Поверхность. Рентгеновские, синхротронные и нейтронные исследования, 2019, № 7, стр. 63-68
Сравнительный анализ углеродных и фторуглеродных покрытий, полученных при помощи низкочастотного плазмотрона при атмосферном давлении
А. Н. Лямин 1, А. В. Шведов 1, *, В. М. Елинсон 1, С. В. Дворяк 2
1 Московский авиационный институт (национальный исследовательский университет)
125993 Москва, Россия
2 Московский государственный университет им. М.В. Ломоносова
119991 Москва, Россия
* E-mail: seriousash@yandex.ru
Поступила в редакцию 29.11.2018
После доработки 12.12.2018
Принята к публикации 14.12.2018
Аннотация
Работа посвящена исследованию свойств углеродных и фторуглеродных покрытий, полученных при помощи низкочастотного плазмотрона при атмосферном давлении. Определены технологические параметры для нанесения покрытий, а также проведен сравнительный анализ свойств полученных покрытий. При помощи горизонтального микроскопа c гониометрической приставкой были исследованы краевые углы смачивания углеродных и фторуглеродных покрытий. Методом рентгеновской фотоэлектронной спектроскопии определен химический состав полученных покрытий.
ВВЕДЕНИЕ
В настоящее время большое внимание исследователей привлекают методы формирования защитных покрытий, используемых в условиях повышенной влажности [1], микробиологических загрязнений и других факторов, приводящих к деструкции поверхности изделий. Для нанесения тонкопленочных материалов наиболее широко применяют вакуумные методы ионно-плазменной технологии.
Использование газовых разрядов при атмосферном давлении для нанесения тонких защитных покрытий имеет ряд преимуществ по сравнению с вакуумным нанесением: отсутствие необходимости создания и поддержания вакуума; возможность локальной обработки поверхности; высокая скорость роста покрытий, что уже позволяет использовать газовые разряды при атмосферном давлении в обрабатывающей промышленности, стерилизаторах [2]. Наибольшее распространение получил диэлектрический барьерный газовый разряд, который в настоящее время широко применяют для модификации различных поверхностей [3–6], а также для проведения химических реакций [7]. В последнее время большое внимание привлекают исследования, связанные с использованием низкочастотного (НЧ) газового разряда, а также НЧ-плазмотроны в силу отсутствия громоздких охлаждаемых электродов и возможности локальной обработки различных проводящих материалов и термолабильных полимерных диэлектриков.
Наиболее перспективными материалами для создания новых тонкопленочных структур с контролируемыми барьерными и изоляционными характеристиками являются углеродные пленочные структуры. В связи с тем, что углерод может существовать в виде множества гетерофазных систем, посредством управления технологическими параметрами осаждения из газовой фазы можно изменить свойства получаемых покрытий в широких пределах [8]. Применение фторуглеродных материалов позволяет значительно расширить диапазон свойств разрабатываемых структур, поскольку эти материалы обладают высокими диэлектрическими свойствами, термической стойкостью и химической инертностью.
Стоит отметить, что в научной литературе практически не описаны работы, посвященные возможности нанесения углеродных или фторуглеродных покрытий с использованием плазмотрона при атмосферном давлении. Поэтому целью настоящей работы был сравнительный анализ возможностей осаждения углеродных и фторуглеродных покрытий в зависимости от технологических параметров нанесения, а также исследование свойств полученных покрытий.
МАТЕРИАЛЫ И МЕТОДЫ
В работе использовался НЧ-плазмотрон при атмосферном давлении с потребляемой мощностью источника питания от 50 до 100 Вт для обеспечения ионизации газовой смеси. Принципиальная электрическая схема плазмотрона представлена на рис. 1.
Углеродсодержащие покрытия формировали при использовании в качестве пленкообразующего газа паров циклогексана (C6H12, марка СТП ТУ КOMП 3-452-11) концентрацией 2.5 об. % от суммарного газового потока через сопло плазмотрона. В качестве транспортного газа для нанесения углеродных покрытий применяли плазмообразующий газ гелий (марка “Б”), а для нанесения фторуглеродных покрытий – тетрафторметан (CF4, марка “Ч”). Суммарный поток газов во всех случаях составлял 7.2 ± 0.2 л/мин. В качестве материалов подложки использовали кремний (марка 100КДБ(7-13)(100)), полиэтилентерефталат (ПЭТФ, ПЭТ-Э ГОСТ 24 234-80) и полистирол (ТУ 9398-046-00480230-2005). Подачу газовой смеси осуществляли согласно схеме, представленной на рис. 2, а также фиксировали при помощи регуляторов расхода газа РРГ-12.
