Проблемы машиностроения и надежности машин, 2021, № 2, стр. 96-103
Обработка крупногабаритного бандажа цементной печи станкороботом
С. Н. Санин 1, *, Н. А. Пелипенко 2
1 Белгородский государственный технологический университет им. В.Г. Шухова
Белгород, Россия
2 Белгородский государственный национальный исследовательский университет
Белгород, Россия
* E-mail: osup-sns@yandex.ru
Поступила в редакцию 23.09.2020
Принята к публикации 18.12.2020
Аннотация
В статье приведена концепция базирования крупногабаритных деталей диаметром до 8300 мм и массой до 120 т типа бандажа вращающейся цементной печи при механической обработке с использованием мобильного станкоробота. Рассмотрен вопрос управляемого резания для обеспечения точного формообразования крупногабаритной детали при толщине снимаемого слоя металла до 6 мм. Обработка осуществляется методом силового шлифования с помощью специального инструмента – абразивного ремня. Обеспечение жесткости в системе “деталь–инструмент” реализуется локальным методом жесткого сопровождения.
Анализ современного состояния рассматриваемой проблемы. Многие промышленные агрегаты в России создавались раньше и создаются сейчас по принципу: чем больше, тем выше производительность. Такие крупногабаритные агрегаты находят свое применение в атомной, горной промышленности и промышленности строительных материалов. Их производство и эксплуатация связаны со значительными издержками. Поэтому одним из важнейших и актуальнейших вопросов тяжелого машиностроения является разработка оптимальных производственных технологий и методов восстановления изношенных деталей [1–8].
Например, длительность обработки бандажа вращающейся цементной печи (ВЦП) диаметром 6300 мм массой 62 000 т в стационарных условиях составляет более 600 станкочасов. Цена бандажа ВЦП составляет более 15 млн рублей. Приводная шестерня для стандартной цементной печи длиной 180 000 мм составляет более 42 млн рублей.
В работах [9–11] были рассмотрены технологические возможности по изготовлению новых или восстановлению изношенных крупногабаритных деталей типа тел вращения, размеры которых превышают 4000 мм с использованием небольших мобильных станков. Однако вопросам базирования крупногабаритных деталей в процессе их производства и механической обработки внимания было уделено не достаточно.
Цель статьи. Авторы ставят целью ознакомление читателя со своими существующими разработками в области механической обработки крупногабаритных деталей с использованием средств безрамной технологии.
Постановка задачи. Создание и применение мобильных станкороботов [12, 13] способствует существенному расширению технологической вооруженности предприятий, включая предприятия горнорудного и атомного машиностроения, промышленности строительных материалов. Для успешного применения средств безрамной технологии необходимо обеспечить правильное базирование обрабатываемых крупногабаритных изделий, а также обеспечить возможность компенсации неопределенности положения режущего инструмента относительно обрабатываемой поверхности крупногабаритной детали.
Изложение существа решения задачи. Механическая обработка наружных поверхностей бандажей ВЦП в заводских условиях [14] осуществляется с использованием схемы базирования (рис. 1), включающей установочную базу – одну из торцовых поверхностей бандажа и центрирующую базу – поверхность отверстия бандажа. Это типовая схема базирования деталей типа кольца, применяемая как для мелких или средних, так и для крупных деталей.
Используя типовую схему базирования можно исключить влияние гравитации на искажения формы обрабатываемой поверхности бандажа, ввиду того, что жесткость сечения бандажа в поперечном направлении на порядок выше, а вес бандажа равномерно распределен вдоль его круговой образующей. Таким образом, именно типовая схема базирования обеспечивает возможность получения наибольшей точности размеров, формы и взаимного расположения поверхностей обрабатываемых крупногабаритных кольцеобразных деталей. Следовательно, ее и следует применять при механической обработке поверхностей бандажей ВЦП.
Применение типовой схемы базирования может сопровождаться двумя методами формообразования. Первый метод формообразования предполагает неподвижное размещение бандажа ВЦП на некоторой опорной поверхности приспособления, при этом режущий инструмент должен совершать перемещение по круговой образующей относительно оси вращения бандажа ВЦП, как это происходит, например, при растачивании отверстий или при ротационном фрезеровании цилиндрических поверхностей.
Второй вариант формообразования предполагает возможность вращения самого бандажа, наподобие того, как это происходит в условиях цеха, например на планшайбе токарно-карусельного станка.
Основным требованием при принятии решения о применяемом методе формообразования является мобильность применяемых средств. Рассмотрим первый вариант формообразования и возможные в его рамках технологические решения.
