Теплоэнергетика, 2021, № 1, стр. 3-20
Современные технологии термической переработки твердых коммунальных отходов и перспективы их реализации в России (обзор)
А. Н. Тугов *
ОАО “Всероссийский теплотехнический институт”
115280 Москва, Автозаводская ул., д. 14, Россия
* E-mail: ANTugov@vti.ru
Поступила в редакцию 28.04.2020
После доработки 06.05.2020
Принята к публикации 20.05.2020
Аннотация
Приводятся данные по состоянию термической переработки твердых коммунальных отходов (ТКО) в США, Китае, европейских и других странах. Выполнен анализ технологий сжигания ТКО в слоевых топках на колосниковых решетках и в кипящем слое, а также с использованием газификации и пиролиза. Показано, что наилучшей технологией для энергетической утилизации ТКО является их сжигание в слоевых топках на механических переталкивающих колосниковых решетках. Отмечается, что, поскольку все предприятия для энергетической утилизации ТКО (по сути это ТЭС, основным топливом которых являются твердые коммунальные отходы) в настоящее время оснащены многоступенчатой газоочисткой, проблемы их экологически безопасной эксплуатации полностью решены. Поэтому исследования направлены главным образом на повышение энергоэффективности этих предприятий, в том числе путем интеграции установок для сжигания ТКО в тепловую схему ТЭС, работающей на органическом топливе. Приводятся примеры зарубежных действующих установок для энергетической утилизации ТКО с электрическим КПД 27–31%, а также работающих в теплофикационным цикле с высокой энергоэффективностью. Показаны современное состояние термической переработки и перспективы реализации современных технологий энергетической утилизации ТКО в России. Несмотря на то что наша страна не имеет достаточного опыта в этой области (за все время построены только три завода в Москве, установленная электрическая мощность которых не превышает 12 МВт), в настоящее время в Московской обл. предусматривается строительство четырех относительно крупных ТЭС электрической мощностью 70 МВт каждая, на которых предполагается сжигать 700 тыс. т ТКО в год. Наиболее перспективной для России представляется ТЭС для энергетической утилизации 360 тыс. т ТКО в год установленной электрической мощностью 24 МВт, которая уже в настоящее время потенциально может быть востребована более чем в двух десятках крупных городов России.
Объем твердых коммунальных отходов в мире растет. Если в 2016 г. в Европе количество отходов составило 392 млн т, то к 2030 г. их количество увеличится на 12% и достигнет 441 млн т/год, а к 2050 г. составит 490 млн т/год [1]. В странах Азии и Африки темпы образования отходов еще больше – к 2030 г. прогнозируется увеличение их объемов на 30–40%.
Во всем мире наблюдается тенденция сокращения полигонного захоронения ТКО, чтобы планета не превратилась в свалку. Основы в области обращения с отходами в странах Европейского союза обозначены в Стратегии Европейского сообщества в области управления отходами, впервые опубликованной в 1989 г. в коммюнике Комиссии ЕС и позднее пересмотренной и подтвержденной решением Совета от 24.02.1998, и законодательно закреплены в Рамочной директиве 2008/98/ЕС “Об отходах” [2]. В соответствии с положениями этих правовых актов определены базовые принципы европейской политики в области обращения с отходами, в том числе иерархия приоритетов, где в качестве предпочтительного варианта рассматривается предотвращение образования отходов, а в качестве наименее благоприятного варианта – размещение отходов на полигонах (захоронение) и сжигание их без получения энергии.
Иерархия приоритетов реализована в так называемой циркулярной экономике (экономике замкнутого типа), главные принципы которой основаны на возобновлении ресурсов, переработке вторичного сырья, переходе от ископаемого топлива к использованию возобновляемых источников энергии [3]. Специалисты организации CEWEP (Confederation of European Waste-to-Energy Plant) провели исследование, в результате которого было установлено, что при практической реализации такой экономики все равно около 30% ТКО необходимо будет утилизировать термическим способом [4]. Дело в том, что некоторые отходы не подлежат вторичной переработке: использованные гигиенические и медицинские средства, различные пластики, композитная упаковка, загрязненная бумага и полиэтиленовая пленка, бумага, полимеры низкого качества, уже прошедшие несколько стадий рециклинга, мелкие фракции отходов. Переработка подобных отходов в энергию является единственно возможным способом их безопасной утилизации. Таким образом, энергетическая утилизация ТКО, т.е. термическая переработка отходов с выработкой электрической и тепловой энергии, является полноценным участником циркулярной экономики и будет в любом случае основным и завершающим этапом на пути комплексного решения проблемы санитарной очистки населенных пунктов от отходов. Она не только позволяет утилизировать непригодные к повторному использованию отходы, но и заменяет природные ресурсы, добываемые для получения энергии, сокращает захоронение отходов и уменьшает выбросы парниковых газов.
