Поверхность. Рентгеновские, синхротронные и нейтронные исследования, 2021, № 1, стр. 20-27
Синтез, особенности морфологии и формирования пленки алюмосиликата на подложке
Е. Н. Грибанов a, *, А. И. Горшков a, Е. А. Синицын b, c, Ю. В. Хрипунов a, Э. Р. Оскотская a
a Орловский государственный университет им. И.С. Тургенева
302026 Орeл, Россия
b ОЦ “Сириус”, лаборатория “Нанотехнологии”
354349 Сочи, Россия
c ОАНО “Школа “Летово”
108814 Москва, Россия
* E-mail: gribanovEN@gmail.com
Поступила в редакцию 04.02.2020
После доработки 22.05.2020
Принята к публикации 28.05.2020
Аннотация
Показана возможность синтеза пленок алюмосиликатов на поверхности подложки электрохимическим методом. Методами РСМА, ИК- и КР-спектроскопии установлена природа образующихся соединений, сделано предположение об их типологии, близкой к структурным типам алюмосиликатов MFI и FAU. Определено влияние условий синтеза (напряжение, природа электролита) на текстурные параметры пленок: толщину, морфологию и удельную площадь поверхности, а также тип и линейные размеры ее характерных элементов. Предложен химизм протекающих процессов. Полученные данные представляют интерес при исследовании свойств низкоразмерных структур, а также при получении новых функциональных материалов на основе алюмосиликатов, обладающих улучшенным комплексом свойств (каталитических, сорбционных, оптических и т.д.).
ВВЕДЕНИЕ
Алюмосиликаты благодаря своей развитой поверхности и высокой стабильности нашли применение в качестве катализаторов и осушителей газов [1–3], при получении композиционных материалов [4], в химическом анализе на стадии разделения и концентрирования аналитов [5–8], при очистке объектов окружающей среды от токсикантов различной природы [9, 10] и т.д. Свойства данного минерала во многом зависят от его текстурных характеристик [3, 11]. Особенность структуры алюмосиликатов связана с наличием в них упорядоченной системы пор, в том числе молекулярного размера. Тем не менее, поры с малым диаметром (<1 нм) затрудняют транспорт более крупных молекул внутрь минерала, что приводит к снижению эффективности использования его поверхности и накладывает ограничения на области практического применения. Одним из способов нивелирования данного эффекта и интенсификации процессов с участием алюмосиликатов является переход от массивного тела к низкоразмерным системам, например, к микро- и нанопленкам, а также организованным на их основе материалам. В тонких пленках алюмосиликатов минимизированы затруднения на проникновение молекул по системе каналов к активным центрам минерала в его объеме, возможно проявление размерного эффекта и связанные с ним изменения электронной структуры, химических и физических свойств. Известны работы [12–17], направленные на изучение возможности практического использования тонкопленочных материалов на основе алюмосиликатов в качестве высокоэффективных катализаторов, матрицы-носителя наночастиц различной природы и размера, защитных покрытий (в том числе для аэрокосмических сплавов) и микробиоцидных покрытий при изготовлении имплантов, в тонкослойной хроматографии, а также при создании тест-систем и сенсоров.
Получение микро- и нанометровых пленок алюмосиликатов на подложке проводят следующими способами [18–20]: химическое осаждение из газовой фазы (CVD), золь-гель синтез с дальнейшим нанесением пленкообразующего раствора на подложку погружением (“dip-coating”) или центрифугированием (“spin-coating”), выращивание пленок на предварительно обработанной поверхности подложки. Эффективным и простым в исполнении способом одностадийного получения наноструктур является электрохимический метод. К его достоинствам можно отнести возможность синтеза соединений с заданной природой и текстурными характеристиками путем варьирования состава электролита, состояния поверхности электродов, напряжения и температуры.
Целью настоящей работы является синтез пленок алюмосиликатов микро- и субмикронной толщины на поверхности подложки, систематическое изучение особенностей их текстурных характеристик в зависимости от величины приложенного напряжения и состава электролита.
ЭКСПЕРИМЕНТАЛЬНАЯ ЧАСТЬ
Электрохимическую реакцию проводили в двухэлектродной ячейке в потенциостатическом режиме с разделением анодного и катодного пространства солевым мостиком. Электроды из алюминиевой фольги (марка A99, толщина 100 мкм) были подготовлены согласно методике [21]. В качестве электролита выступали водные растворы силиката натрия (Na2SiO3) и гидроксида натрия (NaOH) различной концентрации. Для контроля напряжения и силы тока в системе использовали источник постоянного тока GPS 73303 и мультиметр АPPA 208. Эксперименты проводили при температуре окружающей среды 20 ± 1°С. После получения пленки промывали дистиллированной водой и сушили в течение 120 минут при температуре 105 ± 1°С.
