Проблемы машиностроения и надежности машин, 2020, № 1, стр. 56-64
ВЛИЯНИЕ ТЕХНОЛОГИЧЕСКОЙ НАСЛЕДСТВЕННОСТИ НАПРЯЖЕННО-ДЕФОРМИРОВАННОГО СОСТОЯНИЯ НА ТОЧНОСТЬ НЕЖЕСТКИХ ДЕТАЛЕЙ
Г. В. Мураткин 1, В. А. Сарафанова 1, *
1 Тольяттинский государственный университет
г. Тольятти, Россия
* E-mail: sva260159@mail.ru
Поступила в редакцию 28.08.2018
Принята к публикации 25.10.2019
Аннотация
В статье показано влияние технологической наследственности напряженно-деформированного состояния на точность и размерную стабильность нежестких деталей типа валов. Определены отрицательные наследуемые факторы и закономерности наследования напряженно-деформированного состояния заготовок. Приведен усовершенствованный процесс изготовления нежестких валов с учетом технологической наследственности.
Одной из важнейших задач современного машиностроения является повышение надежности высокоскоростного оборудования [1, 2]. Надежность оборудования во многом обусловлена надежностью входящих в него изделий ответственного назначения. К таким изделиям относятся нежесткие валы роторов различных технологических установок. Их надежность бывает недостаточной из-за низкой точности изготовления и размерной стабильности во время эксплуатации. Это приводит к преждевременным отказам и снижению ресурса технологического оборудования из-за ускоренного изнашивания сопряжений. Поэтому проблема обеспечения высокой точности и размерной стабильности валов ответственного назначения является основной при их изготовлении.
Точность и размерная стабильность валов во многом зависят от их жесткости. Существует две категории жесткости деталей [3], от которых зависит уровень технологических упругих и остаточных деформаций, приводящих к погрешностям обработки. При изготовлении валов с отношением длины к диаметру равным 10–20 доминирующей в общем балансе точности изделий является погрешность формы и размеров, а при изготовлении валов с отношением длины к диаметру выше 21 – пространственная погрешность. Пространственная погрешность, проявляющаяся в искривлении оси изделия, в отличие от погрешности формы и размеров, относится к более сложным погрешностям, которые в значительной мере ограничивают применение многих технологических методов обработки. Ее величина зависит не столько от точности технологического оборудования, сколько от уровня самой технологии изготовления. Поэтому обеспечение высокой точности, обусловленной пространственной погрешностью, сопряжено с бóльшими технологическими трудностями, чем в случае, когда она обусловлена погрешностью формы и размеров.
Причиной образования пространственной погрешности являются технологические остаточные деформации изгиба, которые возникают в результате неравномерного изменения напряженного состояния заготовки. В процессе изготовления остаточные деформации возникают при упругой разгрузке под воздействием изгибающего момента, обусловленного несимметричным распределением по сечению заготовки начальных напряжений [4].
Процесс образования технологических остаточных деформаций в общем случае состоит из двух этапов: 1) образование деформаций после обработки и раскрепления детали, либо в процессе обработки, если закрепление заготовки допускает ее деформацию; 2) образование и развитие деформаций, нарушающих стабильность размеров изделия, во время хранения, транспортировки и эксплуатации. Величина остаточных деформаций, возникающих при обработке деталей на порядок больше величины деформаций, образующихся в процессе эксплуатации. Но достаточно часто эксплуатационные остаточные деформации изгиба превышают допустимые значения, что неизбежно приводит к нарушению динамических характеристик роторов, вращающихся с высокой скоростью, и создает опасность возникновения аварийных ситуаций. Поэтому допустимое отклонение от прямолинейности оси вала ответственного назначения не должно превышать 0.01 мм/м. Такие требования относят нежесткие валы в разряд прецизионных изделий.
Чтобы снизить технологические остаточные деформации, переходящие с заготовок на изделие и возникающие непосредственно во время обработки деталей, используются методы снижения технологических остаточных деформаций. Эти методы можно разделить на методы предупреждения (стабилизирующая обработка) и методы устранения (правка) технологических остаточных деформаций. Чередование операций механической обработки и методов снижения технологических остаточных деформаций позволяет добиться минимальной пространственной погрешности изделия, присущей данной технологии. Однако такая технология, основанная на пассивном ослаблении причин образования остаточных деформаций, реализует экстенсивный путь достижения точности ответственных изделий. Ее вряд ли можно признать экономически эффективной, поскольку требуемая точность достигается за счет снижения производительности обработки и увеличения себестоимости изделия. К тому же изготовленные по такой технологии валы обладают низкой надежностью, так как во время эксплуатации достаточно быстро теряют свою первоначальную точность в результате релаксационных процессов.
