Поверхность. Рентгеновские, синхротронные и нейтронные исследования, 2021, № 12, стр. 103-107
Применение порошковых лигатур Ni–Si3N4 для армирования алюминиевых сплавов
А. А. Кузина *
Самарский национальный исследовательский университет
имени академика С.П. Королёва
443086 Самара, Россия
* E-mail: KuzinaAntonina@mail.ru
Поступила в редакцию 22.01.2021
После доработки 20.03.2021
Принята к публикации 25.03.2021
Аннотация
Приводятся результаты армирования алюминиевого сплава АК12 лигатурами, содержащими наночастицы порошка Si3N4, полученного по азидной технологии самораспространяющегося высокотемпературного синтеза (СВС) в СамГТУ. Исследовался ввод в алюминиевый расплав порошковых лигатур, содержащих от 2.5 до 7.5 мас. % Si3N4. Армирование алюминиевого сплава АК12 проводили в печи типа GRAFICARBO в стальном тигле объемом до 0.2 кг. Температуру расплава изменяли в интервале от 850 до 1000°С. Исследовали влияние обработки алюминиевого расплава электромагнитными акустическими полями (ЭМАП) на растворимость вводимых порошковых лигатур Ni–Si3N4 и усвоение их расплавом. Представлена микроструктура образцов до и после армирования. Определено, что максимальная растворимость упрочняющей фазы Si3N4 наблюдается при ее вводе в сплав АК12 в составе порошковой лигатуры Ni + 5% Si3N4.
ВВЕДЕНИЕ
В изделиях авиационной, ракетной и космической техники широкое применение находят алюмоматричные композиционные материалы (АМКМ), отличающиеся малой плотностью, высокими прочностными свойствами и возможностью изготовления из них сложных по форме деталей. В настоящее время активно развиваются технологичные способы получения АМКМ, упрочненных тугоплавкими соединениями. Однако предметом постоянных исследований является ввод в алюминиевый расплав порошковых частиц тугоплавких соединений с наноразмерностью, а также их усвоение и однородное распределение в алюминиевой матрице [1–12], что связано с плохой смачиваемостью жидким металлом таких частиц, большой склонностью их к конгломерации и др. [11]. Для упрощения процесса ввода наночастиц в алюминиевые расплавы применяются различные приемы, в том числе и их ввод в состав порошковых лигатур. Использование керамических наночастиц в качестве упрочняющей фазы при изготовлении АМКМ позволяет при малых объемах их ввода значительно повысить эксплуатационные свойства изделий [1–14].
Таким образом, целью данной работы было исследование возможности ввода наночастиц армирующей фазы Si3N4 при увеличенном ее содержании в алюминиевый расплав.
МАТЕРИАЛЫ И МЕТОДЫ ИССЛЕДОВАНИЯ
Исследован способ ввода наночастиц нитрида кремния в алюминиевый расплав АК12 в процессе плавки в виде брикетов (порошковых лигатур) состава Ni–(2.5–7.5%)Si3N4. В качестве материала (основы лигатур) был выбран никелевый порошок марки ПНЭ-1, представленный на рис. 1а, с размером частиц от 30 до 75 мкм, применяемый как основной металл для легирования с целью повышения прочности сплавов при высоких температурах. В качестве армирующей фазы использовался порошок Si3N4 (рис. 1б), полученный в СамГТУ по азидной технологии самораспространяющегося высокотемпературного синтеза, с размерами частиц до 100 нм.
Рис. 1.
РЭМ-изображение поверхности частиц: а – никелевый порошок марки ПНЭ-1, б – порошок Si3N4 марки СВС-Аз.
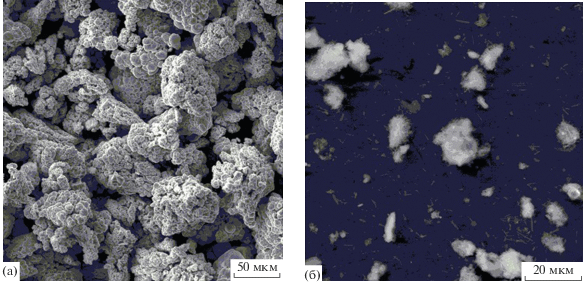
Приготовление порошковых композиций Ni–Si3N4 проводили в шаровой и планетарной (“Пульверизетте-5”) мельницах. При механическом смешивании порошков изменялись время (от 1 до 60 мин) и скорость (от 50 до 300 об./мин) смешивания.