Элементный состав образцов определяли методом рентгеноспектрального микроанализа (РСМА), при этом использовалась энергодисперсионная рентгеновская приставка INCA Energy-250 к электронному микроскопу JSM-6380LV. ИК-спектры регистрировали в области 4000–450 см–1 (ИК-фурье спектрометр ФСМ 2202) таблетированием с KBr. Спектры комбинационного рассеивания регистрировали с помощью спектрометра ИнСпектр R532+ в диапазоне 1000–140 см–1. Морфологию поверхности подложки изучали методами металлографии (микроскоп Альтами МЕТ 1М) и атомно-силовой микроскопии (NanoEducator II, NT-MDT) в полуконтактном режиме сканирования с использованием кантилеверов серии Etalon HA_NC/W2C и радиусом острия иглы ~10 нм. Толщину определяли толщиномером Horstek TC 515, обеспечивающим разрешающую способность 100 нм и точность измерения ±5%. Определение удельной площади поверхности проводили методом адсорбции метиленового синего [22].
РЕЗУЛЬТАТЫ И ИХ ОБСУЖДЕНИЕ
Было обнаружено, что при электролизе водных растворов Na2SiO3 и NaOH при постоянном напряжении в интервале от 8 до 30 В на поверхности подложки происходит формирование механически прочной пленки. Для каждого исследуемого образца пленки были получены РСМА-спектры его различных микроучастков (исследовали поверхностный и приповерхностный слой), где были обнаружены только Si, Al, O, Na (рис. 1). Картирование микроучастков изучаемых пленок показало, что все образцы однородны по распределению данных элементов.
О природе образующегося покрытия судили, сравнивая полосы поглощения его ИК- и КР-спектров с характеристическими полосами поглощения алюмосиликатов.
В ИК-спектрах пленок (рис. 2) присутствуют интенсивные полосы поглощения в области частот 900–1250 см–1 и 400–600 см–1, которые можно отнести к колебаниям внутри тетраэдров [(Al, Si)O4]-каркаса. На положение этих полос влияет отношение Si/Al в минерале. Поглощение колебаний мостиковых связей Si–O–Si(Al) представлено полосами с максимумами при 1163, 1130, 1092 см–1. Появление полос поглощения в области 953 см–1 можно интерпретировать валентными колебаниями немостиковых Si–O-связей. В данных алюмосиликатных системах полосы 940 и 913 см–1 объясняются проявлением деформационных колебаний немостиковой связи Al–O(–H). Полоса поглощения при 872 см–1 может быть отнесена к колебаниям ОН-групп, принадлежащих Si–OH или Si–O(H)–Al. К различного рода колебаниям Si–O–Al, O–Si–O, Si–O–H групп относятся полосы поглощения при 705, 580 и 452 см–1. Полоса поглощения в области 560–580 см–1, относящаяся к колебаниям по внешним связям тетраэдров [AlO4]5– и [SiO4]4– каркаса, обусловлена присутствием сдвоенных четырех, пяти и шестичленных колец в структуре. Чувствительным методом изучения каркасной структуры алюмосиликатов является КР-спектроскопия. КР-спектры пленок (рис. 3) содержат полосы поглощения в области 140–270 см–1, что характерно для алюмосиликатов с шести- и более членными циклами. На основании приведенных данных можно сделать предположение о типе образующихся алюмосиликатов, близком к структуре MFI и FAU.
Рис. 2.
ИК-спектр пленки, полученной электролизом при различном напряжении: 1 – 16, 2 – 26, 3 – 30, 4 – 8 В. Концентрации компонентов водного раствора электролита составляли: [NaOH] = 0.05 М, [Na2SiO3] = = 0.5 М.
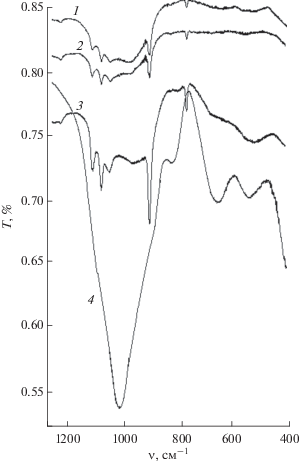
Рис. 3.