Технологический процесс изготовления нежестких валов из горячекатаного прутка можно представить совокупностью их переходов из одного напряженно-деформированного состояния в другое. При этом получить высокоточные изделия можно только в случае, когда эти переходы сопровождаются планомерным снижением технологических остаточных деформаций до требуемых значений. Типовые технологические процессы, включающие многопроходное точение, правку деталей изгибом, стабилизирующий отпуск, чистовое шлифование и вибрационную стабилизацию размеров, не позволяют в достаточной мере устранить исходную остаточную деформацию изгиба заготовки, достигающую 3 мм/м. В результате более 50% обработанных в партии деталей может уходить в брак. Для выполнения заданной программы выпуска деталей предприятию приходиться запускать в производство заведомо большую партию заготовок, увеличенную из расчета потерь на брак. Такое положение отражает неудовлетворительное технологическое состояние производства. Причиной этого являются устаревшие подходы к проектированию технологий изготовления нежестких валов, недостаточно учитывающие механизмы образования технологических остаточных деформаций и закономерности наследования напряженно-деформированного состояния изделий. Поэтому необходимо разработать новые, более совершенные процессы технологической обработки, которые позволят при высоком качестве поверхностного слоя обеспечить высокую точность изделий, не имеющих вредных последствий от проявления технологической наследственности в процессе эксплуатации.
Считается [5], что остаточная деформация изгиба является положительной величиной и, следовательно, нельзя повысить точность изделия за счет корректировки уровня настройки процесса технологической обработки. Точность изделия определяется величиной остаточной деформации изгиба, но при этом ось заготовки в процессе изготовления может изгибаться в разные стороны относительно номинального (прямолинейного) положения. Поэтому пространственную погрешность представим векторной величиной, указывающей направление изгиба оси детали. Это даст возможность выявить закономерность ее изменения в процессе изготовления и позволит управлять остаточной деформацией изгиба.
Благодаря векторному представлению пространственной погрешности экспериментально установлено [6], что точность механической обработки после каждого перехода зависит от величины исходной остаточной деформации заготовки. При этом на разных стадиях токарной обработки происходит изменение направления деформации изгиба заготовки относительно прямолинейного положения оси с неизменным уменьшением ее значения по абсолютной величине. Выявленная закономерность изменения остаточной деформации изгиба свидетельствует о том, что в процессе изготовления действует закон технологического наследования напряженно-деформированного состояния деталей, который носит затухающий характер.
Технологическая наследственность напряженно-деформированного состояния деталей проявляется в пооперационном взаимодействии остаточных деформаций и напряжений.
При установке и закреплении в кулачках подвижного люнета и центрах токарного станка заготовки нежесткого вала, которая имеет остаточную деформацию изгиба $f_{{{\text{исх}}}}^{{{\text{max}}}}$, в ее теле возникают дополнительные напряжения σу в результате совмещения изогнутой оси заготовки с осью центров (рис. 1).
Рис. 1.
Принципиальная схема образования остаточных деформаций и напряжений при токарной обработке заготовки длинномерного вала: 1 – эпюра остаточных напряжений в заготовке; 2 – эпюра напряжений σу от упругого изгиба заготовки; 3 – эпюра начальных напряжений σун от упругого изгиба заготовки, возникающих после токарной обработки; 4 – эпюры начальных напряжений σн, возникающих от процесса резания; 5 – эпюра суммарных начальных напряжений σ$_{{\text{н}}}^{\Sigma }$; 6, 7 – эпюры реактивных напряжений, возникающих в результате продольной σр и изгибной σм деформаций в момент разгрузки; 8 – эпюра суммарных σр + м реактивных напряжений; 9 – эпюра остаточных напряжений в изделии σо; tвп – припуск, снимаемый с выпуклой стороны заготовки.
