Проблемы машиностроения и надежности машин, 2020, № 4, стр. 90-96
ПРОГНОЗИРОВАНИЕ ТОЧНОСТНЫХ ПАРАМЕТРОВ АВТОМАТИЗИРОВАННОГО ТЕХНОЛОГИЧЕСКОГО ПРОЦЕССА ГИБКИ ТРУБ ГТД СЛОЖНОЙ ПРОСТРАНСТВЕННОЙ ФОРМЫ
И. А. Бурлаков 1, *, Г. А. Мангасарян 1, Ю. А. Гладков 1, А. А. Кукуюк 1, Д. Э. Гордин 1
1 Производственный комплекс “Салют” АО “ОДК”
Москва, Россия
* E-mail: burlakov-ia@uecrus.com
Поступила в редакцию 04.09.2019
Принята к публикации 27.03.2020
Аннотация
В статье приведены результаты экспериментального и расчетного методов процесса гибки труб сложной пространственной формы на трубогибочном автомате с применением программы QForm VX, основанной на методе конечных элементов. Показана возможность прогнозирования точностных параметров полуфабриката и возможных дефектов методом моделирования процесса.
Трубопроводы сложной пространственной формы представляют неотъемлемую часть газотурбинных двигателей. Результатом их сложной трассировки является необходимость изготовления труб сложной пространственной формы с большим количеством изгибов разных радиусов и углов, а также с различными, часто очень малыми, расстояниями между изгибами. Детали данной группы подвергаются значительным гидравлическим нагрузкам, вследствие чего к ним предъявляются высокие требования по механическим характеристикам [1]. С целью повышения производительности и снижения трудоемкости, а также, повышения качества деталей применяют трубогибочные автоматы, где весьма важно правильно отработать технологический процесс во избежание дефектов в виде складок (рис. 1а) и вмятин (рис. 1б). Применение моделирования при разработке технологических процессов, в частности, моделирование по методу конечных элементов в программе QForm VX [2], позволяет оптимизировать конструкцию инструмента, существенно сократить объем наладочных работ и время запуска в производство.
Основным способом холодной гибки труб является гибка методом наматывания. Труба под действием крутящего момента наматывается на гибочный ролик. По данному методу осуществляют два типа гибки – бездорновый и дорновый.
Бездорновый вид гибки предназначен для холодной гибки без наполнителя (без дорна) стальных, медных, латунных и т. п. труб с радиусом гиба r ≥ 3d, где d – наружный диаметр трубы.
Дорновый вид гибки предназначен для холодной гибки с дорном стальных труб с радиусом гиба r ≥ 1.5d и отношением толщины стенки s трубы к диаметру d (s/d ≥ 0.03). Принцип действия заключается в следующем: трубу устанавливают в ручей гибочного ролика и закрепляют к прямолинейной его части при помощи прижима, которым труба во врéмя гибки прижимается к гибочному ролику. Приводимый во вращательное движение гибочный ролик увлекает за собой трубу, которая, находясь в ручье между гибочным роликом и прижимом, стаскивается с дорна и изгибается на необходимые угол и радиус. Данный метод применяется для гибки особо точных гнутых труб с тонкой стенкой и малым радиусом гиба.
Типовая оснастка (риc. 2) для гибки полых труб 5 включает в себя задний прижим 1, передний прижим 2, ролик 3, складкодержатель 4 и дорн.
С целью минимизации образования овальности трубы применяют калибрующие дорны как в виде стержня, так и гибкие шариковые. Последние были использованы в настоящем исследовании. Экспериментальному исследованию процесса гибки труб посвящено большое количество работ [3–10]. Однако практически отсутствуют публикации, направленные на анализ данного процесса с применением моделирования методом конечных элементов, однако в некоторой степени могут быть использованы результаты моделирования аналогичных деталей [11, 12]. Настоящая работа направлена на частичное восполнение данного пробела.
Цель работы. Повышение эффективности процесса автоматизированной гибки труб сложной пространственной формы путем применения метода конечных элементов.
