Теплоэнергетика, 2021, № 1, стр. 30-42
Проектирование основного теплообменного оборудования ORC-системы для двигателей внутреннего сгорания судовых установок
И. С. Антаненкова a, *, А. П. Королева a, b, М. С. Французов b, c, **, А. А. Сухих a, В. В. Сычев a
a Национальный исследовательский университет “Московский энергетический институт”
111250 Москва, Красноказарменная ул., д. 14, Россия
b Центральный институт авиационного моторостроения им. П.И. Баранова
111116 Москва, Авиамоторная ул., д. 2, Россия
c Московский государственный технический университет им. Н.Э. Баумана
(Национальный исследовательский университет)
105005 Москва, 2-я Бауманская ул., д. 5, стр. 1, Россия
* E-mail: antanenkovais@mail.ru
** E-mail: mfrancuzov@yandex.ru
Поступила в редакцию 17.03.2020
После доработки 05.05.2020
Принята к публикации 20.05.2020
Аннотация
Внедрение технологии производства электроэнергии с использованием в так называемом органическом цикле Ренкина (Organic Rankine Cycle – ORC) низкокипящих рабочих тел в России перспективно для многих областей науки и техники. Многие промышленные и технологические процессы, работа механизмов и устройств зачастую сопровождаются выделением большого количества низкопотенциального (сбросного) тепла, которое, как правило, полезно не используется и рассеивается в окружающей среде. Одной из наиболее перспективных областей применения этой технологии является утилизация тепла выхлопных газов газотурбинных двигателей и дизель-генераторов на транспорте (автомобильном, железнодорожном, морском и речном), в газотранспортных системах, военной технике и пр. В частности, анализ технологических параметров работы современных судовых установок позволяет судить о применимости ORC-технологии для повышения их энергетической эффективности. Один из важнейших сдерживающих факторов применения на транспорте ORC-установок – необходимость создания компактных теплообменных аппаратов, в основе проектирования которых лежит расчет сложных термогидродинамических явлений – кипения и конденсации низкокипящих рабочих тел. В настоящей работе представлена расчетная методика предварительного проектирования теплообменных аппаратов ORC-установок – фреоновых парогенератора и конденсатора, основанная на методе последовательных приближений и позволяющая учитывать переменность теплофизических свойств используемых рабочих тел, особенности теплообменных процессов, изменения геометрических параметров аппаратов, влияние методов интенсификации процессов и т.д. Также приводятся результаты апробации предложенной методики для парогенератора и конденсатора ORC-установки на фторорганическом рабочем веществе R245fa. Получены основные геометрические и теплотехнические характеристики для проектирования оборудования ORC-установки, утилизирующей тепло уходящих газов двигателей внутреннего сгорания 6М32 судовой установки.
В настоящее время технология органического цикла Ренкина (ORC) переживает период бурного развития. За последние двадцать лет количество введенных в эксплуатацию коммерческих ORC-электростанций в мире достигло уровня 70 единиц в год, а их совокупная мощность – 2000 МВт. Анализ рынка производителей и поставщиков ORC-установок в Европе и США показал, что в последние годы их количество постоянно увеличивается, растет число успешно реализованных проектов и поданных заявок на изобретения и полезные модели. Российский рынок ORC-установок представлен, прежде всего, зарубежными производителями, которые напрямую или через дилерские договора с организациями занимаются разработкой и внедрением такого рода установок “под ключ” [1, 2].
Несмотря на наличие на мировом рынке довольно большого количества производителей ORC-оборудования и представленной ими обширной линейки продукции, далеко не всегда имеется возможность подобрать установку, оптимально соответствующую нуждам конечного потребителя. Однако существует не только проблема адаптации готовых решений к условиям России, актуальны также необходимость преодоления критической зависимости от зарубежных технологий и промышленной продукции с учетом политики импортозамещения и тенденции к энергосбережению ввиду сокращения доли затрат на энергетические ресурсы в себестоимости конечной продукции и услуг, что также стимулирует развитие отечественных исследований и разработок в этой сфере.
Одна из наиболее перспективных областей применения указанной технологии – утилизация тепла выхлопных газов газотурбинных двигателей и дизель-генераторов на транспорте (автомобильном, железнодорожном, морском и речном), в газотранспортных системах, военной технике и пр. Однако важнейшим сдерживающим фактором применения на транспорте ORC-установок является потребность в компактных теплообменных аппаратах, в основе проектирования которых лежит расчет сложных термогидродинамических явлений – кипения и конденсации низкокипящих рабочих тел. Сложность достоверного описания этих процессов при использовании математических моделей различного уровня заключается в необходимости учета теплофизических свойств рабочих тел в жидкой и газообразной фазах при достаточно высоких давлениях. Современный уровень развития вычислительных технологий термогидродинамических процессов позволяет описывать локальные явления в отдельных элементах конструкции теплообменных аппаратов. При этом остаются под вопросом расчет проектных параметров теплообменных аппаратов, а также использование имеющихся экспериментальных данных по теплофизическим свойствам и процессам фазового перехода.
ORC-ТЕХНОЛОГИЯ ДЛЯ СУДОВЫХ ЭНЕРГЕТИЧЕСКИХ УСТАНОВОК
Наибольший интерес при организации конструктивного исполнения элементов ORC-установки в условиях ограниченных возможностей размещения оборудования и специфики параметров внешних систем представляют судовые энергетические установки.
