Проблемы машиностроения и надежности машин, 2020, № 1, стр. 73-82
ТРИБОЛОГИЧЕСКИЕ ПРОТИВОИЗНОСНЫЕ ПОКРЫТИЯ
А. Ю. Албагачиев 1, *, М. Е. Ставроский 2, **, М. И. Сидоров 2, ***
1 Институт машиноведения им. А.А. Благонравова РАН
г. Москва, Россия
2 МИРЭА – Российский технологический университет
г. Москва, Россия
* E-mail: albagachiev@yandex.ru
** E-mail: stavrov@list.ru
*** E-mail: mihail.sidorov0213@gmail.com
Поступила в редакцию 23.03.2018
После доработки 18.10.2019
Принята к публикации 25.10.2019
Аннотация
В статье рассмотрены износостойкие трибологические покрытия для повышения живучести артиллерийских, танковых и винтовочных стволов. С использованием некоторых проведены исследования. Отмечено наличие достаточно большого научно-технического задела в области материаловедения жаропрочных сплавов и антифрикционных противоизносных покрытий.
Проблема повышения живучести артиллерийских стволов является актуальной по многим причинам, в том числе, экономическим. Основной причиной выхода ствола из строя является расширение его канала вследствие износа. Это приводит к прорыву пороховых газов и падению их давления, девиации снаряда и, как следствие – к снижению дульной скорости и кучности стрельбы. Износ канала ствола зависит от количества выстрелов, условий ведения огня, ухода за орудием, состояния боеприпасов. Основной износ 125 мм танковой пушки 2А46М и 2А46М-1, например, происходит при выстреле бронебойно-подкалиберными снарядами. Труба подлежит замене при увеличении диаметра канала ствола на 3.3 мм на расстоянии 850 мм от казенного среза трубы (не более 100 выстрелов при стрельбе бронебойно-подкалиберными снарядами – замена ствола).
Величина износа зависит от ряда факторов, прямо или косвенно приводящих к разрушению поверхностного слоя канала ствола из соответствующего металла: трение ведущих устройств снаряда о стенки ствола; эрозионное и механическое воздействие газопороховой смеси; динамические нагрузки в процессе врезания или опрессовки ведущих устройств в заходном конусе канала ствола; диффузия различных газообразных продуктов разложения пороха в поверхностный слой канала ствола; циклические тепловые нагрузки на материал ствола и, как следствие, структурно-фазовые превращения в металле и усталостное разрушение поверхностного слоя.
Первичная апробация металлоплакирующих составов с целью повышения живучести стволов была выполнена при полигонных испытаниях пушки МТ-12 (ФКП НИИ “Геодезия”, 2001 г.). Перед стрельбой на очищенную и обезжиренную поверхность канала ствола № 1189 был нанесен металлоплакирующий антифрикционный противоизносный состав в объеме 58 см3. Ранее из данного ствола было произведено 64 выстрела бронебойными подкалиберными снарядами. На ведущие пояски снарядов перед каждым выстрелом наносился тонкий слой состава № 2 (для повышения живучести ствола) (на 100 снарядов израсходовано также 58 см3 состава № 2 на основе мелкодисперсного серпинтинита).
Полигонные испытания защитного покрытия, нанесенного при помощи металлоплакирующих противоизносных составов, проводились стрельбой бронебойно-подкалиберными снарядами 5М2 в объеме 20 выстрелов в каждый день испытаний. Всего из пушки МТ-12 произведено 100 выстрелов. После отстрела каждой группы выстрелов (20 шт.) пушка выдерживалась в течение суток при температуре помещения 10–13°С, после чего производился обмер канала ствола механической звездкой через каждые 50 мм, а в сечениях, прилегающих к зарядной каморе (930, 1050, 1260, 1380, 1500 мм), обмер производился прибором контроля износа (ПКИ-19). В табл. 1 помещены данные по износу за 1 выстрел.
Таблица 1.
