Поверхность. Рентгеновские, синхротронные и нейтронные исследования, 2022, № 4, стр. 30-33
Изменение микротвердости композиционной керамики на границе раздела CaO–ZrO2/CaO–ZrO2 + Al2O3
А. А. Дмитриевский a, *, Д. Г. Жигачева a, Г. В. Григорьев a, П. Н. Овчинников a
a Тамбовский государственный университет им. Г.Р. Державина
392000 Тамбов, Россия
* E-mail: aadmitr@yandex.ru
Поступила в редакцию 30.06.2021
После доработки 27.08.2021
Принята к публикации 30.08.2021
- EDN: KFHYBL
- DOI: 10.31857/S1028096022040045
Аннотация
Методом одноосного сухого прессования предварительно подготовленных смесей порошков (содержащих и не содержащих оксид алюминия) изготовлены двухслойные образцы циркониевой керамики, стабилизированной в тетрагональной фазе оксидом кальция (CCaO = 6.5 моль. %). Исследованы микроструктура и механические свойства (микротвердость) в окрестности границы раздела CaO–ZrO2/CaO–ZrO2 + Al2O3. Выявлено скачкообразное увеличение микротвердости (от 13.7 ± 0.2 до 14.4 ± 0.2 ГПа) и модуля Юнга (от 195 ± 6 до 210 ± 7 ГПа) при переходе от CaO–ZrO2 к CaO–ZrO2 + + Al2O3. Продемонстрирована высокая вероятность образования (в процессе спекания) трещин вдоль границы раздела циркониевой керамики, содержащей и не содержащей оксид алюминия.
ВВЕДЕНИЕ
Обнаруженная почти 50 лет назад [1] возможность стабилизации при комнатных температурах тетрагональной фазы диоксида циркония t-ZrO2 (путем введения добавок оксидов Y2O3, CeO2, CaO и других), способной к механоиндуцированной трансформации в моноклинную фазу m-ZrO2 (превращение t → m обеспечивает трансформационный механизм упрочнения), значительно повысила прочностные свойства циркониевой керамики. На сегодняшний день она с успехом применяется для изготовления режущего инструмента, резьбонаправляющих устройств, кулачков, уплотнений, клапанов и колец насосов [2]. Благодаря биосовместимости диоксид циркония стал очень популярным в биомедицинских приложениях [3–5]. Кроме того, циркониевая керамика используется при изготовлении твердооксидных топливных элементов [6], термобарьеров [7], оптических покрытий [8], катализаторов [9], датчиков кислорода [10] и многих других устройств.
Задачу дальнейшего улучшения прочностных свойств циркониевой керамики успешно решает разработка композитов на ее основе. Наибольшую популярность приобрела циркониевая керамика, упрочненная оксидом алюминия (ATZ-керамика) [11, 12]. В ней сильные стороны циркониевой керамики сочетаются с достоинствами керамики на основе Al2O3 за счет проявления дисперсионного механизма упрочнения [13, 14].
Широчайший спектр задач, требующих от конструкционных материалов различия объемных и приповерхностных свойств, предопределил появление нового поколения композиционных материалов – функционально-градиентных материалов [15]. Они представляют собой многослойные композиты, в которых состав и свойства изменяются непрерывно или ступенчато от одной части изделия к другой [16]. Предполагается одновременное использование различных (в том числе взаимоисключающих) свойств компонентов функционально-градиентных материалов. В связи с этим целью работы было исследование структуры и микромеханических свойств двухслойной циркониевой керамики в области границы раздела частей, содержащих и не содержащих оксид алюминия.
МЕТОДИКА
Для изготовления образцов керамики CaO–ZrO2/CaO–ZrO2 + Al2O3 использовали порошки ZrO2 (Sigma-Aldrich), α-Al2O3 (Hongwu) и CaO (Reachem). Молярную концентрацию стабилизатора (CaO) по отношению к ZrO2 (вне зависимости от наличия или отсутствия Al2O3) сохраняли неизменной: CCaO = 6.5 моль. %. В соответствии с полученными ранее результатами [17] использование оксида кальция (вместо “традиционного” оксида иттрия) в качестве стабилизатора тетрагональной фазы диоксида циркония позволяет существенно повысить стойкость циркониевой керамики к низкотемпературной деградации. Для получения состава, содержащего оксид алюминия, к смеси CaO–ZrO2 добавляли 5.8 моль. % Al2O3, что согласно данным [18] обеспечивает высокое соотношение твердости и вязкости разрушения ATZ-керамики.
