Поверхность. Рентгеновские, синхротронные и нейтронные исследования, 2021, № 11, стр. 5-10
Поверхность и структура аморфных сплавов после барической обработки
Е. Ю. Постнова a, *, Г. Е. Абросимова a, **, А. С. Аронин a, ***
a Институт физики твердого тела РАН
142432 Московская область, Черноголовка, Россия
* E-mail: postnova@issp.ac.ru
** E-mail: gea@issp.ac.ru
*** E-mail: aronin@issp.ac.ru
Поступила в редакцию 10.04.2021
После доработки 22.05.2021
Принята к публикации 28.05.2021
Аннотация
Методом растровой электронной микроскопии исследовали морфологию поверхности аморфных сплавов Co65Si12B9Ni10Nb4, Co67Si12B9Fe7Nb5, Co79Si12B9, Co67Fe5B20Nb8, Co67Si13B9Fe1Mn4, Co56Fe16B20Ti8, подвергнутых давлению 5 ГПа. Под действием приложенного давления на поверхности образцов появились ступеньки, образующиеся при выходе полос сдвига на поверхность. Определена высота ступенек. Для определения геометрических характеристик ступенек использовали измерения ступенек на изображениях, полученных при разных углах падения пучка электронов на образцы. Образец крепился на специальном держателе, с помощью которого осуществлялся наклон образца. Съемки проводились при положении плоскости образца, перпендикулярном падающему пучку электронов и под углом в 45°. Высота ступенек в образцах варьировалась от 20 до 400 нм. Ступеньки образовывали системы, расположенные под углом друг к другу. Расположение полос по поверхности образцов было неравномерное. Структура деформированных образцов исследована с помощью метода рентгенографии. Обнаружено, что в сплавах с большой высотой ступенек наблюдалась частичная кристаллизация с образованием нанокристаллов, сплавы с малой высотой ступенек осталась аморфными.
ВВЕДЕНИЕ
Создание новых материалов и технологий основывается на фундаментальных исследованиях структуры и свойств и их корреляции. Принципиальным является определение процессов, приводящих к образованию тех или иных структур, и, в конечном счете, к образованию материалов с повышенными физико-химическими свойствами, что, в свою очередь, приводит к разработке новых приборов и устройств. Абсолютное большинство свойств материалов зависит от их структуры (атомной, магнитной, электронной и т.д.). К перспективным материалам, несомненно, относятся аморфные металлические сплавы (АМС) или, другими словами, металлические стекла и формирующиеся на их основе нанокристаллические сплавы (НКС). Хотя с момента получения первого металлического стекла прошло уже много лет, интерес к ним не уменьшается. Во многом это связано с развитием и постоянным появлением новых материалов и композиций. Интерес к металлическим стеклам был обусловлен как их необычной структурой, совершенно нетипичной для сплавов, так и целым комплексом выдающихся физико-химических свойств. Среди аморфных сплавов есть высокопрочные, магнитно-жесткие и магнитно-мягкие, коррозионностойкие материалы. АМС являются неравновесными материалами. Они обладают удивительной структурой: в них нет кристаллической решетки, т.е. дальнего порядка в расположении атомов (наблюдается структура, более характерная для жидкости), и в то же время они оказываются стабильными при комнатной температуре. Такая необычность структуры привела к совершенно иным (по сравнению с кристаллической структурой) ее изменениям при различных внешних воздействиях. Частично закристаллизованные металлические стекла (своеобразные композиты, состоящие из аморфной и кристаллических фаз) также обладают рядом очень хороших свойств, отличающихся от свойств и аморфных и кристаллических материалов. Важно отметить, что аморфное состояние для металлических стекол является состоянием нестабильным, при нагреве или вылеживании в них может происходить распад аморфной фазы с естественной деградацией свойств. Поэтому и с точки зрения фундаментальной науки, и с точки зрения перспективы промышленного использования новых материалов чрезвычайно важно исследование как собственно структуры аморфной фазы в металлических сплавах, так ее стабильности, т.е. установление температурно-деформационно-временных интервалов перехода в частично-кристаллическое или полностью кристаллическое состояние, а также корреляции структуры и свойств материала.
