Журнал неорганической химии, 2022, T. 67, № 2, стр. 177-184
Синтез железо-иттербиевого граната с применением анионообменного осаждения
С. В. Сайкова a, b, *, Е. А. Киршнева a, b, Н. П. Фадеева a, М. В. Пантелеева a, Е. В. Пикурова a, А. С. Самойло b
a Институт химии и химической технологии СО РАН – обособленное подразделение ФИЦ КНЦ СО РАН
660036 Красноярск, Академгородок, 50/24, Россия
b Сибирский федеральный университет
660041 Красноярск, Свободный пр-т, 79, Россия
* E-mail: ssai@mail.ru
Поступила в редакцию 22.06.2021
После доработки 06.10.2021
Принята к публикации 07.10.2021
- EDN: KPLFOZ
- DOI: 10.31857/S0044457X22020143
Аннотация
Редкоземельные феррит-гранаты (РЗФГ) обладают ярко выраженными магнитными и оптическими свойствами и широко применяются в магнитооптике, лазерной и СВЧ-технике. В данной работе предложен метод получения порошков Yb3Fe5O12 со средним размером кристаллитов 47 ± 9 нм, который заключается в совместном анионообменном осаждении железа(III) и иттербия с дальнейшим отжигом полученного продукта при 1100°C. Определена скорость и оптимальные условия процесса анионообменного осаждения, а также параметры термообработки прекурсоров. Продукты исследованы с помощью химического и рентгенофазового анализа, дифференциальной сканирующей калориметрии и электронной микроскопии. Метод перспективен для получения других РЗФГ и ферритов цветных металлов.
ВВЕДЕНИЕ
Феррит-гранат иттербия образован оксидами железа Fe2O3 и иттербия Yb2О3, проявляет полупроводниковые свойства и наряду с феррит-шпинелями и ортоферритами принадлежит к классу магнитомягких высокочастотных ферритовых материалов. Общая формула редкоземельных феррит-гранатов (РЗФГ) имеет вид M3Fe5O12, где M – редкоземельный элемент [1–3]. Феррит-гранаты редкоземельных металлов (РЗМ) имеют кубическую объемно центрированную кристаллическую решетку. Атомы кислорода образуют три типа подрешеток: тетраэдрическую, октаэдрическую и додекаэдрическую, в пустотах которых размещаются катионы. Бóльшая часть ионов Fe3+ занимает тетраэдрические d-положения, меньшая часть – октаэдрические а-положения, а ионы М3+ расположены в додекаэдрических пустотах (с-положения) [4–9].
Магнитные и оптические свойства РЗФГ определяют их широкое применение в различных сферах, таких как магнитооптика, лазерная и СВЧ-техника. Они используются в диэлектрических резонаторных антеннах, спиновых логических устройствах, магнитооптических фильтрах, при создании лазеров и микроволновых монолитных интегральных схем и т.д. [10, 11].
Основными методами получения соединений со структурой граната являются твердофазный синтез, а также растворные методы, такие как золь-гель или метод химического соосаждения. Классический твердофазный синтез до сих пор остается основным промышленным методом получения редкоземельных феррит-гранатов. Так, в работах [12–15] исходные оксидные порошки измельчали в течение 12–24 ч и отжигали при температуре 1100–1400°С. В результате высокотемпературного отжига образовывались агломерированные продукты с частицами размером ~5 мкм, которые могут содержать примеси от мелющих тел.
При использовании растворных методов смешение катионов металлов происходит на молекулярном уровне в растворе. Полученные прекурсоры однородны по составу и химически активнее, чем оксиды, используемые при твердофазном синтезе. Это позволяет снизить температуру термообработки при получении РЗФГ растворными методами. Однако в этом случае необходим тщательный подбор и контроль условий синтеза, таких как значение рН, скорость подачи, концентрация реагентов и т.д. Кроме того, особенностью золь-гель синтеза является использование дорогостоящих органических добавок, иногда довольно токсичных [16, 17].
