Проблемы машиностроения и надежности машин, 2019, № 2, стр. 99-105
ЭКСПЕРИМЕНТАЛЬНОЕ ИССЛЕДОВАНИЕ ИЗНОСА МАНЖЕТНОГО УПЛОТНЕНИЯ ВРАЩАЮЩЕГОСЯ ВАЛА
С. Н. Яковлев *
Санкт-Петербургский политехнический университет Петра Великого
г. Санкт-Петербург, Россия
* E-mail: stannik59@mail.ru
Поступила в редакцию 19.06.2017
Принята к публикации 24.12.2018
Аннотация
Приведено подробное описание экспериментальной установки для изучения вопросов износа манжетного уплотнения во фрикционном контакте с вращающимся валом. Представлены эмпирические зависимости для определения величины износа резинового и полиуретанового манжетного уплотнения в зависимости от продолжительности работы.
В современном машиностроении технический прогресс в значительной степени определяется качеством уплотнительных устройств. Среди уплотнительных устройств контактного типа наибольшее распространение получили резиновые армированные манжетные уплотнения вращающихся валов.
Процесс герметизации осуществляется за счет внедрения сжатой резины в микронеровности вращающегося вала и их перекрытие [1–3]. Особенностью работы манжетных уплотнений является тот факт, что на небольшой поверхности контакта манжеты и вала развивается высокая температура, которая ускоряет процессы старения и износа резины в зоне трения. Нагрев резины приводит к ее размягчению, снижению контактного давления во фрикционном контакте, нарушению герметичности уплотнения и как следствие снижению надежности системы манжетного уплотнения в целом. На основании этого можно утверждать, что износостойкость резиновых уплотнений определяется следующими факторами: эксплуатационный (температура во фрикционном контакте, величина избыточного давления уплотняемой среды и линейная скорость в контакте вала с манжетой); физико-механические свойства эластомерного материала манжеты; конструктивные параметры манжетного уплотнения.
В современном машиностроении резину во многих технических приложениях стал заменять полиуретан, который характеризуется высокими физико-механическими свойствами, имеет большой диапазон твердости, эластичности, низкую истираемость, высокую прочность, высокое сопротивление раздиру, маслобензостойкость и кислотостойкость [4–8].
Принимая во внимание тот факт, что износостойкость манжетных уплотнений в большой степени определяется физико-механическими свойствами эластомера, его способностью противостоять затвердеванию и утрате эластических свойств, было решено изготовить и провести испытания манжетных уплотнений с использованием фторсилоксанового полиуретана фирмы “Synair” (Великобритания).
Целью настоящей статьи является получение сравнительных экспериментальных данных о работоспособности полиуретановой манжеты и резиновой, а также величине износа манжеты и вала.
Материалы и методы исследования. Для исследования процессов износа манжетных уплотнений вращающихся валов был спроектирован и изготовлен специальный стенд. Стенд позволяет проводить одновременные испытания двух манжет: одной резиновой из фторкаучука СКФ-26 с размерами 120 × 150 × 12 по ГОСТ 8752-79 и второй полиуретановой, которая имеет абсолютно такие же размеры, как и резиновая, и при изготовлении которой использовалась та же арматура и прижимная (браслетная) пружина. Типичная конструкция манжетного уплотнения по ГОСТ 8752-79 представлена на рис. 1.
Манжетное уплотнение состоит из трех основных элементов: уплотняющий элемент из эластомерного материала; металлическая арматура, придающая манжете необходимую жесткость; браслетная пружина, создающая радиальное усилие на уплотнительную губку и прижимающую ее к валу.
У современных резиновых манжет, предназначенных для работы в диапазоне скоростей до 20 м/с, используются фторкаучуки СКФ-26, рабочая температура которых согласно ГОСТ 8752-79 составляет от –20 до +170°С. При этом ресурс составляет 10 000 часов. Такой тип манжет используется для работы в тяжелых условиях: высокая линейная скорость во фрикционном контакте вала и манжеты (до 20 м/с); высокая температура уплотняемой среды (до 90°С); высокое избыточное давление уплотняемой среды (до 0.05 Мпа).