КР-спектр пленки, полученной электролизом при различном напряжении: 1 – 8, 2 – 16, 3 – 26, 4 – 30 В. Концентрации компонентов водного раствора электролита составляли: [NaOH] = 0.05 М, [Na2SiO3] = = 0.5 М.
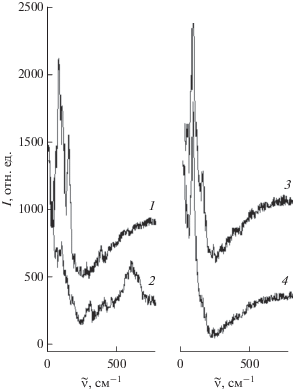
Интенсивность гетерогенных процессов зависит от состояния поверхности раздела фаз. Важным параметром пленок алюмосиликатов является размер структурных образований (кристаллитов), формирующих их поверхность. С уменьшением размера кристаллита увеличивается удельная площадь поверхности и избыточная свободная энергия, что приводит к росту химической активности системы. Типичные АСМ-изображения поверхности подложки после формирования на ней слоя алюмосиликата представлены на рис. 4. Характерными элементами поверхности являются объемные фигуры: глобулы или параллелепипеды, образующие единый каркас из пор, выступающих в качестве транспортных каналов при протекании гетерогенных процессов.
Рис. 4.
АСМ-изображения поверхности пленок алюмосиликата, полученных электролизом при различном напряжении: а – 8 В, размер изображения 20 × × 20 × 2.2 мкм; б – 30 В, размер изображения 4 × 4 × × 0.2 мкм. Концентрации компонентов водного раствора электролита составляли: [NaOH] = 0.05 М, [Na2SiO3] = 0.5 М.
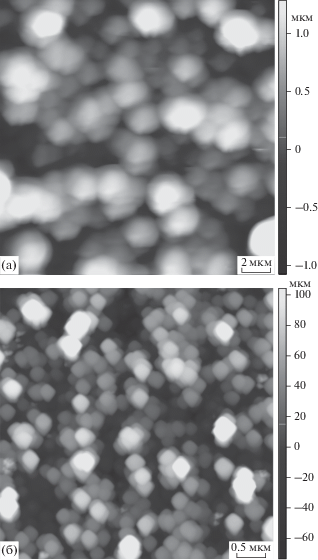
Пленки, полученные при напряжении 8 В, имеют глобулярную структуру, при этом диаметр глобул колеблется от 500 нм до 2.5 мкм. Наблюдаемый перепад высот равен ~ 3–5 мкм, а средняя арифметическая шероховатость профиля Ra, отражающая неровность поверхности, составляет ~270–310 нм. В качестве структурных элементов пленок, полученных при напряжениях 16, 26 и 30 В, выступают параллелепипеды. Для пленок, полученных при большем напряжении, перепад высот не превышает 100–200 нм при значении Ra ~ ~ 10–50 нм. При напряжении 30 В преобладают объемные фигуры, близкие к кубической форме параллелепипеды с углами ∼90°–4° (рис. 5а, 5в), при напряжении 16 В преобладают наклонные параллелепипеды с углами 105°–120° и 60°–75° (рис. 5б). При 26 В присутствуют параллелепипеды как первого, так и второго типа. Длина граней в данных структурных элементах поверхности колеблется в пределах 150–250 нм. Толщина алюмосиликатного покрытия на подложке колеблется в интервале от ~1.0 до ~18.5 мкм, а его удельная площадь поверхности по данным сорбции метиленового синего от ~250 до ~650 м2/г в зависимости от условий синтеза. Текстурные характеристики пленок в зависимости от условий их получения систематизированы в табл. 1. Из нее следует, что увеличение напряжения в системе приводит к повышению удельной площади поверхности и уменьшению толщины пленки. Увеличение концентрации NaOH в системе приводит к росту ее толщины.
Рис. 5.
АСМ-изображения параллелепипедов (размер изображения 450 × 450 × 90 нм), полученных при различном напряжении протекания электролиза: а – 26 В, б – 16 В; концентрации компонентов водного раствора электролита составляли: [NaOH] = 0.05 М, [Na2SiO3] = 0.5 М; в – профиль сечения поверхности.