Предприятия для переработки отходов в энергию по существу являются тепловыми электростанциями, на которых основным топливом служат ТКО (ТЭС на ТКО), за рубежом – Waste-to-Energy Plant (WTE) или Energy-from-Waste (EfW). Благодаря интенсивному строительству в Европе новых и модернизации существующих WTE в 90-х годах прошлого века и в начале этого века таким странам, как Швеция, Дания, Нидерланды, Германия, Бельгия, Австрия, Швейцария и Норвегия, удалось достигнуть главной цели комплексной системы обращения с отходами – практически полного отказа от полигонного захоронения [5]. Стремясь к достижению “нулевого захоронения”, другие европейские страны продолжают увеличивать переработку отходов как во вторичные материалы, так и в энергию. Уже в 2017 г. более чем в половине стран Европы доля отходов, вывозимых на полигоны, не превышала 50% их общего количества.
СОСТОЯНИЕ ТЕРМИЧЕСКОЙ ПЕРЕРАБОТКИ ТКО В МИРЕ
В последнее время устойчиво прослеживается тенденция увеличения количества отходов, утилизируемых термическим способом, особенно в крупных городах. По данным фирмы Ecoprog GmbH, сейчас в мире эксплуатируется примерно 2450 предприятий по термической переработке ТКО общей производительностью 368 млн т/год [6], в том числе более 1700 предприятий по переработке отходов в энергию [3]. Только в период с 2016 г. до середины 2019 г. в эксплуатацию был введен 161 завод WTE суммарной мощностью 60 млн т/год. Прогнозируется, что к 2028 г. количество предприятий по термической переработке ТКО составит около 2700 общей мощностью более 530 млн т/год [6].
В Европе, по данным CEWEP, за 5 лет (с 2012 по 2017 г.) объем ТКО, перерабатываемых термическим способом, увеличился более чем на 20%. В 2017 г. в 22 европейских странах эксплуатировались 492 предприятия по термической переработке ТКО, на которых ежегодно сжигались почти 96 млн т ТКО [7]. Лидером по термической переработке отходов в Европе является Финляндия, отправляющая на энергетическую утилизацию 57% всех ТКО, хотя еще в начале 2000-х годов в этой стране сжигание ТКО считалось неприемлемым. В настоящее время в Финляндии успешно эксплуатируются девять заводов суммарной производительностью 1.61 млн т/год, и страна практически полностью отказалась от полигонного захоронения.
В Великобритании за шесть лет (с 2013 по 2019 г.) количество заводов увеличилось почти в 2 раза (с 26 до 48). Планируется построить еще шесть предприятий, часть из них уже находятся в стадии строительства [8]. Интересно отметить, что доля отходов, направляемых на вторичную переработку в этой стране, начиная с 2012 г. и по настоящее время стабилизировалась на уровне 43–45%, в то время как доля термически перерабатываемых ТКО за шесть лет (с 2012 по 2017 г.) увеличилась более чем вдвое [1].
Польша в настоящее время является одной из динамично развивающихся стран в области энергетической утилизации ТКО. Если до конца 2015 г. отходы практически не перерабатывали термическим способом (имелась лишь небольшая установка в Варшаве, на которой ежегодно сжигали не более 70 тыс. т), то к концу 2017 г. было запущено в эксплуатацию шесть новых заводов суммарной производительностью более 970 тыс. т/год.
Ведется строительство новых ТЭС на ТКО и в бывших республиках СССР. В Эстонии в 2013 г. на ТЭС “Иру”, входящей в состав энергетического концерна Eesti Energia, было завершено строительство энергоблока для сжигания ТКО с комбинированной выработкой тепловой и электрической энергии (тепловая мощность 50 МВт, электрическая – 17 МВт). После ввода его в эксплуатацию более половины образующихся в Эстонии ТКО термически утилизируются. В 2015 г. в результате сжигания 245 тыс. т смешанных коммунальных отходов было отпущено в городские сети более 270 ГВт · ч тепловой энергии (15% потребности г. Таллинн) и примерно 130 ГВт · ч электрической энергии [9]. В 2013 г. в г. Клайпеда (Литва) была пущена в эксплуатацию ТЭЦ установленной электрической мощностью 20 МВт с комбинированной выработкой тепла и электроэнергии, позволяющая перерабатывать термически до 250 тыс. т отходов в год. Тепловая мощность ТЭЦ составляет 50 МВт, а с учетом конденсации водяных паров в зимнее время – до 65 МВт. В начале 2020 г. состоялся пуск второго завода в г. Каунас (Литва). В конце 2012 г. в г. Баку (Азербайджан) был введен в эксплуатацию завод по термической утилизации 500 тыс. т ТКО в год установленной электрической мощностью около 30 МВт.
