Проблемы машиностроения и надежности машин, 2022, № 3, стр. 72-82
Прогнозирование остаточного срока службы гидравлического оборудования с применением методов машинного обучения
А. М. Гареев 1, Е. В. Шахматов 1, А. Б. Прокофьев 1, Д. М. Стадник 1, *
1 Самарский национальный исследовательский университет им. С.П. Королева
(Самарский университет)
Самара, Россия
* E-mail: sdm-63@bk.ru
Поступила в редакцию 22.10.2021
После доработки 09.02.2022
Принята к публикации 11.02.2022
- EDN: UHUFFS
- DOI: 10.31857/S0235711922030051
Аннотация
В настоящем исследовании предложен способ прогнозирования остаточного срока службы гидроцилиндра в составе следящего гидромеханического привода с применением искусственной нейронной сети прямого распространения, для обучения которой используются результаты моделирования, полученные в программе SimulationX в предположении, что развитие неисправности в системе происходит в соответствии с функцией распределения Вейбулла. Представлены результаты прогнозирования остаточного срока службы гидроцилиндра при различных диагностических признаках и способах задания управляющего воздействия в системе.
Современные тенденции развития гидравлических машин сопровождаются ужесточением требований в отношении надежности их агрегатов и систем. Ввиду необходимости повышения безопасности и снижения производственных потерь оценка остаточного срока службы таких систем становится все более актуальной, а многие проблемы, связанные с оценкой остаточного срока службы отдельных узлов и агрегатов, остаются нерешенными. Отказы в гидравлических системах в первую очередь могут приводить к возникновению опасных условий для человека (оператора), а также сопровождаться производственными затратами. В настоящее время в большей степени распространено техническое обслуживание по наработке, зависящее от времени, при котором замена агрегатов системы осуществляется по четко определенному графику. Однако такое техническое обслуживание имеет ряд недостатков, среди которых главным является замена агрегатов при условии, что они все еще являются исправными. В связи с этим возникает необходимость в применении подходов к техническому обслуживанию, которые позволяют вовремя обнаруживать неисправности и сокращать экономические потери. В основе таких подходов должна лежать точная технология прогнозирования, способная оценивать будущее состояние ГС на основе объективных показателей возникающей неисправности [1].
В настоящее время прогнозирование остаточного срока службы системы осуществляется с применением статистических подходов, методов моделирования процессов износа и методов искусственного интеллекта. Статистические подходы основаны на моделях распределения вероятностей отказа, для формирования которых используются данные об отказах агрегатов за прошедшие периоды. Один из таких подходов основан на использовании динамической баейсовской модели, которая позволяет представить вероятностные взаимодействия между параметрами системы и спрогнозировать развитие в ней неисправности [2]. В случае кумулятивного (интегрального) ухудшения характеристик компонента системы, можно использовать экспоненциальную стохастическую модель деградации в сочетании с методом главных компонент для сокращения размерности данных и выявления диагностических признаков, по которым осуществляется прогнозирование состояния системы [3]. Недостатком статических методов является сложная практическая реализация и необходимость большого объема базы данных отказов исследуемых компонентов системы. Прогностические методы на основе моделирования связаны с математическим описанием процессов, характеризующих развитие отказа в системе и должны достаточно точно учитывать его механику в рассматриваемом узле ГС [4]. Основная трудность при использовании такого подхода заключается в выборе физической модели. В связи с интенсивным развитием компьютерных и информационных технологий все более широкое распространение получают методы искусственного интеллекта, которые применяются как мощный инструмент во многих областях, в том числе и при решении задач по прогностическому анализу состояния ГС. Например, в работе [5] представлены результаты прогнозирования остаточного срока службы шестеренного насоса общепромышленного назначения на основе байесовской нейронной сети с использованием данных, полученных в результате ускоренных ресурсных испытаний. Используемая нейронная сеть обучена на основе диагностических признаков, извлеченных из таких характеристик как объемный расход, вибрация, крутящий момент и частота вращения с применением факторного анализа. В результате показано, что относительная погрешность в прогнозировании остаточного срока службы насоса для используемого метода составляет 1.5%. В работе [6] рассматривается подход для прогнозирования остаточного срока службы гидравлического крана-манипулятора на основе нейронной сети прямого распространения. Изучается развитие неисправностей в насосе и пропорциональном распределителе. Для обучения нейросети используются данные, полученные с помощью имитационной модели при одном и том же управляющем воздействии, которое приводит к однотипному поведению объекта в период его эксплуатации. Представлены результаты прогнозирования остаточного срока службы системы при совокупном ухудшении характеристик рассматриваемых агрегатов.