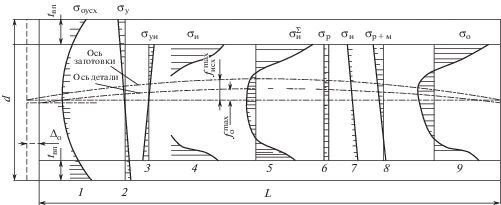
Эти напряжения в соответствии с принципом алгебраической суперпозиции накладываются на имеющиеся в заготовке остаточные напряжения σоисх. При точении заготовки, находящейся в упругодеформированном состоянии, эти результирующие напряжения складываются из условия пластичности с технологическими начальными напряжениями σн, вносимыми в поверхностный слой самим процессом резания [7]. В результате в детали формируется несимметричная относительно нейтральной оси эпюра неуравновешенных начальных напряжений σ$_{{\text{н}}}^{\Sigma }$, вызывающих изгибающий момент, который при разгрузке деформирует вал, изменяя величину и вектор исходной остаточной деформации изгиба. Возникающие при этом реактивные напряжения σр и σм уравновешивают начальные напряжения по всему сечению изделия, преобразуя их в остаточные напряжения σо. После деформации вал принимает новое деформированное состояние с параметрами $f_{{\text{о}}}^{{{\text{max}}}}$ и Δо, отвечающими равновесной эпюре остаточных напряжений. При этом равновесная эпюра остаточных напряжений может иметь существенную асимметрию относительно нейтральной оси изделия. Такое достаточно сложное взаимодействие параметров напряженно-деформированного состояния детали с одновременным действием многих переменных и постоянных факторов, обусловленных материалом заготовки и условиями обработки, делает расчетное прогнозирование пространственной погрешности изделия сложным. Любая остаточная деформация изгиба, возникающая после обработки заготовки с прямолинейной осью, приводит к несимметричному распределению относительно нейтральной оси остаточных напряжений. Причем чем больше деформация изгиба, тем больше асимметрия распределения остаточных напряжений. Более наглядно это проявляется, когда заготовка свободна от остаточных напряжений. Поэтому будем рассматривать характер распределения остаточных напряжений в детали в качестве интегрального информационного показателя истории ее деформирования в процессе изготовления [8].
Остаточная асимметрия распределения напряжений в окончательно изготовленном изделии с течением времени практически всегда приводит к его изгибу и к потере точности. Как и в процессе изготовления изделия, образование и развитие остаточных деформаций во время эксплуатации обусловлено проявлением технологической наследственности напряженно-деформированного состояния детали. После изготовления изделия полученная им асимметрия распределения остаточных напряжений во время эксплуатации порождает неравномерную релаксацию напряжений, так как более высокие остаточные напряжения в поверхностном слое детали снижаются с большей скоростью, чем напряжения с более низким уровнем, а остаточные напряжения растяжения релаксируют более интенсивно, чем напряжения сжатия [9]. Неравномерная релаксация напряжений, приводит к развитию остаточной деформации изгиба. При этом изделие всегда изгибается в направлении к той остаточной деформации, которая была у заготовки перед финишной обработкой. Этот процесс, называемый обратным упругим последействием детали, продолжается в течение длительного времени и приводит к выравниванию остаточных напряжений в объеме изделия и снижению асимметрии остаточных напряжений [10]. При этом весь потенциал развития остаточных деформаций изгиба во время эксплуатации оборудования в штатном режиме, когда напряжения от рабочих температурно-силовых воздействий не оказывают влияния на характер распределения остаточных напряжений в детали, определяется степенью асимметрии распределения напряжений относительно нейтральной оси изделия и не зависит от их уровня. Интенсивность этого процесса обусловлена как внешними (температура в рабочей зоне, величина и характер действующих эксплуатационных нагрузок и др.), так и внутренними (химический, структурно-фазовый состав, физико-механические свойства, уровень напряжений, полученный при изготовлении изделий или сборке узлов и др.) факторами.
Можно сделать вывод, что не сами остаточные напряжения, а их неравномерное изменение является отрицательным фактором технологической наследственности, определяющим точность обработки. Правомерность такого вывода подтверждается тем, что равномерное изменение напряженного состояния заготовки вызывает только ее удлинение-укорочение, но не приводит к образованию пространственной погрешности и, следовательно, не оказывает влияние на точность обработки. Также к отрицательным факторам технологической наследственности следует отнести и саму остаточную деформацию изгиба заготовки, так как при обработке она в той или иной мере приводит к неравномерному изменению ее напряженного состояния. Поэтому следует ограничивать остаточные деформации изгиба заготовок, проводя их предварительную классификацию.
