодержащих полимеров, обладающих повышенной прочностью, биоразлагаемостью и получаемых по экологически чистой безизоцианатной технологии [3].
Известные способы получения ЦПК на основе циклопентена [4] и 1,2‑циклопентандиола [5, 6] имеют существенные недостатки: токсичность используемых реагентов, низкий выход ЦПК и образование значительного количества побочных продуктов. Поэтому возможность получения ЦПК карбоксилированием 1,2‑эпоксициклопентана (ЭЦП) можно рассматривать как наиболее перспективный, конкурентоспособный и экологичный (так называемая технология “зеленой химии”) метод его синтеза.
Реакция карбоксилирования ЭЦП может протекать в основном по двум направлениям:
Образование ЦПК или полициклопентенкарбоната во многом определяется природой катализатора.
Рядом автором описано взаимодействие ЭЦП с СО2 в присутствии четвертичных аммониевых солей (ЧАС) – ТЭАБ, ТМАБ, ТБАБ [7, 8], а также бинарной каталитической системы, состоящей из ТЭАБ и бромида (иодида) щелочного металла [9]. Несмотря на высокий выход ЦПК, достигающий 92%, катализатор теряет свою активность вследствие частичного разложения в условиях реакции.
Для карбоксилирования ЭЦП предложен ряд органометалличестких катализаторов на основе цинка [4, 6, 10 ], применение которых приводит к образованию полициклопентенкарбоната с выходом 65–99%. При 25–70°С и давлении СО2 0.1–5.0 МПа за 12–24 ч конверсия ЭЦП достигает не более 48%. Конверсия окисида циклопентена до 56% получена в этих же условиях за 3–6 ч при использовании бинарных саленовых катализаторов (salen)CоCl/PPNN3 и (salen)CrCl/ТБАХ, однако при этом образуется ЦПК с выходом 68–83% [10].
Использование порфириновых комплексов Mg, Co, Ni, Cu, Zn и Al с со-катализатором (ЧАС) [11] или бифункционального катализатора 5,10,15,20-(порфирин)AlCl/N-метилимидазол [12, 13] позволяет получать ЦПК с выходом 54–90%. Реакция протекает в течение 60 ч при температуре 90–120°С и давлении 1–4.8 МПа в среде апротонного растворителя – ГМФА, ДМФА или целевого ЦПК.
Таким образом, взаимодействие ЭПЦ с диоксидом углерода в присутствии большинства из известных катализаторов протекает с невысоким выходом ЦПК или конверсией ЭЦП, характеризуется большой продолжительностью синтеза, необходимостью использования растворителя, сложностью синтеза катализатора и/или невозможностью его регенерации.
Цель данной работы – поиск и исследование эффективных каталитических систем для синтеза ЦПК на основе ЭЦП и СО2.
ЭКСПЕРИМЕНТАЛЬНАЯ ЧАСТЬ
Реакция карбоксилирования ЭЦП проводилась в титановом реакторе объемом 60 см3, снабженным рубашкой для подачи теплоносителя (глицерина). На крышке реактора имеются манометр, вентили для отбора проб и подачи СО2; в днище реактора – карман для датчика термопары. Исходные 1,2-эпоксициклопентан, растворитель (20 см3) и компоненты катализатора загружали в продутый диоксидом углерода реактор при комнатной температуре. Постоянное давление СО2 поддерживали с помощью редуктора, установленного на линии подачи газа из баллона. Заданную температуру поддерживали с помощью термостата с точностью ±1.0°С. При достижении режимной температуры в реакторе включалась механическая качалка, обеспечивая интенсивность перемешивания не менее 140 об./мин. При проведении опыта в герметичные ампулы периодически отбирали на анализ пробы из реактора. Время включения качалки принималось за начало реакции.