Грансостав порошков определяли на лазерном анализаторе размера частиц “Analysette 22 Compact”, насыпную массу порошков – с помощью волюмометра, сыпучесть порошков – методом Холла, удельную поверхность – с помощью анализатора серии СОРБТОМЕТР. Однородность смешивания оценивали произвольно взятыми пробами. Шихту считали однородной, если не менее 95% произвольно взятых проб имеют почти одинаковый гранулометрический и химический составы.
Далее из полученных смесей Ni–Si3N4 холодным прессованием при давлении от 65 до 700 МПа были получены порошковые лигатуры с различной плотностью (от 68 до 92%).
В алюминиевый расплав АК12 при температурах 850–1000°С вводили полученные порошковые лигатуры Ni–Si3N4 в виде прессованных брикетов (массой 2.5 г) с относительной плотностью 85–90%, полученные прессованием при давлении 540–700 МПа. Ввод армирующей фазы Si3N4 в алюминиевый расплав проводился в печи типа GRAFICARBO в стальном тигле объемом до 0.2 кг. Равномерное распределение дисперсной фазы Si3N4 в алюминиевом расплаве обеспечивалось с помощью перемешивания. В работе исследовали влияние обработки алюминиевого расплава электромагнитными акустическими полями на растворимость вводимых порошковых лигатур Ni–Si3N4 и усвоение их расплавом АК12. Обработку осуществляли с помощью генератора “Сонар”, который создает электромагнитные волны радиочастотного диапазона. Генератор акустических колебаний размещали вблизи тигля с расплавом [15]. В качестве излучателя электромагнитных волн, погруженного в алюминиевый расплав после ввода порошковых лигатур, использовали проволоку в виде петлеобразной антенны диаметром до 3 мм. В процессе экспериментов варьировались частота электромагнитного поля (от 500 до 1000 кГц) и время (от 15 до 30 мин) его воздействия после ввода порошковых лигатур Ni–Si3N4.
Химический состав сплавов до и после ввода порошковых лигатур определяли методом рентгеноспектрального микроанализа (РСМА), при этом использовался энергодисперсионный детектор INCAx-act, являющийся приставкой к растровому электронному микроскопу TESCANVegaSB, на котором также исследовали микроструктуру методом растровой электронной микроскопии (РЭМ). Твердость образцов определяли методом Бринелля.
РЕЗУЛЬТАТЫ ИССЛЕДОВАНИЯ И ИХ ОБСУЖДЕНИЕ
Экспериментально определено, что однородное распределение частиц нитрида кремния в полученных порошковых композициях достигается смешиванием в планетарной мельнице в течение пяти минут со скоростью 300 об./мин. В табл. 1 представлены некоторые физические и технологические свойства полученных порошковых смесей Ni–Si3N4, не обладающих сыпучестью.
Таблица 1.
Свойства полученных порошковых смесей Ni–Si3N4
Порошковая смесь | Гранулометрический состав, мкм | Компактная плотность, г/см3 | Насыпная масса, г/см3 | Удельная поверхность, м2/г |
---|---|---|---|---|
Ni + 2.5% Si3N4 | 40–70 | 8.43 | 2.15 | 1.27 |
Ni + 5% Si3N4 | 35–65 | 8.09 | 2.03 | 1.64 |
Ni + 7.5% Si3N4 | 30–60 | 7.78 | 1.87 | 1.86 |
Согласно табл. 1, с увеличением содержания дисперсной фазы в полученных порошковых смесях Ni–Si3N4 отмечается уменьшение гранулометрического состава, компактной плотности, насыпной массы и увеличение удельной поверхности.
На рис. 2 представлена зависимость относительной плотности порошковых лигатур Ni–Si3N4 от давления прессования.
