Радиотехника и электроника, 2022, T. 67, № 10, стр. 935-945
Технологии формирования электродинамических структур для устройств вакуумной микроэлектроники миллиметрового и терагерцевого диапазонов (обзор)
А. В. Стародубов a, b, *, Д. А. Ножкин a, И. И. Расулов a, А. А. Сердобинцев a, И. О. Кожевников a, В. В. Галушка a, b, В. К. Сахаров b, Д. А. Бессонов c, А. Д. Галкин d, И. Ш. Бахтеев e, С. Ю. Молчанов e, С. В. Герман f, g, Н. М. Рыскин a, b
a Саратовский национальный исследовательский государственный университет им. Н.Г. Чернышевского
410012 Саратов, ул. Астраханская, 83, Российская Федерация
b Саратовский филиал Института радиотехники и электроники им. В.А. Котельникова РАН
410038 Саратов, ул. Зеленая, 38, Российская Федерация
c Саратовский государственный технический университет им. Гагарина Ю.А.
410054 Саратов, ул. Политехническая, 77, Российская Федерация
d Лазерный центр
195067 Санкт-Петербург, ул. Маршала Тухачевского, 22, Российская Федерация
e Институт физики твердого тела РАН
142432 Черноголовка, Московской обл., ул. Академика Осипьяна, 2, Российская Федерация
f Институт спектроскопии РАН
ул. Физическая, 5108840 Москва, Троицк, Российская Федерация
g Сколковский институт науки и технологий
121205 Москва, Большой бульвар, 30, Российская Федерация
* E-mail: StarodubovAV@gmail.com
Поступила в редакцию 12.04.2022
После доработки 12.04.2022
Принята к публикации 25.04.2022
- EDN: ZUOMWP
- DOI: 10.31857/S0033849422100126
Аннотация
Представлен обзор технологий изготовления микроразмерных электродинамических структур для устройств вакуумной микроэлектроники миллиметрового и субмиллиметрового диапазонов, таких как технология, основанная на фотолитографии; глубокое реактивное ионное травление; микро- и нанофрезерование с компьютерным управлением; электроэрозионная микрообработка; аддитивные технологии, такие как трехмерная печать, селективное лазерное спекание и селективное лазерное плавление. Также рассмотрен оригинальный подход к изготовлению планарных замедляющих систем, основанный на использовании магнетронного распыления и лазерной абляции. Проведено сравнение технологических допусков и шероховатости поверхности, которые могут быть достигнуты в рассмотренных технологиях.
ВВЕДЕНИЕ
Исследование и разработка устройств миллиметрового (мм) и субмиллиметрового или терагерцевого (ТГц) диапазонов [1–4] находится в центре внимания ученых и инженеров в различных странах. Актуальность данной проблемы обусловлена, прежде всего, особенностями распространения электромагнитных волн в этих диапазонах и потенциалом их широкого применения для решения задач безопасности и неразрушающего контроля, высокоскоростной беспроводной передачи данных, для радиоастрономических исследований, спектроскопии, биомедицинских приложений. В настоящее время устройства вакуумной электроники являются наиболее мощными источниками миллиметрового (мм) и ТГц-диапазона (вплоть до частот порядка 1.0 ТГц). Излучение в указанных диапазонах длин волн проникает в различные диэлектрические материалы, такие как камень, бетон, текстиль и полимеры, поэтому его можно использовать для обнаружения скрытых объектов внутри перечисленных материалов [5]. Системы формирования радиоизображений, работающие в указанных частотах, могут обеспечить существенно лучшее пространственное разрешение, чем системы, использующие сантиметровый и дециметровый диапазоны длин волн [6]. Кроме того, ТГц-диапазон частот важен для спектроскопии различных материалов, в частности, таких как полупроводники, сегнетоэлектрики, диэлектрики, высокотемпературные сверхпроводники, газы и жидкости [7]. Излучение в мм- и ТГц-диапазонах является неионизирующим, поэтому может быть использовано в медицинских приложениях для обнаружения поврежденных или инфицированных тканей [8].
Миниатюрные электровакуумные усилители мм- и ТГц-диапазонов типа лампы бегущей волны (ЛБВ) представляют особый интерес в силу широкополосности и возможности получения высокой выходной мощности [9]. Одним из ключевых элементов ЛБВ, который во многом определяет выходные характеристики прибора, является замедляющая система (ЗС). При продвижении рабочей длины волны в мм- и ТГц-диапазоны характерные размеры ЗС уменьшаются до сотен микрон и менее, что приводит к ужесточению допусков на изготовление и затрудняет использование традиционных технологических подходов. В последнее время были предложены новые технологии микрообработки, с помощью которых можно изготавливать ЗС и другие базовые компоненты устройств вакуумной микроэлектроники.
В данной работе представлен обзор некоторых предложенных в последнее время методов микрообработки для изготовления базовых компонентов устройств вакуумной микроэлектроники. В настоящее время процессы микрообработки принято разделять на два больших блока: субтрактивные и аддитивные (см. рис. 1). К субтрактивным технологиям, в частности, относят технологии на основе фотолитографии, глубокое реактивное ионное травление, микро- и нанофрезерование с компьютерным управлением (ЧПУ), электроэрозионную микробработку, лазерную микрообработку. На аддитивных технологиях основан принцип действия 3D-принтеров. 3D-печать может быть реализована при помощи различных подходов, таких как селективное лазерное спекание и плавление в порошковом слое, фотополимеризация, электрохимическое микроосаждение.
1. ТЕХНОЛОГИИ НА ОСНОВЕ ФОТОЛИТОГРАФИИ
Технологические подходы, в основе которых лежит фотолитография (оптическая литография), пригодны для изготовления микроразмерных структур [10, 11]. Под фотолитографией понимается формирование в специальном чувствительном слое (резисте), нанесенном на поверхность подложки, рельефного рисунка, повторяющего топологию некоей структуры (например, микросхемы), с последующим переносом этого рисунка на подложку. Основные этапы фотолитографии включают в себя очистку подложки, формирование маски из резиста (нанесение на подложку и сушка), экспонирование, проявление, травление и снятие фотомаски (резиста).
