Журнал неорганической химии, 2023, T. 68, № 5, стр. 682-693
Разработка метода химического полирования нержавеющей стали марки 08Х18Н10 с помощью наноструктурированной среды
П. Е. Тюлягин a, *, Е. С. Мишина a, А. С. Полякова a, Н. М. Мурашова a, А. Г. Мурадова a
a Российский химико-технологический университет им. Д.И. Менделеева
125047 Москва, Миусская пл., 9, Россия
* E-mail: tylagin@vivaldi.net
Поступила в редакцию 13.01.2023
После доработки 08.02.2023
Принята к публикации 22.02.2023
- EDN: SOHEFZ
- DOI: 10.31857/S0044457X23600032
Аннотация
Химическая полировка металлов с помощью наноструктурированных сред – обратных микроэмульсий – интересна с точки зрения усовершенствования методики полировки металлов концентрированными кислотами, поскольку в ней достигается существенное уменьшение концентрации травящего реагента (кислоты). Показана возможность применения обратных микроэмульсий в системе додецилсульфат натрия–бутанол-1–керосин–водный раствор соляной кислоты для химической полировки нержавеющей стали марки 08Х18Н10, в рамках которой определены области существования микроэмульсии в рассматриваемой системе и подобраны условия проведения химической полировки нержавеющей стали микроэмульсией додецилсульфата натрия. Выбраны условия очистки поверхности образца нержавеющей стали после химической полировки, при которых происходит наиболее полное удаление компонентов микроэмульсии с поверхности стали, но при этом не происходит изменения микрорельефа поверхности.
ВВЕДЕНИЕ
Производство изделий из металлов часто сопряжено с образованием на поверхности изделия множества неровностей, совокупность которых формирует микро- и нанорельеф поверхности [1, 2]. В некоторых случаях, например при изготовлении материалов из титана и его сплавов для костных имплантатов, шероховатость поверхности создается искусственно с целью имитации на поверхности металла естественной наноструктуры кости [3, 4]. Однако чаще всего высокие требования качества, предъявляемые к изделиям машиностроения, повышают важность технологических процессов, направленных на уменьшение высоты неровностей микрорельефа этих изделий. Подобные процессы модификации микрорельефа, называемые полировкой, применяются в качестве финишной обработки для широкого класса металлических изделий бытового и технического назначения [5, 6]. Эффективность таких процессов оценивается, главным образом, по двум характеристикам микрорельефа, а именно: по средней шероховатости и наибольшей высоте неровностей.
На данный момент в промышленности широко применяются четыре вида технологических процессов уменьшения неровностей микро- и микрорельефа поверхности: механическая полировка, электрохимическая полировка, электролитно-плазменная полировка и химическая полировка. Причем последние три вида обеспечивают не только уменьшение высот неровностей микрорельефа, но также значительное уменьшение внутренних механических напряжений на поверхности металла и увеличение его химической стойкости [7–11].
Сталь является одним из самых распространенных конструкционных металлических материалов. Для финишной обработки деталей сложной формы из нержавеющей стали различных марок больше всего подходит электролитно-плазменная полировка благодаря своей дешевизне, экологичности и безопасности для рабочего персонала [12–14]. Кроме того, этот вид полировки, наравне с химической полировкой, позволяет обрабатывать стальные изделия относительно сложной формы. Однако, если стальное изделие имеет слишком сложную форму с большим количеством глубоких отверстий и тонкими стенками (подобные изделия могут быть получены с помощью технологии 3D-печати), равномерная полировка его поверхности с помощью указанных выше четырех видов полировки становится некачественной по причине сильно неравномерного съема металла на разных участках такого изделия [15–18].
Наноструктурированные жидкие среды, такие как обратные микроэмульсии, диаметр капель которых может составлять от нескольких единиц до десятков нанометров, могут использоваться для разработки и усовершенствования технологических процессов, происходящих в системах жидкость–твердая фаза. К таким процессам можно отнести синтез наночастиц в микроэмульсиях, извлечение металлов из частиц твердой фазы с помощью экстрагентсодержащих микроэмульсий, а также химическую полировку и травление металлов [19–24]. Преимуществом обратных микроэмульсий для химической полировки является то, что травящий реагент локализован внутри капель микроэмульсии. Это позволяет снизить суммарную концентрацию травящего реагента в полирующей жидкости, что, в свою очередь, снижает токсичность данной жидкости, а также позволяет добиться более равномерного полирования поверхности за счет диффузионных ограничений [25].
Обратные микроэмульсии могут образовываться при содержании в водной фазе соляной кислоты [26–28], что указывает на возможность использования таких систем в качестве носителей реагентов для химического травления поверхности нержавеющей стали. Корректировка состава такой обратной микроэмульсии и условий процесса обработки металла (температура, скорость перемешивания, продолжительность процесса) позволяет регулировать финальный результат: растравливание поверхности стали или ее полировку.
Цель работы – исследование области существования микроэмульсии на основе додецилсульфата натрия (SDS), содержащей соляную кислоту, с последующим подбором составов обратной микроэмульсии и условий, необходимых для осуществления химического полирования нержавеющей стали марки 08Х18Н10.
