Журнал неорганической химии, 2022, T. 67, № 8, стр. 1183-1193
Исследование особенностей процессов фазообразования в высокоглиноземистой области системы СаО–Al2О3
М. А. Трубицын a, *, Л. В. Фурда a, М. Н. Япрынцев a, Н. А. Воловичева a
a Белгородский государственный национальный исследовательский университет
308015 Белгород, ул. Победы, 85, Россия
* E-mail: troubitsin@bsu.edu.ru
Поступила в редакцию 01.02.2022
После доработки 02.03.2022
Принята к публикации 09.03.2022
- EDN: RDHAQX
- DOI: 10.31857/S0044457X2208027X
Аннотация
Изучены процессы фазообразования моноалюмината и диалюмината кальция в системе СаО–Al2О3 с использованием модельной порошковой смеси на основе гидроксидов алюминия и кальция в интервале температур 230–1450°C. Установлено начало образования промежуточной фазы Ca12Al14O33 (С12А7) при 430°С. При 1100°С зафиксировано появление CaAl4O7 (CA2) и присутствие κ-Al2O3. Фаза CaAl2O4 (СА) начинает интенсивно формироваться при 1170°С. В интервале температур 1250–1400°С отмечен существенный рост содержания СА, в то время как доля СА2 практически не меняется. Окончательное формирование целевых фаз CA и CA2 происходит в течение 2 ч при 1450°С. Показано, что процесс синтеза CA и CA2 лимитируется диффузией подвижных катионов Ca2+ к ядру сферолитов, обогащенному алюминием. Методом энергодисперсионной рентгеновской спектроскопии выявлено распределение фаз CA и CA2 в виде концентрических слоев.
ВВЕДЕНИЕ
Исследования системы СаО–Al2О3 проведены в ряде работ [1–3]. Уточненный вариант диаграммы предложен в работе [4]. В зависимости от мольного соотношения CaO/Al2O3 в системе CaO–A12O3 возможно существование следующих фаз: Ca3Al2O6 (C3A), Ca12Al14O33 (C12A7), CaAl2O4 (CA), CaAl4O7 (CA2) и CaAl12O19 (CA6). В практическом плане наибольшее значение имеют моноалюминат (CА) и диалюминат кальция (CA2).
Алюминаты кальция используются в оптической [5] и конструкционной керамике [6]. Моно- и диалюминат кальция являются основными фазами кальций-алюминатных (глиноземистых) цементов, которые широко применяются в строительной, горнодобывающей и металлургической промышленности [7]. В последние годы кальций-алюминатные цементы рассматривают в качестве перспективных биоматериалов, прежде всего в стоматологии и ортопедии [8].
Как следствие большого прикладного значения CA и CA2, синтез этих соединений стал предметом ряда исследований, направленных на увеличение выхода целевых фаз, уменьшение температуры и времени процесса [9–18]. В этих работах использованы различные технологические подходы: метод самопроизвольного высокотемпературного синтеза [19, 20], применение распылительной сушки [21], механохимическая активация прекурсоров [22], процесс Pechini [23] и золь-гель метод [24, 25]. Однако указанные методы малопригодны для организации выпуска глиноземистых цементов в промышленных масштабах.
Традиционно кальций-алюминатные фазы при крупнотоннажном производстве глиноземистых цементов синтезируют высокотемпературным плавлением или спеканием с использованием сырьевых материалов, содержащих Al2O3 и СаO, а также определенное количество примесей [7, 9, 26, 27]. Основные примеси – это кремнезем, оксиды железа, магния, титана и щелочи. Фазовые трансформации и механизм образования соединений кальция в системе CaO–Al2O3–Na2O рассматриваются в работе [28]. В случае применения сырья с повышенным содержанием примесей интервал спекания достаточно близок к температурам плавления, поэтому при массовом производстве глиноземистых цементов, как правило, используют технологию плавления. Наличие примесей оказывает существенное влияние на фазовый состав глиноземистого клинкера и процессы фазообразования, однако эти аспекты не рассматриваются в рамках настоящей статьи.
Большинство известных исследований посвящено синтезу монофазных продуктов, прежде всего СА [12, 13, 22, 29, 30]. Согласно [10], для эквимолярных смесей CaCO3 и Al2O3, термообработанных в течение 3–120 ч при 1045–1405°C, без строго определенной последовательности происходит формирование первичного неравновесного продукта реакции.
Согласно [7], последовательность образования алюминатов кальция может быть представлена следующим образом:
Из приведенных схем реакций следует, что в низкотемпературной области (600–900°С) происходит образование СА и С12А7. При повышении температуры ускоряется взаимодействие глинозема с СаО, в результате чего резко повышается количество СА и уменьшается содержание С12А7. При температуре 1000°С, когда значительная часть СаО связана в СА, образование СА2 происходит за счет реакции взаимодействия СА и Al2O3.