Подобные технологии широко применяются для изготовления планарных микрополосковых ЗС миллиметрового диапазона на диэлектрических подложках. В СФ ИРЭ РАН с помощью фотолитографии были изготовлены ЗС V-диапазона типа меандр и встречные штыри на диэлектрических подложках из кварца и поликора [57]. Ширина полоска составляла 25…50 мкм, толщина 1 мкм. В работе [12] описано создание V-образной планарной ЗС для ЛБВ Ka-диапазона. В качестве диэлектрических подложек были использованы кварц и стеклотекстолит FR4. Ширина металлического полоска составила 40 мкм при толщине в 2 мкм. В [13] с использованием фотолитографии была изготовлена и экспериментально исследована ЗС меандрового типа с логопериодической геометрией Ka-диапазона. В качестве диэлектрической подложки также использовались пластины из кварца. Ширина металлического полоска данной ЗС составила 25 мкм при толщине в 4 мкм. В работе [14] с помощью фотолитографии была изготовлена кольцеобразная ЗС V-диапазона на диэлектрической подложке из кварца, которая была первоначально предложена в [15]. Минимальная ширина металлического полоска оставила 40 мкм при толщине металлизации 1 мкм.
LIGA-технологии11 можно рассматривать как дальнейшее глубокое совершенствование и развитие технологий изготовления микроразмерных структур на основе фотолитографии. Эта технология позволяет в настоящее время изготавливать структуры микронных и субмикронных (нанометровых) размеров с большим аспектным соотношением. Технологический процесс на основе LIGA включает в себя следующие основные этапы: глубокая литография, гальванопластика, формовка (штамповка). Толстый слой резиста облучается через маску, затем осуществляется процесс проявления, после которого на подложке остаются полимерные детали из резиста. Электрогальванопластикой формируются металлические компоненты, после чего остатки резиста удаляются, а металлический микрорельеф можно отделить от подложки и использовать для массового тиражирования деталей литьем или штамповкой. Традиционный технологический подход на основе LIGA-технологии использует рентгеновское излучение с длиной волны в несколько ангстрем от синхротронного источника для экспонирования положительного рентгенорезиста (обычно используется полиметилметакрилат (PMMA)) через маску из золота [16] и позволяет изготавливать металлические структуры с аспектным соотношением до 100 : 1 и высотой до 3 мм. С помощью указанной LIGA-технологии были изготовлены ЗС типа петляющий волновод для ЛБВ, предназначенных для работы вплоть до 1 ТГц (см., например, [17–20]). Шероховатость поверхности изготовленных деталей не превысила 30…40 нм [20].
Хотя технологический процесс LIGA с использованием рентгеновского излучения и является многообещающим для экстремально точного изготовления компонентов устройств вакуумной микроэлектроники с высоким аспектным соотношением и хорошей вертикальностью боковых стенок, он остается очень дорогим (требуется дорогостоящий источник синхротронного излучения и маски из золота для экспонирования фоторезиста). Для снижения стоимости процесса изготовления была разработана и предложена LIGA-технология, в которой для облучения используют ультрафиолет (UV-LIGA) и соответствующие фоторезисты (SU-8, KMPR, AZ 40XT-11D) [21, 22]. С помощью UV-LIGA были изготовлены различные микроразмерные ЗС мм- и ТГц-диапазонов (см., например, [21–25]).
2 . ТЕХНОЛОГИИ НА ОСНОВЕ ГЛУБОКОГО РЕАКТИВНОГО ИОННОГО ТРАВЛЕНИЯ
Процесс глубокого реактивного ионного травления (Deep Reactive Ion Etching, DRIE) является вычитающим и заключается в последовательном удалении определенного объема материала из кремниевой подложки с целью формирования структур с высоким значением аспектного соотношения. Технология на основе DRIE, как и LIGA, использует процесс фотолитографии для создания шаблона, после чего выполняются циклы последовательного травления и нанесения защитного слоя. Производственный цикл травления кремния осуществляется в плазменной среде на основе газа SF6, за которым следует стадия нанесения защитного слоя (пассивирования) в среде C4F8. В результате последовательно повторяющихся процессов травления и пассивации формируется последовательность выступов (наростов) микронных размеров на боковой стенке травленой кремниевой структуры. Чтобы уменьшить размеры наростов на боковой стенке, кремниевую структуру окисляют в высокотемпературной кислородной печи до образования слоя диоксида кремния на боковой стенке. Затем диоксид кремния полностью растворяют с помощью плавиковой кислоты. Таким образом, с помощью указанных процессов сглаживают острые выступы на боковой стенке кремниевой структуры, что значительно улучшает шероховатость поверхности до субмикронного масштаба. На последнем этапе наносят металлическое покрытие на кремниевую структуру.
DRIE-технология была использована при изготовлении различных ЗС для ЛБВ и ЛОВ мм- и ТГц-диапазона (вплоть до 1.03 ТГц) [21, 26–31]. Измерения методами атомно-силовой микроскопии показали, что шероховатость поверхности ЗС, изготовленных по технологическому процессу DRIE, была порядка 30…40 нм, что не уступает шероховатости поверхности структур, изготовленных по технологиям, в основе которых лежит LIGA-процесс. В частности, в работе [26] DRIE-процесс был использован для формирования меандровой структуры из кремния на поверхности подложки. Размер полоска гребня в виде меандра был 30 мкм в ширину и 120 мкм в высоту, что соответствует аспектному соотношению сторон 4 : 1. Верх этой выступающей структуры впоследствии был металлизирован с помощью процесса на основе UV-LIGA с целью создания ЗС для ЛБВ диапазона 83.5 ГГц.