ЭКСПЕРИМЕНТАЛЬНАЯ ЧАСТЬ
В работе использовали реактивы: додецилсульфат натрия (не менее 95% основного вещества), бутанол-1 (ч), керосин ТС-1 (смесь углеводородов, плотность при 20°С 777 кг/м3), ацетон (ч. д. а.), соду пищевую, соляную кислоту 35% (х. ч.) и бидистиллированную воду.
Микроэмульсионную систему получали при одновременном смешивании в бюксе емкостью 50 мл рассчитанного количества SDS, бутанола-1, керосина и водного раствора соляной кислоты при постоянном перемешивании компонентов на магнитной мешалке со скоростью 900 об/мин до полного растворения твердых частиц SDS. Количество каждого компонента микроэмульсионной системы представляется следующими переменными:
где nбут – число молей бутанола-1, nSDS – число молей SDS; где Xj – относительная массовая доля компонента j микроэмульсионной системы, в данном случае Xв.ф (где Аj – масса водной фазы микроэмульсии (mв.ф), которая представляет собой либо воду, либо водный раствор соляной кислоты, Б – сумма масс SDS и бутанола-1) или Xкер (где Аj – масса керосина (mкер), Б = mв.ф). Содержание соляной кислоты выражается в виде ее молярной концентрации в водной фазе микроэмульсионной системы, СHCl в в.ф, моль/л.Область существования микроэмульсии в системе додецилсульфат натрия–бутанол-1–керосин–водная фаза определяли методом титрования смеси SDS–н-бутанол–водная фаза керосином. Максимальное содержание соляной кислоты в микроэмульсии определяли методом приготовления микроэмульсионной системы с фиксированной СHCl в в.ф. В обоих случаях границей области существования микроэмульсии IV типа по классификации Винзора (т.е. микроэмульсии, не находящейся в равновесии с избытком водной и/или масляной фазы) являлось появление устойчивого помутнения и последующее расслоение микроэмульсии. Исследования проводили при температуре 25°С.
Термическую устойчивость микроэмульсий разных составов определяли путем их нагревания в диапазоне температур от 25 до 80°С в циркуляционном жидкостном термостате LT-TW/22 до появления устойчивого помутнения и последующего расслоения микроэмульсии.
Размер капель микроэмульсий оценивали методом динамического светорассеяния на приборе Zetasizer Nano ZS (Malvern, Великобритания). Все измерения проводили при следующих параметрах: дисперсионная среда – керосин (nD = = 1.41; η = 0.86 мПа с), дисперсная фаза – вода (nD = 1.33; абсорбция света = 1.0). Для проведения измерений образцы термостатировали при заданной температуре (25 или 60°C) в течение 3 мин. Из полученной гистограммы распределения размеров высчитывали моду, которую записывали как размер капель микроэмульсии.
Для проведения химической полировки использовали лист прокатной стали марки 08Х18Н10 толщиной 51 ± 1 мкм. Измерение толщины листа стали до и после полировки проводили с помощью микрометра МЕГЕОН 80800, инструментальная погрешность равна 1 мкм. Размер стальной пластинки, подвергаемой полировке, составлял 8 × 8 мм. Процесс химической полировки проводили при температуре 60°C в течение 10–50 мин без механического перемешивания, либо при перемешивании на магнитной мешалке со скоростью 50 и 100 об./мин. По окончании процесса полировки стальную пластинку последовательно промывали в ацетоне, водном растворе соды с концентрацией 20 г/л и кипящей бидистиллированной воде.
Эффективность очистки стальной пластинки от компонентов обратной микроэмульсии оценивали по краевому углу смачивания методом “сидячей капли” с помощью оптической установки на базе микроскопа VEB Carl Zeiss Jena. На поверхность стальной пластинки наносили 5 капель бидистиллированной воды размером 2–3 мм, у каждой из которых измеряли угол смачивания θ и определяли инструментальную погрешность измеряемого угла. После этого с учетом доверительной вероятности, равной 0.95, рассчитывали среднее значение краевого угла смачивания и величину итоговой погрешности рассчитанного среднего.
Поверхность стали качественно оценивали с помощью пьезо-профилометра Nanoeducator II (NT-MDT, Россия), сканирующего электронного микроскопа (СЭМ) Vega3 SBN (Tescan, Чехия) и микроинтерферометра Линника МИИ-4. С помощью микроинтерферометра, после расшифровки интерферограмм также определяли такие параметры, как среднее арифметическое отклонение профиля (Ra) и наибольшую высоту профиля (Rz). Значения этих параметров рассчитывали по ГОСТ 25142-82, при этом базовая длина составила 81.2 мкм, а длина всего участка измерения – 812 мкм.
РЕЗУЛЬТАТЫ И ОБСУЖДЕНИЕ
Определение области существования микроэмульсии в системе додецилсульфат натрия–бутанол-1–керосин–водный раствор соляной кислоты
Для выбора составов микроэмульсионных систем, пригодных для полировки стали, были определены области существования микроэмульсии SDS в диапазоне Xв.ф от 0.2 до 0.7 при S = 10 в присутствии соляной кислоты с СHCl в в.ф = 0.01, 0.1 и 1 моль/л. Их сравнивали с областью существования микроэмульсии в системе аналогичного состава, но не содержащей кислоту в водной фазе. Полученные фазовые диаграммы системы додецилсульфат натрия–бутанол-1–керосин–водная фаза приведены на рис. 1.