Неравномерное изменение напряженного состояния (или асимметрия распределения напряжений в сечениях изделия), остаточная деформация изгиба заготовки, упругие деформации, возникающие при обработке или сборке, являются основными наследственно связанными параметрами напряженно-деформированного состояния нежесткого вала, которые определяют точность обработки и размерную стабильность изделия.
Многолетний опыт показывает, что невозможно обеспечить высокую размерную стабильность изделий в случае устранения больших пространственных погрешностей на завершающем этапе изготовления. Требуется, применяя все прогрессивные технологические способы, обеспечить пооперационное снижение технологических остаточных деформаций и асимметрии распределения остаточных напряжений до определенного уровня. При этом следует учитывать проявление технологической наследственности напряженно-деформированного состояния по всему циклу изготовления изделий. Также требуется использовать все известные специальные технологические приемы, которые позволяют снижать технологические остаточные деформации изгиба. Такими приемами являются: преднамеренное искажение формы упругой линии заготовки, приводящее к созданию предварительных упругих напряжений, которые дают возможность снизить ожидаемые деформации; восстановление технологических баз или применение подпружиненного заднего центра, позволяющие исключить возникновение при обработке дополнительных напряжений в заготовке; использование при термической обработке жестких фиксирующих приспособлений, которые дают возможность свести к минимуму деформацию детали.
Точность и размерная стабильность изделий зависят от того насколько отрицательные факторы технологической наследственности будут подавлены или нейтрализованы в процессе изготовления. Сильное действие отрицательных факторов прекращается после проведения операций, выполняющих роль технологических “барьеров” [11]. Однако операции стабилизирующей обработки и правки упругопластическим изгибом, традиционно причисляемые к технологическим “барьерам”, по сути, таковыми не являются. В большинстве случаев напряженное состояние заготовки преодолевает технологический “барьер” в виде термической стабилизирующей обработки за счет увеличения технологической остаточной деформации изгиба, а ее устранение правкой упругопластическим изгибом приводит к значительной асимметрии распределения остаточных напряжений в сечении детали. При обработке этими методами улучшение одного параметра напряженно-деформированного состояния происходит за счет ухудшения другого, что значительно снижает их технологические возможности. Кроме того, стабилизирующая обработка и правка могут вызвать нежелательное изменение физико-механических свойств, что во многих случаях недопустимо для ответственных деталей, требующих повышенной надежности.
В последние годы разработаны новые методы токарной, электрохимической, термической обработки и поверхностного пластического деформирования (ППД), которые являются действительными технологическими “барьерами” на пути отрицательных факторов технологической наследственности напряженно-деформированного состояния заготовок, позволяющими повысить точность деталей путем одновременного снижения технологических остаточных деформаций и асимметрии распределения остаточных напряжений. Эти методы являются комбинированными методами, включающими в себя разнородные, но технологически совместимые процессы. Они разработаны благодаря современным знаниям в области технологических остаточных деформаций и напряжений. В них успешно реализована научная идея о превращении отрицательного фактора технологической наследственности, каким является неравномерное изменение напряженного состояния или предварительная упругая деформация заготовки, в положительный фактор. В основе методов лежит активное управление напряженно-деформированным состоянием заготовки в процессе обработки с целью создания изгибающего момента от сформированных напряжений, противоположного знака по отношению к имеющейся остаточной деформации изгиба. Изгибающий момент после обработки и раскрепления детали устраняет остаточную деформацию и формирует остаточные напряжения с распределением близким к осевой симметрии. Такие технологические “барьеры” достаточно легко встраиваются в существующие технологические процессы изготовления и дают возможность в определенной мере управлять явлением технологической наследственности. Их место в процессе изготовления обусловлено необходимостью значительного улучшения напряженно-деформированного состояния деталей после операций с низкими показателями точности, которые являются “слабыми звеньями” в технологической цепочке.
Для того чтобы снизить наследственный перенос остаточных деформаций изгиба с заготовок на изделия в начале процесса изготовления операцию классической закалки целесообразно заменить первым технологическим “барьером” – термосиловой правкой (правка заготовок, совмещенная с закалкой материала). Она позволяет в рамках одной технологической операции значительно снизить остаточные деформации изгиба заготовок и обеспечить необходимую структуру материала. Снижение технологических остаточных деформаций изгиба при термосиловой правке с предварительным обратным изгибом заготовки [12] осуществляется путем целенаправленного изменения ее напряженно-деформированного состояния в результате одновременного силового и термического воздействий на материал, приводящих к кинетическим изменениям свойств (явление кинетической пластичности) при закалке. Термосиловая правка позволяет в шесть раз снизить уровень остаточных деформаций изгиба заготовок, выровнять остаточные напряжения в детали и сформировать заданные физико-механические свойства материала, что способствует существенному уменьшению объема последующих термических и механических обработок изделий.