Продукты реакции анализировали на газовом хроматографе “Хроматек-Кристалл 5000.2” с использованием пламенно-ионизационного детектора и капиллярной колонки (длиной 30 м, диаметром 0.32 мм), заполненной сорбентом CR--WAXms. Температуру колонки программировали от 60 до 160°С со скоростью подъема 10°С в минуту, расход газа-носителя водорода 40 см3/мин. Объем вводимой пробы 0.2 мкл. Внутренний стандарт – ундеканол-1.
Растворители – ДМФА, ДМАА, N-МП, ацетонитрил, формамид марки “ч” перед синтезом подвергались ректификации, содержание основного вещества не менее 99.0% по данным ГЖХ.
ЭЦП получен окислением циклопентена водным раствором пероксида водорода известным методом [14] и выделен ректификацией с массовой долей 99.5%; остаточное содержание воды не более 0.3%, Ткип = 102°С, $n_{d}^{{20}}$ = 1.4336.
Газообразный диоксид углерода соответствовал ГОСТ 8050-85.
Тетраэтиламмоний бромид – марка “ч”, ГОСТ, ТУ 71-91-0. Массовая доля основного вещества 99.0%.
CoCl2 · 6H2O – марка “ч”, ГОСТ 4525-77, KI – марка “х. ч.”, ГОСТ 4232-74, AlCl3 ∙ 6H2O – марка “ч”, ГОСТ 3759-75, СrCl3 ∙ 6H2O – марка “ч”, ГОСТ 4473-78, SnCl2 ∙ 2H2O – марка “ч”, ГОСТ 36-78, NiCl2 ∙ 6H2O – марка “ч”, ГОСТ 4038-79.
Циклопентенкарбонат выделен методом ректификации с массовой долей 99.7%, Ткип = = 170°С/2 мм рт. cт., Тпл= 32.5–35°P.
Структура ЦПК подтверждена методами ЯМР 1Н-, ЯМР 13С- и масс-спектроскопии. ЯМР 1H- и 13C-спектры регистрировали на спектрометре “Bruker DRX400”. Растворитель: ДМСО-d6, внутренний стандарт – ТМС.
ИК-спектры регистрировали на спектрометре “Фурье RX-1 Perkin Elmer” с длиной волны 700−4000 см–1. Образец анализировали в виде суспензии в вазелиновом масле, пластины из KBr. Масс-спектры регистрировали на ВЭЖХ/МС спектрометре “Shimadzu Prominence LCMS-2020”, оснащенным хроматографической колонкой (Т = = 40°P, элюент – ацетонитрил) и масс-спектрометром (LCMS-2020, m/z диапазон 0–2000, режимы ионизации: ESI/ACPI)
ИК-спектр, ν/см–1: 1780 (P=O), 1172, 1112, 1047 (P–O–P). Спектр ЯМР 1H (400 МГц, δ, м.д.): 1.45–1.62 м (1H, H5), 1.62–1.77 м (3H, H5, H4, H6), 1.88–2.00 м (2H, H4, H6), 5.12–5.20 м (2H, H3a, H6a). Спектр ЯМР 13C (75 МГц, δ, м.д.): 21.38 (1C, C5), 32.44 (2C, C4, C6), 81.89 (2C, C3a, C6a), 155.07 (1C, P=O). Масс-спектр (ESI), m/z (Iотн (%)): 127 [M]+. Установлено, что в присутствии каталитической системы CoCl2 ∙ 6H2O –ТЭАБ образуется цис‑изомер ЦПК.
РЕЗУЛЬТАТЫ И ИХ ОБСУЖДЕНИЕ
Ранее нами была предложена каталитическая система, состоящая из галогенида кобальта или никеля и ДМФА, которая показала высокую эффективность для синтеза циклических карбонатов на основе моноалкилзамещенных оксидов этилена С5–С16, моноэпоксидов диенов С4, С8, эпихлоргидрина и оксида стирола [15]. Поэтому представляло интерес использовать ее в реакции карбоксилирования ЭЦП. Для сравнения ее активности поставлены опыты в присутствии катализаторов ТЭАБ и KI (табл. 1, строка 2), которые наиболее часто используют в промышленных синтезах низших ЦК [4]. Реакцию карбоксилирования ЭЦП проводили в среде ДМФА и в его отсутствие.