В США ежегодно сжигается около 30 млн т ТКО с производством более 17 ТВт · ч электроэнергии. Следует отметить, что наибольшее развитие метод термической переработки отходов в США получил в 80–90-е годы прошлого века. Так, если в 1980 г. сжигали только 2.7 млн т ТКО в год (1.8% общего объема образующихся коммунальных отходов), то в начале 90-х годов в США действовало уже свыше 160 заводов по термической переработке ТКО, а количество сжигаемых на них отходов увеличилось на порядок и составило 29.7 млн т/год (около 14.3% ТКО, образующихся в стране). В последующие годы в основном в силу ужесточения экологических требований произошла некоторая трансформация в области термической переработки отходов: при сохранении общего объема сжигаемых отходов на прежнем уровне (примерно 29 млн т/год) количество предприятий для сжигания ТКО сократилось с 168 до 77 [10]. Но при этом единичная мощность существующих заводов значительно повысилась, причем все действующие предприятия эксплуатируются с отпуском электроэнергии потребителю. Их общая установленная электрическая мощность составляет примерно 2.7 ГВт. Благодаря выполненной на этих заводах модернизации, в первую очередь систем газоочистки, уровень выбросов вредных веществ от предприятий по сжиганию ТКО уже в 2002 г. в масштабах всей страны по сравнению с 1990 г. существенно сократился: по диоксидам на 99%, по ртути более чем на 95%, по тяжелым металлам (свинцу, кадмию), хлористому водороду и твердым частицам более чем на 90%. Агентство по охране окружающей среды США отметило, что после проведенной реконструкции этих предприятий выработка энергии из отходов оказывает меньшее негативное воздействие на окружающую среду по сравнению с другими способами производства электроэнергии [11].
В Японии с 2010 г. количество образующихся ежегодно отходов стабилизировалось и составляет примерно 41–42 млн т/год [3]. Около 78% всех ТКО перерабатывается термически, причем 70% из них используются для выработки энергии [12]. Всего в Японии в настоящее время действуют примерно 1100 предприятий по термической переработке отходов. По данным [13] на конец 2013 г. на территории Японии общее количество заводов составляло 1172, в том числе 328 предприятий, на которых ТКО утилизировали с выработкой электроэнергии, общей установленной мощностью 1770 МВт [13]. Основной тенденцией в области термической переработки ТКО в Японии является сокращение количества заводов малой мощности, особенно без утилизации энергии, и замещение их установками WTE с сохранением общего количества термически перерабатываемых отходов, что ведет к увеличению суммарной электрической мощности предприятий WTE.
Китай также стремится минимизировать захоронение ТКО за счет строительства предприятий по их переработке в энергию (ТЭС на ТКО). Так, если в 2007 г. в Китае эксплуатировалось 55 заводов общей производительностью около 16 млн т/год, то в 2010 г. их суммарная мощность достигла 24 млн т/год [14]. С 2011 по 2015 г. было построено еще 150 ТЭС на ТКО общей мощностью 50 млн т/год [15]. К концу 2016 г. в Китае действовало 273 предприятия WTE общей установленной мощностью 5.43 МВт, а на начало 2019 г. – 339 предприятий общей мощностью 7.3 МВт, на которых сжигалось около 100 млн т ТКО в год. Причем 113 из них были построены в 2016–2018 г. [1]. В 2020 г. в Китае термически утилизировалось до 50% всех образующихся ТКО. По прогнозам Международного энергетического агентства к 2023 г. установленная мощность китайских предприятий по энергетической утилизации отходов может достигнуть 13 ГВт, а к 2025 г. заводы WTE смогут перерабатывать 260 млн т ТКО в год [16]. Динамика роста строительства заводов WTE и общего количества ТКО, перерабатываемых в Китае термическим способом, показана на рис. 1.
В 2020 г. в Китае введена в эксплуатацию самая большая в мире ТЭС на ТКО Shenzhen East Waste-to-Energy Plant мощностью 165 МВт и производительностью 5500 т/сут. Расположенная в Шэньчжэне эта ТЭС позволяет перерабатывать примерно треть отходов, образующихся в двадцатимиллионном городе [3, 17]. ТЭС располагается в огромном круглом здании, крыша которого имеет площадь 66 тыс. м2. Две трети крыши покрыты фотоэлектрическими панелями, что позволяет обеспечить предприятие дополнительным источником энергии.
