Неорганические материалы, 2019, T. 55, № 4, стр. 438-441
Разработка высоковольтной керамики на основе ZnO с плотностью тока утечки менее 1 мкА/см2
Е. Л. Тихомирова 1, *, Ю. А. Савельев 1, О. Г. Громов 1
1 Институт химии и технологии редких элементов и минерального сырья им. И.В. Тананаева – обособленное подразделение Федерального исследовательского центра “Кольский научный центр Российской академии наук”
184209 Мурманская обл, Апатиты, Академгородок, 26а, Россия
* E-mail: tikhomirova@chemy.kolasc.net.ru
Поступила в редакцию 20.06.2018
После доработки 15.10.2018
Принята к публикации 07.09.2018
Аннотация
Проведены исследования по определению массового соотношения оксидных добавок, обеспечивающего получение в системе ZnO–Bi2O3–Sb2O3–Al2O3–Co3O4 высоковольтной керамики с плотностью тока утечки <1 мкА/см2 при содержании ZnO 90 мас. %. Керамика, полученная с соотношением оксидных добавок Bi2O3 : Sb2O3 : Al2O3 : Co3O4 = 0.25 : 0.17 : 1.4 : 1.4, имеет высокое значение коэффициента нелинейности α = 69, низкую плотность тока Iут = 0.4 мкА/см2 и величину напряжения пробоя Ub = 4.1 кВ/мм.
ВВЕДЕНИЕ
Варисторы (нелинейные резисторы) используют для защиты приборов и оборудования от коммутационных и грозовых перенапряжений. Основные свойства варисторов: Ub – напряжение пробоя, α – коэффициент нелинейности, Iут – плотность тока утечки.
Варисторы производят из керамики на основе ZnO с добавками оксидов легирующих элементов: Вi, Со, Si, Sb, Мn, A1, Cr, Ni. Процесс получения варисторной керамики состоит из следующих стадий: синтез керамического порошка → → прессование → спекание при 900–1200°C.
В промышленном масштабе варисторная керамика производится с Ub = 0.2–0.5 кВ/мм [1]. Для защиты миниатюрных электронных устройств и высоковольтных линий электропередач нужна керамика с Ub ≥ 3 кВ/мм. При этом Iут должна быть как можно ниже (<1 мкА/см2) [2].
Варисторные свойства керамики зависят от состава, метода синтеза керамического порошка и условий спекания. Повысить Ub можно при использовании наноразмерного керамического порошка с гомогенным распределением легирующих оксидов. В настоящее время возрастающее внимание уделяется синтезу наноразмерных керамических порошков методом сжигания [3, 4], основанному на экзотермической восстановительно-окислительной реакции между нитратами цинка и легирующих элементов (окислители) и топливом (восстановитель):
В работе [5] этим методом синтезирован керамический порошок в системе ZnO–Bi2O3–Sb2O3–Al2O3–Co3O4 с содержанием ZnO 90 мас. %. В качестве исходных материалов использовали Zn(NO3)2 ∙ 6H2O, Bi(NO3)3 ∙ 5H2O, А1(NO3)3 ∙ ∙ 9Н2О, Co(NO3)2 ∙ 6H2O, раствор Sb2O3 в винной кислоте; топливом служил коммерческий сахарный песок. Исходные компоненты при массовом соотношении оксидных добавок Bi2O3 : Sb2O3 : : Al2O3 : Co3O4 = 1.0 : 0.7 : 1.2 : 0.72 засыпали в фторопластовый стакан, который помещали в сушильный шкаф, предварительно нагретый до 200°С, выдерживали в течение 40 мин и извлекали для охлаждения на воздухе. Продукт сжигания измельчали и прокаливали в муфельной печи при температуре 700°С в течение 1 ч с получением нанокристаллического порошка. Керамика, полученная из этого порошка спеканием при 975°C с изотермической выдержкой 2 ч, имеет Ub = 4.5 кВ/мм, α = 50, Iут = 1.1 мкА/см2.
В работе [6] для синтеза керамического порошка в системе ZnO–Bi2O3–Sb2O3–Al2O3–Co3O4–NiO с содержанием ZnO 75 мас. % использован метод ускоренного сжигания. Исходные компоненты при массовом соотношении оксидных добавок Bi2O3 : Sb2O3 : Al2O3 : Co3O4 : NiO = 1.0 : 0.69 : 1.00 : : 0.65 : 0.08 и сахарный песок растворяли в дистиллированной воде в стеклянном термостойком стакане на магнитной мешалке при температуре 60°С. Стакан с раствором помещали в муфельную печь, предварительно нагретую до 500°С, выдерживали 10 мин, извлекали из муфеля и охлаждали до комнатной температуры. Продукт сжигания измельчали и прокаливали в муфельной печи при температуре 700°С в течение 1 ч с получением нанокристаллического порошка. Керамика из этого порошка, полученная спеканием таблеток при 975°С с изотермической выдержкой 4 ч, имеет Ub = 4.2 кВ/мм, α = 54, Iут = 0.2 мкА/см2. Преимуществом данной керамики является низкая величина плотности тока утечки, а недостатком – пониженное содержание оксида цинка, являющегося самым дешевым компонентом в составе керамики.