Задачи:
1. Выполнить анализ изготавливаемых труб и выбрать типовой представитель.
2. Разработать твердотельные модели для выбранной трубной заготовки и инструмента.
3. Осуществить моделирование процесса гибки труб сложной пространственной формы с целью:
– определить влияние ширины переднего режима на образование дефектов,
– определить тип дорнов, исключающий образование гофр,
4. Выполнить экспериментальные работы по изготовлению выбранных труб.
5. Выполнить анализ полученных данных и подготовить предложения.
Материал и методы исследования. Материалом исследования являлись бесшовные трубы диаметром 20 мм и толщиной стенки 1.0 мм из нержавеющей стали марки 12Х18Н10Т, химический состав которой (% (мас.): Fe – осн., Cr – 18, Ni – 10, Ti – 0.7), поставляемые по ГОСТ 9941.
Экспериментальные работы по гибке труб проводили на трубогибочном автомате (рис. 3).
Контроль геометрических параметров гнутых труб осуществляли с помощью, автоматизированной оптической измерительной системы “TubeInspect” фирмы “AICON”. Точность измерения составляла ±0.1 мм.
Моделирование. Процесс гибки труб моделировали с применением метода конечных элементов (МКЭ) с помощью пакета QForm VX версии 8.2.4 со следующими исходными данными: обрабатываемый материал – нержавеющая сталь 12Х18Н10Т; материал инструмента – инструментальная 5ХНМ; материал выглаживателя – бронза БрАЖ10-10-4; объем заготовки неизменный; напряженное состояние трехмерное (3D расчет); температура формообразования – 20°С; фактор трения – 0.3, трение по закону Леванова; тепловые процессы не учитываются; формообразование осуществляется на трубогибочном автомате со скоростью 1 об/мин.
В виду того, что толщина обрабатываемых труб составляет 1.0 мм, сетка конечных элементов была принудительно измельчена.
Моделирование с учетом трения в условиях малых давлений на контакте с заготовкой. Обычно для описания граничных условий по трению в условиях малых нормальных к поверхности инструмента напряжений σn принято использовать закон трения Кулона–Амонтона (далее закон трения Кулона)
где τk – касательные напряжения в точке контакта, μ – коэффициент трения Кулона.Такой закон хорошо описывает процессы, в которых на контактирующих поверхностях интенсивность напряжений не достаточна, чтобы началась пластическая деформация. Однако для точного моделирования в зонах гибки и формовки, где ${{{\sigma }}_{n}}$ превышает $k = \frac{{{{{\sigma }}_{s}}}}{{\sqrt 3 }}$, закон трения дает завышенные значения ${{{\tau }}_{k}}$. Для обеспечения моделирования процессов, где на контакте одновременно присутствуют условия для трения по закону Кулона (нет пластической деформации) и трения по закону Зибеля–Треска (в зоне контакта заготовка претерпевает пластическую деформацию) рационально использовать закон трения, совмещающий для разных ${{{\sigma }}_{n}}$ законы трения Кулона и Зибеля–Треска (далее – закон Зибеля).
Как показано в работе [13] удачным решением при моделировании подобных процессов является использование закона трения Леванова, описываемого зависимостью: τk = $mk\left( {1 - \exp \left( { - b\frac{{{{{\sigma }}_{n}}}}{{{{{\sigma }}_{s}}}}} \right)} \right)$, где m – фактор трения Зибеля, σs – сопротивление деформации металла заготовки, b – коэффициент Леванова (фактически задает интерполяцию двух законов Кулона и Леванова, рекомендуемое значение – 1.25). Закон трения Леванова, фактически, интерполирует (рис. 4) законы трения Кулона и Зибеля (τk = mk).
Рис. 4.
Закон трения Леванова интерполирует законы трения Кулона и Зибеля: приведены графики для условий μ = 0.05, m = 0.1, b = 1.25, σs = 500 МПа.
