Теплоэнергетика, 2021, № 1, стр. 85-94
Исследование влияния различных факторов на изменение концентрации щелочных элементов, вызывающих агломерацию слоя
Г. А. Рябов a, *, О. М. Фоломеев a, О. А. Смирнова a, Д. С. Литун a
a Всероссийский теплотехнический институт
115280 Москва, Автозаводская ул., д. 14, Россия
* E-mail: GARyabov@vti.ru
Поступила в редакцию 16.03.2020
После доработки 27.03.2020
Принята к публикации 21.04.2020
Аннотация
В последнее время все более актуальными становятся исследования процессов агломерации слоя при сжигании биомассы. Наибольшее влияние на процессы агломерации оказывают щелочные компоненты золы, которые, вступая в реакцию с силикатами, образуют легкоплавкие эвтектики. Поэтому очень важно определить критическую концентрацию прежде всего калия (наиболее легкоплавкие эвтектики) в слое, при которой начинается спекание частиц. Задачами экспериментальных исследований являлись изучение влияния на процесс агломерации частиц температуры и концентрации щелочных элементов при сжигании различных видов биомассы, а также биомассы и угля, наличия дренажа, определение критической концентрации калия в слое и расчетная оценка времени до начала спекания в условиях увеличения концентрации калия в слое. Приведены методика выполнения экспериментов и характеристики четырех исследованных видов биомассы. Представлены результаты по определению доли образования агломерированных частиц при различных температуре и концентрации щелочных элементов в слое. При замене части песка на оксиды железа агломерация проявляется только при высоких температурах (850°С и более). Полученные данные сопоставлены с результатами подобных опытов, выполнявшихся при ожижении слоя, рассмотрено влияние на процессы агломерации скорости ожижения, размеров частиц и избытка воздуха. Отмечено, что при неподвижном слое предельные концентрации калия минимальны. Показана необходимость изучения на реальных объектах зависимости изменения концентрации калия в слое от времени их эксплуатации. Практический интерес представляет выбор доли дренажа материала слоя с добавкой отсеянного материала или свежего песка. Приведены методика расчета и полученные с ее помощью расчетные данные по изменению концентрации калия в слое в различных условиях. Определены доли дренажа слоя при сжигании подсолнечной лузги и кородревесных отходов, а также показано, что совместное сжигание лузги и угля резко снижает вероятность агломерации слоя.
Актуальность исследования процессов агломерации слоя при сжигании органических видов топлива в производстве тепла и электроэнергии связана с постоянно увеличивающейся долей биомассы, как наиболее доступного возобновляемого источника энергии. Нарастающий интерес к возобновляемым энергетическим ресурсам в мире обусловлен неуклонным ростом энергопотребления, а также с увеличивающимися выбросами парниковых газов в атмосферу. Биоэнергетика, основанная на получении с применением любых высокорентабельных технологий топлива и энергии из биомассы, в том числе из органических отходов растительного и животного происхождения, – это быстроразвивающаяся отрасль современной мировой энергетики.
Одна из важных проблем сжигания биомассы, прежде всего сельскохозяйственных и некоторых промышленных отходов, в кипящем слое (КС) с традиционным наполнителем (песком) – это агломерация слоя. Она может приводить к спеканию частиц материала слоя, ухудшению и даже прекращению ожижения. Процессы агломерации слоя изучаются уже более 20 лет, но до сих пор при эксплуатации котлов возникают те же проблемы [1].
В [2] выполнен анализ зарубежных и отечественных исследований, направленных на выявление основных закономерностей процессов агломерации в котлах с кипящим слоем при сжигании биомассы. Показано, что наибольшее влияние на процессы агломерации оказывают щелочные компоненты золы, которые, вступая в реакцию с силикатами, образуют легкоплавкие эвтектики. Поэтому определение критической концентрации в слое наиболее легкоплавких эвтектик, прежде всего калия в соединении с кремнием, при образовании которой начинается спекание частиц, – это одна из самых важных задач.
Данные по критической концентрации довольно сильно различаются. В [3] указывается, что при температуре более 800°С для K2CO3 критическим является его 1%-ное содержание в слое, что соответствует 0.6% содержания калия в соответствующей химической форме. В [4] по результатам сжигания кукурузных початков в котле с кипящим слоем дается диапазон критических концентраций калия в слое от 1.25% при температуре 800°С до 0.93% при 850°С.
Обзор мер по предотвращению агломерации приведен в работах [1, 5, 6]. Помимо применения технологии совместного сжигания с углем, использования различных аддитивов и наполнителей слоя, традиционным способом предотвращения агломерации слоя при сжигании биотоплив служит повышенный дренаж слоя с соответствующей добавкой свежего инертного материала. Согласно зарубежным данным, для котлов паропроизводительностью более 50 т/ч при сжигании древесных отходов добавка песка может составлять 7–20 т в день. При этом используется схема регенерации донной золы, заключающаяся в том, что проводится ее отсев, крупная фракция удаляется, а мелкая возвращается в топку. В [7] впервые в России был представлен анализ собственных данных и обобщены результаты некоторых зарубежных исследований для составления рекомендаций по предотвращению агломерации слоя – создание повышенного дренажа слоя и добавление свежего песка.