Полученные смеси порошков (содержащие и не содержащие оксид алюминия) диспергировали ультразвуком в дистиллированной воде (массовое соотношение выдерживали 1 : 3). Затем в течение 5 ч осуществляли помол смесей в планетарной мельнице Pulverisette (Fritsch) керамическими шарами из диоксида циркония, стабилизированного оксидом иттрия. Соотношение шаров и измельчаемого порошка выдерживали 1 : 1. Тонкий механический помол проводили с добавлением воды (75%) в качестве среды измельчения. Далее следовала сушка смесей в печи при температуре T0 = 80°С и нормальном давлении в течение 24 ч. Подготовленные таким образом смеси (содержащие и не содержащие Al2O3) последовательно и в равных количествах засыпали в пресс-форму. Формовку двухслойных образцов осуществляли путем одноосного сухого прессования при нагрузке 500 МПа в течение 20 мин. Спекание образцов в электрической печи проводили в двухстадийном режиме (детально описанном в [19]) при температурах T1 = 1300°С и T2 = 1200°С. Согласно [20, 21], двухстадийный режим спекания керамик на основе ZrO2 и Al2O3 обеспечивает сохранение малого размера зерна (в сравнении с одностадийным спеканием) и высокую плотность керамики. Полученные образцы имели средний размер кристаллитов ZrO2 и Al2O3 не более 100 и 250 нм соответственно. Пористость (измеренная методом Архимеда) не превышала 3%. Полученные образцы (в виде двухслойных таблеток) пилили пополам, после чего торцевую поверхность механически шлифовали и полировали для измерения микротвердости.
Визуализацию структуры изготовленных образцов CaO–ZrO2/CaO–ZrO2 + Al2O3 керамики осуществляли с помощью растрового электронного микроскопа (РЭМ) высокого разрешения Merlin (Carl Zeiss). Микротвердость H и модуль Юнга E на разных расстояниях от границы раздела CaO–ZrO2/CaO–ZrO2 + Al2O3 определяли с использованием наноидентометра NanoIndenter G200 (MTS NanoInstruments). В качестве индентора брали пирамиду Берковича, глубина внедрения которой не превышала 6 мкм.
РЕЗУЛЬТАТЫ И ИХ ОБСУЖДЕНИЕ
На рис. 1а представлено характерное РЭМ-изображение участка поверхности среза образца керамики CaO–ZrO2/CaO–ZrO2 + Al2O3. Согласно многочисленным литературным данным и выполненному в [22] элементному картированию участков поверхности близких по составу образцов, темные пятна на представленном РЭМ-изображении идентифицируются как кристаллиты Al2O3. Видно, что кристаллиты оксида алюминия равномерно распределены в одной части образца (слева вверху) и отсутствуют в другой части (справа внизу). Это дает основание утверждать, что в изготовленных образцах наблюдается резкая граница между частями, содержащими и не содержащими кристаллиты Al2O3. Более детальный анализ РЭМ-изображений не позволил выявить других признаков различия этих частей (средний размер кристаллитов ZrO2, наличие пор и другие признаки).
Рис. 1.
Характерные РЭМ-изображения участков поверхности среза образца керамики CaO–ZrO2/CaO–ZrO2 + Al2O3 вдали от трещины (а) и с трещиной, проходящей по границе части, содержащей Al2O3 (б).
