Проблемы машиностроения и надежности машин, 2022, № 3, стр. 102-112
Повышение надежности и эффективности измерений параметров деформации алюминиевых сплавов на универсальной испытательной машине
П. А. Петров 1, *, В. Н. Фам 1, И. А. Бурлаков 1, А. Г. Матвеев 1, Б. Ю. Сапрыкин 1, М. А. Петров 1, У. Ш. Диксит 2
1 Московский политехнический университет
Москва, Россия
2 Индийский институт технологии Гувахати
Гувахати, Индия
* E-mail: petrov_p@mail.ru
Поступила в редакцию 30.08.2021
После доработки 02.11.2021
Принята к публикации 20.12.2021
- EDN: DZBZZJ
- DOI: 10.31857/S0235711922020110
Аннотация
В статье рассматривается методика подготовки лабораторного испытания на сжатие, направленного на сбор данных для построения изотермической кривой текучести деформируемого материала. Особенность методики – определение значения скорости деформации с учетом особенностей испытательной машины. В качестве объекта исследования рассматривается цилиндрический образец с определенным соотношением H0/D0 алюминиевого сплава АМг6. Получены данные о бочкообразности; о выборе соотношения размеров исходного образца H0/D0, обеспечивающих постоянную скорость деформации и формоизменение без разрушения. Полученные данные учитываются при определении технологических свойств деформируемых материалов, применяемых при разработке и исследовании малоизученных технологий обработки давлением – технологии изотермической штамповки и технологии штамповки кручением алюминиевых сплавов.
Для сбора данных о сопротивлении деформации конструкционных материалов, подвергаемых пластической деформации, необходимо проведение лабораторных испытаний [1, 2]. Например, в качестве лабораторного испытания металлических материалов можно применить испытания на сжатие, методы проведения которых, в целом, описаны в ГОСТ 25.503-97.
Важными этапами проведения испытания является: 1) выбор размеров исходного образца исследуемого материала, в частности соотношения его высоты к диаметру (H0/D0); 2) выбор испытательной машины, обеспечивающей достижения требуемых значений скорости деформации (${{\dot {\varepsilon }}_{i}}$) и температуры (Ti); 3) выбор способа сбора экспериментальных данных об испытании и способа их обработки для получения достоверных исходных данных для обработки и построения экспериментальных кривых текучести материала для исследуемых температурно-скоростных условий деформации.
В области обработки давлением знания о технологических свойствах деформируемого материала имеют огромное значение для получения достоверных результатов решения краевой задачи обработки металлов давлением (ОМД), т.к. лежат в основе модели сопротивления деформации (материала). Модель материала является необходимой при решении краевой задачи ОМД вне зависимости от того, какой метод решения задачи выбран: аналитический, численный или инженерный. При компьютерном имитационном моделировании операций ОМД, реализуемом на основе численного(ых) метода(ов), точность моделирования во много определяется качеством и точностью исходных данных о сопротивлении деформации материала. В обобщенном виде взаимосвязь между экспериментом, по результатам которого обеспечивается получение данных для построения модели материала, и вычислительными ресурсами (САЕ-системой), применяемыми для выполнения компьютерного имитационного моделирования, можно представить так: база данных материалов, в которую вводится информация о модели материала – численный(е) метод(ы), применяемые для решения задачи ОМД (САЕ-система) – вычислительный “эксперимент”, направленный на моделирование задачи ОМД.
На вход САЕ-системы загружается модель материала, описывающая его поведение в данных температурно-скоростных условиях деформирования. Чем больше факторов, влияющих на сопротивление деформации материала, учитывает его модель, тем полнее описывает его поведение при деформировании, что в современных условиях является весьма актуальным направлением исследований.
Цель настоящей статьи заключается в анализе влияния соотношения размеров исходного образца (H0/D0) на результаты испытаний на сжатие образцов сплава АМг6, выполненных с постоянной скоростью деформации разного значения. Соотношение H0/D0 определяет предел возможного изменения скорости деформирования в процессе нагружения образца, выполняемого на универсальной испытательной машине, выбранной для проведения эксперимента.
