Неорганические материалы, 2021, T. 57, № 4, стр. 364-371
Взаимодействие смесей HfB2 + SiC + Cr разного состава с углеродными и карбидокремниевыми подложками
Д. А. Банных 1, В. В. Лозанов 1, Н. И. Бакланова 1, *
1 Институт химии твердого тела и механохимии СО Российской академии наук
630128 Новосибирск,
ул. Кутателадзе, 18, Россия
* E-mail: baklanova@solid.nsc.ru
Поступила в редакцию 24.09.2020
После доработки 24.11.2020
Принята к публикации 26.11.2020
Аннотация
На подложки из графита и SiC методом распыления суспензий нанесены два слоя: внутренний, состоящий из Cr–SiC, и внешний, состоящий из HfB2–SiC–Cr. Процесс формирования покрытий идет через образование промежуточной жидкой фазы на основе Cr5Si3Cx. Методами РФА, СЭМ/ЭДС определены фазовый состав и морфология покрытий. Однослойное покрытие, полученное из Cr–SiC, прочно связано с графитовой подложкой, но отслаивается от SiC-подложки. Двухслойные покрытия отслаиваются и от графита, и от SiC. Термодинамический расчет позволил выявить наиболее вероятные химические реакции, протекающие в системе HfB2–SiC–Cr–С при температурах 1300–1900 K. Установлено соответствие между экспериментальными и расчетными результатами.
ВВЕДЕНИЕ
В настоящее время значительное количество исследований направлено на изучение взаимодействия между углеродными или карбидокремниевыми материалами конструкционного назначения и системами, содержащими тугоплавкие карбиды и бориды [1, 2]. Такие системы предназначены для дополнительной защиты поверхности конструкционных материалов от воздействия высокотемпературной агрессивной окислительной среды [1, 2]. Одним из наиболее распространенных методов формирования покрытий на конструкционных материалах является шликерно-обжиговый метод, который заключается в нанесении предкерамических суспензий на поверхность композита с последующей термообработкой [1–3]. Благодаря наличию спекающих добавок при термообработке происходит плавление части шликера. В связи с этим значительный вклад в процессы формирования покрытия и спекания начинают вносить капиллярные эффекты и массоперенос через жидкую фазу [4, 5]. Для эффективного формирования покрытия образующаяся при термообработке жидкость должна смачивать как поверхность подложки, так и тугоплавкие частицы в покрытии.
В настоящей работе для формирования покрытий на углеродных и карбидокремниевых подложках была использована суспензия на основе порошков диборида гафния, карбида кремния и хрома, компоненты которой известны своей окислительной устойчивостью при высоких температурах [1–6]. Особенностью данной системы является то, что хром, входящий в ее состав, взаимодействует с карбидом кремния, образуя при температуре ∼1500°С и выше жидкую фазу Cr–Si–C переменного состава [7].
Ранее было установлено, что в процессе спекания образцов, приготовленных из смесей порошков HfB2, SiC и Cr (78.5, 6.0 и 15.5 мас. % соответственно), при температурах 1500–1900°С образовывалась жидкость Cr–Si–C, при дальнейшем охлаждении которой происходило формирование новых фаз (HfC, CrB, Cr5Si3C0.5) [8]. Относительная плотность полученных при температуре 1600°C образцов достигала 92%. Полученные результаты для объемных образцов позволяют рассматривать эту систему как перспективную и для формирования покрытий на углеродных и карбидокремниевых подложках. В этом случае образование промежуточной жидкой фазы способствовало бы ускорению процессов диффузии и массопереноса при формировании покрытия и увеличивало бы адгезию покрытия к подложке.
В отличие от спекания объемных образцов, состоящих только из фаз HfB2, SiC и Cr, при формировании покрытий возможно химическое взаимодействие между покрытием и подложкой.
Целью настоящей работы являлось установление взаимодействия смесей HfB2 + SiC + Cr разного состава с модельными углеродными и карбидокремниевыми подложками.