Анализ технологических параметров работы современных судовых установок позволяет судить о применимости ORC-технологии для повышения их энергетической эффективности. Прежде всего, технология актуальна для судовых дизельных двигателей внутреннего сгорания (ДВС), дальнейшее технологическое совершенствование которых направлено на повышение энергетического потенциала (среднего эффективного давления), снижение габаритов и массы, увеличение ресурсных показателей и повышение топливной экономичности, но никак не связано с возможным использованием тепла уходящих газов внутри термодинамического цикла [3].
В работе [4] представлены результаты термодинамического анализа эффективности цикла судовой утилизационной энергоустановки на низкокипящем рабочем веществе. При утилизации тепла уходящих газов ДВС 6М32 (MaK, Caterpillar, США) с температурой 300°С (на входе в утилизационный контур) и расходом 21 132 кг/ч максимальным КПД (28.8%) обладает сверхкритический цикл на рабочем веществе R245fa при заданных давлении перед фреоновой турбиной 8 МПа и температуре 280°С, температуре фреона в конденсаторе 20°С.
Следует отметить, что гидрофторуглерод R245fa достаточно часто рекомендуется к использованию в системах рекуперации тепла при повышенных температурах (прежде всего, в ORC-системах) [5]. Нетоксичный, озонобезопасный фреон R245fa относят к слабогорючим веществам (класс опасности А1) с температурой самовоспламенения примерно 410°С, что позволяет использовать его в термодинамическом цикле, сопоставимом по эффективности с циклами на бутане, пентане и его изомерах и обеспечивающем пожаробезопасность установки, поскольку отсутствует традиционный для ORC промежуточный контур с термомаслом.
Однако полученные в [4] термодинамические параметры в характерных точках цикла затруднительно использовать для апробации методики проектирования теплообменного оборудования ORC-установки ввиду отсутствия достоверных данных о теплофизических и переносных свойствах фреона R245fa в сверхкритической области, а также сложного теплообмена в этой области, требующего большого объема дополнительных экспериментальных исследований. Кроме того, проектированию установок на сверхкритические параметры, как правило, предшествуют создание, анализ эффективности и проработка технико-эксплуатационных характеристик установки на докритических параметрах.
Предлагаемая тепловая схема ORC-установки на низкокипящем рабочем веществе докритических параметров представлена на рис. 1. Докритический цикл ORC-контура, реализуемый в предложенной тепловой схеме, приведен на рис. 2.
Рис. 1.
Принципиальная тепловая схема ORC-установки для утилизации тепла уходящих газов судового ДВС. ФПГ – фреоновый парогенератор; ФТ – фреоновая турбина; ЭГ – электрогенератор; Р – рекуператор; К – конденсатор; Н – насос
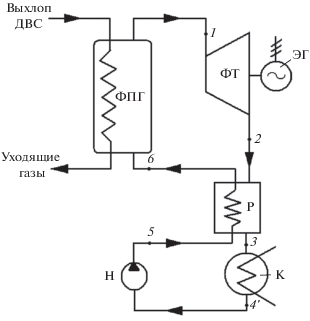
Рис. 2.
Докритический цикл на низкокипящем рабочем веществе, реализуемый в ORC-установке. 1–2 – обратимое расширение пара фреона в ФТ; 1‒2д – необратимое (действительное) расширение пара фреона в ФТ; 2(2д)–3 – охлаждение пара фреона в Р; 3–4' – охлаждение и конденсация фреона в конденсаторе, охлаждаемом забортной водой; 4''–4' – процесс конденсации фреона (фазовый переход из состояния “сухой насыщенный пар” в состояние “кипящая жидкость”); 4'–5 – обратимое сжатие жидкого фреона в Н; 4'–5д – необратимое (действительное) сжатие жидкого фреона в Н; 5(5д)–6 – подогрев жидкого фреона в Р (экономайзерная часть); 6–1 – испарение и перегрев пара фреона в ФПГ; 7'–7'' – процесс кипения фреона (фазовый переход из состояния “кипящая жидкость” в состояние “сухой насыщенный пар”)
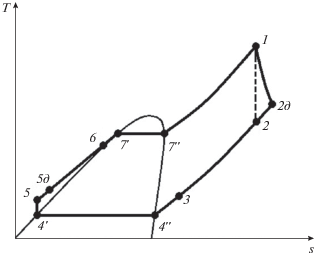
Фреоновый парогенератор (ФПГ) ORC-установки включает в себя две зоны: испарительную (парообразование при постоянных температуре и давлении) и перегревательную (перегрев сухого насыщенного пара от температуры насыщения до температуры на входе в турбину). Подогрев фреона от температуры после насоса до температуры насыщения удобно осуществлять уходящими газами фреоновой турбины в регенеративном теплообменнике. При докритических параметрах цикла этот теплообменник выполняет функции экономайзерной части парогенератора.
Результаты расчета параметров фреона [6] в характерных точках цикла (см. рис. 2) приведены в табл. 1.
Таблица 1.
