Поверхность. Рентгеновские, синхротронные и нейтронные исследования, 2019, № 11, стр. 64-71
Влияние сфокусированного импульсного лазерного излучения на свойства аморфного металлического сплава FeSi6B16
А. В. Жихарев 1, *, В. Я. Баянкин 1, С. Г. Быстров 1, Н. А. Орлова 2, **
1 Физико-технический институт Удмуртского федерального исследовательского центра УрО РАН
426000 Ижевск, Россия
2 Удмуртский государственный университет
426034 Ижевск, Россия
* E-mail: less@udman.ru
** E-mail: orlova@udsu.ru
Поступила в редакцию 24.12.2018
После доработки 07.03.2019
Принята к публикации 10.03.2019
Аннотация
Изучено влияние сфокусированного импульсного лазерного излучения (числа импульсов и плотности мощности) на аморфную металлическую ленту FeSi6B16. Состояние сплава до и после лазерного воздействия проанализировано с помощью методов атомной силовой микроскопии, рентгеновской фотоэлектронной спектроскопии, рентгенографических исследований и измерений микротвердости. Установлено, что сфокусированное лазерное излучение при любом режиме воздействия приводит в зоне облучения к высокотемпературному нагреву поверхности аморфного сплава. Результатом такого нагрева стало плавление поверхности материала и распространение фронта тепловой волны с сильно разогретой поверхности в его внутренние слои, что вызвало в системе Fe–Si–B перераспределение элементов, изменение структуры и рост микротвердости.
ВВЕДЕНИЕ
Аморфные металлические сплавы сочетают в себе различные физико-механические свойства, которые не достижимы для кристаллических материалов, что позволяет создавать на их основе сплавы со специфическими модифицированными свойствами, которые востребованы во многих отраслях науки и техники. Но поскольку аморфное состояние является неравновесным, при внешних воздействиях в аморфных сплавах могут происходить необратимые структурные превращения с потерей всех уникальных свойств. Поэтому исследование поведения аморфных материалов при термическом воздействии представляет научный и практический интерес [1–5].
Одним из способов термического воздействия на аморфные материалы может служить лазерная обработка, в которой сфокусированный световой поток, попадая на непрозрачные материалы, вызывает их нагрев. Регулируя режимы лазерной установки, можно добиться такого энергетического воздействия, которое за время своего действия либо существенно не плавит обрабатываемый материал, либо вызывает его сильное плавление и интенсивное испарение. Это, в свою очередь, позволяет влиять на фазовую структуру, перераспределение элементов и физико-механические свойства или только поверхностного слоя облучаемого материала, или за счет распространения фронта тепловой волны добиваться более глубокого проплавления и изменения свойств его подповерхностных слоев [6–11]. Это весьма важно для обеспечения контролируемого перехода из аморфного состояния в кристаллическое и получения многофазных материалов с уникальными свойствами.
Необходимо отметить одно очень важное преимущество лазерной обработки материалов перед традиционными методами обработки – возможность реализации локального немеханического воздействия лазера на облучаемый материал. Особенно это актуально при неразрушающей обработке хрупких материалов и материалов малой толщины (пленок, лент, фольг, тонких пластин), что как нельзя лучше подходит для обработки аморфных сплавов в виде лент.
В настоящей работе исследовано влияние сфокусированного импульсного лазерного излучения (числа импульсов и плотности мощности) на состав, структуру и микротвердость аморфной металлической ленты из сплава FeSi6B16.
ЭКСПЕРИМЕНТАЛЬНАЯ ЧАСТЬ
В качестве исследуемого объекта использована лента из аморфного металлического сплава FeSi6B16, полученная методом спиннингования – разливкой под давлением расплавленного металла на быстро вращающийся холодный массивный барабан. Для проведения эксперимента от ленты отрезали несколько полос длиной ~70 мм. Толщина полосы была ∼40 мкм, а ширина – 20 мм.