Цель работы – определение оптимального соотношения оксидных добавок для получения высоковольтной керамики с содержанием ZnO 90 мас. % и плотностью тока утечки <1 мкА/см2 при синтезе наноразмерного керамического порошка методом ускоренного сжигания.
ЭКСПЕРИМЕНТАЛЬНАЯ ЧАСТЬ
Образцы высоковольтной варисторной керамики получали в системе ZnO–Bi2O3–Sb2O3–Al2O3–Co3O4 с содержанием ZnO 90 мас. %.
Синтез 5 г керамического порошка осуществляли по методике, изложенной в работе [6], с нижеследующим уточнением. Время полного растворения исходных компонентов по данной методике составляет 54–55 мин. Нами проведены исследования по влиянию на время растворения и удельную поверхность синтезированного керамического порошка добавки в исходную смесь винной кислоты C4H6O6. Из рис. 1 следует, что добавка винной кислоты способствует уменьшению времени полного растворения τ и увеличению удельной поверхности Sуд керамического порошка. Оптимальная добавка винной кислоты принята равной 0.25 г, при этом τ = 26 мин, Sуд = 39 м2/г. Все последующие синтезы керамических порошков проводили с указанной добавкой винной кислоты.
Рис. 1.
Зависимости времени полного растворения τ и удельной поверхности Sуд от содержания добавки C4H6O6.
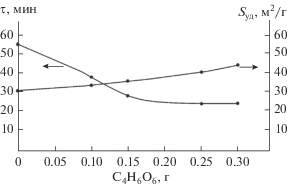
Для получения керамического образца 1 г синтезированного порошка прессовали на гидравлическом прессе с усилием 80 кН в таблетку диаметром 20 мм. Спекание таблетки осуществляли при 975°С с изотермической выдержкой 5 ч со скоростью нагрев 10.8°C/мин с последующим охлаждением до 700°С со скоростью 2°C/мин, затем вместе с печью до комнатной температуры.
Измерение удельной поверхности Sуд керамического порошка проводили методом термической десорбции азота на лабораторном электронном измерителе удельной поверхности и пористости Flow Sorb II 2300. Коэффициент нелинейности α рассчитывали по формуле: α = 0.19(lgU2/U1)–1, где U1 – напряжение на таблетке при плотности тока 1 мА/см2, а U2 – напряжение на таблетке при плотности тока 1.55 мА/см2. Напряжение пробоя Ub (кВ/мм) вычисляли путем деления U1 на толщину таблетки h (мм). Плотность тока утечки Iут (мкА/см2) определяли при напряжении на таблетке U = 0.75Ub.
РЕЗУЛЬТАТЫ И ОБСУЖДЕНИЕ
В табл. 1 (образец 1) представлены значения варисторных свойств полученной исходной керамики К-90 с массовым соотношением оксидных добавок Bi2O3 : Sb2O3 : Al2O3 : Co3O4 = 1.0 : 0.7 : 1.2 : : 0.72. Видно, что она имеет относительно низкий коэффициент нелинейности и повышенную плотность тока утечки.
Таблица 1.