Износ на 1 выстрел в сечениях | Ствол № 1189 с проведением мероприятий антиизноса (60 выстрелов), ИЗНОС – мм | Ствол № 00298 без антиизносных мероприятий (58 выстрелов), ИЗНОС – мм |
---|---|---|
Обмер механической звездкой | ||
4500 мм | 0.0020 | 0.010 |
4900 мм | 0.0008 | 0.014 |
5100 мм | 0.0008 | 0.020 |
Обмер прибором ПКИ | ||
1260 мм | 0.0025 | 0.019 |
1380 мм | 0.0008 | 0.015 |
1500 мм | 0.0008 | 0.013 |
Дополнительно была произведена серия испытаний из 44 выстрелов из изношенного ствола после 200 выстрелов. При анализе результатов из рассмотрения были исключены выстрелы обычными снарядами (ОФС, ОФК), так как по данным обмеров после проведения серии из 34 выстрелов такими снарядами износа не было обнаружено, как до стрельб, так и после них износ в сечениях 1260 мм, 1380 мм и 1500 мм составил 2.6 мм; 2.2 мм, 2.0 мм, соответственно. Кроме этого, не учитывались результаты замеров перед 44 выстрелами подкалиберными снарядами, так как стрельбы из ствола перед этим более 7.5 лет не производились, вследствие чего ствол покрылся коррозионной пленкой, которая удалялась не полностью даже при тщательной чистке. Вместо этого были использованы результаты промежуточных замеров после 22 выстрелов подкалиберными снарядами и замеров после 44 выстрелов, проводившихся прибором ПКС в течение суток.
По результатам испытаний видно, что износ очень велик на начальном участке, но резко падает по мере приближения к дульному срезу. Причем износ у дульного среза становится заметным только после проведения всех стрельб. Темп износа на последних 44 выстрелах, проведенных по антиизносной технологии, резко падает по сравнению с износом на предыдущих 137 выстрелах, проведенных по штатной технологии. В среднем темп износа падает в 3 раза – с 1.8 мм на один выстрел до 0.6 мм на один выстрел. Снижение износа находится в пределах от двух до трехкратного по сравнению со штатной технологией.
Другая серия полигонных испытаний защитного покрытия была выполнена с использованием танковой пушки Д-81 (ФКП НИИ “Геодезия”). Испытания износостойкости покрытия, нанесенного на поверхность канала ствола, проводились стрельбой бронебойно-подкалиберными снарядами индекс ЗБМ42 в объеме 35 выстрелов в ФКП НИИ “Геодезия”. Перед проведением работ поверхность канала ствола была почищена с использованием механизма чистки ствола (МЧТ) из состава передвижного комплекса КПМ 1437 и обезжирена бензином. Затем была измерена величина и характер износа канала ствола прибором ПИНТ (прибор измерения непрямолинейности трубы) из состава КПМ 1437 с инструментальной погрешностью 0.01 мм. После проведения начальных измерений на поверхность канала ствола был нанесен противоизносный состав № 1 (хлорид меди (I) – 2–5 мас. %, оксид кремния – до 4 мас. %, глюкоза – 1–5 мас. %, глицерин – остальное). После нанесения защитного покрытия произведен отстрел двух групп по 7 выстрелов в группе и одна группа из 14 выстрелов, затем одна группа из 7 выстрелов “Манго”, на ведущие пояски которых перед стрельбой наносился состав № 2. После отстрела каждой группы ствол чистился, вытирался насухо. После этого производился обмер канала ствола прибором ПИНТ.
В процессе всех стрельб фиксировались начальная скорость и техническое рассеивание снарядов на дистанции 100 м. Результаты измерений диаметра канала ствола № 512 125 мм пушки № РГ1370 приведены в табл. 2.
Таблица 2.