В работах [18, 19] для получения феррит-граната иттербия и других редкоземельных металлов применяли метод химического осаждения с использованием мочевины. Получить продукт, не содержащий примесей побочных фаз, удалось лишь после термообработки при 1200–1400°C. Наличие примесей ионов осадителя в прекурсорах является существенным недостатком данного метода и может приводить к увеличению температуры термообработки и агломерации продуктов.
Метод анионообменного осаждения [20–23] позволяет избежать указанных недостатков. Анионообменное осаждение предполагает использование в качестве источника ионов осадителя (ОН–, ${\text{CO}}_{3}^{{2 - }}$ и др.) ионообменных органических смол (анионитов). Анионы раствора в ходе ионного обмена сорбируются анионитом, что позволяет исключить загрязнение конечного продукта и избежать стадий многократной промывки и очистки. Постоянное легко контролируемое значение pH в ходе процесса осаждения также является отличительной чертой данного процесса. Благодаря этому обеспечивается однородность частиц продукта по свойствам, морфологии и размерам, а также сохранение его стехиометрии в результате практически полного осаждения ионов. С помощью данного метода ранее нами были получены как простые гидроксиды и оксиды никеля и кобальта, так и их ферриты, а также феррит-гранаты иттрия (Y3Fe5O12), диспрозия (Dy3Fe5O12) и гадолиния (Gd3Fe5O12) [23–30].
Цель настоящей работы – исследование влияния реакционных параметров на анионообменное соосаждение ионов Fe3+ и Yb3+, поиск оптимальных условий синтеза железо-иттербиевого граната и изучение полученного продукта физическими и химическими методами.
ЭКСПЕРИМЕНТАЛЬНАЯ ЧАСТЬ
В работе использовали следующие реактивы: нитрат железа(III) Fe(NO3)3 · 9H2O (х. ч., Химреактивснаб), хлорид иттербия YbCl3 · 6H2O (99.99%, Sigma-Aldrich), гелевые сильноосновные аниониты А400 (Purolite) и АВ-17-8 (ГОСТ 20301-74, ПАО “АЗОТ”), содержащие в качестве ионогенных групп четвертичные триметиламмониевые группы.
Подготовку анионитов к эксплуатации и перевод их в ОН- и СО3-форму в статических условиях осуществляли по описанным ранее методикам [24]. Для получения карбонатной формы (А-400(CO3) и АВ-17-8(CO3)) исходные аниониты в Сl-форме приводили в контакт в течение 1 ч с 1 М раствором Na2CO3 (т : ж = 1 : 2). Обработку повторяли четыре раза, после чего аниониты промывали водой до рН 6–7 и хранили под слоем воды.
Гидроксидную форму (АВ-17-8(OH)) получали путем обработки исходного анионита в Сl-форме 1 М NаОН в течение 1 ч (т : ж = 1 : 3), затем 5–6 раз 2 М NаОН (т : ж = 1 : 3) по 1 ч. Переведенный в ОН-форму анионит дополнительно очищали от примесей карбонат-ионов. Для этого его обрабатывали водной суспензией Ca(OH)2 при перемешивании в течение 12 ч. Суспензию получали путем взаимодействия оксида кальция с водой, освобожденной от CO2 с помощью длительного кипячения. После этого анионит отмывали от фазы СаСО3 и избыточной щелочности очищенной от СО2 водой до нейтральной реакции и для предотвращения сорбции углекислого газа также хранили анионит под слоем воды. Определение статической обменной емкости анионитов (СОЕ, ммоль-экв/мл) проводили по 0.1 М HCl, как описано в [ГОСТ 20255.1-89].
Для проведения анионообменного осаждения рассчитанный объем анионита приводили в контакт со смесью водных 0.24 М растворов YbCl3 и Fe(NO3)3, взятых в молярном соотношении nYb : nFe = 3 : 5, соответствующем стехиометрии граната. Процесс проводили в течение 1 ч при комнатной температуре и перемешивании на магнитной мешалке (способ I).