Таблица 1.
Влияние растворителя и природы катализатора на показатели синтеза циклопентенкарбоната. Температура 150°С, давление углекислого газа 2 МПа, массовая доля ЭЦП в исходной смеси 2.9 моль/дм3, концентрация катализатора 0.0345 моль/моль ЭЦП, продолжительность реакции 180 мин
№ | Катализатор | Растворитель | Конверсия ЭЦП, % | Селективность по ЦПК, % |
---|---|---|---|---|
1 | отс. | ДМФА | 5.55 | 35.11 |
2 | CoCl2 · 6H2О | ДМФА | 86.03 | 48.07 |
3 | отс. | 12.53 | 2.33 | |
4 | ТЭАБ | ДМФА | 90.12 | 91.34 |
5 | отс. | 66.46 | 89.53 | |
6 | KI | ДМФА | 22.55 | 8.71 |
7 | отс. | 3.14 | 3.35 |
Образование ЦПК протекает с высокой селективностью 89.5% в отсутствие растворителя только при катализе ТЭАБ (табл. 1, строка 5). В этих же условиях KI и СоCl2 ∙ 6H2O практически не катализируют превращение ЭЦП в ЦПК: селективность процесса крайне низкая – 2 и 3% при конверсии эпоксида 3 и 12% соответственно (табл. 1, строки 3, 7). Вероятно, это связано с низкой растворимостью галогенидов металлов в окиси циклопентена.
Оказалось, что ДМФА способен катализировать взаимодействие СО2 с ЭЦП. За 3 ч конверсия эпоксида составляет 5.5% при селективности по ЦПК 35% (табл. 1, строка 1). Ранее каталитическую активность ДМФА в реакциях карбоксилирования алифатических эпоксидов отметили авторы работы [16].
Показано, что эффективность действия катализаторов при проведении реакции в среде ДМФА возрастает. Так, в присутствии ТЭАБ при температуре150°С и давлении СО2 2 МПа за 3 ч конверсия ЭЦП составила 90.1% при селективности по ЦПК 91.3% (табл. 1, строка 4). При катализе хлоридом кобальта степень превращения ЭЦП достигла 87%, но селективность остается низкой, не более 48% (табл. 1, строка 2). Использование в качестве катализатора синтеза ЦПК KI, даже в среде ДМФА, крайне не эффективно (табл. 1, строка 6).
Таким образом, применение СоCl2 ∙ 6H2O в среде ДМФА для синтеза ЦПК из ЭЦП и СО2 не позволило достичь столь же высоких показателей, как в реакции карбоксилирования ациклических эпоксидов С5–С16 [15]. Это, по-видимому, связано с более низкой реакционной способностью окисей циклоолефинов в этой реакции по сравнению с алифатическими эпоксидами, что было отмечено в ряде работ [10, 17 ].
Известно, что бинарные каталитические системы рассматриваются в литературе как наиболее эффективные в реакциях карбоксилирования эпоксидов различного строения [4]. Они включают кислоту Льюиса (галогенид металла) и нуклеофильный компонент (обычно ЧАС). Поэтому нами были опробованы бинарные каталитические системы на основе галогенидов хрома, алюминия, кобальта и никеля в сочетании с четвертичными солями аммония (табл. 2). Органометаллические катализаторы на основе этих металлов предложены рядом авторов [18, 17, 16 ] для реакции карбоксилирования алициклических С6–С12-эпоксидов.
Таблица 2.