Бандаж ВЦП должен быть установлен неподвижно на опорные поверхности специального приспособления. Приспособление может быть:
‒ изготовлено в виде сборной металлоконструкции, которую:
▪ перемещают транспортными средствами к месту эксплуатации вместе с мобильным станкороботом, развертывают, монтируют на заранее подготовленной площадке цементного завода, выверяют по уровню и пр.;
▪ заблаговременно изготавливают для нужд цементного завода, хранят на его территории и монтируют на заранее подготовленной площадке цементного завода постоянно или в периоды потребности завода в новых или отремонтированных бандажах;
‒ изготовлено из железобетона в виде стационарной строительной конструкции, укрепленной стальными листами, снабженной необходимыми конструктивными элементами для базирования заготовки бандажа ВЦП (по типу плаза), может:
▪ находиться под открытым небом или под навесом (капитальным, съемным, надувным и пр.);
▪ использоваться в межремонтые периоды для хозяйственных целей цементного завода, отличных от прямого назначения по базированию бандажей ВЦП.
Для целей изготовления или механической обработки бандажей цементному заводу понадобится подготовить специальную железобетонную площадку необходимой площади, выровненную по горизонту и имеющую достаточную прочность (толщиной не менее 600…800 мм), со встроенными стальными элементами под опоры. Эту площадку можно с некоторой натяжкой именовать базовой плитой или плазом по аналогии с плазами, применяемыми в тяжелом машиностроении. Площадка может быть прямоугольной или круглой формы. Диаметр вписанной окружности площадки должен не менее чем в два раза превышать диаметр обрабатываемых бандажей ВЦП.
Бандажи ВЦП имеют ограниченную жесткость в радиальном направлении и чуть большую в осевом. При базировании заготовки бандажа на планшайбе токарно-карусельного станка торцом, он соприкасается с опорной поверхностью планшайбы станка во многих точках своей поверхности, поэтому низкая жесткость конструкции бандажа не играет в процессе резания существенной роли.
Однако в полевых условиях при механической обработке следует учитывать недостаточную жесткость конструкции бандажей. Лучшим вариантом с точки зрения обеспечения точности формы бандажа было бы создание на поверхности плиты сплошной кольцеобразной опоры из бетона или стали (рис. 2, 3).
Рис. 2.
Схема устройства базовой плиты для выполнения механической обработки бандажей ВЦП вне условий механического цеха: 1 – бандаж ВЦП; 2 – стальная защитная накладка; 3 – базовая плита из железобетона с возвышением; 4 – установочные пластины.
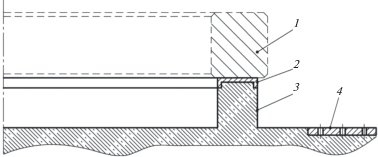
Рис. 3.
Схема установки бандажей ВЦП на базовой плите со съемным кольцевым возвышением: 1 – бандаж ВЦП; 2 – возвышение из профильного проката; 3 – установочные пластины; 4 – базовая плита.
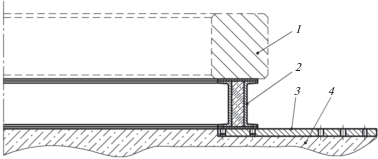
Возвышение 3 над базовой плитой должно обеспечить режущему инструменту доступ по всей длине образующих линий к наружной поверхности катания, к свободному торцу и к поверхности отверстия бандажа ВЦП без необходимости переустановки, т.к. каждая переустановка бандажа – это трудоемкий процесс, сопряженный с рисками тяжелого травмирования людей, разрушения строений и оборудования, деформаций самого бандажа.
Если конструкцию возвышения делать съемной, например, из стального профиля (рис. 3), то для последующей точной установки этого возвышения потребуется в базовой плите предусмотреть опорные поверхности в виде вмонтированных в бетон пластин 4 с отверстиями, в том числе резьбовыми (рис. 3) или пальцами.
С другой стороны наличие сплошной кольцеобразной опоры не является рациональным решением в связи с тем, что заготовка бандажа может оказаться с браком в виде существенного отклонения от параллельности его торцов, отклонения от плоскостности торцов, эксцентриситета отверстия относительно наружной поверхности, овальности и пр. Кроме того базовую плиту может со временем повести, а если не правильно выполнены геологические изыскания, плита может наклониться, получить несимметричную осадку, смещение. В результате может потребоваться выполнение комплекса строительно-монтажных работ по выравниванию плиты, исправлению опорных площадок или изменению положения бандажа на опоре для установки его по уровню.
