Проблемы машиностроения и надежности машин, 2023, № 1, стр. 58-67
Влияние термической обработки на микроструктуру и механические свойства сплава ЭП648, полученного методом селективного лазерного плавления
Д. Ю. Финогеев 1, *, О. П. Решетникова 1
1 Саратовский государственный технический университет им. Гагарина Ю.А.
Саратов, Россия
* E-mail: daniil.sstu@gmail.com
Поступила в редакцию 21.03.2022
После доработки 12.10.2022
Принята к публикации 20.10.2022
- EDN: ASOAIZ
- DOI: 10.31857/S0235711923010042
Аннотация
В статье представлен комплекс исследований жаропрочного сплава на никелевой основе ЭП648, полученного методом селективного лазерного плавления с последующим высокотемпературным отжигом. Проведены исследования макро- и микротвердости, анализ микроструктуры и испытания образцов на сопротивление хрупкому разрушению. Выполненный количественный и качественный анализ свидетельствуют о возможных структурных отклонениях, влияющих на свойства изготавливаемых изделий.
В настоящий момент технология селективного лазерного плавления (SLM) широко применяется в мире для изготовления металлических изделий различного применения. Относительно традиционных методов изготовления деталей SLM имеет ряд преимуществ, таких как: возможность изготовления деталей сложной формы и конфигурации, быстрое изготовление мелкой серии изделий готовых к применению, минимальное количество производственных остатков [1]. Однако в настоящий момент производственный процесс селективного лазерного плавления включает большое количество параметров, что затрудняет оптимизацию и повторяемость процесса производства изделий для каждого нового материала и сплава [2]. К таким параметрам можно отнести показатели, участвующие в синтезировании деталей (мощность лазерного излучения, скорость и шаг сканирования, равномерность распределение температуры и т.д.) и параметры условий термической обработки (максимальная температура нагрева, время выдержки, скорость нагрева и охлаждения) [3]. Перечисленные критерии являются наиболее важными и напрямую влияют на характеристики изделия.
При производстве изделий с высокими физико-механическими требованиями применяют хромоникелевые, кобальт-хромовые и титановые сплавы. Так, например за рубежом учеными были достаточно изучены некоторые сплавы данного типа: Inconel 625, Inconel 718, CM247LC, CMX486 [4]. Исследования свидетельствуют о важности технологических параметров производства на физико-механические и структурные свойства получаемых изделий [5]. В настоящий момент предприятия, использующие технологию SLM, заинтересованы в применении жаропрочных металлопорошковых композиций (МПК). В частности, большой интерес представляют жаропрочные сплавы с высоким содержанием никеля и хрома. Этот факт актуализирует вопрос изучения и выявления нюансов технологии производства деталей из жаропрочных хромоникелевых сплавов методом селективного лазерного плавления.
Целью настоящей статьи являлось исследование влияния режимов термической обработки на структуру и физико-механические свойства образцов из жаропрочного сплава на никелевой основе ЭП648, полученного методом селективного лазерного плавления.
Материалы и методы. В качестве объекта исследования взят жаропрочный сплав марки ЭП648 (ХН50ВМТЮБ) на никелевой основе с высоким содержанием хрома, химический состав которого приведен в табл. 1 и соответствует требованиям ТУ 1-595-16-1260-2011 [6]. Был проведен спектральный анализ, использующий зависимость интенсивности спектральных линий от содержания элементов в образце. Анализ выполняли в спектрометре ДФС-51 “СЛ” на соответствие массовой доле присутствующих химических элементов.
Таблица 1.