Угол смачивания для измерения удельной поверхностной энергии осаждаемых углеродных и фторуглеродных покрытий определяли на подложках из ПЭТФ по стандартной методике измерения контактного угла смачивания в режимах натекания и оттекания в горизонтальном микроскопе марки “МГ” c гониометрической приставкой.
Химический состав углеродных и фторуглеродных покрытий, сформированных на подложках из полистирола исследовали методом рентгеновской фотоэлектронной спектроскопии (РФЭС) на приборе Kratos Axis Ultra DLD (Kratos Analytical Limited, Великобритания).
РЕЗУЛЬТАТЫ И ИХ ОБСУЖДЕНИЕ
Исследования показали, что энергетический вклад в плазменную струю играет существенную роль. Увеличение мощности от 50 до 100 Вт увеличивает в 1.5 раза скорость роста углеродных покрытий и до 10 раз фторуглеродных покрытий (рис. 3). Значительное изменение скорости роста, по-видимому, связано со “встраиванием” ионизированных фторуглеродных соединений в состав покрытий, что приводит к увеличению толщины наносимого покрытия. Поэтому все последующие результаты работы описаны для мощности 100 Вт.
Рис. 3.
Зависимость толщины углеродных (1, 3) и фторуглеродных (2, 4) покрытий от времени нанесения при одинаковых расстояниях плазмотрон–подложка 18 мм и концентрации пленкообразующего газа 2% при мощности источника 50 (1, 2) и 100 Вт (3, 4).
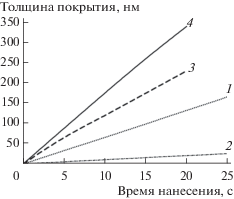
На скорость роста как углеродного, так и фторуглеродного покрытия существенно влияет расстояние плазмотрон–подложка и концентрация пленкообразующего газа (рис. 4). Это связано с увеличением энергетического вклада в газовый разряд между соплом плазмотрона и заземленной поверхностью и со значительным увеличением диффузии частиц газа из плазменной струи в окружающую среду.
Рис. 4.
Зависимость толщины фторуглеродных (1, 2) и углеродных (3, 4) покрытий от времени нанесения при расстояниях плазмотрон–подложка 18 (1, 3) и 24 мм (2, 4) и одинаковых концентрациях пленкообразующего газа 2%.
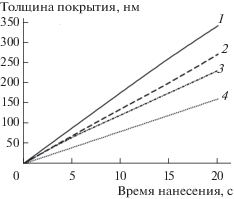
Для оценки воспроизводимости полученных результатов был исследован частотный диапазон зажигания газового разряда для различных смесей газов и определена эффективная частота. Показано, что для эффективной и воспроизводимой работы плазмотрона при использовании различных газовых смесей необходимо поддержание собственного достаточно узкого диапазона частот (рис. 5). Так, при одинаковых суммарных потоках в случае плазмообразующего газа He обнаружены две эффективные частоты: 70 ± 1 и 84 ± 1 кГц в диапазоне горения разряда 63–127 кГц, а в случае смеси плазмообразующего, транспортного и пленкообразующего газов – только одна эффективная частота 70 ± 1 кГц в диапазоне горения разряда 67–80 кГц.
Рис. 5.
Зависимость толщины углеродного (1) и фторуглеродного (2) покрытия от частоты генерации газового разряда при расстоянии плазмотрон–подложка 18 мм и концентрации пленкообразующего газа 2%: 3 – диапазон горения газового разряда в плазмообразующем газе; 4 – эффективная частота.
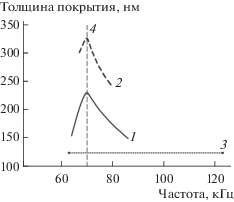
В силу особенностей горения атмосферного газового разряда и его распространения по поверхности подложки покрытия имеют круглую форму с несколько “размытыми” границами диаметром от 6 до 9 мм при времени нанесения более 10 с (рис. 6). Разброс диаметров полученных покрытий при времени нанесения менее 10 с зависит только от времени нанесения покрытия, т.е. от толщины покрытия. При времени нанесения более 10 с влияние толщины покрытия на его диаметр значительно уменьшается.