Лазерное воздействие на полосы осуществляли в естественной атмосфере сфокусированным лучом лазера с матовой стороны сплава (рис. 1а). Эта сторона при спиннинговании прилегала к барабану, что обеспечивало ей быструю закалку и создавало наибольшую степень разупорядочения материала. В качестве источника облучения использовали прецизионный лазерный маркер “БетаМаркер-2010” (Лазерный центр, г. Санкт-Петербург), работающий на базе твердотельного Nd–YAG-лазера с ламповой системой накачки и модуляцией добротности. Согласно паспортным данным длина волны генерируемого излучения установки составляет 1.064 мкм, максимальный ток накачки лампы 25 А, а максимальная мощность лазера 16 Вт. Изменяемыми параметрами при облучении были ток накачки лампы и число импульсов лазера. Число импульсов (N), приходящихся на точку, задавали равным одному, трем, пяти, семи и девяти. Частота генерации импульсов составляла 1000 Гц, а длительность импульса 1000 нс. Фокусное расстояние – 210 мм. Поскольку эффективность и качество процесса лазерного воздействия характеризуются плотностью мощности излучения в фокальном пятне (qf), был проведен перерасчет тока накачки лампы для выбранных режимов облучения [12]. Результаты проведенных расчетов представлены в табл. 1 в соответствии с принятыми обозначениями образцов.
Рис. 1.
Сфокусированное лазерное воздействие на аморфный металлический сплав FeSi6B16: а – схема облучения поверхности образца; б – рисунок полосы после лазерного воздействия с размеченными зонами облучения (указаны номера зон).
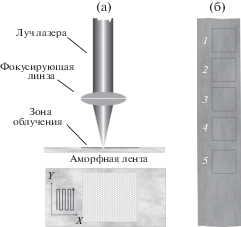
Во время облучения на полосе обрабатывали лазером до пяти зон (рис. 1б). Каждая зона соответствовала определенному режиму облучения. Размер одной зоны 10 × 10 мм. Для того чтобы обработке подвергалась вся зона, шаг перемещения лазерного луча был таким же, как и диаметр фокального пятна. С помощью лазера специально были сделаны буквенные метки и помечены границы облученных областей с целью правильного выбора и выделения из полосы образца с определенным режимом облучения для его дальнейшего исследования. Для этих целей рабочие режимы установки подбирали таким образом, чтобы маркирование приводило лишь к потемнению поверхности в месте касания луча лазера с материалом без каких-либо разрушений или деформации полосы.
Таким образом, была проведена лазерная обработка поверхности исследуемого аморфного сплава двух видов: одноимпульсная обработка при различной плотности мощности лазерного излучения (серия образцов № 1, № 2, № 7, № 8) и многоимпульсная обработка (различная последовательность идентичных импульсов) при постоянной плотности мощности лазерного излучения (серии образцов № 2–6). На каждую полосу приходился один вид лазерной обработки.
Топографию поверхности образцов до и после лазерного воздействия исследовали с использованием сканирующего зондового микроскопа SOLVER-47 PRO фирмы NT-MDT (г. Зеленоград). Поверхность сканировали методом атомно-силовой микроскопией (АСМ) в контактном режиме. В результате для каждого образца было получено не менее четырех сканов его облученной области. Размеры областей сканирования составляли 5 × 5 мкм. Для получения параметров шероховатости поверхности образцов (среднеарифметического отклонения профиля Ra) была проведена обработка снятых сканов методом Roughness Analysis. Для этого использовали специальное программное обеспечение Image Analysis v.3.5, поставляемое дополнительно к зондовому микроскопу. С помощью этой программы оператор задавал размер участка обработки (1 × 1 мкм), который программно наводил на интересующую область ранее отсканированной поверхности образца. Далее он запускал режим анализа и обработки, по завершению которого выдавались числовые значения параметров шероховатости выбранной области поверхности. При перемещении участка по скану образца происходил набор массива данных о шероховатости облученной области поверхности. Для каждого образца получено не менее 15 перекрывающих друг друга таких участков-измерений (рис. 2). Набранный массив измеренных величин Ra в дальнейшем усредняли и рассчитывали среднеквадратичное отклонение.