Расстояние от казенного среза, мм | 1200 | 1100 | 1000 | 900 |
Первичные значения износа, мм | 0.542 | 0.570 | 0.580 | 0.590 |
Величина износа после 7 выстрелов | 0.582 | 0.630 | 0.640 | 0.658 |
Величина износа после 14 выстрелов | 0.617 | 0.685 | 0.698 | 0.726 |
Величина износа после 28 выстрелов | 0.655 | 0.732 | 0.812 | 0.850 |
Величина износа после 35 выстрелов | 0.720 | 0.810 | 0.880 | 0.950 |
Величина удельного износа по антиизносной технологии | 0.0051 | 0.0069 | 0.0086 | 0.0102 |
Величина удельного износа по штатной технологии | 0.012 | 0.015 | 0.018 | 0.020 |
Коэффициент увеличения износостойкости | 2.4 | 2.2 | 2.1 | 2.0 |
Для оценки износостойкости ствола по полученным результатам были построены экспериментальные зависимости износа от настрела по результатам стрельб однотипными снарядами “Манго” из 4-х стволов, проведенными в ФКП НИИ “Геодезия” без применения антиизносной технологии.
Осредненные зависимости показали, что в пределах 120 выстрелов зависимость износа от количества выстрелов носит линейный характер, т.к. отклонения средних значений износа на всех графиках от прямой отличаются незначительно по сравнению с отклонениями от ствола к стволу. Из полученных данных следовало, что в процессе применения “безызносной” технологии на поверхность канала ствола защитного покрытия его износостойкость увеличивается в 2.2 раза.
При использовании вместо линейных зависимостей средних экспериментальных, в области от 0.5 до 1.0 мм коэффициент износостойкости увеличится до 3–3.5 (в сечении 1000 мм удельный износ в этой области равен не 0.015 мм, а 0.022 мм соответственно коэффициент износостойкости возрастает до 3.2).
Таким образом, пробные полигонные испытания антифрикционных противоизносных покрытий, выполненные специалистами ФКП НИИ “Геодезия”, показали перспективность этого направления исследований. Систематические исследования предполагают обзор и оценку опыта, наработанного в этом и смежных направлениях.
Апробации противоизносных триботехнических составов для повышения живучести стволов стрелкового оружия и артиллерийских орудий посвящены работы [1, 2]. Так, в [1] отмечается, что существуют материалы или триботехнические составы (композиции), которые способны в паре трения при определенных условиях инициировать процессы самоорганизации трения в триботехнически выгодном направлении. Эффект наращивания поверхностей трения происходит за счет введения в смазку различных присадок: органических соединений (фторопласт, стирол, спирты, жирные кислоты и др.); металлов (Со, Ni, Си, Zn и др.); катализаторов (Pt, Pd, фуллериды и др.); керамики на основе Nb, Та, Zr и др.; жидких кристаллов (металлов, растворимых в органическом соединении), которые формируют антифрикционный поверхностный слой; наполнителя (природных и искусственных соединений в порошкообразном виде), который формирует подповерхностный слой.
Исследования, проведенные в “ЦКИБ СОО”, показали, что наиболее подходящим для применения в стрелковом оружии является полифункциональный состав “Живой металл” (СПФ “ЖМ”), разработанный НИИ специальных технологий, представляющий собой комплекс специальным образом переработанных природных и синтетических катализаторов, органических структур и керамики. В СПФ “ЖМ” применены специально переработанные (гидротермальный каталитический синтез) минералы и включены специальные и металлорганические (каталитические) системы, что придает СПФ способность к саморегуляции, а также формированию неоднородных (металл, керамика, органические соединения) защитных покрытий, не трескающихся и не откалывающихся при механическом и термическом воздействии. Специальные каталитические системы, включенные в СПФ, снижают насыщение водородом трущихся металлических поверхностей, не допускают снижения прочности поверхностного слоя при диффузии дисперсионно-упрочняющихся систем с поверхностных слоев в более глубокие.
