Нефтехимия, 2020, T. 60, № 5, стр. 708-714
Физико-химические и эксплуатационные свойства уреатных пластичных смазок на основе минеральных базовых масел I группы
А. С. Лядов 1, *, Ю. М. Ярмуш 1, В. А. Ивлев 2
1 Институт нефтехимического синтеза им. А.В. Топчиева РАН
119991 Москва, Россия
2 Российский университет дружбы народов (РУДН)
117198 Москва, Россия
* E-mail: lyadov@ips.ac.ru
Поступила в редакцию 29.04.2020
После доработки 08.05.2020
Принята к публикации 12.05.2020
Аннотация
Проведено комплексное исследование уреатных пластичных смазок, полученных на основе дистиллятных масел I группы, которые имели вязкость в диапазоне от 24.4 до 342.0 мм2/с при 40°С. Полученные результаты позволили установить зависимость различных физико-химических показателей пластичных смазок (температура каплепадения, предел прочности, коллоидная стабильность, показатель износа) от вязкости базового масла и структуры димочевины, используемой в качестве загустителя. Выявленные закономерности позволяют прогнозировать свойства пластичных смазок на этапе выбора исходных компонентов.
ВВЕДЕНИЕ
К современным пластичным смазкам предъявляется целый ряд требований, среди которых основным является способность к уменьшению коэффициента трения, что в свою очередь приводит к снижению скорости изнашивания трущихся поверхностей [1]. Пластичные смазки представляют собой коллоидные системы, в которых дисперсионной средой является базовое масло, а дисперсной фазой – загуститель [2]. При этом на физико-химические эксплуатационные свойства смазок оказывают влияние оба эти компонента. В последнее десятилетие пластичные смазки с загустителями на основе ди-, олиго- и полимочевин получили широкое распространение в мире, так как они способны работать при высоких нагрузках, широком интервале температур и скоростей, в контакте с агрессивными средами, а также устойчивы к радиационному воздействию. При этом в мире доля полимочевинных смазок в общем объеме производства постоянно возрастает [3].
Для производства пластичных смазок используются все группы базовых масел. Несмотря на то, что масла I группы имеют ряд недостатков (низкий индекс вязкости, низкая окислительная стабильность, высокая испаряемость, большое содержание серы), они находят широкое применение при производстве пластичных смазок, так как имеют самую низкую стоимость среди всех масел, а также обладают высоким химическим сродством ко всем загустителям и присадкам, которые вводятся в состав смазок с целью улучшениях их эксплуатационных свойств [4]. К тому же существует большое количество разных марок базовых масел I группы, вязкость которых варьируется в очень широких пределах [5], что позволяет создавать композиции смазок для различных узлов трения. Следует отметить, что до сих пор не было проведено систематических исследований по установлению взаимосвязи между составом, строением и основными эксплуатационными физико-химическими и трибологическими свойствами уреатных пластичных смазок.
Цель данной работы заключалась в установлении взаимосвязи между структурными особенностями димочевин, выступающих в роли загустителя, а также вязкостью базовых масел и основными физико-химическими и эксплуатационными показателями пластичных смазок.
ЭКСПЕРИМЕНТАЛЬНАЯ ЧАСТЬ
Для получения уреатных пластичных смазок была использована широкая номенклатура минеральных базовых масел, производимых в промышленном масштабе с различной вязкостью: ИГП-18, И-20А, АУ, Ц-38, МС-20. Все эти масла, за исключением масла Ц-38, получают селективной очисткой соответствующих нефтяных фракций. Для сравнения также были получены пластичные смазки на основе н-гексадекана. Основные сведения об использованных базовых маслах представлены в табл. 1. Все они по своим физико-химическим характеристикам соответствовали нормативам соответствующих ГОСТов или спецификаций. Кинематическую вязкость масел при 40°С определяли в соответствии с ГОСТ 33-2016 “Нефть и нефтепродукты. Прозрачные и непрозрачные жидкости. Определение кинематической и динамической вязкости”.
Таблица 1.