Для увеличения скорости отслаивания и повышения выхода продукта в некоторых экспериментах использовали осаждение с температурным градиентом (способ II). В этом случае анионообменное осаждение осуществляли, как указано выше, при комнатной температуре в течение 45 мин, после чего реакционную смесь быстро нагревали до 60°C и проводили процесс при этой температуре 10 мин (с учетом времени нагрева), затем систему помещали на ледяную баню и охлаждали до 12°C в течение 5 мин. Общее время – 1 ч.
Еще один использованный вариант осаждения с температурным градиентом (способ III) заключался в следующем: осаждение проводили при температуре 60°C в течение 55 мин, после чего охлаждали на ледяной бане до 12°C в течение 5 мин. Общее время – 1 ч.
После завершения процесса осаждения анионит отделяли, пропуская смесь через сито с диаметром отверстий 0.25 мм, промывали дистиллированной водой и подвергали элюированию, приводя его в контакт с 1 М НNО3 3 раза в течение 1 ч. Полученный осадок отделяли с помощью центрифугирования, высушивали при 60°C и подвергали отжигу для формирования феррит-граната иттербия. Термическую обработку осуществляли при температурах 800–1100°C в течение 4 ч (без учета времени, необходимого для нагрева печи до заданной температуры). Навески образца помещали в холодную муфельную печь, скорость нагрева которой составляла 10 град/мин. По истечении 4 ч обработанные порошки извлекали из горячей печи и охлаждали на воздухе до комнатной температуры (время охлаждения 2 ч).
Измерение электропроводности системы с целью отслеживания скорости и полноты осаждения железа(III) и иттербия проводили на кондуктометре Мультитест КСЛ-101 (НПП “Семико”) по методике, описанной в [23].
Элементный состав осадков устанавливали методами комплексонометрического (совместное содержание ионов гадолиния и железа) и иодометрического (индивидуальное содержание железа) титрования [31]. Ошибка используемых методов не превышала 1%.
Степень осаждения (С.о.), выход осадка (η) и молярную долю (χ) катионов иттербия и железа(III) в фазе анионита (после элюирования) рассчитывали по формулам, приведенным в [23].
Для получения микрофотографий поверхности зерна анионита в ходе анионообменного осаждения небольшие его порции (m = 0.2 г) отбирали через определенные промежутки времени (1 и 24 ч), промывали дистиллированной водой, высушивали при 60°C и фиксировали на алюминиевой подложке размером 5 × 7 × 0.3 мм с помощью эпоксидной смолы. Микрофотографии поверхности зерна анионита выполнены на настольном сканирующем электронном микроскопе ТМ-3000 (Hitachi, Япония).
Термический анализ проводили на синхронном термическом анализаторе SDT Q600, совмещенном с ИК-Фурье-спектрометром Nicolet 380 с TGA/FT-IR интерфейсом (приставка для анализа газовой фазы). Съемку термограмм осуществляли при нагревании со скоростью 10 град/мин в атмосфере воздуха, скорость продувки воздуха составляла 50 мл/мин.
Съемку рентгенограмм выполняли на порошках в диапазоне углов 5° < 2θ < 70° с шагом 0.03° и скоростью сканирования 1.5 град/мин на автоматизированном рентгеновском дифрактометрическом оборудовании фирмы Shimadzu XRD-7000S (излучение CuKα).
Исследование продуктов методом ПЭМ проводили на просвечивающем электронном микроскопе HT-7700 (Hitachi, Япония). Подготовка к исследованию проходила следующим образом: к образцу добавляли этиловый спирт, после чего подвергали ультразвуковому диспергированию в течение 5 мин. Каплю полученной суспензии наносили на медную сетку диаметром 3 мм и высушивали при комнатной температуре.