Влияние природы галогенида металла и растворителя на показатели синтеза циклопентенкарбоната в присутствии бинарной каталитической системы с ТЭАБ. Температура 150°С, давление CO2 2.0 МПа, начальная концентрация ЭЦП 2.9 моль/дм3, концентрация катализатора MeX 0.0041 моль/моль ЭЦП, мольное соотношение катализаторов MeX : ТЭАБ 1 : 4, продолжительность реакции 240 мин
№ | Галогенид металла | Растворитель | Конверсия ЭЦП, % | Селективность, % | ||
---|---|---|---|---|---|---|
ЦПК | ЦПДол | прочие | ||||
1 | AlCl3 ∙ 6H2O | ДМФА | 73.78 | 22.55 | 14.10 | 63.35 |
2 | СrCl3 ∙ 6H2O | ДМФА | 96.36 | 87.18 | 12.80 | 0.02 |
3 | SnCl2 ∙ 2H2O | ДМФА | 96.41 | 83.29 | 16.45 | 0.26 |
4 | NiCl2 ∙ 6H2O | ДМФА | 97.16 | 96.88 | 2.77 | 0.35 |
5 | NiBr2 ∙ 3H2O | ДМФА | 98.80 | 96.28 | 2.43 | 1.29 |
6 | СоCl2 ∙ 6H2O | ДМФА | 99.71 | 97.15 | 2.81 | 0.04 |
7 | N-МП | 99.41 | 96.01 | 2.17 | 1.82 | |
8 | ДМАА | 87.54 | 96.26 | 0.72 | 1.57 | |
9 | Формамид | 69.00 | 94.47 | 1.27 | 4.26 | |
10 | Ацетонитрил | 31.49 | 96.80 | 2.47 | 0.73 | |
11 | ЦПК | 99.63 | 97.84 | 2.11 | 0.05 | |
12 | отс.1) | 98.30 | 98.11 | 0.81 | 1.08 | |
13 | ДМФА2) | 99.12 | 96.84 | 3.03 | 0.13 |
Анализ полученных результатов (табл. 2) показал, что для направленного синтеза ЦПК наиболее активны каталитические системы на основе галогенида кобальта (или никеля) и ТЭАБ (или ТБАБ) как в среде растворителя: ДМФА, N-МП, так и в его отсутствии (табл. 2, строки 4–7, 12, 13). Такая бинарная каталитическая система позволила при температуре 150°С и давлении 2 МПа достичь конверсии ЭЦП свыше 99% при селективности по ЦПК до 97%. Данные по влиянию природы растворителя на показатели реакции карбоксилирования (табл. 2, строки 6–11), (табл. 1) показывает его существенное воздействие на скорость реакции циклоприсоединения, что неоднократно отмечали и другие авторы [10]. По-видимому, растворитель не только изменяет физико-химические свойства реакционной среды, но и является частью каталитической системы.
Как и ожидалось, при использовании кристаллогидратов солей металлов побочной реакцией, при карбоксилировании, является гидролиз ЭЦП с образованием 1,2‑циклопентадиола (ЦПДол, табл. 2), который затрудняет выделение ЦПК из реакционной массы. Кроме этого, в продуктах синтеза ЦПК отмечено наличие циклопентанона, образующегося при изомеризации ЭЦП в присутствии кислот Льюиса [19], и галогенгидринов, образование которых мы также наблюдали при карбоксилировании оксида дивинила [15]. Полициклопентенкарбонат в реакционной смеси не обнаружен.
При исследовании влияния начальной концентрации ЭЦП на показатели синтеза ЦПК в присутствии каталитической системы из CoCl2 ∙ 6H2O и ТЭАБ в среде ДМФА (рис. 1) установлено, что с увеличением содержания ЭЦП в исходной смеси до 2 моль/дм3 происходит быстрое возрастание конверсии эпоксида и селективности по ЦПК, за 240 мин они достигают 93.2 и 97.1%, соответственно. Дальнейшее повышение начальной концентрации ЭЦП приводит лишь к медленному росту конверсии ЭЦП, и при значении С0(ЭЦП), равном 8.93 моль/дм3 (синтез без растворителя), конверсия эпоксида составила 98.3% при селективности по ЦПК 98.1%. По-видимому, образующийся в ходе реакции ЦПК, способствует активации взаимодействия ЭЦП с СО2. На это указывают также высокие показатели синтеза циклокарбоната в среде целевого ЦПК и в отсутствии растворителя (табл. 2, строки 11, 12). Дальнейшее исследование осуществляли при проведении реакции карбоксилирования ЭЦП в отсутствии растворителя.