Авторы [11] изучали формирование алюминатов кальция в диапазоне температур 1200–1460°C с использованием в качестве прекурсоров CaO и Al2O3.
Фазы C3A и C12A7 были идентифицированы после термообработки при 1250°С, а затем их количество со временем уменьшалось. Доля CA2 была незначительной. Сделан вывод, что CA в смесях образуется не в результате прямой реакции между CaO и Al2O3, а путем трансформации промежуточных соединений.
Кинетика и механизм синтеза СА в интервале температур 1250–1400°С рассмотрены в работе [12]. Авторы подтвердили результаты [10] и показали, что наступление фазовых равновесий ускоряется с увеличением температуры и времени изотермической выдержки, а C3A и C12A7 следует рассматривать как промежуточные соединения в формировании CA.
Моноалюминат кальция CA высокой степени чистоты был синтезирован в интервале 900–1550°C с использованием смесей Al2O3 либо аморфного Al(OH)3 с CaCO3, предварительно измельченных в высокоэнергетической мельнице [13]. Порошковые смеси после совместного помола обладали высокой степенью гомогенности и имели следующие параметры: Sуд = 5.6–8 м2/г; d50 частиц CaO = 2 мкм, d50 частиц Al2O3 = 0.35 мкм. При 920°С зафиксировано появление фазы С12А7 по реакции:
${\text{7A}}{{{\text{l}}}_{{\text{2}}}}{{{\text{O}}}_{{\text{3}}}} + {\text{12CaO}} \to {\text{C}}{{{\text{a}}}_{{{\text{12}}}}}{\text{A}}{{{\text{l}}}_{{{\text{14}}}}}{{{\text{O}}}_{{{\text{33}}}}}{\text{(}}{{{\text{C}}}_{{{\text{12}}}}}{{{\text{A}}}_{{\text{7}}}}{\text{)}}{\text{.}}$
При 1100°С отмечено начало образования моноалюмината кальция CA. Согласно [13], термодинамически возможны следующие реакции:
По данным авторов, предварительное измельчение смесей снижает начальную температуру фазообразования CA. При использовании для приготовления смеси Al2O3 минимальная температура образования C12A7 и CA составляла 900 и 1100 соответственно, а в случае Al(OH)3 обе фазы начинали формироваться при 900°C.
В работе [14] перед синтезом смеси реагентов предварительно перемешивали в барабане с помощью мелющих тел из Al2O3 в среде изопропанола, а затем дополнительно вручную измельчали в гексане. Размер исходных зерен CaCO3 и Al2O3 был <10 и <1 мкм соответственно. Термообработку образцов проводили при 1300, 1400 и 1500°C и различном времени изотермической выдержки. Результаты, полученные авторами, не подтверждают мнение о том, что богатые кальцием фазы C12A7 и C3A образуются как промежуточные фазы, в то время как CA2 образуется в результате начальной побочной реакции. Локальные области с низким содержанием Ca приводят к образованию CA2 в равновесии с Al2O3. Единственной фазой алюмината кальция, которая образуется при 900°C, является CA.
В последние десятилетия имеет место увеличение объемов выпуска особо чистых высокоглиноземистых цементов с содержанием Al2O3 >70%. Такие цементы в качестве гидравлического вяжущего широко применяют в технологии низкоцементных огнеупорных литьевых композиционных масс нового поколения [15].
Для достижения высоких технологических и эксплуатационных свойств таких огнеупорных композитов большое значение имеет стабильность характеристик высокоглиноземистых цементов. Промышленное производство особо чистых кальций-алюминатных цементов с содержанием Al2O3 70–80% в настоящее время осуществляют методом твердофазного спекания во вращающихся, туннельных или камерных печах [7].
Получение высокоглиноземистого клинкера с содержанием оксида алюминия 70% и выше, согласно диаграмме состояния CaO–Al2O3, предполагает наличие двух целевых фаз: CaO ⋅ Al2O3 (CA) и CaO ⋅ 2Al2O3 (CA2). В условиях реального производства, как правило, процесс фазообразования протекает в неравновесных условиях. В результате формируются гетерогенные продукты переменного фазового состава, содержащие различные количества CA и CA2 в качестве основных фаз, а также C12A7 и непрореагировавший α-Al2O3 в качестве побочных фаз. Однако количество современных работ, посвященных теоретическим и практическим аспектам получения особо чистых высокоглиноземистых клинкеров, крайне мало [16–18].
