Журнал неорганической химии, 2021, T. 66, № 8, стр. 1070-1076
Создание барьерных покрытий с помощью термической и термохимической обработки для формирования однонаправленных градиентных структур в двухфазных титановых сплавах
С. В. Скворцова a, О. Н. Гвоздева a, *, А. В. Шалин a, А. С. Степушин a, С. М. Сарычев a
a Московский авиационный институт (национальный исследовательский университет)
125993 Москва, Волоколамское ш., 4, Россия
* E-mail: gon7133@mail.ru
Поступила в редакцию 27.02.2021
После доработки 24.03.2021
Принята к публикации 27.03.2021
Аннотация
Проведен анализ влияния изотермической выдержки при нагреве в воздушной атмосфере и напыления нитрида в вакууме на закономерности формирования оксидных и нитридных покрытий на титановом сплаве ВТ6. Изучена кинетика их растворения при последующем высокотемпературном вакуумном отжиге. Показан принцип работы оксида и нитрида в качестве “барьерного” покрытия при создании однонаправленной градиентной структуры с помощью термоводородной обработки. Установлено, что создание на поверхности мелкодисперсной структуры путем термоводородной обработки позволяет повысить до 40.5 ед. HRC ее твердость по сравнению с твердостью сердцевины (33.5 ед. HRC).
ВВЕДЕНИЕ
Как правило, формирование структуры и свойств полуфабрикатов происходит в процессе их деформационной и последующей термической обработки. При этом по комплексу механических свойств такая структура не всегда удовлетворяет требованиям, предъявляемым к изделиям, поэтому необходимо проводить дополнительную обработку [1–3]. Например, в изделиях, испытывающих при эксплуатации циклические или динамические нагрузки, необходимо поверхностное преобразование структуры, при котором происходит плавный переход от одного типа структуры на поверхности к другому типу в центре [4–7]. Одним из инновационных способов создания таких структур является термоводородная обработка, основанная на обратимом легировании водородом [8–11]. Благодаря различной диффузионной подвижности атомов водорода и основных легирующих элементов на поверхности полуфабриката или изделия создается мелкодисперсная структура, а в сердцевине сохраняется неизмененная пластинчатая структура. В работах [12–15] была показана возможность применения термоводородной обработки для поверхностного формоизменения структуры полуфабриката. Это позволило в два раза увеличить предел выносливости материала по сравнению с литым состоянием, при этом ударная вязкость снизилась всего на 15%. Но для изделий, испытывающих динамические нагрузки, необходимо создание поверхностных однонаправленных градиентных структур, что требует временной защиты остальных сторон полуфабриката от проникновения водорода [1, 2, 7, 16].
Оксидная пленка, формирующаяся на поверхности титана при естественном окислении, придает ему высокие коррозионные свойства и предохраняет от проникновения газов, в частности водорода. Однако при нагревании в вакууме выше 600°С она растворяется, что приводит к объемному насыщению сплава водородом [8, 9]. Из литературных источников [17–19] известно, что на поверхности титановых сплавов можно искусственно выращивать оксидные пленки (например, при микродуговом оксидировании), препятствующие проникновению водорода. Альтернативным способом изолирования сторон полуфабриката от проникновения водорода могут стать нитридные покрытия [20–22]. Однако исследований по влиянию высокотемпературного нагрева в вакууме на нитридные покрытия на титановых сплавах не проводилось.
Настоящая работа является продолжением авторских исследований в этом направлении [23, 24]. Исследования проводили на титановом сплаве ВТ6 – одном из наиболее часто используемых в России (ВТ6с, ВТ6к, ВТ6ч) и за рубежом (Ti64, IMI318, TC4, SAT-64) [25]. В работах определены защитные свойства, достоинства и недостатки оксидных покрытий при одностороннем наводороживающем отжиге. Показан принцип их работы при создании однонаправленных градиентных структур.
Цель настоящей работы – сравнительный анализ различных способов защиты поверхности полуфабрикатов из сплава ВТ6 для создания в них однонаправленных градиентных структур с помощью термоводородной обработки.
ЭКСПЕРИМЕНТАЛЬНАЯ ЧАСТЬ
Исследования проводили на образцах, вырезанных из горячекатаной плиты титанового сплава ВТ6 толщиной 12.5 мм. Химический состав плиты соответствовал требованиям стандарта ГОСТ 19807-91 [26].