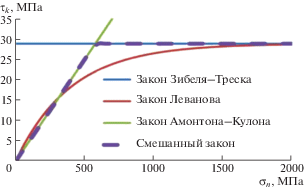
Результаты и обсуждение. В качестве типового представителя была выбрана труба наружным диаметром d = 20 мм и толщиной стенки s = 1.0 мм с тремя изгибами радиусом 40 мм. Твердотельные модели трубной заготовки и реального формообразующего инструмента показаны на рис. 2.
Влияние ширины переднего прижима. Для оценки роли ширины в формировании вмятины было осуществлено моделирование с шириной прижима (рис. 3) w = 20; 25; 30 и 50 мм, что составляет относительную ширину w/d = 1.0; 1.25; 1.50 и 2.50. Результаты показаны на рис. 4. Как видно из представленных данных относительная ширина прижима 1.0 и 1.25 приводит к образованию дефектов в виде вмятин. При относительной ширине прижима 1.50 и более (рис. 5в, г) такие дефекты отсутствуют, что было подтверждено экспериментально.
Рис. 5.
Влияние ширины переднего прижима на образование дефектов: (а) – w/d = 1.0; (б) – w/d = 1.25; (в) – w/d = 1.50; (г) – w/d = 2.50.
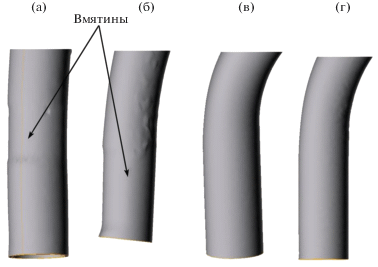
Серьезную проблему при гибке труб представляют дефекты в виде гофр (рис. 1а), особенно при малых радиусах гиба. Для исключения таких дефектов часто применяют наполнитель, что крайне нежелательно при реализации процесса гибки на автоматах. В таких случаях переменяют дорны (рис. 3б).
Моделирование процесса с дорном (рис. 6) представляет довольно сложную задачу, т.к. в случае применения трехсекционного дорна в расчетной схеме предусматривается восемь инструментов, три заделки и бокс скорости осевого перемещения для заготовки.
Рис. 6.
Моделирование процесса гибки трубной заготовки с трехсекционным дорном: (а) – начало процесса; (б) – гибка на угол 5 градусов; (в) – гибка на угол 20 градусов; радиус гибки – 40 мм.
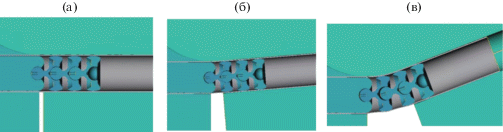
Полученная модель позволяет определять режимы технологического процесса, заранее проверить правильность геометрических параметров инструмента и настроечные параметры (величину зазора между заготовкой и прижимами, а также между дорном и внутренним диаметром трубы), скорость проталкивания заготовки, скорость перемещения заднего прижима и т.д.) и в результате получать заготовку с требуемыми параметрами (рис. 7).
Как показала эксплуатация оборудования, минимальную стойкость имеет выглаживатель, изготавливаемый, с целью снижения трения и снижения вероятности образования царапин на трубной заготовке, из бронзы БрАЖ10-10-4. Моделирование инструмента позволило установить, что в наиболее высокие контактные напряжения возникают на тонкой входной кромке выглаживателя (рис. 8), где они превышают 1800 МПа. Повышение стойкости выглаживателя требует обязательного применения смазки и тщательной его доводки как по геометрическим параметрам, так и по минимальной шероховатости поверхности.
Рис. 8.
Область высоких (свыше 1800 МПа) напряжений, возникающих на выглаживателе в процессе гибки труб.

Выводы. 1. Выполненное компьютерное моделирование процесса гибки труб сложной пространственной формы в программе QForm, в том числе с дорном, позволило оценить напряженно-деформированное состояние не только в заготовке, но и в инструменте. 2. При моделировании для заданий условий трения процессов гибки рационально использовать закон трения Леванова, обеспечивающий приемлемый расчет контактных касательных напряжений как в зонах без деформации, так и в зонах, где наблюдается пластическая деформация. 3. Было установлено, что во избежание дефектов в виде вмятин от переднего прижима, его ширина должна быть не менее 1.5 диаметров трубы. 4. Величина контактных напряжений на острой кромке выглаживателя превышают 1800 МПа, что требует тщательной доводки инструмента как по геометрическим параметрам, так и по минимально возможной шероховатости ее поверхности.
