Поверхность. Рентгеновские, синхротронные и нейтронные исследования, 2021, № 11, стр. 86-89
Влияние шероховатости подложки на точность измерения методом вторичной ионной масс-спектрометрии распределения примеси по глубине
А. С. Гынгазов a, А. П. Суржиков b, С. А. Гынгазов b, *
a Акционерное общество “Научно-исследовательский, проектно-конструкторский
и технологический кабельный институт (НИКИ)”
634003 Томск, Россия
b Национальный исследовательский Томский политехнический университет
634050 Томск, Россия
* E-mail: ghyngazov@tpu.ru
Поступила в редакцию 07.02.2021
После доработки 25.05.2021
Принята к публикации 30.05.2021
Аннотация
Знание о распределении концентрации примеси в приповерхностных слоях твердых тел имеет большое значение для технологий модификации материалов методами поверхностной обработки. Для этих целей перспективно использовать метод вторичной ионной масс-спектрометрии. В силу того, что глубины анализируемых этим методом приповерхностных слоев не превышают нескольких микрон, актуальной становится задача снижения влияния микронеровностей анализируемой поверхности на результаты измерения распределения концентрации примеси по глубине. На примере системы “циркониевая керамика–тонкая пленка алюминия” решаются методические вопросы минимизации влияния микрорельефа поверхности керамики на измерение распределения ионов примеси алюминия по глубине образцов после термического отжига. Показано, что точность измерений возрастает на порядок и более, если в дополнение к основному измерению образца после термического отжига проводить измерение базового образца, идентичного контрольному образцу, до проведения термического отжига. Искомое распределение ионов примеси по глубине образца определяется вычитанием из распределения примеси в контрольном образце распределения, полученного для базового образца.
ВВЕДЕНИЕ
Состояние поверхности твердых тел во многом определяет их прочностные и функциональные свойства. Большое развитие получили работы по направленной модификации материалов с использованием диффузионного легирования [1], облучения ускоренными ионами [2, 3] и электронами [4, 5]. При отработке данных технологий большое значение приобретают методы исследования поверхности твердых тел. Среди наиболее распространенных методов следует отметить инфракрасную фурье-спектроскопию [6], растровую электронную микроскопию [7], рентгеноструктурный анализ [8], атомно-силовую микроскопию [9], спектроскопию комбинационного рассеяния [10]. Для решения задач материаловедения важно иметь информацию о распределении примесных элементов в приповерхностном тонком слое изделия. Для этих целей могут быть применены методы электронной оже-спектроскопии [11] и вторичной ионной масс-спектрометрии (ВИМС) [12]. По сравнению с электронной оже-спектроскопией метод ВИМС более предпочтителен для исследования глубинных профилей диффузанта в силу большей скорости травления материала по глубине. Как правило, для обеспечения высокой скорости поверхностного травления используют ионы аргона. В основе метода ВИМС лежит масс-спектрометрическая регистрация выбиваемых с поверхности вторичных ионов. Перспективность использования метода ВИМС была показана при определении концентрационных профилей примесей по глубине щелочно-галоидных кристаллов [13] и оксидной керамики [14]. Этот метод обладает высокой чувствительностью и может быть использован для исследования диффузии примесей в данных материалах. Диффузионные параметры получают аппроксимацией экспериментального концентрационного профиля уравнением Фика [15] с граничными условиями, соответствующими условиям эксперимента. В этой связи особое внимание следует уделять точности определения искомого концентрационного профиля примеси. Кроме проблем обработки сигнала [16] возникают трудности, обусловленные самим процессом ионного травления и проявлением размерных факторов. При ионном травлении диэлектрика происходит накопление заряда на его поверхности, что резко снижает эффективность травления. В современных масс-спектрометрах накапливаемый на поверхности подложки положительный заряд снимают дополнительной электронной обработкой. Размерные эффекты проявляются в том, что глубина травления исследуемой поверхности, которая обычно составляет 1–5 мкм, сравнима с ее шероховатостью. Даже на идеально полированных поверхностях присутствуют