Одной из самых важных предпосылок пристального изучения структуры и эволюции структуры АМС при внешних воздействиях является то, что АМС могут быть основой для получения наноструктур, обладающих выдающимися свойствами (магнитными, механическими, электрохимическими). Металлические наноструктурные материалы могут быть получены методом контролируемой кристаллизацией АМС, при этом переход из аморфного в нанокристаллическое состояние происходит при нагреве или отжиге аморфных сплавов и параметры возникающей наноструктуры регулируются условиями обработки. Этот метод оказался перспективным для получения материалов самого различного назначения (магнитных, износостойких и др.). Поскольку процесс кристаллизации обычно можно остановить на любой стадии, то появляется возможность менять в широких пределах параметры образующейся структуры (варьируя, например, скорость нагрева, температуру отжига и т.д.). Образование кристаллов происходит в неупорядоченной среде, казалось бы, как и при охлаждении жидкости, но фундаментальное отличие состоит в том, что аморфный сплав – твердый. Из этого следует, что образование кристаллов происходит в поле напряжений (плотность кристаллов и аморфного сплава разная), которые могут определять фазовый состав, морфологию и расположение кристаллов.
Еще один способ получения нанокристаллических материалов связан с применением деформационного воздействия. Применение различного типа деформационного воздействия к аморфным материалам дает возможность получения новых композиций НКС (в том числе НКС, которые не могут быть получены традиционными способами с помощью термообработки), а также позволяет получать нанокристаллические образцы большего размера. К настоящему времени методами интенсивной пластической деформации (кручения под высоким давлением) была сформирована нанокристаллическая структура в ряде систем (Fe–Si–B, Ni–Ti–Cu, Fe–B, Nd–Fe–B и др.). Во многих НКС расположение нанокристаллов, образующихся при деформации, коррелирует с расположением полос сдвига.
Пластическая деформация АМС протекает по-разному в разных температурных интервалах: при низких температурах – гетерогенно путем образования и распространения полос сдвига, при высоких (в окрестностях и выше температуры стеклования) – гомогенно путем вязкого течения. При высоких напряжениях и сравнительно низких температурах деформация происходит гетерогенно и является очень сильно локализованной. В результате деформирования образуются полосы сдвига (толщина полос сдвига составляет, как правило, несколько нанометров или десятков нанометров [1]), их ориентация близка к ориентации максимальных сдвиговых напряжений [2]. Материал в полосе сдвига ведет себя подобно жидкости и содержит повышенную концентрацию свободного объема, т.е. увеличенное среднее расстояние между атомами [3, 4].
На поверхности образца полосы сдвига проявляются в виде ступенек, образующихся в местах выхода полос сдвига на поверхность. Характеристики этих ступенек исследовались рядом авторов [5, 6], и на первых этапах исследований считалось, что их толщина составляет 5–20 нм [7–12]. В ряде случаев деформация может приводить к ветвлению полос сдвига [11, 13]. Более поздние исследования показали, что ситуация может быть более сложной: толщина полосы сдвига может быть существенно больше указанных выше значений [3, 8, 13–15], изменения структуры аморфной фазы могут распространяться на большие расстояния от полосы, толщина и изменение плотности материала вдоль полосы зависят от положения полосы сдвига в образце. Авторы [16] предположили, что после деформации методом кручения под давлением образец может полностью состоять из полос сдвига и зон воздействия полос сдвига. Авторы [13] показали, что изменение структуры вокруг полосы может простираться на расстояние до 200 нм, причем саму полосу сдвига следует рассматривать не как один наноразмерный дефект, а как множество областей, в которых произошел локальный сдвиг. Однако сформировавшихся представлений о распределении зон деформации и полос сдвига в деформированном образце в настоящее время нет.