Основу дисперсионно-упрочняющей системы составляет серпентинит. Серпентинит – метафорическая (вторичная) ультраосновная горная порода, имеющая плотность 2.5–2.7 г/см3, и состоящая из серпентина, магнитного железняка Fe304, хромистого железняка и остатков исходных первичных горных пород – оливинов и пироксенов. Основным элементом серпентинита является серпентин, который состоит из силикатов и куросиликатов магния, кадмия и железа. Общая формула – ${\text{M}}{{{\text{g}}}_{6}}\left[ {{\text{S}}{{{\text{i}}}_{4}}{{{\text{O}}}_{{10}}}} \right]{{\left( {{\text{OH}}} \right)}_{8}}$. Незначительная часть кремния замещается алюминием, а магния – Al, Fe2+, Fe3+, Ni, образуя новые минералы. Минералогическая структура серпентинов напоминает структуру подшипниковых сплавов: в мягкой волокнистой основе распределены твердые кристаллы (кремнекислородные тетраэдры ${{\left[ {{\text{Si}}{{{\text{O}}}_{4}}} \right]}^{{4 - }}}$). Плотность серпентина 2.55 г/см3, твердость по шкале Мооса 2.5–3.5, что соответствует микротвердости 73–149 кгс/мм2 или твердости мало- и среднеуглеродистых сталей в отожженом состоянии.
СПФ “ЖМ” состоит из: 27.5% – дисперсионно-упрочняющиеся системы, полученные из минералов; 9% – специальные каталитические системы, полученные методом каталитического органического синтеза; 10% – металлоорганический комплекс, содержащий клатратные гетероциклические органические соединения, полученные в результате биосинтеза, а также себациновую и изоциануровую кислоты; 3.5% – клатратная система, содержащая органометаллические и фторорганические компоненты; 25% – кремний-фторорганические, полиэфирные, полиамидные органические соединения; 25% – масло И20А.
Исследования по определению коэффициента трения страгивания (покоя) для триботехнических пар сталь 30ХН2МФА без покрытия, с хромовым покрытием и СПФ “ЖМ” в сочетании со сталью 20, медью и бронзой (табл. 3) показали, что наибольшее сопротивление страгиванию создает хромовое покрытие, наименьшее – СПФ “ЖМ”.
Таблица 3.
Коэффициенты трения страгивания (покоя)
Материалы триботехнических пар | Коэффициенты трения | ||
---|---|---|---|
сталь 20 | медь | бронза | |
Сталь 30ХН2МФА | 0.079 | 0.093 | 0.084 |
Сталь 30ХН2МФА + хром | 0.131 | 0.178 | 0.150 |
Сталь 30ХН2МФА + СПФ “ЖМ” | 0.071 | 0.089 | 0.067 |
Технология нанесения трибологического покрытия на поверхность канала ствола описана в работе [1]. Предварительно канал ствола обрабатывается смесью природных материалов и биологических ферментных систем, растворенных и взвешенных в изиопропиловом спирте при температуре 50–80°С в течение 60–90 мин. Затем на поверхность канала ствола наносится покрытие, представляющее собой полифункциональный состав, состоящий из смеси гомогенных и гетерогенных катализаторов и дисперсионно-упрочняющих систем в вязком носителе. Далее производится термообработка первого слоя в течение 2–4 часов при температуре 110–120°С. После чего ствол присоединяется к образцу оружия, оружие заряжается и производится выстрел, упрочняя тем самым нанесенное покрытие. Количество упрочняющих выстрелов зависит от калибра оружия.
Установлено [1], что апробация данного способа на различных моделях спортивно-охотничьего и снайперского оружия с последующим их испытанием показало, что полученное покрытие не уступает хромовому по износостойкости и превосходит его по сохранению параметров внутренней и внешней баллистики оружия. Применение СПФ “ЖМ” позволило увеличить ресурс стволов 12.7 мм снайперской винтовки ОСВ-96 в 2–2.5 раза при стрельбе как моноблочными, так и оболочечными пулями.