Исходя из изложенного экспериментальные исследования проводились с целью изучить влияние температуры слоя и концентрации щелочных элементов при сжигании различных видов биомассы, определить критическую концентрацию калия и оценить расчетным путем время до начала агломерации в условиях накопления концентрации калия в слое, а также установить влияние дренажа и совместного сжигания биомассы и угля на процесс спекания.
МЕТОДИКА ПРОВЕДЕНИЯ ОПЫТОВ
Опыты проводили в печи на золе разных видов биомасс, песке и смеси песка и золы. Масса пробы составляла 5 г. На подложку насыпали слой материала высотой до двух-трех диаметров частиц (1–2 мм). Диапазон температур обработки слоя составлял 670–900°С. Выдержка проб варьировалась от 15 мин до 1 ч при постоянной температуре. Затем пробы вынимали, охлаждали и взвешивали неспекшийся материал. В качестве биомассы использовали золу подсолнечной лузги ООО “Элеватор” (г. Кумертау) (№ 1), золу пеллет из подсолнечной лузги (г. Тамбов) (№ 2), золу древесных строительных отходов (Подмосковье) (№ 3) и золу пеллет из торфа (№ 4). Состав золы на прокаленную массу для четырех видов проб представлен в таблице.
Состав золы различного происхождения на прокаленную массу, % (по массе)
Элемент | Вид золы биомассы | |||
---|---|---|---|---|
№ 1 | № 2 | № 3 | № 4 | |
SiO2 | 2.94 | 14.32 | 9.46 | 50.50 |
TiO2 | 0.05 | 0.36 | 0.32 | 0.68 |
Al2O3 | 0.85 | 2.83 | 1.52 | 15.15 |
Fe2O3 | 0.50 | 11.45 | 5.11 | 9.11 |
CaO | 26.98 | 11.31 | 35.17 | 11.20 |
MgO | 14.16 | 8.19 | 4.25 | 2.71 |
K2O | 36.46 | 25.73 | 3.96 | 1.30 |
Na2O | 0.74 | 3.44 | 0.62 | 0.45 |
P2O5 | 5.27 | 6.81 | 2.31 | 1.77 |
SO3 | 12.05 | 7.57 | 7.31 | 7.13 |
СО2 | – | 7.99 | 26.80 | – |
Элементный состав золы разных видов биомассы существенно различается. Так, в золе торфяных пеллет очень много оксида кремния (более 50%), также имеется значительное количество оксидов железа и алюминия, но мало оксидов щелочных металлов (1.47%) и карбонатов. Максимальная доля щелочных металлов в золе подсолнечника – до 37.2%, причем в пеллетах из подсолнечника из г. Тамбов заметно больше Na2O, чем в золе подсолнечника из г. Кумертау. Среди важных микроэлементов прежде всего следует отметить хлор. Его максимально много в золе подсолнечника ООО “Элеватор” (г. Кумертау) – 5335 мкг, тогда как в остальных золах – от 140 до 358 мкг.
Склонность к агломерации зачастую определяют по отношению доли щелочных металлов к содержанию оксида кремния [8]. Для указанных в таблице видов золы это соотношение имеет следующие значения:
№ 1 .............................................12.600 |
№ 2 ..............................................2.050 |
№ 3 ..............................................0.490 |
№ 4 ..............................................0.035 |
Считается, что при соотношении больше единицы агломерация крайне вероятна. Необходимо отметить, что все пробы золы обладают довольно высокими температурами плавления. Так, для золы № 1, наиболее склонной к агломерации, температура начала размягчения составляет 1280–1300°С.
Предварительные опыты для доработки методики были выполнены именно для золы № 1, наиболее склонной к агломерации. Оказалось, что эта зола без песка (так же как и песок без золы) не агломерирует даже при температуре 900°С и выдержке 1 ч. При такой температуре смеси песка и золы № 1 почти полностью спекались, причем время выдержки от 15 мин до 1 ч не играло существенной роли. Поэтому решили проводить опыты с определением влияния температуры на долю спекшихся частиц с выдержкой 1 ч.