Параметры фреона R245fa в характерных точках цикла ORC-установки
Точка (см. рис. 2) | Давление р, МПа | Температура t, °С | Плотность ρ, кг/м3 | Энтальпия h, кДж/кг | Энтропия s, кДж/(кг · К) | Теплоемкость ср, кДж/(кг · К) |
---|---|---|---|---|---|---|
1 | 2.500 | 250.00 | 86.27 | 649.96 | 2.1507 | 1.306 |
2 | 0.178 | 174.07 | 6.50 | 574.41 | 2.1507 | 1.122 |
2д | 0.178 | 190.72 | 6.25 | 593.30 | 2.1922 | 1.146 |
3 | 0.178 | 50.14 | 9.35 | 445.94 | 1.8157 | 0.969 |
4'' | 0.178 | 30.00 | 10.17 | 426.43 | 1.7534 | 0.973 |
4' | 0.178 | 30.00 | 1324.9 | 239.10 | 1.1355 | 1.333 |
5 | 2.500 | 30.83 | 1330.2 | 240.87 | 1.1355 | 1.327 |
5д | 2.500 | 32.17 | 1326.6 | 242.64 | 1.1413 | 1.329 |
6 | 2.500 | 130.00 | 945.58 | 390.00 | 1.5570 | 1.926 |
7' | 2.500 | 133.38 | 917.46 | 396.71 | 1.5736 | 2.056 |
7'' | 2.500 | 133.38 | 170.57 | 488.36 | 1.7990 | 2.092 |
Давление насыщения фреона в испарителе выбиралось максимально возможным (${{p}_{{{\text{кр}}}}}$ = = 3.651 МПа) при условии обеспечения минимального температурного напора на холодном конце испарителя не менее 15°С. Для проектируемой установки температура фреона на входе в турбину принята 250°С. Температура фреона в конденсаторе, равная 30°С, принималась исходя из рекомендаций по проектированию теплообменников судовых установок, охлаждаемых забортной водой [7]. Внутренний относительный КПД турбины был выбран 75%, насоса – 50% (по результатам анализа различных оценок, приведенных в литературе и каталогах производителей).
По расчетным данным, внутренний КПД цикла рассматриваемой ORC-установки электрической мощностью 184.25 кВт составляет 20.4% при расходе фреона 3.9 кг/с.
МЕТОДИКА РАСЧЕТА ТЕПЛООБМЕННИКОВ ORC-УСТАНОВКИ
Как правило, для проведения инженерных расчетов используются общеинтегральные методы, основанные на использовании усредненных показателей: температур, теплофизических свойств рабочих веществ, коэффициентов теплоотдачи и т.д., что может существенно сказаться на точности полученных результатов.
В настоящей работе предлагается методика выполнения проектных расчетов основного теплообменного оборудования ORC-установки, позволяющая учитывать такие локальные характеристики, как переменность теплофизических свойств рабочих тел, особенности теплообменных процессов, переменность геометрических параметров и т.д. В ее основу положен метод последовательных приближений геометрических характеристик проектируемого аппарата. В первом приближении задаются геометрические размеры теплообменника, после чего производится поинтервальная разбивка (последовательные сечения 1, 2, …, i, i + 1, …, N) условной теплообменной поверхности на участки, на каждом из которых выполняется условие равенства тепловых потоков от греющего теплоносителя к стенке и от стенки к нагреваемому теплоносителю. Затем определяются коэффициенты теплоотдачи, коэффициент теплопередачи и необходимая площадь теплообмена. В конечном итоге, сопоставление каждой новой итерации геометрических размеров теплообменника (исходя из полученной площади теплообмена) с заданными в предыдущем приближении позволяет получить проектные параметры аппарата.
Укрупненно методику расчета теплообменных аппаратов ORC-установки, обеспечивающих взаимодействие с внешними тепловыми источниками, можно представить следующим алгоритмом. После идентификации объекта производится расчет:
1) тепловой нагрузки;
2) температурных напоров;
3) теплоотдачи от внешнего теплоносителя;
4) теплоотдачи к низкокипящему рабочему телу на участке испарения/конденсации;
5) теплоотдачи к низкокипящему рабочему телу на участке перегрева/охлаждения;
6) коэффициентов теплопередачи на участках теплообменника;
7) необходимой поверхности теплообмена.
На рис. 3 представлена упрощенная расчетная схема теплообменного аппарата, условно разделенного на две зоны. Для фреонового парогенератора зона I является зоной кипения, зона II – перегрева пара; для конденсатора зона I – это зона охлаждения пара, зона II – конденсации. Из термодинамического расчета и уравнений теплового баланса определяются температуры рабочих тел на входе и выходе каждой зоны теплообменного аппарата.
Согласно схеме разбиения (см. рис. 3) в пределах каждой зоны рассчитывается температурный напор на каждом из участков i,…, N:
(1)
${{{\theta }}_{{I\_i}}} = \frac{{\Delta {{t}_{{{\text{max}}\_i}}} - \Delta {{t}_{{{\text{min}}\_i}}}}}{{\ln \left( {\frac{{\Delta {{t}_{{{\text{max}}\_i}}}}}{{\Delta {{t}_{{{\text{min}}\_i}}}}}} \right)}},$Следует отметить, что количество участков разбиения N зависит от интенсивности температурного перепада, реализованного на эффективной длине труб теплообменного аппарата: чем больше температурный перепад, тем больше и число участков. При дальнейшей апробации данной методики для разрабатываемого парогенератора количество участков разбиения было принято равным 100, для конденсатора – 10.
Для расчета теплоотдачи как со стороны внешних теплоносителей (дымовых газов, забортной воды), так и со стороны фреона необходимо задать геометрические параметры теплообменного оборудования. В то же время целью проектного расчета теплообменного оборудования является определение геометрических параметров. Решение поставленной задачи может быть получено методом последовательных приближений.
При проектировании теплообменного аппарата, помимо выбора геометрических параметров, следует также задать схему движения рабочих тел. В качестве первого приближения при апробации указанной методики расчета предлагается рассмотреть случай продольного обтекания внутренних трубок аппарата греющим рабочим телом. Такое предположение позволяет использовать одномерное приближение в расчетах, когда параметры изменяются только вдоль течения рабочих тел.