В работе [2] износ канала ствола определяется, как изменение его размеров, контура и качественного состояния элементов (зарядной каморы, нарезов, внутреннего диаметра), и возникает вследствие многократно повторяемого чрезвычайно мощного воздействия на его поверхность пороховых газов и ведущих частей снарядов. Характеристикой износа канала ствола гладкоствольной пушки является увеличение внутреннего диаметра, а у нарезного ствола – изменение геометрических размеров нарезов и удлинение зарядной каморы.
У гладкоствольных пушек увеличение диаметра канала ствола под воздействием ударно-вибрационных нагрузок может происходить в нескольких сечениях по длине трубы, а это сказывается на изменении боя пушек. В нарезных стволах уже после первых выстрелов в начале нарезов можно наблюдать появление мелких трещин (рис. 1а). В дальнейшем (после 200–300 выстрелов) трещины увеличиваются и образуют сетку с замкнутыми петлями, постепенно распространяющуюся по каналу в направлении к дульной части (рис. 1б); при этом наблюдаются сплющивание и стирание полей в начале нарезов. После 1000–2000 выстрелов большинство трещин оказываются сориентированными вдоль оси канала ствола из-за эрозионного действия пороховых газов (рис. 1в, г), кроме того, наблюдается выкол полей у начала нарезов, их боевые грани стираются, поля округляются.
Рис. 1.
Износ стенки нарезного ствола: (а) – мелкие трещины; (б) – сетка с замкнутыми нитями; (в), (г) – сориентированные трещины.
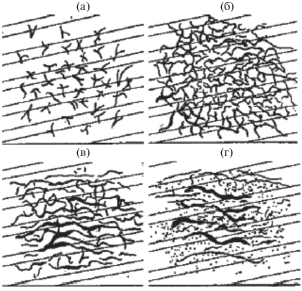
Одним из решений проблемы снижения трения и последствий ударно-вибрационных нагрузок в системе ствол–снаряд [2], может быть применение уже известных в различных отраслях промышленности специальных антифрикционных составов. В области борьбы с трением и сопутствующим ему износом более 10 лет работает научно-производственная инновационная фирма (НПИФ) “ЭНИОН – БАЛТИКА”. В работе [2] авторы отмечают, что существует принципиально новое и эффективное решение проблемы трения. В 2001 году совместно с ОАО “Научно-производственное предприятие “Радий” разработан и запатентован триботехнический состав направленной ионной диффузии (ТС НИОД). Его применение позволяет добиться уникального антифрикционного эффекта в любых парах трения за счет существенного изменения триботехнических свойств взаимодействующих поверхностей. Процесс происходит непосредственно в пятне контакта под действием рабочих нагрузок и температур во время штатной эксплуатации механизма. Этот триботехнический состав существенно отличается от существующих присадок к смазкам и модификаторов тем, что для нормального функционирования механизма не требуется его постоянное присутствие в смазке, т.е. НИОД позволяет эксплуатировать некоторые механизмы вообще без смазки. Триботехнический состав НИОД – мелкодисперсный материал (размеры частиц 5–50 мкм), основой которого является серпентинит. Состав не является модификатором либо присадкой к смазке, а также собственно смазкой. Эффект при применении ТС НИОД возникает не вследствие изменения свойств смазки, т.е. “третьего тела”, а за счет изменения свойств взаимодействующих поверхностей, и проявляется этот эффект в течение длительного времени, когда самого триботехнического вещества в пятне трения уже нет [2]. Предполагается что в отличие от присадок, ТС не образует пленку на поверхности металла, а внедряется в приповерхностные слои под действием взаимного контактного давления двух соприкасающихся деталей (например, зубья шестерен, шарик и дорожка качения обойм в подшипнике, компрессионное кольцо и стенка цилиндра и т.п.). В действии ТС выделяют следующие фазы: очистка и микрошлифование поверхностей трения; внедрение в поверхность деталей под действием контактного давления; распределение ТС в приповерхностном объеме с возможным образованием твердых растворов путем замещения катионов магния в ТС катионами железа; микровосстановление формы и размеров деталей; образование антифрикционного эффекта на контактирующих поверхностях за счет уменьшения шероховатости до Ra = 0.16 мкм и выравнивания твердости обеих поверхностей.