Кроме того, не менее важен выбор концентрации золы в смеси с песком. Для этого были проведены опыты на смесях с долей золы от 5 до 50% при температуре 850–900°С. Оказалось, что для золы № 1 влияние ее доли несущественно – во всех опытах происходило почти полное спекание. Однако при низких концентрациях золы в смесях трудно обеспечить хорошее перемешивание ее с песком. Это может давать дополнительные погрешности в определении массы спекшегося материала. Поэтому было принято решение проводить опыты с концентрацией золы в смеси 5%. При пуске котла с КС в слое находится только песок, а затем в процессе работы происходит его частичная замена на золу топлива. Применительно к углям с высокой зольностью состав стабилизируется примерно через 2 сут работы [9]. Для биомассы с малой зольностью этот процесс более длительный. Содержание оксида кремния в донной золе снижается существенно, а при небольшой агломерации частиц через одну неделю работы становится равным 92.4% [7]. Это значит, что в донной золе (при содержании оксида кремния в золе биомассы 26.6%) содержится уже почти 9% золы биомассы. В слое ее несколько меньше, так как в донной золе сосредоточены наиболее крупные частицы. В результате можно заключить, что принятое значение концентрации золы в смеси с песком 5% вполне достоверно отражает реальную ситуацию для котлов с КС.
РЕЗУЛЬТАТЫ ИССЛЕДОВАНИЯ ВЛИЯНИЯ ТЕМПЕРАТУРЫ ОБРАБОТКИ И КОНЦЕНТРАЦИИ ЩЕЛОЧНЫХ ЭЛЕМЕНТОВ НА АГЛОМЕРАЦИЮ СЛОЯ
Часть результатов исследований приведена в статье [10]. Показано, что при температуре около 750°С для золы подсолнечной лузги доля агломератов уже достигает 80%. Следует отметить, что при низких температурах для всех зол имеется фоновая доля агломерированных частиц. Можно в качестве тестовой золы, совершенно не склонной к агломерации, принять золу пеллет из торфа № 4, доля агломератов составит 3–5%. По-видимому, это связано с прилипанием небольшой доли частиц к металлической сетке в процессе термической обработки. При последующем повышении температуры доля агломератов лишь немного увеличивается. Эта температура примерно соответствует температуре плавления тетра- и дисиликатов калия [11]. Таким образом, можно заключить, что при высокой концентрации калия в золе агломерация наступает уже при 750°С. Агломераты при относительно низких температурах непрочны и могут распадаться. Однако даже интенсификация массообмена в кипящем слое лишь растягивает этот процесс во времени.
Концентрацию калия и натрия в золе увеличивали путем добавления в нее раствора KCl и NaCl, затем ее сушили при комнатной температуре. Методически подход авторов подобен примененному в [3]. Опыты проводили с добавкой растворов KCl различной концентрации (от 3 до 36%) в золу № 4. Диапазон температур составил от 670 до 900°С, концентрации калия в смеси с песком – от 538 до 8450 ppm (от 0.054 до 0.845%), выдержка была одинакова – 1 ч.
На рис. 1 показано влияние температуры на образование агломератов для золы № 1, 2 и 4 с добавкой максимального количества калия и натрия. Все кривые практически совпали, что неудивительно, так как концентрация щелочных элементов в смеси очень велика и находится в узком диапазоне 1.08–1.53%.
Рис. 1.
Влияние температуры на долю возникающих агломератов для зол № 1 (1), 2 (2) и золы № 4 с добавкой максимального количества калия и натрия (3)
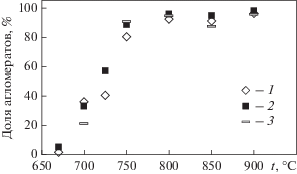
На рис. 2 приведены все точки (результаты экспериментов с добавкой как калия, так и натрия к золе № 4) в виде зависимости доли агломератов от концентрации щелочных элементов в золе. Можно предположить, что натрий очень сильно увеличивает количество агломератов при высоких температурах, но в наибольшей степени температура начала агломерации зависит от концентрации калия.
Рис. 2.
Зависимость доли агломератов от концентрации щелочных элементов в золе. Температура обработки, °С: 1 – 700; 2 – 800; 3 – 900
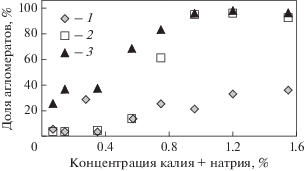
Последняя серия опытов была проведена с изменением материала слоя. Известно, что при большом содержании в слое оксидов железа и алюминия агломерация маловероятна. Температура размягчения щелочных элементов, образующихся по реакциям с этими оксидами, превышает 1100°C. Таким образом, при наличии в золе большого количества Fe2O3 щелочные компоненты прежде всего могут вступать в реакцию с Fe2O3, не образуя легкоплавких соединений. В работах [4, 12] приведены результаты опробования на экспериментальной установке и промышленном котле различных материалов слоя: корунда (Al2O3), чистого оксида железа (Fe2O3) и железной руды (39.5% Fe2O3) – при сжигании кукурузных початков. Оказалось, что критическая концентрация калия при температурах слоя 800–850°С при использовании железной руды снижается в 3 раза.
Результаты опытов с золой № 1 и долей Fe2O3 100, 50 и 0% приведены на рис. 3. Для смеси 50% песка и 50% Fe2O3 спекание частиц проявляется только при высоких температурах (850°С и более). Для реальных условий кипящего слоя доля оксидов железа безусловно ниже. Поэтому для предотвращения агломерации слоя при сжигании топлив с очень высоким содержанием оксидов натрия и калия можно применять оливиновый песок с содержанием оксида кремния около 40% или ильменит. Оливин практически инертен к газообразным соединениям калия, но взаимодействует с соединениями кальция в топливе.