Геометрическими параметрами, задаваемыми для расчета кожухотрубного теплообменника в начальном приближении, являются следующие: внешний диаметр трубок теплообменника ${{d}_{{out}}},$ м; внутренний диаметр трубок теплообменника ${{d}_{{in}}},$ м; длина теплообменника L, м; диаметр теплообменника D, м; число трубок n.
Проходная площадь межтрубного пространства, м2, рассчитывается как
а омываемый периметр межтрубного пространства, м, по формуле
Тогда эквивалентный диаметр межтрубного пространства, м, равен
Допустив, что рабочее тело течет в межтрубном пространстве теплообменника в одном направлении, получаем возможность рассчитать его скорость, м/с, по формуле
где ${{G}_{{out}}}$ – расход рабочего вещества, кг/с; ${{\rho }_{{out\_i}}} = {{f}_{1}}\left( {{{p}_{{out}}},\,\,{{t}_{{out\_i}}}} \right)$ – плотность, определяемая термодинамическими параметрами рабочего вещества (давлением ${{p}_{{out}}}$ и температурой ${{t}_{{out\_i}}}$) в межтрубном пространстве, кг/м3.Число Рейнольдса для рассматриваемого потока
(6)
${\text{R}}{{{\text{e}}}_{{out\_i}}} = \frac{{{{w}_{{out\_i}}}{\kern 1pt} {{d}_{e}}}}{{{{{\nu }}_{{out\_i}}}}},$Расчет коэффициентов теплоотдачи для рабочих веществ является самостоятельной теплофизической задачей, решение которой применительно к фреоновому парогенератору и конденсатору ORC-установки будет предложено далее при апробации данной методики.
После определения коэффициентов теплоотдачи рассчитывается коэффициент теплопередачи, который учитывает особенности теплообмена при фазовом переходе фреона, конвекции внешнего теплоносителя и теплопроводности в твердой стенке трубы. Для расчета этого коэффициента на каждом участке предлагается использовать следующую упрощенную зависимость:
(7)
${{k}_{{I\_i}}} = \frac{1}{{\frac{1}{{{{\alpha }_{{out\_i}}}}} + \frac{{{{\delta }_{w}}}}{{{{\lambda }_{w}}}} + \frac{1}{{{{\alpha }_{{in\_i}}}}}}},$Одним из известных способов совершенствования теплообменных аппаратов является интенсификация теплообмена. В рассматриваемых аппаратах это возможно осуществить путем поперечного оребрения внешней поверхности труб.
Эффект интенсификации теплоотдачи вследствие развития поверхности может быть учтен введением коэффициента оребрения ${{{\eta }}_{f}}$ в качестве поправки к коэффициенту конвективной теплоотдачи потока в межтрубном пространстве
где ${{{\eta }}_{f}} = 1 + \left( {2\frac{{{{h}_{f}}}}{s}E - \frac{{{{\delta }_{f}}}}{s}} \right);$ ${{h}_{f}}$ – высота ребра, м; $E = \frac{{{\text{th}}\psi }}{\psi }$ – коэффициент эффективности работы одиночного прямого ребра; ${{\delta }_{f}}$ – толщина ребра, м; $s$ – шаг оребрения, м; $\psi = \frac{{{{h}_{f}}}}{{{{\delta }_{f}}}}\sqrt {2\frac{{{{\alpha }_{f}}{{\delta }_{f}}}}{{{{\lambda }_{f}}}}} ;$ ${{\alpha }_{f}}$ – коэффициент теплоотдачи на поверхности ребер, Вт/(м2 · К); ${{\lambda }_{f}}$ – коэффициент теплопроводности материала ребра, Вт/(м · К).Для теплообменных аппаратов, рассчитываемых в настоящей работе, коэффициент оребрения вводится как заданная величина для учета развития поверхности теплообмена со стороны межтрубного потока и не включает в себя поправки, которые могут быть вызваны комплексом сложных гидродинамических явлений, таких как разрыв пленки конденсата, шероховатость поверхности, залив межреберного пространства и т.д. Несомненно, что при увеличении степени детализации предлагаемой методики данные эффекты также могут быть учтены в расчетах.
Площадь поверхности теплообмена, м2, необходимая для зоны I, может быть получена из уравнения теплопередачи
(9)
${{S}_{I}} = \sum\limits_{i = 1}^N {\frac{{{{Q}_{{I\_i}}}}}{{{{k}_{{I\_i}}}{{{\theta }}_{{I\_i}}}}}} ,$Аналогично зоне I теплообменника (см. рис. 3) рассчитывается требуемая площадь поверхности зоны II. После определения коэффициента теплопередачи в этой зоне можно перейти к расчету необходимой теплообменной поверхности
(10)
${{S}_{{II}}} = \mathop \sum \limits_{i = 1}^N \frac{{{{Q}_{{II\_i}}}}}{{{{k}_{{II\_i}}}\,\,{{{\theta }}_{{II\_i}}}}}$,Суммарная площадь поверхности теплообмена, м2, складывается из полученных ранее площадей поверхностей зон I и II:
Таким образом, задачу проектного расчета теплообменника предлагается свести к определению необходимого числа труб, имеющих конкретные диаметр, длину, толщину стенки, по формуле
Сходимость предложенной методики проверяется методом последовательных приближений по числу труб.
РАСЧЕТ ФРЕОНОВОГО ПАРОГЕНЕРАТОРА
Рассматриваемый парогенератор представляет собой кожухотрубный теплообменник, в котором фреон R245fa заданных параметров (см. рис. 1, 2 и табл. 1) движется в трубном пространстве, а уходящие газы ДВС судовой установки – в межтрубном.