В ряде статей исследователи указывают на факт изменения соотношения фаз СА/СА2 в области высоких температур, в то время как в системе уже отсутствуют непрореагировавшие прекурсоры Al2O3 и СаО и промежуточная фаза С12А7. Например, в работе [7] отмечается изменение фазового состава клинкера даже при небольших колебаниях температур изотермической выдержки в пределах 1420–1480°C. Аналогичные результаты были получены в наших предварительных исследованиях. Однако удовлетворительные объяснения вышеприведенных фактов в настоящее время отсутствуют.
В настоящей статье представлены результаты исследований факторов, обеспечивающих целенаправленное протекание процессов фазообразования моноалюмината и диалюмината кальция в высокоглиноземистой области системы СаО–Al2О3.
ЭКСПЕРИМЕНТАЛЬНАЯ ЧАСТЬ
Изучение процессов образования фаз CA и CA2 в системе СаО–Al2О3 проводили с использованием модельной порошковой смеси, содержащей соответствующие прекурсоры. В качестве прекурсора Al2О3 использовали гидроксид алюминия Al(OH)3 (х. ч.), в качестве прекурсора CaO – гидроксид кальция Са(OH)2 (х. ч.).
Гранулометрический состав исходных порошков определяли методом лазерной дифракции на анализаторе Microtrac s3500. Исследуемый образец погружали в ячейку анализатора, заполненную дистиллированной водой для Al(OH)3 или этиловым спиртом для Са(OH)2, затем производили диспергирование ультразвуком в течение 60 с. Определение размера частиц проводили по трем измерениям.
Согласно полученным данным, для Al(OH)3 медианный размер частиц составляет 114 мкм. Для порошков Са(OH)2 наблюдается бимодальный характер распределения частиц по размерам. Первая мода соответствует ~3 мкм, а вторая – ~30 мкм. При этом медианный размер равен 5.0 мкм.
С учетом требуемого содержания Al2О3 в интервале 70–71 мас. % количество Al(OH)3 и Са(OH)2 в модельной смеси брали в молярном соотношении СаО : Al2О3 = 1 : 1.36. Это при равновесном протекании твердофазных процессов должно было обеспечить проектное содержание целевых фаз СА и СА2 в количестве 65 и 35 мас. % соответственно.
Сухую порошковую смесь увлажняли дистиллированной водой до пастообразного состояния и гомогенизировали при помощи верхнеприводной лопастной мешалки. Далее полученную массу помещали в полипропиленовые формы диаметром 40 мм и высотой ~30 мм с последующим виброуплотнением в течение 10–20 с. Сформованные образцы предварительно выдерживали при комнатной температуре в течение 8 ч, а затем в сушильном шкафу с принудительной конвекцией при температуре 120°С в течение 2 ч.
На начальном этапе эксперимента для определения параметров дальнейшей термообработки высушенный образец из модельных смесей исследовали методами ТГА/ДСК с использованием комбинированного термоанализатора SDT Q600. Режим съемки: интервал температур 20–1400°C; скорость нагрева 10 град./мин; инертная атмосфера аргона. Обработку результатов термического анализа проводили с использованием программного обеспечения OriginPro2021.
Термообработку образцов осуществляли в высокотемпературной печи Nabertherm LHT 02/17 в режиме: скорость нагрева 250 град/ч, выдержка при максимальной температуре в течение 60 и 120 мин.
Рентгенофазовый анализ (РФА) выполняли на дифрактометре Ultima IV (Rigaku, Япония) с использованием CuKα-излучения (λ = 1.54056 Å, схема съемки Брэгга–Брентано, скорость сканирования 2 град/мин, 2θ = 10°–70°, шаг сканирования 0.02°). Идентификацию пиков проводили с использованием базы данных PDF-2. Экспериментальные дифрактограммы обрабатывали с помощью программы PDXL (Rigaku corporation).
Морфологические исследования материалов проводили на растровом электронном микроскопе FEI Nova NanoSEM 450. Изображения получали с использованием детектора обратно-рассеянных электронов в режиме низкого вакуума при давлении в камере 80 Па и ускоряющем напряжении 30 кВ. Для исследования в сканирующем режиме образцы наклеивали на медную подложку с помощью проводящего углеродного клея. Излучаемые образцом вторичные электроны при увеличении до 20 000 раз фиксировали регистрирующей системой, сигнал с которой подавался на систему обработки и регистрировался в оцифрованном виде.
РЕЗУЛЬТАТЫ И ОБСУЖДЕНИЕ
Кривые термогравиметрического и дифференциального термического анализа модельных образцов представлены на рис. 1. Изменение массы в процессе нагрева – на кривой ТГ, изменение скорости потери массы – на кривой ДТГ, тепловые эффекты процессов – на кривых ТП и ДТА. Согласно данным ТГ и ДТГ, на кривых присутствуют пять экстремумов, которые соответствуют максимальной скорости изменения массы исследуемого образца в процессе нагрева. Положение экстремумов на кривых ТГ, ДТГ, ТП и ДТА совпадают, поэтому во избежание усложнения рисунков излишней информацией положение пиков отмечено только на кривой ТП.