Химический состав сплава ХН50ВМТЮБ (ЭП648), % мас., Ni – основа
Данные | Cr | Al | Ti | Nb | Mo | Mn | Fe |
---|---|---|---|---|---|---|---|
ТУ 1-595-16-1260-2011 | 32–35 | 0.5–1.1 | 0.5–1.1 | 0.5–1.1 | 2.3–3.3 | ≤0.5 | ≤4 |
W | C | S | P | Si | B | Ce | |
4.3–5.3 | ≤0.1 | ≤0.01 | ≤0.015 | ≤0.4 | ≤0.008 | ≤0.03 | |
Спектральный анализ | Cr | Al | Ti | Nb | Mo | Mn | Fe |
33.5 | 0.85 | 0.91 | 0.89 | 3.1 | 0.26 | 2.3 | |
W | C | S | P | Si | B | Ce | |
4.93 | 0.09 | 0.008 | 0.098 | 0.32 | 0.007 | 0.029 |
Для производства образцов взят фракционный состав порошка 10–63 мкм, полученный методом газовой атомизации. Печать образцов проводили на установке селективного лазерного плавления “SLM Solutions 280” в атмосфере азота. Оптимальные режимы и стратегия синтеза выбраны на основании существующих рекомендаций, табл. 2 [7–9].
Таблица 2.
Параметры режимов и стратегий синтеза образцов
Мощность лазера, Вт |
Скорость сканирования, мм/с | Интервал сканирования, мкм | Толщина слоя, мкм | Диаметр лазерного луча, мкм | Стратегия сканирования |
---|---|---|---|---|---|
200 | 1100 | 87.5 | 70 | 80 | шахматная |
Для выполнения исследования структурных и физико-механических характеристик были изготовлены образцы для испытания на ударную вязкость (рис. 1а). Выращивание образцов производилось по подготовленной 3D-модели, форма и размеры которой соответствуют ГОСТ 9454-78 [10] (рис. 1б).
Рис. 1.
Образцы для исследования: (а) – выращенные на установке селективного лазерного плавления; (б) – CAD 3D-модель.
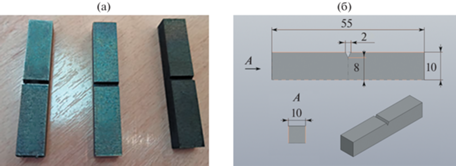
Печать выполнялась под углом 45° относительно платформы построения (рис. 2а). Расположение и направление роста образцов выбрано таким образом чтобы добиться максимально возможных физико-механических характеристик от материала (рис. 2а, б) [11].
Рис. 2.
Расположение образцов относительно платформы построения: (а) – в декартовой системе координат; (б) – серии образцов и поддерживающей структуры при подготовке управляющей программы.
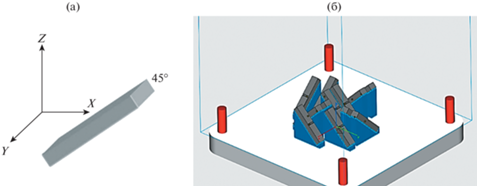
После синтезирования образцы были подвергнуты термической обработке в защитной (аргон) и воздушной средах. Для выполнения исследования было отобрано три образца. Первый образец не был подвергнут термической обработке. Второй образец был подвергнут высокотемпературному отпуску при температуре 600 ± 15°С в воздушной среде. Термообработка третьего образца проводилась в инертной среде аргона при температуре 600 ± 15°С.
Для получения более обширной информации о поведении структуры материала было выполнено исследование параметров макротвердости и микротвердости по предварительно выбранным участкам образца. Точки для замеров подбирались согласно ГОСТ 9450-76 [12]. Измерение макротвердости выполнялось от поверхности и в срезе 1 мм материала. Измерение параметров микротвердости выполнялось в перпендикулярном сечении образца относительно треков сплавления (рис. 3а). Определение макротвердости производилось на твердомере ТК-2М. Микротвердость определялась на приборе ПМТ-3М.
Рис. 3.
Пробоподготовка образцов: (а) – схема сечений исследуемых синтезированных образцов; (б) – подготовленный срез толщиной 2 мм.