3. ТЕХНОЛОГИИ НА ОСНОВЕ ЭЛЕКТРОИСКРОВОЙ МИКРООБРАБОТКИ
Технологические подходы, основанные на электроискровой микрообработке (Electric Discharge Machining, EDM), используются для удаления материала из заготовки с помощью серии быстро повторяющихся разрядов между двумя электродами (один называется инструментальным электродом, другой – заготовкой), разделенными диэлектрической средой и находящимися под определенной разностью потенциалов [32]. Электроискровая обработка с применением проволоки (Wire Electric Discharge Machining, WEDM) использует диэлектрическую среду на водной основе и проволоку в качестве инструментального электрода. Данный технологический процесс позволяет изготавливать структуры с допуском до нескольких микрон, но в конечном счете все сильно зависит от условий технологичного процесса (диаметр проволоки, состав диэлектрической среды, величина разности потенциалов между электродами и т.д.). В качестве материала проволоки в основном используется латунь, молибден или вольфрам, а диаметр проволоки варьируется от 20 до 400 мкм. По сравнению с классическим процессом электроискровой обработки на масляной основе, технологический процесс с использованием проволоки и диэлектрической среды на водной основе может обеспечить лучшее качество поверхности. Микрообработка WEDM позволяет изготавливать отверстия и стержни микронного размера с большим аспектным соотношением вне зависимости от твердости обрабатываемых материалов [33, 34]. С помощью данной технологии были изготовлены ЗС типа петляющий волновод ЛБВ W‑диапазона [19]. К сожалению, шероховатость поверхностей изготовляемых структур не позволяет использовать технологию электроискровой микрообработки для создания ЗС в рабочих диапазонах существенно свыше 110 ГГц.
4. ТЕХНОЛОГИИ НА ОСНОВЕ МИКРО/НАНОФРЕЗЕРОВАНИЯ С ЧИСЛОВЫМ ПРОГРАММНЫМ УПРАВЛЕНИЕМ
Технологические процессы микрообработки на основе использования фрезерных станков с числовым программным управлением (ЧПУ), как и процессы на основе электроискровой микрообработки, относятся к классу так называемых вычитающих процессов. Используя классические фрезерные станки с ЧПУ, можно изготавливать ЗС с рабочей частотой до V-диапазона (50…75 ГГц) в силу недостаточной точности изготовления (порядка десятков микрон) и шероховатости поверхности. Недавно разработанные технологии так называемой наноразмерной обработки с использованием фрезерных ЧПУ-станков могут обеспечить точность порядка 1…5 мкм и шероховатость поверхности до 40 нм [35], что сравнимо с параметрами технологических процессов на основе UV-LIGA и DRIE. Такие технологии были использованы для создания различных ЗС в ТГц-диапазоне [35–38]. Технология наноразмерной обработки с использованием фрезерных станков с ЧПУ позволяет изготавливать структуры с точностью в единицы микрон и с шероховатостью в десятки нанометров. Однако они мало пригодны для массового производства из-за дороговизны и длительности процесса изготовления.
5. АДДИТИВНЫЕ ТЕХНОЛОГИИ
Технологические подходы на основе методов 3D-печати для изготовления базовых компонентов устройств вакуумной микроэлектроники представляются наиболее перспективными и многообещающими в ближайшем будущем. В последнее время было проведено немало исследований, направленных как на совершенствование технологий 3D-печати, так и на изучение их возможностей и пределов применения для изготовления базовых компонентов устройств вакуумной микроэлектроники [39–44], а также специальной измерительной оснастки. Среди методов 3D-печати рассмотрим технологические подходы на основе фотополимеризации жидкого полимера в ванне с использованием стереолитографии (SLA-технология и ее дальнейшее развитие в виде DLP/LCD-технологий и др.), селективное лазерное плавление (SLM) и селективное лазерное спекание (SLS), а также весьма перспективный подход, который основан на электрохимическом микроосаждении.
5.1. Аддитивные технологии с использованием жидких фотополимерных смол
Технологии на основе SLA и DLP используют жидкие фотополимерные смолы и источник света для изготовления деталей посредством 3D-печати. Ключевое различие между этими технологиями заключается в типе источника света, используемого для затвердевания фотополимерных смол: в SLA используется точечный источник УФ-излучения (лазерный луч), а в DLP используется микроэлектронно-механическое устройство из микрозеркал, положение которых управляется цифровым образом, при этом само микроэлектронно-механическое устройство может облучаться как видимым, так и ИК- или УФ-источником. Структуры, изготовленные по технологиям SLA и DLP, представляют собой трехмерные объекты из диэлектрика, которые требуют последующего покрытия необходимых частей конструкции металлом и дальнейшей сборки.
Анализ научной литературы показал, что применение технологических подходов на основе 3D-печати полимерными материалами для создания элементов устройств вакуумной микроэлектроники началось с изготовления компонентов устройств мм- и ТГц-диапазонов (вплоть до 325 ГГц) [40, 42, 44], в частности, прямых волноводных секций, делителей мощности, направленных ответвителей, волноводных секций с винтовой гофрировкой для СВЧ-ондуляторов, ЗС типа петляющий волновод и гребенка для ЛБВ и ЛОВ, рупорных антенн и т.д. Было установлено, что минимально достижимое на данный момент значение шероховатости поверхности изготовленных устройств составляет порядка 150 нм, что позволяет использовать указанные технологии в мм- и ТГц-диапазонах. В работе [41] с использованием 3D-принтера на основе DLP-технологии (“P4 Mini”, EnvisionTEC, Inc.) были изготовлены экземпляры ЗС типа петляющий волновод для ЛБВ W- и D-диапазонов. Точность изготовления указанных структур составила порядка 0.2…0.3%, что практически сравнимо с параметрами структур, изготовленных с использованием технологических подходов на основе UV-LIGA или нанофрезерования на основе станков с ЧПУ. Шероховатость поверхности изготовленных элементов после процедуры нанесения металлического покрытия, измеренная с использованием лазерного конфокального микроскопа, составила порядка 400 нм. Уровень обратных потерь в W- и D-диапазонов был не хуже 15…20 дБ, при этом потери на передачу не превысили 3 дБ, при длине всей системы порядка 15 мм.