Стоит отметить, что в настоящем исследовании предлагается способ прогнозирования остаточного срока службы гидромеханического следящего привода, который находит широкое применение в дорожной и строительной технике. Главной особенностью рассматриваемой системы является наличие автомата разгрузки, обеспечивающего уменьшение потребляемой энергии насосом за счет соединения его со сливом, в то время как питание гидроусилителя (ГУ) осуществляется от пневмогидравлических аккумуляторов (ПГА). Переключения автомата разгрузки приводят к цикличности работы системы и сопровождаются колебаниями расхода и давления в диапазоне, соответствующем его настройке. Это характерное свойство в сочетании с потенциальными рисками возникновения неисправностей требует проведения подробных исследований рассматриваемой системы, которые можно выполнить на основе ее имитационного моделирования.
Расчетная модель. На рис. 1 представлена принципиальная схема следящего гидравлического привода общего промышленного назначения.
Рис. 1.
Принципиальная схема следящего гидравлического привода: 1 – бак; 2 – предохранительный клапан; 3, 6 – фильтр; 4 – автомат разгрузки насоса; 5 – ПГА; 7 – ГУ; 8 – гидроцилиндр; 9 – шток; 10 – крепление корпуса; 11 – командный золотник; 12 – привод насоса; 13 – насос.
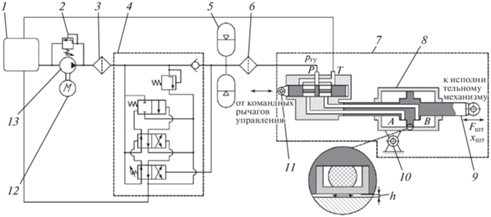
При воздействии на командный золотник 11 происходит соединение линии высокого давления Р с полостью А или B в зависимости от направления его перемещения. В результате шток 9, преодолевая внешнюю нагрузку, начинает движение вместе с корпусом и гильзой командного золотника в том же направлении, что и последний. Перемещение штока не прекращается, пока не остановится командный золотник и не будет перекрыта линия Р. Автомат разгрузки необходим для обеспечения холостого режима работы насоса при повышении давления выше настроечного в линии за ним. ПГА используются для питания ГУ в периоды, когда насос разгружен на бак. На шток гидроцилиндра (ГЦ) действует усилие, передаваемое на него от какого-либо исполнительного механизма.
Наиболее частой причиной снятия приводов с эксплуатации является нарушение герметичности полостей ГЦ [7]. Появление утечки рабочей жидкости между полостями ГЦ вследствие износа уплотнительного элемента поршня может приводить к падению эффективности его работы, снижению скорости и развиваемого усилия. Для исследования процессов в рассматриваемой системе и выявления диагностических признаков, характеризующих увеличение внутренней утечки в ГЦ, используется имитационная модель, разработанная авторами настоящего исследования и описанная в [8]. Основные данные для расчета системы приведены в табл. 1.
Таблица 1.
Исходные данные и конструктивно-настроечные параметры системы
Наименование | Символ | Значение |
---|---|---|
Рабочее давление в системе | $p$ | 4.5–6.5 МПа |
Производительность насоса при 2500 об/мин и давлении 6.5 МПа | Qн | 30 л/мин |
Ход штока ГЦ (от среднего положения) | хшт | ±35 мм |
Внешняя нагрузка, действующая на шток ГЦ | Fшт | ±15 000 Н |
Рабочая жидкость | – | АМГ-10 |
Утечка между полостями ГЦ определяется на основе выражения, описывающего ламинарное течение рабочей жидкости в кольцевом зазоре с учетом относительного движения стенок [9]. Основным параметром, влияющим на величину утечки, является зазор h между внешней поверхностью уплотнения и внутренней поверхностью ГЦ. На рис. 2 представлен график переходных процессов в системе при изменении величины зазора в уплотнительном элементе поршня ГЦ. Для имитации воздействия оператора на командный золотник ГУ используется ступенчатый сигнал с величиной “ступеньки”, задаваемой случайным образом в диапазоне от –35 до +35 мм (что соответствует рабочей величине хода штока ГЦ) с шагом в 5 с. Такое управляющее воздействие позволяет оценить работоспособность системы и выявить ее особенности.