ТЕОРЕТИЧЕСКИЙ АНАЛИЗ
Термодинамический расчет был проведен для выявления наиболее вероятных химических реакций, протекающих в системе HfB2–SiC–Cr–С в диапазоне температур 1300–1900 K. При расчетах использовали предположение, что все химические соединения являются стехиометрическими, твердые растворы отсутствуют, в реакцию вступают и образуются только твердые компоненты (термодинамические данные для жидких двойных и тройных фаз отсутствуют), также не учитывали образование интерметаллидов в системе Hf–Cr. В расчете использовали термодинамические данные ${{\Delta }_{f}}H_{{298.15}}^{0},$ $S_{{298.15}}^{0},$ $C_{p}^{0}(T)$ для следующих соединений: графит, HfC, HfB2, α-SiC, Cr, Cr7C3, Cr3C2, Cr3Si, Cr5Si3, CrB, Cr5B3, Cr3B4, CrB2 [9]. Реакции с участием Cr23C6 (Tm = 1791 K), CrSi (Tm = 1686 K) и CrSi2 (Tm= 1763 K) рассматривали только до температуры плавления этих соединений. Для сравнения химических реакций использовали приведенную на 1 моль атомов энергию Гиббса реакции $\overline {{{\Delta }_{r}}G_{T}^{0}} = \frac{{{{\Delta }_{r}}G_{T}^{0}}}{{{{N}_{{{\text{ат}}}}}}}.$
В системе HfB2–SiC–Cr–С возможно протекание трех параллельно-последовательных процессов: взаимодействие металлического хрома с карбидом кремния (процесс I), взаимодействие металлического хрома с углеродом (процесс II) и взаимодействие карбидов хрома, образующихся в первых двух процессах, с диборидом гафния (процесс III). Как показали расчеты, процессы I и II являются наиболее термодинамически выгодными ($\overline {{{\Delta }_{r}}G_{T}^{0}} \ll 0$) во всем рассчитанном интервале температур. При этом наибольшую термодинамическую вероятность имеют реакции (1) и (2) для процессов I и II соответственно. Реакции процесса III (например, реакция (3)), наоборот, имеют положительную энергию Гиббса. Следует обратить внимание, что фаза Cr3C2 является с термодинамической точки зрения более предпочтительной, чем фаза Cr7C3, в условиях избыточного содержания SiC и/или углерода [7, 10]. Образование фазы Cr3C2 из Cr7C3 объясняется сопряжением реакции (4) или (5) с реакцией (1). В условиях значительного избытка углерода фаза Cr5Si3 переходит в SiC и Cr3C2 (реакция (6)), а сопряжение реакций (1), (5) и (6) приводит к реакции (2):
(1)
$12{\text{Cr}} + 3{\text{SiC}} = {\text{C}}{{{\text{r}}}_{{\text{5}}}}{\text{S}}{{{\text{i}}}_{3}} + {\text{C}}{{{\text{r}}}_{{\text{7}}}}{{{\text{C}}}_{3}}\,\,\,\,\,\overline {{{\Delta }_{{{{r}_{1}}}}}G_{{1873}}^{^\circ }} = - 14.5,$(2)
$3{\text{Cr}} + 2{\text{C}} = {\text{C}}{{{\text{r}}}_{{\text{3}}}}{{{\text{C}}}_{2}}\,\,\,\,\,\overline {{{\Delta }_{{{{r}_{2}}}}}G_{{1873}}^{^\circ }} = - 22.9,$(3)
${\text{3Hf}}{{{\text{B}}}_{2}} + 2{\text{C}}{{{\text{r}}}_{{\text{3}}}}{{{\text{С}}}_{2}} = {\text{3HfC}} + 6{\text{CrB}} + {\text{C}}\,\,\,\,\overline {{{\Delta }_{{{{r}_{3}}}}}G_{{1873}}^{^\circ }} = + 1.9,$(4)