На рис. 4 представлены распределения температуры дымовых газов и R245fa в парогенераторе по зонам.
Рис. 4.
Изменение температуры рабочих тел во фреоновом парогенераторе по зонам. a–b – охлаждение дымовых газов для перегрева фреонового пара; b–c – охлаждение дымовых газов для испарения фреона, 7'–7'' – испарение фреона, 7''–1 – перегрев пара фреона
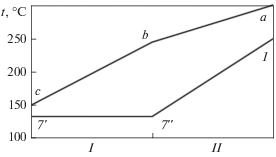
Температура дымовых газов на выходе из зоны II (перегрева пара) может быть определена из уравнения теплового баланса парогенератора при известных тепловых мощностях на участках теплообмена.
Тепловая мощность испарительного участка, Вт,
и участка перегрева пара ФПГ
где ${{G}_{R}}$ – расход фреона22, кг/с; ${{h}_{{{\kern 1pt} i}}}$ – энтальпии фреона в характерных точках цикла, кДж/кг (см. рис. 4 и табл. 1).Следует отметить, что теплофизические свойства дымовых газов существенно зависят от температуры (рис. 5) [8]. Как видно из представленных зависимостей, на участках испарения и перегрева в парогенераторе теплофизические свойства дымовых газов изменяются, что, в свою очередь, оказывает влияние на интенсивность теплоотдачи. В рассматриваемом диапазоне температур наименьшим изменениям подвержена изобарная теплоемкость – не более 3%, в то время как другие теплофизические свойства меняются не менее, чем на 20%.
Геометрические параметры фреонового парогенератора, заданные для расчета в начальном приближении, следующие:
Диаметр трубок теплообменника, м: |
внешний ${{d}_{{out}}}$ ............................................0.025 |
внутренний ${{d}_{{in}}}$ .........................................0.020 |
Длина теплообменника L, м ..........................2.0 |
Диаметр теплообменника D, м .......................1.0 |
Число трубок n, шт. .......................................200 |
Изменение числа Рейнольдса в последовательных сечениях теплообменника, рассчитанных по зависимости (6) для потока дымовых газов, движущегося в межтрубном пространстве парогенератора, показано на рис. 6, а.
Режим течения не только определяет интенсивность конвективного теплопереноса, но и влияет на суммарные гидравлические потери при движении дымовых газов в межтрубном пространстве. Теоретически в межтрубном пространстве могут реализоваться все три режима течения: ламинарный, переходный и турбулентный. Практически же гидравлические потери на выхлопном тракте способны привести к дополнительным потерям мощности основной силовой установки, в данном случае судового ДВС. Ввиду того что определение границы ламинарного режима течения осуществляется по критическому значению числа Рейнольдса ${{\operatorname{Re} }_{{cr}}},$ для обеспечения достаточного уровня теплоотдачи принимается условие, что ${{\operatorname{Re} }_{{e.g}}} > {{\operatorname{Re} }_{{cr}}},$ где ${{\operatorname{Re} }_{{e.g}}}$ – число Рейнольдса для потока дымовых газов33. Максимальное же значение числа Рейнольдса должно быть ограничено исходя из максимально допустимых потерь в выхлопном тракте ДВС.
После определения режима течения дымовых газов в межтрубном пространстве вычисляется безразмерный коэффициент теплоотдачи по зависимости [8]
(15)
${\text{N}}{{{\text{u}}}_{{e.g}}} = 0.113{{C}_{z}}{{C}_{s}}{\text{Re}}_{{e.g}}^{m}{\text{Pr}}_{{e.g}}^{{0.33}},$Вычисленное по (15) изменение числа Нуссельта дымовых газов в межтрубном пространстве приведено на рис. 6, б.
Как уже отмечалось, в отличие от дымовых газов, для которых по всей длине аппарата происходит только конвективный теплоперенос, для фреона теплообмен в парогенераторе осуществляется двумя процессами – кипением (испарением) и перегревом пара. Полное математическое описание гидродинамического процесса кипения рассматриваемой органической жидкости (R245fa) является довольно сложной задачей. К основным параметрам, влияющим на процесс испарения, можно отнести следующие: давление, форму и длину канала, массовую скорость, плотность теплового потока, теплофизические свойства рабочего тела.
При апробации методики постановка задачи была упрощена и процесс рассматривался как кипение в горизонтальных трубах. При этом жидкость, непрерывно подогреваемая снаружи, подавалась в канал и последовательно проходила несколько следующих характерных зон [9]:
пузырькового кипения с увеличивающимся паросодержанием потока, вплоть до перехода к дисперсно-кольцевому течению по достижении плотной упаковки пузырьков;
испарения кольцевой пленки при дисперсно-кольцевом течении;
испарения дисперсной влаги в ядре потока.
Поскольку в двух первых зонах в основном происходит контакт жидкой пленки с поверхностью твердой стенки, то можно считать, что параметры переноса определяются свойствами рабочего тела в жидком состоянии. Одним из параметров, характеризующих изменение теплоотдачи в двухфазном потоке, является паросодержание. В предлагаемой методике используется расходное массовое паросодержание
(16)
$x = {{{{G}_{{R\_{v}}}}} \mathord{\left/ {\vphantom {{{{G}_{{R\_{v}}}}} {{{G}_{{R\_mix}}}}}} \right. \kern-0em} {{{G}_{{R\_mix}}}}},$Следует также отметить, что зачастую в каналах наблюдается кризис кипения, под которым понимается резкое уменьшение коэффициента теплоотдачи вследствие прекращения контакта обогреваемой стенки с жидкой фазой и перехода к контакту с паровой фазой. На сегодняшний день не существует исчерпывающей теории, описывающей процесс высыхания жидкой пленки при кипении в канале, поэтому предлагаемые модели носят полуэмпирический или корреляционный характер.