нарушения в виде микроострий и царапин. Поскольку травящий ионный пучок направлен под углом к поверхности, эти дефекты затеняют часть исследуемой области, что приводит к искажению определяемого в эксперименте концентрационного профиля элементов. Это особенно должно проявляться при измерениях концентрационных профилей примесей, попавших в объем материалов в результате диффузии ионов из нанесенных на их поверхность пленочных покрытий. Во время измерений ионный пучок первоначально стравливает пленку, и только после этого идет травление основной матрицы и определяется концентрация диффузанта по глубине. Наличие затененных участков проводит к тому, что во время травления основной матрицы одновременно регистрируется сигнал от диффузанта и сигнал, обусловленный вкладом остатков пленочного покрытия в затененных местах. В силу малой глубины проникновения диффузанта ошибка в определении истинного концентрационного профиля примеси может быть катастрофически большой, что может свести на нет преимущества метода ВИМС. К сожалению, даже современные приборы ВИМС не предусматривают возможность устранения или компенсации размерных эффектов. Можно предложить два способа их устранения. Первый заключается в улучшении качества полировки, что крайне трудно реализовать на практике. К тому же нанесенные на идеально гладкую поверхность тонкопленочные покрытия, как правило, обладают определенным микрорельефом, зависящим от материала подложки и условий нанесения (температура подложки, скорость осаждения). В качестве альтернативы мог бы быть использован предлагаемый авторами второй способ, основанный на учете исходной шероховатости подложки при обработке экспериментальных данных, полученных методом ВИМС.
В настоящей работе на примере керамики на основе диоксида циркония с тонкопленочным алюминиевым покрытием рассматривается новый для метода ВИМС подход, основанный на компенсации вклада микронеровностей в измерение концентрационного профиля, сформированного в керамике во время диффузионного отжига.
МАТЕРИАЛЫ И ТЕХНИКА ЭКСПЕРИМЕНТА
Для компенсации вклада шероховатости предложено проводить измерения двух идентичных керамических образцов, на поверхность которых нанесена тонкая пленка примеси. Важно отметить, что необходимым требованием является равномерная шероховатость поверхности подложки и высокая равномерность нанесенного тонкопленочного покрытия по толщине. Один из образцов без каких-либо дополнительных воздействий на него используют как базовый для измерений ВИМС. Это измерение имеет целью определение вклада шероховатости в получаемое методом ВИМС распределение диффузанта по глубине. Второй образец подвергают термическому отжигу и используют для контрольного измерения ВИМС с целью получения информации о распределении диффузанта по глубине. Исходя из факта, что во время термического отжига толщина пленочного покрытия практически не изменяется, можно считать, что вклад шероховатости в результаты измерений концентрационных профилей ионов алюминия будет одинаковым для обоих испытуемых образцов. Отличия концентрационного профиля отожженного образца от концентрационного профиля образца, не подверженного термическому отжигу, будут обусловлены вкладом распыленных из объема керамики ионов примеси, продиффундировавших вглубь керамики во время отжига. В данных условиях эксперимента искомый концентрационный профиль диффузанта можно получить вычитанием профиля неотожженного образца из профиля отожженного образца.
МАТЕРИАЛЫ И МЕТОДЫ
В качестве исходного сырья для изготовления образцов циркониевой керамики использовали ультрадисперсные порошки состава 97ZrO2–3Y2O3, полученные плазмохимическим методом [17]. Порошковые компакты в виде таблеток получали методом одноосного прессования с помощью пресса ПГр-10. Спекание прессовок проводили в атмосферных условиях в объеме печи сопротивления типа СНОЛ. Температура спекания и время спекания были 1400°С и 3 ч соответственно. Готовые образцы циркониевой керамики имели диаметр 9 мм и толщину 2.7 мм. Их пикнометрическая плотность и пористость были 5.7 г/см3 и 6.5% соответственно. Перед нанесением тонкой металлической пленки измеряли шероховатость поверхности образцов с помощью Профилометра 296. Стандартное отклонение составляло менее 10% от среднего значения средней шероховатости, шероховатость всех испытуемых образцов – 0.4 мкм.
