Проблемы машиностроения и надежности машин, 2022, № 2, стр. 33-40
Расчет показателей надежности подвижного состава в период нормальной эксплуатации
И. А. Майба 1, Д. В. Глазунов 1, *, А. М. Лященко 1
1 Ростовский государственный университет путей сообщения
Ростов-на-Дону, Россия
* E-mail: glazunovdm@yandex.ru
Поступила в редакцию 01.04.2021
После доработки 10.11.2021
Принята к публикации 20.12.2021
- EDN: XOOMWP
- DOI: 10.31857/S0235711922020092
Аннотация
В статье рассмотрены основные методы поиска неисправностей электрооборудования подвижного состава: органолептический метод, метод параметрического анализа, вероятностно-временной метод, метод половинного разбиения (метод дихотомии), логический метод диагностирования, метод применения теории графов. Определено, что наибольший эффект можно получить за счет создания и внедрения в каждом локомотивном депо средств диагностики на базе вычислительной техники и совершенствования системы планово-предупредительных ремонтов, а также перехода на ремонт локомотивов по фактическому техническому состоянию. Предложен практический пример диагностирования электрооборудования подвижного состава методом взаимной нагрузки.
Анализ современного состояния рассматриваемой проблемы. В последние годы выполнено много работ по повышению надежности локомотивов и совершенствованию их обслуживания и ремонта. Однако обеспечение требуемого уровня надежности для сложного оборудования и аппаратуры при существующих средствах контроля весьма трудная задача. Большинство неисправностей оборудования в настоящее время обнаруживается визуально, во время непосредственного внешнего осмотра [1–5]. В связи с этим возникла потребность в создании методов и устройств, позволяющих обнаружить и устранить дефекты до выхода из строя отдельного агрегата или всего локомотива.
Методы поиска неисправностей электрооборудования. В технической диагностике наиболее широко известны следующие методы поиска неисправностей электрооборудования [1–12]:
1. Органолептический метод. Этот метод предусматривает использование органов чувств испытателя – зрения, слуха, осязания, обоняния. Метод практически всегда предшествует применению любых других методов и является как бы вспомогательным. В результате его применения по внешним признакам практически сразу же обнаруживаются некоторые повреждения или вышедшие из строя узлы объекта.
2. Метод параметрического анализа. Метод основан на определении параметров контролируемого объекта с помощью приборов и инструментов. Проверяя параметры, обнаруживают отклонения и таким образом, устанавливают отказавший элемент. Способ прост, нагляден и не требует подробной исходной информации. Результаты ранее выполненных проверок не учитываются при выполнении последующих проверок. Недостаток метода – последовательность поиска неисправностей не оптимальна. Применяется для разнообразного оборудования.
3. Вероятностно-временной метод. Метод можно применять при произвольном соединении элементов системы. Исходная информация содержит сведения об отказах элементов (вероятность безотказной работы или вероятность отказа), время, затраченное на проверку элемента, а также отношение ${t \mathord{\left/ {\vphantom {t p}} \right. \kern-0em} p}$ или ${t \mathord{\left/ {\vphantom {t q}} \right. \kern-0em} q}$ (t – время; p – вероятность безотказной работы; q – вероятность отказа). Алгоритм поиска составляется с учетом функциональной схемы и матрицы неисправностей (табл. 1).
Таблица 1.