Рис. 2.
Переходный процесс изменения положения штока ГЦ (xшт) и давления на входе в ГУ (pгу) при различных зазорах в уплотнительном элементе поршня.
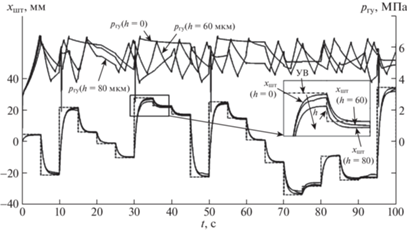
Наблюдаемые циклические колебания давления на входе в гидроусилитель характерны для рассматриваемой системы, которая включает автомат разгрузки и ПГА. Диапазон изменения давления составляет 3.8–6.5 МПа: участки с возрастающим давлением соответствуют периодам зарядки ПГА, когда насос через автомат разгрузки соединен с системой; участки с падающим давлением соответствуют периодам разрядки ПГА, которые питают ГУ, в то время как насос через автомат разгрузки соединен с баком. Случайное управляющее воздействие приводит к разному расходу рабочей жидкости, которую потребляет ГУ, вследствие чего частота колебаний давления во время переходного процесса меняется, а переключения автомата разгрузки происходят нерегулярно. Провалы по давлению (например, в моменты времени 10.5, 30, 50 и 95 с) связаны с действием на шток ГЦ попутной нагрузки в моменты резких переходов по управляющему воздействию. Анализируя влияние зазора в уплотнительном элементе поршня, можно отметить, что его увеличение приводит к более частым переключениям автомата разгрузки, т.к. давление из-за наличия утечки падает быстрее по сравнению с исправной системой. Также можно отметить уменьшение средней составляющей сигнала давления. Перемещение штока ГЦ в меньшей степени подвержено влиянию утечки по сравнению с давлением. Это можно объяснить наличием переразмеренных источников расхода рабочей жидкости в рассматриваемой системе (насос и ПГА), обеспечивающих питание ГУ с большим запасом. Тем не менее, изменение зазора сказывается и на положении штока в моменты его остановки. Это можно объяснить следующим образом. С остановкой командного золотника шток также прекращает движение, но не достигает заданной величины из-за уменьшения давления в полости ГЦ: утечка приводит к падению давления, следовательно, усилие, развиваемое ГЦ, становится меньше. Из условия баланса сил – меньшему усилию со стороны ГЦ соответствует меньшая внешняя сила. Так как в качестве внешнего воздействия рассматривается сила пружины, то при своей постоянной жесткости упругая сила может уменьшиться только в случае уменьшения ее деформации. В связи с этим можно отметить, что с увеличением величины зазора возрастает статическая ошибка регулирования положения штока ГЦ.
Из анализа полученных результатов следует, что давление в системе и перемещение штока ГУ не только адекватно и однозначно характеризуют свойства исследуемой системы, но и могут быть легко измерены в реальной установке. В связи с этим целесообразно выбрать диагностические признаки рассматриваемой неисправности с использованием измеренных параметров. Таким образом, для прогнозирования развития внутренней утечки в ГЦ в качестве диагностических признаков можно принять среднее квадратичное перемещения штока и среднее значение давления на входе в ГУ.
Закон развития неисправности в системе. Типичную деградацию агрегата можно описать кривой, имеющей два участка: первый – в котором состояние агрегата практически не изменяется; второй – после появления неисправности происходит резкое ухудшение состояния агрегата [10]. Как отмечено в работах [11, 12] распределение Вейбулла можно рассматривать не только для оценки вероятности наступления случайных событий, но и для описания развития неисправности в системе. Согласно работе [13] функция распределения Вейбулла является наиболее “гибкой” для описания процесса деградации агрегатов ГС. На основе формулы, определяющей интенсивность отказов в соответствии с функцией распределения Вейбулла, можно записать обобщенную или универсальную функцию интенсивности отказов, используемую для аппроксимации экспериментальных данных, описывающих деградацию элементов системы [6]
где t – наработка до отказа (фактический срок службы); $\lambda $ – коэффициент масштаба; k – коэффициент формы; Y – параметр смещения, характеризующий начальное состояние изделия; X – параметр для изменения масштаба.Изменяя значения параметров Y, X, $\lambda $ и k, представляется возможным аппроксимировать экспериментальные данные, получаемые из исследуемой системы с учетом различных условий эксплуатации. На рис. 3 представлен график с зависимостями изменения величины зазора в уплотнительном элементе поршня ГЦ, рассчитанными по формуле (2) с шагом наработки t = 100 ч при изменении параметров Y, X, $\lambda $ и k (табл. 2).