$2{\text{C}}{{{\text{r}}}_{{\text{7}}}}{{{\text{С}}}_{3}} + 3{\text{SiC}} = {\text{C}}{{{\text{r}}}_{{\text{5}}}}{\text{S}}{{{\text{i}}}_{3}} + 3{\text{C}}{{{\text{r}}}_{{\text{3}}}}{{{\text{C}}}_{2}} + 3{\text{C}}\,\,\,\overline {{{\Delta }_{{{{r}_{4}}}}}G_{{1873}}^{^\circ }} = + 2.3,$(5)
$3{\text{C}}{{{\text{r}}}_{{\text{7}}}}{{{\text{C}}}_{3}} + 5{\text{C}} = 7{\text{C}}{{{\text{r}}}_{{\text{3}}}}{{{\text{C}}}_{2}}\,\,\,\,\overline {{{\Delta }_{{{{r}_{5}}}}}G_{{1873}}^{^\circ }} = - 3.9,$(6)
$3{\text{C}}{{{\text{r}}}_{{\text{5}}}}{\text{S}}{{{\text{i}}}_{3}} + 19{\text{C}} = 9{\text{SiC}} + 5{\text{C}}{{{\text{r}}}_{{\text{3}}}}{{{\text{C}}}_{2}}\,\,\,\overline {{{\Delta }_{{{{r}_{6}}}}}G_{{1873}}^{^\circ }} = - 10.6.$Таким образом, в системе имеется термодинамическое сопряжение процессов I и III (в условиях избытка SiC), II и III (в условиях избытка углерода) или I, II и III. Это позволяет записать три термодинамически выгодных брутто-процесса:
(7)
$16{\text{Cr}} + 6{\text{SiC}} + 3{\text{Hf}}{{{\text{B}}}_{2}} = 3{\text{HfC}} + 2{\text{C}}{{{\text{r}}}_{{\text{5}}}}{\text{S}}{{{\text{i}}}_{3}} + 6{\text{CrB}} + 3{\text{С}}\,\,\,\overline {{{\Delta }_{{{{r}_{7}}}}}G_{{1873}}^{^\circ }} = - 7.3,$(8)
$2{\text{Cr}} + {\text{Hf}}{{{\text{B}}}_{2}} + {\text{С}} = {\text{HfC}} + 2{\text{CrB}}\,\,\,\overline {{{\Delta }_{{{{r}_{8}}}}}G_{{1873}}^{^\circ }} = - 10.7,$(9)
$24{\text{Cr}} + 7{\text{Hf}}{{{\text{B}}}_{2}} + 6{\text{SiC}} + {\text{C}} = 7{\text{HfC}} + 14{\text{CrB}} + 2{\text{C}}{{{\text{r}}}_{{\text{5}}}}{\text{S}}{{{\text{i}}}_{3}}\,\,\,\overline {{{\Delta }_{{{{r}_{9}}}}}G_{{1873}}^{^\circ }} = - 9.1.$Объединение реакций (7) и (9) приводит к уравнению (10), которое хорошо описывает ранее полученный нами экспериментальный результат [8]. Соответствие между экспериментальными и расчетными результатами указывает на применимость предложенной теоретической модели
ЭКСПЕРИМЕНТАЛЬНАЯ ЧАСТЬ
В качестве подложки были использованы пластины спеченного α-SiC (Lianyungang Baibo New Material Co., Китай, чистота 99%), графит (ГОСТ Р МЭК 60239-2014, ЭПМ, Россия). Шлифовка и полировка поверхности подложек проводились на шлифовально-полировальном станке П12М+ (ПОЛИЛАБ, Россия) c использованием алмазных суспензий. Для формирования покрытий были использованы порошки HfB2 (ТУ 6-09-03-418-76, 99%, УНИХИМ, Россия), α-SiC (GMF-15H2, 99%, Pacific Rundum Co., Япония) и хрома (ТУ 14-5-298-99, 99%, НПО РУСРЕДМЕТ, Россия). Порошковые смеси гомогенизировали с помощью планетарной мельницы АГО-2 (ЗАО “НОВИЦ”, Россия). Использованы следующие составы (мас. %): SiC : Cr = 27.9 : 72.1 (SC); HfB2 : : SiC : Cr = 78.5 : 6.0 : 15.5 (HSC). Для формирования покрытий были приготовлены суспензии порошков в этиловом спирте (массовое соотношение 1 : 10), которые распыляли на подложки со скоростью ~1 мл/мин.