Матрица неисправностей
Причина отказа или отказавшие элементы | Признаки отказа | |||
---|---|---|---|---|
${{b}_{1}}$ | ${{b}_{2}}$ | … | ${{b}_{n}}$ | |
${{a}_{1}}$ | 1 | – | – | 1 |
${{a}_{2}}$ | – | 1 | 1 | – |
${{a}_{n}}$ | 1 | – | – | – |
Цифрой 1 обозначено наличие связи между признаками неисправности элемента и элементом системы или причиной отказа. Каждому признаку отказа соответствует свое множество причин неисправностей. Значения вероятности отказа или вероятности безотказной работы устанавливаются статистическим путем и используются для определения последовательности выполнения проверок. Эта последовательность устанавливается по величине отношения
(1)
${{{{p}_{1}}} \mathord{\left/ {\vphantom {{{{p}_{1}}} {{{t}_{1}}}}} \right. \kern-0em} {{{t}_{1}}}} > {{{{p}_{2}}} \mathord{\left/ {\vphantom {{{{p}_{2}}} {{{t}_{2}}}}} \right. \kern-0em} {{{t}_{2}}}} > ... > {{{{p}_{n}}} \mathord{\left/ {\vphantom {{{{p}_{n}}} {{{t}_{n}}}}} \right. \kern-0em} {{{t}_{n}}}},$Поиск начинают с проверки элемента, имеющего наибольшее отношение p/t.
Построенная таким образом программа обеспечивает минимальное время на поиск неисправности. Лучше учитывать минимум средних затрат на проведение поиска
где ${{C}_{i}}$ – общая стоимость проверок для обнаружения i-го отказавшего элемента; ${{g}_{i}}$ – вероятность того, что отказ объекта обусловлен отказом i-го элемента.Известен критерий минимакса: наилучшая последовательность проверок – та, при которой максимальная стоимость отказавшего элемента является наименьшей по сравнению с другими последовательностями. Целесообразная последовательность при наличии одного отказавшего элемента устанавливается в порядке увеличения отношения
При вероятности нескольких отказавших элементов
Введение показателя стоимости предпочтительнее только времени проверки, т.к. учитывается помимо времени стоимость применяемого оборудования, квалификация персонала и другие показатели.
4. Метод половинного разбиения (метод дихотомии). Этот метод позволяет получить экономичные (не избыточные) тесты и основывается на математической теории информации. Согласно этой теории получение информации – это уменьшение неопределенности суждения о состоянии объекта. Допустим, объект может находиться в одном из k состояний, каждому из которых соответствует одна неисправность. Любому из названных состояний объекта соответствует определенная вероятность. Без проверки технического состояния можно судить о нем с долей неопределенности. Эта неопределенность тем меньше, чем ближе к нулю или единице вероятность исправного состояния объекта. Максимальная неопределенность соответствует равенству вероятностей исправного и неисправного состояний, когда вероятность исправного состояния равна 0.5. Если вероятность неисправного состояния равна 0.99, с полной уверенностью можно считать, что элемент требует ремонта. В дальнейшем полагаем, что у неисправного элемента может быть только одна из k неисправностей. Предсказать, какая это неисправность, можно лишь с долей неопределенности. Причем, эта неопределенность тем больше, чем больше количество равновозможных вариантов требуется рассмотреть.
Основными достоинствами аналитических диагностических моделей являются их глубина и полнота описаний, но они сложны в расчетах и не обладают инженерной наглядностью. Чтобы устранить эти недостатки, при разработке диагностических моделей используют графоаналитические модели.
5. Логический метод диагностирования. Метод (иногда называемый эвристическим), который в отличие от формальных не задает жестких и обязательных правил выполнения, технологических переходов. Этот метод также требует предварительного перечня всех возможных в объекте дефектов и разработки модели объекта. По своей сущности логический метод можно назвать методом гипотез, т.к. поиск дефекта ведется путем проверки выдвинутых при анализе проявлений дефекта гипотез о возможных причинах искомого дефекта. При получении результатов выполнения тех или иных технологических переходов выдвигаются уточняющие гипотезы о причине дефекта, которые также проверяются до обнаружения дефекта. Контроль состояния элементов схемы требует использования контрольных точек, которые обеспечивают доступ к проводникам, соединяющим между собой элементы. Практически контрольные точки выполняются в виде клемм, электрических гнезд, проводников с зажимами и т.п. Рассмотрим диагностику схемы, представленной на рис. 1. Здесь контакты обозначены К1, К2, К3, а контрольные точки цифрами 1, 2, 3, 4.