Известно [17–19], что полосы сдвига являются местами облегченного зарождения нанокристаллов. В связи с указанным выше, настоящая работа посвящена исследованию изменений структуры аморфных сплавов разного состава на основе Co под действием высокого давления (без кручения) и установлению связи между характеристиками полос сдвига и нанокристаллизацией.
МАТЕРИАЛЫ И МЕТОДЫ ИССЛЕДОВАНИЯ
Исследовали группу аморфных сплавов, полученных в виде лент методом скоростной закалки расплава со скоростью охлаждения 106 К/с. В базовый состав Co–Si–B были внесены 1–20 ат. % Fe, Nb, Ti, Ni, Mn. Состав сплавов контролировали методом рентгеновского микроанализа.
Образцы всех составов одновременно подвергали барической обработке при давлениях 5 ГПa. При проведении барической обработки все исследуемые образцы последовательно закладывались в ячейку высокого давления; средой, передающей давление, служил порошок гексагонального нитрида бора. При этих условиях воздействия были близкими к гидростатическим. Структуру образцов исследовали методами рентгенографии, структуру поверхности – методом растровой электронной микроскопии (РЭМ). При исследовании поверхности основное внимание уделялось измерению высоты и ширины ступенек, образующихся при выходе полос сдвига на поверхность. Для определения геометрических характеристик ступенек измерение каждого объекта проводилось при разных углах относительно регистрирующего детектора. Детектор расположен в колонне электронного микроскопа и регистрирует электроны, вылетающие из образца в направлении, перпендикулярном поверхности. Образец крепился на специальном держателе, с помощью которого осуществлялся наклон образца. Съемки проводились при положении плоскости образца, перпендикулярном падающему пучку электронов образца, и под углом Δβ = π/4 радиан. Таким образом снималась стереопара, по которой можно рассчитать высоту ступеньки. Высота ступеньки вычислялась по формуле [20]:
где Δβ − угол дополнительного наклона образца в микроскопе, y – ширина полосы сдвига в исходном положении, х – ширина этой же полосы сдвига в образце, наклоненном на угол Δβ. В данном случае Δβ = π/4 радиан, поэтому формула для расчета высоты ступеньки приобретает вид:Рентгеноструктурные исследования проводились на дифрактометре SIEMENS D-500 с использованием CоKα-излучения. При обработке спектров использовались специальные программы, позволяющие проводить сглаживание, коррекцию фона, разделение перекрывающихся максимумов и др. Размер образующихся нанокристаллов определялся по данным рентгенографии. Оценка размера нанокристаллов по полуширине дифракционной линии проводилась с использованием известной формулы Селякова–Шеррера [21].
РЕЗУЛЬТАТЫ И ОБСУЖДЕНИЕ
На рис. 1 представлена микрофотография поверхности аморфного сплава Co65Si12B9Ni10Nb4 после барической обработки при 5 ГПа. Видно, что на поверхности присутствуют многочисленные ступеньки, образовавшиеся в результате выхода на поверхность полос сдвига. Из этого и аналогичных изображений поверхности других образцов после барической обработки следует, что в образцах прошла пластическая деформация. Следует отметить, что для образования полос сдвига нужны сдвиговые напряжения. Если условия деформации были полностью гидростатическими, то таких полос и ступенек на поверхности образцов быть не должно. Поскольку они наблюдаются, то условия деформации были не совсем гидростатическими.
Рис. 1.
РЭМ-изображение поверхности образца Co65Si12B9Ni10Nb4 после барической обработки (Р = 5 ГПа).