Рис. 3.
Кривые изменения средней высоты зазора между уплотнением поршня и внутренней поверхностью ГЦ в зависимости от его наработки: 1–10 – номера кривых, рассчитанных в соответствии с параметрами в табл. 2.
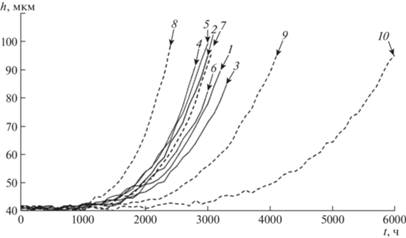
Таблица 2.
Значения коэффициентов уравнения (2), используемые для расчета точек кривых на рис. 3
№ кривой | X | $\lambda $ | k | № кривой | X | $\lambda $ | k |
---|---|---|---|---|---|---|---|
1 | 0.5 | 1400 | 5.0 | 6 | 0.55 | 1350 | 4.8 |
2 | 0.5 | 1300 | 5.0 | 7 | 0.69 | 1460 | 5.2 |
3 | 0.4 | 1400 | 5.0 | 8 | 2 | 1460 | 5.2 |
4 | 0.5 | 1300 | 5.2 | 9 | 0.2 | 1460 | 5.2 |
5 | 0.6 | 1300 | 4.9 | 10 | 0.08 | 1800 | 5.5 |
Приведенные параметры могут характеризовать изменение зазора в зависимости от наработки ГЦ при различных условиях эксплуатации, например, при изменении температуры жидкости или при наличии загрязненной жидкости в системе.
В связи с этим кривые отличаются скоростью роста и временем начала деградации. Учитывая, что реальные экспериментальные данные могут содержать различного рода погрешности, в результаты расчетов дополнительно включена шумовая составляющая.
Исправное состояние ГЦ характеризуется значениями среднего зазора, находящихся в диапазоне от 40 до 43 мкм (hmin = Y). После начала эксплуатации износ в уплотнительных элементах ГЦ происходит по различным сценариям. Процесс износа продолжается до момента времени, когда величина зазора становится равной 100 мкм (${{h}_{{\max }}}$), что соответствует состоянию отказа ГЦ в рассматриваемой системе. Исходя из этого, можно вывести формулу для оценки остаточного срока службы в зависимости от величины среднего зазора в процентах
(3)
$RUL = 100\left( {1 - \frac{{h(t) - {{h}_{{\min }}}}}{{{{h}_{{\max }}} - {{h}_{{\min }}}}}} \right).$Несмотря на то, что полученное выражение представляет собой прямую зависимость RUL от зазора, состояние гидроцилиндра меняется не линейно, а в соответствии с одной из кривых Вейбулла. Таким образом, рассчитанные кривые представляют собой совокупность значений зазора, которые можно подставить в имитационную модель для получения обучающих выборок. То есть каждая точка кривой представляет собой частный расчетный случай, в результате которого определяются значения диагностических признаков, используемых в качестве обучающих данных для нейронной сети.
Настройка нейронной сети и генерация обучающих выборок. Принимая во внимание нелинейность решаемой задачи, в качестве инструмента для прогнозирования остаточного срока службы ГЦ в рассматриваемой системе используется искусственная двухслойная нейронная сеть прямого распространения с сигмоидальной функцией активации нейронов скрытого слоя и линейной функцией активации нейронов выходного слоя. Выходным сигналом нейронной сети является значение остаточного срока службы ГЦ, а входным – набор данных, включающих рассмотренные ранее диагностические признаки. Реальные данные для обучения НС можно получить как при выполнении тестовых манипуляций, так и собрать непосредственно в процессе эксплуатации. В связи с этим в качестве входной информации для нейронной сети предлагается использовать два независимых набора данных.