Для однослойного, состоящего из SC покрытия на графите введено обозначение C/SC, для двухслойного с объемным соотношением слоев SC : HSC = 1 : 1 – C/SС/HSC, а для соотношения SC : HSC = 10 : 1 – C/SС10/HSC. Аналогичным образом обозначены образцы с покрытиями на SiC-подложке: SiC/SC, SiC/SC/HSC, SiC/SC10/HSC. Образцы с нанесенными суспензиями подвергали термообработке при 1600°С в течение 2 ч в высоковакуумной печи СНВЭ-1,7.3.1,7/20 (ООО “Призма”, г. Искитим). Микроструктура и элементный состав покрытий и поперечных шлифов образцов были исследованы с помощью сканирующего электронного микроскопа (СЭМ) ТМ-1000 (Hitachi, Япония), оснащенного ЭДС-приставкой ThermoScientific® (Oxford Cryosystems, Великобритания).
Рентгенограммы образцов были записаны на порошковом дифрактометре D8 Advance (Bruker, Германия) с характеристическим излучением CuKα в диапазоне углов 15° ≤ 2θ ≤ 90°. Рентгенофазовый анализ проводили с помощью программных пакетов Search-Match (Oxford Cryosystems, Великобритания) и TOPAS 4.2 (Bruker, Германия) с использованием баз данных PDF-4 и ICSD.
РЕЗУЛЬТАТЫ И ОБСУЖДЕНИЕ
На рис. 1а представлен СЭМ-снимок смеси порошков SiC + Cr после гомогенизации. Видно, что в смеси находится достаточно большое количество агломератов вытянутой формы, во внутренней части которых, по данным энергодисперсионной спектроскопии (ЭДС), присутствует хром, а во внешней – кремний. Возникновение таких образований можно объяснить эффектом “вдавливания” более твердой фазы (SiC) в пластичную фазу (Cr) при механических соударениях в мельнице. Из данных гранулометрического анализа (рис. 1б) видно, что на кривой присутствуют два пика с максимумами при 1 и 18 мкм. Первый максимум характеризует размеры исходных частиц SiC, второй можно отнести к агломератам, образующимся при помоле.
Рис. 1.
Морфология частиц смеси порошков SiC + Cr (а) и ее гранулометрический состав после гомогенизации (б).
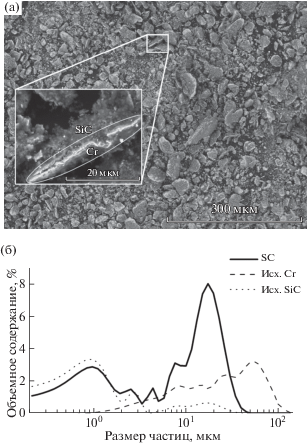
Морфология частиц смеси HSC после помола отличается от морфологии частиц смеси SC (рис. 2а). Здесь присутствуют как отдельные частицы HfB2 и SiC размером до 10 мкм, так и агломераты частиц неправильной формы, в которых методом ЭДС обнаружены гафний, кремний и хром. Смесь демонстрирует полидисперсный профиль распределения частиц по размерам (рис. 2б).
Рис. 2.
Морфология частиц смеси порошков HfB2 + + SiC + Cr (а) и ее гранулометрический состав после гомогенизации (б).