Рис. 1.
Псевдотрехкомпонентная фазовая диаграмма системы додецилсульфат натрия–бутанол-1–керосин–водный раствор соляной кислоты. Область существования микроэмульсионной системы типа IV выделена серым цветом. Границы области существования микроэмульсии: 1 – без кислоты; 2 – при СHCl в в.ф. = 0.01 моль/л; 3 – при СHCl в в.ф = = 0.1 моль/л; 4 – предел растворимости додецилсульфата натрия [30]; 5 – выбранный состав обратной микроэмульсии для химической полировки стали.
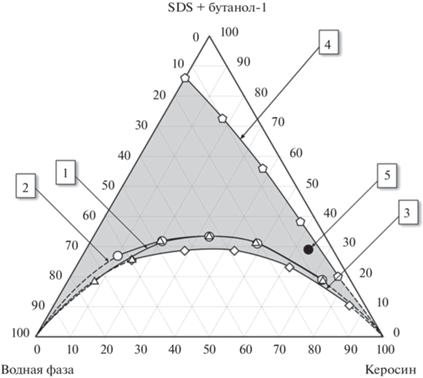
На фазовой диаграмме показаны границы области существования микроэмульсии додецилсульфата натрия, относящейся к IV типу по классификации Винзора. Область существования такой микроэмульсии в присутствии СHCl в в.ф = 0.01 моль/л (линия 2) практически не изменяется по сравнению с системой без кислоты (линия 1). Если СHCl в в.ф увеличить до 0.1 моль/л, область существования микроэмульсии немного расширяется (линия 3). Однако при увеличении СHCl в в.ф до 1 моль/л микроэмульсия IV типа в рассматриваемой системе не образуется. Следует также отметить, что при малом содержании воды в системе область существования микроэмульсии ограничивается пределом растворимости додецилсульфата натрия [30].
Предполагаем, что для эффективной полировки металлов предпочтительно использовать обратные микроэмульсии с небольшим содержанием водной фазы. Для этого на основании полученной фазовой диаграммы была выбрана обратная микроэмульсия следующего состава: S = 10. Xв.ф = 0.2, Xкер = 0.9 (рис. 1, точка 5). Было определено, что в водной фазе такой микроэмульсионной системы может содержаться до 0.6 моль/л соляной кислоты. При увеличении СHCl в в.ф до 0.7 моль/л обратная микроэмульсия в данной системе не образуется. Гидродинамический размер капель обратной микроэмульсии данного состава без кислоты при 25°С составил ⁓3 нм.
Поскольку процесс химической полировки стали может проводиться при повышенной температуре, была определена термическая устойчивость выбранной обратной микроэмульсии, содержащей СHCl в в.ф от 0.1 до 0.6 моль/л, в интервале температур от 25 до 80°С. Определено, что во всех случаях расслоения микроэмульсионной системы на несколько фаз не происходит и обратная микроэмульсия сохраняет свою устойчивость в исследуемом диапазоне температур. Гидродинамический диаметр капель обратных микроэмульсий, содержащих указанные концентрации соляной кислоты, при температуре 60°С по сравнению с диаметром капель микроэмульсии без кислоты при 25°С не изменяется. Он также составляет около 3 нм.
Таким образом, обратная микроэмульсия выбранного состава (S = 10, Xв.ф = 0.2, Xкер = 0.9) может использоваться для проведения химической полировки стали. Рекомендуемая СHCl в в.ф не должна превышать 0.6 моль/л.
Выбор условий очистки поверхности образца нержавеющей стали после химической полировки
Для обеспечения качественного измерения шероховатости микрорельефа поверхности стали после полировки необходимо отмыть пластинку от компонентов обратной микроэмульсии, в частности, от додецилсульфата натрия, который в процессе полировки адсорбируется на поверхности стали. Присутствие SDS на поверхности стали оказывает влияние на смачивание этой поверхности водой. Таким образом, эффективность очистки нержавеющей стали можно контролировать по величине краевого угла капли бидистиллированной воды, нанесенной на поверхность пластинки.
Краевой угол смачивания, образованный каплей воды на поверхности стали, взятой для проведения исследования, без какой-либо предварительной обработки поверхности (θ1) составил 78° ± 6°. Это значение соответствует литературным данным для стали марки AISI 304 (аналог 08Х18Н10), на которой краевой угол смачивания капли воды составляет 70° ± 10° [31, 32]. Погружение этой пластинки в обратную микроэмульсию состава S = 10, Xв.ф. = 0.2, Xкер = 0.9 без кислоты на 15 мин при нагревании до 60°C и перемешивании при 300 об/мин привело к значительному уменьшению краевого угла смачивания до 15° ± 7°. Пример капли приведен на рис. 2а.
Рис. 2.
Микрофотографии капель бидистиллированной воды на поверхности стали, обработанной микроэмульсией додецилсульфата натрия, с результатами измерения краевого угла смачивания вместе с инструментальной погрешностью (а), а затем промытой последовательно в ацетоне, растворе соды 20 г/л и в кипящей воде при продолжительности каждой стадии промывки 30 мин (б).
