Поверхность. Рентгеновские, синхротронные и нейтронные исследования, 2020, № 9, стр. 12-19
Влияние шероховатости поверхности подложек на стабильность параметров тонкопленочных резистивных элементов
В. Е. Сергеев a, b, *, В. М. Воротынцев a, Т. С. Сазанова a, И. В. Воротынцев a, С. В. Кононов b
a Нижегородский государственный технический университет им. Р.Е. Алексеева
603950 Нижний Новгород, Россия
b Филиал “РФЯЦ-ВНИИЭФ Научно-исследовательский институт измерительных систем им. Ю.Е. Седакова
603137 Нижний Новгород, Россия
* E-mail: sergeev1980sergeev@yandex.ru
Поступила в редакцию 14.12.2019
После доработки 17.01.2020
Принята к публикации 20.01.2020
Аннотация
В статье исследуется влияние шероховатости поверхности подложек на стабильность параметров тонкопленочных резистивных элементов. Определена шероховатость поверхности подложек методами оптической и атомно-силовой микроскопии (АСМ). Разработана технология получения, сглаживающего поверхность покрытия на основе тонких пленок Ta2O5 с аморфной когерентной структурой, применение которого уменьшает высоту микронеровностей профиля поверхности Rz до значений 12 нм и менее. Покрытие позволяет формировать на его поверхности тонкие наноразмерные пленки, снижает температурный коэффициент сопротивления ~ в два раза и повышает стабильность тонкопленочных резисторов.
ВВЕДЕНИЕ
Прогресс современной микроэлектроники во многом определяется развитием тонкопленочных технологий, позволяющих создавать новые структуры с уникальными свойствами.
Состояние поверхности подложки оказывает существенное влияние на структуру наносимых пленок и параметры тонкопленочных элементов. Большая шероховатость поверхности подложки и наличие на ней микронеровностей изменяет толщину тонких пленок, тем самым вызывая локальное изменение электрофизических свойств пленок, а также снижение воспроизводимости параметров тонкопленочных элементов и их надежности. Поэтому подложки для тонкопленочных резистивных элементов должны иметь минимальную шероховатость и не должны содержать поры и трещины [1–3].
При формировании тонкопленочных резистивных пленок толщиной менее 30 нм поверхность подложек должна соответствовать как минимум 14 классу чистоты поверхности, то есть допустимая высота микронеровностей не должна превышать 20 нм, что не всегда реализуется из-за наличия пор и царапин, которые снижают показатели шероховатости.
Целью настоящей работы является проведение исследований шероховатости поверхности подложек, оценки влияния ее на стабильность параметров тонкопленочных резистивных элементов, а также исследование способов сглаживания поверхности подложек.
ТЕОРЕТИЧЕСКИЙ АНАЛИЗ
Исследование шероховатости поверхности
В настоящее время в мировой практике не выработан единый подход к оценке шероховатости. Например, в таких странах, как США, Англия, Германия, Япония, количество параметров шероховатости значительно различается [4].
Ранее при оценке шероховатости поверхности ограничивались традиционными измерениями параметров средней арифметической шероховатости Ra и высоты неровностей профиля Rz [5].
Ra – среднее арифметическое из абсолютных значений отклонений профиля в пределах базовой длины, рассчитывается по формуле [6]:
(1)
${{R}_{a}} = \frac{1}{l}~~\mathop \smallint \limits_0^l \left| {y\left( x \right)} \right|dx \approx \frac{1}{n}~~\mathop \sum \limits_{i\,\, = \,\,1}^n \left| {{{y}_{i}}} \right|,$Rz – сумма средних абсолютных значений высот пяти наибольших выступов профиля и глубин пяти его наибольших впадин профиля в пределах базовой длины, определяется по формуле [6]:
(2)
${{R}_{z}} = \frac{{\sum\limits_{i\,\, = \,\,1}^5 {\left| {{{y}_{{{\text{p}}i}}}} \right|} + \sum\limits_{i\,\, = \,\,1}^5 {\left| {{{y}_{{{\text{v}}i}}}} \right|} }}{5},$Однако традиционно контролируемые параметры шероховатости поверхности Ra и Rz не дают полной картины формы микрорельефа. Для полной оценки микрорельефа необходимо также изучение функциональных параметров, таких как, например, высота пиков Rpk и впадин Rvk, которые, в отличие от амплитудных, характеризуют рельеф в локальной области.