В работе [44] с использованием 3D-принтера Projet 3500 HDMax (3D Systems), работающего по технологии послойного распыления жидкого полимера при помощи многоструйных головок с последующим фотоотверждением (Multi Jet Modeling – MJM), успешно продемонстрировано создание секции круглого волновода с винтовой гофрировкой для СВЧ-ондулятора, а также ЗС Ka-диапазона для лампы обратной волны с ленточным электронным пучком. Металлизация изготовленных полимерных изделий осуществлялась гальваническим способом с предварительной активацией поверхности палладием. Анализ полученных результатов холодных измерений потерь на передачу и на отражение изготовленных электродинамических структур показал перспективность предложенного подхода.
Авторами данной работы предложен и апробирован технологический маршрут, включающий 3D-печать с использованием LCD-технологии стереолитографической печати (LCD 3D-принтер Anycubic Photon, Shenzhen Anycubic Technology Co., Ltd), а также последующую металлизацию поверхности изготовленной структуры с использованием магнетронного распыления. Как и в классической 3D-печати на основе стереолитографии, в данном случае осуществляется отверждение жидкого фотополимерного материала (фотополимерная смола) слой за слоем. Источником света выступает система, где ультрафиолетовое излучение от светодиодов проходит сквозь жидкокристаллическую (LCD) матрицу, аналогичную той, что используется в дисплее смартфона или планшета, и засвечивает одновременно весь слой изделия целиком. Далее процесс повторяется для всех последующих слоев. Существенное преимущество LCD-технологии – низкая стоимость оборудования (в сравнении с SLA/DLP оборудованием), что позволяет значительно снизить затраты на прототипирование, при этом точность изготовления новейших версий LCD 3D-принтеров доходит до 22 мкм. На следующем этапе изготовленное изделие металлизируется с использованием технологии магнетронного распыления. Так как в процессе магнетронного распыления образец может нагреваться до температуры порядка 100°С, потребовалось использовать специализированную температуростойкую фотополимерную смолу Harz Labs Dental Yellow Clear, которая характеризуется длительной температурной стабильностью при 140°С и кратковременной стабильностью вплоть до 180°С, при этом усадка изделия не превышает 0.5%.
С целью тестирования и отработки всего технологического маршрута было изготовлено несколько образцов прямых волноводных секций D-диапазона (фланец WR6, сечение волноводного канала 1.651 × 0.8255 мм, частотный диапазон 110…170 ГГц). Образцы прямых волноводных секций проектировали и изготавливали таким образом, чтобы обеспечить металлизацию волноводного канала (рис. 2а). Измеренная с использованием стилусного профилометра Dektak 150 (Veeco Inc.) шероховатость (среднеквадратичное значение – СКЗ) стенок волноводного канала образцов изготовленных волноводных секций составила 1.5…2.0 мкм. Далее изготовленные образцы волноводных секций были металлизированы с использованием процесса магнетронного распыления (система NexDep, Angstrom Engineering). В качестве мишени для магнетронного распыления использована бескислородная медь марки М00б (чистота 99.99%), при этом с целью улучшения адгезии к поверхности полимерной смолы использован адгезионный подслой хрома толщиной порядка 50 нм. Профилометрические исследования образца-свидетеля показали, что толщина медного покрытия составила порядка 2 мкм. Измеренная шероховатость стенок волноводного канала волноводных секций после металлизации не превысила 1000 нм (СКЗ).
Рис. 2.
Прямая волноводная секция D-диапазона, изготовленная с помощью LCD фотополимерного 3D-принтера до процесса металлизации (а), изготовленная и собранная прямая волноводная секция D-диапазона в сравнении со стандартной волноводной секцией, входящей в комплект калибровочной оснастки векторного анализатора цепей (б), измерительная установка (в): 1 – векторный анализатор цепей ZVA40 (Rohde & Schwarz), 2 – частотные конвертеры D-диапазона ZVA170 (Rohde & Schwarz), 3 – прямая волноводная секция, изготовленная с помощью фотополимерной 3D-печати по LCD-технологии и металлизированная с использованием магнетроного распыления.
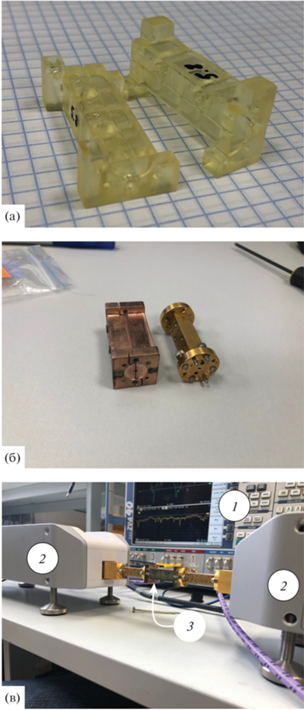
Было проведено исследование потерь на передачу и на отражение изготовленных образцов волноводных секций (рис. 2б): для измерений использовали измерительную установку на базе векторного анализатора цепей ZVA40 (Rohde & Schwarz) с частотными конвертерами ZVA-Z170 (Rohde & Schwarz) в D-диапазоне (рис. 2в). Анализ полученных результатов показал, что в диапазоне 110…170 ГГц погонные потери на передачу составляют порядка 1.3 дБ/см, при этом потери на отражение не хуже 10 дБ. Таким образом, были успешно отработаны основные этапы технологии прототипирования вспомогательной и измерительной оснастки для исследований в мм-диапазоне длин волн.
5.2. Аддитивные технологии на основе селективного лазерного спекания и плавления
Селективное или выборочное лазерное спекание (SLS) представляет собой метод аддитивного производства, в котором в качестве источника энергии для спекания порошкообразного материала используется лазерное излучение. Луч лазера проходит по поверхности порошкообразного материала согласно траекториям заложенной в компьютерную программу 3D-модели структуры и послойно спекает гранулы порошкообразного материала между собой. Селективное или выборочное лазерное плавление (SLM) использует аналогичную концепцию, но в SLM гранулы порошкообразного материала полностью расплавляются, что позволяет добиваться требуемых свойств материала готовой структуры (твердость, прочность, пористость и т.д.). Таким образом, процесс селективного лазерного спекания применяют для порошкообразных материалов из полимеров, пластмасс, керамики, в то время как селективное лазерное плавление подходит для металлических и металлокерамических порошкообразных материалов.