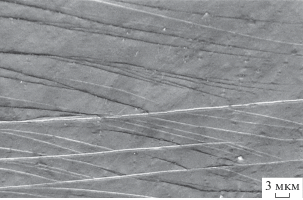
На РЭМ-изображениях (рис. 1–3) видно, что ступеньки имеют разный размер и расположение. Условно их можно разделить на первичные (самые большие) и вторичные (они имеют меньшую толщину и расположены под углом к первичным полосам сдвига). Расстояние между большими ступеньками в образцах меняется в диапазоне от 1.5 до 30 мкм, расстояние между вторичными – от 0.2 до 2 мкм. Подобные ступеньки (различающиеся геометрическими параметрами и частотой расположения в образце) присутствовали во всех исследованных образцах. Так как деформация была очень неоднородная, распределение ступенек по поверхности также неоднородное. Видимо, максимальная их частота наблюдалась в местах образцов, соответствующих максимальным сдвиговым напряжениям. Как отмечалось выше, полосы сдвига являются местами локализации пластической деформации в образце. Как известно [1, 22, 23], свойства и структура аморфной фазы в полосе сдвига полосы отличается от свойств и структуры окружающей аморфной фазы. Аморфная фаза в полосе более разупорядочена, в ней более высокая концентрации свободного объема. Эти причины определяют в полосе сдвига более высокие параметры массопереноса, существенно увеличивая коэффициент диффузии [24]. Более высокие параметры массопереноса могут приводить к образованию нанокристаллов в аморфной фазе при деформации. Такие примеры известны, причем образование нанокристаллов в полосах сдвига наблюдались даже при комнатной температуре после окончания деформирования [17, 19]. При деформации вследствие локализации пластической деформации в полосах сдвига может происходить и разогрев полосы сдвига [25].
Рис. 2.
РЭМ-изображение поверхности образца Co67Si12B9Fe7Nb5 после барической обработки (Р = 5 ГПа).
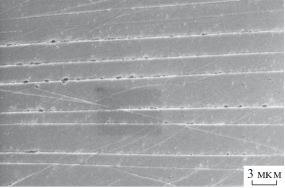
Высота ступеньки на поверхности образца характеризует степень деформации. Высота ступенек была определена для образцов следующих составов: Co65Si12B9Ni10Nb4, Co67Si12B9Fe7Nb5, Co79Si12B9, Co67Fe5B20Nb8, Co67Si13B9Fe1Mn4, Co56Fe16B20Ti8. На рис. 4, 5 показано одно и то же место образца Co67Fe5B20Nb8 в исходном положении (пучок электронов перпендикулярен поверхности) и при наклоне образца на 45°. Видно, что в первом положении размер ступеньки составляет 94 нм, в наклоненном – 163 нм. Определенная по формуле (2) высота ступеньки составляет 31 нм.
Рис. 5.
РЭМ-изображение поверхности образца Co67Fe5B20Nb8 (наклон 45 градусов). Ширина ступеньки указана.
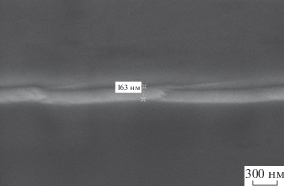
Максимальная средняя высота ступеньки наблюдалась в сплаве Co56Fe16B20Ti8 и составляла 303 нм. Следует отметить, что усреднение проводилось по пяти результатам для каждого сплава. Определяли высоты только больших ступенек. Минимальное значение средней высоты ступенек наблюдалось в сплаве Co67Si13B9Fe1Mn4 и составляло 75 нм. Поскольку данные измерения являются чрезвычайно трудоемкими, полученные результаты следует рассматривать как оценочные. Для значений высот полос для каждого сплава наблюдался существенный разброс, что также свидетельствовало о неоднородном распределении деформации по образцу. Однако полученные значения средней высоты для крайних случаев отличаются более чем в четыре раза и представляются достоверными.
На рис. 6 приведена рентгенограмма сплава Co56Fe16B20Ti8. Именно у этого сплава ступеньки имели большую высоту. На дифрактограмме имеется диффузное гало от аморфной фазы (кривая 2) и 2 дифракционных отражения (кривые 3 и 4) от кристаллических фаз. Кривая 3 соответствует линии (002) ГПУ-Со, слабое отражение 4 может отвечать фазам типа Co3B или Co23B6, для окончательного вывода необходимо получение образцов с большей долей этой фазы. Таким образом, при деформации образовались нанокристаллы, средний размер которых составил 30 нм. На рис. 7 приведена рентгенограмма от деформированного сплава Co67Si13B9Fe1Mn4. Высота ступенек у этого сплава была минимальной. На рентгенограмме присутствует только гало от аморфной фазы, т.е. образец при такой деформации остался аморфным.