Рис. 1.
Результаты термогравиметрического и дифференциального термического анализа модельных образцов: а – кривые ТГ и ДТГ; б – кривые ДТА и ТП.
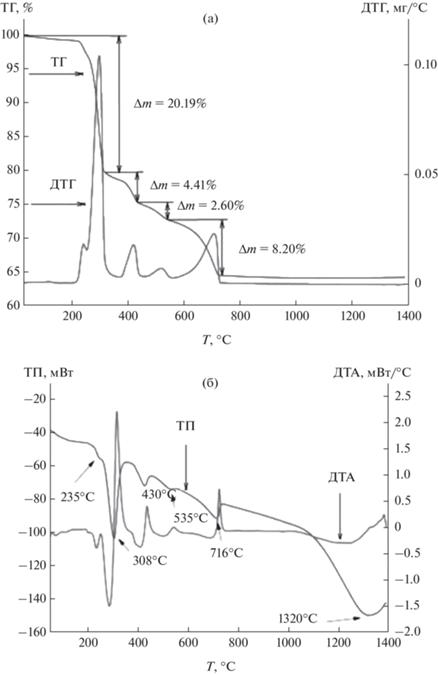
На кривых ТГ и ТП в температурном интервале 90–200°С наблюдается незначительная потеря массы и размытый по температуре эндотермический эффект, соответствующий удалению физически связанной воды.
Для корректной оценки процессов фазообразования в системе СаО–Al2О3 в модельных условиях экспериментальные образцы были обработаны в электропечи при температурах, соответствующих тепловым эффектам, наблюдаемым на кривых ДТА. Кроме того, термическую обработку проводили при температурах, выбранных для исследования влияния режимов обжига на процесс синтеза кальций-алюминатных фаз. Полученные экспериментальные образцы после каждой термообработки исследовали методом рентгенофазового анализа.
На рис. 2 представлены порошковые дифрактограммы исходного образца и образцов, обработанных при температурах, соответствующих выявленным тепловым эффектам.
Рис. 2.
Порошковые дифрактограммы исходного образца и образцов, термообработанных при 235, 308, 430, 535 и 716°С, выдержка 1 ч.
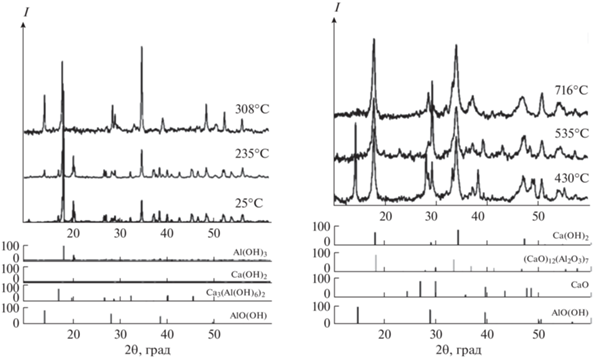
Методом рентгенофазового анализа установлено, что эндотермический эффект на кривой ДТА при 235°С может соответствовать деструкции гидроксида алюминия с образованием метагидроксида алюминия AlO(OH), а при достижении 308°С происходит полное разложение гидроксида алюминия, сопровождаемое значительной потерей массы.
При увеличении температуры до 430°С интенсивность рефлексов на порошковой дифрактограмме (рис. 2), соответствующих фазе AlO(OH), снижается с одновременным уширением рефлексов, отвечающих Ca(OH)2.
На дифрактограмме при данной температуре можно также наблюдать наличие рефлексов, соответствующих C12A7. Таким образом, эндотермический эффект на кривой ДТА, вероятно, отвечает процессу образования фазы C12A7 за счет взаимодействия продуктов разложения гидроксидов кальция и алюминия.
Увеличение температуры до 535°С, по данным РФА, приводит к полному разложению AlO(OH) и повышению содержания кальций-алюминатной фазы C12A7.
Эндотермический эффект на кривой ДТА при 716°С соответствует разложению гидроксида кальция, что подтверждается максимальной скоростью потери массы, наблюдаемой на кривых ТГ и ДТГ, и значительным уширением рефлексов на порошковой дифрактограмме, соответствующих Ca(OH)2.
На кривой ТП (рис. 1б) в интервале температур от ~1100 до 1400°С наблюдается широкий эндотермический эффект, который обусловлен процессами, протекающими без изменения массы образца. Наличие эффектов такого рода можно объяснить протеканием кристаллизационных процессов (разрушение кристаллической решетки исходных веществ и образование новых продуктов реакции, кинетически ограниченных диффузией отдельных компонентов).