Для получения первого набора данных в качестве управляющего воздействия рассматривается трапециевидный сигнал с постоянной амплитудой, соответствующей максимальному ходу штока ГЦ. Данный сигнал является относительно простым по форме, и легко реализуем на практике. В реальных условиях этот сигнал можно получить при выполнении тестовых манипуляций оператора, когда последний воздействует на органы управления, добиваясь однотипных движений исполнительного механизма. Так как в настоящем исследовании для обучения и тестирования нейронной сети предполагается использовать данные имитационного моделирования, описанный выше сигнал УВ используется в каждой симуляции (расчетном случае) при изменении величины зазора в уплотнительном элементе в соответствии с кривыми Вейбулла. В качестве диагностического признака в данном случае принимается среднее квадратичное значение перемещения штока за время интегрирования, которое в каждом расчетном случае составляет 120 с.
В реальных условиях эксплуатации рассматриваемой системы, воздействия оператора на командный золотник ГУ являются трудно прогнозируемыми и в какой-то степени их можно описать как случайный процесс. В связи с этим для формирования второго набора данных в качестве управляющего воздействия можно использовать случайный ступенчатый сигнал с величиной “ступеньки”, лежащей в диапазоне от ‒35 мм до +35 мм. При этом сигнал для каждого расчетного случая не повторяется в отличие от первого набора данных (рис. 2). В качестве диагностического признака в данном случае принимается среднее значение давления на входе в ГУ за время интегрирования, которое в каждом расчетном случае составляет 2000 с. Время интегрирования для получения второго набора данных значительно больше, чем в первом случае, т.к. используется более сложный сигнал.
На рис. 4 представлены графики изменения средних квадратичных значений перемещения штока ГЦ и средних значений давления на входе в ГУ, полученных при одних и тех же эволюциях неисправности в соответствии с кривыми Вейбулла, но при различных способах задания управляющего воздействия.
Рис. 4.
Кривые изменения средних квадратичных значений перемещения штока ГЦ (а) и средних значений давления на входе в ГУ (б): 1–10 – номера кривых, полученных при изменении зазора в соответствии с зависимостями на рис. 3.
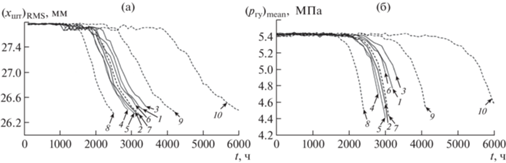
Из анализа полученных графиков следует, что диагностические признаки практически не изменяются с наработкой, пока зазор в уплотнительном элементе сохраняется постоянным. После появления неисправности, рассматриваемые значения начинают уменьшаться, достигая критических значений, соответствующих полному отказу. Также с увеличением зазора в уплотнительном элементе ГЦ среднее давление уменьшается, и эта тенденция сохраняется, несмотря на случайный способ задания управляющего воздействия.
Полученные графики представляют собой количественные характеристики диагностических признаков и используются в качестве информации, подаваемой на вход нейросети. При этом необходимо создать и обучить две независимые нейронные сети в соответствии с первым и вторым набором данных. Разработанные сети в обоих случаях имеют одинаковый выход, т.е. предсказывают RUL. В качестве входа для обеих сетей используются значения наработки и соответствующего диагностического признака. Для того чтобы ввести динамическую составляющую в данные сети и тем самым улучшить их способность к прогнозированию, на вход необходимо подавать как текущие значения параметров, так и значения с предыдущего шага [6]. Шаг наработки, с которым подаются данные для обучения, проверки и тестирования нейронной сети, как и в случае моделирования, составляет 100 ч. Таким образом, входом каждой сети является матрица размерностью [4 × N], а выходом [1 × N], где N – общее количество точек обучающей выборки (samples). В качествe обучающего набора данных используются значения кривых (рис. 4), обозначенные на графиках сплошными линиями, и целевые значения остаточного срока службы, рассчитываемые по формуле (3).