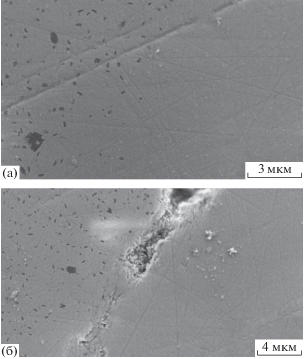
Важно отметить, что практически в каждом образце имеются трещины, проходящие строго по границе раздела керамики CaO–ZrO2/CaO–ZrO2 + Al2O3 (рис. 1б). Появление трещин происходит в процессе спекания. Наиболее вероятной причиной наблюдаемого растрескивания является различие температурных коэффициентов линейного расширения циркониевой и корундовой керамик [23] и, как следствие, частей исследуемых образцов, содержащих и не содержащих Al2O3.
Индентирование проводили на участках полированной поверхности, удаленных от трещин не менее чем на 500 мкм. Сторона отпечатка индентора (пирамида Берковича) не превышала 45 мкм. Отметим, что наблюдаемые на РЭМ-изображениях борозды являются следами механической полировки, имеют малый (по сравнению с отпечатком индентора) размер и не оказывают заметного влияния на определяемую величину микротвердости. Строгий контроль пространственного расположения отпечатков индентора позволил построить зависимости микротвердости H и модуля Юнга E материала от расстояния d до границы раздела керамики CaO–ZrO2/CaO–ZrO2 + Al2O3 (рис. 2).
Рис. 2.
Зависимости микротвердости H (а) и модуля Юнга E (б) от расстояния d до границы раздела между частями образца циркониевой керамики, содержащей и не содержащей Al2O3.
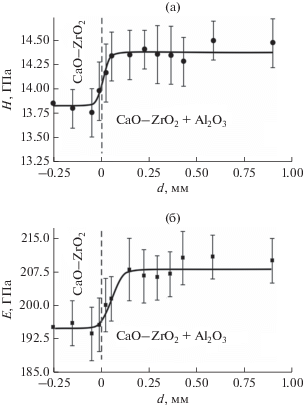
Из представленных зависимостей видно, что в ближайшей окрестности границы раздела наблюдается скачкообразное изменение величин H и E. На расстояниях d, превышающих 100 мкм от границы раздела (в два раза превышающих сторону отпечатка индентора), зависимости H(d) и E(d) выходят в насыщение. Микротвердость и модуль Юнга принимают значения, характерные для соответствующих керамик CaO–ZrO2 и CaO–ZrO2 + Al2O3.
ЗАКЛЮЧЕНИЕ
Показана возможность изготовления (методом одноосного сухого прессования с последующим двухстадийным спеканием) циркониевой керамики с резкой границей раздела составов CaO–ZrO2/CaO–ZrO2 + Al2O3. В ближайшей окрестности границы раздела (~100 мкм) наблюдается скачкообразное изменение микротвердости и модуля Юнга от значений, характерных для CaO–ZrO2 (H = 13.7 ± 0.2 ГПа, E = 195 ± 6 ГПа) до значений, типичных для керамики CaO–ZrO2 + + Al2O3 (H = 14.4 ± 0.2 ГПа, E = 210 ± 7 ГПа). Полученный результат может быть использован при разработке изделий из композиционной керамики на основе диоксида циркония, объемные и поверхностные механические свойства которых должны удовлетворять различным требованиям.
Недостатком предложенного метода является высокая вероятность образования трещин (вызванных различием температурных коэффициентов линейного расширения ZrO2 и Al2O3) на границе раздела керамики, содержащей и не содержащей оксид алюминия. Разработка способов реализации идеологии функционально-градиентных материалов – формирование плавного перехода от CaO–ZrO2 к CaO–ZrO2 + Al2O3 – обеспечит сохранение целостности композиционной керамики при спекании и будет предметом ближайших исследований.
Список литературы
Garvie R.C., Hannink R.H.J., Pascoe R.T. // Nature. 1975. V. 258. P. 703. https://doi.org/10.1038/258703a0
Zhang X., Wu X., Shi J. // J. Mater. Res. Technol. 2020. V. 9. № 4. P. 9029. https://doi.org/10.1016/j.jmrt.2020.05.131
Akagawa Y., Ichikawa Y., Nikai H., Tsuru H. // J. Prosthet. Dent. 1993. V. 69. № 6. P. 599. https://doi.org/10.1016/0022-3913(93)90289-z
Shin H., Ko H., Kim M. // Restor. Dent. Endodont. 2016. V. 41. № 3. P. 167. https://doi.org/10.5395/rde.2016.41.3.167
Galante R., Figueiredo-Pina C.G., Serro A.P. // Dent. Mater. 2019. V. 35. № 6. P. 825. https://doi.org/10.1016/j.dental.2019.02.026
Mahato N., Gupta A., Balani K. // Nanomater. Energy. 2012. V. 1. P. 27. https://doi.org/10.1680/nme.11.00004
Shackelford J.F., Doremus R.H. // Ceramic and Glass Materials: Structure, Properties and Processing. Springer Science&Business Media, 2008. P. 169.