Согласно рис. 2, в порошковых лигатурах Ni–Si3N4 минимальная относительная плотность получена при давлении прессования 65 МПа и составляет 75% (для лигатуры Ni + 2.5% Si3N4), 73% (для лигатуры Ni + 5% Si3N4) и 68% (для лигатуры Ni + 7.5% Si3N4), а максимальная относительная плотность получена в порошковых лигатурах при давлении прессования 700 МПа и составляет 92% (для лигатуры Ni + 2.5% Si3N4), 91% (для лигатуры Ni + 5% Si3N4) и 87% (для лигатуры Ni + 7.5% Si3N4).
В табл. 2 представлен химический состав образцов на основе алюминиевого сплава АК12 после ввода порошковых лигатур Ni–Si3N4.
Таблица 2.
Химический состав полученных образцов
Материал-основа | Вводимая лигатура | Элементный состав, мас. % | ||||||
---|---|---|---|---|---|---|---|---|
N | С | Al | Ni | Si | О | Ag | ||
АК12 | Ni + 2.5% Si3N4 | 0.15 | 0.73 | 80.82 | 2.37 | 12.22 | 2.39 | 1.32 |
Ni + 5% Si3N4 | 0.27 | 0.86 | 80.11 | 2.44 | 12.36 | 2.48 | 1.48 | |
Ni + 7.5% Si3N4 | 0.33 | 0.98 | 79.95 | 2.38 | 12.41 | 2.38 | 1.57 |
Согласно табл. 2, в полученных литых образцах отмечается наличие следов некоторых элементов (азота и углерода), содержание которых не превышает 1%. Присутствие кислорода в химическом составе литых образцов связано с тем, что перемешивание расплава проводилось вручную при помощи приспособления, представляющего собой стальной пруток диаметром 10 мм. Наличие никеля в составе полученных образцов подтверждает ввод порошковых лигатур Ni–Si3N4 в расплав АК12.
Общее время перемешивания расплава составило 6 мин (при средней скорости – 5 об./мин). В ходе экспериментов определено, что частота (500 и 1000 кГц) и время воздействия (2–45 мин) ЭМАП на растворимость вводимых порошковых лигатур Ni–Si3N4 и усвоение их расплавом АК12 практически не влияют.
На рис. 3 представлена микроструктура сплава АК12 и образца АК12 + 2.5% (Ni + 5% Si3N4), полученного после ввода порошковой лигатуры при температуре 900°С.
Рис. 3.
РЭМ-изображение микроструктуры образцов до и после ввода порошковой лигатуры (Ni + 5% Si3N4) при температуре 900°С: а – сплав АК12, б – АК12 + 2.5% (Ni + 5% Si3N4).
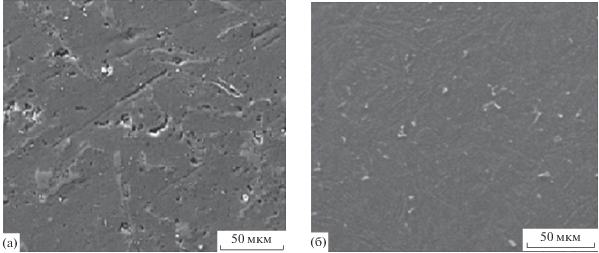
Экспериментально определено, что оптимальная температура ввода порошковой лигатуры (Ni + 5% Si3N4) – 900°С, так как при температурах от 850 до 900°С данная лигатура растворяется частично. Полное растворение применяемой лигатуры наблюдается при 900°С, поэтому дальнейшее увеличение температуры (до 1000°С) является не рациональным. Изменение температуры расплава от 850 до 1000°С при вводе порошковой лигатуры (Ni + 7.5% Si3N4) положительного влияния на полную растворимость данной лигатуры не оказало.
Согласно рис. 3, армирующая фаза Si3N4 на микроструктуре не видна ввиду малого ее количества. Однако после ввода порошковой лигатуры Ni + 5% Si3N4 в образце АК12 + 2.5% (Ni + 5% Si3N4) отмечается измельчение структуры. Максимальная растворимость упрочняющей фазы Si3N4 наблюдается при вводе в алюминиевый сплав АК12 порошковых лигатур на никелевой основе, содержащих 2.5 и 5% армирующей фазы.