После разделения канала на две части: докризисную и закризисную – коэффициент теплоотдачи вычисляют на каждом из участков в предположении малых значений передаваемых тепловых потоков и преимущественного влияния конвективной составляющей теплопереноса. Расчетная оценка, выполненная для условий поставленной задачи, подтверждает обоснованность такого предположения.
Плотность теплового потока, Вт/м2, необходимая для расчета коэффициента теплоотдачи фреона при пузырьковом кипении, может быть рассчитана по формуле В.В. Ягова [10]
(17)
$\begin{gathered} q = 3.43 \times {{10}^{{ - 4}}}\frac{{{{{\lambda }}_{{R\_l}}}^{2}{\Delta }{{T}^{3}}}}{{{{\nu }_{{R\_l}}}{{\sigma }_{{R\_l}}}{{T}_{s}}}} \times \\ \times \,\,\left( {1 + \frac{{{{r}_{R}}{\Delta }T}}{{2{{R}_{R}}T_{s}^{2}}}} \right)\left( {1 + \sqrt {1 + 800B} + 400B} \right), \\ \end{gathered} $На докризисном участке канала для определения конвективного коэффициента теплоотдачи может быть использована зависимость
(18)
${\text{N}}{{{\text{u}}}_{R}} = 0.023{\text{Re}}_{{R\_l}}^{{0.8}}{\text{Pr}}_{{R\_l}}^{{0.4}}\sqrt {1 + x\left( {\frac{{{{\rho }_{{R\_l}}}}}{{{{\rho }_{{R\_{v}}}}}} - 1} \right)} {\kern 1pt} ,$Для закризисной области теплоотдача может быть вычислена по следующей формуле:
(19)
${\text{N}}{{{\text{u}}}_{R}} = 0.023{\text{Re}}_{{R\_{v}}}^{{0.8}}{\text{Pr}}_{{R\_{v}}}^{{0.4}}\sqrt {x + \left( {1 - x} \right)\frac{{{{\rho }_{{R\_{v}}}}}}{{{{\rho }_{{R\_l}}}}}{\kern 1pt} } ,$Для оценки критического паросодержания можно использовать следующую полуэмпирическую зависимость [9]:
(20)
${{x}_{{cr}}} = \frac{{0.39 + 0.16{{p}_{s}} - 0.0212p_{s}^{2} + 0.00072p_{s}^{3}}}{{{{{\left( {\frac{{{{G}_{{R\_mix}}}}}{{{{F}_{{in}}} \times {{{10}}^{3}}}}} \right)}}^{{0.5}}}}},$Таким образом, функцию для расчета безразмерного коэффициента теплоотдачи на участке испарения фреона можно представить в виде [9]
(21)
$\left. \begin{gathered} {\text{N}}{{{\text{u}}}_{{R\_I}}}\left( {{\text{R}}{{{\text{e}}}_{R}},x} \right) = \\ = \,\,0.023{\text{Re}}_{{R\_l}}^{{0.8}}{\text{Pr}}_{{R\_l}}^{{0.4}}\sqrt {1 + x\left( {\frac{{{{\rho }_{{R\_l}}}}}{{{{\rho }_{{R\_{v}}}}}} - 1} \right)} ~ \\ {\text{для}}~\,\,\,\,x < {{x}_{{cr}}}; \\ {\text{N}}{{{\text{u}}}_{{R\_I}}}\left( {{\text{R}}{{{\text{e}}}_{R}},x} \right) = \\ = 0.023{\text{Re}}_{{R\_{v}}}^{{0.8}}{\text{Pr}}_{{R\_{v}}}^{{0.4}}\sqrt {x + \left( {1 - x} \right)\frac{{{{\rho }_{{R\_{v}}}}}}{{{{\rho }_{{R\_l}}}}}} \\ {\text{для}}~\,\,\,\,x > {{x}_{{cr}}}. \\ \end{gathered} \right\}.$Поскольку определение истинного паросодержания является весьма сложной задачей, для его расчета также рекомендуется использовать метод последовательных приближений. При этом в нулевом приближении задается линейное распределение паросодержания от 0 до 1.0 по длине испарительного участка парогенератора (i = 0, 1, 2, …, …, 100). Если предположить, что теплообмен между дымовыми газами и фреоном происходит без тепловых потерь, тогда для коэффициента теплоотдачи фреона в зоне I справедливо следующее выражение:
(22)
${{\alpha }_{{R{\text{\_}}I{\text{\_}}i}}} = {{\alpha }_{{e.g\_i}}}\frac{{\Delta {{F}_{{e.g\_i}}}}}{{\Delta {{F}_{{R\_I\_i}}}}}\frac{{\Delta {{t}_{{e.g\_i}}}}}{{\Delta {{t}_{{R\_I\_i}}}}}\frac{{{{G}_{{e.g}}}}}{{{{G}_{R}}}},$Выражение (22) позволяет оценить паросодержание на каждом из участков разбиения (рис. 7, а) и с использованием полученного распределения паросодержания определить изменение числа Нуссельта в последовательных сечениях теплообменника (рис. 7, б).
На рис. 7, б можно видеть скачкообразное изменение теплоотдачи, обусловленное кризисом кипения в канале. Представленная зависимость демонстрирует качественный характер изменения теплоотдачи на участке испарения. Наблюдаемое резкое ее падение вызвано образованием паровой пленки на стенке.