Для достижения поставленной цели требуется решить следующие задачи: 1) разработать методику проведения испытания на сжатия цилиндрических образцов с разным соотношением H0/D0; 2) выбрать размеры образцов и скоростные условия проведения экспериментальных исследований, позволяющих реализовать разрабатываемую методику; 3) исследовать влияние соотношение размеров на характер кривых текучести при проведении испытаний на универсальной испытательной машине с возможностью управления программой нагружения.
Основная особенность испытаний на сжатие заключается в создании однородного напряженного состояния по всей высоте образца [3]. При неудачном выборе формы и размеров исходного образцов, полученные результаты сопротивления деформации несут в себе не только данные о поведении материала как такового, но и влияние на него вторичных факторов, связанных с неидеальными условиями проведения эксперимента.
Материалы и оборудование для проведения испытания. Испытания на сжатие выполнены на универсальной испытательной машине, имеющей числовое программное управление, а также систему подготовки, контроля и сбора данных об испытании. Характеристики испытательной машины (LFM-250, Walter+Bai AG, Швейцария) представлены в табл. 1.
Таблица 1.
Характеристики испытательной машины
Параметр | Показатель |
---|---|
Максимальная нагрузка | 250 кН |
Минимальная нагрузка | 1.25 кН |
Максимальная скорость испытания | 500 мм/мин |
Ход траверсы | до 1000 мм |
Тип привода | Электромеханический |
Пределы допускаемой относительной погрешности: | |
силоизмерителя | 0.5% |
измерения перемещения подвижной траверсы | ±1.0% |
задания скорости перемещения подвижной траверсы без нагрузки | ±1.0% |
Выделим полезные особенности универсальной машины: наличие автоматизированной системы контроля и сбора данных об испытании; наличие программного обеспечения, обеспечивающего двустороннюю связь с данной системой; наличие возможности управления программой нагружения, учитывая особенности проводимых испытаний.
Исследуемый материал – сплав АМг6, относящийся к категории деформируемых алюминиевых сплавов системы Al–Mg. Сплав АМг6 является термически неупрочненным, при этом обладает повышенной устойчивостью к коррозийным изменениям [4]. Химический состав сплава, из которого были изготовлены образцы для исследования (% мас.): Al – 93.27; Mg – 5.835; Mn – 0.565; Fe – 0.26; Si – 0.13.
Из прессованного прутка исследуемого сплава АМг6 были изготовлены цилиндрические образцы с разным соотношением H0/D0: 1) диаметр 11.8 мм, высота 18 мм, соотношение H0/D0 = 1.5; 2) диаметр 11.8 мм, высота 11.8 мм, соотношение H0/D0 = 1.0; 3) диаметр 10.0 мм, высота 10.0 мм, соотношение H0/D0 = 1.0.
Образцы для испытания получены точением с последующим шлифованием торцевых поверхностей. Температура во всех экспериментах составляла 20°С и испытания проводили при различных значениях скорости деформации: 0.001 с–1; 0.01 с–1; 0.10 с–1; 0.22 с–1, 0.40 с–1. Деформирование образца выполнялось без смазки.
Методика испытания на сжатие образцов материалов с разным соотношением H0/D0. В некоторых работах [5–7] показано на примере осадки цилиндрических образцов при комнатной и повышенной температуре, что при деформации до 50% у образцов отсутствует заметная бочкообразность боковой поверхности, т.е. деформацию можно считать однородной, а напряженное состояние – линейным и интенсивность напряжения определяется выражением
где Pi – текущее (измеренное) значение силы деформирования; Fi – значение площади поперечного сечения образца, соответствующее значению Pi и текущей высоте деформируемого образца Hi.При этом перед началом испытаний на сжатие на торцовую поверхность образцов наносится смазка. При таком подходе очень сложно контролировать в процессе испытания истинную температуру деформируемого материала и материала инструмента, если проводится испытание материала при повышенных температурах, т.к. при нанесении смазки, нагретый образец контактирует с окружающей средой и его температура, как и температура материала инструмента, уменьшается. В этом случае, полученные экспериментальные кривые текучести не будут соответствовать температуре испытания, заданной при подготовке. С другой стороны, если рассматривать испытания на сжатие при комнатной температуре, то вышеназванная проблема изменения температуры отсутствует. Однако, влияние контактного трения на форму боковой поверхности, остается и оно тем меньше, чем более эффективная смазка применяется.