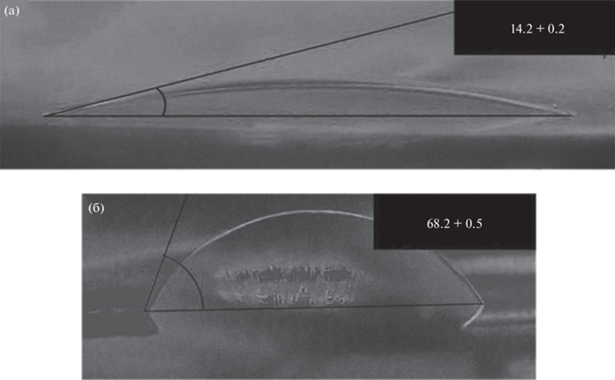
Для очистки поверхности стали после ее обработки обратной микроэмульсией в условиях, указанных выше, было предложено использовать последовательную промывку в ацетоне, водном растворе соды с концентрацией 20 г/л и в кипящей бидистиллированной воде, так как данные реагенты чаще всего используются для очистки поверхности различных металлов [33–35]. Было изучено влияние температуры раствора соды и продолжительности обработки пластинки в указанных реагентах на качество очистки поверхности стали. Продолжительность каждой стадии очистки варьировали в диапазоне 15–30 мин, так как большая продолжительность очистки сильно замедлила бы проведение исследования, а меньшая, скорее всего, не приводила бы к эффективной очистке. Условия проведения очистки и полученные значения краевого угла смачивания капли воды на поверхности приведены в табл. 1.
Таблица 1.
Изменение краевого угла смачивания капли бидистиллированной воды на поверхности нержавеющей стали после очистки различными способами
Очистка стали последовательным промыванием реагентами | Краевой угол θ ± Δθ, град |
№ способа очистки | |||||
---|---|---|---|---|---|---|---|
реагент 1 | время, мин | реагент 2 | время, мин | реагент 3 | время, мин | ||
Ацетон | 30 | Кипящая вода | 30 | – | – | 59 ± 3 | 1 |
15 | Раствор соды при 40°C | 15 | Кипящая вода | 15 | 65 ± 4 | 2 | |
30 | 30 | 30 | 64 ± 2 | 3 | |||
Раствор соды при 70°C | 69 ± 4 | 4 | |||||
Раствор соды при 95°C | 61 ± 3 | 5 |
Как видно из представленных в таблице данных, 69° ± 4° – это единственное значение краевого угла смачивания, статистически пересекающееся со значением θ1. Исходя из этого, следует, что способ очистки 4 является достаточным для удаления компонентов обратной микроэмульсии с поверхности стали. Небольшое различие между этими величинами, возможно, связано с тем, что на пластинке изначально присутствовали маслянистые загрязнения.
Для проверки предположения о том, что выбранный способ очистки не оказывает влияния на микрорельеф поверхности нержавеющей стали, был проведен анализ шероховатости поверхности пластинки до и после ее очистки способом 4, а также после обработки пластинки обратной микроэмульсией состава S = 10, Xв.ф = 0.2, Xкер = = 0.9 без кислоты в течение 15 мин при 60°C и перемешивании при 300 об/мин с последующей очисткой таким же способом. Полученные величины Ra и Rz для поверхности нержавеющей стали марки 08Х18Н10 приведены в табл. 2.
Таблица 2.
Средняя шероховатость (Ra) и наибольшая высота профиля поверхности (Rz) нержавеющей стали до и после обработки обратной микроэмульсией додецилсульфата натрия и очистки
Тип образца | Ra± ΔRa, нм | Rz ± ΔRz, нм |
---|---|---|
Сталь без очистки | 96 ± 4 | 490 ± 20 |
Сталь, очищенная способом 4 | 90 ± 4 | 470 ± 10 |
Сталь, погруженная в обратную микроэмульсию, а затем очищенная способом 4 | 91 ± 4 | 480 ± 20 |
Из полученных данных следует, что значения Ra и Rz исследованных образцов находятся в пределах погрешности измерения. Таким образом, очистка поверхности стали от компонентов обратной микроэмульсии с помощью предложенного способа последовательной промывки ацетоном, раствором соды и кипящей водой не оказывает влияния на результат измерения шероховатости. Поэтому в дальнейшем для очистки поверхности стали перед исследованием микрорельефа поверхности использовали именно этот метод.
Выбор условий химической полировки стали с помощью обратной микроэмульсии
Обработка стали обратной микроэмульсией с составом S = 10, Xв.ф. = 0.2, Xкер = 0.9, СHCl в в.ф = = 0.6 моль/л в течение 50 мин привела к значительному растравливанию поверхности металла. Данный эффект хорошо виден при сравнении топографии микрорельефа стали до и после обработки, полученной с помощью пьезопрофилометра (рис. 3). Разница между наименьшей и наивысшей точками микрорельефа поверхности после обработки микроэмульсией увеличилась почти в 2 раза, что говорит об избыточности такой СHCl в в.ф для применения в полировании. Измерить величины Ra и Rz данной растравленной поверхности с помощью микроинтерферометра не удалось из-за полного отсутствия какой-либо регулярности рельефа хотя бы по одной из двух перпендикулярных осей, лежащих на плоскости, которая соответствует поверхности стали. Данная нерегулярность поверхности хорошо заметна при сравнении двух микрофотографий, полученных с помощью СЭМ (рис. 4). На первой микрофотографии видно, что сталь до обработки обратной микроэмульсией имела регулярность рельефа вдоль оси, проходящей из нижнего левого угла в верхний правый угол микрофотографии. На второй микрофотографии не существует такой оси, вдоль которой наблюдалась бы какая-либо регулярность рельефа, что приводило к значительным шумам при расшифровке интерферограмм, полученных с помощью микроинтерферометра для данной поверхности, вследствие чего не удалось измерить значения Ra и Rz.