Для количественной оценки степени равномерности поверхности логично применять соотношение приведенных высот пиков Rpk и впадин Rvk, поскольку эти величины в одинаковой степени характеризуют отклонение профиля поверхности от базовой линии. Таким образом, можно полагать, что при приближении значения этого соотношения к 1, поверхность становится более равномерной и упорядоченной [7].
Методы контроля шероховатости поверхности можно отнести к двум группам:
1) методы, основанные на дифракции электромагнитного излучения на неоднородной границе раздела сред (оптические [8] и рентгеновские);
2) прямые методы контроля микрорельефа (механическая профилометрия, атомно-силовая (АСМ) [9] и сканирующая туннельная микроскопия (СТМ) [10]).
Выбор метода изучения микрорельефа обычно определяется конкретными задачами исследований и обычно каждый метод дополняет друг друга. Методы, основанные на анализе рассеяния и отражения рентгеновского излучения, привлекают в настоящее время большое внимание [11] вследствие ряда неоспоримых достоинств:
1) относятся к неразрушающим методам контроля;
2) обладают высокой чувствительностью, позволяющей исследовать шероховатость сверхгладких поверхностей с высотой микронеровностей 0.1–1 нм;
3) характеризуются высокой информативностью, поскольку минимальный продольный размер регистрируемых неоднородностей по порядку величины соответствует длине волны зондирующего пучка.
Однако, в отличие от прямых измерений (профилометрия, АСМ), методы рентгеновского рассеяния являются косвенными и существенным образом основываются на использовании теории взаимодействия излучения с шероховатой поверхностью и модели поверхности. В связи с этим возникает проблема выбора адекватного теоретического приближения, позволяющего извлечь данные о шероховатостях однозначным образом [12].
Для исследования поверхности образцов в настоящей работе выбран метод АСМ из-за его высокой чувствительности и точности. В тоже время следует отметить, что применение метода АСМ для изучения микрорельефа образцов значительного размера (более десятков микрон) является затруднительным и длительным процессом. Поэтому для сопоставления результатов в работе проведены исследования шероховатости поверхности с помощью оптической микроскопии, позволяющей проводить измерения на большей площади.
Таким образом, с помощью АСМ будет детально изучена структура поверхности подложек, а с помощью оптической микроскопии получена информацию о регулярности данной структуры в большем масштабе.
Исследование технологии получения сглаживающего поверхность покрытия
С целью минимизации высоты и сглаживания краев микронеровностей целесообразно нанесение грунтующего слоя из материала, обладающего хорошими диэлектрическими и адгезионными свойствами, а также однородной структурой [13].
Известно, что в качестве грунтующих материалов подложек применяют эмаль (глазурование) толщиной 25–100 мкм, монооксид кремния SiO толщиной ~1 мкм. Пленки SiO, как правило, имеют высокую напряженность и, следовательно, низкую адгезию, а на слоях глазури наблюдается цек, то есть волосяные трещины, образуемые из-за разности температурных коэффициентов линейного расширения.
Перспективным грунтующим материалом поверхности подложек является оксид тантала Та2О5, сформированный на поверхности в виде тонкой пленки. Существует большое количество методов получения пленок Та2О5, основные из них: химические методы (химическое газофазное осаждение, анодное оксидирование, золь-гель метод, атомное-слоевое осаждение) и методы вакуумного напыления (электронно-лучевое испарение, катодное распыление). В настоящей работе для получения пленок Та2О5 применен метод ионно-плазменного распыления тантала [14, 15] с последующим его термическим окислением на подложке. Метод обеспечивает высокую скорость осаждения пленок, позволяет получать пленки с аморфной когерентной структурой, высокой плотностью и адгезией.
Исследование стабильности параметров резистивных элементов
Согласно общепринятым представлениям, формирование тонких пленок происходит в результате образования зародышей, роста и слияния островков. Однако на шероховатой поверхности подложек могут происходить специфические механизмы роста, не требующие начального образования зародышей. Пленки на шероховатых поверхностях характеризуются, как правило, неравномерной толщиной, значительно различающимися размерами зерен, большими межзеренными напряжениями, что существенно влияет на их температурную и временнýю стабильность.
Явления старения в пленках связаны с процессами фазовых, структурных и субструктурных превращений, свойственными многокомпонентным системам в активированном состоянии.
Одним из основных параметров резистора является температурный коэффициент сопротивления (ТКС), который характеризует обратимое изменение сопротивления под действием температуры или тока, протекающего через резистор.