Можно также провести аналогию с испытанием на растяжение: образец растягивается и до начала формирования шейки напряженное состояние считается линейным, а начиная с момента формирования шейки – объемным. Для компенсации объемного напряженного состояния (НС) вводится поправочный коэффициент k, например поправочный коэффициент П. Бриджмена или поправочный коэффициент Давиденкова–Спиридоновой. Тогда, формула для расчета интенсивности напряжения ($\sigma _{i}^{k}$) по результатам испытания на растяжения записывается в виде
где $\sigma _{i}^{k}$ – интенсивность напряжения при линейном НС; k – поправочный коэффициент, учитывающий объемное состояние в шейке; ${{\sigma }_{i}}$ – интенсивность напряжения, определяемая по формуле (1).В работах [8, 9] исследователи применяют подобный подход (2) для компенсации объемного НС, формируемого за счет бочкообразности боковой поверхности образца при проведении испытания на сжатие.
Еще один современный подход к обработке данных испытаний на сжатие и учету бочкообразности описан в работе профессора Петржика и его коллег [2]. Он связан с применением метода постановки обратной задачи, которая предполагает проведение двух экспериментов: натурного и вычислительного. При этом вычислительный эксперимент позволяет определить оптимальное сочетание исходных данных, обеспечивающих минимальное отклонение от данных натурного эксперимента. В этом случае применение смазки либо ее отсутствие становятся второстепенным параметром для испытания на сжатие.
Учитывая, что в эксперименте сжатие образцов проводилось без смазки, на этапе обработки результатов использовали методику, подробно описанную в работе [10] и основанную на методе постановки обратной задачи [2]. Несмотря на выбранный подход, для испытания на сжатие остается важным выбор соотношения размеров исходного образца по двум причинам: 1) отсутствие в эксперименте продольной устойчивости образца; 2) возможность проведения эксперимента с максимальным изменением скорости деформирования в процессе нагружения образца при фиксированной (ограниченной конструкцией машины) скорости перемещения траверсы испытательной машины.
Подбор соотношение высоты (H0) исходного образца к его диаметру (D0) принято выполнять в диапазоне от 1 до 2.5. При значении отношения H0/D0 равном или более 1.0, считается, что влияние трения существенно меньше; при осадке высоких размеров (H0/D0 ≥ 2.5) – происходит потеря устойчивости образца, трудно избежать его продольного изгиба и результаты натурного эксперимента не могут быть обработаны.
На рис. 1 приведены диаграммы, полученные при испытании на сжатие цилиндрических образцов из среднеуглеродистой стали одинакового диаметра D0, но с различным начальным отношением H0/D0 [11]. При переходе от относительно длинных образцов с начальным отношением H0/D0 = 2 к коротким образцам (H0/D0 = 0.5) сопротивление пластическому деформированию возрастает ∼1.3 раза в области значений деформаций от 1.0 до 1.4. В области значений деформаций от 0 до ∼0.6 (рис. 1) влияние значения соотношения H0/D0 на сопротивление деформации практически минимальное. То есть значение истинной деформации в эксперименте не должно превышать 0.6, что соответствует примерно осадке образца на 50% его исходной высоты H0.