АНАЛИЗ РЕЗУЛЬТАТОВ И СОПОСТАВЛЕНИЕ ИХ С ДАННЫМИ, ПОЛУЧЕННЫМИ ПРИ ПСЕВДООЖИЖЕНИИ СЛОЯ
Как было указано ранее, эксперименты проводили на неожиженном тонком слое смеси песка и золы с возможностью поступления окислителя в слой как сверху, так и снизу. Поэтому важно сопоставить результаты этих исследований с подобными опытами при ожижении. Прежде всего необходимо рассмотреть процессы агломерации. Согласно [13] существуют три варианта спекания при сжигании твердых топлив в КС:
частичное расплавление золы;
частичное плавление с образованием вязкой жидкости;
химическая реакция, в результате которой на частицах формируется пленка нового соединения.
Преобладание одного из них зависит главным образом от химического и минералогического состава золы.
При сжигании угля основные процессы – это расплавление золы и химические реакции, склеивающие частицы одну с другой. Вязкое спекание происходит в силикатных системах, особенно при использовании богатых щелочью видов топлива, таких как биомасса. Щелочные элементы золы осаждаются на материале слоя или фрагментах силиката самой золы в виде мелких частиц при конденсации щелочных соединений (KCl, KOH, K2SO4, K) или при химических реакциях на поверхности частиц с последующей гомогенизацией и укреплением внутреннего слоя покрытия, что окончательно приводит к расплавлению и усилению прилипания [14–16]. Эта поверхностная жидкая фаза обычно очень вязкая, так что она остается стекловидной, даже если температура падает ниже линии Солидуса. Вязкость вещества зависит от его химического состава и температуры, а наряду со временем определяет образование шеек между отдельными частицами.
Автор [17] выявил два основных пути реализации процесса агломерации. На первом вследствие расплавленной фазы из-за локальных пиковых температур частицы прилипают одна к другой, а их химический состав напоминает состав золы. Агломерация, вызванная покрытием (второй путь), считается более распространенной: при определенных критических условиях (например, температуре и толщине) на частицах образуется слой покрытия, а между ними – связывающие их шейки. Частичная дефлюидизация (прекращение ожижения) сопровождается возникновением локальных областей высокой температуры, при которой возможно образование расплава, и тогда агломерация продолжается уже двумя путями. В рассматриваемом случае при отсутствии ожижения наиболее вероятен первый – причиной адгезии частиц слоя является расплавленная зола (щелочные соединения), которая действует как клей, и между частицами слоя образуются жидкие мостики.
Для переноса полученных в экспериментах данных на реальные объекты и сопоставления их с опытами с псевдоожижением важно определить влияние скорости ожижения, размеров частиц и избытка воздуха на процесс агломерации. Увеличение скорости ожижения приводит к замедлению дефлюидизации, так как улучшается перемешивание и усиливается воздействие на материал слоя пузырьков, разрушающих агломераты. Согласно [18] (сжигание измельченных пеллет из соломы на лабораторной установке диаметром 68 мм) увеличение скорости воздуха в 2 раза привело к небольшому росту времени дефлюидизации (по утверждению авторов – на 30%). Однако это заметно только при температуре ниже 830°С, а при высоких температурах точки практически совпадают (рис. 4).
Рис. 4.
Влияние температуры на время дефлюидизации слоя [18]. Расход воздуха при нормальных условиях, дм3/мин: 1 – 28; 2 – 14
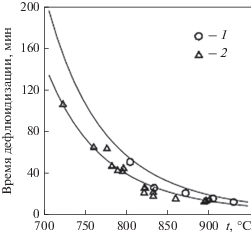
Скорости газов при указанной температуре составляли примерно 0.26 и 0.52 м/с. Расчетная скорость минимального псевдоожижения для частиц, средний диаметр которых составляет 0.275 мм, равна 0.03 м/с, а частиц размером 0.460 мм – 0.07 м/c. Это означает, что ожижение было довольно интенсивным. Увеличение размеров частиц приводит к снижению времени дефлюидизации (рис. 5). Этот факт авторы [18] объясняют как худшим перемешиванием (это не вполне точно и возможно только при наименьшей скорости газов), так и меньшей площадью поверхности, которая может быть покрыта пленкой расплавленных щелочных элементов.
Рис. 5.
Влияние крупности песка на время дефлюидизации слоя по данным [18]. Размер частиц, мм: 1 – 0.275; 2 – 0.328
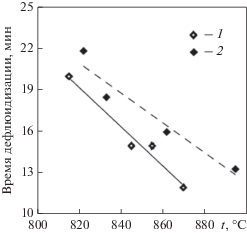
Изменение избытка воздуха в пределах 1.0–2.5 при температуре 830°С давало очень маленькое увеличение времени дефлюидизации. С одной стороны, уменьшение времени при снижении избытка воздуха может происходить из-за снижения температуры плавления при недостатке кислорода. С другой стороны, температура горящих частиц может быть ниже при малых избытках воздуха, что и должно увеличивать время дефлюидизации.