Термическую обработку в воздушной атмосфере и вакууме проводили в электропечах СНОЛ-2.2.5.1,8/10-И3 и Вега-3М соответственно. Напыление нитрида титана осуществляли в установке “Булат-6”. Толщину оксидного покрытия определяли методом измерения микротвердости на косых шлифах, толщину нитридного покрытия – с помощью толщинометра Calotest методом шарового истирания.
Наводороживающий отжиг проводили на установке Сивертса в среде чистого молекулярного водорода. Концентрацию вводимого водорода определяли по привесу с точностью 0.0001 г, концентрацию остаточного водорода после вакуумного отжига – спектральным методом на спектрографе ИСП-51 с электронной аналитической приставкой МОРС-1/2048/PCI и специализированным программным обеспечением.
Структуру исследовали на оптическом микроскопе AXIO Observer.A1m (увеличение ×1000). Глубину проникновения водорода определяли на металлографических шлифах по изменению микротвердости с нагрузкой 50 г. На каждой линии измерений ставили по 70 отпечатков с шагом 100 мкм. Твердость определяли по методу Роквелла на приборе Macromet 5100T в соответствии с ГОСТ 9013-59.
РЕЗУЛЬТАТЫ И ОБСУЖДЕНИЕ
В исходном состоянии структура плиты из сплава ВТ6 однородна и представлена β-фазой и частично деформированными пластинами α-фазы. Для формирования крупнопластинчатой структуры все образцы были подвергнуты отжигу в β-области. Полученная структура также однородна по сечению и представлена крупными β-зернами, окруженными α-пластинами, собранными в колонии.
На первом этапе было исследовано влияние времени изотермической выдержки при термической обработке в воздушной атмосфере и вакуумной ионно-плазменной обработке на стойкость и толщину покрытий, формирующихся на образцах из титанового сплава ВТ6. На основании проведенных ранее исследований [20, 21, 23] с учетом обеспечения хорошей адгезионной прочности защитных покрытий окисление проводили при температуре 900°С от 1 до 4 ч, а напыление нитрида – при 400°С от 5 до 30 мин.
Осмотр внешнего вида образцов после окисления и напыления нитрида показал, что на их поверхности образуются сплошные бездефектные оксидные и нитридные покрытия характерного коричневого и золотисто-желтого цвета соответственно (рис. 1). Увеличение времени изотермической выдержки не оказывает существенного влияния на качество и цвет покрытий.
Рис. 1.
Вид оксидного (а, б) и нитридного покрытий (в, г) после изотермической обработки (а, в) и вакуумного отжига при 800°С в течение 1 ч (б, г).
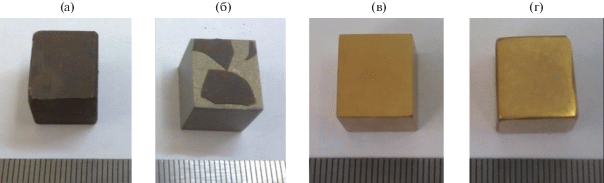
Измерение толщины покрытия показало, что со всех шести сторон толщина оксидного покрытия примерно одинаковая. Увеличение времени окисления от 1 до 4 ч приводит к увеличению его толщины примерно в 2 раза (рис. 2а). Следует отметить, что в процессе окисления происходит не только образование окалины, но и альфированного слоя твердого раствора α-фазы, насыщенного кислородом. Для нитридного покрытия установлено, что с одной стороны его толщина в ~1.7 раза меньше, чем на остальных пяти сторонах (рис. 3а). Такое существенное различие в толщине формирующегося покрытия связано с ориентацией образца относительно катода в процессе напыления. Увеличение времени напыления от 5 до 30 мин приводит к увеличению толщины покрытия в 3.7 раза (рис. 3а).
Рис. 2.
Толщина оксидного и альфированных слоев после изотермического окисления в течение разного времени (а) и после вакуумного отжига при 800°С в течение 1 ч (б).
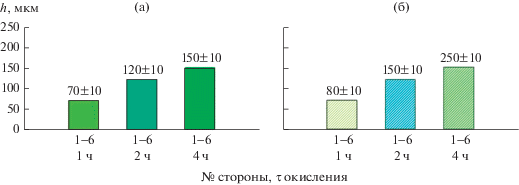
Рис. 3.
Толщина нитридного покрытия после изотермического напыления в течение различного времени (а) и после вакуумного отжига при 800°С в течение 1 ч (б).
