Проблемы машиностроения и надежности машин, 2021, № 1, стр. 43-50
Оценка возможности замены чугуна СЧ24 детали “диск тормозной” автомобиля на дисперсно-упрочненный композиционный материал на основе алюминия, полученный внутренним окислением
Е. А. Чернышов 1, А. Д. Романов 1, И. Д. Романов 1, Л. А. Кривина 2, И. Н. Царева 2, *
1 Нижегородский государственный технический университет им. Р.Е. Алексеева
Н. Новгород, Россия
2 Институт проблем машиностроения РАН – филиал ФИЦ Института прикладной физики РАН
Н. Новгород, Россия
* E-mail: npktribonika@yandex.ru
Поступила в редакцию 16.06.2020
Принята к публикации 22.10.2020
Аннотация
В статье освещены результаты разработки фрикционного материала – дисперсно-упрочненного композиционного материала на основе алюминия, полученного методом внутреннего окисления. Были использованы различные виды триботехнических испытаний: фрикционные испытания образцов для определения коэффициента трения ДУКМ-тормозная колодка; испытания образцов для определения износа в системе ДУКМ-тормозная колодка с последующим применением макро- и микроструктурного анализа материала испытанных образцов. Показаны результаты износа модели детали из дисперсно-упрочненного композиционного материала “диск тормозной” автомобиля на основе фрикционных испытаний при сухом трении в зависимости от состава композиционного материала. На основании результатов исследований сделано заключение о возможности замены чугуна СЧ24 на дисперсно-упрочненный композиционный материал на основе алюминия.
В настоящее время в различных отраслях промышленности (автомобилестроении, авиационной и космической технике) заметно возрастает применение дисперсно-упрочненных композиционных материалов (ДУКМ). Актуальность использования этих материалов применительно к автотранспорту объясняется следующими основными причинами: стремлением снижения массы узлов и агрегатов автомобилей и, соответственно, уменьшением расхода горючего, а также экономическими и экологическими причинами. При этом одним из активно развивающихся в настоящее время направлений является применение ДУКМ в деталях подвески, в частности, в тормозных дисках, что позволяет значительно уменьшить неподрессоренные массы [1].
Серийно элементы тормозной системы из ДУКМ производят более 20 лет. В частности, одними из первых были Lotus Elise (1996 г.), Plymouth Prowler (1997 г.), Volkswagen Lupo 3L (1998 г.), Audi A2 (1999 г.). Высокие показатели износостойкости и теплопроводности алюминиевого ДУКМ позволяют заменить в тормозных дисках и барабанах чугун и сталь, обеспечивая экономию массы на 50–60% [2, 3].
Для определения удельного сопротивления ДУКМ абразивному износу в работе [4] предложено уравнение
(1)
$\Omega = \frac{{{{A}_{p}}}}{A}{{\Omega }_{p}} + \frac{{{{A}_{{\text{м}}}}}}{A}{{\Omega }_{{\text{м}}}},$Из приведенного уравнения следует, что ДУКМ с большей долей дисперсного наполнителя имеют более высокую износостойкость. При этом разные исследователи указывают различные размеры частиц упрочняющей фазы как оптимальные. В частности, в работе [5] показано, что при равном объемном содержании частиц наиболее высокие трибологические свойства – износостойкость, задиростойкость – характерны для ДУКМ с более прочной матрицей, армированной более крупными керамическими частицами. В работах [6, 7] показано, что в случае присутствия наноразмерных частиц наблюдается увеличение дисперсности структуры матричного сплава, что приводит к существенному уменьшению изнашивания материала. По результатам работы [8] улучшенную износостойкость имеет ДУКМ с повышенным содержанием армирующих частиц. Сравнительные исследования по износостойкости ДУКМ на основе алюминиевого сплава, проведенные в [9], показали, что износостойкость ДУКМ увеличивается с уменьшением размера частиц.