Рис. 6.
Зависимость диаметра углеродных (1, 2) и фторуглеродных (3, 4) покрытий от времени нанесения при расстояниях плазмотрон–подложка 18 (1, 3) и 24 мм (2, 4) и одинаковых концентрациях пленкообразующего газа 2%.
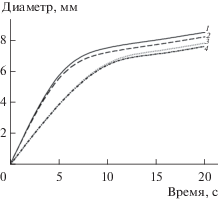
Меньший диаметр покрытий и, соответственно, меньший разброс их диаметров в случае фторуглеродных пленок связан с увеличением молекулярной массы компонентов плазменной смеси, т.е. с увеличением устойчивости горения газового разряда и уменьшением диффузии пленкообразующего и транспортного газов в атмосферу. Этими же причинами, по-видимому, определяется максимальный диаметр покрытий при расстоянии плазмотрон–подложка 21 мм вне зависимости от типа покрытия. При меньших расстояниях плазмотрон–подложка наблюдается большая толщина покрытий, связанная с малой диффузией частиц плазменной струи в окружающую среду за счет скорости вылета из сопла плазмотрона, а при больших расстояниях – увеличение диффузии возбужденных частиц и радикалов пленкообразующего газа в окружающую среду с их последующим рассеянием вне подложки.
В связи с незначительным увеличением диаметра покрытия при времени его нанесения более 10 с увеличение толщины осаждаемого покрытия сопровождается значительным уменьшением степени его равномерности (рис. 7), которая была рассчитана по формуле:
Рис. 7.
Равномерность осаждения углеродных (1, 2) и фторуглеродных (3) покрытий в зависимости от времени нанесения при расстояниях плазмотрон–подложка 18 (1, 3) и 24 мм (2) и одинаковых концентрациях пленкообразующего газа 2%.
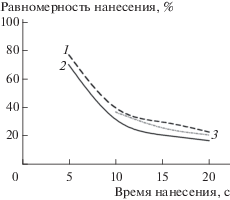
Особенно это заметно при малых расстояниях плазмотрон–подложка. Таким образом, для равномерного нанесения покрытий необходимо соблюдать расстояния плазмотрон–подложка от 18 до 21 мм. С точки зрения экономической целесообразности время формирования углеродных и фторуглеродных покрытий не должно превышать 60 с. То есть для оптимального режима работы плазмотрона необходимы следующие условия: расстояние плазмотрон–подложка 18–21 мм, время нанесения от 5 до 15 с.
Для определения удельной поверхностной энергии был измерен угол смачивания. Результаты измерений, представленные на рис. 8, свидетельствуют о неизменности типа смачиваемости поверхности, т.е. об ее гидрофильности. В случае обработки поверхности только одним плазмообразующим газом и осаждения углеродных пленок наблюдается уменьшение угла смачивания на 30°, что, по-видимому, связано как с тепловым воздействием плазменной струи на поверхность полимера, так и с формированием новой поверхности – углеродной пленки. Аналогичный эффект наблюдается и при осаждении углеродных пленок по вакуумной ионно-плазменной технологии [9]. Увеличение гидрофобности поверхности при осаждении фторуглеродной пленки связано с образованием связей С–F в пленке. Этот вывод был подтвержден данными РФЭС.
Рис. 8.
Зависимость контактного угла смачивания углеродных (1, 2) и фторуглеродных (3, 4) покрытий от расстояния плазмотрон–подложка при концентрации пленкообразующего газа 2.5%, время нанесения покрытия: 1 – 5; 2 – 10; 3 – 10; 4 – 15 с; 5 – ПЭТФ, контроль.