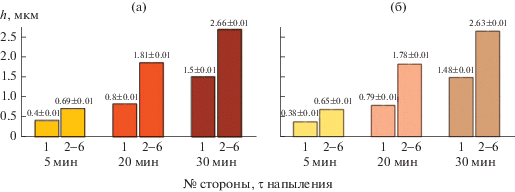
Первые этапы процесса наводороживающего отжига происходят в вакууме: образцы вакуумируют, нагревают до заданной температуры и проводят изотермическую выдержку для приведения системы в равновесие. Поэтому для оценки стойкости сформированных защитных покрытий все образцы были подвергнуты вакуумному отжигу при температуре 800°С в течение 1 ч.
Анализ полученных результатов показал, что вакуумный отжиг приводит к частичному растворению оксидного покрытия, сформированного в процессе изотермической выдержки при 900°С в течение 1 ч, и к полному его сохранению после выдержки в течение 4 ч (рис. 1а). После вакуумного отжига наблюдается увеличение протяженности окисленного слоя от 20 до 40% (рис. 2б). Это обусловлено диффузией кислорода в глубь металла. В то же время обработка в вакууме не оказывает влияния на внешний вид (рис. 1г) и толщину нитридного покрытия при напылении в течение различного времени (рис. 3б).
Таким образом, установлено, что лучшими защитными свойствами обладает оксидное покрытие, сформированное в процессе изотермической выдержки в воздушной атмосфере при температуре 900°С в течение 4 ч. А для нитридных покрытий время нанесения не оказывает влияния на их стойкость при последующей обработке в вакууме. Поэтому для оценки способности оксидных и нитридных покрытий противостоять проникновению водорода были выбраны образцы, сформированные в процессе окисления при 900°С в течение 4 ч и напыления нитрида при 400°С в течение 30 мин.
Выбор температуры и концентрации водорода для наводороживающего отжига осуществляли на основании полученных ранее фундаментальных закономерностей его взаимодействия с титановыми сплавами разных классов [8, 9], а также с учетом особенностей одностороннего поглощения водорода. Поэтому наводороживание проводили при температуре 800°С до концентраций 0.3−0.5% водорода. Перед началом наводороживающего отжига с одной стороны образца удаляли оксидное покрытие с альфированным слоем и нитридное покрытие путем механической обработки. Следует отметить, что в случае удаления окалины выбор стороны не имел значения, в то время как для нитридного покрытия имел – его удаляли со стороны, имеющей наименьшую толщину.
Во избежание протекания процессов диффузии основных легирующих элементов и перераспределения водорода сразу после завершения процесса поглощения проводили ускоренное охлаждение.
Анализ распределения микротвердости по сечению образцов после наводороживающего отжига показал, что с увеличением концентрации вводимого водорода глубина его проникновения со стороны, свободной от защитного оксидного или нитридного покрытия, изменяется по параболической зависимости (рис. 4). Причем при одной и той же концентрации водорода глубина преобразованной структуры больше на образце с нитридным защитным покрытием (рис. 4а, 4б). Режим наводороживающего отжига обеспечивает условия, при которых практически весь водород концентрируется в приповерхностном слое образца, поэтому преобразование структуры происходит не по всему сечению, а только на определенную глубину (рис. 5). Поэтому по мере удаления от поверхности в глубь образцов вследствие снижения содержания водорода происходит закономерная последовательная смена структур: (α" + β)-, (α" + β + α)-, (α + β)-, т.е. формируется однонаправленная или линейная градиентная структура. Так, на образце с защитным оксидным покрытием на глубине 4000 мкм и с нитридным покрытием на глубине 6000 мкм структура уже не отличается от отожженного состояния (рис. 5).
Рис. 4.
Изменение глубины проникновения водорода со стороны без защитного покрытия (а, в) и со стороны с защитным (б, г) оксидным (б) и нитридным (г) барьерным покрытием.
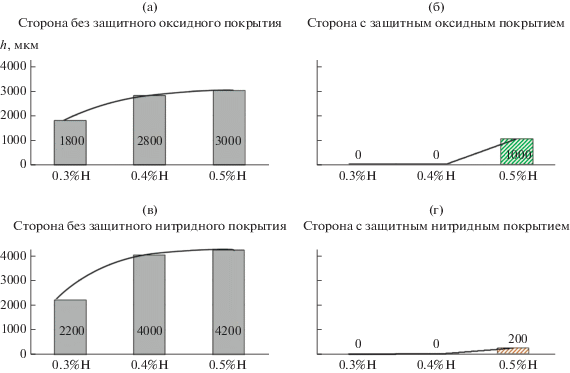
Рис. 5.
Изменение структуры по глубине образцов после наводороживающего отжига при 800°С до концентрации водорода 0.4% со стороны, свободной от оксидного (а) и нитридного (б) барьерного покрытия.