Интенсивность внедрения ТС в поверхность пропорциональна локальному давлению и температуре в пятне контакта. Поэтому вызванные износом деталей биения стимулируют внедрение ТС именно в наиболее изношенные участки поверхности, что приводит к микровосстановлению линейных размеров сопрягаемых деталей.
В результате изменения свойств взаимодействующих поверхностей на поверхностях трения образуется “псевдолегированный” слой, обладающий высокой твердостью и низкой шероховатостью поверхности. Коэффициент трения между “новыми” поверхностями снижается в 2–3 раза, а их износостойкость значительно возрастает. Характерной особенностью процесса является его способность к саморегуляции, обусловленная тем, что он происходит одновременно в обеих контактирующих поверхностях под воздействием одной и той же нагрузки. При этом внедрение ТС НИОД в более твердую поверхность происходит медленнее, что приводит в итоге к полному выравниванию микротвердости поверхностных слоев контактирующих поверхностей. Считается, что одинаковая микротвердость в сочетании с низкой шероховатостью поверхности приводит к возникновению уникального антифрикционного эффекта.
В целом применение ТС НИОД обеспечивает снижение коэффициента трения, увеличение в несколько раз ресурса узлов и механизмов; высокую износостойкость, значительный срок последействия и возможность работы некоторых узлов трения в “сухом режиме” (без смазки). ТС НИОД испытаны на артиллерийских системах. В период с 2002 по 2007 г. на базе Коломенского артиллерийского училища проводились экспериментальные стрельбы с целью исследования влияния триботехнического состава на живучесть стволов как нарезных, так и гладкоствольных орудий. Стрельбы из 152 мм гаубиц 2А65 проводились с нанесением триботехнического состава НИОД четырьмя различными способами: на нормальную крышку, на ведущий поясок, на центрующие утолщения и без нанесения ТС.
По результатам стрельб было установлено, что наиболее эффективным способом применения ТС НИОД является обработка центрующих утолщений снаряда. При этом способе после 100 выстрелов удлинение зарядной каморы было на 67.4% меньше, чем у орудия, на котором состав не применялся. Менее эффективным по результатам стрельбы явился способ обработки ведущего пояска снаряда, снижающий удлинение зарядной каморы при тех же условиях на 30.4%. Самая низкая эффективность состава была установлена при обработке нормальной крышки метательного заряда: уменьшение износа зарядной каморы составило 3.7%.
Целью проверки длительности сохранения достигнутого результата были продолжены исследования [2], которые проводились при тех же условиях стрельбы и из тех же гаубиц 2А-65. Для этого из каждого орудия было произведено по 100 контрольных выстрелов. Анализ результатов последствий стрельбы и их сопоставление с предыдущими испытаниями позволил сделать вывод, что наибольшая сохраняемость результатов получена в орудии, у которого ТС обрабатывались центрующие утолщения снарядов. Износ канала ствола оказался на 20% меньше, чем у орудия, не обработанного триботехническим составом.
Для определения влияния триботехнического состава на повышение живучести стволов в условиях более высоких нагрузок по давлению и температуре (стрельба на полном заряде) были проведены стрельбы из гладкоствольных противотанковых орудий МТ-12. По результатам испытаний установлено, что после производства 118 выстрелов с обработанным ТС центрующим утолщением и обтюрирующим пояском снарядов уменьшение износа канала ствола составило в среднем 30% (расход состава на каждый снаряд составляет примерно 10 г). Через год с момента проведения стрельбы, были проведены дополнительные исследования с целью определения степени сохранности защитного металлокерамического покрытия у контрольного орудия МТ-12. В ходе эксперимента выяснилось, что примерно через 100 выстрелов (220 выстрелов в сумме с первыми испытаниями) наступил процесс стабилизации износа, а при последующих 14 выстрелах диаметр канала ствола уменьшился. Начался процесс восстановления изношенной поверхности.