Такие условия работы свойственны для крупных дизельных двигателей внутреннего сгорания, винтовых и поршневых компрессоров и т.д.
Для экспериментальной манжеты используется полиуретан, который согласно [9–13] сохраняет работоспособность (эластичность, отсутствие оплавления и растрескивания) в диапазоне рабочих температур от –60 до +200°С. Эти материалы нашли широкое применение в технике, благодаря малой зависимости физико-механических свойств от температуры.
В качестве движителя специального стенда используется асинхронный электродвигатель АИР71А2 мощностью 0.75 кВт и частотой вращения 3000 об/мин с частотным преобразователем, который позволяет плавно регулировать частоту вращения от 350 до 3000 об/мин. Кинематическая схема испытательного стенда представлена на рис. 2.
Рис. 2.
Кинематическая схема установки: 1 – электродвигатель; 2 – муфта; 3 – винт; 4 – вал; 5 – резиновая манжета; 6, 12 – крышки; 7 – прокладка; 8 – корпус; 9 – штуцер; 10 – подшипник; 11 – распорная втулка; 13 – полиуретановая манжета; 14 – технологическое отверстие; 15 – зубчатый венец; 16 – полиуретановый вкладыш; 17 – стойка; 18 – полиуретановая прокладка; 19 – плита.
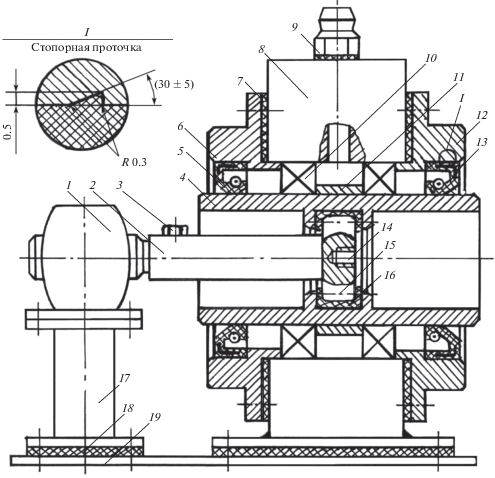
Центральным звеном испытательного стенда является вал 4, установленный на двух подшипниках 10 в корпусе 8. Вал изготовлен из стали 40Х, закаленной до твердости 60 HRC. Наружный диаметр вала прошлифован, шероховатость поверхности составляет Rа 0.32. Для предотвращения осевого смещения вала относительно корпуса, опорные шарикоподшипники своими внутренними кольцами упираются в распорную втулку 11, при этом наружные кольца подшипников поджимаются крышками 6 и 12 для устранения осевого люфта.
Между крышками, в которых установлены манжеты 5 и 13, используемые в экспериментальном исследовании, и корпусом располагаются паронитовые прокладки 7, которые допускают относительную деформацию при сжатии ε = 20…25%, что вполне достаточно для выборки осевого люфта подшипников. Для исключения осевого перемещения манжет от вибраций, в крышках 6 и 12 выполнены кольцевые проточки в виде прямоугольного треугольника, острие которого направлено в сторону запрессовки манжеты.
Передача крутящего момента от электродвигателя к валу осуществляется с помощью зубчатой муфты 2, на конце которой установлен полиуретановый вкладыш 16, служащий для компенсации осевой и угловой расцентровки между валом и муфтой. Муфта имеет центральное технологическое резьбовое отверстие 14, в которое при сборке стенда вкручивается оправка. Для предотвращения осевого смещения муфты вдоль выходного вала электродвигателя используется винт 3. Уплотняемая смазочная среда подается по шлангу через штуцер 9 под давлением в корпус испытательного стенда. Корпус испытательного стенда и электродвигатель установлены на плите 19 через виброизолирующие полиуретановые пластины 18 для уменьшения вибраций.
Таким образом испытательный стенд позволяет проводить экспериментальные исследования в диапазоне скоростей от 2 до 18 м/с и избыточном давлении уплотняемой среды от 0 до 0.05 МПа.