В любом случае правильным решением будет являться установка бандажа не на монолитное возвышение, а на систему регулируемых опор (рис. 4). Трех опор не достаточно, должны быть предусмотрены дополнительные опоры, расположенные между тремя основными. Таким образом, общее количество опор должно составлять не менее шести [14], а лучше, если их количество будет достигать девяти или даже двенадцати для распределения нагрузки от установленной детали между ними.
Рис. 4.
Схема установки бандажей ВЦП на базовой плите с регулирумыми опорами: 1 – бандаж ВЦП; 2 – регулируемая самоустанавливающаяся опора со встроенными датчиками; 3 – механизм радиального перемещения; 4 – установочная пластина; 5 – базовая плита.
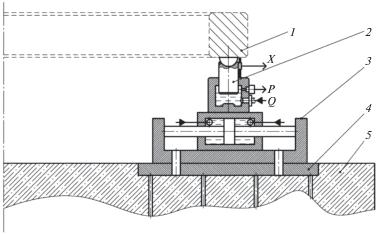
Выбор варианта конструкции опор под установку бандажа ВЦП требует глубокого экономического анализа и сложного проектирования. Однако нам представляется необходимым предварительно сформулировать следующие требования к опорам: 1) опора крепится к основанию анкерными болтами; 2) грузоподъемность одной опоры должна быть достаточна для удержания половины полного веса бандажа (в случае неравномерного нагружения опор при установке бандажа краном); 3) опоры должны быть регулируемыми по высоте и иметь управляемый привод (гидравлический или электрический); 4) опоры должны иметь возможность радиального перемещения для корректировки их положения с учетом диаметра устанавливаемой заготовки за счет продольных пазов на подошве опоры; 5) опоры должны иметь встроенные элементы системы измерения: уровня, величины нагрузки, пределов перемещений для автоматизации процесса выверки положения установленного бандажа; 6) рабочие поверхности опор должны иметь плоскую площадку (возможно с рифлениями) с возможностью самоустановления (для обеспечения наибольшей площади контакта с базовым торцом бандажа); 7) опоры должны легко монтироваться и демонтироваться.
Съемная конструкция опор имеет следующие положительные свойства: 1) съемные опоры можно хранить на специальном складе или транспортировать вместе с мобильным станкороботом с одного цементного завода на другой завод (достаточно иметь один комплект основной и один запасной, а не изготавливать комплект для каждого завода); 2) повышается надежность и ремонтопригодности системы базирования; 3) на территории цементного завода вне периода ремонта или строительства специальная площадка может использоваться для целей складирования материалов или иных хозяйственных целей и не будет содержать ненужных возвышений; 4) отпадает необходимость в дополнительных средствах для защиты высокотехнологичных опор от атмосферных воздействий и загрязнений, достаточно защитить опорные поверхности плиты основания; 5) при использовании на цементном заводе разных типоразмеров ВЦП, как это имеет место на Белгородском цементном заводе, съемные опоры достаточно передвинуть ближе к центру площадки или дальше от него, а не строить дополнительную площадку под другой типоразмер бандажей.
Из типовой схемы базирования (рис. 1) мы видим, что кроме установочной базы деталям типа кольца требуется центрирующая база. В случае базирования на опорные поверхности (рис. 2–4) контактную центрирующую технологическую базу выделить не представляется возможным. Можно говорить лишь об использовании настроечной технологической базы, в качестве которой может выступать или отверстие бандажа, или его наружная поверхность.
Если в качестве настроечной технологической базы рассматривать именно центральное отверстие бандажа ВЦП, то будет соблюдаться принцип единства баз в части совпадения с конструкторской основной базой детали: своим отверстием бандаж устанавливается на поверхность обечайки ВЦП (вваривается или центрируется и закрепляется системой башмаков).
Вопрос базирования бандажа ВЦП следует рассматривать в совокупности с вопросом обеспечения точности траекторий движения режущего инструмента относительно выбранных базовых поверхностей.
Траекторией движения режущего инструмента, каким бы он ни был (резец, фреза, абразивный ремень) [15, 16], должна быть правильная окружность с центром, совпадающим с центром отверстия бандажа. В условиях безрамной обработки решение этого вопроса всегда оказывалось наиболее трудоемким и трудноосуществимым. Однако на смену простым технологическим методам [1, 2, 4, 6] пришли современные цифровые технологии контроля и управления.