Структурные исследования образцов проводили с помощью рентгеновской дифрактометрии на дифрактометрах “ДРОН-6” и “ДРОН-3.0” (FeKα-излучение). Дифракционную картину регистрировали по точкам в режиме постоянного времени. Время набора импульса составляло 5 с. Систематическая погрешность ∆(2θ) – 0.02°.
Элементный состав поверхностных слоев образцов исследован методом рентгеновской фотоэлектронной спектроскопией (РФЭС) на спектрометре SPECS (MgKα-излучение с энергией 1253.6 эВ). Вакуум в камере спектрометра при съемке спектров был ∼10–9 Торр. Разрешение (ширина на половине высоты) по линии Au4f 7/2 составляло 1.2 эВ. Очистка поверхности от адсорбированных загрязнений и послойный анализ проведены путем травления поверхности ионами аргона с энергией 4 кэВ и плотностью тока 30 мкА/см2. Расчетная скорость травления ~1 нм/мин. Обработку результатов и разложение спектров проводили с помощью лицензионной программы CasaXPS. На основе полученных РФЭС-данных были построены профили распределения концентраций элементов по глубине образцов. Относительная погрешность определения концентрации элементов составляла ±3% (в области средних концентраций).
Микротвердость образцов измеряли и рассчитывали согласно ГОСТу 2999-75 методом Виккерса. Чтобы избежать следов продавливания на противоположной стороне образцов, нагрузку на индентор подбирали такую, чтобы обеспечить незначительную глубину отпечатка. Замеры диагоналей отпечатков проведены с помощью микротвердомера “ПМТ-3” при нагрузке на индентор 50 г в течение 10 с. Для повышения достоверности измеренных величин было получено не менее десяти отпечатков для каждого исследуемого состояния образца. Величины усредняли и рассчитывали среднеквадратичное отклонение.
РЕЗУЛЬТАТЫ И ИХ ОБСУЖДЕНИЕ
Исходное состояние образцов (до облучения)
Согласно дифрактограммам исходные образцы сплава FeSi6B16 находились в рентгеноаморфном состоянии, соответствующем однофазному связанному состоянию пересыщенного твердого раствора на основе железа без признаков присутствия каких-либо кристаллических фаз (рис. 3).
Рис. 3.
Дифрактограммы аморфного сплава FeSi6B16 до (образец № 0) и после облучения (образцы № 1–8).
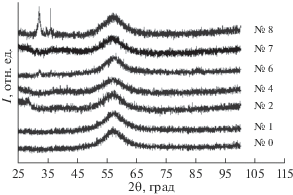
Анализ химического состава поверхностного слоя образцов показал, что в исходном состоянии в слое толщиной до 5 нм наблюдается высокая концентрация кислорода (∼40 ат. %) и низкое содержание железа (∼25 ат. %), кремния (∼15 ат. %), бора (∼6 ат. %) (рис. 4). В спектрах железа, кремния и бора присутствуют компоненты с высокими значениями энергии связи, что может говорить о возможном связывании этих элементов с кислородом. Дополнительно в этом слое на глубине до 2 нм был зафиксирован углерод (содержание ∼12 ат. %), который, скорее всего, можно отнести к оставшимся после предварительной очистки некоторым загрязнениям поверхности. В слоях глубиной более 5 нм концентрация элементов системы Fe–Si–B постепенно перераспределяется в соответствии с составом сплава FeSi6B16. На глубине свыше 10 нм и более содержание железа достигает ∼74 ат. %, бора – ∼16 ат. %, а кремния – ∼6 ат. %. Интенсивности линий O1s и C1s в спектрах кислорода и углерода близки к уровню фона.
Рис. 4.
Профили концентраций элементов в исходном аморфном сплаве FeSi6B16, скорость травления ~1 нм/мин.