Технологические подходы на основе SLS и SLM использовались для изготовления прямых волноводных секций и рупорных антенн для работы в диапазонах частот до 325 ГГц [39, 43]. Было установлено, что поверхность устройств, изготовленных с использованием процессов SLS и SLM, имеет шероховатость порядка 1.5 и 2 мкм соответственно. В работе [39] отмечается, что измеренная шероховатость поверхности устройств, изготовленных с помощью процессов SLS и SLM, не отражает оптимального значения, которое может быть достигнуто путем применения ряда методов постобработки, например, микрообработкой с использованием потока жидкости под высоким давлением, содержащим абразивные микроразмерные частицы. Можно выделить несколько путей развития методов SLS и SLM, которые позволят решить существующие проблемы, связанные с неоптимальной величиной шероховатости поверхности изготовляемых структур, а также точностью их изготовления:
− измельчение порошкообразного материала (уменьшение размеров гранул),
− уменьшение длины волны используемого лазерного излучения,
− совершенствование оптических и механических систем транспортировки лазерного излучения с целью увеличения точности позиционирования и улучшения скоростных характеристик перемещения лазерного луча,
− разработка и развитие методов постобработки поверхности,
− оптимизация процесса печати за счет использования систем контроля размеров изготовляемых структур в трех измерениях.
5.3. Аддитивные технологии на основе электрохимического микроосаждения
Относительно недавно был предложен [45] и впоследствии реализован уже в виде коммерчески доступной системы [46] процесс 3D-печати, основанный на электрохимическом микроосаждении. В данном случае 3D-печать осуществляется посредством микролокального гальванопокрытия с использованием специально изготовленного кантилевера для атомно-силовой микроскопии, в котором сформировано сопло диаметром 300 нм. На указанное сопло подается электролит на основе сульфата меди. Печать изделия осуществляется посредством формирования трехмерных (объемных) пикселей – вокселей. Сопло перемещается по заданным координатам в трехмерном пространстве, осуществляя последовательную печать вокселей. Точность перемещения составляет не хуже 1 мкм, объем вокселя также не превышает 1 мкм3. Данная система позволяет печатать трехмерные изделия из меди, золота и никеля. Таким образом, было продемонстрировано построение нескольких периодов медной спирали из практически бесшовно сливающихся вокселей, которые печатаются последовательно [47]. В настоящее время одним из основных недостатков описанной системы является то, что она позволяет печатать объекты, размеры которых не должны превышать 1 × 1 × 1 мм3. Другими словами, построение полноразмерных макетов ЗС с использованием такой системы на данный момент не представляется возможным. Тем не менее, принципиальные технологические трудности, которые позволили бы увеличить размеры изготовляемых изделий, в первом приближении, отсутствуют.
Современная технология 3D-печати, в частности непосредственно металлом, еще не конкурентоспособна с точки зрения допусков на размеры и шероховатости поверхности изготовляемых структур по сравнению с большинством используемых технологий, таких как LIGA-процессы, DRIE-процессы, микроэлектроискровая обработка и т.д. Однако представляется, что с развитием технологий 3D-печати, а также смежных дисциплин, таких как материаловедение и технология микрообработки поверхности, она станет одной из основных при изготовлении ключевых элементов устройств вакуумной микроэлектроники мм- и ТГц-диапазонов [39].
6. МИКРООБРАБОТКА НА ОСНОВЕ ЛАЗЕРНОЙ АБЛЯЦИИ
Технологические подходы на основе процессов лазерной абляции с использованием нано-, пико- и фемтосекундных импульсов уже продемонстрировали свою применимость для высококачественной микрообработки металлов, полупроводников и диэлектриков в научных, технологических и медицинских применениях [48–52]. Среди преимуществ технологий микрообработки на основе лазерной абляции можно выделить бесконтактность процесса, малое количество составных стадий, отсутствие использования опасных химикатов, высокую гибкость процесса. В последнее время в связи с развитием технологий изготовления полупроводниковых лазерных источников, а также технологий управления положением лазерного луча, существенно возрос интерес к лазерной микрообработке нано-, пико- и фемтосекундными импульсами. Система на основе фемтосекундного лазерного источника обеспечивает прецизионную микрообработку с минимальной зоной термического воздействия, однако скорость обработки крайне низка, а стоимость оборудования довольно высока. Наносекундная лазерная система микрообработки намного более рентабельна и обеспечивает быструю скорость обработки, однако характеризуется довольно большой зоной термического воздействия и требует существенной постобработки поверхности. Эффективность и точность обработки с помощью пикосекундной лазерной системы позиционируется примерно посередине упомянутых выше преимуществ и недостатков фемто- и наносекундных систем.
В работах [53–55] предложен оригинальный подход к изготовлению планарной ЗС в виде металлической микрополосковой меандровой линии на диэлектрической подложке. Такие конструкции ЗС в настоящее время привлеклают большое внимание. Среди их преимуществ следует выделить относительную простоту и компактность конструкции, возможности работы при относительно низких ускоряющих напряжениях и широкополосность [56–59]. Предлагаемый подход основан на сочетании технологических процессов магнетронного распыления и наносекундной лазерной абляции с ЧПУ. Процесс магнетронного распыления гибок в плане возможности нанесения тонкопленочных покрытий из различных металлов, полупроводников и диэлектриков толщиной вплоть до 10 мкм и более, а также позволяет изготавливать многослойные тонкопленочные покрытия. Наносекундная лазерная абляция осуществлялась с использованием коммерчески доступных прецизионных лазерных станков с ЧПУ “МиниМаркер-2” и “МикроСет” (ООО “Лазерный центр”) на основе импульсного волоконного YAG:Nd лазера с длиной волны 1064 нм (IPG Photonics) и гальваносканерами (рис. 3а). Длительность лазерных импульсов варьировалась от 200 до 4 нс, частота следования импульсов изменялась в диапазоне 1.6…100 кГц, скорость движения лазерного луча составляла 50…4000 мм/с.
Рис. 3.
Прецизионная коммерчески доступная система “МикроСет” для микрообработки наносекундными лазерными импульсами (а) и оригинальная конструкция системы лазерной микрообработки пикосекундными импульсами (б).