Особо важная роль при проектировании технологических процессов изготовления изделий ответственного назначения отводится финишным операциям, которые в значительной мере определяют качество поверхностного слоя, точность и размерную стабильность изделий. В существующих технологических процессах окончательная механическая обработка валов производится шлифованием. Но у заготовки, которая имеет остаточную деформацию изгиба, процесс шлифования сопровождается неравномерными термическими и силовыми воздействиями абразивного круга на обрабатываемую поверхность. Это приводит к снижению качества поверхностного слоя, формированию нежелательных остаточных напряжений растяжения и неравномерному изменению напряженного состояния заготовки. Последующая стабилизирующая вибрационная обработка, направленная на ускоренную реализацию активной фазы релаксационного процесса материала детали в производственных условиях, также приводит к некоторому неравномерному изменению напряженного состояния изделия. Возникающие в результате этого технологические остаточные деформации изгиба в подавляющем большинстве случаев превышают допустимое отклонение от прямолинейности оси и требуют проведения прецизионной правки деталей. Кроме того, само по себе максимальное снижение остаточных напряжений стабилизирующей обработкой негативно сказывается на несущей способности ответственных валов, поскольку не учитывает, какие (благоприятные или неблагоприятные с точки зрения эксплуатационных свойств) снимаются остаточные напряжения. Благоприятными для большинства эксплуатационных свойств изделий являются остаточные напряжения сжатия и технологическое увеличение их уровня в поверхностном слое способствует значительному повышению усталостной прочности и в целом несущей способности изделий, работающих в условиях больших скоростей и знакопеременных нагрузок [7, 11, 13, 14].
Для обеспечения заданных параметров качества поверхностного слоя, точности и высокой размерной стабильности изделий на завершающем этапе изготовления следует ввести в технологический процесс второй “барьер” – правку поверхностным пластическим деформированием (ППД). Ее применение в качестве финишной механической обработки, совмещающей процесс правки детали с отделочно-упрочняющей обработкой поверхности, с успехом позволяет заменить в типовом технологическом процессе операции чистового шлифования и вибрационной стабилизирующей обработки, ограничив механическую обработку операцией чистового (или тонкого) точения. Правка ППД, являясь высокотехнологичным процессом, дает возможность с высокой точностью исправить малые по величине (0.01–0.3 мм/м) остаточные деформации изгиба, которые образуются при чистовом точении, и сформировать при этом остаточные напряжения с распределением близким к осевой симметрии, способствующим стабилизации размеров изделий [15]. При этом поверхностное упрочнение при проведении правки ППД позволяет существенным образом повысить релаксационную стойкость материала поверхностного слоя в результате формирования тонкой (блочной) структуры [16]. Обкатывание упрочняющим шаром и сглаживающими роликами при правке ППД создает на рабочих поверхностях плавный, обтекаемый микрорельеф с высотой неровностей Rа = 0.1–0.22 мкм, повышает на 25–30% поверхностную твердость, завальцовывает поверхностные дефекты (трещины, риски и др.) и формирует практически новое напряженное состояние изделий с остаточными напряжениями сжатия в поверхностном слое в пределах 550–730 МПа. Повышенная релаксационная стойкость материала поверхностного слоя, приобретенная в результате пластического деформирования, является устойчивым наследственным признаком при действии различных температурно-силовых факторов, что положительным образом влияет на размерную стабильность изделия.
Для экспериментального подтверждения эффективности правки ППД в повышении размерной стабильности изделий по сравнению с другими методами правки, применяемыми для снижения остаточных деформаций изгиба, в том числе на завершающем этапе изготовления были проведены экспериментальные исследования [17] трех партий образцов из стали 45. Для экспериментов выбирались валики, имевшие перед правкой одинаковую форму изогнутой оси и остаточные деформации изгиба равные по величине 0.3 мм, которые были получены при одинаковых условиях токарной обработки. Установлено, что размерная стабильность валиков после правки ППД практически в семь раз выше, чем после правки упругопластическим изгибом и 2.6 раза выше, чем после правки растяжением. Полученные результаты экспериментов подтвердили безусловную необходимость проведения правки ППД на заключительном этапе изготовления длинномерных валов ответственного назначения.