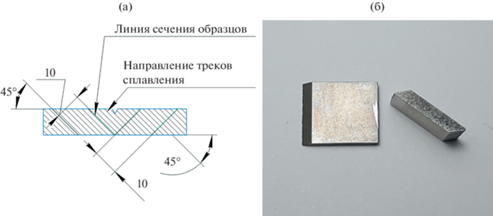
Микроструктурный анализ выполнялся на срезах материала каждого образца в двух сечениях перпендикулярно и параллельно трекам сплавления (рис. 3а, б). Учитывая направление выращивания каждого образца, была выполнена выборка срезов на расстоянии 10 мм друг от друга (рис. 3а).
Подготовленные шлифы были подвергнуты электрохимическому травлению в растворе бихромата калия в ортофосфорной кислоте. Изучение структуры и элементного состояния синтезированного образца после травления выполнено на растровом электронном микроскопе РЭМ/ЭДРА “Aspex Explorer”.
Рентгенофазовый анализ (РФА) образцов осуществляли на дифрактометре ARLX’TRA “Thermo Fisher Scientific” (Швейцария) методом рентгеновской дифракции в излучении Cu–Kα с длиной волны λ = 0.154178 нм в интервале 5–90°. Результаты РФА приведены на рис. 4.
Результаты и обсуждение. Энергодисперсионный (ЭДРА) анализ трех образцов приведен на рис. 5 и подтверждает, что распределение основных и легирующих элементов равномерно и их отношение количественно близко друг к другу (рис. 5а–в), что свидетельствует об удовлетворительном качестве печати [13, 14].
Рис. 5.
Энергодисперсионный рентгеновский анализ (ЭДРА) образцов 1–3: (а) – образец 1 без термической обработки; (б) – образец 2 с термической обработкой на воздухе; (в) – образец 3 с тремической обработкой в среде аргона.
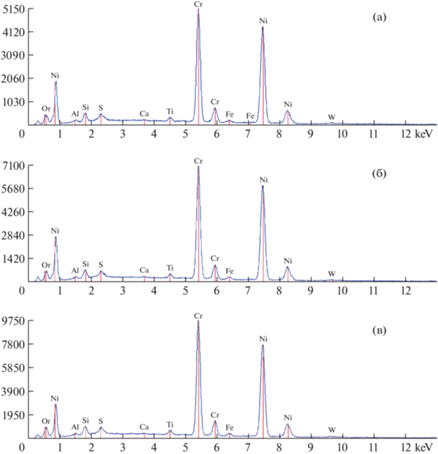
Рентгенофазовый анализ образца 3 показал наличие основных и упрочняющих фаз в исследуемом материале. В сплаве формируется преобладание ГЦК γ-фазы Fe–Ni, которой принадлежат линии {111} (на 2Θ ~ 43.1°), {200} (на 2Θ ~ 50.1°) и {220} (на Θ ~ 74.9°). Также в структуре материала образца различимы ОЦК α-фазы Fe–Сr, которой принадлежат линии {110} (на 2Θ ~ 44.1°), {200} (на 2Θ ~ 64°) и {211} (на 2Θ ~ 82.1°) (рис. 4). Показатели РФА для образцов 1 и 2 имеют аналогичные характеристики с образцом 3 с минимальным расхождением по интенсивностям рефлексов [15, 16].
Выполненный анализ микротвердости материала показал, что твердость отдельных участков микроструктуры материала образцов распределена неравномерна. Показатели микротвердости снижаются от поверхности к внутреннему объему – сердцевине образца (рис. 6б).
Рис. 6.
Измерение микротвердости: (а) – схема расположения точек измерения микротвердости; (б) – график показателей микротвердости исследуемых образцов.
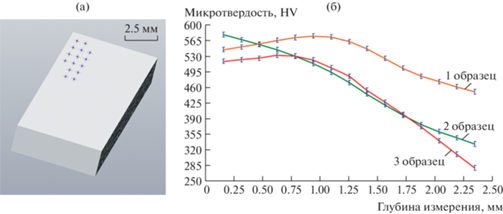
Для подтверждения зависимости снижения твердости материала были выполнены замеры макротвердости (рис. 7) на поверхности (корке) и в срезе 1 мм материала образца. Наилучший результат показал образец 3, подвергнутый термической обработке в среде аргона.