Для более детальной оценки процессов фазообразования в модельной системе термообработку исследуемых образцов проводили во всем интервале данного температурного эндотермического эффекта (1100, 1170, 1250, 1300, 1350, 1400 и 1450°С).
При 1100°С происходит кристаллизация оксида кальция (рис. 3а). Основными фазами являются CaO (~48 мас. %) и C12A7 (~21 мас. %). При данной температуре зафиксировано также присутствие CA2 (~13 мас. %) и κ-Al2O3 (~23 мас. %).
Рис. 3.
Порошковые дифрактограммы образцов, термообработанных при 1100 (а) и 1170°С (б), выдержка 1 ч.
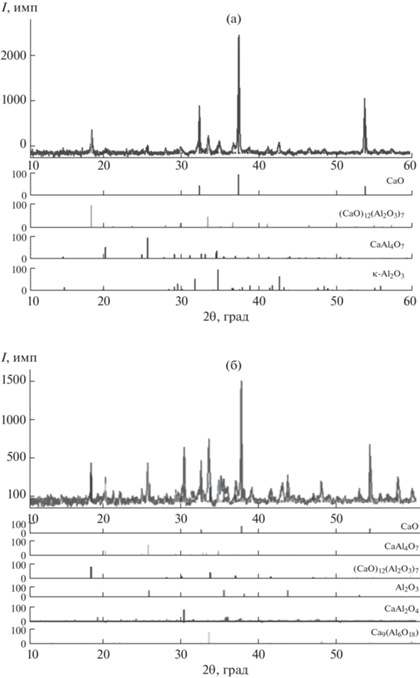
При 1170°С (рис. 3б) содержание CaO снижается до ~16 мас. % с одновременным увеличением содержания фазы CA2 (~17 мас. %). Также в образце интенсивно формируется CA (~31 мас. %). Вместе с тем содержание оксида алюминия практически не меняется (~22 мас. %). По-видимому, это возможно лишь в случае формирования кристаллических решеток, присущих нестехиометрическим соединениям СА и СА2 с вакансиями в позициях катионов алюминия. Также при 1170°С происходит фазовый переход κ-Al2O3 → α-Al2O3.
Далее с целью выявления зависимости фазового состава от режима термообработки образцы обжигали при 1250, 1300, 1350 1400 и 1450°С. Результаты РФА приведены в виде диаграмм на рис. 4 и 5.
Рис. 5.
Фазовый состав образцов, термообработанных при 1250, 1300, 1350, 1400 и 1450°С, выдержка 2 ч.
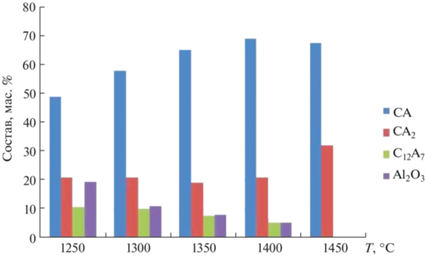
При 1250°С и выдержке в течение 1 ч (рис. 4) фазовый состав представлен CA, CA2 C12A7, α-Al2O3 и СаО. Для образцов, термообработанных в интервале 1300–1400°С, наблюдается отсутствие СаО. В данном диапазоне температур происходят количественные изменения, связанные с уменьшением содержания фаз Al2O3, C12A7 и CA. Так, при изотермической выдержке в течение 1 ч содержание α-Al2O3 понижается от 20.3 до 10.0 мас. %, а содержание C12A7 – от 12.6 до 5.0 мас. %. Одновременно наблюдается увеличение доли СА от 42.7 до 69.0 мас. %.
Время изотермической выдержки образцов оказывает значительное влияние на скорость изменения содержания фаз CA, C12A7 и α-Al2O3 (рис. 4, 5). Для образцов, термообработанных при температурах 1250–1400°С в течение 2 ч (рис. 5), наблюдается существенное увеличением содержания СА с максимумом при 1400°С (69 мас. %). В то же время содержание CA2 в диапазоне температур 1250–1400°С остается практически на одном уровне (19–21 мас. %). Окончательное и практически равновесное формирование целевых фаз CA и CA2 (67.9 и 32.1 мас. % соответственно) происходит в течение 2 ч при 1450°С. Следует отметить, что при данной температуре наблюдается снижение содержания СА в сторону образования фазы CA2.