РЕЗУЛЬТАТЫ И ОБСУЖДЕНИЕ
Исследование скорости анионообменного соосаждения железа и иттербия
Для образования монофазного граната важно добиться полного осаждения катионов металлов. Анионообменное соосаждение ионов иттербия и железа(III) в случае использования анионита в ОН-форме можно представить следующим уравнением:
(1)
$\begin{gathered} 24{\text{RОН}} + 3{\text{YbС}}{{{\text{l}}}_{3}} + 5{\text{FeС}}{{{\text{l}}}_{3}} \to \\ \to 24{\text{RСl}} + 3{\text{YbО}}{{{\text{Н}}}_{3}}{\kern 1pt} \downarrow + {\text{ }}5{\text{FeО}}{{{\text{Н}}}_{3}}{\kern 1pt} \downarrow , \\ \end{gathered} $В процессе анионного обмена анионы раствора переходят в фазу анионита, а катионы связываются высвобожденными анионами смолы в малорастворимые соединения, что приводит к снижению электропроводности системы. Основываясь на этом положении, осуществляли контроль за скоростью и полнотой осаждения катионов металлов путем измерения электропроводности реакционной смеси. Рис. 1 демонстрирует зависимости степени осаждения железа(III) и иттербия от времени, типа и формы анионита. Рис. 2 отображает аналогичную зависимость для смеси катионов.
Рис. 1.
Зависимости степени анионообменного осаждения (способ I) ионов железа(III) (а) и иттербия (б) от времени и типа применяемого анионита: 1 – А400(СО3), 2 – АВ-17-8 (СО3), 3 – АВ-17-8 (ОН).
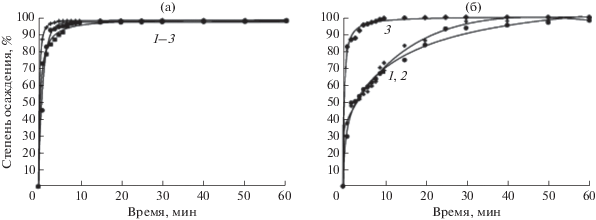
Рис. 2.
Зависимости степени совместного анионообменного осаждения ионов иттербия и железа(III) от времени и типа применяемого анионита: 1 – А400(СО3), 2 – АВ-17-8 (СО3), 3 – АВ-17-8 (ОН).
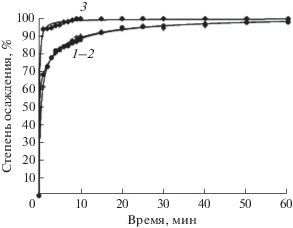
Вследствие низкой величины произведения растворимости Fe(OH)3 (6.3 × 10–38) скорость и полнота осаждения железа(III) (рис. 1а) очень высоки и практически не зависят от типа анионита и природы противоиона. Однако эти факторы являются определяющими при осаждении иттербия (рис. 1б).
Наибольшая скорость осаждения иттербия достигается при использовании анионита АВ-17-8 в ОН-форме, поскольку в этом случае наблюдается высокое значение pH – 10.9–11.0 для ОН-формы по сравнению с 6.8–7.0 для всех остальных используемых анионитов (табл. 1).
Таблица 1.
Условия и результаты совместного анионообменного осаждения железа(III) и иттербия
Номер образца | Марка и форма анионита | Способ осаждения | Время, ч | С.о., % | χ, % | pH | η, % | nYb : nFe |
---|---|---|---|---|---|---|---|---|
1 | А-400 (СО3) | I | 1 | 98.8 | 16 | 6.8 | 72 | 0.6 |
2 | АВ-17-8(СО3) | I | 1 | 99.3 | 18 | 7.0 | 71 | 0.6 |
3 | 24 | 99.8 | 6 | 7.0 | 87 | 0.6 | ||
3 | AB-17-8 (OH) | I | 1 | 99.8 | 13 | 11.0 | 79 | 0.6 |
4 | II | 1 | 99.8 | 5 | 11.0 | 88 | 0.6 | |
5 | III | 1 | 99.8 | 7 | 11.0 | 86 | 0.6 |
Вероятно, это связано с более высокой по сравнению с Fe(OH)3 растворимостью гидроксида иттербия (2.9 × 10–24), а также с тем, что иттербий, в отличие от железа(III), при взаимодействии с карбонат-ионами образует гидроксокарбонаты переменного состава Yb(OH)3 – 2x(CO3)x, а при избытке CO3-ионов – растворимые карбонатные комплексы [Yb(CO3)n](2n– 3)– (n = 1–4) [32].