В связи с этим вопрос обеспечения точности размеров и формы обрабатываемого бандажа в большей степени возлагается на мобильный станкоробот и его систему автоматического управления [13]. Иначе говоря, нет необходимости в очень точной установке бандажа на опоры, нет необходимости в очень точной установке направляющих мобильного станкоробота или очень высокой жесткости его конструкции. Вопрос обеспечения точности формообразования решается в системе “бандаж–инструмент”. И поэтому очень важно обеспечить точность траектории движения именно режущего инструмента относительно обрабатываемого бандажа. И эта задача возложена на сам станкоробот за счет предусмотренных в его конструкции технологических возможностей, конструктивных особенностей и информационных алгоритмов.
Чтобы мобильный станкоробот мог перемещать режущий инструмент по круговой траектории относительно обрабатываемых поверхностей бандажа ВЦП, сам станкоробот должен иметь соответствующую круговую или квазикруговую траекторию движения. Это обеспечивается: размещением мобильного станкоробота на вращающейся относительно центра бандажа консоли (рис. 5); размещением мобильного станкоробота на круговых рельсовых направляющих.
Рис. 5.
Вариант консольного размещения мобильного станкоробота: 1 – консоль мобильного станкоробота; 2 – обрабатываемый бандаж ВЦП; 3 – модуль режущего инструмента; 4 – опора.
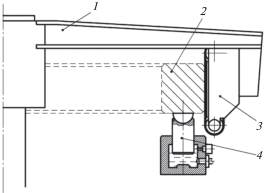
Использование консольного размещения мобильного станкоробота имеет ряд ограничивающих недостатков: 1) станкоробот предположительно имеет большой вес, а следовательно консоль, длина которой может превышать 3 м, и ее подшипники будут подвержены высоким нагрузкам от удержания веса станкоробота, а также от сил резания; 2) требуется подвод электропитания через консоль с использованием скользящего контакта, который может оказаться весьма ненадежным и создавать электромагнитные помехи системе управления; 3) при установке бандажа на опорную поверхность возвышенности консоль станкоробота нужно демонтировать или сворачивать (регулировать вылет, отклонять или поднимать сам станкоробот); 4) ввиду большой длины консоли возможно снижение жесткости технологической системы.
Преимуществом консольного размещения является точное центрирование самого станкоробота.
Размещение мобильного станкоробота на рельсовых направляющих предполагает высокую точность изготовления самих направляющих и относительно высокую точность их монтажа для обеспечения круговой (или квазикруговой) траектории движения режущего инструмента. Рельсовые направляющие размещаются по кругу вне кольца обрабатываемого бандажа на базовой плите (рис. 6).
Рис. 6.
Вариант размещения мобильного станкоробота на рельсовых направляющих: 1 – опора; 2 – обрабатываемый бандаж ВЦП; 3 – модуль режущего инструмента; 4 – мобильный станкоробот.
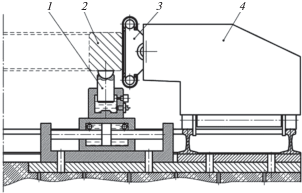
Среди недостатков применения рельсовых направляющих можно выделить: 1) если подводить электропитание через центральную консоль, то также придется использовать скользящие контакты; 2) высокая сложность и трудоёмкость монтажа и выверки рельсовых направляющих относительно горизонта и центра; 3) рельсовые направляющие предполагается транспортировать теми же средствами, что и мобильный станкоробот, и они будут занимать много места, имея при этом большой собственный вес.
Преимущества размещения станкоробота на рельсовых направляющих: 1) возможность подводить электропитание через рельсы; 2) высокая жесткость направляющих, размещенных на базовой плите; 3) маленький вылет станкоробота относительно рельсовых направляющих и, как следствие, уменьшенные нагрузки от его веса и повышенная жесткость технологической системы; 4) станкоробот не мешает установке бандажа на опоры.
Сравнивая преимущества и недостатки вариантов установки мобильного станкоробота, получаем вывод о превалировании достоинств рельсового варианта. При этом подводить электроэнергию следует через рельсы, а трудоемкость монтажа рельсовых направляющих следует минимизировать за счет оптимальных конструктивных решений. Погрешности выверки рельсовых направляющих наравне с другими погрешностями должен будет компенсировать сам мобильный станкоробот, управляемый интеллектуальной цифровой системой.