В работе [12] представлены диаграммы сжатия образцов алюминиевого сплава А6061-Т651 (рис. 2), имеющие характер влияния значения H0/D0 на сопротивления деформации аналогичный тому, что представлен на рис. 1.
Рис. 2.
Диаграммы сжатия цилиндрических образцов из алюминиевого сплава А6061 термически обработанного по режиму Т651 (российский аналог – сплав АД33): H0/D0 = 1 – сплошная линия; H0/D0 = 2 – штриховая линия [12].
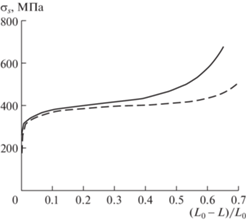
Для повышения надежности метода испытания на сжатие при комнатной и, особенно, при повышенной температуре, в работе [8] представлена методика компенсации влияния контактного трения на сопротивления деформации – значение коэффициента k в формуле (2) определено следующим образом:
(3)
$k = \frac{1}{A},\quad A = 1 + \frac{{2m}}{{3\sqrt 3 }}\frac{{{{R}_{0}}}}{{{{H}_{0}}}}\exp \left( { - \frac{{3{{\varepsilon }_{i}}}}{2}} \right),$Проверка справедливости формулы (3) выполнена по результатам испытаний на сжатие цилиндрических образцов (H0/D0 = 1.55) с плоскими торцами без проточек со смазкой [8]. Материал образцов – алюминиевый сплав А2024 (российский аналог – сплав Д16) в отожженном состоянии и термообработанные по режиму Т351 [11].
На рис. 3 представлены результаты расчета коэффициента А формулы (3) при соотношении H0/D0 от 0.5 до 3.
Рис. 3.
Влияние соотношения H0/D0 на значение коэффициента А: 1 – H0/D0= 0.5; 2 – H0/D0 = 1.0; 3 – H0/D0 = 1.5; 4 – H0/D0= 2.0; 5 – H0/D0= 3.0.
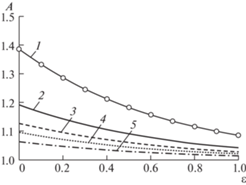
Значение А в формуле (3) зависит от значения истинной деформации, показателя трения и соотношения H0/D0. Принимая, что показатель трения m = 1 (сжатие образца без смазки), значение А определяется только размерами образца. Чем меньше отношение высоты образца к его диаметру, тем больше значение А и, соответственно, меньше значение k в формуле (3), меньше значение напряжения текучести (2) после его корректировки.
Основываясь на рассмотренных результатах других исследователей, в настоящей статье принята следующая методика проведения испытания на сжатие и последующей обработки его результатов: 1) расчет программы нагружения, обеспечивающей постоянную скорость деформации в процессе нагружения образца – 0.001 с–1; 0.01 с–1; 0.1 с–1; 0.22 с–1, 0.40 с–1; 2) сжатие цилиндрических образцов с плоскими торцами с соотношением H0/D0 = 1 и 1.5 (абсолютные размеры представлены выше) без смазки; 3) обработка результатов испытания в соответствии с методикой, подробно изложенной в работах [10, 13], основываясь на методе постановки обратной задачи; 4) оценка влияния соотношения H0/D0 на получаемую кривую текучести сплава АМг6.
На рис. 4 представлены примеры программ нагружения (зависимость “время t, с”–“высота образца h, мм”), обеспечивающие постоянную скорость деформации на протяжении всего рабочего хода испытательной машины.
Рис. 4.
Программы нагружения при постоянной скорости деформации и различных размерах исходного образца: 1 – высота 18 мм, диаметр 11.8 мм; 2 – высота 11.8 мм, диаметр 11.8 мм; 3 – высота 10 мм, диаметр 10 мм.