По нашему мнению, результаты исследования влияния режимов термообработки на процесс синтеза кальций-алюминатных фаз в выбранной модельной системе можно интерпретировать следующим образом (рис. 6). В интервале 500–800°С, когда идет разложение Al(OH)3 и Ca(OH)2 c образованием субмикронных реакционно-активных частиц κ-Al2O3 и CaO (рис. 6б), в контактной зоне преимущественно протекает реакция синтеза фазы C12A7:
При температурах 1000–1170°С благодаря присутствию химически активных частиц κ-Al2O3 становится возможной прямая реакция:
Выше 1200°С (рис. 6в) в связи с переходом κ-Al2O3 в стабильную и, соответственно, химически инертную форму α-Al2O3 вероятность протекания вышеприведенной реакции будет крайне мала. Поэтому в диапазоне температур 1200–1400°С начнут превалировать следующие реакции:
Протекание этих реакций обусловливает существенное возрастание концентрации фазы CA при одновременном уменьшении содержания фаз Ca12Al14O33 и α-Al2O3. Массоперенос вещества в реакционную зону происходит в результате преимущественной диффузии Ca2+ и в меньшей степени ${\text{AlO}}_{4}^{{5 - }}.$
Предложенная нами схема процессов фазообразования подтверждается результатами сканирующей электронной микроскопии (рис. 7). На микрофотографиях образца (t = 1250°С) зафиксированы два типа частиц: ультрадисперсные кальцийсодержащие округлые пластинки размером от 1 до нескольких долей мкм и более крупные изометричные зерна ячеистой структуры размером ~10–25 мкм, идентифицируемые как смесь оксида алюминия и фазы CA2 (рис. 7а, 7б). При указанной температуре отчетливо наблюдается процесс консолидации обогащенных кальцием субмикронных частиц вокруг зарождающихся сферолитов с повышенным содержанием алюминия.
Рис. 7.
СЭМ-изображения образцов, термообработанных при 1250 (а, б), 1350 (в, г), 1450°С (д, е), выдержка 2 ч.
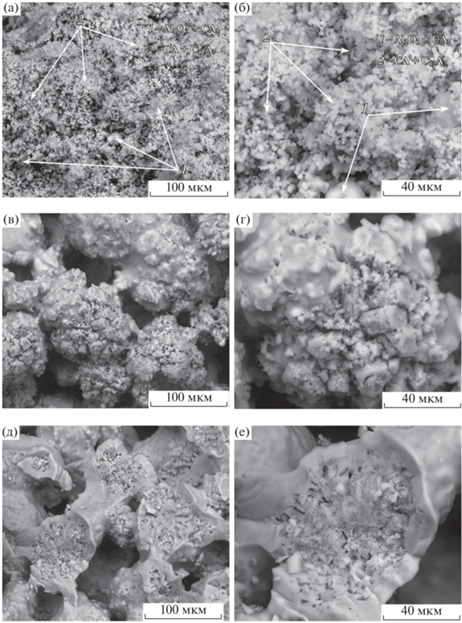
На СЭМ-изображениях образцов (t = 1350°С) хорошо различимы сферолиты размером ~70 мкм (рис. 7в, 7г), представляющие собой плотноупакованные глобулы из призматических частиц состава CA2 + Al2O3. Поверхность сферолитов фрагментарно покрыта тонким слоем микрорасплава кальцийобогащенных фаз CA и C12A7. При 1350°С между сферолитами появляются тонкие перешейки как результат спекания субмикронных частиц, что обусловливает формирование ячеистого порового пространства.
При температуре 1450°С (рис. 7д, 7е) вокруг сферолитов можно отметить наличие толстой однородной оболочки преимущественно фазы CA. Размер перешейков, связывающих деформированные сферолиты в единый каркас, заметно увеличен. Четко наблюдается образование поровых каналов. Твердый каркас и поровое пространство взаимосвязаны и представляют собой единую морфологическую систему как результат интенсивно протекающих процессов спекания. СЭМ-фотографии частиц иллюстрируют особенность их морфологии, в частности, хорошо заметна четкая граница между ячеистой структурой, составляющей ядро сферолитов, и плотной гомогенной оболочкой.
С учетом вышеизложенного формирование целевых продуктов CA и CA2, по нашему мнению, является следствием диффузии высвобождаемых в процессе разрушения фазы C12A7 более подвижных катионов Ca2+ в области сферолитов, богатых алюминием.
Данное предположение подтверждается энергодисперсионной рентгеновской спектроскопией (EDX) образца, обожженного в течение 2 ч при 1450°С. Результаты EDX, обработанные методом сканирования по линии, а также с применением картирования, приведены на рис. 8.
Рис. 8.
СЭМ-изображения с результатами EDX: а – распределение содержания элементов по сечению сферолита; б – карта распределения элементов (Al – зеленый цвет, Ca – красный цвет).