В работе [11] для оценки износа была предложена формула
где с – постоянная величина, зависящая от свойств материала матрицы; L – нагрузка; S – расстояние скольжения; Vf – объемная доля частиц; d – средний размер частиц.В работе [12] отмечено, что увеличение размера частиц SiC приводит к снижению скорости износа, в работе [13] аналогичный эффект отмечен для частиц Al2O3. В работе [14] показано, что при постоянной объемной доле упрочняющих частиц материалы с более крупными частицами имеют более высокую износостойкость. В работе [15] приводятся сведения, что более высокую износостойкость имеют композиты, содержащие частицы Al2O3 размером 66 мкм, по сравнению с композитами, содержащими частицы Al2O3 размером 16 мкм. Это связано, в частности, с разными механизмами износа. Крупные частицы более эффективно противостоят проникновению и разрезанию в поверхности и нелегко вырезаются ползунком из-за их больших размеров, высоких значений твердости и хорошей связи с матрицей (рис. 1). Обладая более тонкой микроструктурой, изнашиваемый материал работает как гомогенный материал.
Целью настоящей статьи являлось изучение возможности замены материала тормозного диска из СЧ24 на ДУКМ на основе алюминиевого сплава АК9 с содержанием частиц оксида алюминия 10–30%. Технология внутреннего окисления позволяет [16, 17] не только существенно снизить стоимость получения ДУКМ, но и обеспечить большую вариабельность армирующей фазы. На рис. 2 приведены примеры микроструктуры образцов, полученных внутренним окислением, с размером частиц от 1 мкм до 2 мм.
Рис. 2.
Микроструктура полученного материала ДУКМ со средним размером частиц: ∼1 мкм (а); ∼6 мкм (б) и ∼60 мкм (в); (г) – пример твердой фракции с размером включений более 1 мм, ×3000.

Методика исследований. Для получения механических характеристик ДУКМ, аналогичных СЧ24, были проведены эксперименты по влиянию легирующих компонентов и степени насыщения ими матрицы. По достижению заданных параметров прочности (240 МПа) эксперименты были прекращены с переходом к экспериментам на стойкость к истиранию. Заливка металла осуществлялась с температуры 700–710°С при температуре кокиля 100–120°С. Термическая обработка состояла из закалки и искусственного старения. Разливка полученного расплава осуществлялась в стальные разъемные кокили, предназначенные для определения прочности при растяжении образцов по ГОСТ 1497-84 (тип IV с диаметром рабочей части и 20 мм). Из полученных отливок СЧ24 и ДУКМ были изготовлены модельные образцы для проведения испытаний в масштабе 1:10 и тормозные колодки двух типов. Испытания на растяжение выполняли на установках ZD 10/90 и УМЭ-10ТМ. Микроструктуру материала разрабатываемых ДУКМ исследовали с использованием оптических микроскопов KEYENCE VHX-1000 и ЛОМО РВ-21.
Испытания на стойкость к истиранию образцов по схеме “кольцо–тормозная колодка” (ближайший аналог УМТ-1) показали, что рост насыщения частицами Al2O3 свыше 30% в условиях высокоскоростного трения неэффективен, так как происходит расплавление алюминия в пространстве между частицами и разрушение образца (рис. 3а).
Рис. 3.
Примеры разрушения и деформации образцов со степенью насыщения более 30% (а); менее 10% (б); со степенью насыщения 10–15% (в); 20–25% (г).
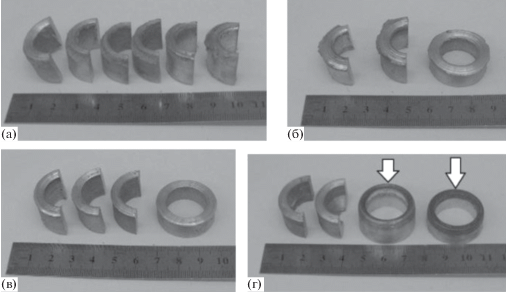
Низкое содержание упрочняющей фазы (рис. 3б) также приводит к разрушению образцов, но в данном случае образцы прогреваются, частично оплавляются и оседают под нагрузкой. На рис. 3в показаны примеры образцов со степенью насыщения порядка 10–15%, видна пластическая деформация образцов под нагрузкой. На рис. 3г приведен пример испытания образцов со степенью насыщения по 20–25%. Разрушение и деформация практически отсутствуют. На образцах, отмеченных стрелкой, виден износ при длительной работе. При этом в ряде случаев износ отличается в 1.5 раза даже в ходе испытания одной модели по одной колодке вследствие неоднородности состава материала колодки. Причем, глубина борозд зависит как от содержания армирующей фазы, так и от содержания медной составляющей в тормозной накладке. В частности, в одном случае износ практически отсутствовал, так как в районе приложения нагрузки наблюдалось повышенное содержание медной фазы.