В работе [16] установлена связь между ТКС и характеристиками стабильности: минимальному значению ТКС соответствует максимальная стабильность материала в процессе старения или термообработки. Таким образом, температурный коэффициент сопротивления является структурно-чувствительным параметром резистивной пленки, по величине которого можно прогнозировать поведение резистора на длительные сроки хранения или эксплуатации.
ЭКСПЕРИМЕНТАЛЬНАЯ ЧАСТЬ
Объекты исследования
В качестве объектов исследования в настоящей работе выбраны образцы:
1) для изучения шероховатости поверхности – подложки из ситалла марки СТ 50-1 с грунтующим покрытием Та2О5 и без него;
2) для оценки стабильности параметров тонкопленочных резистивных элементов – резистивные тонкопленочные элементы на основе сплава РС-3710 с удельным поверхностным сопротивлением ps = 1000 Ом/квадрат с контактами ванадий–алюминий, сформированные на подложках из ситалла марки СТ 50-1 с грунтующим покрытием Та2О5 и без него.
Грунтующее покрытие Та2О5 представляет собой тонкие пленки, сформированные методом термического выращивания, а именно в начале методом ионно-плазменного распыления на установке УВН-75П-1 на ситалловую подложку напылялись пленки тантала, а затем пленки окислялись в муфельной электропечи в кислороде воздушной среды.
Резистивные пленки с удельным поверхностным сопротивлением ps = 1000 Ом/квадрат формировались в одном вакуумном цикле напыления методом ионно-плазменного распыления на установке УВН-75П-1 при температуре 623 К. Контакты ванадий–алюминий напылялись методом магнетронного распыления на установке “Оратория-5”.
Атомно-силовая микроскопия
Исследование шероховатости поверхности подложек из ситалла проводилось методом АСМ на сканирующем зондовом микроскопе SPM-9700 (Shimadzu, Япония).
Сканирование проводили в полуконтактном режиме, в процессе реализации которого одновременно со сканированием образца кантилевер совершает вертикальные периодические колебания (в нашем случае с постоянной частотой) таким образом, чтобы в нижнем полупериоде касаться поверхности образца, а в верхнем – нет. Выбор этого режима основан на том, что он является наиболее универсальным из возможных режимов АСМ, кроме того, в отличие от контактной моды, в полуконтакте максимально устранены латеральные силы, действующие на зонд со стороны поверхности, что упрощает интерпретацию получаемых изображений [17].
Полуконтактный режим сканирования реализовывали с применением кремниевых вибрационных кантилеверов POINTPROBE FMR-20 (NanoWorld Innovative Technologies, США) с коэффициентом жесткости 1.3 Н/м и типичным радиусом кривизны острия не более 8 нм (гарантировано – не более 12 нм), высота иглы – от 10 до 15 мкм.
Обработка полученных АСМ-изображений и их количественный анализ осуществляли с помощью инструментов программного обеспечения SPM Manager ver. 4.02. Количественный анализ результатов АСМ-сканирования включал в себя анализ метрических параметров шероховатости, а именно амплитудных (средняя арифметическая шероховатость Ra и высота неровностей поверхности Rz) и функциональных (приведенные высота Rpk, вершины и впадины Rvk).
Оптическая микроскопия
Для сравнения и определения идентичности результатов измерения микрорельефа методом АСМ в работе проведены исследования шероховатости поверхностей подложек из ситалла с помощью оптического анализатора микросистем MSA-500 (PolytecGmbH, Германия) со сканирующим виброметром Polytec на базе микроскопа, функционирующего по принципу лазерной интерферометрии.
Управление системой измерения проводилось при помощи программного обеспечения MSA (PolytecGmbH, Германия), а обработка полученных изображений и их количественный анализ осуществляли с помощью программы Polytec Losk Mouse (Polytec GmbH, Германия).
Измерение температурного коэффициента сопротивления
Определение температурного коэффициента сопротивления резистивной пленки проводилось путем измерения сопротивления пленки при температуре 298 ± 1 К с помощью омметра Щ-34, нагрева ее в камере тепла и холода “Brabender” до температуры 398 ± 1 К, выдержки при данной температуре в течение 30 мин и измерения сопротивления пленки с последующим расчетом величины температурного коэффициента сопротивления по формуле [18]:
(3)
${\text{ТКС}} = \frac{{{{R}_{2}} - {{R}_{1}}}}{{{{R}_{1}}\left( {{{T}_{2}} - {{T}_{1}}} \right)}},$Выдержка при заданной температуре в течение 30 мин осуществлялась с целью исключения влияния переходных процессов.