Заявленная цель экспериментального исследования является первой в целом ряду вопросов изучения долговечности, работоспособности и надежности манжетных уплотнений. По результатам опубликованных работ установлено, что основным видом износа уплотнений вращающихся валов является усталостный, когда частицы износа эластомера отделяются от уплотнительной губки манжеты в результате многократного действия повторных сжимающих и сдвиговых деформаций.
При выборе параметров нагружения манжеты для проведения экспериментального исследования, мы ориентировались на применение манжет в конструкции дизеля в составе дизель-электростанции. В качестве рабочих параметров нагружения манжетного уплотнения была выбрана линейная скорость 10 м/с и величина избыточного давления уплотняемой среды (моторное масло) 0.03 Мпа. Продолжительность стендовых испытаний приняли равной ресурсу стандартной манжеты, т.е. 10 000 часов.
Методика экспериментального исследования представляет собой последовательность следующих шагов: испытания проводим с частотой вращения вала n = 1500 об/мин (Vлин = 9.42 м/с) и давлении уплотняемой среды Pизб = 0.03 Мпа; замер радиального износа манжеты Им, максимальной глубины канавки изношенной поверхности вала Ив и ширины контакта рабочей кромки манжеты производим после разборки испытательного стенда через каждые 1000 часов испытаний; полученные в ходе экспериментального исследования данные сводим для наглядности в табл. 1 и обрабатываем, полученные в ходе экспериментального исследования результаты, методами математической статистики.
Таблица 1.
Износ манжеты и вала
Продолжительность работы, тыс. ч. | Износ, мм | |||
---|---|---|---|---|
Износ резиновой манжеты, мм | Износ вала в контакте с резиновой манжетой, мм | Износ полиуретановой манжеты, мм | Износ вала в контакте с полиуретановой манжетой, мм | |
1 | 0.18 | 0.13 | 0.15 | 0.10 |
2 | 0.25 | 0.17 | 0.20 | 0.13 |
3 | 0.30 | 0.20 | 0.24 | 0.14 |
4 | 0.35 | 0.22 | 0.28 | 0.16 |
5 | 0.39 | 0.24 | 0.30 | 0.17 |
6 | 0.43 | 0.25 | 0.33 | 0.18 |
7 | 0.46 | 0.26 | 0.35 | 0.19 |
8 | 0.49 | 0.28 | 0.37 | 0.20 |
9 | 0.52 | 0.29 | 0.39 | 0.21 |
10 | 0.54 | 0.30 | 0.41 | 0.22 |
Результаты исследования. Проведенные экспериментальные исследования показывают, что острая кромка манжеты притупляется, на валу в месте фрикционного контакта образуется канавка. Решающее влияние на работоспособность манжеты оказывает величина радиального износа ее кромки.
Величину износа манжеты определяли по разности тороидных диаметров браслетной пружины, замеренных с помощью специального приспособления до испытаний и после определенного периода работы (через 1000 часов). Износ вала замеряли на профилографе А-7 завода “Калибр” (при глубине канавки до 0.1 мм) и на инструментальном микроскопе УИМ-21 (при глубине канавки свыше 0.1 мм) с использованием проекционного (теневого) метода.
При проведении замеров величины износа вала на инструментальном микроскопе удалось разглядеть профиль канавки износа. Он полностью соответствует профилю рабочей кромки манжеты. Очевидно причиной образования канавки стали металлические частицы износа вала, внедрившиеся в эластомерный материал манжеты, о чем свидетельствует их наличие в кромке манжеты и кольцевой характер рисок по всей площади канавки.
Процесс износа манжет и валов аналогичен, несмотря на огромное различие физико-механических свойств материалов. Радиальное изнашивание рабочей уплотнительной кромки манжеты происходит с убывающей во времени интенсивностью. Максимальная интенсивность согласно [14–16] наблюдается в начальный период работы, когда кромка манжеты острая и полоска контакта имеет минимальную ширину, вследствие упругой деформации эластомера.
Полученные экспериментальные данные об износе манжет и вала сведены в таблицу 1 и для большей наглядности показаны на рис. 3, где 1 – полиуретан, 2 – резина.
Рис. 3.
Зависимость износа манжет Им и вала Ив от продолжительности испытания: 1 – полиуретан; 2 – резина.