Схема исправна, если каждый из контактов может находиться в замкнутом или разомкнутом состоянии в зависимости от управления им. Предполагаем, что в схеме может быть только одна неисправность. В состоянии каждого из трех контактов можно убедиться с помощью трех проверок, проверяя электрическую цепь между контрольными точками 1–2, 2–3 и 2–4. Внутренняя контрольная точка (точка 2) не всегда может быть доступна для контроля. В таком случае, применяя логический метод контроля цепи по участкам 1–3, 1–4 или 3–4, можно за три проверки обнаружить неисправный элемент. Кроме того, такой метод позволяет решить задачу, уменьшив количество проверок до двух. Порядок проверок и их результаты представлены в табл. 2.
Таблица 2.
Результаты проверок схемы
Результат проверки | Проверяемый участок | Отказавший элемент | ||
---|---|---|---|---|
1–3 | 1–4 | 3–4 | ||
001 | 0 | 0 | 1 | К1 |
010 | 0 | 1 | 0 | К2 |
100 | 1 | 0 | 0 | К3 |
В таблице цифры 1 и 0 соответствуют ответам “да” и “нет” на вопрос: “Есть ли цепь между контрольными точками?”. Таким образом, как показал рассмотренный пример, не всегда необходимо использовать все контрольные точки.
6. Метод применения теории графов. Практический интерес представляет решение задачи по диагностике схемы с применением минимального количества контрольных точек. Рассмотрим метод определения места расположения и количества контрольных точек на примере (рис. 2).
Представленная на рис. 2 схема содержит пять исполнительных контактных элементов К1…К5, каждый из которых управляется соответствующей катушкой. Для диагностики схемы выведены контрольные точки 1…6, а для подачи управляющих воздействий, изменяющих состояние схемы, точки 7…11. Подавая управляющие воздействия на точки 7…11 и определяя проводимость контактов между точками 1–2, 2–3, 3–4, 3–5, 2–6, можно найти неисправный контакт. Однако напомним, перед нами поставлена задача – определить минимальное количество контрольных точек и их расположение. Решение задачи удобно проводить с использованием теории графов. Графом называют графическую модель электрической схемы, в которой элементы схемы заменяют ребрами, а соединения элементов (электрические проводники) – вершинами (кружками), являющимися контрольными точками. Ниже приведен граф рассматривающий схемы, на ребрах которого (прямые линии) показаны элементы схемы (контакты) и точки, на которые нужно подавать воздействия (рис. 3).
Оказалось, что контрольные точки в вершинах графа с количеством ребер больше двух можно для контроля схемы не использовать (точки 2 и 3). Такие точки называют избыточными. Для проверки рассматриваемой схемы нужно подавать воздействия в точки 7…11, контрольное воздействие, не приводящее к изменению состояния схемы (напряжение питания) – в точку 1, а реакции снимать с точек 4, 5, 6. Появление напряжения в последних обозначим единицей, а отсутствие – нулем. Тогда каждому неисправному элементу соответствует свой код, если допустить в схеме наличие только одной неисправности. Результаты проверок схемы на рис. 3 приведены в табл. 3.
Таблица 3.
Результаты проверок схемы с исполнительными элементами
Номер контрольных точек | Неисправный элемент | |||
---|---|---|---|---|
4 | 5 | 6 | граф | схема |
0 | 0 | 0 | 1–2 | К1 |
0 | 0 | 1 | 2–3 | К2 |
0 | 1 | 1 | 3–4 | К3 |
1 | 0 | 1 | 3–5 | К4 |
1 | 1 | 0 | 2–6 | К5 |
1 | 1 | 1 | норма | норма |
К недостаткам рассмотренных методов (их называют формальными методами) следует отнести то, что для их применения необходима статистическая информация, полученная при диагностировании объекта. Однако дефекты и их проявление в данном объекте могут отличаться от известных ранее. Формальные методы в практике диагностики и настройке систем из-за недостатков, присущих им, используются редко. Более широкое распространение получил логический метод.