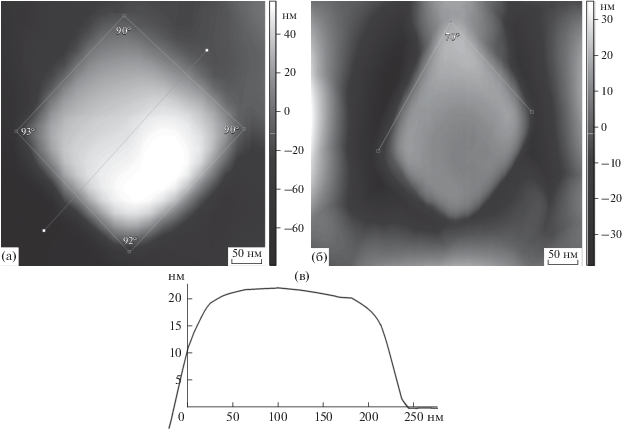
Таблица 1.
Параметры синтезированных пленок и условия их получения
U, В | [NaOH] = 0.05 М | [NaOH] = 0.10 М | ||||
---|---|---|---|---|---|---|
Толщина, мкм | Sуд, м2/г | Ra, нм | Толщина, мкм | Sуд, м2/г | Ra, нм | |
8 | 12.3 ± 0.4 | 246.9 | 281 | 18.5 ± 0.5 | 259.4 | 273 |
16 | 7.4 ± 0.3 | 290.3 | 18 | 9.6 ± 0.5 | 349.8 | 22 |
26 | 2.1 ± 0.6 | 585.2 | 16 | 2.1 ± 0.1 | 508.6 | 8 |
30 | 0.9 ± 0.4 | 648.3 | 55 | 1.0 ± 0.3 | 631.8 | 13 |
Скорость роста пленки определяется ее ионной проводимостью. График зависимости плотности тока в системе от времени электролиза при постоянном напряжении – j(t), представлен на рис. 6 и соответствует типичному виду при образовании самоорганизованных наноструктурированных оксидных пленок. В начальный момент времени формирования пленки потенциостатический режим является условным, так как перераспределение напряжения между катодом и анодом контролируется ростом высокоомного слоя алюмосиликата. Часть анодного потенциала приходится на электролит и слой пленки, другая часть – на электрохимическую реакцию и образование кислорода и водорода. Пульсации протекающего в цепи тока, связанные с образованием и всплытием пузырьков газа, отражают зависимости j(t), на начальном этапе процесса (рис. 7). После прекращения пульсаций наблюдается резкое падение плотности тока, проходящее через минимум, затем j увеличивается до максимального значения и далее уменьшается по экспоненциальному закону (рис. 6). Медленное уменьшение плотности тока связано с ограниченной диффузией ионов электролита в каналах формирующейся пористой пленки алюмосиликата.
Рис. 6.
Вид кривых анодирования при различном напряжении протекания электролиза: 1 – 26, 2 – 30, 3 – 16, 4 – 8 В. Концентрации компонентов водного раствора электролита составляли: [NaOH] = 0.1 М, [Na2SiO3] = 0.5 М.
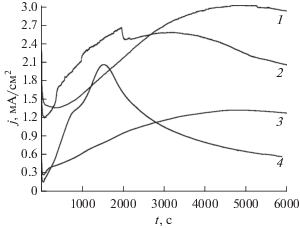
Рис. 7.
Вид кривых анодирования в начальный этап электролиза при различном напряжении: 1 – 30, 2 – 26, 3 – 16, 4 – 8 В. Концентрации компонентов водного раствора электролита составляли: [NaOH] = 0.1 М, [Na2SiO3] = 0.5 М.
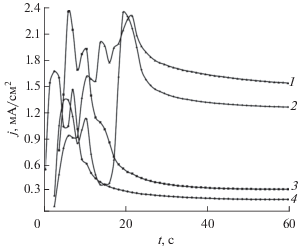
Можно предположить следующий химизм формирования пленки. Травление алюминиевой подложки в водных растворах NaOH приводит к образованию ионов ${\text{AlO}}_{2}^{ - }$ и ${\text{Al}}\left( {{\text{OH}}} \right)_{4}^{ - }{\text{:}}$
Происходит образование ямок травления, концентрация которых возрастает с увеличением приложенного напряжения и концентрации NaOH. Типичный вид поверхности алюминиевого электрода после его электрохимического травления в водном растворе NaOH при разном напряжении в течение одинакового времени, полученный методом металлографической микроскопии, приведен на рис. 8.