Рис. 1.
Влияние начальной концентрации ЭЦП на ее конверсию и селективность по ЦПК. Температура 150°С; давление СО2 2.0 МПа; мольное соотношение CoCl2 ∙ 6H2O : ТЭАБ = 1 : 1; концентрация CoCl2 ∙ 6H2O 0.0345 моль/моль ЭЦП; растворитель ДМФА, время реакции 240 мин. 1 – Селективность по ЦПК, %; 2 – конверсия ЭЦП, %
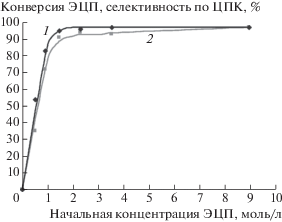
Исследовано влияние концентрации компонентов каталитической системы на показатели синтеза ЦПК (рис. 2), при постоянном начальном мольном соотношении CoCl2 ∙ 6H2O : ТЭАБ = 1 : 1. Установлено, что с увеличением концентрации каталитической системы CoCl2 ∙ 6H2O–ТЭАБ от 0.0044 до 0.0087 моль/моль ЭЦП, при мольном соотношении компонентов 1/1, конверсия ЭЦП и селективность по ЦПК возрастают, достигая за 240 мин максимальной величины 98.5–99.2%. При дальнейшем повышении содержания катализатора в реакционной смеси до 0.0348 моль/моль ЭЦП эти показатели процесса практически не изменяются (кривые 1, 2), однако наблюдается снижение выхода циклопентандиола (кривая 4) и возрастает доля продуктов изомеризации эпоксида и др. Необходимо отметить, что продолжительность реакции (240 или 120 мин) оказывает влияние только на конверсию эпоксида (кривые 1 и 3), селективность по ЦПК в течение всей реакции не изменяется (кривая 2, линия и точки).
Рис. 2.
Влияние концентрации компонентов каталитической системы на конверсию ЭЦП; селективность по ЦПК и ЦПДол. Температура 150°С; давление СО2 2.0 МПа; начальная концентрация ЭЦП 8.93 моль/дм3, мольное соотношение CoCl2 ∙ 6H2O : : ТЭАБ = 1 : 1, без растворителя. Обозначения: конверсия ЭЦП, %: 1 – за 240 мин; 3 – за 120 мин; селективность, %: 2 – по ЦПК – линия – за 240 мин, точки – за 120 мин, 4 – по ЦПДол за 240 мин.
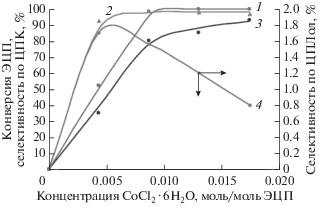
Полагая, что исходные компоненты системы первоначально образуют каталитический комплекс(ы), активирующий реакцию карбоксилирования было исследовано влияние мольного соотношения CoCl2 ∙ 6H2O и ТЭАБ (табл. 3). При этом варьировали как избыток, так и недостаток компонентов каталитической системы друг к другу.
Таблица 3.