Накопление калия в слое в опытах [18] показано на рис. 6. Прямая – результат расчета по концентрации калия в золе, расходу золы и массе песка в ситуации, когда весь калий аккумулируется в слое. На начальном участке опытные значения при температурах 814–697°С не отличаются от расчетных. После 10 мин наблюдается снижение значений опытной концентрации калия по сравнению с расчетными. Это может быть связано с уносом мелких частиц золы, содержащих калий, количество которых должно увеличиваться со временем. Из рис. 6 следует, что влияние температуры горения на рост концентрации калия незначительно, по крайней мере до 900°С. Это означает, что соединения калия в соломе, как правило, остаются в слое и мало испаряются при горении в диапазоне температур от 810 до 900°С.
Рис. 6.
Накопление калия в слое cс при различных температурах по данным [18]. Температура слоя, °С: 1 – 814; 2 – 831; 3 – 832; 4 – 843; 5 – 855; 6 – 864; 7 – 897
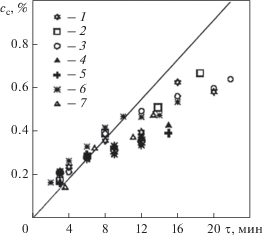
Учитывая, что размеры частиц в опытах авторов и по данным работы [18] примерно одинаковы, можно считать, что избыток воздуха не оказывает существенного влияния на агломерацию, важна только скорость ожижения. Очевидно, что при неподвижном слое критическая концентрация калия и начальная температура процесса будут ниже, значит результаты экспериментов, проведенных авторами, должны давать их минимальные значения. Так как наиболее важный фактор процесса агломерации частиц – это концентрация калия в слое, то на рис. 7 приведена зависимость от нее доли агломератов при различных температурах обработки. Исходя из этой зависимости, можно определить, при какой предельной концентрации калия происходит агломерация неподвижного слоя частиц.
Рис. 7.
Зависимость доли агломератов от концентрации калия при различных температурах слоя. Температура, °С: 1 – 700; 2 – 800; 3 – 900; 4 – 750; 5 – 850
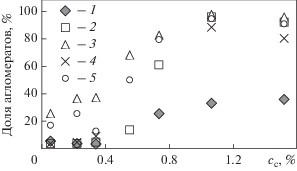
Для сравнения полученных значений с результатами исследований при псевдоожижении была выполнена обработка данных [18], приведенных на рис. 4 и 6. Зная размеры установки, массу песка, расход биомассы и содержание в ней калия, можно вычислить значения его предельных концентраций для различных температур слоя. Это было сделано как для условий расчетного накопления частиц, так и с учетом снижения концентраций калия в соответствии с рис. 6. На рис. 8 для сопоставления приведены значения, полученные в настоящем исследовании и обработанные в двух этих вариантах [18], а также результаты работ [4, 12].
Показания [4, 12], полученные на небольшом котле с кипящим слоем при высоких скоростях ожижения, находятся вблизи опытных данных [18] [между пересчетом по балансу (см. рис. 6) и значениями с учетом снижения концентрации калия в слое] при относительно низких скоростях ожижения. Результаты авторов настоящего исследования дают наименьшие значения критических концентраций, особенно при относительно низких температурах слоя – менее 800°С. Вместе с тем необходимо отметить, что в работах [4, 12, 18] критические концентрации соответствует прекращению псевдоожижения, а не началу агломерации слоя.
В указанных работах, особенно в [18], прекращение псевдоожижения происходило довольно быстро – в течение нескольких десятков минут, как и накопление калия в слое. Это связано с малым размером установки, в которой отношение массы частиц песка к расходу поступающей биомассы (а соответственно, и калия) было невелико. Поэтому интерес представляет изучение изменения концентрации калия в слое во времени для реальных объектов. Эта задача важна для практического использования одного из методов борьбы с агломерацией слоя – дренажа материала слоя с добавкой отсеянного материала или свежего песка.
РАСЧЕТНАЯ ОЦЕНКА ИЗМЕНЕНИЯ КОНЦЕНТРАЦИИ КАЛИЯ В СЛОЕ. РАСХОД ДРЕНАЖА СЛОЯ И СОВМЕСТНОЕ СЖИГАНИЕ БИОМАССЫ С УГЛЕМ
Впервые попытка оценить требуемый расход дренажа слоя была сделана в [7], для чего были записаны уравнения материального баланса и баланса соединений натрия и калия. Такой подход аналогичен расчетам баланса солей в барабане котла с естественной циркуляцией. Следует напомнить, что для поддержания требуемого качества пара и котловой воды необходима непрерывная и периодическая продувка воды из барабана котла. Непрерывная продувка обычно составляет 0.5–1% расхода пара, а периодическая может достигать 5%.