РЕЗУЛЬТАТЫ И ОБСУЖДЕНИЕ
На рис. 1 представлены АСМ-изображения поверхности подложки из ситалла без грунтующего покрытия. Согласно полученным АСМ-результатам, шероховатость подложек из ситалла в отношении Rz варьируется в интервале от 15.33 до 29.08 нм и является критичной для формирования тонких резистивных пленок.
Рис. 1.
АСМ-изображения поверхности подложки из ситалла на областях сканирования 30 × 30 мкм (а) и 10 × 10 мкм (б).
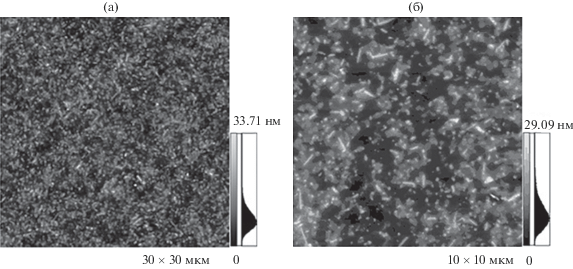
На рис. 2, 3 представлены результаты измерения шероховатости поверхности подложки из ситалла без грунтующего покрытия, полученные с помощью оптического анализатора микросистем MSA-500. Значения шероховатости подложек из ситалла, полученные с помощью оптического анализатора микросистем MSA-500, варьируются в отношении Rz в интервале от 18.88 до 27.98 нм, что в полной мере согласуется с результатами, полученными на АСМ. Таким образом, сочетание обоих методов позволило получить достоверную и важную информацию о микрорельефе поверхности.
Рис. 2.
Фрагмент визуализации шероховатости подложки из ситалла, полученный с помощью оптического анализатора микросистем MSA-500.
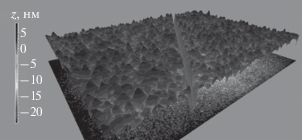
Рис. 3.
Профилограмма поверхности подложки из ситалла, полученная с помощью оптического анализатора микросистем MSA-500 на области сканирования 180 × 130 мкм.
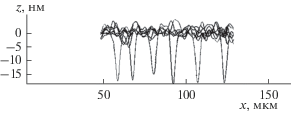
На рис. 4–6 приведены результаты измерений шероховатости поверхности подложки из ситалла с грунтующем слоем Та2О5. Нанесенные пленки Та2О5 имеют аморфную когерентную структуру и повторяют рельеф подложки.
Рис. 4.
АСМ-изображения поверхности подложки из ситалла с грунтующем слоем Та2О5 на области сканирования 30 × 30 мкм (а) и 10 × 10 мкм (б).
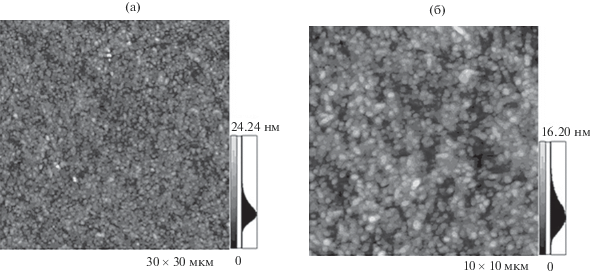
Рис. 5.
Фрагмент визуализации результата измерений шероховатости подложки из ситалла с грунтующем слоем Та2О5, полученный с помощью оптического анализатора микросистем MSA-500.
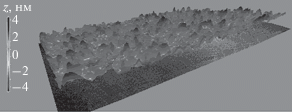
Рис. 6.
Профилограмма поверхности подложки из ситалла с грунтующем слоем Та2О5, полученная с помощью оптического анализатора микросистем MSA-500 на области сканирования 180 × 130 мкм.
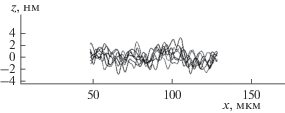
Результаты данных исследований показывают, что нанесенное покрытие уменьшает параметры шероховатости. Изменение характеристик шероховатости после нанесения покрытия, исследованное на основании профилограмм, обусловлено поверхностной диффузией и миграцией атомов при столкновении с подложкой, которая приводит к заполнению впадин и выравниванию выступов.
В табл. 1 приведены параметры шероховатости поверхности подложек из ситалла.
Таблица 1.