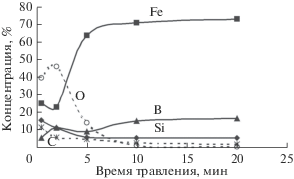
Морфология поверхности необлученных образцов согласно АСМ-исследованиям представляет собой рельеф переменного профиля, без каких либо резких перепадов высот (рис. 5а), Ra = = 3.0 ± 1.9 нм. Микротвердость образцов, измеренная до облучения, равна (567.6 ± 8.5) HV.
Рис. 5.
АСМ-изображения рельефа поверхности (область 5 × 5 мкм) аморфного сплава FeSi6B16 до (а) и после (б–к) облучения: б–д – при одном импульсе лазера и различной плотности мощности лазерного излучения; е–к – при постоянной плотности мощности лазерного излучения 5 × 105 Вт/см2 и различном числе импульсов лазера N. Везде указаны номера образцов.
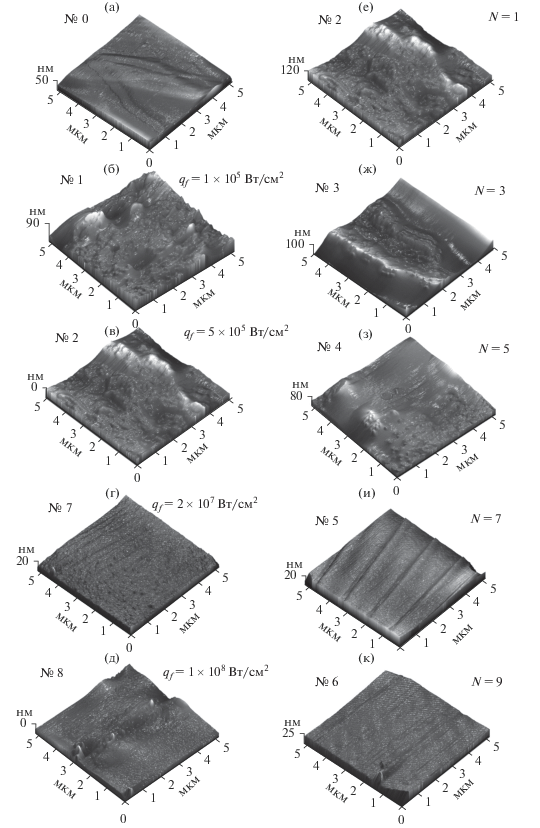
Состояние системы Fe–Si–B после лазерного воздействия
Для оценки степени влияния лазерного излучения на систему Fe–Si–B в зоне облучения образцов были проведены АСМ-исследования рельефа поверхности. Установлено, что рельеф поверхности образцов № 1–3 становится более развитым (менее однородным) по сравнению с исходным состоянием (рис. 5а, 5б, 5в, 5е, 5ж). На поверхности наблюдаются как плоские оплавленные участки подобно оплывшей гребенчатой структуре, так и области с холмообразными образованиями. Соответственно, увеличивается перепад высот рельефа облученных поверхностей (от 50 до 90, 120 и 100 нм) и повышается значение Ra (рис. 6), хотя визуально какие-либо изменения на полосе в зоне облучения образцов не наблюдаются. У образца № 4 рельеф поверхности выглядит еще более оплавленным (рис. 5з), а на полосе в зоне облучения наблюдается легкое потемнение поверхности. Значение Ra в сравнении с образцами № 1–3 снижается (рис. 6), а перепад высот уменьшается до 80 нм, хотя по сравнению с исходным состоянием рельеф образца № 4 выглядит также неоднородным. Рельеф поверхности образцов № 5–8 становится полностью плоским и оплавленным, характеризуется низким значением Ra. Визуально зона облучения образцов выглядела сильно потемневшей по сравнению с образцом № 4. У образцов № 6 и № 8 в зоне облучения произошел изгиб аморфной полосы по направлению действия лазера (рис. 7).
Рис. 7.
Фотография части аморфной полосы с обратной, необлучаемой, стороны (область полосы под зоной облучения образца № 8).