После определения теплоотдачи рассчитываются коэффициент теплопередачи (7) и площадь поверхности теплообмена, необходимая для участка испарения фреона (9).
На участке перегрева пара, происходящего в зоне II парогенератора, и для дымовых газов, и для фреона осуществляется конвективный теплоперенос. При этом для расчета коэффициента теплоотдачи со стороны газа также используется зависимость (15), а теплоотдача со стороны фреона на участке перегрева рассчитывается по формуле М.А. Михеева [11]
где ${\text{R}}{{{\text{e}}}_{R}}$ и ${\text{P}}{{{\text{r}}}_{R}}$ – числа Рейнольдса и Прандтля для перегретого пара фреона.Полученное изменение теплоотдачи со стороны дымовых газов и со стороны перегретого пара фреона в последовательных сечениях теплообменника приведено на рис. 8.
После определения изменения теплоотдачи можно рассчитать необходимую площадь поверхности теплообмена участка перегрева рабочего тела по формуле (10).
Таким образом, методом последовательных приближений при достижении сходимости расчета по числу труб были определены геометрические параметры фреонового парогенератора, представленные в табл. 2.
Таблица 2.
Геометрические параметры ФПГ
Характерный размер парогенератора | Значение | Без оребрения | С оребрением при ${{{\eta }}_{f}}$ = 3 | ||||
---|---|---|---|---|---|---|---|
$\frac{{{{S}_{{S\,G\_I}}}}}{{{{S}_{{S\,G\_\Sigma }}}}}$ | $\frac{{{{S}_{{S\,G\_II}}}}}{{{{S}_{{S\,G\_\Sigma }}}}}$ | n | $\frac{{{{S}_{{S\,G\_I}}}}}{{{{S}_{{S\,G\_\Sigma }}}}}$ | $\frac{{{{S}_{{S\,G\_II}}}}}{{{{S}_{{S\,G\_\Sigma }}}}}$ | n | ||
Диаметр трубок, м: | |||||||
${{d}_{{out}}}$ | 0.025 | 0.135 | 0.865 | 547 | 0.107 | 0.893 | 332 |
${{d}_{{in}}}$ | 0.020 | ||||||
Длина L, м | 2.0 | ||||||
Диаметр D, м | 1.0 | ||||||
Диаметр трубок, м: | 0.201 | 0.799 | 805 | 0.201 | 0.799 | 568 | |
${{d}_{{out}}}$ | 0.020 | ||||||
${{d}_{{in}}}$ | 0.018 | ||||||
Длина L, м | 3.0 | ||||||
Диаметр D, м | 1.5 |
В табл. 2 приведены также результаты расчета количества труб в парогенераторе при изменяемых геометрических параметрах ФПГ с учетом возможной интенсификации теплообмена путем оребрения стенок с принятым коэффициентом оребрения ${{{\eta }}_{f}}$ = 3.
Проведенный сравнительный анализ геометрических параметров показывает существенное влияние оребрения на характеристики проектируемого фреонового парогенератора.
РАСЧЕТ ФРЕОНОВОГО КОНДЕНСАТОРА
Рассматриваемый конденсатор представляет собой кожухотрубный теплообменник (см. рис. 3), в межтрубное пространство которого в состоянии перегретого пара поступает фреон R245fa заданных параметров (см. рис. 1, 2, табл. 1) и конденсируется на трубках, охлаждаемых забортной водой.
На участках охлаждения пара фреона (зона I) и конденсации (зона II) тепловая мощность определяется следующим образом:
где ${{h}_{i}}$ – энтальпия фреона в характерных точках цикла (см. табл. 1).Ввиду постоянства свойств забортной воды, используемой для охлаждения фреона в конденсаторе, с достаточной степенью точности ее массовый расход может быть вычислен как
(26)
${{G}_{{wat}}} = \frac{{{{Q}_{{C\_I}}} + {{Q}_{{C\_II}}}}}{{{{c}_{{p\_wat}}}\Delta {{t}_{{wat}}}}},$Основные геометрические параметры теплообменника-конденсатора (внутренний диаметр, рабочая длина трубок) выбраны по рекомендациям, приведенным в работе [7].
Методика проектного расчета предполагает корректное описание движения теплоносителей при сохранении условия равенства тепловых потоков от фреона к стенке трубы и от стенки к забортной воде. Для расчета коэффициентов теплоотдачи конденсатора, так же как и для испарителя, использовались реальные теплофизические свойства рабочих тел [6], зависящие от температуры.
Для расчета чисел Рейнольдса потоков рабочих тел в зоне I (охлаждения пара) для трубного и межтрубного пространства применялась зависимость (6), а для расчета теплоотдачи рабочих веществ – формула (23).
Изменения чисел Нуссельта по длине зоны I для пара фреона и забортной воды представлены на рис. 9.
На участке конденсации со стороны охлаждающей забортной воды теплоотдача определяется так же, как и для зоны I.
Полученные оценки чисел Рейнольдса пленки ${{\operatorname{Re} }_{{R\_l}}}$ конденсирующегося фреона свидетельствуют о ламинарном характере течения (${{\operatorname{Re} }_{{R\_l}}}$ < 1600), что позволяет использовать для расчета среднего коэффициента теплоотдачи следующую зависимость [10]:
(27)
${{\overline {{\text{Nu}}} }_{{R\_II}}} = 0.728{{\left( {\frac{{{{r}_{R}}g{{{\rho }}_{{R\_l}}}d_{{out}}^{3}}}{{{{{\lambda }}_{{R\_l}}}\Delta T{{{\nu }}_{{R\_l}}}}}} \right)}^{{{1 \mathord{\left/ {\vphantom {1 4}} \right. \kern-0em} 4}}}},$Рассчитанные по (27) числа Нуссельта со стороны фреона по длине зоны конденсации представлены на рис. 10.