В Южной Корее в 2013 г. находилось в эксплуатации 198 предприятий для термической переработки ТКО общей производительностью 6.1 млн т/год. В среднем мощность каждого завода была невелика и составляла примерно 30 тыс. т/год. Активное строительство заводов в этой стране велось в 2000-е годы (до 19 установок в год суммарной мощностью до 450 тыс. т/год). Начиная с 2010 г. ежегодный ввод новых установок снизился до 10–11, но при этом их производительность возросла. В основном это заводы WTE. Следует отметить, что с вводом в эксплуатацию новых предприятий старые закрывались: за период с начала 2009 г. до начала 2013 г. было запущено в эксплуатацию около 50 новых предприятий и в то же время закрыто около 45 старых. В настоящее время в Корее эксплуатируются 35 заводов WTE, на которых перерабатывается около 5.0 млн т ТКО в год [3].
Заводы WTE планируются или находятся в стадии строительства и в других странах Азиатско-Тихоокеанского региона, в том числе в Таиланде, Индонезии, Мьянме, Малайзии, на Филиппинах [3, 18]. В 2018 г. был построен первый завод во Вьетнаме. Один из крупнейших заводов по термической переработке ТКО производительностью 4300 т/сут был пущен в эксплуатацию в Сингапуре в 2000 г. [18]. В 2019 г. в этом островном государстве был введен в эксплуатацию еще один завод по выработке энергии из отходов – шестой по счету. Мощность завода составляет 1.3 млн т/год [1]. В Нью-Дели (Индия) в 2017 г. был введен в эксплуатацию крупнейший в стране завод WTE (24 МВт). К 2027 г. в Индии планируется построить предприятия по термической переработке ТКО общей мощностью около 1.5 млн т/год [16]. В Тегеране (Иран) в феврале 2015 г. был открыт завод по сжиганию ТКО мощностью 64 тыс. т/год. Один из двух проектов в Шардже (ОАЭ) был сдан в эксплуатацию в 2018 г. [6]. Второй, крупнейший в мире завод, наряду с китайским в Шэньчжэне, производительностью 5500 т/год и мощностью 185 МВт по данным [3] планировалось запустить в Дубае в 2020 г. В Катаре в 2011 г. был введен в эксплуатацию завод производительностью примерно 500 тыс. т/год (1500 т/сут) электрической мощностью 40 МВт. Другие страны Ближнего Востока: Кувейт и Бахрейн – также рассматривают возможности строительства заводов WTE. Предприятия WTE мощностью 1.0 млн т/год строятся в Турции, мощностью 1.6 млн т/год – в Мексике [1]. Шесть объектов по выработке энергии из отходов планируется запустить к 2027 г. в Австралии [6]. Первая в Африке установка для сжигания мусора уже введена в эксплуатацию в Аддис-Абебе (Эфиопия) [19].
ОСНОВНЫЕ МЕТОДЫ ТЕРМИЧЕСКОЙ ПЕРЕРАБОТКИ ТВЕРДЫХ КОММУНАЛЬНЫХ ОТХОДОВ
Апробированными методами термической переработки ТКО являются слоевое сжигание на механических колосниковых решетках и в кипящем слое, а также с использованием пиролиза и газификации. Другие методы (сжигание во вращающихся барабанных и металлургических печах, плазменная переработка) находят ограниченное применение, как правило, на установках небольшой мощности. Большинство предприятий по термической переработке ТКО применяют технологию сжигания на колосниковой решетке, примерно 8% предприятий сжигают отходы в кипящем слое. Доля заводов, где используют газификацию или пиролиз ТКО, составляет менее 5% (в основном в Японии). В справочнике по наилучшим доступным технологиям [20] определено, что сжигание на колосниковых решетках и в топках с кипящим слоем – основные и приоритетные методы термической переработки ТКО. Доминирующая роль этих технологий определяется тем, что именно они наиболее приспособлены для энергетической утилизации ТКО.
Слоевое сжигание на колосниковых решетках. Мировыми лидерами в области создания и поставки оборудования для сжигания ТКО на колосниковых решетках являются фирмы Martin GmbH, Hitachi Zosen Inova (HZI), Babcock&Wilcox Volund A/S, Doosan Lentjes и Fisia Babcock Environment GmbH (более 75% общего количества).
Фирма Martin GmbH в настоящее время поставляет решетки четырех типов: классическую обратно-переталкивающую (ОПР), усовершенствованную ОПР – Vario®, ОПР конструкции Alstom под маркой SITY 2000 и переталкивающую колосниковую решетку (ПКР) горизонтального типа конструкции Widmer + Ernst.
Топочное устройство с классической ОПР показано на рис. 2. В конце 2020 г. на разные предприятия было поставлено более 615 решеток данного типа.
Рис. 2.