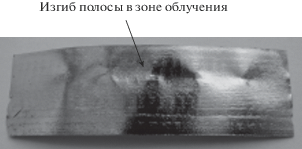
Подводя итог, можно сказать, что термическое воздействие лазера на образцы было достаточно сильным и приводило к плавлению их поверхности. Чем интенсивнее и мощнее было воздействие, тем сильнее происходил нагрев и плавление образцов. Согласно полученным дифрактограммам исследуемые образцы после облучения остаются рентгеноаморфными (рис. 3). Дифрактограмма образца № 1 практически идентична дифрактограмме исходного образца. На фоне аморфного гало не наблюдались какие-либо отражения, соответствующие новым метастабильным фазам. На дифрактограмме были видны сильные рефлексы, присущие только исходной фазе. На дифрактограммах образцов № 2, № 3, № 4, № 5 и № 7 относительно исходного состояния уже регистрировались изменения. В области 2θ = 30–45° перед основным гало появилось дополнительное, а интенсивность основного гало увеличилась. Соответственно, уменьшилась ширина основного гало. Эти изменения могут свидетельствовать о процессах начинающейся кристаллизации фаз из аморфного состояния сплава. В образцах № 6 и № 8 дополнительно к наблюдаемым изменениям как в предыдущих образцах, было отмечено появление в интервале углов 2θ = 25–40° рефлексов с d1 = 3.49 Å и d2 = 3.12 Å. Однако идентифицировать фазу с таким малым числом отражений нельзя, но можно предположить продолжающиеся процессы кристаллизации фаз из аморфного состояния. При сопоставлении данных рентгеновской дифрактометрии и АСМ учитывали, что при многоимпульсной лазерной обработке количество и частота следования импульсов будет влиять на конечную температуру в зоне облучения материала. В одном случае это может проявиться в накоплении тепла от импульса к импульсу, что будет способствовать значительному росту температуры на облучаемой поверхности. Это может привести к изменениям не только в поверхностных слоях материала, но и во внутренних слоях вследствие распространения фронта тепловой волны с сильно нагретой поверхности вглубь материала. В другом случае многоимпульсное лазерное воздействие может происходить без накопления тепла, когда поверхность успевает остыть до следующего импульса. Следовательно, температура в зоне облучения будет зависеть только от энергетических параметров отдельных импульсов. Изменения в материале в основном будут происходить в приповерхностных слоях. Подобные результаты облучения можно наблюдать и в случае одноимпульсной лазерной обработки, но их причиной уже будет количество энергии, поглощаемой материалом вследствие увеличения или уменьшения плотности мощности лазерного излучения [13–15].
Таким образом, проанализировав данные АСМ и рентгеновской дифрактометрии облученных образцов, можно предположить следующие причины изменений, происходящих в аморфном сплаве. Лазерное воздействие на образец № 1, возможно, затронуло только саму поверхность образца, а площадь нагрева оказалась локализованной приповерхностной областью. Ввиду малого объема сплава, подвергшегося нагреванию и плавлению, произошло очень быстрое охлаждение и затвердевание зоны облучения. Следовательно, времени на образование зародышей кристаллов в расплаве и их рост недостаточно. Для остальных образцов, где наблюдались процессы кристаллизации сплава, кристаллизация может быть следствием сильного разогрева большего объема аморфного сплава, приводящего к падению скорости его охлаждения и зарождению в аморфной матрице областей с кристаллической фазой при остывании сплава. Разогрев мог происходить из-за распространения фронта тепловой волны с сильно нагретой поверхности во внутренние слои сплава. Поскольку толщина образов небольшая (∼40 мкм), прогреться он мог на большую глубину. Значит во время лазерного воздействия, возможно, происходит не только плавление поверхности аморфного сплава, но и размягчение его подповерхностных слоев в зоне облучения. Возникший в результате перегрева слой расплава имеет больше времени на остывание и образование кристаллических зародышей.