Рис. 8.
Металлографическое изображение поверхности анода после травления в водном растворе 0.1 М-NaOH при 8 В (а) и 26 В (б) в течение 60 мин.
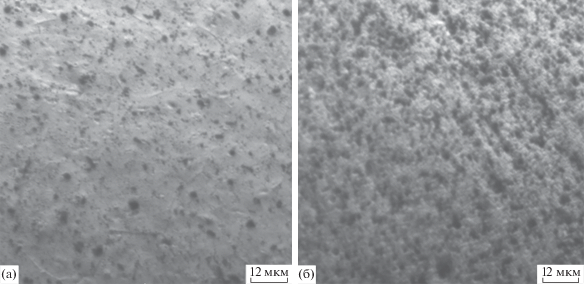
Одновременно в результате анодного растворения алюминия происходит высвобождение катионов металла в электролит:
Здесь они могут вступить в реакцию с гидроксид- или силикат- ионами:
В результате окисления воды происходит выделение кислорода, который ионизируется с образованием анионов O2–, мигрирующих к аноду, реагируя с катионами алюминия с образованием оксида алюминия:
Одновременно протекает реакция растворения оксида алюминия:
В катодном цикле происходит осаждение металла и выделение водорода:
Таким образом, на поверхности анода формируется Al2O3, выступающий в качестве основания для роста слоя алюмосиликатов. Данное предположение доказывает морфология поверхности подложки после механического снятия с нее пленки алюмосиликата (рис. 9а). Она представляет собой типичный вид пленки анодированного алюминия [24]: упорядоченная периодическая структура с узким распределением пор по размерам. При этом диаметр пор (рис. 9б) совпадает с максимальным размером диагонали параллелепипеда алюмосиликата. Следовательно, одновременно с ростом ячеек оксидного слоя Al2O3 происходят процессы, связанные с нуклеацией алюмосиликатов в приэлектродном пространстве, обусловленные наличием в нем алюминатов и силикатов [25, 26]. Можно предположить многослойную структуру пленок, в которой содержание фазы алюмосиликата возрастает от поверхности подложки к ее наружной части.
Рис. 9.
АСМ-изображение (контактная мода, фазовый контраст) поверхности анода под плёнкой алюмосиликата, полученной электролизом при напряжении 26 В и концентрации компонентов водного раствора электролита: [NaOH] = 0.1 М, [Na2SiO3] = 0.5 М, размер изображения 3 × 3 × 0.07 мкм (а); профиль сечения поверхности (б).
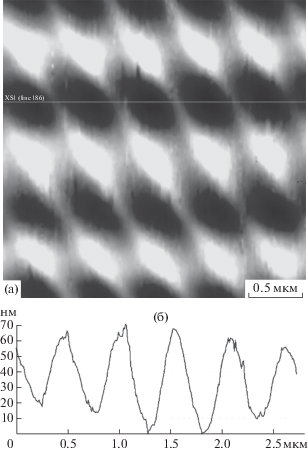
ЗАКЛЮЧЕНИЕ
В работе предложен и реализован способ электрохимического получения тонких пористых пленок алюмосиликатов микро- и субмикротолщины на алюминиевой подложке в силикатно-щелочном водном растворе. На основе данных РСМА, ИК- и КР-спектроскопии установлена природа образующихся соединений, сделано предположение об их типологии, близкой к структурным типам алюмосиликатов MFI и FAU. Систематически изучено влияние напряжения электролиза в интервале 8–30 В и природы электролита на текстурные характеристики пленок. Установлено, что их толщина колеблется в интервале от ~1.0 до ~18.5 мкм, а удельная площадь поверхности от ~250 до ~650 м2/г в зависимости от условий синтеза. Методом атомно-силовой микроскопии изучена морфология поверхности пленок: аморфная глобулярная структура при напряжении 8 В и кристаллическая при большем напряжении. Предложен механизм формирования алюмосиликатного покрытия, заключающийся в формировании на поверхности анода ячеек Al2O3, выступающих в качестве основания для роста слоя алюмосиликатов. Полученные пленки отличаются достаточной механической прочностью и представляют интерес при создании новых функциональных материалов, обладающих улучшенным комплексом свойств (каталитических, сорбционных, оптических и т.д.).
Список литературы
Feng-Shou Xiao, Xiangju Meng. Zeolites in Sustainable Chemistry: Synthesis, Characterization and Catalytic Applications. Berlin: Springer, 2016. 485 p.