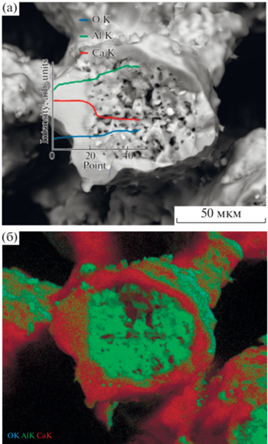
Несмотря на то, что данный вид анализа не дает точных количественных оценок содержания элементов, их относительное изменение позволяет сформировать четко определенную картину, характеризующую динамику изменения содержания кальция и алюминия при движении от периферии (оболочки) к центру сферолита (ядру). Видно, что при движении по линии от центра к периферии содержание кальция возрастает с одновременным уменьшением концентрации алюминия (рис. 8а). При этом в момент перехода границы между ядром и оболочкой происходит резкий рост содержания кальция, что свидетельствует о наличии четкой границы раздела фаз с различным содержанием кальция. Анализ карты распределения элементов (рис. 8б) подтверждает четкое зональное распределение кальция, алюминия и, соответственно, кальций-алюминатных соединений на завершающем этапе фазообразования. На поверхности сферолита наблюдается высокая концентрация кальция (фаза СА), а ядро сформировано фазой, богатой алюминием (СА2). Полученные данные хорошо согласуются с выводами, приведенными в работе [31].
В результате протекания химической реакции в разных точках реакционного пространства устанавливаются различные концентрации реагирующих веществ и продуктов реакции. Градиент концентраций наиболее подвижного реагента является причиной возникновения диффузии – самопроизвольного процесса переноса вещества в результате движения молекул до установления равновесного распределения концентраций. Хаотичное тепловое движение частиц вещества вызывает упорядоченный, направленный его перенос в области, где возникают градиенты концентрации или распределение концентраций отличается от равновесного состояния. Скорость диффузии зависит от плотности и вязкости среды, температуры, природы диффундирующих частиц, воздействия внешних сил и т.д.
Учитывая тот факт, что при минимальных температуре и времени выдержки исследуемых образцов основными фазами являются целевые кальций-алюминатные фазы (СА и СА2), можно предположить, что скорость химической реакции их образования в условиях эксперимента превышает скорость диффузионных стадий. И данный случай соответствует диффузионной области протекания химической реакции.
ЗАКЛЮЧЕНИЕ
С использованием модельных смесей гидроксидов кальция и алюминия исследованы процессы фазообразования кальций-алюминатных соединений в высокоглиноземистой области системы СаО–Al2О3. Выявлено, что образование промежуточной фазы С12А7 начинается при температуре 430°С. При 1100°С основными фазами являются CaO и C12A7. При данной температуре зафиксировано также появление CA2 и присутствие κ-Al2O3. Интенсивное формирование фазы СА начинается при 1170°С. В диапазоне температур 1250–1400°С отмечен существенный рост содержания СА, в то время как доля СА2 практически не меняется. По нашему мнению, это связано с переходом κ-Al2O3. в стабильную и, соответственно, химически инертную форму α-Al2O3. Как следствие, в интервале температур 1200–1400°С превалируют реакции с участием промежуточной фазы Ca12Al14O33, обеспечивающие существенное возрастание концентрации CA. Массоперенос вещества в реакционную зону происходит в результате преимущественной диффузии Ca2+.
Окончательное формирование целевых фаз CA и CA2 происходит в течение 2 ч при 1450°С. На завершающем этапе фазообразования нами установлено зональное распределение целевых фаз, а именно формирование СА2 в ядрах сферолитных зерен и образование на их поверхности плотной оболочки преимущественно фазы CA.
Список литературы
Rankin G.A., Wright E.F. // Am. J. Sci. Ser. 1915. V. 39. № 4. P. 1.
Nurse R.W., Welch J.H., Majumdar A.J. // Trans. Brit. Ceram. Soc. 1965. № 64. P. 409.
Торопов Н.А., Барзаковский В.П., Лапин В.В. и др. Диаграммы состояния силикатных систем. Справочник. Выпуск первый. Двойные системы. Л.: Наука, 1969. 822 с.
Jerebtsov D.A., Mikhailov G.G. // Ceram. Int. 2001. V. 27. № 1. P. 25. https://doi.org/10.1016/S0272-8842(00)00037-7
Rojas-Hernandez R.E., Fernando Rubio-Marcos F., José Francisco Fernandez J.F. et al. // Materials. 2021. V. 14. № 16. P. 4591. https://doi.org/10.3390/ma14164591
Kargin Yu.F., Lysenkov A.S., Ivicheva S.N. et al. // Inorg. Mater. 2010. V. 46. № 7. P. 799. [Каргин Ю.Ф., Лысенков А.С., Ивичева С.Н. и др. // Неорган. материалы. 2010. Т. 46. № 7. С. 892.] https://doi.org/10.1134/S0020168510070204
Кузнецова Т.В., Талабер Й. Глиноземистый цемент. М.: Стройиздат, 1988. 272 с.