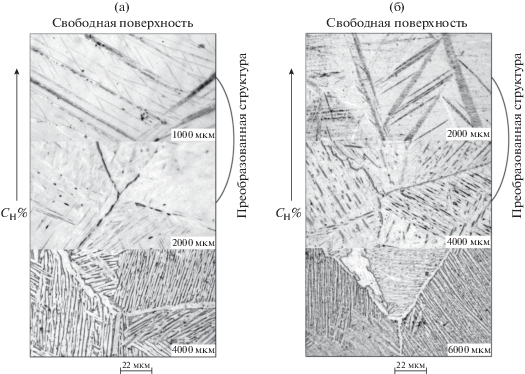
Изучение структуры со сторон, “защищенных” оксидным покрытием, показало, что уже на расстоянии 100 мкм от поверхности образцов, предварительно наводороженных до 0.3 и 0.4% водорода, формируется (α + β)-структура, что свидетельствует о практически полном отсутствии проникновения водорода (рис. 5в). Увеличение концентрации водорода до 0.5% приводит к частичному растворению оксидного покрытия, проникновению водорода и, как следствие, к формированию (α" + β)-структуры на глубину до 1000 мкм. Вероятно, именно с этим связано значительно меньшее увеличение толщины преобразованной структуры со стороны, свободной от оксидного покрытия, при 0.5% водорода по сравнению с 0.4% водорода (рис. 4а).
Исследование структуры и измерение микротвердости на образцах со сторон, изолированных нитридным покрытием и предварительно наводороженных до 0.3 и 0.4% водорода, показало аналогичные результаты. Проникновение водорода через нитридный слой не зафиксировано (рис. 4г). При концентрации 0.5% водорода хоть и наблюдается его проникновение, однако его глубина составляет не более 200 мкм (рис. 4 г). Можно предположить, что для увеличения защитных свойств нитридного покрытия при больших концентрациях водорода необходимо увеличить его толщину за счет времени нанесения.
На заключительном этапе работы для удаления водорода до безопасных концентраций (0.006%) и формирования окончательной градиентной структуры был проведен вакуумный отжиг при температуре 625°С образцов с покрытиями обоих видов, предварительно наводороженных до концентрации водорода 0.4%. Предварительно все образцы подвергали механической обработке для удаления барьерного покрытия.
Проведенные исследования показали, что в процессе дегазации при низкотемпературном вакуумном отжиге развивается (β → α)-превращение и формируется дисперсная структура в приповерхностных слоях со стороны, с которой перед наводороживающем отжигом было удалено барьерное покрытие. По мере удаления от поверхности в глубь образца наблюдается уменьшение степени диспергации структурных составляющих и на глубине 4000−6000 мкм структура уже мало отличается от отожженного состояния (рис. 6). При этом твердость приповерхностного слоя с дисперсной (α + β)-структурой составляет ~40.5 ед. HRC, а внутренний слой с неизменной крупнопластинчатой (α + β)-структурой обеспечивает твердость на уровне 33.5 ед. HRC. Таким образом, сформированная однонаправленная градиентная структура, изменяющаяся от мелкодисперсной на поверхности до крупнопластинчатой в центре, способствует повышению динамической стойкости образцов из сплава ВТ6.
ЗАКЛЮЧЕНИЕ
Проведенный сравнительный анализ защитных свойств оксидных и нитридных покрытий показал, что формирующееся при вакуумной ионно-плазменной обработке нитридное покрытие, в 100 раз более тонкое, чем оксидное, практически не пропускает водород при наводороживающем отжиге. Следует отметить, что хотя технология нанесения нитридного покрытия более дорогостоящая по сравнению с технологией оксидирования, но за счет существенно меньшей его толщины, возможно, не требуется его последующее удаление с готового изделия. Показано, что оба покрытия эффективно предотвращают проникновение водорода до концентраций не более 0.4%. Установлено, что при концентрации водорода более 0.4% нитридное покрытие имеет более высокие защитные свойства по сравнению с оксидным покрытием. Показана принципиальная возможность однонаправленного преобразования структуры в плите из титанового сплава ВТ6 путем совместной термической или химико-термической обработки и наводороживающего отжига. Варьируя концентрацию вводимого водорода, можно получать различный по глубине слой с преобразованной структурой. Показано, что создание в приповерхностных слоях дисперсной структуры позволяет повысить твердость до 40.5 ед. HRC. Таким образом, сформированная с помощью термоводородной обработки однонаправленная градиентная структура в образцах из сплава ВТ6 может обеспечить повышенную ударную вязкость и замедленную скорость распространения трещины в образцах.