На основе полученных результатов можно сделать вывод, что при применении состава описанными способами после 250 выстрелов износ прекращается, проявляется безызносный эффект и наступает процесс восстановления изношенной части канала ствола, что в конечном итоге приводит к продлению ресурса живучести ствола (по расчетам) более чем на 166 выстрелов.
Последние достижения в трибологии и триботехнике обобщены в монографиях [3–13]. В них показан прогресс экспериментальных и теоретических исследований. Противоизносные покрытия различного состава прошли апробацию во многих областях техники и технологии [6, 7], что позволило обобщить результаты:
1. На абразивный износ детали влияет толщина покрытия. Если в качестве поверхностного слоя используют материал с меньшей твердостью, чем материал детали, и этот слой тоньше, чем абразивная пыль, возникающая из материала поверхностного слоя, то абразивный износ этого тонкого слоя значительно меньше, чем абразивный износ толстого слоя того же материала. В случае использования твердой поверхности также существует оптимальная в отношении долговечности толщина слоя. Согласно [3, 14, 15] для обеспечения нормального трения обработанная поверхность детали должна соответствовать правилу градиента механических свойств, которое состоит в том, что прочность на сдвиг должна расти по мере удаления от поверхности трения вглубь тела детали.
2. Оловянное покрытие [16] при условии хорошего сцепления с основной деталью подобно жидкому смазочному материалу локализует процесс металлического взаимодействия поверхностей в слое олова и устраняет заедание при значительных давлениях. Свинцовое покрытие достаточно пластично и легкоплавко, улучшает прирабатываемость, повышает сопротивляемость задиру, но сравнительно быстрее окисляется. Кадмий близок по свойствам к олову, однако менее пластичен.
3. Из фрикционных методов нанесения пленки широкое распространение получил метод латунирования [3, 17–21]. Наибольшее применение фрикционное латунирование нашло при обработке деталей цилиндропоршневой группы двигателей внутреннего сгорания (ДВС) и дизелей. По результатам испытаний было определено, что ресурс ДВС повысился на 30% при сокращении расхода горючего на 3%. Установлено повышение износостойкости пар трения в 2–4 раза. Для получения фрикционных пленок высокого качества [20–26] необходимо, чтобы шероховатость поверхности перед их нанесением составляла 0.06–0.60 мкм. При латунировании поверхности стальной детали ее покрывают слоем латуни толщиной 2–3 мкм, а при бронзировании и меднении – слоем бронзы или меди толщиной 1–2 мкм [20, 22, 25, 26].
4. Разработан метод финишной антифрикционной безабразивной обработки (ФАБО), который основан на использовании явления схватывания и переноса металла при трении. Оксидные и масляные пленки не позволяют осуществить схватывание металлов при трении, поэтому при фрикционной обработке необходимо обезжирить покрываемую поверхность и удалить с нее оксидные пленки. При сухом трении схватывание металлов сопровождается интенсивным окислением поверхностей и проявляется в виде вырывов отдельных сравнительно крупных частиц с поверхности менее прочного материала и налипания их на поверхность более прочного материала. Для обеспечения схватывания наносимого материала с основным и образования прочного сцепления между ними, обрабатываемую поверхность обезжиривают и перед обработкой смазывают глицерином.
5. Формирование защитной пленки производится фрикционным воздействием на поверхности детали специальным инструментом в присутствии рабочей среды, содержащей соли плакирующего металла и поверхностно-активные вещества. Один из составов рабочей среды: хлорид меди(I) – 2–5 мас. %, оксид кремния – до 4 мас. %, глюкоза – 1–5 мас. %, глицерин – остальное [27].