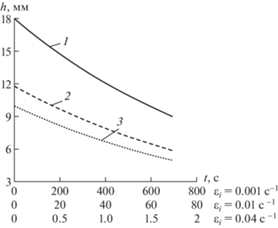
Программа нагружения зависит от размеров исходного образца H0 и D0 (рис. 4). Уменьшение высоты H0 позволяет получать программу нагружения, обеспечивающую большую постоянную скорость деформации. При этом следует учитывать допустимое соотношение H0/D0 и максимальную скорость деформации выбранной испытательной машины. Так, например, для испытательной машины (табл. 1) максимальная скорость перемещения траверсы 250 мм/мин и при высоте образца H0 = 10 мм (H0/D0 = 1.0) возможно выполнить нагружения с постоянной скоростью деформации ∼0.4 с–1.
Это значение скорости деформации является максимально возможным для выбранной испытательной машины. Если увеличить соотношение H0/D0 до 1.5, то максимально возможная для данной испытательной машины скорость деформации составит ∼0.28 с–1.
Результаты исследования и их обсуждение. На рис. 5 представлены цилиндрические образцы после проведения испытания на сжатие без смазки, направленные на изучение влияния соотношения размеров образца на кривые текучести материала.
Рис. 5.
Образцы сплава АМг6 после осадки: (а) – соотношение H0/D0 = 1.5; (б) – соотношение H0/D0 = 1 (H0 = 10 мм, D0 = 10 мм); (в) – соотношение H0/D0 = 1 (H0 = 11.8 мм, D0 = 11.8 мм).
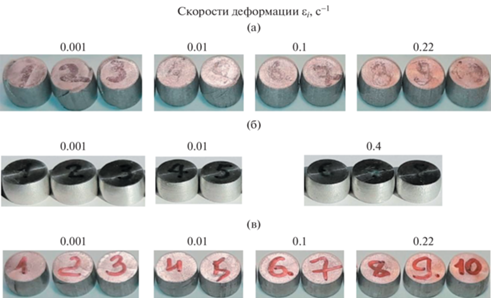
Проанализируем полученные результаты, учитывая наиболее важные аспекты испытаний: 1) характер изменения формы образца с разным значением соотношения H0/D0; 2) сопоставление кривых текучести, полученных для образцов с разным соотношением H0/D0.
В табл. 2 представлены результаты, иллюстрирующие сравнение высоты hм осаженного образца (в конце рабочего хода машины), полученной в эксперименте, с конечной высотой hф образца, рассчитанной по значению перемещения траверсы испытательной машины, записанному ее процессором в протокол испытания. Наблюдаемая относительная погрешность δh может говорить о наличии в эксперименте факторов, влияющих на значение hф и не учитываемых при формировании протокола испытания. Например, жесткость машины, выборка зазоров в инструменте для проведения сжатия, избыточный холостой ход траверсы и т.п. Это отклонение компенсируется на этапе обработки результатов экспериментов в соответствии с методикой, описанной в работе [10].
Таблица 2.
Высота образца после проведения сжатия: эксперимент и расчет
H0/D0= 1 (11.8/11.8) | H0/D0= 1.5 | H0/D0= 1 (10/10) | |||||||||
---|---|---|---|---|---|---|---|---|---|---|---|
${{\dot {\varepsilon }}}$, c–1 | 0.001 | 0.01 | 0.1 | 0.22 | 0.001 | 0.01 | 0.1 | 0.22 | 0.001 | 0.01 | 0.4 |
hм, мм | 6.7 | 6.4 | 6.4 | 6.5 | 9.4 | 9.4 | 9.3 | 9.3 | 5.7 | 5.6 | 5.6 |
hф, мм | 8.1 | 7.9 | 7.8 | 7.9 | 11.3 | 11.1 | 11.2 | 11.1 | 6.7 | 6.8 | 6.6 |
δh, % | 20.9 | 23.4 | 21.9 | 21.5 | 20.2 | 18.1 | 20.4 | 19.4 | 17.5 | 21.4 | 17.9 |
По результатам проведения испытаний выполняется расчет значения напряжения текучести (интенсивности напряжения) и интенсивности (накопленной) деформации. На рис. 6 показаны результаты испытаний образцов с разным исходным соотношением H0/D0.