В НГТУ при попытке прямого измерения коэффициента трения в системе “кольцо–колодка” был получен значительный разброс полученных данных, причем, с одним и тем же образцом ДУКМ на одной и той же колодке. Причиной является неоднородность колодки в условиях модельных испытаний. На рис. 4 представлена микроструктура материала такой колодки. Кроме того, оказалось, невозможно точно смоделировать давление в системе “диск–колодка”, так как давление в реальной системе составляет порядка 5 МПа.
Рис. 4.
Микроструктура материала колодки в различных зонах: (а) – зона с меньшим содержанием упрочняющей фазы; (б) – зона с высокой концентрацией упрочняющих частиц.
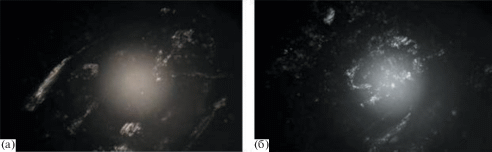
Определить коэффициент трения в системе “тормозной диск–колодка” оказалось затруднительно, так как проводить испытания необходимо при определенных контактных давлениях. Поэтому коэффициент трения трибопары “ДУКМ–колодка” определен в сравнении с чугуном СЧ24. Фрикционные свойства образцов исследовали на лабораторной установке трения (ИПМ РАН) (рис. 5). Узел трения представляет собой неподвижный сферический индентор (диаметром 3 × 10–6 м из закаленной стали ШХ-15) и поступательно движущийся испытуемый образец. Индентор укреплен на коромысле, который может свободно перемещаться в вертикальной и горизонтальной плоскостях. В вертикальной плоскости коромысло уравновешено противовесом. Столик с образцом получает поступательное движение от электромотора и за счет силы трения упирается в тензодатчик сопротивления. Касательное усилие преобразуется тензодатчиком в электрический сигнал, который подается на цифровой регистратор ЭнИ-701. Если тензодатчик предварительно проградуировать на усилие (для этого датчик надо повернуть на 90° и снять зависимость напряжения от нагрузки), то, зная нормальную нагрузку Р (Н) и касательное усилие F (Н), можно определить коэффициент трения по формуле
Рис. 5.
Лабораторная установка трения (ИПМ РАН) для проведения фрикционных испытаний: 1 – индентор; 2 – образец; 3 – коромысло; 4 – противовес; 5 – столик; 6 – электромотор; 7 – тензодатчик; 8 – нагрузка.
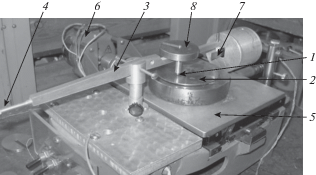
Коэффициент трения измеряли при сухом скольжении при переменной нагрузке (0.3–1 Н) на индентор при скорости скольжения 0.00004 м/с. Коэффициент трения определяли как среднее значение из двух проходов индентора по образцу. Абсолютная погрешность при измерении коэффициента трения составляла +/–0.005.
Результаты исследований. На рис. 6 приведены графики зависимостей коэффициента трения от нагрузки при контакте стального индентора с поверхностью исследуемых образцов ДУКМ и чугуна СЧ24.
Рис. 6.
Зависимости коэффициента трения от нагрузки при контакте индентора с поверхностью исследуемых образцов: 1 – чугун СЧ24; 2 – 6ТП; 3 – 8ТП; 4 – 4ТИ.