Обучение нейронной сети и результаты прогнозирования. Для обучения НС используется метод обратного распространения ошибки, которая минимизируется на основе алгоритма градиентного спуска. Исходный обучающий набор данных разделяется на выборки для обучения, проверки (валидации) и тестирования в соотношении 70%, 15% и 15% соответственно. Количество нейронов для скрытого слоя подбирается опытным путем на основе анализа показателей качества обучаемой нейронной сети, к которым относятся среднеквадратичная ошибка и гистограмма распределения ошибок.
При обучении нейронной сети на первом наборе данных, полученных при тестовых воздействиях, среднеквадратичная ошибка составляет 0.25, а максимальная разница между истинными значениями RUL и предсказанными составляет 3%. При обучении нейронной сети на втором наборе данных, полученных для управляющего воздействия в виде случайного ступенчатого сигнала, среднеквадратичная ошибка составляет 4.38, а максимальная разница между истинными значениями RUL и предсказанными составляет 4.2%. Полученные результаты указывают на лучшую способность НС к обучению на данных, полученных при управляющих воздействиях в виде трапециевидного сигнала.
Для тестирования обученных нейронных сетей используются данные, соответствующие кривым 7, 8, 9 и 10 (рис. 4). На рис. 5 представлены графики изменения предсказанных и истинных значений остаточного срока службы ГЦ при его наработке на тестовых данных.
Рис. 5.
График изменения предсказанных и истинных значений RUL для НС, обученной на основе средних квадратичных значений перемещений штока ГЦ (хшт)RMS (а) и для НС, обученной на основе средних значений давления на входе в ГУ (pгу)MEAN (б): 8–10 – номера кривых, соответствующих зависимостям 8–10 на рис. 4.
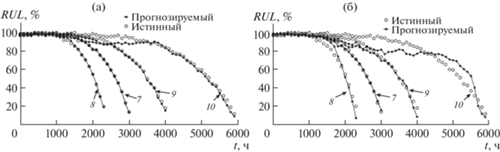
Из анализа полученных результатов следует, что наибольшие абсолютные отклонения предсказанных значений RUL от истинных наблюдаются в часы наработки, которые соответствуют возникновению неисправности в ГЦ, когда значения диагностических признаков начинают уменьшаться быстрее. Ошибка может быть связана с резким изменением производной диагностического признака, как функции по наработке. Результаты тестирования нейросети, обученной по набору данных в виде средних значений давления на входе в ГУ (pгу)MEAN, имеют более существенные расхождения между прогнозируемыми и истинными значениями RUL по сравнению с результатами тестирования нейронной сети, обучаемой на основе средних квадратичных значений перемещения штока ГЦ (хшт)RMS. Причиной является способ задания управляющего воздействия, который используется для генерации данных. Случайный ступенчатый сигнал создает более сложные условия для нейронной сети при обобщении данных по сравнению с управляющим воздействием в виде трапециевидного сигнала с постоянной амплитудой. При этом в обоих случаях максимальные расхождения получены для кривой 10, наиболее удаленной от ансамбля кривых, используемых в обучении. На рис. 6 представлен график изменения относительной погрешности прогнозирования RUL (ΔRUL) в соответствии с набором данных, относящихся к кривой 10.
Рис. 6.
График изменения относительной погрешности прогнозирования RUL по тестовому набору 10 для обученных НС: НС 1 – на основе средних квадратичных значений перемещения штока ГЦ; НС 2 – на основе средних значений давления на входе в ГУ.
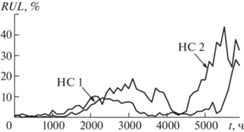
Как видно из графика, для большей части срока эксплуатации, максимальное значение относительной погрешности прогнозирования RUL с использованием нейронной сети, обученной на основе диагностического признака (хшт)RMS, не превышает 10%, а для нейронной сети, обученной на основе диагностического признака (pгу)MEAN, – 20%. Возрастание относительной погрешности в конце срока службы для обеих нейронных сетей может указывать на недостаточное количество данных (точек), собираемых для этого периода, характеризующих наступление полного отказа ГЦ.
Полученные результаты указывают на то, что обучение НС на данных, которые можно собрать непосредственно в условиях эксплуатации, когда имеет место неопределенное (случайное) воздействие на систему, в целом является выполнимой задачей при условии выбора подходящего диагностического признака. Нейросеть, обученная на основе данных, полученных путем тестовых манипуляций, дает меньшую ошибку в прогнозировании ввиду относительно простого вида управляющего воздействия. Использование в качестве обучающих выборок непосредственно временных сигналов протекающих в системе процессов (а не извлеченных из них интегральных характеристик) может значительно повысить точность прогнозирования, но требует использования нейронных сетей более сложной структуры.