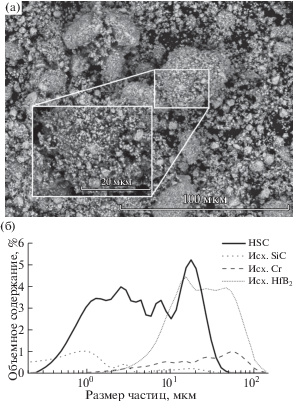
На рис. 3а, 3б представлены исходные графитовая и SiC-подложки. Морфология гомогенизированных смесей SC и HSC после их распыления в виде покрытий на графитовые и SiC-подложки не меняется. Значительные изменения в морфологии происходят после прогрева образцов при 1600°С. Из рис. 3в, 3г видно, что поверхности С/SC- и SiC/SC-образцов состоят из частиц двух типов: темные крупные ограненные вытянутые и мелкие светлые частицы, расположенные преимущественно на гранях и в стыках между темными частицами, причем на поверхности SiC/SC-образца светлые частицы попадаются очень редко. Размер темных частиц на поверхности SiC/SС-образца варьируется от 10 до 200 мкм. По данным ЭДС, эти частицы содержат кремний и, вероятно, являются фазой карбида кремния, перекристаллизованной из жидкости на основе Cr5Si3Cx в процессе формирования покрытия [10]. Отметим, что на поверхности исходной SiC-подложки такие вытянутые кристаллы отсутствуют. Светлые мелкие частицы, по данным ЭДС, содержат хром. Относительно малое содержание хромсодержащей фазы на поверхности образцов может быть следствием ее перемещения в глубь подложки при термообработке.
Рис. 3.
Морфология поверхности образцов: а – исходная графитовая подложка, б – исходная SiC-подложка, в – С/SС (1600°С), г –SiC/SС (1600°С).
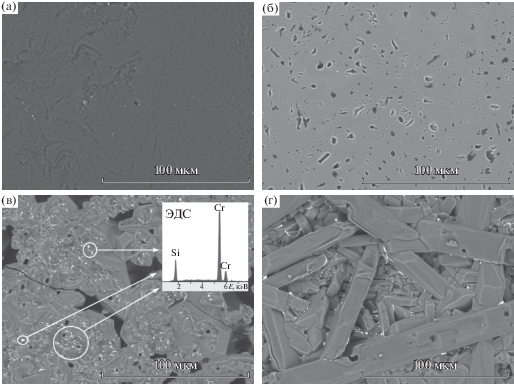
Действительно, как видно на СЭМ-снимке поперечного сечения образца C/SС, покрытие состоит из светлой хромсодержащей фазы и темных включений карбида кремния, при этом хромсодержащая часть покрытия экранирована сверху слоем карбида кремния (рис. 4а). Формирование такой микроструктуры, по-видимому, является следствием “всплывания” более легкой SiC-фазы (ср. ρSiC = 3.13 г/см3 и ${{\rho }_{{{\text{C}}{{{\text{r}}}_{{\text{5}}}}{\text{S}}{{{\text{i}}}_{{\text{3}}}}{\text{,ж}}}}}$ ≈ 4.63 г/см3 при 1600°C, оценены по данным [11, 12]). Микротрещины подложки и прилегающие к ее поверхности поры заполнены материалом покрытия, что можно объяснить затеканием жидкости, образующейся в процессе формирования покрытия. Отслаивания покрытия не наблюдается. Толщина слоя достигает 40 мкм. На рентгенограммах покрытия на графите присутствуют интенсивные пики кубического и гексагонального SiC, а также малоинтенсивные пики Cr3С2 (рис. 4в), что хорошо согласуется с наблюдаемой микроструктурой покрытия. Полученные результаты также находятся в соответствии с результатами термодинамического расчета (реакции (1), (2), (5) и (6)).
Рис. 4.
Микроструктура поперечного среза образцов с покрытием SС на графите после термообработки при 1600°С: a – общий вид, б – детали микроструктуры (участок I), в – рентгенограмма образца с покрытием.