Рис. 7.
Измерение макротвердости: (а) – массив точек измерения макротвердости; (б) – график показателей твердости исследуемых образцов, где: 1, 2, 3 – измерения на поверхности (корке) образцов; 1.1, 2.1, 3.1 – измерения в толще материала, в срезе 1 мм.
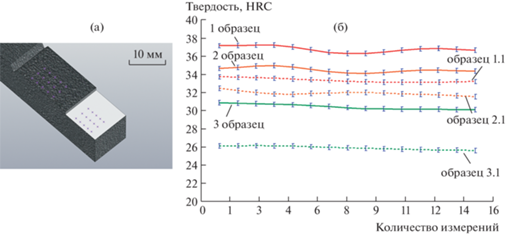
Полученные результаты подтверждают, что значения твердости материала в значительной степени зависят от термической обработки. Также анализ подтвердил, что технологический этап высокотемпературного отпуска является наиболее важным в изготовлении изделий методом селективного лазерного плавления, так как напрямую влияет на стабилизацию структуры материала.
Микроструктура синтезированных образцов представлена на рис. 8. На фотографиях отображена типичная для данного сплава структура. На рис. 8а показаны срезы треков сплавления. В большей части объема отдельных треков наблюдаются включения, поры и субструктура (рис. 8б–г). Субструктура представляет собой обрамленные скоплениями ячейки. Направление ячеек сплава выражено как равноосной, так и столбчатой морфологией (рис. 8д). Такое расположение зависит от ориентации субзерен внутри трека сплавления при направлении теплоотвода и стартовой зоны кристаллизации [14].
Рис. 8.
Микроструктура образцов ЭП648, полученных методом SLM: (а) – пространственное строение микроструктуры синтезированного материала; (б)–(г) – несплошности на границах зерен в плоскости синтеза; (д) – микроструктура строения зерен в плоскости синтеза; (е) – субзерна на границах стыка треков.
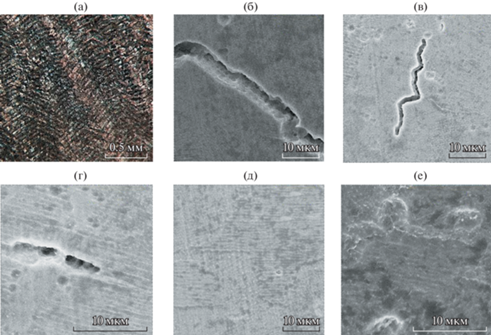
Формирование направления кристаллизации структуры трека при сплавлении МПК основной строй кристаллизации следует за фокусным пятном лазера, это обеспечивает теплоотвод как по длине движения трека, так и в предыдущий слой сплавленного материала. При формировании профиля оплавления лунки зарождаются субзерна (рис. 8е) в противоположных направлениях от трека сплавленного материала. Данный процесс инициирует появление субграниц ячеек. Именно по этим субграницам образуются структурные трещины, часто проходящие через несколько треков сплавления (рис. 8б, в, г). Этот процесс характерен литейным и ограниченно свариваемым сплавам [17].
Наличие несплошностей микроструктуры образцов 1–3 коррелирует в зависимости от вида и степени термической обработки (рис. 9а–в). Наличие повышенной пористости первого образца без ТО значительно отличается (в 3–4 раза) от образцов 2 и 3 с высокотемпературным отпуском. Таким образом, термическая обработка способствует рекристаллизации и уплотнению структуры материала.
Рис. 9.
Микроструктура образцов с разной термической обработкой: (а) – синтезированный образец без термической обработки; (б) – образец с термической обработкой на воздухе; (в) – образец с термической обработкой в инертной среде аргона.