Заключение. В настоящей статье продемонстрирована возможность применения технологий машинного обучения для диагностирования сложных технических систем на примере прогнозирования остаточного срока службы ГЦ в составе гидравлического следящего привода. Как показывают результаты теоретических исследований, диагностические признаки на основе сигналов перемещения штока ГЦ и давления на входе в ГУ однозначно характеризуют процесс развития внутренней утечки в ГЦ и их можно использовать при обучении нейронной сети с целью прогнозирования остаточного срока службы системы. Диагностические признаки в виде уменьшения средних значений давления на входе в ГУ проявляются при управляющем воздействии в виде случайного ступенчатого сигнала, в связи с чем могут быть использованы для обучения нейронной сети на основе данных, собираемых непосредственно в процессе эксплуатации системы. Предложенный подход можно применять при проектировании систем прогностического анализа гидравлических приводов, используемых в транспортных и технологических машинах.
Дальнейшие исследования будут направлены на определение подходящей модели нейронной сети с целью прогнозирования остаточного срока службы системы при одновременном возникновении сразу нескольких неисправностей.
Список литературы
Jardine A.K.S., Lin D., Banjevic D. A review on machinery diagnostics and prognostics implementing condition-based maintenance // Mechanical Systems and Signal Processing. 2006. V. 20 (7). P. 1483.
Xu B., Li H., Pang W., Chen D., Tian Y., Lei X., Gao X., Wu C., Patelli E. Bayesian network approach to fault diagnosis of a hydroelectric generation system // Energy Science and Engineering. 2019. V. 7 (5). P. 1669.
Anis M.D. Towards Remaining Useful Life Prediction in Rotating Machine Fault Prognosis: An Exponential Degradation Model // Condition Monitoring and Diagnosis, CMD 2018. https://doi.org/10.1109/CMD.2018.8535765
Zhao F., Tian Z., Liang X., Xie M. An Integrated Prognostics Method for Failure Time Prediction of Gears Subject to the Surface Wear Failure Mode // IEEE Transactions on Reliability. 2018. V. 67 (1). P. 316.
Guo R., Li Y., Zhao L., Zhao J., Gao D. Remaining Useful Life Prediction Based on the Bayesian Regularized Radial Basis Function Neural Network for an External Gear Pump // IEEE Access. 2020. V. 8. P. 107498.
Ghini Y., Vacca A. A method to perform prognostics in electro-hydraulic machines: the case of an independent metering controlled hydraulic crane // Int. J. Hydromechatronics. 2018. V. 1 (2). P. 197.
Алексеева Т.В., Бабанская В.Д., Башта Т.М. и др. Техническая диагностика гидравлических приводов / Под общей ред. Т.М. Башты. Москва: “Машиностроение”, 1989. 264 с.
Гареев А.М., Гимадиев А.Г., Стадник Д.М., Попельнюк И.А. Определение динамической погрешности измерения параметров электрогидромеханических систем с учётом быстродействия датчиков // Вестник Самарского университета. Аэрокосмическая техника, технологии и машиностроение. 2020. Т. 19. № 2. С. 85.
Башта Т.М. Машиностроительная гидравлика. Москва: “Машиностроение”, 1971. 672 с.
Moubray J. Reliability-centered maintenance, 2nd ed. Oxford 1997: Butterworth Heinemann. Oxford.
Kuhlhoff R., Orth A., De Negri V., Moreno U.A. Application of Weibull reliability model for functional safety of electro-hydraulic system // IFK2018, Aachen, March. 2018.
Lorenzoni A., Kempf M. Degradation processes modelled with dynamic Bayesian networks // IEEE 13th International Conference on Industrial Informatics (INDIN), IEEE. 2015. P. 1694.
Kuhlhoff I.R. Method for application of Weibull distribution to the reliability calculation of functional safety for industrial machinery // Engineering. 2014. https://repositorio.ufsc.br/xmlui/handle/123456789/132745
Дополнительные материалы отсутствуют.
Инструменты
Проблемы машиностроения и надежности машин