Рис. 3.
Топография микрорельефа поверхности стали: а – до обработки обратной микроэмульсией, б – после обработки обратной микроэмульсией с составом S = 10, Xв.ф. = 0.2, Xкер = 0.9, СHCl в в.ф. = 0.6 моль/л в течение 50 мин.
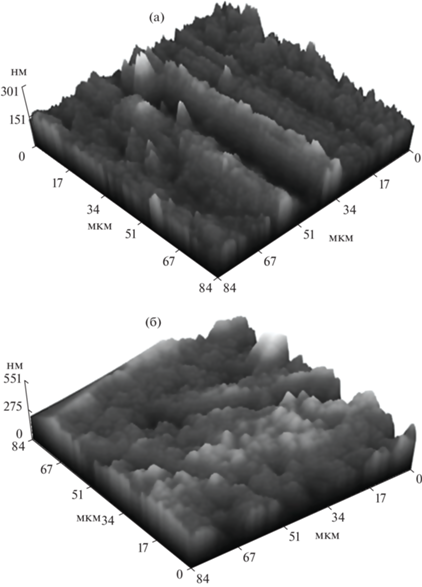
Рис. 4.
Полученные с помощью СЭМ микрофотографии поверхности стали: а – до обработки обратной микроэмульсией, б – после обработки обратной микроэмульсией с составом S = 10, Xв.ф. = 0.2, Xкер = 0.9, СHCl в в.ф. = 0.6 моль/л в течение 50 мин.
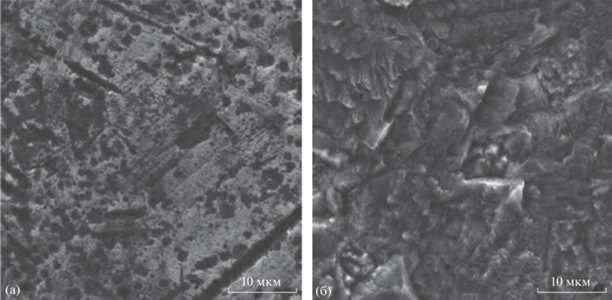
Важно отметить, что изменения толщины стальной пластинки в пределах 1 мкм при таком сильном воздействии травящего реагента зафиксировано не было. В связи с этим при полировке стали обратными микроэмульсиями с меньшей концентрацией кислоты измерения толщины стальной пластинки не проводили, так как считали, что их толщина в вышеуказанных пределах также не изменяется.
На основании полученного результата более детально изучено изменение микрорельефа поверхности нержавеющей стали при обработке обратной микроэмульсией с составом S = 10, Xв.ф = 0.2, Xкер = 0.9 и СHCl в в.ф от 0.1 до 0.4 моль/л с шагом 0.1 моль/л. Продолжительность воздействия на поверхность стали варьировалась от 10 до 50 мин с шагом в 10 мин.
Результат химической полировки оценивали по параметрам Ra и Rz с помощью микроинтерферометра. На рис. 5 приведены зависимости этих параметров от продолжительности полировки при разных СHCl в в.ф. В качестве нулевой точки были выбраны значения Ra = 90 ± 4 нм и Rz = 470 ± 10 нм, полученные для стали, очищенной последовательной промывкой ацетоном, раствором соды 20 г/л, кипящей водой (способ очистки 4, табл. 2).
Рис. 5.
Зависимости параметров Ra и Rz для стали от продолжительности обработки при полировке нержавеющей стали обратными микроэмульсиями додецилсульфата натрия с разными концентрациями соляной кислоты в водной фазе.
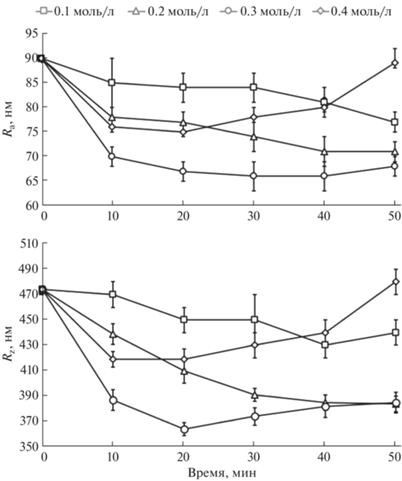
По характеру изменения параметра Ra видно, что статистически значимое уменьшение средней шероховатости поверхности стали при полировке обратной микроэмульсией с СHCl в в.ф = 0.1 моль/л наблюдается только в последние 20 мин процесса и составляет 8% по сравнению с нулевой точкой. Наибольшая высота профиля поверхности (Rz) также уменьшается в последние 20 мин, однако это изменение незначительно относительно нулевой точки. Такой вид зависимостей Ra и Rz от продолжительности обработки пластинки может говорить о недостаточной концентрации соляной кислоты в системе для эффективной полировки стали.