Следует отметить, что совместное осаждение иттербия и железа(III) анионитами в карбонатной форме (рис. 2) протекает быстрее и полнее, чем осаждение только иттербия: за 10 мин достигается степень осаждения 85%. Возможно, это результат того, что фаза гидроксида железа выступает коллектором иттербийсодержащей фазы.
Таким образом, совместное осаждение ионов иттербия и железа целесообразно проводить с использованием анионита АВ-17-8 в ОН-форме, поскольку в этом случае достигается практически полное (99.8%) осаждение металлов уже за 10 мин осуществления процесса.
Определение оптимальных условий анионообменного соосаждения железа и иттербия
В табл. 1 представлены результаты совместного анионообменного осаждения ионов иттербия и железа(III) в течение 1 ч. Проведение процесса в соответствии со способом I при использовании анионитов А-400 и АВ-17-8 в карбонатной форме обеспечивает выход осадка 71–72%. При этом молярная доля металлов в фазе анионита довольно высока – 16 и 18% соответственно. При использовании АВ-17-8(ОН) в тех же условиях за счет большего значения pH при осаждении выход осадка увеличивается до 79%, как и в случае использования карбонатной формы анионита, значительная доля металлов (13%) фиксируется в фазе сорбента. Ранее [23, 30] нами было показано, что это происходит вследствие образования поверхностного осадка, который фиксируется на зерне ионообменной смолы и не удаляется в ходе обычных процедур отделения ионита от продукта. Образование поверхностного осадка на смоле – первая стадия анионообменного осаждения. По мере протекания процесса толщина осадка увеличивается до 1 мкм, и он отслаивается, формируя отдельную фазу. Время, необходимое для отслаивания осадка, определяется его адгезионными свойствами и условиями осуществления анионообменного осаждения [32]. Исследование зерен анионита АВ-17-8(СО3) методом сканирующей электронной микроскопии (рис. 3а) позволяет увидеть, что через 1 ч после начала синтеза значительная часть поверхности зерна покрыта слоем осадка. При проведении синтеза в течение 24 ч количество поверхностного осадка на зерне анионита уменьшается, а выход продукта осаждения в виде отдельной фазы увеличивается до 87% (рис. 3б, табл. 1).
Рис. 3.
Микрофотографии поверхности зерен анионитов АВ-17-8 в СО3-форме (а – спустя 1 ч синтеза (способ I); б – спустя 24 ч синтеза (способ I)) и АВ-17-8 в ОН-форме (в – спустя 1 ч синтеза (способ II)) в процессе совместного анионообменного осаждения ионов железа(III) и иттербия.
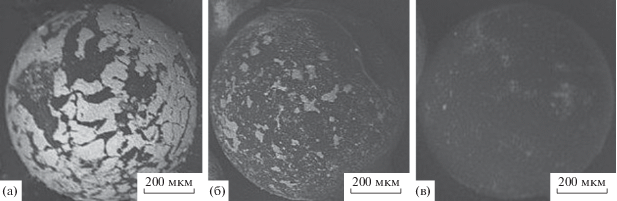
Применение температурного градиента (способы II, III) обеспечивает увеличение отслаивания поверхностного осадка, что приводит к значительному повышению (до 86–88%) выхода продукта осаждения и уменьшению содержания металлов в анионите (до 5–7%) уже после 1 ч проведения процесса (рис. 3в). Этот результат можно объяснить различными коэффициентами температурного расширения ионообменной смолы и поверхностного осадка. Анионообменное осаждение по способу II проводится при более низкой температуре, чем по способу III, и обеспечивает высокий выход осадка, поэтому применение данного варианта предпочтительнее. В связи с этим для анионообменного осаждения был выбран более дешевый и доступный отечественный анионит АВ 17-8 в ОН-форме, поскольку с его использованием достигнуты максимальные значения степени осаждения и выхода продукта (табл. 1).