Thakare V. // Int. J. Eng. Res. Dev. 2012. V. 5. P. 25. http://www.ijerd.com/paper/vol5-issue1/F05012528.pdf
Krumov E., Dikova J., Starbova K., Popov D., Blaskov V., Kolev K., Laude L.D. // J. Mater. Sci.: Mater. Electronics. 2003. V. 14. P. 759. https://doi.org/10.1023/A:1026176431171.pdf
Lee J.H. // J. Mater. Sci. 2003. V. 38. P. 4247. https://doi.org/10.1023/A:1026366628297.pdf
Soon G., Pingguan-Murphy B., Lai K.W., Akbar S.A. // Ceram. Int. 2016. V. 4. P. 12543. https://doi.org/10.1016/j.ceramint.2016.05.077
Maji A., Choubey G. // Mater. Today Proceed. 2018. V. 5. P. 7457. https://doi.org/10.1016/j.matpr.2017.11.417
Zhang F., Lin L.F., Wang E.Z. // Ceram. Int. 2015. V. 41. P. 2417. https://doi.org/10.1016/j.ceramint.2015.06.081
Lee J.-K., Kim M.J., Lee E.G. // J. Mater. Sci. Lett. 2002. V. 21. P. 259. https://doi.org/10.1023/A:1014737614591
Минько Д.В., Белявин К.Е., Шелег В.К. Теория и практика получения функционально-градиентных материалов. Минск: БНТУ, 2020. 450 с.
Ewais E.M.M., Besisa D.H.A., Zaki Z.I., Kandil A.E.H.T. // J. Eur. Ceram. Soc. 2012. V. 32. P. 1561. https://doi.org/10.1016/j.jeurceramsoc.2012.01.016
Дмитриевский А.А., Жигачева Д.Г., Ефремова Н.Ю., Умрихин А.В. // Российские нанотехнологии. 2019. Т. 14. № 3–4. С. 39. https://doi.org/10.21517/1992-7223-2019-3-4-39-45
Дмитриевский А.А., Жигачев А.О., Жигачева Д.Г., Тюрин А.И. // ЖТФ. 2019. Т. 89. № 1. С. 107. https://doi.org/10.21883/JTF.2019.01.46970.102-18
Дмитриевский А.А., Тюрин А.И., Жигачев А.О., Гусева Д.Г., Овчинников П.Н. // Письма в ЖТФ. 2018. Т. 44. № 4. С. 25. https://doi.org/10.21883/PJTF.2018.04.45635.16933
Binner J., Annapoorani K., Paul A., Santacruz I. // J. Eur. Ceram. Soc. 2008. V. 28. P. 973. https://doi.org/10.1016/j.jeurceramsoc.2007.09.002
Galusek D., Ghillányová K., Sedláček J., Kozankova J. // J. Eur. Ceram. Soc. 2012. V. 32. P. 1965. https://doi.org/10.1016/j.jeurceramsoc.2011.11.038
Дмитриевский А.А., Жигачев А.О., Жигачева Д.Г., Родаев В.В. // ЖТФ. 2020. Т. 90. № 12. С. 2108. https://doi.org/10.21883/JTF.2020.12.50128.84-20
Комоликов Ю.И., Кащеев И.Д., Хрустов В.Р. // Новые огнеупоры. 2016. № 9. С. 59. https://doi.org/10.17073/1683-4518-2016-9-59-62
Дополнительные материалы отсутствуют.
Инструменты
Поверхность. Рентгеновские, синхротронные и нейтронные исследования