Используемые в работе базовые масла
№ | Марка масла | Вязкость при 40°С, мм2/с | Состав |
---|---|---|---|
1 | н-Гексадекан | 2.93 | Индивидуальный углеводород (С16H34), 98% |
2 | ИГП-18 | 24.4 | Масло индустриальное гидравлическое с присадками, полученное с применением технологии глубокой селективной очистки |
3 | И-20А | 32.1 | Минеральное масло из малосернистых нефтей, получаемое селективной очисткой и не содержащее присадок |
4 | АУ | 34.8 | Минеральное масло, получаемое из малосернистых парафинистых нефтей с использованием процессов глубокой селективной очистки фенолом и глубокой депарафинизации; содержит антиокислительную присадку |
5 | Ц-38 | 38.6 | Минеральное дистиллятное масло, получаемое перегонкой масляного гудрона со щелочью |
6 | МС-20 | 342.0 | Минеральное авиационное масло селективной очистки по доусол-процессу без присадок |
Загущение базовых масел осуществляли введением в них диизоцианата и соответствующих аминов при варьировании температуры смешения исходных компонентов. В качестве диизоцианата был использован 2,4-диизоциано-1-метил-бензол (2,6-ТДИ), в качестве первого амина во всех случаях брали анилин, а природу второго амина варьировали за счет длины углеводородного радикала (н-гексиламин, н-октиламин, н-додециламин, н‑гексадециламин). Подробно методика получения пластичных смазок описана в работе [6]. Содержание уреатного загустителя во всех исследуемых образцах составляло 20 мас. %.
Для всех пластичных смазок были определены следующие базовые физико-химические показатели (табл. 2): температура каплепадения, предел прочности, коллоидная стабильность. Трибологические характеристики полученных смазок изучали на четырехшариковой машине, узел трения которой представляет собой пирамиду из четырех контактирующих друг с другом стальных шариков.
Таблица 2.
Методы определения физико-химических характеристик пластичных смазок
№ | Определяемый параметр | Методика | Прибор |
---|---|---|---|
1 | Температура каплепадения, °С | ГОСТ 6793-74 “Нефтепродукты. Метод определения температуры каплепадения” | ЛинтеЛ КАПЛЯ-20И, БСКБ Нефтехимавтоматика |
2 | Предел прочности, Па | ГОСТ 7143-73 “Смазки пластичные. Метод определения предела прочности и термоупрочнения” | ЛинтеЛ СК-20, БСКБ Нефтехимавтоматика |
3 | Коллоидная стабильность, % отделяемого масла при испытании | ГОСТ 7142-74 “Смазки пластичные. Методы определения коллоидной стабильности” | ЛинтеЛ АКС-20, БСКБ Нефтехимавтоматика |
4 | Диаметр пятна износа, мм | ГОСТ 9490-75 “Материалы смазочные жидкие и пластичные. Метод определения трибологических характеристик на четырехшариковой машине” | Машина трения четырехшариковая ЧМТ-1 |
Термический анализ пластичных смазок проводили на термоанализаторе Q-600 в интервале температур 25–1000°С в атмосфере воздуха, скорость нагрева составляла 10°С/мин. Спектры ЯМР 1Н регистрировали на приборе Bruker WP-300.
РЕЗУЛЬТАТЫ И ИХ ОБСУЖДЕНИЕ
Диизоцинаты являются крайне реакционноспособными соединениями, и их взаимодействие с аминами начинается уже при комнатной температуре, но при этом не происходит формирование консистентной структуры пластичной смазки; образцы смазок, полученных при комнатной температуре, характеризовались очень низкими значениями предела прочности (не более 50 Па). Было установлено, что повышение температуры загущения приводит к существенному увеличению значения предела прочности. В случае использования н-гексадекана и загустителя на основе ТДИ, анилина и гексиламина предел прочности пластичной смазки, получаемой при температуре смешения компонентов 25°С составлял 47 Па, при 50°С – 130 Па, а при 100°С уже 400 Па. Было установлено, что оптимальной температурой начала реакции загущения базовых масел димочевинами, синтезируемыми in situ, является интервал 85–110°С; при этих условиях для всех базовых масел были получены пластичные смазки с хорошо сформированной структурой. Таким образом, в настоящем исследовании введение исходных компонентов в базовое масло проводили при 90°С, затем нагревали реакционную смесь до 130°С и выдерживали при этой температуре в течение 30 мин для формирования однородной консистенции пластичных смазок, после чего их охлаждали до комнатной температуры.