Параметры шероховатости поверхности подложек из ситалла до и после нанесения покрытия
Поверхность | Метод измерения | Параметры шероховатости поверхности, нм | |||
---|---|---|---|---|---|
Ra | Rz | Rpk | Rvk | ||
В исходном состоянии | АСМ | 2.42 ± 0.01 | 15.33 ± 0.02 | 25.53 ± 0.01 | 8.18 ± 0.01 |
2.85 ± 0.01 | 29.08 ± 0.02 | 20.76 ± 0.01 | 8.32 ± 0.01 | ||
Оптический метод | 1.72 ± 0.15 | 18.88 ± 0.15 | 20.39 ± 0.15 | 5.39 ± 0.15 | |
2.52 ± 0.15 | 27.98 ± 0.15 | 18.92 ± 0.15 | 6.09 ± 0.15 | ||
После нанесения покрытия | АСМ | 1.62 ± 0.01 | 11.47 ± 0.02 | 16.21 ± 0.01 | 7.98 ± 0.01 |
1.68 ± 0.01 | 8.05 ± 0.02 | 10.17 ± 0.01 | 6.03 ± 0.01 | ||
Оптический метод | 0.95 ± 0.15 | 8.98 ± 0.15 | 7.05 ± 0.15 | 5.10 ± 0.15 | |
0.86 ± 0.15 | 4.73 ± 0.15 | 6.72 ± 0.15 | 4.65 ± 0.15 |
Анализ значений параметров шероховатости показывает, что после нанесения покрытия параметры шероховатости изменяются следующим образом: среднее арифметическое отклонение профиля Ra уменьшается в ~2 раза; высота неровностей профиля по десяти точкам Rz уменьшается в ~2.7 раза; соотношение приведенных высот увеличивается в ~2 раза. Полученные результаты свидетельствуют о росте равномерности поверхности образцов.
Также следует отметить, что согласно микрореологической теории, которая заключается в том, что в процессе формирования покрытия происходит заполнение впадин шероховатости поверхности, а также трещин и пор подложки, увеличивается площадь фактического контакта. Следовательно, увеличивается число связей между покрытием и подложкой, что в свою очередь приводит к увеличению адгезии.
В табл. 2 приведены результаты расчета ТКС резистивных элементов, сформированных на подложках с разной шероховатостью. Зависимость ТКС от шероховатости поверхности подложки приведена на рис. 7.
Таблица 2.
ТКС резистивных пленок на основе сплава РС-3710
Поверхность подложки | ТКС × 10–4, К–1 | |||
---|---|---|---|---|
1 | 2 | 3 | 4 | |
Без грунтующего покрытия | 2.14 ± 0.03 | 2.50 ± 0.03 | 3.00 ± 0.03 | 3.05 ± 0.03 |
С грунтующим покрытием | 1.01 ± 0.03 | 1.25 ± 0.03 | 1.32 ± 0.03 | 1.40 ± 0.03 |
Рис. 7.
Зависимость ТКС от шероховатости поверхности подложки без покрытия (а), (в) и с покрытием (б), (г).
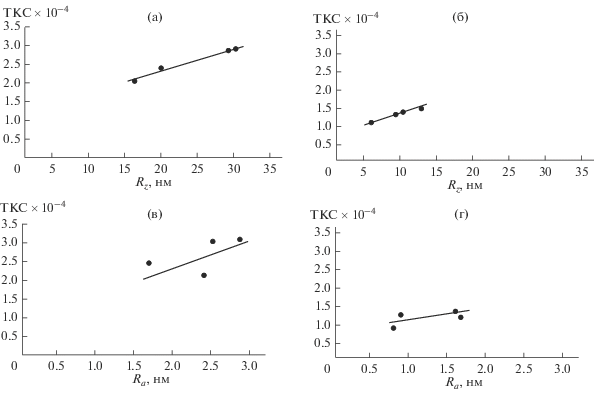
Проанализировав результаты, можно заключить, что резистивные элементы, сформированные на поверхности подложки с большей шероховатостью имеют большие значения ТКС вследствие того, что микронеровности уменьшают толщину пленок, вызывают локальное изменение электрофизических свойств пленок и повышают сопротивление, ухудшая стабильность резистивных элементов.
Для резистивных элементов величина ТКС должна быть менее 2 × 10–4 К–1, следовательно, шероховатость поверхности в отношении Rz для формирования тонких резистивных слоев должна быть не более 16 нм, что обеспечивает применение сглаживающего поверхность покрытия на основе Та2О5, обладающего хорошими диэлектрическими и адгезионными свойствами.