Топочное устройство (а) с обратно-переталкивающей решеткой (б) фирмы Martin. 1 – загрузочная воронка; 2 – питатель; 3 – ОПР; 4 – шлаковыгружатель; 5 – топочное устройство; 6 – паровой воздухоподогреватель; 7, 8 – первичный и вторичный воздух; 9, 10 – подвижная и неподвижная ступень колосников; 11 – подвижная рама; 12 – гидроцилиндр; 13 – скользящая опора
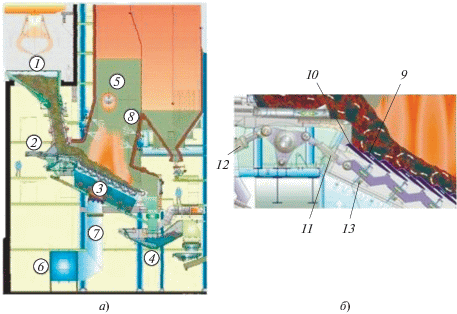
Решетка Vario® была специально разработана для топлив с высокой теплотой сгорания и низким содержанием инертного вещества (например, после предварительной обработки ТКО) и является модернизированной конструкцией классической ОПР фирмы Martin. Решетка разделена по длине на три секции, каждая из которых имеет индивидуальный привод. Это позволяет регулировать скорость подачи отходов по зонам и, в зависимости от их характеристик, контролировать процесс горения. Головной образец решетки успешно работает на заводе Pozzilli (Италия) с 2007 г. В конце 2020 г. были поставлены 19 комплектов решеток данного типа.
Обратно-переталкивающая решетка SITY 2000 отличается от предыдущих углом наклона полотна решетки – он был уменьшен с 26° до 24° и количеством независимо регулируемых секций. Всего в конце 2020 г. было поставлено более 195 комплектов решеток данного типа. Особый интерес к таким решеткам проявляет Китай – бо́льшая часть изготовленных к настоящему времени ОПР (83%) поставлена на заводы WTE этой страны.
Горизонтальная решетка фирмы Martin (конструкция Widmer+Ernst) представляет собой встречно-переталкивающую решетку, в которой подвижные ряды колосников, перемещающиеся в противоположных направлениях, разделены рядом неподвижных колосников (рис. 3). Такие ПКР обеспечивают хорошую шуровку и перемещение отходов даже при их горизонтальном положении. Обычно решетка состоит из трех последовательно расположенных по ее длине модулей и от одного до трех модулей по ее ширине. В период с 1980 по 2008 г. были изготовлены и запущены в эксплуатацию 114 комплектов решеток горизонтального типа.
Рис. 3.
Горизонтальная переталкивающая колосниковая решетка ПКР конструкции Widmer + Ernst (поставки фирмы Martin) (а) и ряды колосников (б)
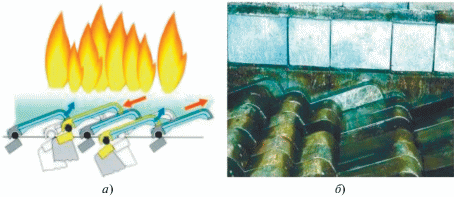
Всего на конец 2020 г. поставлены более 940 решеток фирмы Martin. До 1980 г. были введены в эксплуатацию 126 ОПР классического типа. Динамика ввода в эксплуатацию решеток различных типов (nреш – количество решеток) по годам, начиная с 1980 г., показана на рис. 4.
Рис. 4.
Ввод в эксплуатацию решеток фирмы Martin. 1 – классическая ОПР; 2 – горизонтальная решетка; 3 – SITY 2000; 4 – ОПР типа Vario®
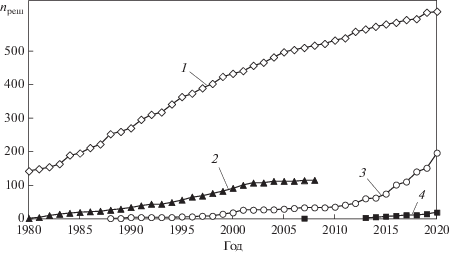
Фирма HZI поставляет устройство для сжигания ТКО с наклонными ПКР конструкции Von Roll (рис. 5). Типовая колосниковая решетка содержит от двух до четырех модулей в длину и от одного до четырех модулей в ширину.
Рис. 5.
Типовая наклонная переталкивающая решетка конструкции Von Roll. а – общий вид; б – элементы конструкции
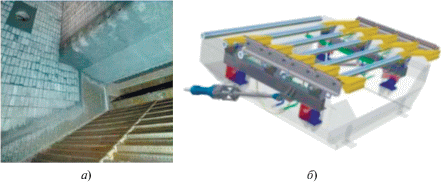
Решетки фирмы HZI изготавливаются в трех модификациях для отходов с теплотой сгорания 4–11, 8–14 и 10–18 МДж/кг. Всего поставлено более 500 комплектов решеток конструкции Von Roll.