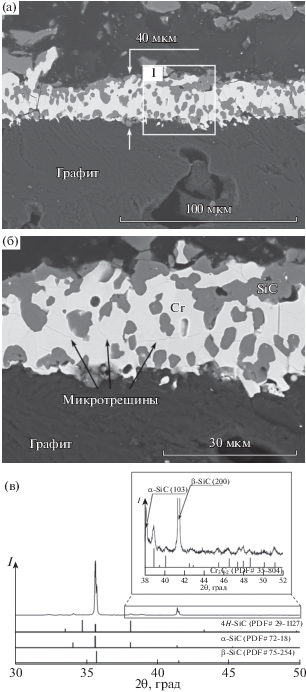
Исследование поперечного среза SiC/SС-образца методом ЭДС показывает, что хром присутствует только в местах затекания жидкости в трещины (рис. 5а). На рентгенограммах покрытия на SiC-подложке присутствуют только пики разных модификаций SiC, пики хромсодержащих фаз отсутствуют (рис. 5б). Можно предположить, что вследствие очень низкой вязкости промежуточной жидкости (${{\eta }_{{{\text{C}}{{{\text{r}}}_{{\text{5}}}}{\text{S}}{{{\text{i}}}_{{\text{3}}}}{\text{,ж}}}}}$ ≈ 5.1 мПа с при 1600°С, оценено по данным [12, 13]), большого поверхностного натяжения жидкости (~0.75 Н/м2 [14], что в 10 раз выше, чем у воды), высокой относительной плотности и низкой пористости SiC-подложки, а также вследствие отсутствия взаимодействия жидкости на основе Cr5Si3Cx с SiC жидкость не удерживается на подложке, несмотря на смачиваемость (θ ~ 32°–35° [14]). Специальные эксперименты с геометрией SiC-поверхности в виде глубокой “чаши” показали, что, действительно, при охлаждении жидкость собирается в виде отдельных “каплевидных” образований, состоящих из фаз: Cr3C2, Cr5Si3Cx, α-SiC, 4H-SiC (рис. 5в, 5г), а не в виде сплошного слоя. Полученный результат подтверждается данными о фазовом равновесии в системе Cr–Si–C, согласно которым жидкость на основе Cr5Si3Cx может сосуществовать с SiC [7, 10]. Следует заметить, что на графитовой подложке жидкость формирует сплошной слой вследствие взаимодействия Cr5Si3Cx с графитом с образованием твердых фаз SiC и Cr3C2.
Рис. 5.
СЭМ-снимок (а) и рентгенограмма (б) образца SiC/SС; СЭМ-снимок (в) и рентгенограмма (г) “каплевидных” образований на SiC-подложке.
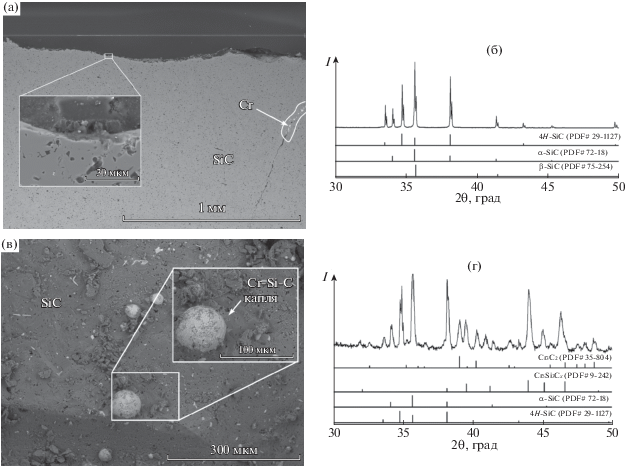
По данным СЭМ/ЭДС графитового образца с двухслойным покрытием, состоящим из внутреннего (SC) и внешнего (HSC) слоев с одинаковым объемным соотношением (рис. 6а), на поверхности образца наблюдается сложная микроструктура, состоящая из частиц трех типов: светлых размером 0.5–4 мкм, содержащих преимущественно гафний; серых хромсодержащих частиц размером 10–40 мкм, окруженных светлыми частицами; темных кремнийсодержащих частиц неправильной формы (~10 мкм). Кроме того, наблюдаются более крупные гафнийсодержащие частицы. Согласно данным ЭДС и ранее полученным данным [8], крупные гафнийсодержащие частицы представляют собой HfB2, а мелкие частицы – карбид гафния HfC, образовавшийся в ходе приготовления покрытия по реакции (4). Данные РФА покрытий, формирующихся на графитовой и SiC-подложках, подтверждают присутствие фаз HfB2, HfC, SiC, CrB и Cr5Si3Cx. В системах с десятикратным содержанием внутреннего слоя наблюдается полное превращение HfB2 в HfC (рис. 6б). Можно отметить хорошее согласие экспериментальных данных по фазовому составу покрытий с оценкой термодинамической вероятности протекания различных реакций в системе HfB2–SiC–Cr.