При СHCl в в.ф = 0.2 и 0.3 моль/л прослеживается снижение шероховатости профиля поверхности с увеличением продолжительности проведения процесса. При СHCl в в.ф. = 0.2 моль/л статистически значимое уменьшение Ra наблюдается уже через 10 мин полировки и составляет 12% по сравнению с нулевой точкой, а через 40 мин достигает уже 19%. Наибольшая высота профиля поверхности при этом постепенно уменьшается в течение первых 30 мин процесса, после чего статистически значимых изменений этого параметра не наблюдается. При СHCl в в.ф = 0.3 моль/л значение Ra уже на 10 мин опускается на 22% от нулевой точки, далее статистически значимых изменений не наблюдается. Для наибольшей высоты профиля поверхности наблюдаются три статистически различимых этапа: резкое уменьшение Rz на 20% в первые 10 мин полировки, уменьшение Rz на 5% через 20 мин от начала полировки, увеличение Rz на 5% через 30 мин от начала полировки, после чего данный параметр не изменяется.
Постепенное снижение средней шероховатости и наибольшей высоты профиля говорит о том, что в ходе полировки растворяются как самые крупные, так и мелкие выступы. Из увеличения параметра Rz спустя 30 мин полировки обратной микроэмульсией с СHCl в в.ф = 0.3 моль/л следует, что обратная микроэмульсия перестает взаимодействовать с крупными выступами, однако продолжает оказывать влияние на более мелкие неровности, о чем свидетельствует снижение средней шероховатости. Такой характер кривых указывает на эффективную полировку стали обратной микроэмульсией с СHCl в в.ф = 0.3 моль/л уже в течение первых 10 мин с сохранением эффекта в течение следующих 40 мин, однако наилучший результат достигается за 20 мин.
При СHCl в в.ф = 0.4 моль/л можно выделить три статистически различимых этапа изменения средней шероховатости: в первые 10 мин полировки параметр Ra уменьшается на 11% относительно нулевой точки, затем через 40 мин происходит увеличение параметра Ra на 5% по сравнению со значением Ra через 10 мин полировки, а через 50 мин средняя шероховатость пластины становится равной средней шероховатости нулевой точки. Аналогичным образом изменяется и параметр Rz. В данном случае можно предположить, что выбранная концентрация кислоты слишком высокая для химической полировки стали и, скорее всего, при дальнейшем воздействии приведет к растравливанию поверхности металла.
Поскольку рассмотренный выше процесс химической полировки стали проводился при нагревании в отсутствие механического перемешивания, дополнительно была проведена оценка влияния перемешивания микроэмульсии на микрорельеф поверхности стали. Полировку в данном случае проводили с помощью обратной микроэмульсии с составом S = 10, Xв.ф. = 0.2, Xкер = 0.9 и СHCl в в.ф = 0.3 моль/л в течение 20 мин при температуре 60°C. Сравнивали значения Ra и Rz при полировке стали без перемешивания и при перемешивании на магнитной мешалке со скоростью 50 и 100 об/мин. Полученные результаты приведены в табл. 3.
Таблица 3.
Средняя шероховатость (Ra) и наибольшая высота профиля поверхности (Rz) нержавеющей стали после полировки обратной микроэмульсией додецилсульфата натрия в течение 20 мин при различных скоростях перемешивания
Скорость механического перемешивания, об/мин | Ra ± ΔRa, нм | Rz ± ΔRz, нм | ||
---|---|---|---|---|
до полировки | после полировки | до полировки | после полировки | |
Без перемешивания | 95 ± 9 | 68 ± 6 | 490 ± 40 | 400 ± 20 |
50 | 92 ± 9 | 87 ± 4 | 490 ± 40 | 510 ± 50 |
100 | 85 ± 6 | 99 ± 6 | 490 ± 20 | 561 ± 20 |
Из представленных данных видно, что механическое перемешивание оказывает негативное влияние как на среднюю шероховатость, так и на наибольшую высоту профиля поверхности нержавеющей стали, причем при увеличении скорости перемешивания уже до 100 об/мин наблюдается растравливание поверхности. Наиболее вероятной причиной увеличения Ra и Rz при использовании перемешивания микроэмульсии во время полировки стали является то, что процесс полировки контролируется диффузией капель с травящим реагентом к поверхности металла, а перемешивание способствует ускорению данного процесса [25] и тем самым увеличивает скорость полировки стали. Из этого следует, что механическое перемешивание микроэмульсии в процессе химической полировки нержавеющей стали является избыточным.
Таким образом, значительное уменьшение шероховатости нержавеющей стали происходит в широком диапазоне составов обратной микроэмульсии SDS с СHCl в в.ф = 0.2–0.3 моль/л при продолжительности процесса химической полировки в широком временном диапазоне от 10 до 40 мин в отсутствие механического перемешивания микроэмульсии.
На рис. 6 приведены типичные изображения топографии микрорельефа поверхности стальной пластины до обработки обратной микроэмульсией (нулевая точка) и после обработки обратной микроэмульсией с СHCl в в.ф = 0.2 моль/л в течение 20 мин без механического перемешивания, полученные с помощью микроинтерферометра.
Рис. 6.