Возможность выявления дефектов и прогнозирования состояния контролируемого узла или всей системы в целом дает техническая диагностика. Наибольший эффект при этом можно получить за счет создания и внедрения в каждом локомотивном депо средств диагностики на базе вычислительной техники и совершенствования системы планово-предупредительных ремонтов, а также перехода на ремонт локомотивов по фактическому техническому состоянию. Рассмотрим практическое применение методов определения показателей надежности системы в эксплуатации.
Диагностирование электрооборудования локомотивов методом взаимной нагрузки. Анализ токовых нагрузок силовой схемы электровоза, приводящих к образованию источников его нагрева, показал возможность диагностирования отдельных элементов электрооборудования с использованием различных режимов их работы. Эти выводы были подтверждены в ходе испытаний технических средств в условиях технического ремонта и эксплуатации [1, 2, 6, 7]. Определение превышений температур обмоток выполняем для часового режима работы, по возможности с учетом тех видов дополнительных потерь, возникающих при работе на пульсирующем токе, которые поддаются сравнительно точному определению. Для проведения экспериментальных исследований по обнаружению температурных структур тяговых двигателей электровоза, испытываемых после заводского ремонта методом взаимной нагрузки, был использован переносной тепловизор NEC TH-9100. Тепловизоры фирмы NEC – это тепловизоры высокого уровня. Серия TH9100 самая дорогая из представленных, но при этом эти тепловизоры самые функциональные и обладают наилучшими техническими характеристиками. Измерения проводились на испытательной станции электромашинного цеха на Ростовском электровозоремонтном заводе (РЭРЗ) АО “Желдорреммаш”. Опытная эксплуатация предложенного в статье метода ИК-диагностики показала высокую вероятность обнаружения дефектных узлов тяговых двигателей электровозов после проведения заводского ремонта. С целью проверки его точности предварительно были проведены опытные измерения температуры тяговых двигателей НБ-418К6 после испытания в часовом режиме после заводского ремонта в электромашинном цехе РЭРЗ на стенде (рис. 4, 5) испытательной станции.
Рис. 4.
Испытательная станция: (а) – внешний вид стенда для испытания тяговых двигателей в часовом режиме; (б) – стенд для испытания тяговых двигателей методом взаимной нагрузки.
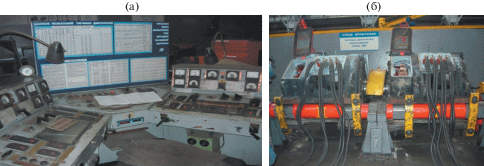
Рис. 5.
Вид через коллекторный люк тягового двигателя: (а) – фото коллекторного люка; (б) – визуализация коллекторного люка при помощи тепловизора.
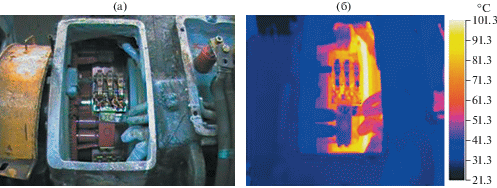
Результаты испытаний представлены на рис. 5.