Измерения микротвердости образцов после сфокусированного лазерного воздействия выявили ее повышение по сравнению с исходным состоянием для всех режимов облучения (рис. 8). Для образца № 1, оставшегося после облучения полностью рентгеноаморфным, увеличение микротвердости, предположительно, связано с уменьшением свободного объема в области плавления аморфного сплава. В результате нагрева и плавления поверхности образца в образовавшемся расплаве могло происходить перераспределение компонентов сплава (атомов и дефектов аморфного сплава (оборванных связей, неправильных связей, пор, трещин)), приведшее к появлению областей с повышенной плотностью большего размера. После прекращения лазерного воздействия в сплаве в результате быстрого охлаждения зоны облучения происходит “замораживание” состояния [1, 16, 17]. Повышение микротвердости образцов № 2–8 после лазерного воздействия, скорее всего, связано с процессами образования в аморфной матрице сплава FeSi6B16 кристаллической фазы, которая повышает прочностные свойства материала. Возникновение кристаллической фазы может быть следствием диффузионного перераспределения составляющих элементов сплава во время лазерного воздействия, которое обусловлено стремлением облучаемой метастабильной системы к упорядочению исходной структуры. Диффузионная подвижность элементов системы обеспечивается за счет плавления и размягчения аморфного сплава в результате высокоэнергетического воздействия на образцы. Итогом такого перераспределения элементов может быть появление в аморфном сплаве концентрационных неоднородностей, которые могут стать зародышами кристаллической фазы [3, 4, 16–18]. После прекращения лазерного воздействия количество закристаллизовавшегося материала в сплаве будет пропорционально времени остывания материала, которое, в свою очередь, зависит от степени разогрева и проплавления сплава. Поскольку по дифрактограмме образцов идентифицировать образующуюся кристаллическую фазу невозможно (ввиду малого числа отражений), был проведен литературный анализ исследований кристаллизации сплава Fe–Si–B. На основе приведенных в [4] экспериментальных данных можно полагать, что сплав FeSi6B16 с содержанием Si менее 10 ат. % будет кристаллизоваться с образованием фаз α-Fe1 – ZSiZ и Fe2B. Наблюдаемое повышение микротвердости образцов № 2–8 может быть следствием образования кристаллической фазы Fe2B. Косвенно в пользу этого предположения свидетельствуют обработанные РФЭС-данные для этих образцов. Согласно построенным профилям распределения концентрации бора по глубине в поверхностных слоях образцов после лазерного воздействия наблюдается тенденция снижения количества бора (рис. 9). Так, для образца № 2 по сравнению с исходным состоянием на глубине до 17 нм содержание бора понижено примерно в 1.3 раза. Однако далее на глубине до 20 нм количество бора растет от 12 до 19 ат. %. В исходном состоянии содержание бора на этой же глубине было ∼16 ат. %. Для остальных образцов (№ 3–8) также отмечалось снижение концентрации бора, но уже во всем анализируемом слое. Скорее всего, вследствие большего прогрева и размягчения объема аморфного сплава бор мог мигрировать на большую глубину. Вероятно, можно будет ожидать такое же повышение его концентрации, но уже на больших глубинах, чем было проанализировано методом РФЭС для этих образцов.
Рис. 9.
Профили концентрации бора по глубине образцов аморфного сплава FeSi6B16 (скорость травления ~1 нм/мин): а – в зависимости от плотности мощности лазерного излучения при одном импульсе лазера; б – в зависимости от числа импульсов лазера при постоянной плотности мощности лазерного излучения 5 × 105 Вт/см2.