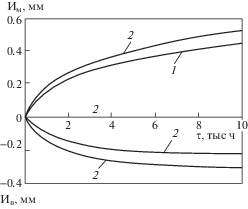
Долговечность манжетного уплотнения до выхода из строя можно определить, установив момент наступления предельного состояния, когда оно теряет герметичность. Для данного типоразмера манжеты согласно ГОСТ 8752-79 принимается срок ее службы пока утечка уплотняемой среды не превысит 0.5 см3/ч. Результаты испытаний показали, что резиновая манжета начала терять герметичность после 8000 часов работы при радиальном износе рабочей кромки примерно 0.5 мм и глубине канавки на валу 0.3 мм.
У полиуретановой манжеты потери герметичности в течение всего срока испытания не произошло.
Выводы.
1. При рабочих температурах, не вызывающих растрескивания кромки, износ манжеты и вала является главным фактором, определяющим долговечность уплотнения.
2. Износ полиуретановой манжеты и вала примерно на 20…25% меньше, чем у резиновой, что объясняется различием фрикционных свойств полиуретана и резины. Этот факт подтверждает перспективность применения полиуретана в качестве эластомерного материала манжеты.
3. Радиальное изнашивание рабочей кромки манжеты и вала происходит с убывающей во времени интенсивностью.
Список литературы
Лепешкин А.В., Михайлин А.А. Гидравлические и пневматические системы // М.: Академия, 2013. 336 с.
Схиртладзе А.Г. Гидравлические и пневматические системы // М.: Высшая школа, 2006. 405 с.
Винников В.А. Гидромеханика // М.: МГГУ, 2003. 384 с.
Janusz Datta. Influence of Glycols on the Glycolysis Process and the Structure and Properties of Polyurethane Elastomers // Journal of Elastomers and Plastics. 2011. № 43. P. 529–541.
Sheng Li. Effect of Elastomer on Flame Retardancy, Thermal Degradation, and Mechanical Properties of Intumescent Flame-Retardant Polyethylene // Journal of Elastomers and Plastics. 2011. № 43. P. 257–273.
Janusz Datta. Synthesis and Investigation of Glycolysates and Obtained Polyurethane Elastomers // Journal of Elastomers and Plastics. 2010. № 42. P. 117–127.
Yakovlev S.N. Dynamic Hardening of Structural Polyurethanes // Russian Engineering Research. 2016. № 4. P. 255–257.
Franssen O., Bayerl H. Die Erfolgsgeschichte der Siliconelastomere. Siliconelastomere // Gummi. Fasern. Kunststoffe 2012. № 7. P. 462–470.
Neise E., Zepp C. Optische Deformations analyse von Fahrzeugreifen. Dynamische Reifenanalyse // Gummi. Fasern. Kunststoffe. 2013. № 1. P. 23–30.
Marcos Pacheco, Thermal F.M. Chemical, and Morphological Characterization of Microcellular Polyurethane Elastomers // Journal of Elastomers and Plastics. 2009. № 41. P. 323–338.
Yakovlev S.N. Self-Oscillation of an Elastic Polyurethane Coating in Polishing // Russian Engineering Research. 2014. № 5. P 295–298.
Kahraman H., Haberstroh E. Einfluss von aktiven Fullstoffen in Elastomeren auf den anisotropen Mullins–Effekt. Anisotroper Mullins–Effekt // Gummi. Fasern. Kunststoffe. 2014 № 5. P. 296–298.
Cai-Hong Lei. Thermoplastic vulcanizates based on compatibilized and silicone rubber blend // Journal of Elastomers and Plastics. 2012. № 44. P. 563–574.
Уорд И. Механические свойства твердых полимеров // М.: Химия, 1975. 357 с.
Логиновас А.К. Исследование износа манжетного уплотнения вращающегося вала // Каучук и резина. 1971. № 3. С. 26–29.
Коморницкий-Кузнецов В.К., Рыбалов С.Л., Юровский В.С. и др. Фрикционные свойства резино-армированных манжет, уплотняющих вращающиеся валы // Каучук и резина. 1971. № 11. С. 36–38.
Дополнительные материалы отсутствуют.
Инструменты
Проблемы машиностроения и надежности машин