Фирма Babcock&Wilcox Volund A/S поставляет наклонные ПКР двух модификаций: Volund и Dyna Grate® (Brаun&Sorensen). Фирма Doosan Lentjes для сжигания ТКО также использует решетки двух видов: ПКР и валковые. Фирма Fisia Babcock Environment GmbH осуществляет поставку трех типов решеток: ПКР конструкции Steinmuller и Noell, а также валковые (конструкции Babcock). Описание конструкций решеток этих фирм приведено в [21].
Сжигание отходов в кипящем слое. В некоторых странах термическая переработка отходов осуществляется путем их сжигания в топках с пузырьковым (стационарным), циркулирующим (с внешней или внутренней циркуляцией) и вихревым кипящим слоем (ТКС).
Наибольший опыт в изготовлении оборудования для сжигания отходов в пузырьковом кипящем слое имеет финская фирма Metso Power (с конца 2013 г. Valmet), разработавшая оригинальную технологию HYBEX ACZTM. Первая топка с пузырьковым кипящим слоем для сжигания отходов была пущена этой фирмой в эксплуатацию в Lidköping (Швеция) в 1994 г. К настоящему времени изготовлено около 20 топок с пузырьковым кипящим слоем для сжигания ТКО, работающих по технологии HYBEX ACZTM. В качестве примера на рис. 6 изображен котел тепловой мощностью 20 МВт, оборудованный такой топкой. Котел работает с конца 2013 г. на электростанции, принадлежащей компании Västervik Miljö&Energi, и генерирует пар давлением 6 МПа и температурой 410°С.
Рис. 6.
Профиль котла для сжигания отходов в пузырьковом кипящем слое по технологии HYBEX ACZTM (а) и схема его топки (б). 1 – подача отходов; 2 – рециркуляция дымовых газов; 3, 4 – третичный и вторичный воздух; 5 – зона выгрузки донной золы (шлака); 6 – сопловая решетка; 7 – течка донной золы
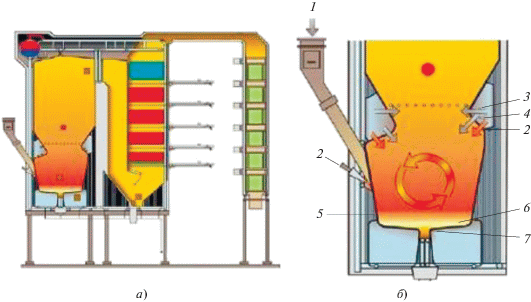
Топки с пузырьковым кипящим слоем для сжигания отходов нашли применение в Италии, Франции, Швеции, Германии и Великобритании. Зачастую в этих топках наряду с ТКО сжигают осадок сточных вод, древесные отходы (кору, опилки). Однако широкого распространения такие топки для сжигания ТКО не получили. Более того, в последние годы наблюдается тенденция по замене топок с пузырьковым кипящим слоем, для которых требуется тщательная подготовка ТКО, на обычное слоевое сжигание на колосниковой решетке. Так, на заводе Eksjö (Швеция), где с 1979 г. эксплуатировались два котла с ТКС общей мощностью 17.5 МВт, в 2005 г. закончилась реконструкция, в результате которой они были заменены на котлы с решеткой Volund производительностью 7.75 т/ч (18 МВт).
Накоплен значительный опыт по сжиганию ТКО в котлах с циркулирующим кипящим слоем (ЦКС). Следует отметить, что для сжигания твердых коммунальных отходов в котлах с ЦКС необходимо проводить их предварительную подготовку (измельчение, удаление металла и крупных инертных материалов, перемешивание), и качество этой подготовки оказывает значительное влияние на надежность работы всей установки, а зачастую и определяет ее. Но при этом в котлах с ЦКС можно сжигать отходы, обладающие широким диапазоном теплоты сгорания, в том числе и высоковлажные. Энергоустановки с котлами с ЦКС имеют достаточно высокий для такого топлива, как ТКО, электрический КПД, который составляет около 28%.
Наибольшее распространение сжигание ТКО в ЦКС получило в Китае [22]. Уже в 2012 г. число предприятий с котлами ЦКС составляло 47, а их суммарная производительность по сжигаемым в таких котлах отходам достигла 40 170 т/сут [22]. В 2011 г. был запущен в эксплуатацию самый крупный в то время котел с ЦКС, в котором сжигалось до 800 т ТКО в сутки и генерировался пар давлением 5.3 МПа и температурой 485°С. В настоящее время в Китае доля отходов, сжигаемых в кипящем слое по разработанной в стране технологии, составляет примерно 20%. Однако прослеживается тенденция постепенного сокращения количества установок с ЦКС в пользу традиционного слоевого сжигания на колосниковой решетке [23].