Влияние мольного соотношения компонентов каталитической системы CoCl2 ∙ 6H2O–ТЭАБ на показатели синтеза ЦПК. Температура 150°С; давление СО2 2.0 МПа; начальная концентрация ЭЦП 8.93 моль/дм3; без растворителя
№ | Мольное соотношение CoCl2 ∙ 6H2O : ТЭАБ | Время, мин | Конверсия ЭЦП, % | Селективность, % | ||
---|---|---|---|---|---|---|
ЦПК | ЦПДол | прочие* | ||||
Концентрация ТЭАБ 0.0044 моль/моль ЭЦП | ||||||
1 | 0.125 : 1 | 120 | 61.1 | 98.6 | 1.1 | 0.3 |
180 | 74.8 | 98.0 | 1.2 | 0.8 | ||
240 | 83.1 | 97.9 | 1.1 | 1.0 | ||
2 | 0.25 : 1 | 120 | 74.3 | 98.1 | 0.4 | 1.5 |
180 | 90.9 | 97.8 | 0.4 | 1.8 | ||
240 | 97.0 | 97.8 | 0.4 | 1.8 | ||
3 | 0.5 : 1 | 120 | 84.1 | 98.0 | 0.7 | 1.3 |
180 | 96.0 | 97.5 | 0.7 | 1.8 | ||
240 | 98.3 | 97.5 | 0.7 | 1.8 | ||
4 | 1 : 1 | 120 | 83.0 | 98.3 | 0.8 | 0.9 |
180 | 97.3 | 98.5 | 0.7 | 0.8 | ||
240 | 98.1 | 98.6 | 0.7 | 0.7 | ||
5 | 2 : 1 | 120 | 80.5 | 97.3 | 1.0 | 1.7 |
180 | 93.1 | 96.2 | 1.0 | 2.8 | ||
240 | 98.0 | 96.5 | 1.0 | 2.5 | ||
Концентрация CoCl2 ∙ 6H2O 0.0044 моль/моль ЭЦП | ||||||
6 | 1 : 2 | 120 | 97.9 | 98.7 | 0.7 | 0.6 |
180 | 99.3 | 98.8 | 0.7 | 0.5 | ||
240 | 99.6 | 99.1 | 0.7 | 0.2 | ||
7 | 1 : 0.5 | 120 | 38.6 | 96.2 | 1.5 | 2.3 |
180 | 52.0 | 96.3 | 1.5 | 2.2 | ||
240 | 65.3 | 96.2 | 1.4 | 2.4 |
При изменении содержание хлорида кобальта в реакционной смеси от 0.0006 до 0.0088 моль/моль ЭЦП (табл. 3, строки 1–5) и постоянной концентрации ТЭАБ 0.0044 моль/моль ЭЦП, видно, что конверсия ЭЦП не превышает 84% во всем интервале концентраций CoCl2 ∙ 6H2O за время реакции 120 мин при селективности по ЦПК около 98%. Конверсии ЭЦП не ниже 97% удается достичь за 4 ч при мольном соотношении CoCl2 ∙ ∙ 6H2O : ТЭАБ равном (0.25–0.5) : 1 (табл. 3, строки 2, 3) или за 3 ч при их соотношении 1 : 1 (табл. 3, строка 4). Образование ЦПК при этом протекает с селективностью 97.5–98%. Однако, уже при концентрации хлорида кобальта 0.0088 моль/моль ЭЦП (табл. 3, строка 5) наблюдается снижение селективности по ЦПК до 96% при увеличении времени реакции. Выход ЦПДол на прореагировавший ЭЦП с ростом концентрации CoCl2 ∙ 6H2O несколько увеличивается, составляя 0.8 ± 0.2%. Это происходит, по-видимому, за счет внесения с катализатором бóльшего количества кристаллизационной воды. В тоже время выход по другим побочным продуктам, в основном циклопентанону, имеет минимум при эквимолярном соотношении хлорида кобальта и ТЭАБ (табл. 3, строка 4). Следует отметить, что селективность по ЦПДол и “Прочим” мало изменяется при увеличении продолжительности реакции от 1 до 3 ч.
Умеренное содержание ТЭАБ в реакционной смеси (0.0022 моль/моль ЭЦП) в 2 раза большее по отношению к гексагидрату хлорида кобальта (табл. 3, строка 7) приводит к значительному снижению скорости карбоксилирования, хотя селективность по ЦПК остается достаточно высокой – 96%. При возрастании количества ТЭАБ до 0.0044 моль/моль ЭЦП и выше удается повысить скорость реакции. Это позволило достичь конверсии ЭЦП свыше 99% за 3 ч реакции при селективности по ЦПК около 99% (табл. 3, строка 6). Следует отметить, что мольный избыток CoCl2 ∙ 6H2O к ТЭАБ приводит к увеличению доли продуктов изомеризации ЭЦП в реакционной смеси (табл. 3, строки 5, 7).