Тонкую пленку алюминия на поверхность двух керамических образцов наносили одновременно методом термического испарения навески алюминия, помещенной в вольфрамовый тигель. Толщину нанесенной пленки оценивали, исходя из массы навески Мн, расстояния от испарителя до держателя R и плотности вещества наносимой металлической пленки ρ с использованием выражения:
Толщина нанесенной на керамические образцы пленки алюминия была 130 нм. Диффузионный отжиг керамического образца с нанесенной пленкой алюминия проводили в объеме дилатометра DIL-402C при остаточном давлении 2 × 10–5 мм рт. ст. в течение 1 ч. Указанные условия предотвращали окисление пленки алюминия во время отжига.
После этого последовательно образцы керамики, не подвергнутой и подвергнутой диффузионному отжигу, исследовали методом ВИМС. Для измерений использовали масс-спектрометр PHI 6300 (США). При обработке экспериментальных данных предполагали, что интенсивность тока вторичных ионов пропорциональна их концентрации.
РЕЗУЛЬТАТЫ И ИХ ОБСУЖДЕНИЕ
Экспериментальные распределения ионов алюминия по глубине травления для неотожженного и отожженного образца представлены на рис. 1 (кривые 1 и 2 соответственно). Графики построены путем обработки временных спектров травления с учетом скорости травления образцов по глубине. Скорость травления определяли, измеряя с помощью профилометра глубину кратера травления. Кривая 3 получена вычитанием из кривой 2 кривой 1. Она представляет собой распределение продиффундировавших по глубине циркониевой керамики ионов алюминия. Благодаря указанному способу обработки влияние на измерение ионов алюминия из затененных неровностями областей сводится к минимуму.
Рис. 1.
Экспериментальные распределения ионов алюминия по глубине травления неотожженного (1) и отожженного (2) образцов и по глубине диффузии в циркониевой керамике (3).
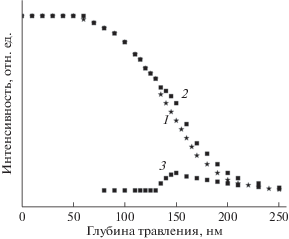
Кривую 3 на рис. 1 использовали для определения коэффициента диффузии D ионов алюминия в исследуемом образце циркониевой керамики. Для этого участок кривой 3 правее точки максимума аппроксимировали решением уравнением Фика (2), описывающим распределение ионов алюминия в объеме подложки на глубине x в случае, когда диффузия осуществляется из неограниченного источника в полубесконечный кристалл в течение времени t при заданной температуре и исходной концентрации ионов алюминия в тонкой пленке C0 [15]:
Получен коэффициент диффузии ионов алюминия D = 3.0 × 10–10 см2/с. Определение коэффициента диффузии алюминия путем аппроксимации экспериментальной кривой 2 (рис. 1) дало значение D = 2.0 × 10–9 см2/с. То есть неучет шероховатости поверхности приводит к завышению коэффициента диффузии на порядок.
ЗАКЛЮЧЕНИЕ
В ходе исследований решены вопросы методического плана, позволяющие компенсировать влияние микрорельефа подложки при построении концентрационных профилей диффузанта в керамике методом ВИМС. Установлено, что точность определения концентрационных профилей методом ВИМС сильно зависит от шероховатости керамической подложки. Для компенсации вклада микрорельефа в измерения достаточно проводить два измерения идентичных по свойствам и состоянию микрорельефа подложек с нанесенной на их поверхность тонкой пленкой диффузанта. Одна из подложек не подвергается дополнительной обработке (базовое измерение), а другая предварительно подвергается диффузионному отжигу (контрольное измерение). Искомый концентрационный профиль диффузанта по глубине керамики определяют вычитанием из контрольного измерения базового. Указанные действия дают возможность увеличить точность измерения диффузионных коэффициентов на порядок и более.