Исследование продукта анионообменного соосаждения железа и иттербия химическими и физическими методами
По данным элементного анализа (табл. 1), полученные продукты осаждения соответствуют стехиометрии граната Yb3Fe5O12 и не содержат анионов-примесей ${\text{NO}}_{3}^{ - }$ и Cl–. На рис. 4 представлены данные термического анализа образца 4.
Рис. 4.
Термограмма (кривые ТГ, ДСК) образца 4 (а) и зависимость оптической плотности выделяющихся газов (Н2О) от температуры (б).
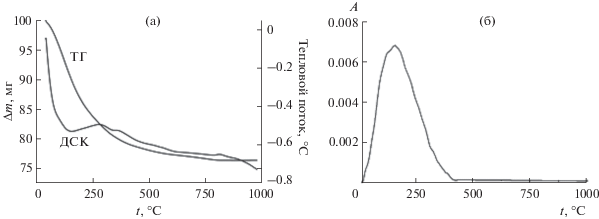
На кривой ДСК наблюдается выраженный минимум при 130°C и гораздо более слабый при температуре 360°C, что можно объяснить протекающими одновременно процессами удаления сорбированной воды и деструкции ОН-ионов гидроксидов. Выше 400°C можно заметить незначительную потерю массы, не связанную с выделением воды. Вероятно, при этой температуре происходит разложение примесных карбонат-ионов, источником которых является углекислый газ воздуха, сорбированный образцом при высушивании. Общая потеря массы образца составляет 23%. Эффект, связанный с кристаллизацией фазы граната, на термограмме не наблюдается, поэтому для получения Yb3Fe5O12 термический отжиг образцов проводили в широком температурном интервале (800–1100°C).
Результаты рентгенофазового анализа образца 4, прошедшего термическую обработку при температурах 800–1100°C в течение 4 ч, представлены на рис. 5. При температурах 800–1000°C (рис. 5а–5в) образуется смесь Yb3Fe5O12 и ортоферрита YbFeO3, кристаллизующегося в структуре перовскита [33].
Рис. 5.
Рентгенограммы образца 4, прошедшего термическую обработку в течение 4 ч при температурах: а – 800, б – 900, в – 1000, г – 1100°C.
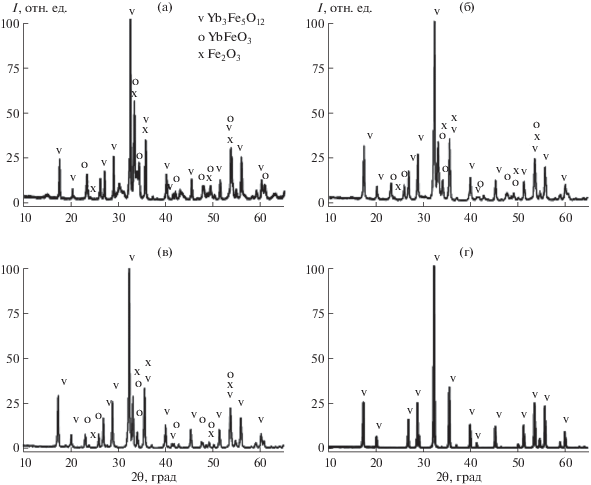
При этом с увеличением температуры содержание фазы граната увеличивается (с 65% при 800°C до 71% при 1000°C), а при проведении отжига при 1100°C в течение 4 ч формируется чистая фаза Yb3Fe5O12 (рис. 5г).
Авторами [34] было установлено, что при термической обработке соосажденных гидроксидов РЗМ и железа сначала формируются промежуточные фазы Fe2O3 и МFeO3, где М – редкоземельный элемент. Дальнейший отжиг системы приводит к увеличению массовой доли фазы граната:
Средний размер частиц, полученных при отжиге образца 4 при температуре 1100°C, рассчитанный с использованием формулы Шеррера из рентгенографических данных (рис. 5г) по четырем самым интенсивным максимумам (17.69°, 29.5°, 32.6° и 35.84°), составил 47 ± 9 нм. Эти результаты согласуются с данными просвечивающей электронной микроскопии высокого разрешения (рис. 6в, 6г), согласно которым частицы полученного феррит-граната иттербия имеют близкую к сферической форму и размер 60–65 нм. Следует отметить, что вследствие значительных магнитных свойств частицы Yb3Fe5O12 формируют более крупные агломераты сферической формы (рис. 6а, 6б).