Топография микрорельефа поверхности стали: а – до обработки обратной микроэмульсией; б – после обработки обратной микроэмульсией с составом S = 10, Xв.ф. = 0.2, Xкер = 0.9, СHCl в в.ф. = 0.3 моль/л в течение 20 мин.
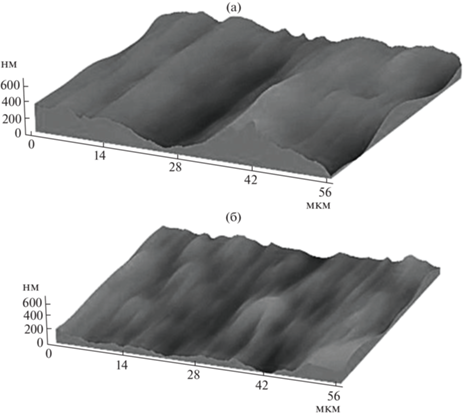
На представленном рисунке хорошо видно уменьшение высоты неровностей поверхности почти на 200 нм. С учетом сохранности формы стальной пластинки можно говорить о верности предположения механизма химической полировки с помощью обратной микроэмульсии [25]. Вследствие броуновского движения капли обратной микроэмульсии, размер которой на три порядка больше размера молекулы неорганической кислоты, с наибольшей вероятностью будут сталкиваться с выступами, а не со впадинами микрорельефа поверхности металла и тем самым растворять выступы на поверхности, не увеличивая размер впадин. Поскольку гидродинамический диаметр капель обратной микроэмульсии SDS до полировки и спустя 50 мин проведения процесса сохраняется на уровне 3 нм, можно предположить, что продукты реакции взаимодействия соляной кислоты с компонентами нержавеющей стали не оказывают значительного влияния на микроэмульсионную систему, а следовательно, и на предложенный процесс химической полировки стали.
ЗАКЛЮЧЕНИЕ
Определена область существования микроэмульсии IV типа по классификации Винзора в системе додецилсульфат натрия–бутанол-1–керосин–водный раствор соляной кислоты при S = = 10 и СHCl в в.ф от 0.01 до 1 моль/л. Показано, что присутствие соляной кислоты с концентрацией 0.01 моль/л почти не изменяет область существования микроэмульсии, а с концентрацией 0.1 моль/л – увеличивает ее по сравнению с такой же микроэмульсионной системой, но без кислоты. Увеличение СHCl в в.ф до 1 моль/л препятствует образованию в системе микроэмульсии IV типа.
Для проведения процесса химической полировки нержавеющей стали марки 08Х18Н10 предложен состав обратной микроэмульсии в системе додецилсульфат натрия–бутанол-1–керосин–водный раствор соляной кислоты: S = 10, Xв.ф = = 0.2, Xкер = 0.9. Определено, что такая обратная микроэмульсия имеет широкую область существования, может содержать в водной фазе до 0.6 моль/л соляной кислоты и сохраняет свою устойчивость в диапазоне температур от 25 до 80°С. Гидродинамический диаметр капель таких обратных микроэмульсий составляет 3 нм.
Определено влияние СHCl в в.ф и продолжительности процесса полировки на микрорельеф поверхности нержавеющей стали. Показано, что наибольшее статистически значимое изменение средней шероховатости поверхности достигается при СHCl в в.ф = 0.2 моль/л спустя 40 мин полировки (изменение Ra на 19% по сравнению с Ra необработанной стальной пластины) и при СHCl в в.ф = = 0.3 моль/л через 10 мин (изменение Ra на 22% по сравнению с Ra необработанной стальной пластины). Данные результаты получены при полировке стали при температуре 60°С в отсутствие механического перемешивания микроэмульсии. Проведение полировки в аналогичных условиях при перемешивании микроэмульсии приводит к ухудшению результата полировки, а также к растравливанию поверхности стали.
Выбран способ очистки поверхности нержавеющей стали после химической полировки, а именно: последовательная промывка в ацетоне, растворе соды с концентрацией 20 г/л, нагретом до 70°C, и в кипящей бидистиллированной воде. Продолжительность каждой стадии промывки составляет 30 мин. Показано, что выбранный способ очистки не влияет на шероховатость поверхности нержавеющей стали.
Список литературы
Marinescu I.D., Rowe B., Dimitrov B. et al. Tribology of abrasive machining processes. William Andrew, 2012. 586 p.
Grechishnikov V.A., Petukhov Yu.E., Pivkin P.M. et al. // Russ. Eng. Res. 2016. V. 36. № 3. P. 229. https://doi.org/10.3103/S1068798X16030059
Камынина О.К., Кравчук К.С., Лазов М.А. и др. // Журн. неорг. химии. 2021. Т. 66. № 8. С. 958.
Nazarov D.V., Smirnov V.M., Zemtsova E.G. et al. // ACS Biomater. Sci. Eng. 2018. V. 4. № 9. P. 3268. https://doi.org/10.1021/acsbiomaterials.8b00342
Xi J., Shentu L., Hu J. et al. // Appl. Opt. 2017. V. 56. № 2. P. 184. https://doi.org/10.1364/AO.56.000184
Maiboroda V., Tarhan D., Dzhulii D. et al. // Acta Mech. Automat. 2020. V. 14. № 1. P. 1. https://doi.org/10.2478/ama-2020-0001
Догадкина Е.В., Донцов М.Г., Парфенюк В.И. // Физикохимия поверхности и защита материалов. 2016. Т. 52. № 5. С. 554.