Рис. 6.
Кривые текучести (экспериментальные) сплава АМг6 для образцов с разным значением H0/D0 при скорости деформации: (а) – соотношение H0/D0 = 1.0 (H0 = 11.8 мм, D0 = 11.8 мм); (б) – соотношение H0/D0 = 1/5 (H0 = 10 мм, D0 = 10 мм); (в) – соотношение H0/D0 = 1.0 (H0 = 10.0 мм, D0 = 10.0 мм). 1 – 0.001 с–1; 2 – 0.01 с–1; 3 – 0.1 с–1; 4 – 0.22 с–1; 5 – 0.4 с–1.
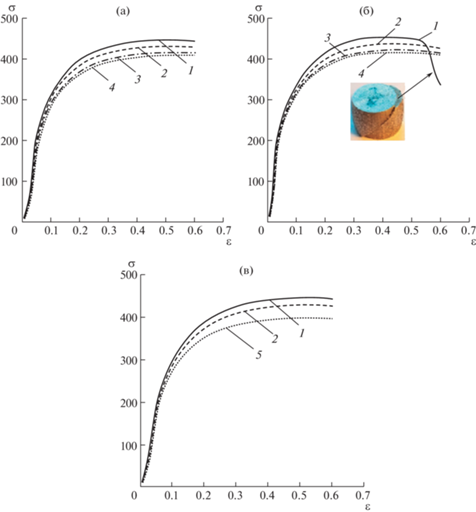
Кривые текучести (рис. 6), полученные в результате сжатия образцов с разным исходным соотношением H0/D0 при разных скоростях деформации, практически не отличаются друг от друга по уровню напряжения текучести и характеру его изменения. Имеющиеся отличия (рис. 6б) связаны с появлением трещины на поверхности образца при деформации ∼0.5. Трещина вышла на поверхности в случае сжатия образца при скорости деформации 0.001 с–1. Причина возникновения трещины, по всей видимости, связана с проявлением эффекта Портевена–Ле Шателье, характерным для сплавов системы Al-Mg при их холодной деформации. С этим же эффектом может быть связана аномалия в изменении напряжения текучести при нагружении образцов с разной скоростью деформации. Однако более углубленное исследование такой аномалии требует отдельного исследования. Подобного рода исследования, например, проведены и опубликованы в работе [14]. Характер распространения трещины по боковой поверхности образца после сжатия примерно соответствует углу 45° к оси образца.
Падение напряжения текучести (рис. 6; образец с H0/D0 = 1.5) обусловлено выходом трещины на боковую поверхность и продолжающимся рабочим ходом машины. Рабочий ход машины продолжается в соответствии с заданной программой нагружения до достижения конечной высоты; после раскрытия трещины (∼ с деформации 0.51) верхняя часть образца скользит относительно нижней по плоскости трещины, что не требует преодоления сопротивления материала деформации, а только свободного сдвига одного твердого тела относительно другого в условиях отсутствия трения в плоскости трещины.
При сжатии образцов с соотношением H0/D0 = 1 разрушения не наблюдается.
Заключение и выводы. Проведенное экспериментальное исследование позволяет сделать следующие основные выводы: 1. В случае сжатия цилиндрических образцов с соотношением H0/D0 = 1.5 при деформировании со скоростью 0.001 с–1 наблюдается появление трещины на боковой поверхности образца, что не позволяет довести испытание до конечной высоты, соответствующей сжатию на 50% от исходной высоты образца, заданной при расчете программы нагружения. 2. Выявлено аномальное изменение напряжения текучести при увеличении скорости деформации, что, по всей видимости, связано с проявлением эффекта Портевена–Ле Шателье [14], требующее проведения детального металлографического исследования. 3. Соотношение исходных размеров (H0/D0) не оказывает влияние на характер кривых текучести при комнатной температуре и скоростях деформации 0.001 c–1; 0.01 c–1; 0.1 c–1; 0.22 c–1; 0.4 c–1. 4. Для обеспечения постоянной скорости деформации возможно применение методики [13], обеспечивающей расчет программы нагружения для современной универсальной испытательной машины. 5. Учитывая характеристики испытательной машины, в том числе максимальную скорость перемещения траверсы, возможен выбор соотношения H0/D0, обеспечивающего максимальную скорость деформации и соблюдение условия, накладываемого на выбор значения исходной высоты (H0) и диаметра (D0) образца. 6. Результаты проведенных испытаний и их анализ показывают, что для построения кривых текучести могут быть использованы цилиндрические образцы с соотношением H0/D0 = 1 (10/10 мм), при условии, что расчет программы нагружения и обработка результатов испытаний проводится по методикам, описанным в работах [10, 13].