Рис. 6.
СЭМ-снимки и рентгенограммы двухслойного покрытия на графите и SiC: а – морфология покрытия на графите, в – микроструктура сечения образца с покрытием на SiC, б – рентгенограммы образцов с двухслойным покрытием на графите (1) и SiC (2).
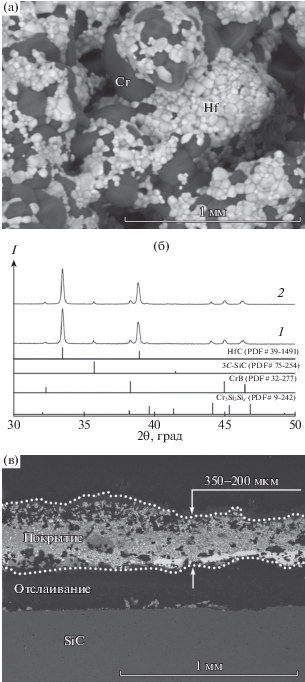
Из анализа данных СЭМ видно, что двухслойные SC/HSC-покрытия растрескиваются и отслаиваются и от графитовой, и от SiC-подложки, что, по-видимому, обусловлено разницей в коэффициентах термического расширения (КТР) подложек и компонентов покрытий (рис. 6а, 6в). Так, например, КТР Cr5Si3 или CrB отличаются от КТР SiC более чем в 2.5 раза [15]. Это накладывает некоторые ограничения на использование предложенных составов смесей HfB2 + SiC + Cr в качестве защитных покрытий для графитовых и SiC-подложек.
Полученные результаты демонстрируют применимость порошковых смесей Cr + SiC для формирования промежуточного слоя комплексных защитных покрытий на графите. Для формирования надежной комплексной системы защиты углеродных материалов необходимо модифицировать состав внешнего слоя таким образом, чтобы избежать отслаивания от подложки.
ЗАКЛЮЧЕНИЕ
На подложки из графита и карбида кремния методом распыления суспензий были нанесены два слоя: внутренний, состоящий из Cr–SiC, и внешний, состоящий из HfB2–SiC–Cr. В процессе термообработки при 1600°С образуется жидкость на основе Cr5Si3Cx, которая затем взаимодействует с подложкой и другими компонентами покрытия. Методами РФА, СЭМ/ЭДС определены фазовый состав и морфология покрытий. Термодинамический расчет позволил выявить наиболее вероятные химические реакции, протекающие в системе HfB2–SiC–Cr–С в диапазоне температур 1300–1900 K. Установлено хорошее соответствие между экспериментальными и расчетными результатами.
Однослойное покрытие, полученное из Cr–SiC, прочно связано с графитовой подложкой, но на SiC-подложке формируется в виде отдельных округлых образований, легко отслаивающихся от подложки. Двухслойные покрытия отслаиваются и от графита, и от карбида кремния.
Таким образом, для формирования надежной комплексной системы защиты графита и других углеродных материалов можно использовать порошковые смеси Cr + SiC для внутреннего слоя покрытия, однако состав внешнего слоя, предложенный в настоящей работе, необходимо оптимизировать.
Список литературы
Симоненко Е.П., Симоненко Н.П., Севастьянов В.Г., Кузнецов Н.Т. Ультравысокотемпературные керамические материалы: современные проблемы и тенденции. М.: ИП Коняхин А.В. (Book Jet), 2020. 324 с.