В полученных литых образцах на основе АК12 твердость изменялась по шкале HВ в пределах от 56 до 67 МПа (твердость сплава АК12 по ГОСТу 1583-93 составляет НВ 50 МПа). Незначительное повышение твердости наблюдается в образце АК12 + 2.5% (Ni + 7.5% Si3N4) и составляет НВ 56 МПа, данный результат связан с тем, что порошковая лигатура растворяется не полностью. Максимальное повышение твердости отмечается в образце АК12 + 2.5% (Ni + 5% Si3N4) и составляет НВ 67 МПа.
ЗАКЛЮЧЕНИЕ
Применение порошковых лигатур Ni–Si3N4 позволяет вводить в алюминиевый расплав наночастицы Si3N4 в малом количестве (не более 0.1%). Проведенные исследования показали, что доля упрочняющей фазы – нанопорошка Si3N4, полученного по азидной технологии СВС в СамГТУ, в прессованной лигатуре не может быть более 5%. При содержании в порошковой лигатуре на никелевой основе наночастиц Si3N4 более 5% полученные лигатуры практически не растворяются в расплаве и при температурах 950–1000°С. Таким образом, оптимальное содержание упрочняющей фазы Si3N4 с материалом-основой (никелем) в прессованных порошковых лигатурах составляет 5%. Температура алюминиевого расплава, при которой отмечается полное растворение порошковой лигатуры Ni + 5% Si3N4, составляет 900°С.
Определено, что заметного влияния на растворимость порошковых лигатур Ni–Si3N4 в алюминиевых расплавах электромагнитные акустические поля не оказывали.
Список литературы
Манолов В., Черепанов А., Лазарева Р., Константинова С. // Литейное производство. 2011. № 4. С. 17.
Сарасеко М.Н., Лалетин В.М., Бохан Ю.И. // Конструкции из композиционных материалов. 2014. № 3. С. 21.
Рязанов С.А., Амосов А.П., Никитин В.И., Марков Ю.И., Ермошкин А.А., Титова Ю.В. // Литейное производство. 2014. № 7. С. 16.
Анисимов О.В., Костиков В.И., Лобачева Е.В., Пузик В.И., Штанкин Ю.В. // Известия вузов. Порошковая металлургия и функциональные покрытия. 2011. № 3. С. 33.
Петрунин А.В., Панфилов А.В., Панфилов А.А. // Литейное производство. 2009. № 10. С. 17.
Косников Г.А., Баранов В.А., Петрович С.Ю. // Литейное производство. 2012. № 2. С. 4.
Крушенко Г.Г. // Металлургия машиностроения. 2011. № 1. С. 20.
Крушенко Г.Г. // Нанотехника. 2011. № 3. С. 55.
Панфилов А.В. // Литейщик России. 2008. № 7. С. 23.
Кузина А.А., Титова Ю.В. // Вестник СамГТУ. Серия “Технические науки”. 2017. № 4(56). С. 166.
Амосов А.П., Никитин В.И., Никитин К.В., Рязанов С.А., Ермошкин А.А. // Наукоёмкие технологии в машиностроении. 2013. № 8. С. 3.
Калинина Н.Е., Кавац О.А., Калинин В.Т. // Авиационно-космическая техника и технология. 2008. № 7. С. 16.
Панфилов А.В., Петрунин А.В., Панфилов А.А. // Нанотехника. 2007. № 3(11). С. 76.
Vorozhtsov S., Zhukov I., Vorozhtsov A., Zhukov A., Eskin D., Kvetinskaya A. // Advances in Materials Science and Engineering. 2015. V. 2015. Article ID 718 207. 6 p. https://doi.org/10.1155/2015/718207
Тимошкин И.Ю., Никитин К.В., Никитин В.И., Деев В.Б. // Известия вузов. Цветная металлургия. 2016. № 3. С. 28.
Дополнительные материалы отсутствуют.
Инструменты
Поверхность. Рентгеновские, синхротронные и нейтронные исследования