Список литературы
Каплунов С.М., Вальес Н.Г., Горелов Е.В. Определение собственных частот для произвольных многокомпонентных трубных систем в жидкости // Проблемы машиностроения и надежности машин. 2007. № 5. С. 22.
Сайт разработчика ПО QForm. М.: ООО “КванторФорм”, 2019; https://www.qform3d.ru (дата обращения: 13.08.2019).
Корнилов В.А. Совершенствование технологии многоколенной пространственной гибки труб проталкиванием на роликовой машине. Диссертация на соискание ученой степени кандидата технических наук. М. 2013. 105 с.
Глазков А.В. Технология холодной гибки труб методом продольного раскатывания, Научно-технические ведомости СПбГПУ. Наука и образование. 2012. С. 133.
Технология и оборудование для гибки труб с раскатыванием / Под ред. С.Г. Лакирев, A.B. Козлов, Ю.Г. Миков, A.B. Бобылев // Тематический сб. науч. тр. ЗФ ЧГТУ. Челябинск: ЧГТУ. 1996.
Салирьянц Н.М. A.с. 582873. Способ гибки труб / Н.М. Салирьянц, И.В. Губин, В.Т. Бондаренко // Открытия. Изобретения. М.: ВНИТИ, 1977. № 45.
Особенности гибки мелкоразмерных труб из нержавеющих сталей / Под. ред. A.B. Козлов, Ю.Г. Миков, С.Г. Чиненов, A.B. Бобылев // XVI Российская школа по проблемам проектирования неоднородных конструкций: сборник трудов. Миасс: МНУЦ, 1997.
Белкин Н.М. Гибка труб методом пластического шарнира // Строительство трубопроводов. 1989. № 8. С. 37.
Забельян Д.М., Колотов Ю.В., Мангасарян Г.А., Гладков Ю.А. Изготовление изделий из тонкостенных трубчатых заготовок методами гидроформовки // Машиностроение и инженерное образование, 2017. № 4 (53). С. 20.
Sukhorukov R.Yu., Sidorov A.A., Alimov A.I., Nagimov M.I., Mukhtarov Sh.Kh, Utyashev F.Z. Physical and Numerical Modeling of the Process of Rolling Off of a Tapered Shaft of Aviation Purpose // Journal of Machinery Manufacture and Reliability. 2016. V. 45. № 6. P. 538.
Раков Д.Л., Сухоруков Р.Ю., Гаврилина Л.В. Анализ и оценка технологий и оборудования для изготовления заготовок длинномерных полых валов газотурбинных двигателей из жаропрочных никелевых и титановых сплавов на базе морфологического подхода // Проблемы машиностроения и оптимизации. 2015. № 4. С. 136.
Burlakov I.A., Valitov V.A., Ganeev A.A., Zabel’yan D.M., Morozov S.V., Sukhorukov R.Yu., Utyashev F.Z. Modeling the Structure Formation during Hot Deforming the Billets of the Parts of Gas-Turbine Engines Made of Heat-Resistant Nickel Alloy // Journal of Machinery Manufacture and Reliability. 2016. N. 5. P. 95.
Yury Gladkov, Ilya Peshekhodov, Milan Vucetic, Anas Bouguecha, Bernd-Arno Behrens. Implementation of the Bai & Wierzbicki fracture criterion in QForm and its application for cold metal forming and deep drawing technology / Proceedings of ICNFT 2015, August, 6–9, Glasgow, UK / MATEC Web of Conferences 21 12009. 2015. P.1. https://doi.org/: https://doi.org/10.1051/matecconf/20152112009
Дополнительные материалы отсутствуют.
Инструменты
Проблемы машиностроения и надежности машин