Изменение фракционного состава материала слоя в процессе работы также определяется по балансовым уравнениям [9]. Применительно к условиям эксплуатации котла с циркулирующим кипящим слоем Новочеркасской ГРЭС были сделаны подробные расчетные оценки изменения фракционного состава с учетом добавки известняка и золы рециркуляции в процессе работы. Их результаты были представлены в ключевом докладе на 9-м Международном симпозиуме по сжиганию угля, состоявшемся в г. Квиндао, Китай, в 2019 г.11
Уравнение изменения концентрации калия в слое может быть записано следующим образом:
(1)
$\begin{gathered} M\frac{{{\text{d}}{{c}_{{\text{с}}}}}}{{{\text{d}}\tau }} = {{G}_{{\text{з}}}}{{c}_{{\text{з}}}}{{a}_{{{\text{ун}}{\text{.з}}}}}{{G}_{{\text{з}}}}{{c}_{{{\text{ун}}}}} - \left( {1 - {{a}_{{{\text{ун}}{\text{.з}}}}}} \right){{G}_{{\text{з}}}}{{c}_{{{\text{др}}}}} - \\ - \,\,{{G}_{{{\text{ун}}}}}{{c}_{{{\text{п}}{\text{.с}}}}} + {{G}_{{\text{п}}}}{{c}_{{\text{п}}}}, \\ \end{gathered} $Расход поступающей золы равен
где Вр – расчетный расход топлива, кг/с; Ар – зольность топлива на рабочую массу (в долях).Масса слоя определяется сечением слоя Fc, м2, его высотой hc, м, и насыпной плотностью песка ρн, кг/м3:
Сечение слоя выбирается исходя из заданной скорости газов в слое Uc, м/с. Формулу для его расчета можно записать так:
(4)
${{F}_{{\text{с}}}} = \frac{{{{B}_{{\text{р}}}}{\kern 1pt} {{{\beta }}_{{\text{с}}}}{{V}_{{\text{г}}}}}}{{{{U}_{{\text{с}}}}}}\frac{{273 + {{t}_{{\text{с}}}}}}{{273}},$Отношение K массы слоя к расходу поступающей золы зависит от свойств топлива и скорости газов в слое, расход же топлива сокращается следующим образом:
(5)
$\frac{M}{{{{B}_{{\text{р}}}}{{A}_{{\text{р}}}}}} = K = \frac{{{{h}_{{\text{с}}}}{{B}_{{\text{р}}}}{\kern 1pt} {{{\beta }}_{{\text{с}}}}{{V}_{{\text{г}}}}}}{{{{B}_{{\text{р}}}}{\kern 1pt} {{A}_{{\text{р}}}}{\kern 1pt} {{U}_{{\text{с}}}}}}\frac{{273 + {{t}_{{\text{с}}}}}}{{273}}.$Оказалось, что для реальных аппаратов с кипящим слоем отношение меняется в довольно узких пределах 60–110 ч–1. Согласно данным [19] доля уноса составляет 0.95, из них 0.07 приходится на песок (доля уноса золы топлива – 0.88). В этих условиях можно принять, что cп = 0, а сдр = cс. Тогда уравнение (1) упрощается и может быть записано следующим образом:
(6)
$K\frac{{\Delta {{c}_{{\text{с}}}}}}{{\Delta {\tau }}} = 0.12{{c}_{{\text{з}}}} - {{c}_{{\text{с}}}}\left( {0.07 + {{a}_{{{\text{др}}}}}} \right),$Расчеты выполнены для двух видов биомассы – кородревесных отходов (КДО) целлюлозно-бумажного комбината (ЦБК) (содержание калия в золе около 10% [7]) и подсолнечной лузги с характеристиками, приведенными в таблице. На рис. 9 показано изменение концентрации калия во времени при сжигании лузги без дополнительного дренажа слоя. Наибольшие значения (кривая 1) относятся к расчету при изменении концентрации калия по балансу его поступления. Если учитывать, что концентрация в слое снижается в соответствии с [18] (в расчет введен понижающий коэффициент, полученный по опытным данным [18] и зависящий от времени процесса), то концентрация калия становится минимальной. В [18] указывается, что снижение концентрации калия происходит в основном вследствие истирания и уноса мелких частиц, а также потери его в газовой фазе. Унос уже в основном учтен в формулах (1)–(6), поэтому достаточно было учесть экспериментально установленную долю перехода калия в газовую фазу (кривая 3). В связи с качественной оценкой сравнительных характеристик режимных параметров роста концентрации калия в слое такой упрощенный подход вполне целесообразен.
На рис. 10 показано влияние доли дренажа на рост концентрации калия в слое во времени при сжигании КДО (температура слоя 800°С).
Рис. 10.