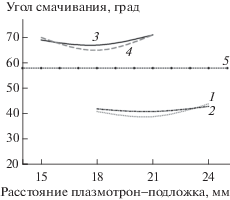
В спектрах РФЭС (рис. 9) наблюдаются линии углерода, кислорода, фтора и азота. Соотношение концентраций углерода и фтора на поверхности исследованных образцов было рассчитано по РФЭС-спектрам C1s и F1s высокого разрешения (при энергии пропускания 40 эВ). В спектрах F1s (рис. 9) наблюдаются два состояния фтора в исследованных образцах: с энергией связи около 686 эВ, что соответствует ковалентной связи F–C, и состояние с энергией связи около 685 эВ, что характерно для ионной связи фтора во фторидах металлов. Наличие фторидов металлов, по-видимому, связано с незначительным распылением острия материала НЧ-электрода.
Рис. 9.
РФЭС-спектры F1s высокого разрешения фторуглеродных (1–6) и углеродных (7) покрытий, нанесенных при концентрации пленкообразующего газа 2% и технологических параметрах (расстояние плазмотрон–подложка, время нанесения): 1 – 15 мм, 10 с; 2 – 15 мм, 15 с; 3 – 24 мм, 10 с; 4 – 24 мм, 15 с; 5 – 18 мм, 10 с; 6 – 18 мм, 15 с; 7 –18 мм, 15 с.
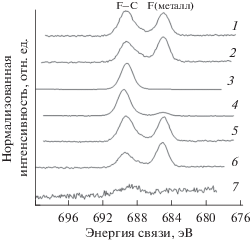
ЗАКЛЮЧЕНИЕ
Таким образом, в работе показано, что увеличение мощности плазмотрона, вкладываемой в разряд, позволяет увеличить в 1.5 раза скорость роста углеродных покрытий и почти в 10 раз фторуглеродных покрытий.
Исследование частотного диапазона формирования газового разряда позволило определить эффективную частоту его горения и критическое расстояние плазмотрон–подложка для формирования углеродных и фторуглеродных пленок и оптимальный режим работы плазмотрона.
Установлено, что разброс диаметров полученных покрытий незначительно зависит от расстояния плазмотрон–подложка и толщины покрытия при времени нанесения более 10 с, что по-видимому, связано с формированием равномерного и устойчивого покрытия. Это свидетельствует также о воспроизводимости результатов.
На основе анализа контактных углов смачивания и данных РФЭС установлено влияние химического состава на изменение угла смачивания, а также показана возможность формирования фторуглеродных пленок с различным количеством ковалентных связей С–F. Выявлен аналогичный характер формирования углеродных и фторуглеродных покрытий вакуумными методами и плазменным методом при атмосферном давлении [9].
Список литературы
Нефедоров Н.И., Семенова Л.В. // Успехи в химии и химической технологии. 2012. Т. 26. С. 53.
Слепцов В.В., Баранов А.М., Бердник В.И. и др. // Приборы и техника эксперимента. 2015. № 2. С. 122. https://doi.org/10.7868/S0032816215020111 (Sleptsov V.V., Baranov A.M., Berdnik V.I. et al. // Instruments and Experimental Techniques. V. 58. № 3. 2015. P. 445. doi https://doi.org/10.1134/S0020441215030288)
Rehn P., Wolkenhauer A., Bente M., Forster S. et al. // Surf. Coat. Technol. 2003. V. 174. P. 515. https://doi.org/10.1016/ S0257-8972(03)00372-4
Vinogradov I.P., Dinkelmann A., Fateev A., Lunk A. // Surf. Coat.Technol. 2003. V. 174. P. 509. https://doi.org/10.1016/ S0257-8972(03)00615-7
Inagaki N. // Atmospheric Pressure Plasma Treatment of Polymers. 2013. P. 83. https://doi.org/10.1002/9781118747308.ch3
Кутепов А.М., Захаров А.Г., Максимов А.И., Титов В.А. // Рос. хим. журн. 2002. Т. 46. № 1. С. 103.
Kaiser M., Emmerich R., Joos M. et al. // Surf. Coat. Technol. 2003. V. 174. P. 498.
Суздалев И.П. Нанотехнология: физико-химия нанокластеров, наноструктур и наноматериалов. М.: КомКнига, 2006. 592 с.
Лямин А.Н., Щур П.А., Елинсон В.М. // Поверхность. Рентген., синхротр. и нейтрон. исслед. 2016. № 7. С. 63. https://doi.org/10.7868/S0207352816070131
Дополнительные материалы отсутствуют.
Инструменты
Поверхность. Рентгеновские, синхротронные и нейтронные исследования