После определения коэффициентов теплоотдачи коэффициенты теплопередачи по (7) и необходимая площадь поверхности теплообмена по (9)–(11) определяются аналогично тому, как это было сделано для ФПГ. Полученные в результате расчета геометрические параметры конденсатора приведены в табл. 3. Как и ранее для ФПГ, в этой таблице представлены результаты вычислений геометрических параметров конденсатора при интенсификации теплообмена путем оребрения стенок с принятым коэффициентом оребрения ${{{\eta }}_{f}}$ = 3.
Таблица 3.
Геометрические параметры конденсатора
Характерный размер конденсатора | Значение | Без оребрения | С оребрением при ${{{\eta }}_{f}}$ = 3 | ||||
---|---|---|---|---|---|---|---|
$\frac{{{{S}_{{C\_I}}}}}{{{{S}_{{C\_\Sigma }}}}}$ | $\frac{{{{S}_{{C\_II}}}}}{{{{S}_{{C\_\Sigma }}}}}$ | n | $\frac{{{{S}_{{C\_I}}}}}{{{{S}_{{C\_\Sigma }}}}}$ | $\frac{{{{S}_{{C\_II}}}}}{{{{S}_{{C\_\Sigma }}}}}$ | n | ||
Диаметр трубок, м: | |||||||
${{d}_{{out}}}$ | 0.025 | 0.235 | 0.765 | 213 | 0.197 | 0.803 | 112 |
${{d}_{{in}}}$ | 0.020 | ||||||
Длина L, м | 2.0 | ||||||
Диаметр D, м | 1.0 | ||||||
Диаметр трубок, м: | 0.287 | 0.713 | 402 | 0.224 | 0.776 | 174 | |
${{d}_{{out}}}$ | 0.020 | ||||||
${{d}_{{in}}}$ | 0.018 | ||||||
Длина L, м | 3.0 | ||||||
Диаметр D, м | 1.5 |
Предложенная в настоящей работе методика расчета может быть расширена и детализирована на основании более точного и полного описания теплофизических свойств рабочих веществ, механизмов теплообмена и гидродинамики при явлениях фазового перехода. Кроме того, актуальным представляется введение дополнительного гидравлического и прочностного одномерного расчета, что позволит более тщательно спроектировать конструкцию теплообменного аппарата.
ВЫВОДЫ
1. Приведенная в настоящей работе методика предварительного проектирования теплообменных аппаратов ORC-установок основана на методе последовательных приближений и позволяет учитывать переменность теплофизических свойств рабочих тел, особенности теплообменных процессов, изменения геометрических параметров аппаратов и пр.
2. Методика является универсальной, т.е. применима для различных рабочих веществ, схем их движения в проектируемых аппаратах, процессов теплообмена. Кроме того, она дает возможность анализировать влияние применяемых методов интенсификации теплообмена, что наглядно продемонстрировано полученными результатами.
3. Методика может быть дополнена имеющимися эмпирическими данными для более точного описания теплофизических свойств используемых рабочих веществ, механизмов теплообмена и гидродинамики при явлениях фазового перехода, расчетов теплотехнических характеристик аппаратов и пр.
4. Дополнение предложенной методики гидравлическим и прочностным расчетами позволит сформировать законченное представление о проектируемой конструкции теплообменного аппарата.
Список литературы
Денисов-Винский Н.Д. Некоторые экономические аспекты внедрения ORC-установок на промышленных предприятиях России // Энергорынок. 2014. Т. 119. № 4. С. 38–43.
Анализ современных технических решений при разработке ORC установок с органическими рабочими жидкостями / Ю.М. Бродов, О.В. Комаров, В.А. Седунин, В.Л. Блинов, И.С. Елагин // Проблемы энергетики. 2016. № 7–8. С. 24–31.
Барановский В.В., СаадЕддин Али. Обоснование выбора главных двигателей для перспективных надводных кораблей // Морской вестник. 2011. Т. 39. № 3. С. 56–58.
Антаненкова И.С., Ветренко А.А. Термодинамический анализ эффективности цикла судовой утилизационной энергоустановки на низкокипящем рабочем веществе // Морской вестник. 2019. Т. 70. № 2. С. 58–61.
Огуречников Л.А. Выработка электроэнергии на фреоне R245fa // Холодильная техника. 2019. № 1. С. 26–29.
База данных о теплофизических и переносных свойствах веществ NIST REFPROP DATABASE Version 8.0.
Агафонов В.А. Судовые конденсационные установки. Л.: Судпромгиз, 1963.
Тепловой расчет котлов (Нормативный метод). 3-е изд., перераб. и доп. СПб.: НПО ЦКТИ, 1998.
Солодов А. Электронный курс тепломассообмена. Математические и компьютерные модели тепломассообмена. В 2 т. Saarbrucken: Palmarium Academic Publishing, 2014.
Ягов В.В. Теплообмен в однофазных средах и при фазовых превращениях: учеб. пособие для вузов. М.: Издательский дом МЭИ, 2014.
Михеев М.А., Михеева И.М. Основы теплопередачи. М.: Энергия, 1977.
Дополнительные материалы отсутствуют.
Инструменты
Теплоэнергетика