Влияние доли дренажа на рост концентрации калия в слое во времени при сжигании КДО. Температура слоя 800°С. Доля дренажа, %: 1 – 0; 2 – 0.5; 3 – 1
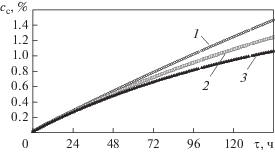
Критические концентрации для условий ожиженного слоя достигаются только спустя 5 сут работы. При этом увеличение расхода дренажа до 1% расхода топлива снижает концентрацию калия в слое на 40%. Для сжигания лузги требуется значительно больший дренаж слоя – 5%, что уже превышает весь расход поступающей с топливом золы (рис. 11).
Рис. 11.
Влияние доли дренажа на рост концентрации калия в слое во времени при сжигании лузги. Температура слоя 800°С, дренаж начинали с достижения концентрации калия 0.6%. Доля дренажа, %: 1 – 1; 2 – 5
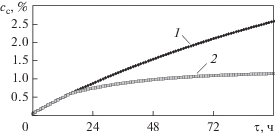
Еще одна серия расчетов была выполнена для условий повышенного отвода агломератов из слоя с дренажом. Считалось, что после достижения критической концентрации и начала образования агломератов с дренажом отводится не только материал слоя, но и агломераты с такой же концентрацией калия, как и в поступающей золе. Доля этих частиц оценивалась по данным авторов об изменении доли агломератов в зависимости от температуры слоя и концентрации калия. Если вывод агломератов с дренажом учитывается (кривая 1 на рис. 12), то при расчетах концентрация калия в слое быстро стабилизируется, в отличие от расчетов, выполненных без учета этого фактора (кривая 3 на рис. 12).
Рис. 12.
Сравнение данных по лузге при учете агломерации с дренажом (1) и без него (2) и данных с максимальным дренажом без учета дренажа агломератов (3)
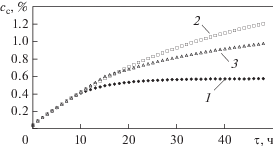
Результаты расчетов изменения концентрации калия в слое при совместном сжигании подсолнечной лузги (50% по теплу) и антрацитового штыба (АШ) (50%) приведены на рис. 13. Но даже при таком сжигании существенного изменения роста концентрации калия в слое не происходит (кривые 1 и 2), если не учитывать возможной реакции с оксидами железа, которые появляются при полной или частичной замене песка железной рудой. Этот учет выполнялся исходя из данных статьи [12], в которой показано, что в слое из железной руды с концентрацией 39% (по массе) Fe2O3 критическая концентрация калия увеличивается примерно в 3 раза. В опытах авторов данной статьи она также увеличивалась примерно в 3 раза: при 50% (по массе) Fe2O3 в слое критическая концентрация возрастала до 1.6% в слое песка при температуре 850°С. Это значит, что около 2/3 калия вступает в реакцию с оксидами железа, но эвтектики при этом получаются не легкоплавкие, поэтому агломераты не образуются. Соответственно, условная концентрация калия в слое, приводящая к агломерации, пропорционально снижается. При такой упрощенной оценке получается, что совместное сжигание АШ и лузги подсолнечника не приводит к агломерации слоя.
ВЫВОДЫ
1. Исследования влияния температуры слоя и концентрации щелочных элементов в нем на массовую долю образующихся агломератов для четырех видов биомассы, выполненные по разработанной авторами методике, показали, что температура начала агломерации в наибольшей степени зависит от концентрации калия. При высокой концентрации калия в золе агломерация наступает уже при 750°С. Агломераты при относительно низких температурах весьма непрочные и могут распадаться.
2. При замене песка, используемого в качестве материала слоя, на оксиды железа и их смесь с песком агломерация проявляется только при высоких температурах (850°С и более), а критическая концентрация калия в слое увеличивается в 3 раза и более.
3. При отсутствии ожижения наиболее вероятен тот вариант процесса агломерации, когда адгезия частиц слоя происходит благодаря расплавленной золе (щелочным соединениям), которая действует как клей, и между частицами слоя образуются жидкие мостики. В опытах с неподвижным слоем получены наименьшие значения критических концентраций, особенно при относительно низких температурах слоя – менее 800°С.
4. Применение разработанной методики расчета для двух видов биомассы показало, что для кородревесных отходов ЦБК (содержание калия в золе около 10%) увеличение расхода дренажа до 1% расхода топлива снижает концентрацию калия в слое на 40%. Для сжигания подсолнечной лузги (содержание калия в золе около 30.3%) требуется значительно больший дренаж слоя – 5%, что превышает количество поступающей с топливом золы.
5. Результаты расчетов изменения концентрации калия в слое при совместном сжигании подсолнечной лузги и антрацитового штыба в соотношении 50/50% по теплу показали, что агломерация резко снижается из-за большого содержания оксидов железа в золе АШ.
Список литературы
Scala F. Particle agglomeration in fluidized beds: mechanisms, early detection and possible countermeasures // Proc. of 12th Intern. Conf. on Fluidized Bed Technology. Krakow, Poland, 23–26 May 2017. P. 65–76.