Рис. 6.
Рентгенограмма сплава Co56Fe16B20Ti8 (1 – экспериментальная кривая, 2 – диффузное отражение от аморфной фазы, 3, 4 – дифракционные отражения от кристаллических фаз, 5 – суммарная кривая (кривые 2–4).

Из полученных данных следует, что при барической обработке образцы аморфных сплавов деформируются пластически. Местом локализации пластической деформации являются полосы сдвига, которые при выходе на поверхность образуют ступеньки. Если деформация становится существенной, то происходит кристаллизация. Мощность полосы сдвига можно определить по высоте и ширине ступеньки. Величину деформации сдвига для большой ступеньки можно оценить, используя формулу для оценки истинной деформации при прохождении одной полосы сдвига ln(е) = a/b, где a – высота ступеньки, b – ее ширина. Для оценки будем использовать литературные данные по толщине полосы сдвига (20 нм). Тогда величина истинной деформации для ступеньки средней высоты в сплаве Co56Fe16B20Ti8 (максимальная средняя высота ступенек) составила e = 2.7, а для сплава Co67Si13B9Fe1Mn4 (с минимальной средней высотой ступенек) e = 1.3. Эти значения следует рассматривать как оценочные по следующим причинам. Во-первых, количество измерений высоты полос сдвига невелико, и ошибка может быть существенной. Во-вторых, ступеньки на поверхности могут быть образованы в результате активации не одной, а нескольких близко расположенных полос сдвига. В этом случае величина истинной деформации материала полосы сдвига будет другой. Для ответа на этот вопрос необходимы исследования морфологии ступенек с более высоким разрешением, которые в данной работе не проводили. Однако из полученных результатов, несомненно, следует связь между высотой полос сдвига и образованием нанокристаллов при деформации. Эта связь прослеживалась на всех исследованных образцах, кроме сплава системы Co–Si–B, в котором высота ступенек была промежуточной, а в соответствии с рентгеновскими данными, нанокристаллы в нем при деформации образовались. Но такое расхождение опять может быть связано с погрешностями при определении средней высоты ступенек.
ЗАКЛЮЧЕНИЕ
Проведено исследование морфологии поверхности аморфных сплавов Co65Si12B9Ni10Nb4, Co67Si12B9Fe7Nb5, Co79Si12B9, Co67Fe5B20Nb8, Co67Si13B9Fe1Mn4, Co56Fe16B20Ti8 после барической обработки при 5 ГПа. В процессе деформации образцы пластически деформировались путем образования и распространения полос сдвига, при выходе которых на поверхность образовывались ступеньки. Определена высота ступенек во всех исследованных образцах, которая составила от десятков до сотен нанометров. В сплавах с большой высотой ступенек наблюдалась частичная кристаллизация с образованием нанокристаллов, сплавы с малой высотой ступенек осталась аморфными.
Список литературы
Greer A.L., Cheng Y.Q., Ma E. // Mater. Sci. Eng. 2013. V. R74. P. 71. https://doi.org/10.1016/j.mser.2013.04.001
Pampillo C.A., Chen H.S. // Mater. Sci. Eng. 1974. V. 13. P. 181.