Установлено, что наименьшим коэффициентом трения обладает образец из чугуна СЧ24. Близкие значения fтр имеет сплав 6ТП с мелкодисперсным размером частиц упрочняющей фазы (3–5 мкм) (рис. 7). Коэффициент трения для этих материалов имеет постоянное значение во всем интервале приложенных нагрузок. Для образцов из сплавов 4ТИ и 8ТП с более крупным размером частиц (рис. 6: 10–15 мкм и 15‒20 мкм соответственно) коэффициент трения приблизительно в два раза превышает значение коэффициента трения для образца из СЧ24. Повышение коэффициента трения обусловлено увеличением сопротивления срезу при фрикционном пропахивании материала с более крупными упрочняющими частицами. При этом с увеличением нагрузки коэффициент трения возрастает, что позволяет прогнозировать эффект усиления эффективности торможения при возрастании усилия. По результатам лабораторных фрикционных испытаний в качестве фрикционного материала наилучшим образом показали ДУКМ из сплавов марок 4ТИ и 8ТП с более крупным размером частиц упрочняющей фазы.
Рис. 7.
Микроструктура образцов ДУКМ с разным размером частиц упрочняющей фазы Al2О3: (а) – 6ТП (3–5 мкм); (б) – 4ТИ (10–15 мкм); (в) – 8ТП (15–20 мкм), ×100.
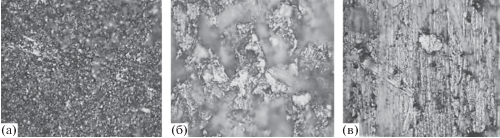
На рис. 8 показано изменение твердости и коэффициента трения ДУКМ относительно СЧ24, который принят за 100%. Установлено, что для образцов системы легирования “Al–Si”, насыщенных 25% Al2O3, но различным размером частиц, при близких значениях твердости материала сплавов коэффициент трения существенно отличается. В качестве перспективных материалов для тормозных колодок рекомендованы сплавы 4ТИ и 8ТП.
Для сплава 6ТП, как наиболее близкого по характеристикам к чугуну СЧ24, дополнительно были проведены исследования в центре коллективного пользования научным оборудованием “Функциональные наноматериалы и высокочистые науки” Института металлургии и материаловедения им. А.А. Байкова Российской академии наук. Испытания на трение и износ проводили по схеме “палец–диск”. Палец изготавливали из разных материалов (СЧ24, сплав ДУКМ). Диск изготавливали из автомобильной тормозной колодки отечественного производства. Путь трения составлял 900 м, скорость – 0.5 м/с. Давление изменялось от 0.5 до 2 МПа, что соответствует прикладываемой нагрузке 15.58 и 62.31 Н соответственно. В ходе испытания нагрузка линейно увеличивалась с 15.58 до 62.31 Н в течение первых 300 с, затем нагрузка оставалась постоянной 62.31 Н в течение 1500 с.
Коэффициент трения определяли на стадии установившегося трения. Интенсивность изнашивания определяли как отношение разницы масс до и после испытания к пути трения. Данные по коэффициентам трения и интенсивности изнашивания приведены в табл. 1.
Таблица 1.
Результаты испытаний на трение и износ по схеме “палец–диск”.
Материал образца | Коэффициент трения fтр | Интенсивность изнашивания образца Im, 10–3, г/м |
---|---|---|
СЧ24 | 0.3118 | 0.000833 |
6ТП | 0.3238 | 0.000611 |
По результатам стендовых испытаний материал марки 6ТП имеет более высокие значения коэффициента трения и меньшую интенсивность износа по сравнению с чугуном СЧ24.
Заключение. Испытания на стойкость к истиранию образцов по схеме “кольцо–тормозная колодка” (ближайший аналог УМТ-1) показали, что рост насыщения матрицы частицами Al2O3 свыше 30% в условиях высокоскоростного трения неэффективен, так как происходит расплавление алюминия в пространстве между частицами и, как следствие, разрушение образца. При этом большинство формул не учитывают нагрев до высоких температур в условиях высокоскоростного трения.