6. Наряду с этим проверялась возможность повышения износостойкости пары трения сталь–алюминиевый сплав нанесением антифрикционного медного покрытия на стальную деталь. Испытаниям подвергались образцы из стали марки 45 (ролик) и колодки из АЛЗО при работе в маслах И-20А и ХФ12-16 на воздухе и хладоне – 12 со скоростью скольжения 2 м/с и удельной нагрузкой 5 МПа. Результаты испытаний показали, что нанесение покрытия на стальной ролик позволяет повысить износостойкость пары: сталь 45-АЛЗО, и снизить интенсивность изнашивания в 2–2.5 раза. Было отмечено также снижение коэффициента трения на 20%. Покрытие позволило сократить время приработки в 2 раза.
Таким образом, по результатам рассмотренных работ, можно заключить, что для повышения живучести артиллерийских стволов имеется достаточно большой научно-технический задел в области материаловедения жаропрочных сплавов и антифрикционных противоизносных покрытий. Этот задел может быть активно использован в обеспечение модернизации системы полигонных испытаний артиллерийских стволов, для чего должна быть поставлена проблема разработки на базе этого задела соответствующих теоретических основ.
Список литературы
Зеленко В.К. Повышение живучести стволов стрелкового оружия путем применения противоизносных триботехнических составов // Ж. Известия ТулГУ. Технические науки. 2011. № 1. С. 252.
Албагачиев А.Ю., Лукашев Е.А., Сидоров М.И., Ставровский М.Е. Теория внешнего трения // Ж. Фундаментальные и прикладные проблемы техники и технологии. 2017. № 2. С. 53.
Сидоров М.И., Ставровский М.Е., Албагачиев А.Ю. Исследование влияния технологических параметров на зависимость процессов изнашивания и образования водорода // Ж. Проблемы машиностроения и надежности машин. 2017. № 4. С. 72.
Албагачиев А.Ю., Лукашев Е.А., Сидоров М.И., Ставровский М.Е. Сопоставление трибохимической кинетики внешнего трения и основных положений адгезионной и молекулярно-механической теорий трения // Ж. Вестник машиностроения. 2017. № 5. С. 47.
Албагачиев А.Ю., Сидоров М.И. Исследование микротвердости и трибологических характеристик покрытий // Ж. Вестник машиностроения. 2017. № 3. С. 63.
Вагин А.В., Албагачиев А.Ю., Сидоров М.И., Ставровский М.Е. Факторы, определяющие живучесть артиллерийской системы, и технологические методы ее повышения // Ж. Вестник машиностроения. 2016. № 12. С. 60.
Карюкин С.П., Митрохин О.В. Подход к обеспечению живучести стволов артиллерийских орудий // Ж. Военная мысль. 2012. № 1. С. 72.
Гаркунов Д.Н., Мельников Э.П., Гаврилюк В.С. Триботехника. КноРус, 2017. 408 с.
Гаркунов Д.Н. Современная трибология. Итоги и перспективы / Под ред. К.В. Фролова. М.: ЛКИ, 2008. С. 480.
Балабанов В.И., Беклемышев В.И., Махонин И.И. Трение, износ, смазка и самоорганизация в машинах. М.: Изумруд, 2004. С. 192.
Балабанов В.И., Ищенко С.А., Беклемышев В.И. Триботехнология в техническом сервисе машин. М.: Изумруд, 2005. С. 192.
Мышкин Н.К., Петроковец М.И. Трение, смазка, износ. Физические основы и технические приложения трибологии. М.: Физматлит, 2007. С. 368.
Дроздов Ю.Н., Юдин Е.Г., Белов А.И. Прикладная трибология (трение, износ, смазка. М.: Эко-Пресс, 2010. С. 604.
Лукашев Е.А. Трибохимическая кинетика внешнего трения: монография. М.: Эко-Пресс, 2016. С. 344.
Лукашев Е.А. Механохимическая кинетика накопления повреждений, разрушения и износа: монография. М.: Эко-Пресс, 2017. С. 422.
Прокопенко А.К., Голина С.И. и др. Состав для нанесения покрытий. А. С. СССР № 1203126. Опубл. Бюл. № 1.
Дополнительные материалы отсутствуют.
Инструменты
Проблемы машиностроения и надежности машин