Заключение. Благодаря имеющимся у авторов практического опыта и наработкам в области безрамной технологии предлагаемое технологическое решение, касающееся станочной обработки крупногабаритных деталей с помощью небольших станко-роботов, является экономически оправданной, актуальной, реализуемой и открывает широкие перспективы для применения в условиях России. Предлагаемая концепция механической обработки крупногабаритных деталей позволяет снять ограничения по их габаритным размерам и массе и исключает потребность в раздельном изготовлении элементов одной детали, их транспортировке на большие расстояния, сборке на месте эксплуатации и последующей трудоемкой доработке или выверке.
Список литературы
Бондаренко В.Н., Кудеников А.А., Куденикова М.В. Комплексный подход к ремонтной обработке поверхностей катания цементных печей // Вестник БГТУ им. В.Г. Шухова. 2011. № 5. С. 274.
Мурыгина Л.В., Шрубченко И.В. Математическая модель оптимизации ленточно-абразивной обработки базовых поверхностей опор технологических барабанов // СТИН. 2012. № 3. С. 31.
Рыбалко В.Ю., Мурыгина Л.В., Шрубченко И.В. Оптимизация режимов ленточного шлифования поверхностей бандажей по гарантированному обеспечению заданного уровня шероховатости // Молодежь и научно-технический прогресс: сб. докл. Междунар. науч.-практич. конф. студ., аспир. и молодых ученых. Губкин, 2012. С. 47.
Стативко А.А. Обеспечение процесса формообразования при бесцентровой обработке бандажей цементных печей // Вестник БГТУ им. В.Г. Шухова. 2003. № 7. С. 64.
Шрубченко И.В., Рыбалко В.Ю., Мурыгина Л.В., Щетинин Н.А. К исследованию режимов ленточного шлифования поверхностей качения бандажей и роликов технологических барабанов // Вестник БГТУ им. В.Г. Шухова. 2013. № 3. С. 77.
Шрубченко И.В., Хуртасенко А.В., Гончаров М.С. Контактные проявления погрешности формы и расположения в технологических барабанах // Вестник БГТУ им. В.Г. Шухова. 2016. № 2. С. 81.
Chepchurov M.S., Tyurin A.V., Zhukov M.Eu. Getting Flat Surfaces in Turning // World Applied Sciences Journal. 2014. V. 30 (10). P. 1208.
Shrubchenko I.V., Hurtasenko A.V., Voronkova M.N., Murygina L.V. Optimization of cutting conditions for the processing of bandages of rotary cement kilns at a special stand // World Applied Sciences Journal. 2014. V. 31. № 9. P. 1593.
Pelipenko N.A., Sanin S.N., Pikalova A.A., Dujun T.A., Gunkin A.A. Theoretical Basis of the Principle of Roundness Ensuring Under Centreless Machining of Large Capacity Parts // Research Journal of Pharmaceutical, Biological and Chemical Sciences. 2014. № 5 (5). P. 1748.
Пелипенко Н.А., Санин С.Н. Технология прецизионного формообразования крупногабаритных пустотозаполненных колец диаметром более 4000 мм // Тяжелое машиностроение. 2016. № 5. С. 34.
Pelipenko N.A., Sanin S.N., Afanasjev A.A., Dujun T.A., Gunkin A.A. Introduction to Theory of Transverse Centerless Grinding of Large Cylindrical Surfaces // Research Journal of Applied Sciences. 2014. № 9. P. 696.
Tratar J., Kopač J. Robot Milling Of Welded Structures // Journal of Production Engineering. 2013. V. 16. № 2. P. 29.
Санин С.Н., Пелипенко Н.А. Инновационная технология изготовления крупногабаритных изделий // Записки Горного института. 2018. Т. 230. С. 185. https://doi.org/10.25515/PMI.2018.2.185
Санин С.Н., Оникиенко Д.А. Разработка концепции мобильного стенда для механической обработки бандажей вращающихся печей с базированием по торцовой поверхности и отверстию // Вестник БГТУ им. В.Г. Шухова. 2016. № 2. С. 104.
Qingni Y., Jian L., Weiji P., Qingyun Y. Dynamics analysis and simulation of roll grinder components // Manufacturing Technology. 2014. № 14 (4). P. 600.
Gostimirović M., Rodić D., Kovač P., Jesić D., Kulundžic № Investigation Of The Cutting Forces In Creep-Feed Surface Grinding Process // Journal of Production Engineering. 2015. V. 18. № 1. P. 21.
Дополнительные материалы отсутствуют.
Инструменты
Проблемы машиностроения и надежности машин