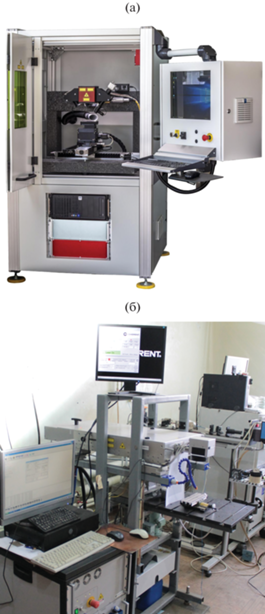
На основании анализа полученных результатов можно выделить несколько преимуществ предлагаемого подхода:
– высокая скорость изготовления ЗС, весь технологический процесс может быть проведен за один день,
– низкая стоимость изготовления ЗС по сравнению с технологиями на основе фотолитографии,
– высокая гибкость процесса изготовления, которая позволяет оперативно вносить изменения в дизайн ЗС.
Были изготовлены экземпляры микрополосковых меандровых ЗС для V- [53, 60, 61] и W-диапазонов [62, 63] (рис. 4).
Рис. 4.
Микрополосковые меандровые ЗС V- (а) и W‑диапазонов (б), изготовленные с использованием наносекундной лазерной абляции, а также ЗС D-диапазона, изготовленная с использованием пикосекундной лазерной абляции (в); пластины из кварца толщиной 500 и 200 мкм использованы в качестве диэлектрических подложек; (изображения получены с помощью СЭМ).
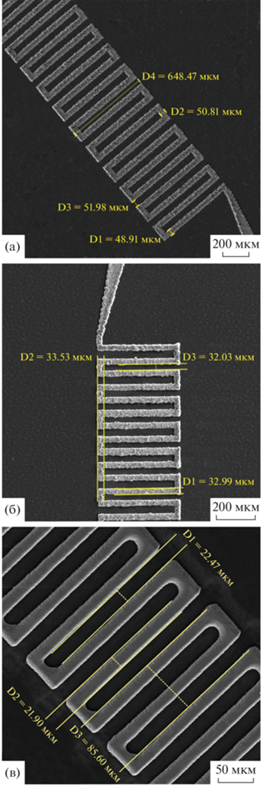
Результаты холодных измерений электродинамических параметров показали, что потери на передачу (S21) изготовленных ЗС не превышают 10 дБ/см, а потери на отражения (S11) не хуже 10 дБ. Полученные результаты экспериментальных исследований согласуются с численным моделированием с использованием программных пакетов ANSYS HFSS и COMSOL Multiphysics.
Описанный выше подход был усовершенствован с целью изготовления планарных ЗС меандрового типа на диэлектрической подложке для D-диапазона с помощью различных прецизионных лазерных станков с ЧПУ, работающих с лазерными импульсами нано- и пикосекундной длительности [64]. Для осуществления процесса пикосекундной лазерной абляции был использован лазерный станок с ЧПУ оригинальной сборки (см. рис. 3б), оснащенный импульсным лазерным источником с длиной волны 1064 нм (Coherent Inc.). Параметры лазерной абляции были следующие: длительность одиночного импульса 10 пс, частота повторения импульсов варьировалась в диапазоне 80 кГц…1 МГц, скорость перемещения лазерного луча – в диапазоне 200…1000 мм/с.
Несколько образцов ЗС D-диапазона были изготовлены и исследованы методами сканирующей электронной микроскопии и профилометрии. Кроме того, были измерены потери на передачу и на отражение изготовленных структур с использованием векторного анализатора цепей и частотных конвертеров D-диапазона [14]. Установлено, что потери на передачу (S21) изготовленных ЗС не превышают 8.5 дБ/см, а потери на отражение (S11) не хуже 10 дБ.
Таким образом, как нано-, так и пикосекундный процесс лазерной абляции позволяет изготавливать микрополосковые структуры D-диапазона с необходимыми размерами, однако существенным преимуществом лазерной абляции пикосекундными импульсами является практически полное отсутствие продуктов абляции (капли, наплывы и т.д.) по краям зоны абляции. Образцы ЗС, изготовленные с использованием наносекундной лазерной абляции, требуют существенной постобработки из-за образования продуктов абляции микронного размера на краях формируемых структур. Предварительный анализ полученных результатов показал, что следует обращать внимание на следующие моменты при использовании процесса на основе лазерной абляции:
– шероховатость поверхности после процесса лазерной абляции, особенно вблизи краев зоны абляции;
– адгезия тонкой металлической пленки к диэлектрической подложке до и после процесса лазерной абляции;
– постобработка поверхности структур, особенно после наносекундной лазерной абляции.
В качестве следующего шага планируется изучить перспективы использования фемтосекундной лазерной абляции для формирования планарных ЗС на диэлектрических подложках G-диапазона (170…260 ГГц).
Авторы заявляют об отсутствии конфликта интересов.
Список литературы
Dhillon S.S., Vitiello M.S., Linfield E.H. et al. // J. Phys. D. Appl. Phys. 2017. V. 50. № 4. P. 043001. https://doi.org/10.1088/1361-6463/50/4/043001
Lewis R.A. // J. Phys. D. Appl. Phys. 2014. V. 47, № 37. P. 374001. https://doi.org/10.1088/0022-3727/47/37/374001
Booske J.H., Dobbs R.J., Joye C.D. et al. // IEEE Trans. 2011. V. THZ-1. № 1. P. 54. https://doi.org/10.1109/TTHZ.2011.2151610
Song H.-J., Nagatsuma T. // IEEE Trans. 2011. V. TST-1. № 1. P. 256. https://doi.org/10.1109/TTHZ.2011.2159552
Appleby R., Wallace H.B. // IEEE Trans. 2007. V. AP-55. № 11. P. 2944. https://doi.org/10.1109/TAP.2007.908543
Wallace H.B. // Appl. Opt. 2010. V. 49. № 19. P. E38. https://doi.org/10.1364/AO.49.000E38
Federici J.F. // J. Infrared, Millimeter, Terahertz Waves. 2012. V. 33. № 2. P. 97. https://doi.org/10.1007/s10762-011-9865-7
Siegel P.H. // IEEE Trans. 2004. V. MTT-52. № 10. P. 2438. https://doi.org/10.1109/TMTT.2004.835916
Grigoriev A.D., Ivanov V.A., Molokovsky S.I. Microwave Electronics. Cham: Springer, 2018. https://doi.org/10.1007/978-3-319-68891-6
Madou M.J. Fundamentals of Microfabrication. Boca Raton: CRC Press, 2002.