ЗАКЛЮЧЕНИЕ
В работе измерена микрошероховатость поверхности подложек из ситалла методами оптической микроскопии и АСМ. Сочетание обоих методов позволило получить достоверную и важную информацию о микрорельефе поверхности. Установлено, что высота микронеровностей Rz подложек из ситалла без покрытия достигает до 30 нм, что критично для формирования тонких резистивных пленок. Продемонстрировано растущее влияние шероховатости поверхности на стабильность тонкопленочных резистивных элементов, что объясняется специфичными механизмами роста пленок на шероховатой поверхности, при которых пленки имеют неравномерную толщину, различающиеся размеры зерен и большое межзеренное напряжение.
Показано, что разработанная технология формирования, сглаживающего поверхность покрытия на основе Та2О5 позволяет снизить высоту микронеровностей Rz до значений 12 нм и менее. Кроме того, увеличение соотношения приведенных высот с 0.32 до 0.62 свидетельствует о росте равномерности поверхности образцов. Установлено, что тонкопленочные резистивные элементы, сформированные на сглаженной поверхности подложки, имеют ~ в 2 раза меньший температурный коэффициент сопротивления.
Таким образом, применение сглаживающего поверхность покрытия на основе Та2О5 позволяет формировать на поверхности тонкие наноразмерные пленки и повышает стабильность тонкопленочных резисторов.
Список литературы
Данилина Т.И. Технология тонкопленочных микросхем. Томск: ТУСУР, 2006. 164 с.
Уткин В.Н., Исаков М.А., Хапугин О.Е. // Современные наукоемкие технологии. 2007. № 11. С. 38.
Макарова Ю.С., Васильев Д.Д. // Машиностроительные технологии. 2014. № 1. С. 214.
Лисовская В.В., Беляев Г.Я., Котов С.Ю. // Прикладные разработки науки и техники. 2013. № 4. С. 135.
Гимадеев М.Р. // Ученые заметки ТОГУ. 2015. Т. 6. № 4. С. 429.
Маркова Т.В., Крыжановская И.М. Шероховатость поверхности. СПб.: Изд-во Политехнического университета, 2006. 32 с.
Сазанова Т.С., Добрынин В.С., Янбиков Н.Р., Калинина А.А., Шурыгин А.Ю., Воротынцев И.В. // Коррозия: Материалы, защита. 2019. № 6. С. 42.
Zhenrong Z., Jing Z., Peifu G. // Optica Applicata. 2010. V. 40. № 4. P. 811.
Сазанова Т.С., Воротынцев А.В., Петухов А.Н., Отвагина К.В., Воротынцев И.В. Атомно-силовая микроскопия: от теории к практике. Нижний Новгород: НГТУ им. Р.Е. Алексеева, 2018. 122 с.
Усанов Д.А., Яфаров Р.К. Исследование поверхности материалов методом сканирующей туннельной микроскопии. Саратов: Изд-во Саратовского университета, 2007. 51 с.
Протопопов В.В., Валиев К.А., Имамов Р.М. // Заводская лаборатория. Диагностика материалов. 2000. Т. 66. № 1. С. 32.
Кривоносов Ю.С. Определение шероховатости подложек и тонких пленок по рассеянию рентгеновских лучей в условиях внешнего отражения: Дис. … канд. ф.-м. н.: 01.04.07. М.: МГУ, 2003. 126 с.
Невлюдов И.Ш., Жарикова И.В., Перепелица И.Д., Резниченко А.Г. // Прикладная физика. 2014. № 2/5. С. 47.
Исмаилов Т.А., Шангереева Б.А., Шахмаева А.Р. // Известия вузов. Северо-Кавказский регион. Технические науки. 2006. № 1. С. 102.
Смирнова К.И. Тонкие пленки в микроэлектронике. Томск: ТУСУР, 2007. 94 с.
Смолин В.К. // Новые промышленные технологии. 2001. № 2–3. С. 17.
Сазанова Т.С., Воротынцев И.В., Куликов В.Б., Давлетбаева И.М., Зарипов И.И. // Мембраны и мембранные технологии. 2016. Т. 6. № 2. С. 166.
Седаков А.Ю., Смолин В.К. Тонкопленочные элементы в микроэлектронике: основы проектирования и изготовления. М.: Радиотехника, 2011. 168 с.
Дополнительные материалы отсутствуют.
Инструменты
Поверхность. Рентгеновские, синхротронные и нейтронные исследования