Список литературы
Купрюнин Д.Г., Гавзе А.Л., Чусов С.Ю. // Вопросы оборонной техники. 2017. С. 114.
Григорян В.А., Кобылкин И.Ф., Маринин В.М., Чистяков Е.Н. Материалы и защитные структуры для локального и индивидуального бронирования. М.: РадиоСофт, 2008. 406 с.
Петров А.П., Шлёнский А.Г. // Технология легких сплавов. 2019. № 3. С. 76.
Ильин А.А., Скворцова С.В., Гуртовая Г.В., Ламзин Д.А. // Авиационная промышленность. 2007. № 4. С. 3.
Vozdvizhenskaya M.V., Mamonov A.M., Vozdvizhensky I.N. // Bulletin of the Rybinsk State Aviation Technological Academy named after P.A. Solovieva. 2018. № 3. P. 104.
Рааб Г.И., Кодиров И.С., Алешин Г.Н. и др. // Вестник магнитогорского ГТУ им. Г.И. Носова. 2019. Т. 17. № 1. С. 64.
Анастасиади Г.П., Сильников М.В. // Работоспособность броневых материалов. СПб.: Астерион, 2004. 624 с.
Ильин А.А., Колачёв Б.А., Носов В.К., Мамонов А.М. Водородная технология титановых сплавов. М.: МИСИС, 2002. 392 с.
Колачев Б.А., Ильин А.А., Носов В.К., Мамонов А.М. // Технология легких сплавов. 2007. № 3. С. 10.
Kollerov M.Yu., Mamonov A.M., Spektor V.S. et al. // Metal Sci. Heat Treatment. 2016. V. 58. № 56. P. 335.
Mamonov A.M., Zasypkin V.V., Agarkova E.O., Caфapян A.И. // Titan. 2016. № 1. P. 20.
Коваленко В.В. Физическая основа формирования и эволюции градиентных структурно-фазовых состояний в сталях и сплавах. Новокузнецк: Полиграфист, 2009. С. 557.
Скворцова С.В., Спектор В.С., Куделина И.М. и др. // Технология легких сплавов. 2011. № 2. С. 37.
Senkevich K.S., Skvortsova S.V., Kudelina I.M. et al. // Russ. Metallurgy (Metally). 2014. P. 66.
Mamonov A.M., Agarkova E.O., Zhilyakova M.A. et al. // Metal Sci. Heat Treatment. 2018. T. 60. № 1–2. C. 80. https://doi.org/10.1007/S11041-018-0243-0
Илларионов А.Г., Жлоба А.В., Ледер М.О. и др. // Титан. 2018. № 2. С. 13.
Shatalov V.K., Lysenko L.V., Shtokal A.O. et al. // Protection Metals Phys. Chem. Surfaces. 2019. T. 55. № 7. P. 1352.
Betsofen S.Y., Ashmarin A.A., Lozovan A.A. et al. // J. Synch. Investig. 2016. V. 10. P. 705. https://doi.org/10.1134/S1027451016040054
Lukina E.A. // J. Phys.: Conf. Series. 2019. V. 1396. № 1. Art. 012030.
Lukina E.A., Kollerova M.Y., Panin P.V. et al. // Materials Today: Proceedings. 2017. P. 4675.
Mamonov A.M., Sarychev S.M., Slezov S.S., Chernyshova Yu.V. // Metal Sci. Heat Treatment. 2018. V. 60. № 5−6. P. 290. https://doi.org/10.1007/s11041-018-0274-6
Lozanov V.V., Il’in I.Yu., Baklanova N.I. et al. // Russ. J. Inorg. Chem. 2020. V. 65. P. 1781.
Gvozdeva O.N., Shalin A.V., Stepushin A.S. // IOP Conf. Ser. Mater. Sci. Engineer. 2020 V. 709. № 1. Art. 022082. https://doi.org/10.1088/1757-899X/709/2/022082
Скворцова С.В., Гвоздева О.Н., Шалин А.В., Степушин А.С. // Титан. 2019. № 3. С. 25.
Ильин А.Н., Колачев Б.А., Полькин И.С. Титановые сплавы. Состав, структура, свойства. Справочник. М., 2009. 520 с.
ГОСТ 26492-85. “Прутки, катаные из титана и титановых сплавов. Технические условия”. М.: Изд-во стандартов, 32 с.
Дополнительные материалы отсутствуют.
Инструменты
Журнал неорганической химии