Zaouk R., Park B.Y., Madou M.J. Microfluidic Techniques / Ed. by S.D.Menteer. Totowa: Humana Press Inc., 2006. P. 5.
Wang S., Aditya S., Xia X. et al. // IEEE Trans. 2019. V. PS-47. № 10. P. 4650. https://doi.org/10.1109/TPS.2019.2940254
Li X., He T., Wang H. et al. // J. Eng. 2018. V. 2018. № 14. P. 692. https://doi.org/10.1049/joe.2018.0095
Ryskin N.M., Torgashov R.A., Starodubov A.V. et al. // J. Vacuum Sci. Technol. B. 2021. V. 22. № 1. P. 013204. https://doi.org/10.1116/6.0000716
Ulisse G., Krozer V. // IEEE Electron Device Lett. 2017. V. 38. № 1. P. 126. https://doi.org/10.1109/LED.2016.2627602
Tolfree D.W.L. // Reports Prog. Phys. 1998. V. 61. № 4. P. 313–351. https://doi.org/10.1088/0034-4885/61/4/001
Bhattacharjee S., Booske J.H., Kory C.L. et al. // IEEE Trans. 2004. V. PS-32. № 3. P. 1002. https://doi.org/10.1109/TPS.2004.828886
Han S.-T., Jang K.-H., So J.-K. et al. // IEEE Trans. 2004. V. PS-32. № 1. P. 60. https://doi.org/10.1109/TPS.2004.823978
Shin Y.M., So J.K., Han S.T. et al. // Appl. Phys. Lett. 2006. V. 88. № 9. P. 091916. https://doi.org/10.1063/1.2178770
Jang K.H., Choi J.J., Kim J.H. // J. Korean Phys. Soc. 2019. V. 75. № 9. P. 716. https://doi.org/10.3938/jkps.75.716
Shin Y.M., Barnett L.R., Gamzina D. et al. // Appl. Phys. Lett. 2009. V. 95. № 18. P. 181505. https://doi.org/10.1063/1.3259823
Chua C., Tsai J.M., Aditya S. et al. // IEEE Trans. 2011. V. ED-58. № 11. P. 4098. https://doi.org/10.1109/TED.2011.2165284
Li H., Li Y., Feng J. // IEEE Electron Device Lett. 2013. V. 34. № 3. P. 462. https://doi.org/0.1109/LED.2013.2241389
Joye C.D., Cook A.M., Calame J.P. et al. // IEEE Trans. 2014. V. ED-61. № 6. P. 1672. https://doi.org/10.1109/TED.2014.2300014
Yao L. Yao J.-Y., Yang Z.-Q. et al. // IEEE Nanotechnology Magazine. V. 13. № 5. P. 35. 2019. https://doi.org/10.1109/MNANO.2019.2927798
Sengele S., Jiang H., Booske J.H. et al. // IEEE Trans. 2009. V. ED-56. № 5. P. 730. https://doi.org/10.1109/TED.2009.2015416
Lueck M.R., Malta D., Gilchrist K. et al. // J. Micromechanics Microengineering. 2011. V. 21. № 6. P. 065022. https://doi.org/10.1088/0960-1317/21/6/065022
Kreischer K.E., Tucek J.C., Gallagher D.A., Mihailovich R.E. // 2008 33rd Int. Conf. Infrared, Millimeter and Terahertz Waves. Pasadena. 15–19 Sept. N.Y.: IEEE, 2008. P. 4665704. https://doi.org/10.1109/ICIMW.2008.4665704
Tucek J.C., Basten M.A., Gallagher D.A., Kreischer K.E. // 2013 IEEE 14th Int. Vacuum Electronics Conf. (IVEC). Paris. 21–23 May. N.Y.: IEEE, 2013. P. 6571144. https://doi.org/10.1109/IVEC.2013.6571144
Tucek J.C., Basten M.A., Gallagher D.A., Kreischer K.E. // IEEE Int. Vacuum Electronics Conf. Monterey. 22–24 Apr. 2014. N.Y.: IEEE, 2014. P. 153. https://doi.org/10.1109/IVEC.2014.6857535
Tucek J.C., Basten M.A., Gallagher D.A., Kreischer K.E. // 2016 IEEE Int. Vacuum Electronics Conf. (IVEC). Monterey. 19–21 Apr. N.Y.: IEEE, 2016. P. 7561772. https://doi.org/10.1109/IVEC.2016.7561772
Chung D.K., Lee K.H., Jeong J., Chu C.N. // Int. J. Precis. Eng. Manuf. 2014. V. 15. № 9. P. 1785. https://doi.org/10.1007/s12541-014-0530-7
Lim H.S., Wong Y.S., Rahman M., Lee M.K.E. // J. Mater. Process. Technol. 2003. V. 140. № 1–3. P. 318. https://doi.org/10.1016/S0924-0136(03)00760-X
Uriarte L., Herrero A., Ivanov A. et al. // Proc. Inst. Mech. Eng. Pt C. J. Mech. Eng. Sci. 2006. V. 220. № 11. P. 1665. https://doi.org/10.1243/09544062JMES220
Baig A., Gamzina D., Kimura T. et al. // IEEE Trans. 2017. V. ED-64. № 5. P. 2390. https://doi.org/10.1109/TED.2017.2682159
Gamzina D., Himes L.G., Barchfeld R. et al. // IEEE Trans. 2016. V. ED-63. № 10. P. 4067. https://doi.org/10.1109/TED.2016.2594027
Choi W., Lee I., Choi E.M. // IEEE Trans. 2017. V. ED-64. № 7. P. 2955. https://doi.org/10.1109/TED.2017.2706059
Hu P., Lei W., Jiang Y. et al. // IEEE Trans. 2018. V. ED-65. № 6. P. 2164. https://doi.org/10.1109/TED.2017.2787682