В Европе котлы для сжигания ТКО в ЦКС часто устанавливают на обычных ТЭС. В качестве примера можно привести ТЭС Handelo в г. Норрчёпинг (Швеция), на которой в 2003 г. был запущен в эксплуатацию котел с ЦКС, изготовленный фирмой Metso Power (Valmet, Финляндия), тепловой мощностью 75 МВт, позволяющий сжигать около 20 т ТКО/ч (200 тыс. т/год) и генерировать пар расходом 27 кг/с, давлением 6.5 МПа и температурой 470°С. Другой котел с ЦКС этой фирмы тепловой мощностью 126 МВт с 2010 г. работает в составе энергоблока электрической мощностью 43 МВт на ТЭС Langerbrugge (г. Гент, Бельгия).
В 2014 г. в Västerås (Швеция) был введен в строй самый большой в мире котел с ЦКС для сжигания отходов, изготовленный фирмой Valmet для компании Mälarenergi. Тепловая мощность котла составляет 155 МВт. Котел входит в состав энергоблока электрической мощностью 50 МВт и генерирует пар давлением 7.5 МПа и температурой 470°С. Всего фирма Valmet изготовила семь котлов для сжигания в ЦКС подготовленных ТКО.
Технология сжигания отходов в вихревом кипящем слое (ВКС) (технологии с кипящим слоем ROWITEC®) была разработана японской фирмой Ebara Corporation и в настоящее время широко применяется в Японии (более чем на 80 заводах). Суть этой технологии заключается в том, что в нижней части топки, где происходит основное горение отходов, вследствие соответствующей подачи воздуха, формы решетки и конструкции топки формируется так называемый вихревой кипящий слой. В Европе первая установка с ВКС производительностью 8.5 т/ч была построена в 1997 г. в Берлине. В настоящее время в Европе построены и пущены в эксплуатацию восемь заводов, на которых установлена топка ROWITEC®, в том числе и в Москве – Московский спецзавод № 4 “Руднево” (МСЗ № 4) производительностью 250 тыс. т/год.
Опыт эксплуатации предприятий с котлами, в которых сжигание отходов происходит в кипящем слое, показал, что для реализации данной технологии требуется предварительная подготовка ТКО, и это существенно повышает затраты на собственные нужды. Поэтому наиболее предпочтительной технологией термической переработки твердых коммунальных отходов, цель которой – их энергетическая утилизация, все же является слоевое сжигание на механической колосниковой решетке.
Газификация и пиролиз. Процесс переработки с использованием газификации и пиролиза наибольшее распространение получил в Японии, где ведущими фирмами – поставщиками газогенераторного оборудования являются Nippon Steel, Kobelco Eco, JFE, Hitachi Zosen, Ebara, Mitsui Engineering&Shipbuilding (MES). По данным [24] три четверти всех заводов, где применяются газификация и пиролиз, укомплектованы установками этих фирм (рис. 7).
Рис. 7.
Количество заводов для термической переработки ТКО с использованием пиролиза и газификации, установки для которых изготовлены японскими фирмами. 1 – MES (8 и 6%); 2 – Ebara (12 и 9%); 3 – Hitachi Zosen (9 и 7%); 4 – JFE (11 и 8%); 5 – Kobelco Eco (19 и 14%); 6 –Nippon Steel (44 и 32%); 7 – другие фирмы (33 и 24%)

Основу технологии крупнейшего поставщика газификационных установок Nippon Steel составляет газификация в плотном слое с жидким шлакоудалением и кислородно-воздушным дутьем (рис. 8). Отходы в смеси с коксом и известняком поступают в верхнюю часть шахтного газогенератора и постепенно движутся в направлении, противоположном направлению обогащенного кислородом дутья, в котором содержание О2 составляет примерно 36%. Образующийся в процессе газификации синтез-газ отводится из верхней части газификатора, очищается в циклоне от твердых частиц и направляется в камеру сгорания. Продукты сгорания синтез-газа с температурой приблизительно 1100°С поступают в котел-утилизатор, где генерируется перегретый пар, который может использоваться для выработки электроэнергии в турбоагрегате. Шлак и металлы в расплавленном состоянии выводятся из пода газификатора, охлаждаются в водяном грануляторе и после их разделения направляются на дальнейшую переработку.
Рис. 8.