Для определения структуры образующихся in situ в базовом масле органических мочевин, которые являются загустителями, пластичные смазки на основе н-гексадекана были растворены в н‑гексане, после чего выпавшие белые осадки выделяли фильтрованием. Полученные таким образом осадки органических мочевин растворяли в ДМСО-D6 и записывали 1H-ЯМР-спектры (табл. 3). Анализ данных 1H-ЯМР-спектров показал, что при введении диизоцианата и аминов в базовое масло происходит формирование соответствующих органических димочевин, структура которых представлена в табл. 3.
Таблица 3.
Данные 1H-ЯМР-спектров уреатных загустителей, выделенных из исследуемых пластичных смазок
№ | Пластичная смазка | Данные 1H-ЯМР-спектров | Структура уреатного загустителя |
---|---|---|---|
1 | Базовое масло: н-гексадекан Компоненты загустителя: ТДИ, анилин, н-гексиламин Содержание загустителя: 20 мас. % |
0.87 м.д. (3Н, N–CH2–CH2–(CH2)3–CH3); 1.29 м.д. (6Н, N–CH2–CH2–(CH2)3–CH3); 1.43 м.д. (2Н, N–CH2–CH2–(CH2)3–CH3); 2.11 м.д. (3H, Ar–CH3); 3.09 м.д. (2Н, N–CH2–CH2–(CH2)3–СH3); 6.9–7.5 (8Н, Ar); 7.8–8.6 (4Н, NH) |
![]() |
2 | Базовое масло: н-гексадекан Компоненты загустителя: ТДИ, анилин, н-октиламин Содержание загустителя: 20 мас. % |
0.86 м.д. (3Н, N–CH2–CH2–(CH2)5–CH3); 1.28 м.д. (10Н, N–CH2–H2–(CH2)5–CH3); 1.43 м.д. (2Н, N–CH2–CH2–(CH2)5–CH3); 2.11 м.д. (3H, Ar–CH3); 3.07 м.д. (2Н, N–CH2–CH2–(CH2)5–CH3); 6.9–7.5 (8Н, Ar); 7.8–8.6 (4Н, NH) |
![]() |
3 | Базовое масло: н-гексадекан Компоненты загустителя: ТДИ, анилин, н-додециламин Содержание загустителя: 20 мас. % |
0.85 м.д. (3Н, N–CH2–CH2–(CH2)9–CH3); 1.24 м.д. (18Н, N–CH2–CH2–(CH2)9–CH3); 1.43 м.д. (2Н, N–CH2–CH2–(CH2)9–CH3); 2.10 м.д. (3H, Ar–CH3); 3.07 м.д. (2Н, N–CH2–CH2–(CH2)9–CH3); 6.9–7.5 (8Н, Ar); 7.8–8.6 (4Н, NH) |
![]() |
Температура каплепадения является одним из важнейших показателей свойств пластичной смазки, характеризующих ее работоспособность и возможность функционирования в узлах трения, подверженных воздействию высоких температур, и выступает наглядным показателем целостности структуры смазки и верхнего температурного предела эффективного обслуживания узлов агрегата. На рис. 1а представлены зависимости температур каплепадения пластичных смазок от числа атомов углерода в углеводородном радикале в молекуле загустителя для пластичных смазок, полученных с использованием различных базовых масел. Как и следовало ожидать, с увеличением длины углеводородного радикала, а также при повышении вязкости базового масла происходит увеличение температуры каплепадения. Так, для пластичной смазки на основе н-гексадекана (2.93 мм2/с) при увеличении углеводородного радикала в 2.5 раза температура каплепадения увеличивается всего на 30°С, в то время как для смазки на основе масла МС-20 (342 мм2/с) увеличение составляет более 100°С. Для детального изучения процессов, происходящих в пластичных смазках при нагревании, исследуемые образцы были изучены методом термического анализа. Все полученные термограммы имеют схожий вид; для примера на рис. 1б приведена термограмма пластичной смазки на основе н-гексадекана и загустителя ТДИ–анилин–гексиламин. При температуре 60–70°С для изученных смазок наблюдается ярко выраженный эндотермический эффект, не сопровождающийся изменением массы образцов, что свидетельствует об изменении фазового состояния загустителя. При температуре, равной примерно температуре каплепадения, также наблюдается эндотермический эффект, который соответствует фазовым изменениям изучаемых материалов, происходящих при их плавлении. Нагревание выше температуры каплепадения приводит к постепенному уменьшению массы образцов, связанному с испарением базового масла, а также происходящими процессами горения, о чем свидетельствует ряд последовательных экзотермических эффектов. Уреатные пластичные смазки являются беззольными, так как при нагревании их масса уменьшается на 100%.