Варисторные свойства керамики К-90 в зависимости от коэффициента пропорциональности конкретной оксидной добавки
Состав | Соотношение компонентов | Свойства | ||||||
---|---|---|---|---|---|---|---|---|
Bi2O3 | Sb2O3 | Al2O3 | Co3O4 | Ub, кВ/мм | α | Iут, мкА/см2 | h, мм | |
К-90 | 1.0 | 0.7 | 1.2 | 0.72 | 4.1 | 37 | 4.5 | 1.0 |
К-90-Sb – | » | 0.35 | » | » | 4.7 | 40 | 2.1 | 1.0 |
К-90-Sb + | » | 1.05 | » | » | 4.5 | 20 | 3.0 | 1.03 |
К-90-Co – | » | » | » | 0.36 | 3.6 | 36 | 10 | 1.01 |
К-90-Co + | » | » | » | 1.08 | 5.0 | 22 | 4.5 | 1.0 |
К-90-Al – | » | » | 0.60 | » | 2.7 | 28 | 3.0 | 0.92 |
К-90-Al + | » | » | 1.80 | » | 4.1 | 30 | 1.5 | 1.04 |
К-90-Bi – | 0.5 | » | » | » | 3.8 | 50 | 1.0 | 1.05 |
К-90-Bi + | 1.5 | » | » | » | 2.75 | 40 | 5.0 | 0.96 |
Для определения оптимального соотношения оксидных добавок, способствующего повышению коэффициента нелинейности и понижению плотности тока утечки, было исследовано влияние каждой оксидной добавки на варисторные свойства керамики К-90. Для этого коэффициент пропорциональности одной оксидной добавки уменьшали или увеличивали на 50% (“–” и “+” при указании состава образцов в табл. 1). Полученные значения варисторных свойств сопоставляли с исходными (табл. 1).
Установлено, что:
– повышению Ub способствуeт увеличение содержания оксидов алюминия и кобальта или уменьшение содержания оксидов висмута и сурьмы;
– повышению α способствуeт увеличение содержания оксида алюминия или уменьшение содержания оксидов висмута, сурьмы и кобальта;
– уменьшению Iут способствуeт увеличение содержания оксидов алюминия и кобальта или уменьшение содержания оксидов висмута и сурьмы.
– возрастанию плотности керамики, о чем можно косвенно судить по толщине таблетки h, способствуют уменьшение содержания оксида алюминия и увеличение содержания оксида висмута.
С учетом полученных данных проведены исследования по получению образцов керамики К-90 с уменьшением содержания оксидов висмута и сурьмы и одновременным повышением содержания оксидов алюминия и кобальта. Результаты исследований представлены в табл. 2. Установлено, что снижение содержания оксидов висмута и сурьмы способствует увеличению коэффициента нелинейности и уменьшению плотности тока утечки. При дополнительном варьировании содержания оксидов алюминия и кобальта найдено, что минимальное значение Iут = 0.3 мкА/см2 достигается при соотношении оксидных добавок Bi2O3 : Sb2O3 : Al2O3 : Co3O4 = 0.36 : : 0.25 : 1.2 : 1.2 (табл. 2, образец 5). При этом α = 54. Максимальное значение α = 83 достигается при соотношении оксидных добавок Bi2O3 : Sb2O3 : : Al2O3 : : Co3O4 = 0.25 : 0.17 : 1.4 : 1.6 (табл. 2, образец 9). При этом Iут = 1.0 мкА/см2. Соотношение оксидных добавок Bi2O3 : Sb2O3 : Al2O3 : Co3O4 = 0.25 : 0.17 : : 1.4 : 1.4 (табл. 2, образец 7) принято за оптимальное. Полученная с этим соотношением керамика имеет высокое значение α = 69, низкую Iут = 0.4 мкА/см2 и хорошую величину Ub = 4.1 кВ/мм.
Таблица 2.
Зависимость свойств керамики К-90 от соотношения оксидных добавок
Образец | Соотношение компонентов | Свойства | ||||||
---|---|---|---|---|---|---|---|---|
Bi2O3 | Sb2O3 | Al2O3 | Co3O4 | Ub, кВ/мм | α | Iут, мкА/см2 | h, мм | |
1 | 1.0 | 0.7 | 1.2 | 0.72 | 4.1 | 37 | 4.5 | 1.00 |
2 | 0.5 | 0.45 | 1.2 | 1.0 | 3.4 | 53 | 1.7 | 1.00 |
3 | 0.43 | 0.30 | 1.4 | 1.0 | 4.0 | 51 | 0.9 | 1.02 |
4 | 0.36 | 0.25 | 1.4 | 1.4 | 3.8 | 50 | 0.9 | 0.99 |
5 | 0.36 | 0.25 | 1.2 | 1.2 | 3.7 | 54 | 0.3 | 0.99 |
6 | 0.25 | 0.17 | 1.2 | 1.4 | 3.2 | 54 | 0.5 | 0.98 |
7 | 0.25 | 0.17 | 1.4 | 1.4 | 4.1 | 69 | 0.4 | 0.99 |
8 | 0.25 | 0.17 | 1.6 | 1.4 | 4.2 | 70 | 1.8 | 1.01 |
9 | 0.25 | 0.17 | 1.4 | 1.6 | 3.9 | 83 | 1.0 | 1.00 |
В табл. 3 представлены результаты исследования зависимости свойств варисторной керамики от содержания ZnO при оптимальном соотношении оксидных добавок. Видно, что повышение содержания ZnO на 2.5 мас. % вызывает резкое увеличение плотности тока утечки – до 3 мкА/см2 и снижение коэффициента нелинейности до 32, немного увеличивается плотность керамики. С уменьшением содержания ZnO на 2.5 мас. % существенно увеличивается напряжение пробоя – до 4.8 кВ/мм, снижаются коэффициент нелинейности и плотность керамики, плотность тока утечки увеличивается до 0.6 мкА/см2. Отсюда следует, что керамика (мас. %): ZnO – 90, Bi2O3 – 1.06, Sb2O3 – 0.74, Al2O3 – 4.10, Co3O4 – 4.10 имеет наилучшие варисторные характеристики и перспективна для использования в производстве высоковольтных варисторов.