Parreira R.M., Andrade T.L., Luz A.P. et al. // Ceram. Int. 2016. V. 42. P. 11732. https://doi.org/10.1016/j.ceramint.2016.04.092
Zhang D., Pan X., Yu H., Zhai Y. // J. Mater. Sci. Technol. 2015. V. 31. № 12. P. 1244. https://doi.org/10.1016/j.jmst.2015.10.012
Williamson J., Glasser F. // J. Appl. Chem. 2007. V. 12. № 12. P. 535. https://doi.org/10.1002/jctb.5010121203
Singh V.K., Ali M.M., Mandal U.K. // J. Am. Ceram. Soc. 1990. V. 73. P. 872. https://doi.org/10.1111/j.1151-2916.1990.tb05128.x
Mohamed B.M., Sharp J.H. // J. Mater. Chem. 1997. V. 7. P. 1595. https://doi.org/10.1039/A700201G
Rivas Mercury J.M., De Aza A.H., Pena P. // J. Eur. Ceram. Soc. 2005. V. 25. P. 3269. https://doi.org/10.1016/j.jeurceramsoc.2004.06.021
Iftekhar Sh., Grins J., Svensson G. et al. // J. Eur. Ceram. Soc. 2008. V. 28. № 4. P. 747. https://doi.org/10.1016/j.jeurceramsoc.2007.08.012
Parr Chr., Auvray J.M., Szepizdyn M. et al. // Refractories Worldforum. 2015. V. 7. P. 63.
Pereira A.L., Reis M.A., Ferreira L. et al. // Refractories Worldforum. 2017. V. 9. P. 67.
Кащеев И.Д., Михеенков М.А., Земляной К.Г. // Новые огнеупоры. 2013. № 12. С. 15. https://doi.org/10.17073/1683-4518-2013-12-15-18
Migal V.P., Rusakova G.V., Fedorova O.S. et al. // Refract. Ind. Ceram. 2012. V. 53. № 1. P. 4.
Yang Sh., Xiao G., Ding D. et al. // Int. J. Appl. Ceram. Technol. 2018. V. 15. P. 678. https://doi.org/10.1111/ ijac.12831
Yang Sh., Xiao G., Ding D. et al. // Ceram. Int. 2018. V. 44. № 6. P. 6186. https://doi.org/10.1016/J.ceramint.2018.01.003
Douy A., Gervais M. // J. Am. Ceram. Soc. 2000. V. 83. № 1. P. 70. https://doi.org https://doi.org/10.1111/j.1151-2916.2000.tb01150.x
Kumar V., Singh V.K., Srivastava A., Kumar P.H. // J. Am. Ceram. Soc. 2015. V. 3. P. 92. https://doi.orghttps://doi.org/10.1016/j.jascer.2014.11.004
Choi S.W., Hong S.H. // Mater. Sci. Eng. 2010. V. 171. № 1–3. P. 69. https://doi.orghttps://doi.org/10.1016/j.mseb.2010.03.071
Amera A.A., El-Didamonya H., El-Sokkaryb T.M. et al. // Bol. Soc. Espan. Ceram. Vidr. 2020. V. 240. № 10. P. 9. https://doi.org/10.1016/j.bsecv.2020.07.006
Khomidov F.G., Kadyrova Z.R., Usmanov K.L. et al. // Am. J. Interdisc. Innov. Res. 2021. V. 3. № 6. P. 69. https://doi.org/10.37547/tajiir/Volume03Issue06-11
Бурлов И.Ю., Бурлов Ю.А., Кривобородов Ю.Р. // Цемент и его применение. 2002. № 6. С. 25.
Krivoborodov Y., Samchenko S. // IOP Conference Series: Mater. Sci. Eng. 2019. V. 687. № 2. https://doi.org/10.1088/1757-899X/687/2/022034
Yu H., Pan X., Tian Y., Tu G. // Int. J. Miner. Met. Mater. 2020. V. 27. № 7. P. 924. https://doi.org/10.1007/s12613-019-1951-1
Gakia A., Perrakib Th., Kakali G. // J. Am. Ceram. Soc. 2007. V. 27. № 2–3. P. 1785. https://doi.org/10.1016/j.jeurceramsoc.2006.05.006
Rodríguez M.A., Aguilar C.L., Aghayan M.A. // Ceram. Int. 2012. V. 38. № 1. P. 395. https://doi.org/10.1016/j.ceramint.2011.07.020
Tian Y., Pan X., Yu H., Tu G. // J. Alloys Compd. 2016. № 670. P. 96. https://doi.org/10.1016/j.jallcom.2016.02.059
Дополнительные материалы отсутствуют.
Инструменты
Журнал неорганической химии