Рябов Г.А., Литун Д.С. Агломерация при сжигании и газификации топлив в кипящем слое // Теплоэнергетика. 2019. № 9. С. 42–59. https://doi.org/10.1134/S0040363619090042
Yrjas P., Sevonius C., Hupa M. Bed agglomeration due to addition of KCl and K2CO3 – first results from a laboratory fluidized bed reactor // Proc. of 21st Intern. Conf. on Fluidized Bed Combustion. Naples, Italy, 3‒6 June 2013. P. 203–210.
Biomass FBC combustion – bed agglomeration problems / B.G. Grubor, S.N. Oka, M.S. Ilic, D. Dakic, B. Grubor // Proc. of 13th Conf. on Fluidized Bed Combustion. Florida, Orlando, USA, 7–10 May 1995. V. 1. P. 515–522.
Mettanant V., Basu P., Butler J. Agglomeration of biomass fired fluidized bed gasifier and combustor // Canad. J. Chem. Eng. 2009. V. 87. P. 656–684.
Niy Y., Tan H., Hui S. Ash-related issues during biomass combustion: Alkali-induced slagging and related countermeasures // Prog. Energy Combust. Sci. 2016. V. 52. P. 1–61. https://doi.org/10.1016/j.pecs.2015.09.003
Ryabov G.A., Litoun D.S., Dik E.P. Agglomeration of bed material: influence on efficiency of biofuel fluidized bed boiler // Therm. Sci. 2003. V. 7. Is. 1. P. 5–16. https://doi.org/10.2298/TSCI0301005R
Basu P. Combustion and gasification in fluidized beds. Taylor & Francis Group, LLC, 2006. https://doi.org/10.1201/9781420005158
The dynamic balance of bed material size distribution in start-up process for circulating fluidized bed boiler / Su-Xia Ma, Jun Guo, Wei-Ming Chang, Guang-Xi Yue, Hai Zhang // Proc. of Intern. Conf. FBC22. Turku, Finland, 2015. P. 788–796.
Особенности структуры и химического состава биомассы и агломерированных частиц при пиролизе и сжигании / Г.А. Рябов, Д.С. Литун, О.М. Фоломеев, Е.А. Шорина, О.А. Смирнова // Машиностроение: сетевой электрон. науч. журн. 2019. Т. 7. № 4. С. 9–14. https://doi.org/10.24892/RIJIE/20190402
Горшков В.С., Савельев В.Г., Федоров Н.Ф. Физическая химия силикатов и других тугоплавких соединений: учеб. для вузов. М.: Высшая школа, 1988.
Grubor B., Ilec M., Dakic D. Hematite – a definite solution for FB combustion of biomass // Proc. of Intern. Conf. on Heat and Mass Transfer. MIF-96. Minsk, 20–24 May 1996. P. 227–234.
Sintering mechanisms of FBC ashes / B.J. Skrifvars, M. Hupa, R. Backman, M. Hiltunen // Fuel. 1994. V. 73. Is. 2. P. 171–176. https://doi.org/10.1016/0016-2361(94)90110-4
Bed agglomeration characteristics during fluidized bed combustion of biomass fuels / M. Öhman, A. Nordin, B.-J. Skrifvars, R. Backman, M. Hupa // Energy Fuels. 2000. V. 14. Is. 1. P. 169–178. https://doi.org/10.1021/ef990107b
Drift A. van der, Olsen A. Conversion of biomass, prediction and solution methods for ash agglomeration and related problems, final report. ECN Biomass, 1999.
The behavior of inorganic material in biomass-fired power boilers: field and laboratory experiences / L.L. Baxter, T.R. Miles, T.R. Miles, Jr., B.M. Jenkins, T. Milne, D. Dayton, R.W. Bryers, L.L. Oden // Fuel Process. Technol. 1998. V. 54. Is. 1–3. P. 47–78. https://doi.org/10.1016/S0378-3820(97)00060-X
Visser H.J.M. The influence of fuel composition on agglomeration behavior in fluidized-bed combustion: Report on the project “Influence of fuel composition on agglomeration behavior in fluidized-bed combustion/gasification of biomass” (ECN-C-04-054). Project 2020-01-12-14-006. Novel subsidy programme. Renewable Energy in the Netherlands, Sept. 2004.
Lin W., Dam-Johansen K., Frandsen F. Agglomeration in bio-fuel fired fluidized bed combustors // Chem. Eng. J. 2003. V. 96. Is. 1–3. P. 171–185. [Amsterdam, Netherlands.] https://doi.org/10.1016/j.cej.2003.08.008
Литун Д.С., Рябов Г.А. Расчет уноса золы и потерь тепла с механическим недожогом в кипящем слое при сжигании биомассы // Изв. РАН. Энергетика. 2015. № 5. С. 90–102.
Дополнительные материалы отсутствуют.
Инструменты
Теплоэнергетика