Pan S., Chen Q., Liu L., Li Y. // Acta Materialia 2011. V. 59. P. 5146. https://doi.org/10.1016/j.actamat.2011.04.047
Li J., Wang, Z.L. Hufnagel T.C. // Phys. Rev. B 2002. V. 65. P. 144201. https://doi.org/10.1103/PhysRevB.65.144201
Maab R., Samver K., Arnold W., Volkert C.F. // Appl. Phys. Lett. 2014. V. 105. P. 171902. https://doi.org/10.1063/1.4936388
Glezer A.M., Khriplivets I.A., Sundeev R.V., Louzguine-Luzgin D.V., Pogozhev Yu.S., Rogachev S.O., Bazlov A.I., Tomchuk A.A. // Mater. Let. 2020. V. 281. P. 128659. https://doi.org/10.1016/j.matlet.2020.128659
Rösner H., Peterlechner M., Kübel C., Schmidt V., Wilde G. // Ultramicroscopy 2014. V. 142. P. 1. https://doi.org/10.1016/j.ultramic.2014.03.006
Davani F.A., Hilke S., Rösner H., Geissler D., Gebert A., Wilde G. // J. Alloys Compd. 2020. V. 837. P. 155494. https://doi.org/10.1016/j.jallcom.2020.155494
Jiang W.H., Atzmon M. // Scr. Mater. 2006. V. 54. P. 333. https://doi.org/10.1016/j.scriptamat.2005.09.052
Shao H., Xu Y., Shi B., Yu Ch, Hahn H., Gleiter H., Li J. // J. Alloy. Compd. 2013. V. 548. P. 77. https://doi.org/10.1016/j.jallcom.2012.08.132
Shao Y., Yao K., Li M., Liu X. // Appl. Phys. Let. 2013. V. 103. P. 171901. https://doi.org/10.1063/1.4826117
He J., Kaban I., Mattern N., Song K., Sun B., Zhao J., Kim D. H., Eckert J., Greer A. L. // Sci. Reports. 2016. V. 6. P. 25832. https://doi.org/10.1038/srep25832
Şopu D., Scudino S., Bian X.L., Gammer C., Eckert J. // Scripta Mater. 2020. V. 178. P. 57. https://doi.org/10.1016/j.scriptamat.2019.11.006
Liu C., Roddatis V., Kenesei P., Maab R. // Acta Mater. 2017. V. 140. P. 206. https://doi.org/10.1016/j.actamat.2017.08.032
Shahabi H.S., Scudino S., Kaban I., Stoica M., Escher B., Menzel S., Vaughan G.B.M., Kühn U., Eckert J. // Acta Mater. 2016. V. 111. P. 187. https://doi.org/10.1016/j.actamat.2016.03.035
Hassanpour A., Vaidya M., Divinski S.V., Wilde G. // Acta Mater. 2021. V. 209. P. 116 785. https://doi.org/10.1016/j.actamat.2021.116785
Boucharat N., Hebert R., Rösner H., Valiev R., Wilde G. // Scripta. Mater. 2005. V. 53. P. 823. https://doi.org/10.1016/j.scriptamat.2005.06.004
Kovacs Zs., Henits P., Zhilyaev A.P., Revesz A. // Scr. Mater. 2006. V. 54. P. 1733. https://doi.org/10.1016/j.scriptamat.2006.02.004
Abrosimova G., Aronin A., Barkalov O., Matveev D., Rybchenko O., Maslov V., Tkach V. // Phys. Solid State 2011. V. 53. P. 229. https://doi.org/10.1134/S1063783411020028
Утевский Л.М. Дифракционная электронная микроскопия в металловедении. Москва: Металлургия, 1973. 584 с.
Guinier A. Theorie et technique de la radiocristallographie. Paris: Dumond, 1956. 389 p.
Mironchuk B., Abrosimova G., Bozhko S., Drozdenko A., Postnova E., Aronin A. // Mater. Let. 2020. V. 273. 127 941. https://doi.org/10.1016/j.matlet.2020.127941
Chen Y.M., Ohkubo T., Mukai T., Hono K. // J. Mater. Res. 2009. V. 24. P. 1. https://doi.org/10.1557/jmr.2009.0001
Aronin A.S., Louzguine-Luzgin D.V. // Mechanics of Materials 2017. V. 113. P. 19. https://doi.org/10.1016/j.mechmat.2017.07.007
Lewandowski J. J., Greer A. L. // Nature Mater. 2006. V. 5. P. 15. https://doi.org/10.1038/nmat1536
Дополнительные материалы отсутствуют.
Инструменты
Поверхность. Рентгеновские, синхротронные и нейтронные исследования