Таблица 3.
Зависимость свойств варисторной керамики от содержания ZnO при оптимальном соотношении оксидных добавок
Состав | Соотношение компонентов | Свойства | ||||||
---|---|---|---|---|---|---|---|---|
Bi2O3 | Sb2O3 | Al2O3 | Co3O4 | Ub, кВ/мм | α | Iут, мкА/см2 | h, мм | |
К-90* | 0.25 | 0.17 | 1.4 | 1.4 | 4.1 | 69 | 0.4 | 0.99 |
К-92.5 | » | » | » | » | 3.3 | 32 | 3.0 | 0.97 |
К-87.5 | » | » | » | » | 4.8 | 58 | 0.6 | 1.05 |
* Образец 7 из табл. 2.
ЗАКЛЮЧЕНИЕ
Проведены исследования по определению оптимального массового соотношения оксидных добавок для получения высоковольтной керамики в системе ZnO–Bi2O3–Sb2O3–Al2O3–Co3O4 с содержанием ZnO 90 мас. % и плотностью тока утечки <1 мкА/см2. Синтез наноразмерного керамического порошка осуществляли методом ускоренного сжигания. Исходная керамика К-90 имела массовое соотношение оксидных добавок Bi2O3 : Sb2O3 : Al2O3 : Co3O4 = 1.0 : 0.7 : 1.2 : 0.72, Ub = 4.1 кВ/мм, α = 37, Iут = 4.5 мкА/см2.
При варьировании коэффициента пропорциональности конкретной оксидной добавки установлено, что уменьшение содержания оксидов висмута и сурьмы с одновременным повышением содержания оксидов алюминия и кобальта способствует увеличению коэффициента нелинейности и уменьшению плотности тока утечки. Найдено оптимальное соотношение оксидных добавок: Bi2O3 : Sb2O3 : Al2O3 : Co3O4 = 0.25 : 0.17 : : 1.4 : 1.4. Полученная с этим соотношением керамика состава (мас. %): ZnO – 90, Bi2O3 – 1.06, Sb2O3 – 0.74, Al2O3 – 4.10, Co3O4 – 4.10 имеет высокое значение коэффициента нелинейности α = = 69, низкую плотность тока утечки Iут = 0.4 мкА/см2 и величину напряжения пробоя Ub = 4.1 кВ/мм.
Список литературы
Pillai P.C., Kelly J. Self-Assembled Arrays of ZnO Nanoparticles and Their Application as Varistor Materials // J. Mater. Chem. 2004. V. 14. P. 1572–1578.
Pillai P.C., Kelly J.M., McCormackad D.E., Rameshc R.J. High Performance ZnO Varistors Prepared from Nanocrystalline Precursors for Miniaturised Electronic Devices // J. Mater Chem. 2008. V. 18. P. 3926–3932.
Hembram K., Sivaprahasam D., Rao T.N. Combustion Synthesis of Doped Nanocrystalline ZnO Powders for Varistors Applications // J. Eur. Ceram. Soc. 2011. V. 31. P. 1905–1913.
Ianos R., Laz I., Pacurariua C., Sfirloag P. The Influence of Combustion Synthesis Conditions on the α-Al2O3 Powder Preparation // Mater. Chem. Phys. 2011. V. 129. P. 881–886.
Громов О.Г., Савельев Ю.А., Тихомирова Е.Л., Беляевский А.Т., Локшин Э.П. Оптимизация состава и режима спекания высоковольтной варисторной ZnO-керамики // Неорган. материалы. 2017. Т. 53. № 5. С. 542–546.
Громов О.Г., Савельев Ю.А., Тихомирова Е.Л. Синтез варисторных порошков методом ускоренного сжигания и свойства керамики на их основе // ЖПХ. 2017. Т. 90. Вып. 8. С. 72–75.
Дополнительные материалы отсутствуют.
Инструменты
Неорганические материалы