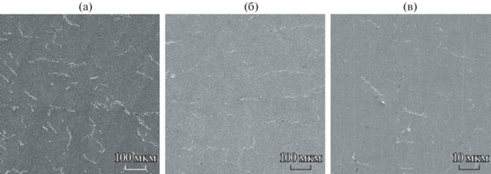
Для оценки качества механических свойств полученных образцов были проведены испытания на сопротивление хрупкому разрушению по ГОСТ 9454-78 [18]. Полученные результаты приведены в табл. 3. Для сравнения приведен показатель ударной вязкости образца, полученного методом пластической деформации – ковки [19].
Таблица 3.
Механические свойства сплава ЭП648 с различной термической обработкой
Метод изготовления | Температурные режимы ТО, °С | Температура испытания t°С | Ударная вязкость (среднее значение), КСV, Дж/см2 |
---|---|---|---|
Пластическая деформация | 880–920 | 20 | 92.50 |
SLM + без ТО (1 образец) | – | 42.33 | |
SLM + ТО, воздух (2 образец) | 600 ± 5 | 47.13 | |
SLM + ТО, аргон (3 образец) | 600 ± 5 | 56.93 |
Анализ табл. 3 показывает, что термическая обработка образцов в значительной степени положительно влияет на способность материала воспринимать динамические нагрузки. Полученные показатели ударной вязкости свидетельствуют о снижении внутренних напряжений в образце в зависимости от термической обработки. Наилучший результат показал третий образец, подвергнутый высокотемпературному отпуску в среде инертного газа аргона.
Выводы. 1. Выполнен анализ влияния режимов термической обработки на структуру и физико-механические свойства образцов из жаропрочного сплава на никелевой основе ЭП648, полученного методом селективного лазерного плавления. Показано, что высокотемпературный отпуск в значительной степени влияет на структурные и физико-механические свойства изделия, полученного методом селективного лазерного плавления. 2. Анализ микротвердости материала марки ЭП648 показал, что твердость синтезированных образцов неравномерно распределена по структуре материала и в значительной степени зависит от способа термической обработки. Наилучший результат испытаний показал образец 3, подвергнутый высокотемпературному отпуску в срезе аргона. 3. Выполненный анализ микроструктуры показал наличие большого кол-ва несплошностей в поле SLM-печати образцов. Наличие повышенной пористости первого образца без ТО значительно отличается (в 3–4 раза) от образцов 2 и 3 с высокотемпературным отпуском. Таким образом, термическая обработка способствует рекристаллизации и уплотнению структуры материала. 4. Испытания на сопротивление хрупкому разрушению, подтвердили, что влияние качественной термической обработки образцов в значительной степени влияет на снижение внутренних напряжений в структуре материала.
Список литературы
Гибсон Я., Розен Д., Стакер Б. Технологии аддитивного производства. Пер. с англ. И.В. Шишковского. М.: Техносфера, 2020. 646 с.
Петров И.М. Основные тенденции российского рынка металлических порошков для аддитивных технологий // Аддитивные технологии. 2019. № 1. С. 24.
Евгенов А.Г., Рогалев A.M., Карачевцев Ф.Н., Мазалов И.С. Влияние горячего изостатического прессования и термической обработки на свойства сплава ЭП648, синтезированного методом селективного лазерного сплавления // Технология машиностроения. 2015. № 9. С. 11.
Baitimerov R.M., Lykov P.A., Gu D. et al. Selective laser melting of nickel base heat resistance alloy EP648 // Proceedings of the Int. Conf. on Progress in Additive Manufacturing. 2016. V. 2. P. 445.