При пределе прочности ДУКМ, сравнимом с чугуном СЧ24 (240–280 МПа), и твердости +/–10% от твердости чугуна СЧ24 коэффициент трения образцов из ДУКМ не менее чем на 10% выше, чем у образцов из СЧ24. Причем, возможно создание сплавов с коэффициентом трения до 200% от СЧ24, что обеспечивает более эффективное торможение. При этом износостойкость ДУКМ выше по сравнению с СЧ24, а масса тормозного диска в два раза ниже массы диска из СЧ24.
Список литературы
Курганова Ю.А. Дисперсно-упрочненные композиционные материалы в условиях трения. Ульяновск: УлГТУ, 2008. 188 с.
Allison J.E., Cole G.S. Metal-matrix Composites in the Automotive Industry: opportunities and challenges // Journal of the Minerals, Metals and Materials Society. 1993. № 45 (1). P. 19.
Rahman M.M., Adebisi A.A. Maleque Metal Matrix Composite Brake Rotor: Historical Development and Product Life Cycle Analysis // International Journal of Automotive and Mechanical Engineering (IJAME). 2011. № 4. P. 471.
Axen N., Jacobson S. A model for the abrasive wear resistance of multiphase // Mater. Wear. 1994. № 174. P. 127.
Чернышева Т.А., Курганова Ю.А., Кобелева Л.И., Болотова Л.К., Калашников И.Е., Катин И.В., Панфилов А.В., Панфилов А.А. Композиционные материалы с матрицей из алюминиевых сплавов, упрочненных частицами, для пар трения скольжения // Конструкции из композиционных материалов. 2007. № 3. С. 38.
Калашников И.Е., Чернышова Т.А., Болотова Л.К. Синтез композиционных материалов с наполнителями различного вида для применения в узлах трения // Перспективные материалы. 2011. № 13. С. 519.
Калашников И.Е., Болотова Л.К., Чернышова Т.А. Трибологические характеристики литых алюмоматричных композиционных материалов, модифицированных наноразмерными тугоплавкими порошками // Российские нанотехнологии. 2011. Т. 6. № 1–2. С. 135.
Ramesh D. et al. Sand abrasive behavior of aluminium–frit particulate metal matrix composites // International Journal of Engineering Trends in Engineering and Development. 2012. V. 5. I. 2. P. 231.
Honnaiah C. et al. Effect of particle size on dry sliding wear of cast A356-Al2O3 Metal matrix composites // International Journal of Engineering Trends and Technology. 2014. V. 12. P. 438.
Hutchings I.M. Proc. Conf. Advanced Materials and Processes, University of Cambridge. 22–24 July. 1991. P. 56.
Sahin Y. Preparation and Some Properties of SiCp-Reinforced Aluminum alloy // Composites, Materials and Design. 2003. V. 24. P. 671.
Yilmaz O., Buytoz S. Abrasive Wear of Al2O3-Reinforced Aluminum-Based MMCs // Composites Science and Technology. 2001. V. 61. P. 2381.
Chung S., Hwang B.H. A microstructural study of the wear behavior of SiCp/Al Composites // Tribol. Int. 1994. V. 27. P. 307.
Kok M. Abrasive wear of Al2O3 particle reinforced 2024 aluminium alloy composites fabricated by vortex method // Composites: Part A Appl. Sci. Manuf. 2005. P. 1.
Varun Sethi. Effect of Aging on Abrasive Wear Resistance of Silicon Carbide Particulate Reinforced Aluminum Matrix Composite // Master of Science. 2007.
Чернышов Е.А., Лончаков С.З., Романов А.Д., Мыльников В.В., Романова Е.А. Исследование микроструктуры алюмоматричного дисперсно-наполненного литого композиционного материала, полученного методом внутреннего окисления // Перспективные материалы. 2016. № 9. С. 78.
Чернышов Е.А., Романов А.Д., Романова Е.А., Мыльников В.В. Разработка технологии получения алюмоматричного литого композиционного материала с помощью синтеза упрочняющей фазы оксида алюминия в расплаве алюминия // Известия высших учебных заведений. Порошковая металлургия и функциональные покрытия. 2017. № 4. С. 29.
Дополнительные материалы отсутствуют.
Инструменты
Проблемы машиностроения и надежности машин