Методы термосиловой правки и правки ППД не требуют применения сложного технологического оборудования и позволяют перейти от экстенсивного к интенсивному пути достижения точности изделий. Они дают возможность существенным образом усовершенствовать технологический процесс изготовления длинномерных валов роторов насосно-компрессорного оборудования и повысить его эффективность в обеспечении высокой точности и размерной стабильности. Новый технологический процесс состоит из следующих основных операций: отрезания заготовки из проката, контроля химического состава металла и остаточных деформаций изгиба заготовок, термосиловой правки (правка заготовок, совмещенная с закалкой металла), стабилизирующего отпуска, контроля физико-механических свойств, структуры металла и остаточных деформаций изгиба заготовок, создания базовых поверхностей, чернового обтачивания в один проход, получистового обтачивания в один проход, центродоводочной операции, чистового обтачивания в один проход, фрезерования шпоночных пазов и лысок, правки ППД и контроля качества.
Достоинствами усовершенствованного технологического процесса изготовления длинномерных нежестких валов являются сокращенный производственный цикл, уменьшение брака и более низкие издержки в расчете на единицу продукции при надлежащем ее качестве. Поэтому он может быть рекомендован к широкому практическому использованию в производстве длинномерных валов ответственного назначения.
Список литературы
Veprev A.A., Pashkov A.E. Complex technology of the aircraft panels forming // J. UAMFO. January–June. 2012. V. 4. № 1. P. 39.
Citti P., Giorgetti A., Millefanti U. Current challenges in material choice for high-performance engine crankshaft // International Conference on Stress Analysis, AIAS, Pisa, Italy. 2017. P. 486.
Мураткин Г.В., Котова И.В. Критерии изгибной жесткости стержневых деталей // Ж. Ремонт, восстановление, модернизация. 2006. № 2. С. 42.
Овсеенко А.Н. Технологические остаточные деформации маложестких деталей и методы их снижения // Ж. Вестник машиностроения. 1991. № 2. С. 58.
Колкер Я.Д. Математический анализ точности механической обработки деталей. Киев: Техника, 1976. С. 200.
Мураткин Г.В. Образование технологических остаточных деформаций и напряжений при изготовлении нежестких валов // Ж. Автоматизация и современные технологии. 2003. № 8. С. 16.
Подзей А.В. Технологические остаточные напряжения. М.: Машиностроение, 1978. С. 216.
Суслов А.Г., Дальский А.М. Научные основы технологии машиностроения. М.: Машиностроение, 2002. С. 684.
Коцюбинский О.Ю. Стабилизация размеров чугунных отливок. М.: Машиностроение, 1974. С. 296
Термическая обработка в машиностроении: Справочник / Под ред. Ю.М. Лахтина, А.Г. Рахштадта. М.: Машиностроение, 1980. С. 783.
Ящерицын П.И., Рыжов Э.В., Аверченков В.И. Технологическая наследственность в машиностроении. Минск: Наука и техника, 1977. С. 256.
Мураткин Г.В. Правка нежестких деталей при термической обработке // Ж. Ремонт, восстановление, модернизация. 2004. № 8. С. 21.
Asi O., Can A.C. The comparison of the residual stresses between carburized and only quenched steels // J. Pamukkale University Journal of Engineering Sciences. 2001. № 7. P. 182.
Mahmoudi A.H., Ghasemi A., Farrahi G.H., Sherafatnia K. A comprehensive experimental and numerical study on redistribution of residual stresses by shot peening // J. Materials & Design. 2016. № 90. P. 478.
Зайдес С.А., Мураткин Г.В. Упрочнение, восстановление, правка валов: Учебн. пособие. Иркутск: ИрГТУ, 2005. С. 336.
Мураткин Г.В., Сарафанова В.А., Суворов М.О. Повышение релаксационной стойкости материала поверхностным пластическим деформированием // Ж. Технология металлов. 2017. № 7. С. 19.
Мураткин Г.В. Исследование влияния методов правки на размерную стабильность длинномерных валов ответственного назначения // Ж. Металлообработка. 2014. № 4 (82). С. 37.
Дополнительные материалы отсутствуют.
Инструменты
Проблемы машиностроения и надежности машин