Каблов Е.Н., Евгенов А.Г., Мазалов И.С. и др. Структура и свойства синтезированных методом селективного лазерного сплавления сплавов ЭП648 и ВЖ159 после имитационных отжигов // Материаловедение. 2020. № 6. С. 3. https://doi.org/10.31044/1684-579X-2020-0-6-3-10
Новые стандарты в области аддитивных технологий – РОССТАНДАРТ, 2020 [Электронный ресурс] URL: https://www.rst.gov.ru/portal/gost/home/presscenter/news
Min P.G., Vadeev V.E., Rogalev A.M., Knyazev A.E. The investigation of the chemical composition, structure, and mechanical properties of EP648 alloy at different stages of additive manufacturing // Inorg. Mater. 2019. V. 10. P. 906.
Каблов Д.Е., Сидоров В.В., Мин П.Г., Пучков Ю.А. Влияние поверхностно-активных примесей и добавки лантана на структуру и свойства монокристаллического жаропрочного никелевого сплава ЖС36 // Труды ВИАМ. 2017. № 4 (52). С. 2. https://doi.org/10.18577/2307-6046-2017-0-4-2-2
Каталог продукции – ВИАМ, 2022 [Электронный ресурс] URL: https://catalog.viam.ru/catalog/khn50vmtyub-ep648/poroshok-iz-zharoprochnogo-nikelevogo-splava-marki-khn50vmtyub-ep648/
ГОСТ 9454-78 Метод испытания на ударный изгиб при пониженных, комнатной и повышенных температурах [Электронный ресурс] URL: https://docs.cntd.ru/document/1200005045
Gibson I., Shi D. Material properties and fabrication parameters in selective laser sintering process // Rapid Prototyping J. 1997. V. 3. № 4. P. 129.
ГОСТ 9450-76 Измерение микротвердости вдавливанием алмазных наконечников [Электронный ресурс] URL: https://docs.cntd.ru/document/1200012869
Сухов Д.И., Мазалов П.Б., Неруш С.В., Ходырев Н.А. Влияние параметров селективного лазерного сплавления на образование пористости в синтезированном материале коррозионностойкой стали // Труды ВИАМ. 2017. № 8 (56). С. 4. https://doi.org/10.18577/2307-6046-2017-0-8-4-4
Shifeng W. et al. Effect of molten pool boundaries on the mechanical properties of selective laser melting parts // J. of Materials Processing Technology. 2014. № 214. P. 2660.
Финогеев Д.Ю., Решетникова О.П., Викулова М.А., Пичхидзе С.Я. Исследование фазового состояния жаропрочного сплава ЭП648, полученного методом селективного лазерного сплавления // “Молодежь и XXI век-2022” Материалы XII Международной молодежной научной конференции в 4 т., Курск, 17–18 февраля 2022 года. Курск: Юго-Западный государственный университет, 2022. С. 205.
Финогеев Д.Ю., Войко А.В., Решетникова О.П., Костин К.Б., Пичхидзе С.Я. Влияние процессов селективного лазерного плавления на структуру жаропрочного сплава ЭП648 // Перспективы развития технологий обработки и оборудования в машиностроении: Сборник научных статей 7-й Всероссийской научно-технической конференции с международным участием, Курск, 10–11 февраля 2020 года. Курск: Юго-Западный государственный университет, 2022. С. 203.
Каблов Е.Н., Евгенов А.Г., Оспенникова О.Г. и др. Металлопорошковые композиции жаропрочного сплава ЭП648 производства ФГУП “ВИАМ” ГНЦ РФ в технологиях селективного лазерного сплавления, лазерной газопорошковой наплавки и высокоточного литья полимеров, наполненных металлическими порошками // Известия высших учебных заведений. Машиностроение. 2016. № 9 (678). С. 62.
ГОСТ 9454-78 Метод испытания на ударный изгиб при пониженных, комнатной и повышенных температурах [Электронный ресурс] URL: https://docs.cntd.ru/document/1200005045
Зубченко А.С., Каширский Ю.В., Дегтярев А.Ф. Марочник сталей и сплавов. М.: Научно-техническое издательство “Машиностроение”, 2015.
Дополнительные материалы отсутствуют.
Инструменты
Проблемы машиностроения и надежности машин