Список литературы
Voce E. The relationship between stress and strain for homogeneous deformation // J. Inst. Met. 1948. V. 74. P. 537.
Szeliga D., Gawad J., Pietrzyk M. Inverse analysis for identification of rheological and friction models in metal forming // Computer methods in applied mechanics and engineering. 2006. V. 195. P. 6778.
Komurlu E. Loading rate conditions and specimen size effect on strength and deformability of rock materials under uniaxial compression // International Journal of Geo-Engineering. 2018. V. 9. Article number: 17.
Skripnyak N.V. The Features of Fracture Behavior of an Aluminum-Magnesium Alloy AMg6 Under High-Rate Straining // Russian Physics Journal. 2015. V. 58. P. 691.
Hung J.C., Lin C.C. Investigations on the material property changes of ultrasonic-vibration assisted aluminum alloy upsetting // Materials & Design. 2013. V. 45. P. 412.
Efremov D.V., Uvarov S.V., Spivak L.V., Naimark O.B. Statistical patterns of deformation localization during plastic flow in the AMg6 alloy // Lett. Mater. 2020. V. 10 (1). P. 38.
Razali M.K., Joun M.S. A new approach of predicting dynamic recrystallization using directly a flow stress model and its application to medium Mn steel // Journal of Materials Research and Technology. 2021. V. 11. P. 1881.
Charpentier P.L., Stone B.C., Ernst S.C., Thomas J.R. Characterization and Modelling of High Temperature Flow Behavior of Aluminum Alloy 2024 // Met. Trans. A. 1986. V. 17. P. 2227.
Ebrahimi R., Najafizadeh A. A new method for evaluation of friction in bulk metal forming // J. Mater Process Technol. 2004. V. 152 (2). P. 136.
Петров П.А., Матвеев А.Г., Сапрыкин Б.Ю., Петров М.А., Бурлаков И.А., Диксит У.Ш. Повышение надежности технологического процесса штамповки с кручением изделий из алюминиевого сплава // Проблемы машиностроения и надежности машин. 2021. № 4. С. 3.
Багмутов В.П., Водопьянов В.И., Кондратьев О.В., Коробов А.В. Испытания на сжатие: метод. указ. к лабораторной работе. Волгоград: ВолгГТУ, 2015. 16 с.
Papirno R., Mescall J.F., Hansen A.M. Fracture in Axial Compression Tests of Cylinders. Compression Testing of Homogeneous Materials and Composities, ASTM STP 808, Richard Chait and Ralph Papirno, Eds., American Society for Testing and Materials, 1983. P. 40.
Петров П.А., Фам В.Н., Сапрыкин Б.Ю., Диксит У.Ш. Моделирование программ монотонного нагружения с постоянной скоростью деформации на современной универсальной испытательной машине // Технология легких сплавов. 2021. № 3. С. 45.
Mogucheva A., Saenko M., Kaibyshev R. The Portevin–Le Chatelier effect in an Al-Mg alloy. AIP Conference Proceedings 1783, 2016. 020156.
Дополнительные материалы отсутствуют.
Инструменты
Проблемы машиностроения и надежности машин