Показатель надежности – температуру меди обмотки якоря тягового двигателя НБ-520В определим из уравнения
(3)
${{T}_{{\text{м}}}} = \frac{{\sum {\Delta {{P}_{{\text{м}}}}\left[ {1 + \frac{{{{\alpha }_{{\text{a}}}}}}{{{{\lambda }_{{{\text{из}}{\text{.a}}}}}p{\kern 1pt} '}}\left( {{{t}_{1}} + \frac{{{{m}_{{\text{к}}}}\pi {{d}_{{\text{к}}}}}}{{2Z}}} \right)} \right] + \sum {\Delta {{P}_{{{\text{ca}}}}}\left( {1 - \frac{{{{\alpha }_{{\text{a}}}}}}{{{{\lambda }_{{{\text{из}}{\text{.a}}}}}p{\kern 1pt} '}}{{t}_{1}}\frac{{{{l}_{{\text{л}}}}}}{{{{l}_{{\text{a}}}}}}} \right)} } }}{{{{\alpha }_{{\text{a}}}}\pi \left[ {{{D}_{{\text{a}}}}\left( {{{l}_{{\text{a}}}} + {{l}_{{\text{л}}}}} \right) + \frac{{{{m}_{{\text{к}}}}{{d}_{{\text{к}}}}}}{2}{{l}_{{\text{a}}}}} \right]}} + {{T}_{{\text{В}}}},$При подстановке известных численных значений получим
Таким образом, температура меди обмотки якоря расчетным путем с учетом охлаждающего воздуха составила 105°С. При испытании тяговых двигателей подвижного состава в эксплуатации в часовом режиме температура составила 101°С. В связи с незначительной погрешностью расчетных и эксплуатационных значений, можно сделать вывод о целесообразности применения данной методики теплового контроля в испытаниях тяговых двигателей.
Обсуждение результатов в научном и прикладном аспектах. Описаны основные методы поиска неисправностей электрооборудования подвижного состава, применение которых связано с необходимостью получения статистической информация при диагностировании объекта.
Предложен практический пример диагностирования электрооборудования подвижного состава методом взаимной нагрузки, основная особенность которого заключается в обнаружении температурных структур тяговых двигателей электровоза, испытываемых после заводского ремонта при помощи тепловизора.
Список литературы
Тептиков Н.Р., Резниченко А.А., Губарев П.В., Глазунов Д.В. Математические методы принятия решений в системах диагностики и управления на тяговом подвижном составе // Сборка в машиностроении, приборостроении. 2018. № 1. С. 13.
Бабков Ю.В., Перминов В.А., Белова Е.Е. и др. Гарантийные локомотивы – упущенная готовность // Локомотив. 2013. № 5. С. 34.
Кохановский В.А., Глазунов Д.В., Зориев И.А. Макрокомпозиционные полимерпорошковые подшипники // Проблемы машиностроения и надежности машин. 2019. № 2. С. 40. https://doi.org/10.1134/S0235711919020081
Kochanowski V.A., Mayba I.A., Glazunov D.V., Zoriev I.A. Powder bearings with polymer inserts // Journal of Friction and Wear. 2019. T. 40. № 3. C. 229. https://doi.org/10.3103/S1068366619030048
Kokhanovskii V.A., Maiba I.A., Glazunov D.V., Bol’shikh I.V. Lubricator casings for locomotive wheel rims // Russian Engineering Research. 2016. T. 36. № 5. C. 364. https://doi.org/10.3103/S1068798X160500993
Четвергов В.А., Пузанков А.Д. Надежность локомотивов. М.: Маршрут, 2003. 415 с.
Приложение к распоряжению ОАО “РЖД” от 12.11.2008 г. № 2367р. Методические положения для расчета показателей безотказности локомотивов по результатам их эксплуатации. М.: ОАО “РЖД”, 2010. 48 с.
Горский А.В., Воробьев А.А. Надежность электроподвижного состава. М.: Маршрут, 2005. 303 с.
Гриценко А.В., Стрекопытов В.В. Основы теории и практики надежности технических устройств. СПб.: Сударыня, 2004. 272 с. ISB5-88718-050-1
Пугачев В.С. Теория вероятностей и математической статистики. М.: Наука, 1979. 496 с.
РД50-690-89. Технические условия строительства локомотивов. Руководящий документ по стандартизации. Группа Т51 – Надежность в технике. Методы оценки показателей надежности по экспериментальным данным. Введен 01.01.1999.
ГОСТ Р 56046-2014. Показатели использования локомотивов. Термины и определения.
Дополнительные материалы отсутствуют.
Инструменты
Проблемы машиностроения и надежности машин