Рис. 1.
Зависимость температуры каплепадения (а) исследуемых пластичных смазок (1 – н-гексадекан, 2 – ИГП-18, 3 – И-20А, 4 – АУ, 5 – Ц-38, 6 – МС-20) от длины углеводородного радикала в молекуле загустителя и термограмма (б) пластичной смазки на основе н-гексадекана и загустителя ТДИ–анилин–гексиламин.
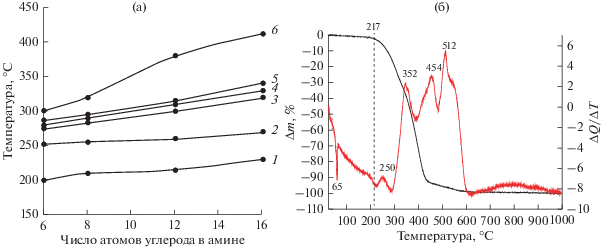
Другим важным показателем пластичных смазок является предел прочности, характеризующий способность смазки удерживаться в узлах трения под влиянием инерционных сил. Былo установлено, что увеличение вязкости приводит к уменьшению предела прочности (рис. 2а), что, в свою очередь, приводит к разрушению каркаса смазки при более меньших силах воздействия. Это может объясняться тем, что с увеличением вязкости базового масла в нем повышается доля высокомолекулярных компонентов, которые, в свою очередь, неравномерно распределяются внутри каркаса, образованного загустителем. Увеличение длины углеводородных радикалов в молекуле загустителя, вероятнее всего, позволяет формировать элементы каркаса с большим объемом, в которых могут располагаться компоненты базового масла. Данное предположение подтверждается увеличением предела прочности при увеличении длины углеводородного радикала в молекулах загустителя.
Рис. 2.
Зависимости предела прочности (а) и коллоидной стабильности (б) исследуемых пластичных смазок (1 – н-гексадекан, 2 – ИГП-18, 3 – И-20А, 4 – АУ, 5 – Ц-38, 6 – МС-20) от длины углеводородного радикала в молекуле загустителя.
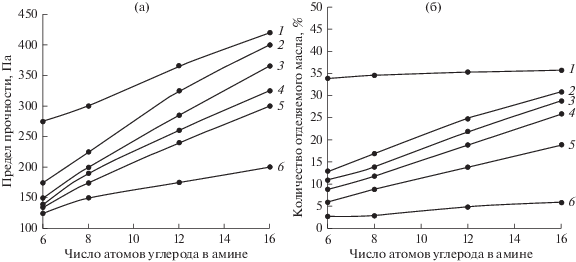
Так как по своей природе пластичные смазки являются коллоидными системами, то со временем под действием разных факторов происходит разрушение их коллоидной структуры. Поэтому для всех пластичных смазок определяют такой показатель, как коллоидная стабильность, который показывает способность смазки сопротивляться расслаиванию. На коллоидную стабильность оказывает влияние вязкость дисперсионной среды: чем выше вязкость масла, тем труднее ему вытекать за пределы структурного каркаса (рис. 2б). Увеличение длины углеводородных радикалов в молекулах загустителя приводит к увеличению единичных элементов каркаса пластичных смазок, что, в свою очередь, приводит к уменьшению коллоидной стабильности смазочных материалов, что выражается в увеличении количества отделяемого масла в процессе испытания. Полученные данные хорошо согласуются с данными, полученными при изучении предела прочности.