Доморощина Е.Н., Кравченко Г.В., Кузьмичева Г.М., Чумаков Р.Г. // Поверхность. Рентген., синхротр. и нейтрон. исслед. 2019. № 2. С. 56.
Рабо Дж. Химия цеолитов и катализ на цеолитах. Т. 1. М.: Мир, 1980. 506 с.
Lopes A.C., Martins P., Lanceros-Mendes S. // Prog. Surf. Sci. 2014. V. 89. P. 239.https://doi.org/10.1016/j.progsurf.2014.08.002
Poniedzialek K., Bielicka-Daszkiewicz K., Sandomierski M., Voelkel A. // Anal. Lett. 2017. V. 51. № 13. P. 2026.https://doi.org/10.1080/00032719.2017.1407329
Jamshidi R., Afzali Z., Afzali K. // Asian J. Chem. 2009. V. 21. № 5. P. 3381.https://doi.org/10.1016/j.cej.2009.10.029
Oskotskaya E.R., Gribanov E.N. // XX Mendeleev Congress on General and Applied Chemistry. V. 4: Abstracts. Ekaterinburg: Ural Branch of the Russian Academy of Sciences, 2016. P. 366.
Оскотская Э.Р., Грибанов Е.Н., Саунина И.В. // Журн. аналит. химии. 2017. Т. 72. № 2. С. 170.
Huai-Te Shu, Danyun Li, Alfred A. Scala, Hua Ma Yi. // Sep. Purif. Technol. 1997. V. 11. № 1. P. 27.
Crini G., Lichtfouse E. Green Adsorbents for Pollutant Removal: Fundamentals and Design. Switzerland: Springer International Publishing, 2018. 399 p.
Ruren Xu, Wenqin Pang, Jihong Yu and etc. Chemistry of Zeolites and Related Porous Materials: Synthesis and Structure. Singapore: John Wiley & Sons (Asia), 2007. 679 p.
Lew C.M., Cai R., Yan Y. // Accounts Chem. Res. 2010. V. 43. № 2. P. 210.https://doi.org/10.1021/ar900146w
Tiwari S.K., Mishra T., Gunjan M.K., Bhattacharyya A.S., Singh T.B., Singh R. // Surf. Coat. Technol. 2007. V. 201. P. 7582.https://doi.org/10.1016/j.surfcoat.2007.02.026
Binions R., Davies H., Afonja A. et al. // J. Electrochem. Soc. 2009. V. 156. P. 46.
Vilaseca M., Coronas J., Cirera A. et al. // Catal. Today. 2003. V. 82. P. 179.
Hugon O., Sauvan M., Benech P. et al. // Sens. Actuat. B-Chem. 2000. V. 67. P. 235.
Hauck H., Schulz M. // Chromatographia. V. 57. 2003. P. 331.
Vernal N. Richards, Jason K. Vohs, Bradley D. Fahlman // J. Am. Ceram. Soc. 2005. V. 88. № 7. P. 1973.
Adamczyk A. // Mat. Sci. 2015. V. 33 № 4. P. 732.https://doi.org/10.1515/msp-2015-0109
Gutmann E., Levin A., Pommrich I. et al. // Cryst. Res. Technol. 2005. V. 40. № 1–2. P. 114. https://doi.org/10.1002/crat.200410314
Jinsub Choi. Fabrication of monodomain porous alumina using nanoimprint lithography and its applications: Dissertation…Doktor-Ingenieur. 2004. 103 p.
Jacobs P., Derouane E., Weitkamp J. // J. Chem. Soc., Chem. Commun. 1981. № 12. P. 591.
Yi Yu, Guang Xiong, Can Li et al. // Micropor. Mesopor. Mater. 2001. V. 46. № 1. P. 23.
Росляков И.В., Куратова Н.С., Кошкодаев Д.С., Hermida Merino D., Лукашин А.В., Напольский К.С. // Поверхность. Рентген., синхротр. и нейтрон. исслед. 2016. № 2. С. 39.
Almjasheva O.V., Gusarov V.V. // Nanosyst.-Phys. Chem. Math. 2014. V. 5. № 3. P. 405.
Valtchev V., Mintova S., Tsapatsis M. Ordered Porous Solids. France: Elsevier Science, 2008. 800 p.
Дополнительные материалы отсутствуют.
Инструменты
Поверхность. Рентгеновские, синхротронные и нейтронные исследования