Список литературы
Peng C., Gao X., Wu L. et al. // Appl. Phys. Lett. 2019. V. 114(1). P 011905. https://doi.org/10.1063/1.5054954
Zhong H., Zhang J., Shen J., Liang G., Zhang S., Xu M., Yu X., Yan S., Remnev G.E., Le X. // Vacuum. 2020. V. 179. 109541. https://doi.org/10.1016/j.vacuum.2020.109541
Konusov F., Pavlov S., Lauk A., Tarbokov V., Karpov S., Karpov V., Gadirov R., Kashkarov E., Remnev G. // Surf. Coat. Technol. 2020. V. 389. 125564. https://doi.org/10.1016/j.surfcoat.2020.125564
Gromov V.E., Gorbunov S.V., Ivanov Y.F., Vorobiev S.V., Konovalov S.V. // J. Surf. Invest.: X-Ray, Synchrotron Neutron Tech. 2011. V. 5. № 5. P. 974. https://doi.org/10.1134/S1027451011100107
Zhang C., Lv P., Xia H., Yang Z., Konovalov S., Chen X., Guan Q. // Vacuum. 2019. V. 167. P. 263. https://doi.org/10.1016/j.vacuum.2019.06.022
Strazdaite S., Navakauskas E., Kirschner J., Sneideris T., Niaura G. // Langmuir. 2020. V. 36. № 17. P. 4766. https://doi.org/10.1021/acs.langmuir.9b03826
Choudhary O.P., Priyanka // Int. J. Curr. Microbiol. Appl. Sci. 2017. V. 6. № 5. P.1877. https://doi.org/10.20546/ijcmas.2017.605.207
Grozdanov A., Paunovic P., Nikodinovska V.V., Dimitrov A.T. // Mater. Sci. Eng. 2019. V. 3. № 4. P. 141. https://doi.org/10.15406/mseij.2019.03.00105
Palve A.M., Garje S.S. // Semicond. Sci. Technol. 2021. V. 36. № 2. P. 025007. https://doi.org/10.1088/1361-6641/abcdfa
Kurouski D., Dazzi A., Zenobi R., Centrone A. // Chem. Soc. Rev. 2020. V. 49. № 11. P. 3315. https://doi.org/10.1039/c8cs00916c
Gunawardane R.P., Arumainayagam C.R. // Handbook of Applied Solid State Spectroscopy. / Ed. Vij D. Boston: Springer, 2006. https://doi.org/10.1007/0-387-37590-2_10
Kambalathmana H., Flatae A.M., Hunold L., Sledz F., Müller J., Hepp M., Schmuki P., Killian M.S., Lagomarsino S., Gelli N., Sciortino S., Giuntini L., Wörner E., Wild C., Butz B., Agio M. // Carbon. 2021. V. 174. P. 295. https://doi.org/10.1016/j.carbon.2020.12.031
Gyngazov S.A., Surzhikov A.P., Frangul’yan T.S., Chernyavskii A.V. // Russ. Phys. J. 2002. V. 45. № 8. P. 753. https://doi.org/10.1023/A:1021956128414
Ghyngazov S.A., Chernyavskii A.V., Petrova A.B. // Russ. Phys. J. 2017. V. 60. № 5. P. 812. https://doi.org/10.1007/s11182-017-1143-2
Бенье Ф. // Физика электролитов. Ред. Хладик Дж. М.: Мир, 1978. С. 218.
Кудрявцев Ю.А. // Поверхность. Рентген., синхротр. и нейтрон. исслед. 2020. № 1. С. 106. https://doi.org/10.31857/S1028096020010094
Ларин В.К., Кондаков В.М., Малый Е.Н. Матюха В.А., Дедов Н.В. и др. // Изв. вузов. Цветная металлургия. 2003. № 5. С. 59.
Дополнительные материалы отсутствуют.
Инструменты
Поверхность. Рентгеновские, синхротронные и нейтронные исследования