Dzhemelinskyi V., Lesyk D., Goncharuk O. et al. // Eastern-European J. Enterprise Technol. 2018. V. 1. № 12. P. 35. https://doi.org/10.15587/1729-4061.2018.124031
Tseng W., Wang Y., Chin J. // J. Electrochem. Soc. 1999. V. 146. № 11. P. 4273. https://doi.org/10.1149/1.1392627
Habibzadeh S., Li L., Shum-Tim D., Davis E.C. et al. // Corrosion Sci. 2014. V. 87. P. 89. https://doi.org/10.1016/j.corsci.2014.06.010
Gomez-Gallegos A.A., Mill F., Mount A.R. // J. Manufacturing Processes. 2016. V. 23. P. 83. https://doi.org/10.1016/j.jmapro.2016.05.010
Duradji V.N., Kaputkin D.E., Duradji A.Y. // J. Electrochem. Soc. 2017. V. 164. № 14. P. E513. https://doi.org/10.1149/2.0811714jes
Belkin P.N., Kusmanov S.A., Parfenov E.V. // Appl. Surface Sci. Adv. 2020. V. 1. P. 100016. https://doi.org/10.1016/j.apsadv.2020.100016
Quitzke S., Kröning O., Safranchik D. et al. // J. Manuf. Process. 2022. V. 75. P. 1123. https://doi.org/10.1016/j.jmapro.2022.01.064
Tyagi P., Goule T., Riso C. et al. // Additive Manufacturing. 2019. V. 25. P. 32. https://doi.org/10.1016/j.addma.2018.11.001
Tyagi P., Goulet T., Riso Chr. et al. // Int. J. Adv. Manufacturing Technol. 2019. V. 100. № 9. P. 2895. https://doi.org/10.1007/s00170-018-2890-0
Smithells metals reference book / Eds. Gale W.F., Totemeier T.C. Elsevier, 2003. 2033 p.
Zhu W.-L., Beaucamp A. // Int. J. Machine Tools Manufacture. 2020. V. 158. 103634. https://doi.org/10.1016/j.ijmachtools.2020.103634
Арымбаева А.Т., Шапаренко Н.О., Поповецкий П.С. и др. // Журн. неорган. химии. 2017. Т. 62. № 7. С. 1001.
Демидова М.Г., Шапаренко Н.О., Подлипс-кая Т.Ю. и др. // Журн. неорган. химии. 2017. Т. 62. № 6. С. 729
Полякова А.С., Мурашова Н.М., Юртов Е.В. // Журн. прикл. химии. 2020. Т. 93. № 2. С. 249.
Полякова А.С., Мурашова Н.М. // Изв. Вузов. Химия и хим. технология. 2021. Т. 64. № 2. С. 66.
Мурашова Н.М., Левчишин С.Ю., Субчева Е.Н. и др. // Физикохимия поверхности и защита материалов. 2020. Т. 56. № 3. С. 309.
Guo Y., Li Hy., Yuan Yh. et al. // Int. J. Miner. Metall. Mater. 2021. V. 28. № 6. P. 947. https://doi.org/10.1007/s12613-020-2105-1
Huang Y.J., Yates M.Z. // Colloids Surf. A. 2006. V. 281. № 1–3. P. 215. https://doi.org/10.1016/j.colsurfa.2006.02.041
Guo Y., Zhao J., Yang Sh. et al. // Powder Technol. 2006. V. 162. № 2. P. 83. https://doi.org/10.1016/j.powtec.2005.12.012
Nassar N.N. // J. Dispersion Sci. Technol. 2010. V. 31. P. 1714. https://doi.org/10.1080/01932690903297306
Подлипская Т.Ю., Булавченко А.И. // Журн. структ. химии. 2016. Т. 57. № 8. С. 1655.
Wang F., Fang B., Zhang Z. et al. // J. Chem. Engineer. Data. 2008. V. 53. № 6. P. 1256. https://doi.org/10.1021/je700601a
da Silva V.L., Ribeiro L.S., de Oliveira Freitas J.C. et al. // J. Pet. Sci. Technol. 2020. V. 10. № 7. P. 2845. https://doi.org/10.1007/s13202-020-00952-y
Krylach I.V., Kudryashov S.I., Olekhnovich R.O. et al. // Laser Phys. Lett. 2019. V. 16. № 10. P. 105602. https://doi.org/10.1088/1612-202X/ab3d32
Shchedrina N., Karlagina Y., Itina T. E. et al. // Optical and Quantum Electronics. 2020. V. 52. № 3. P. 1. https://doi.org/10.1007/s11082-020-02280-1
Rudawska A. // Int. J. Adhesion Adhesives. 2014. V. 50. P. 235. https://doi.org/10.1016/j.ijadhadh.2014.01.032
Olefjord I., Kozma L. // Mater. Sci. Technol. 1987. V. 3. P. 954. https://doi.org/10.1179/mst.1987.3.11.954
Гадалов В.Н., Гвоздев А.Е., Стариков Н.Е. и др. // Изв. Тульского гос. ун-та. Технические науки. 2017. № 11–12. С. 124.
Дополнительные материалы отсутствуют.
Инструменты
Журнал неорганической химии