ЗАКЛЮЧЕНИЕ
Изучено влияние реакционных параметров (марки анионита и типа его противоиона, температуры и режима осуществления анионообменного осаждения) на скорость и полноту совместного анионообменного осаждения ионов иттербия и железа. Максимальный выход продукта (88%) в виде отдельной фазы совместно осажденных гидроксидов железа и иттербия достигается при использовании доступной и дешевой отечественной анионообменной смолы АВ-17-8 в OH-форме. С целью снижения количества осадка, сорбированного на поверхности зерен смолы, использован режим процесса, в котором температура меняется по мере его осуществления (с температурным градиентом). Различия в коэффициентах температурного расширения смолы и осадка приводят к легкому его отслаиванию с поверхности зерен.
По данным РФА установлено, что образование железо-иттербиевого граната проходит через формирование промежуточной фазы перовскита YbFeO3. Термический отжиг продуктов осаждения в течение 4 ч при температуре 1100°C приводит к формированию монофазы феррит-граната Yb3Fe5O12. Полученные частицы имеют близкую к сферической форму со средним размером 47 ± 9 нм. Выявленные закономерности и условия синтеза могут быть использованы для получения феррит-гранатов других редкоземельных металлов.
Список литературы
Самохвалов А.А. Магнитные редкоземельные полупроводники Л.: Наука, 1977.
Goldman A. Modern Ferrite Technology. Springer Science & Business Media, 2006. 438 p.
Pardavi-Horvath M. // J. Magn. Magn. Mater. 2000. V. 215–216. P. 171. https://doi.org/10.1016/S0304-8853(00)00106-2
Журавлев Г.И. Химия и технология ферритов. Л.: Химия, 1970. 192 с.
Летюк Л.М., Костишин В.Г., Гончар А.В. Технология ферритовых материалов магнитоэлектроники. М.: МИСиС, 2005. 352 с.
Popov A.I., Gareeva Z.V., Zvezdin A.K. // Phys. Rev. B. 2015. V. 92. № 14. P. 144420. https://doi.org/10.1103/PhysRevB.92.144420
Nakamoto R., Xu B., Xu C. et al. // Phys. Rev. B. 2017. V. 95. P. 1. https://doi.org/10.1103/PhysRevB.95.024434
Wang W., Li D. // J. Magn. Magn. Mater. 2009. V. 321. P. 3307. https://doi.org/10.1016/j.jmmm.2009.05.068
Колмакова Н.П., Копцик С.В., Критик Г.С., Саранцев А.Я. // Физика твердого тела. 1991. Т. 33. № 9. С. 2674.
Mallmann E.J.J., Sombra A.S.B., Goes J.C., Fechine P.B.A. // Solid State Phenom. 2013. V. 202. P. 65. https://doi.org/10.4028/www.scientific.net/SSP.202.65
Sharma V., Kuanr B.K. // J. Alloys. Compd. 2018. V. 748. P. 591. https://doi.org/10.1016/j.jallcom.2018.03.086
Siao Yu-J., Qi X. // J. Alloys Compd. 2017. V. 691. P. 672. https://doi.org/10.1016/j.jallcom.2016.08.316
Ikesue A., Aung Y.L. // J. Sel. Top. Quantum Electron. 2018. V. 24. № 5. P. 1. https://doi.org/10.1109/JSTQE.2018.2811901
Su J., Lu X., Zhang J. et al. // J. Appl. Phys. 2012. № 111. P. 1148. https://doi.org/10.1063/1.3676450
Gasgnier M., Ostorero J., Petit A. // J. Alloys Compd. 1998. V. 275. № 277. P. 41. https://doi.org/10.1016/S0925-8388(98)00270-9
Opuchovica O., Kareiva A., Mazeikab K., Baltrunasb D. // J. Magn. Magn. Mater. 2017. № 422. P. 425. https://doi.org/10.1016/j.jmmm.2016.09.041
Jakeš V., Rubešová K., Havlíček J. et al. // IOP Conf. Ser.: Mater. Sci. Eng. 2019. V. 465. P. 012003. https://doi.org/10.1088/1757-899x/465/1/012003
Haneda H., Yanagitani T., Watanabe A., Shirasaki S. // J. Ceram. Soc. Jpn. 1991. V. 98. P. 285. https://doi.org/10.2109/jcersj.98.285
Haneda H., Yanagitani T., Sekita M. et al. // Mater. Sci. Monographs. 1991. V. 2. P. 2401.