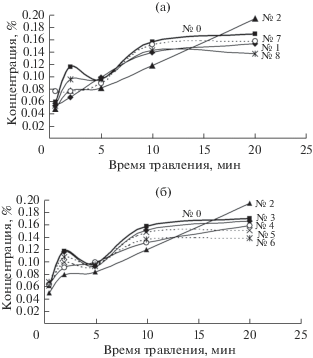
ЗАКЛЮЧЕНИЕ
Во всех случаях лазерного воздействия аморфный сплав FeSi6B16 подвергался сильному термическому воздействию. Нагрев сплава до высоких температур привел как к плавлению поверхности образцов, так и к распространению фронта тепловой волны с нагретой поверхности во внутренние слои материала. В образцах происходили процессы кристаллизации фаз из аморфного состояния сплава, но из-за быстрого охлаждения зоны облучения произошло “замораживание” роста образовавшихся зародышей кристаллической фазы. Из-за этого образцы в объеме остались рентгеноаморфными. Кристаллизация сплава была следствием диффузионного перераспределения составляющих его элементов при стремлении метастабильной системы к равновесию. Подвижность элементов системы Fe–Si–B обеспечивалась проплавлением внутренних слоев образцов вследствие их высокотемпературного нагрева, что способствовало появлению в аморфной матрице областей с концентрационной неоднородностью. Также в образцах после лазерного воздействия отмечался рост микротвердости по сравнению с исходным значением. Повышение микротвердости связано с возникновением в аморфной матрице сплава FeSi6B16 кристаллической фазы Fe2B.
Список литературы
Глезер А.М., Молотилов Б.В. Структура и механические свойства аморфных сплавов. М.: Металлургия, 1992. 208 с.
Фельц А. Аморфные и стеклообразные неорганические твердые тела. М.: Мир, 1986. 558 с.
Люборский Ф.Е. Аморфные металлические сплавы. М.: Металлургия, 1987. 584 с.
Манохин А.И., Митин Б.С., Васильев Б.С., Ревякин А.В. Аморфные сплавы. М.: Металлургия, 1984. 160 с.
Абросимова Г.Е. Эволюция металлических стекол при внешних воздействиях: Дис. … д-ра ф.-м. н.: 01.04.07. Черноголовка: ИФТТ РАН, 2012. 294 с.
Сэм М.Ф. // Соросовский образовательный журн. 1996. № 6. С. 92.
Арутюнян Р.В., Баранов В.Ю., Большов Л.А. и др. Воздействие лазерного излучения на материалы. М.: Наука, 1989. 367 с.
Рыкалин Н.Н., Углов А.А., Зуев И.В., Кокора А.Н. Лазерная и электронно-лучевая обработка материалов. М.: Машиностроение, 1985. 496 с.
Быковский Ю.А., Неволин В.Н., Фоминский В.Ю. Ионная и лазерная имплантация металлических материалов. М.: Энергоатомиздат, 1991. 240 с.
Климков Ю.М., Майоров В.С., Хорошев М.В. Взаимодействие лазерного излучения с веществом: учебное пособие. М.: МИИГАиК, 2014. 108 с.
Хомич В.Ю., Шмаков В.А. // Успехи физических наук. 2015. Т. 185. № 5. С. 489.
Жихарев А.В., Климова И.Н., Баянкин В.Я. и др.// Физика твердого тела. 2013. Т. 55. № 10. С. 1887.
Григорьянц А.Г., Сафонов А.Н. Основы лазерного термоупрочнения сплавов. М.: Высш. шк., 1988. 159 с.
Вейко В.П. Опорный конспект лекций по курсу ”Физико-технические основы лазерных технологий“. Раздел ”Лазерная микрообработка“. СПб.: СПбГУ ИТМО, 2005. 110 с.
Вейко В.П., Шахно Е.А. Сборник задач по лазерным технологиям. СПб.: СПбГУ ИТМО, 2007. 67 с.
Скаков Ю.А. Аморфные металлические сплавы. Научные труды № 147. М.: Металлургия, 1983. 128 с.
Баянкин В.Я., Васильев В.Ю., Шабанова И.Н. Сегрегационные эффекты на поверхности метастабильных металлических систем. Ижевск: Изд-во Ин-та прикладной механики УрО РАН, 1999. 288 с.
Журавлев В.А., Лихачев В.А., Ермолаева Н.А. и др. Металлоаморфные сплавы. Сб. науч. тр. Ижевск: УдГУ, 1988. 192 с.
Дополнительные материалы отсутствуют.
Инструменты
Поверхность. Рентгеновские, синхротронные и нейтронные исследования