Кроме этого, данные табл. 2, 3 указывают на то, что для достижения высоких показателей в синтезе ЦПК важно выдержать не только определенное молярное соотношение компонентов бинарной системы, но и их суммарное содержание относительно начальной концентрации ЭЦП.
Исследовано влияние давления диоксида углерода и температура реакции в значительной степени влияют только на конверсию ЭЦП (табл. 4).
Таблица 4.
Влияние давления СО2 и температуры на реакцию карбоксилирования ЭЦП. Начальная концентрация ЭЦП 8.93 моль/дм3; концентрация CoCl2 0.0010 моль/моль ЭЦП, мольное соотношение CoCl2 ∙ 6H2O : ТЭАБ 1 : 4
№ | Температура, °С | Давление СО2, МПа | Время, мин | Конверсия ЭЦП, % | Селективность, % | ||
---|---|---|---|---|---|---|---|
ЦПК | ЦПДол | прочие | |||||
1 | 150 | 1.0 | 120 | 65.9 | 97.4 | 0.5 | 2.1 |
180 | 81.5 | 97.1 | 0.5 | 2.4 | |||
240 | 91.1 | 97.1 | 0.5 | 2.4 | |||
2 | 150 | 2.0 | 120 | 74.3 | 98.1 | 0.4 | 1.5 |
180 | 90.9 | 97.8 | 0.4 | 1.8 | |||
240 | 97.0 | 97.8 | 0.4 | 1.8 | |||
3 | 150 | 3.5 | 120 | 91.2 | 98.5 | 0.4 | 1.1 |
180 | 98.8 | 98.7 | 0.4 | 0.9 | |||
240 | 99.9 | 98.0 | 0.4 | 1.6 | |||
4 | 150 | 4.5 | 120 | 88.2 | 98.4 | 0.4 | 1.2 |
180 | 98.1 | 98.6 | 0.4 | 1.0 | |||
240 | 99.5 | 98.4 | 0.4 | 1.2 | |||
5 | 110 | 2.0 | 240 | 2.4 | 90.9 | 2.5 | 6.6 |
6 | 130 | 2.0 | 240 | 15.7 | 96.4 | 2.3 | 1.3 |
7 | 160 | 2.0 | 120 | 52.5 | 95.7 | 2.0 | 2.3* |
180 | 77.6 | 95.5 | 1.9 | 2.6* | |||
240 | 89.4 | 95.7 | 1.8 | 2.5* |
Оказалось, что почти полного исчерпывания эпоксида удается достичь за 4 ч при давлении СО2 от 3.5 МПа и выше. При этом селективность образования ЦПК составляет не менее 98% (табл. 4, строки 3, 4). Выход ЦПДол с ростом давления практически не изменяется, составляя 0.4–0.5%, а образование “Прочих” продуктов уменьшается до 1 ± 0.2% при давлении 4.5 МПа. При температурах 110, 130°С (табл. 4, строки 5, 6) реакция протекает очень медленно, конверсия ЭЦП за 240 мин при 130°С не превышает 20%. Снижение скорости процесса при 160°С (строка 7) объясняется, по-видимому, частичным термическим разложением ТЭАБ [20]. В реакционной смеси происходит возрастание количества ЦПДол и образование других высококипящих соединений (табл. 4, строка 7).
Таким образом, в результате проведенных исследований синтеза ЦПК карбоксилированием ЭЦП выбрана каталитическая система из доступных компонентов: кристаллогидрат хлорида (бромида) кобальта или никеля и четвертичной аммониевой соли – ТЭАБ. ТБАБ. Синтез ЦПК рекомендуется проводить под давлением углекислого газа 3.5–4.5 МПа и температуре 140–150°С, без растворителя или в среде растворителя. В качестве растворителя можно использовать ЦПК, ДМФА или N-МП, при массовой доле ЭЦП в исходной смеси не ниже 25%. При загрузке компонентов реакционной смеси концентрация CoCl2 составляет от 0.0043 до 0.0357 моль/моль ЭЦП, при мольном соотношении CoCl2 ∙ 6H2O : ТЭАБ от 1 : 4 до 1 : 1. Эти условия позволяют в течение 2– 4 ч получить ЦПК с селективностью от 97 до 99% при практически полной конверсии эпоксида.