Pashkov G.L., Saikova S.V., Panteleeva M.V. // Theor. Found. Chem. Eng. 2016. V. 50. P. 575. https://doi.org/10.1134/S0040579516040254
Сайкова С.В., Пашков Г.Л., Пантелеева М.В. // Монография. Красноярск. Сиб. Федер. ун-т. 2018. 198 с.
Pashkov G.L., Saikova S.V., Panteleeva M.V. et al. // Glass Ceram. 2016. V. 73. P. 107. https://doi.org/10.1007/s10717-016-9836-5
Saikova S.V., Kirshneva E.A., Panteleeva M.V. et al. // Russ. J. Inorg. Chem. 2019. V. 64. № 10. P. 1191. [Сайкова С.В., Киршнева Е.А., Пантелеева М.В. и др. // Журн. неорган. химии. 2019. Т. 64. № 10. С. 1013.]https://doi.org/10.1134/S0044457X1910012X
Ivantsov R., Evsevskaya N., Saikova S. et al. // Mater. Sci. Eng. B. 2017. V. 226. P. 171. https://doi.org/10.1016/j.mseb.2017.09.016
Пашков Г.Л., Сайкова С.В., Пантелеева М.В. и др. // Химия и хим. технология. 2013. Т. 56. № 8. С. 77.
Saykova D., Saikova S., Mikhlin Y. et al. // Metals. 2020. V. 10. P. 1075. https://doi.org/10.3390/met10081075
Trofimova T.V., Saikova S.V., Panteleeva M.V. et al. // Glass Ceram. 2018. V. 75. P. 74. https://doi.org/10.1007/s10717-018-0032-7
Saikova S.V., Trofimova T.V., Pavlikov A.Y., Samoilo A.S. // Russ. J. Inorg. Chem. 2020. V. 65. P. 291. https://doi.org/10.1134/S0036023620030110
Pashkov G.L., Saikova S.V., Panteleeva M.V. et al. // Glass Ceram. 2013. V. 70. P. 225. https://doi.org/10.1007/s10717-013-9549-y
Evsevskaya N., Pikurova E., Saikova S.V., Nemtsev I.V. // ACS Omega. 2020. V. 5. № 9. P. 4542. https://doi.org/10.1021/acsomega.9b03877
Шапиро С.А. Аналитическая химия. М.: Высшая школа, 1973. 344 с.
Spahiu K., Bruno J. A selected thermodynamic database for REE to be used in HLNW performance assessment exercises. Cerdanyola: MBT Tecnologia Ambiental, 1995. 91 p. https://inis.iaea.org/collection/NCLCollectionStore/_Public/28/019/28019633.pdf?r=1
Markova-Velichkova M., Lazarova T., Tumbalev V. et al. // Chem. Eng. J. 2013. V. 231. P. 236. https://doi.org/10.1016/j.cej.2013.07.029
Xu H.K., Sorensen C.M., Klabunde K. // J. Materials Res. 1992. V. 7. № 3. P. 712. https://doi.org/10.1557/JMR.1992.0712
Дополнительные материалы отсутствуют.
Инструменты
Журнал неорганической химии