Lespade P., Richet N., Goursat P. Oxidation Resistance of HfB2-SiC Composites for Protection of Carbon-Based Materials // Acta Austronautica. 2007. V. 60. P. 858–864. https://doi.org/10.1016/j.actaastro.2006.11.007
Wang P., Li H., Yuan R., Wang H., Zhang Y., Zhao Z. The Oxidation Resistance of Two-Temperature Synthetic HfB2–iC Coating for the SiC Coated C/C Composites // J. Alloys Compd. 2018. V. 747. P. 438–446. https://doi.org/10.1016/j.jallcom.2018.03.043
Monteverde F. Ultra-High Temperature HfB2-SiC Ceramics Consolidated by Hot-Pressing and Spark Plasma Sintering // J. Alloys Compd. 2007. V. 428. P. 197–205. https://doi.org/10.1016/j.jallcom.2006.01.107
Sciti D., Guicciardi S., Nygren M. Densification and Mechanical Behavior of HfC and HfB2 Fabricated by Spark Plasma Sintering // J. Am. Ceram. Soc. 2008. V. 91. P. 1433–1440. https://doi.org/10.1111/j.1551-2916.2007.02248.x
Mouche P., Koyanagi T., Kato Y. Evaluation of PVD Cr and Cr Multilayer Coatings on SiC for Nuclear Fuel Cladding Applications // 10th International Conf. HT‑CM-C. Bordeaux: LCTS, 2019. P. 388. http://ht-cmc10.event-vert.org/wp-content/uploads/2019/ 09/Book-of-Abstracts-HT-CMC-10.pdf
Du Y., Schuster J.C., Perring L. Experimental Investigation and Thermodynamic Description of the Constitution of the Ternary System Cr–Si–C // J. Am. Ceram. Soc. 2000. V. 83. P. 2067–2073. https://doi.org/10.1111/j.1151-2916.2000.tb01513.x
Bannykh D., Utkin A., Baklanova N. Effect of Chromium Additive on Sintering and Oxidation Behavior of HfB2–SiC Ceramics // Ceram. Int. 2018. V. 44. P. 12451–12457. https://doi.org/10.1016/j.ceramint.2018.04.035
Binnewies M., Milke E. Thermochemical Data of Elements and Compounds. Weinheim: Wiley-VCH, 2002. 928 p. https://doi.org/10.1002/9783527618347
Pellegrini P.W., Giessen B.C., Feldman J.M. A Survey of the Cr-rich Area of the Cr-Si-C Phase Diagram // J. Electrochem. Soc. 1972. V. 119. P. 535–537. https://doi.org/10.1149/1.2404246
Li Z., Bradt R.C. Thermal Expansion and Thermal Expansion Anisotropy of SiC Polytypes // J. Am. Ceram. Soc. 1987. V. 70. P. 445–448. https://doi.org/10.1111/j.1151-2916.1987.tb05673.x
Kawanishi S., Yoshikawa T., Shibata H. Thermomigration of Molten Cr-Si–C Alloy in 4H-SiC at 1873–2273 K / J. Cryst. Growth. 2019. V. 518. P. 73–80. https://doi.org/10.1016/j.jcrysgro.2019.04.022
Баум Б.А., Гельд П.В., Кочеров П.В. Вязкость жидких кремния, хрома и его силицидов // Изв. АН СССР. Металлы. 1967. № 1. С. 62–69.
Yupko V.L., Gnesin G.G. Wetting of Silicon Carbide by Binary Si-Ti and Si–Cr Alloys / Sov. Powder Metall. Met. Ceram. 1974. V. 13. P. 59–61. https://doi.org/10.1007/BF00790688
Свойства, получение и применение тугоплавких соединений. Справ. изд. / Под ред. Косолаповой Т.Я. М.: Металлургия, 1986. 928 с.
Дополнительные материалы отсутствуют.
Инструменты
Неорганические материалы