В вышеприведенных параметрах синтеза проведена серия укрупненных наработок ЦПК в присутствии каталитической системы CoCl2 ∙ 6H2O – ТЭАБ в среде ДМФА и без растворителя. При использовании реактора объемом 1 дм3 конверсия ЭЦП за 240 мин составила 99.1–99.6%, селективность по ЦПК – 97.5–99%. ЦПК выделен из реакционной массы ректификацией под вакуумом с последующей отмывкой водой от примесей при 80°С. ЦПК-сырец сушили под вакуумом при 20°С и 20 мм рт. ст. Содержание основного вещества ЦПК составляет не ниже 99.5%.
Кубовый остаток, полученный после ректификации продуктов реакции, представляющий собой раствор катализатора в ЦПК и содержащий 4.39% кобальта, возвращается в рецикл. Показана возможность его многократно использования в качестве катализатора реакции на протяжении 4 циклов работы без снижения показателей синтеза ЦПК.
Список литературы
Sakakura. T., Kohno. K. // Chem. Commun. 2009. № 11. P. 1312.
Aresta M., Dibenedetto A., Quaranta E. // Springer-Verlag Berlin Heidelberg. 2016. P. 409.
Михеев В.В. Неизцианатные полиуретаны, Монография. Казань: КНИТУ, 2011. 292 с.
Carmen M., Giulia F., Arjan W., Kleij J. // ACS Catal. 2015. № 5(2). P. 1353.
Taisuke I., Takehiko I., Itaru N., Masashi O. // Chem. Pharm.Bull. 2002. № 50(1). P. 83.
Bartolo G., Raffaella M., Giuseppe S., Lucia V., Mirco P., Angela D. // ChemSusChem. 2011. V. 4. P. 1778.
Cooper J.F., Lichtenwalter M. // Patent US № 2773070. 1956.
Crosby G.W., Millikan A.F. // Patent US № 2994705. 1961.
Okamoto H., Someya K. // Patent US № 7199253B2. 2007.
Darensbourg D.J., Chung W.P., Wilson S.J. // ACS Catal. 2013. № 3(12). P. 3050.
Bhalchandra M., Bhanage, Masahiko A. // Springer-Verlag Berlin Heidelberg. 2014. P. 245.
Cannarsa M.J., Hsiang-Ning, Sun Haven S., Kesling Jr. // Patent Evro № 0321207. 1989.
William J., Kruper J. // Patent US № 4663467. 1987.
Мельник Л.В., Мешечкина А.Е., Рыбина Г.В., Среднев С.С., Москвичев Ю.А., Козлова О.С. // Нефтехимия. 2012. Т. 52. № 5. С. 348.
Рыбина Г.В., Бобылева Л.И., Среднев С.С. // Журн. прикл. химии. 2003. Т. 76. № 5. С. 870.
Rui L., Xin T., Xiaofang L., Changwen H. // Pure Appl. Chem. 2012. T. 84. № 3. P. 621.
Darensbourg D.J., Matthew W. // Coordination Chem. Reviews. 1996. № 153. P. 155.
Richard G., Austin R.P., Michaelson R.M. // Patent US № 4824969. 1989.
Рыбина Г.В., Мельник Л.В., Среднев С.С., Москвичев Ю.А., Медведев В.Г., Козлова О.С., Мешечкина А.Е. // Патент РФ № 2448945. 2012.
Демлов Э., Демлов З. Межфазный катализ. М.: Мир, 1987. 482 с.
Дополнительные материалы отсутствуют.