Zhang B., Guo Y.-X., Zirath H., Zhang Y.P. // Proc. IEEE. 2017. V. 105. № 4. P. 723. https://doi.org/10.1109/JPROC.2016.2639520
Shen J., Ricketts D.S. // IEEE Trans. 2019. V. MTT-67. № 3. P. 883. https://doi.org/10.1109/TMTT.2018.2889452
Cook A.M., Joye C.D., Calame J.P. // IEEE Access. 2019. V. 7. P. 72561. https://doi.org/10.1109/ACCESS.2019.2920291
Dimitriadis A.I., Debogović T., Favre M. et al. // Proc. IEEE. 2016. V. 105. № 4. P. 668. https://doi.org/10.1109/JPROC.2016.2629511
Zhang B., Zirath H. // IEEE Trans. 2016. V. CPMT-6. № 5. P. 796. https://doi.org/10.1109/TCPMT.2016.2550483
Проявин М.Д., Вихарев А.А., Федотов А.Э. и др. // Изв. вузов. Радиофизика. 2020. Т. 63. № 5–6. С. 521. https://doi.org/10.1007/s11141-021-10072-0
Hirt L., Ihle S., Pan Z. et al. // Adv. Mater. 2016. V. 28. № 12. P. 2311. https://doi.org/10.1002/adma.201504967
Ercolano G., Zambelli T., van Nisselroy C. et al. // Adv. Eng. Mater. 2020. V. 22. № 2. P. 1900961. https://doi.org/10.1002/adem.201900961
Ulisse G., Schurch P., Koelmans W.W., Krozer V. // 46th Int. Conf. Infrared, Millimeter and Terahertz Waves (IRMMW-THz). Chengdu. 29 Aug.–3 Sept. N.Y.: IEEE, 2021. P. 9567223. https://doi.org/10.1109/IRMMW-THz50926.2021.9567223
Žemaitis A., Gaidys M., Brikas M. et al. // Sci. Rep. 2018. V. 8. P. 17376. https://doi.org/10.1038/s41598-018-35604-z
Liu C., Fu X., Wu Y. et al. // J. Vac. Sci. Technol. B Microelectron. Nanom. Struct. 2009. V. 27. № 3. P. 1319. https://doi.org/10.1116/1.3119676
Leitz K.H., Redlingshöfer B., Reg Y. et al. // Phys. Procedia. 2011. V. 12, Pt 2. P. 230. https://doi.org/10.1016/j.phpro.2011.03.128
Keller W.J., Shen N., Rubenchik A.M. et al. // J. Appl. Phys. 2019. V. 125. № 8. P. 085103. https://doi.org/10.1063/1.5080628
Sugioka K., Cheng Y. // Appl. Phys. Rev. 2014. V. 1. № 4. P. 041303. https://doi.org/10.1063/1.4904320
Ryskin N.M., Rozhnev A.G., Starodubov A.V. et al. // IEEE Electron Device Lett. 2018. V. 39. № 5. P. 757. https://doi.org/10.1109/LED.2018.2821770
Starodubov A.V., Serdobintsev A.A., Pavlov A.M. et al. // Progress in Electromagnetics Research Symp. (PIERS-Toyama). Toyama. 1–4 Aug. N.Y.: IEEE, 2018. P. 506. https://doi.org/10.23919/PIERS.2018.8597953
Starodubov A.V., Serdobintsev A.A., Pavlov A.M. et al. // IEEE Int. Vacuum Electronics Conf. (IVEC-2018). Monterey. 26–28 Apr. N.Y.: IEEE, 2018. P. 333. https://doi.org/10.1109/IVEC.2018.8391512
Гуляев Ю.В., Жбанов А.И., Захарченко Ю.Ф. и др. // РЭ. 1994. V. 39. № 12. P. 2049.
Benedik A.I., Rozhnev A.G., Ryskin N.M. et al. // 2015 IEEE Int. Vacuum Electronics Conf. (IVEC). Beijing. 27–29 Apr. N.Y.: IEEE, 2015. P. 7223750. https://doi.org/10.1109/IVEC.2015.7223750
Sumathy M., Augustin D., Datta S.K. et al. // IEEE Trans. 2013. V. ED-60. № 5. P. 1769. https://doi.org/10.1109/TED.2013.2252179
Wang S., Aditya S., Xia X. et al. // IEEE Trans. Electron Devices. 2018. V. ED-65. № 6. P. 2142. https://doi.org/10.1109/TED.2018.2798575
Starodubov A.V., Serdobintsev A.A., Pavlov A.M. et al. // IEEE Int. Vacuum Electronics Conf. (IVEC-2018). Monterey. 26–28 Apr. N.Y.: IEEE, 2018. P. 421. https://doi.org/10.1109/IVEC.2018.8391530
Ulisse G., Starodubov A.V., Galushka V.V. et al. // Int. Vacuum Electronics Conf. (IVEC). Busan. 28 Apr.–1 May. N.Y.: IEEE, 2019. P. 8744932. https://doi.org/10.1109/IVEC.2019.8744932
Starodubov A.V., Pavlov A.M., Galushka V.V. et al. // Int. Vacuum Electronics Conf. (IVEC). Busan. 28 Apr.–1 May. N.Y.: IEEE, 2019. P. 8745185. https://doi.org/10.1109/IVEC.2019.8745185
Торгашов Р.А., Рыскин Н.М., Рожнев А.Г. и др. // ЖТФ. 2020. Т. 20. № 4. С. 686. https://doi.org/10.21883/JTF.2020.04.49096.294-19
Starodubov A.V., Serdobintsev A.A., Kozhevnikov I.O. et al. // Proc. SPIE. 2020. V. 11458. Article № 1145803. https://doi.org/10.1117/12.2564423
Дополнительные материалы отсутствуют.
Инструменты
Радиотехника и электроника