В качестве основного показателя противоизносных свойств пластичных смазок используют показатель износа (диаметр пятна износа). Для всех образцов были определены диаметры пятен износа на четырехшариковой машине (табл. 4). Анализ полученных данных показал, что, в целом, наблюдается тенденция к уменьшению диаметра пятна износа с увеличением числа атомов углерода в молекуле амина. Данный факт хорошо согласуется с результатами, полученными при исследовании коллоидной стабильности смазок. Так в случае смазок, загущенных димочевиной с более длинным углеводородным радикалом, наблюдается наибольшее количество выделяемого масла, что благоприятствует снижению интенсивности изнашивания трущихся поверхностей.
Таблица 4.
Показатели износа исследуемых пластичных смазок
№ | Базовое масло | Диаметр пятна износа, мм | ||
---|---|---|---|---|
ТДИ + анилин + + н-гексиламин | ТДИ + анилин + н-октиламин | ТДИ + анилин + + н-доцециламин | ||
1 | н-Гексадекан | 0.95 | 0.87 | 0.72 |
2 | ИГП-18 | 0.59 | 0.51 | 0.45 |
3 | И-20А | 0.73 | 0.69 | 0.67 |
4 | АУ | 0.60 | 0.50 | 0.44 |
5 | Ц-38 | 0.59 | 0.50 | 0.40 |
6 | МС-20 | 0.71 | 0.65 | 0.50 |
Таким образом, в ходе работы было впервые проведено систематическое исследование влияния уреатного загустителя на физико-химические и трибологические свойства пластичных смазок, при этом была использована широкая номенклатура базовых масел I группы. Установлено, что такие показатели пластичных смазок, как предел прочности и температура каплепадения, возрастают с увеличением длинны углеводородных радикалов в молекуле димочевины, а коллоидная стабильность при этом наоборот снижается. Увеличение вязкости, в свою очередь, приводит также к изменению свойств смазок: температура каплепадения и коллоидная стабильность возрастают с увеличением вязкости, а предел прочности при этом наоборот уменьшается. Все эти данные хорошо согласуются друг с другом.
Полученные научные результаты имеют не только важное фундаментальное значение для развития современного смазочного материаловедения, но и прикладное значение для производителей смазочных материалов, так как позволяют прогнозировать эксплуатационные свойства создаваемых уреатных пластичных смазок.
Список литературы
Lugt P.M. // Tribology Transactions. 2009. V. 52. № 4. P. 470. https://doi.org/10.1080/10402000802687940
Rizvi S. A Comprehensive Review of Lubricant Chemistry, Technology, Selection, and Design, 2009. West Conshohocken. PA: ASTM International. https://doi.org/10.1520/MNL59-EB.
Лядов А.С., Максимова Ю.М., Шахматова А.С., Кириллов В.В., Паренаго О.П. // Журнал прикладной химии. 2018. Т. 91. № 6. С. 761 [Russian J. Applied Chemistry. 2018. V. 91. №. 6. P. 885. https://doi.org/10.1134/S1070427218060010]
Casserly E., Langlais T., Springer S.P., Kumar A. // European Lubricants Industry Magazine. 2018. № 114. P. 32.
Цветков О.Н. // Мир нефтепродуктов. Вестник нефтяных компаний. 2008. № 2. С. 23.
Лядов А.С., Максимова Ю.М., Алексеева О.А., Ильин С.О., Паренаго О.П., Антонов С.В. // Журнал прикладной химии. 2018. Т. 91. № 11. С. 1523 [Russian J. Applied Chemistry. 2018. V. 91. №. 11. P. 1733. https://doi.org/10.1134/S1070427218011014]https://doi.org/10.1134/S0044461818110014
Дополнительные материалы отсутствуют.