Схема термической переработки ТКО по технологии Nippon Steel. 1 – бункер ТКО; 2 – газификатор; 3 – циклон; 4 – котел; 5 – газоохладитель; 6 – рукавный фильтр; 7 – дымосос; 8 – мокрый скруббер; 9 – теплообменник; 10 – установка селективной каталитической очистки газов от оксидов азота; 11 – дымовая труба; 12 – камера сгорания; 13 – паровая турбина; 14 – гранулятор; 15 – дутьевой вентилятор; 16 – зола уноса; 17 – магнитный сепаратор; 18 – шлак; 19 – металл; 20 – дутьевой вентилятор; 21 – подача кислорода; 22 – кокс и известняк
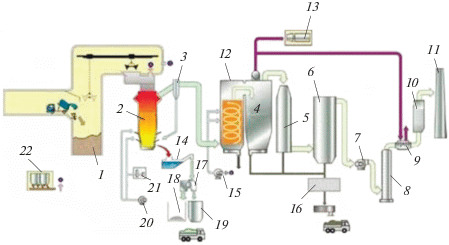
Установка позволяет перерабатывать различные отходы, в том числе наряду с ТКО отходы свалок, золошлаковые остатки от сжигания ТКО, осадок сточных вод, медицинские отходы. Однако энергоэффективность технологии Nippon Steel значительно ниже по сравнению со сжиганием на колосниковой решетке или в кипящем слое из-за потребности в дополнительном топливе (коксе) и высоких затрат на собственные нужды. Кроме того, для обеспечения стекловидного состояния удаляемого шлака требуется подача в газификатор известняка.
В отличие от многих стран (например, стран ЕС), где повышение эффективности преобразования энергопотенциала отходов в энергию в настоящее время имеет приоритетное значение, в Японии одной из главных целей термической переработки отходов являются ликвидация существующих свалок и освобождение земель для дальнейшего использования. В основном именно поэтому предприятия с установками газификации наряду с WTE получили в Японии широкое распространение. По данным [25] фирма Nippon Steel поставила оборудование для 42 заводов (87 установок), еще два завода находятся в стадии строительства. Производительность установок невелика и составляет от 2 до 11 т/ч. Самый крупный завод в городе Кутакюсю (префектура Фукуска), запущенный в 2007 г., состоит из трех линий мощностью 240 т/сут и перерабатывает до 216 тыс. т отходов в год.
Некоторые данные по другим японским фирмам – поставщикам установок, использующих пиролиз и газификацию, приводятся в [24]. Анализ этих данных показывает, что установки имеют ограниченную производительность (до 13 т/ч), а средняя мощность заводов составляет 45–75 тыс. т/год и не превышает 300 тыс. т/год.
Следует отметить, что некоторые фирмы используют технологии, ранее разработанные в Европе, но не получившие там применения из-за низкой энергоэффективности. Так, MES изготавливает оборудование по лицензии фирмы Siemens. Описание этой технологии, основу которой составляет пиролиз, представлено в [26]. По результатам опытной эксплуатации головного образца в г. Фюрт (Германия) фирма-разработчик Siemens отказалась от тиражирования своей разработки в Европе. Компания JFE построила семь заводов по лицензированной технологии Thermoselect (ее описание приводится в [27]). Из-за высоких капитальных и эксплуатационных затрат эта технология также не используется в других странах. Впрочем, и JFE от дальнейших поставок установок по технологии Thermoselect уже отказалась [24].
В Европе ведущим поставщиком газификационных установок является норвежская фирма ENERGOS. Первый завод был введен в эксплуатацию в 1997 г., а всего по этой технологии было построено восемь заводов производительностью 30–78 тыс. т/год (пять в Норвегии, по одному в Германии и Великобритании) [28]. Еще три завода производительностью 144.4 тыс. т/год планировалось запустить в Глазго, Милтон-Кейсе и Дерби (Великобритания).
Заводы по термической переработке ТКО методом газификации существенно проигрывают традиционным заводам WTE. Экологические преимущества также не очевидны. Поэтому в 2019 г. было принято решение о прекращении строительства завода в Дерби [29]. Ранее запущенная в эксплуатацию установка ENERGOS для газификации на заводе Isle of White Plant была преобразована в традиционную установку для сжигания ТКО на колосниковой решетке [30].
Таким образом, технологии газификации для термической переработки ТКО используются в основном только в Японии с целью расширить спектр перерабатываемых отходов в одной установке и ликвидировать свалки. По показателям энергетической утилизации ТКО газификация и пиролиз существенно проигрывают не только традиционному слоевому сжиганию на колосниковой решетке, но и сжиганию в кипящем слое.
ПОВЫШЕНИЕ ЭНЕРГОЭФФЕКТИВНОСТИ ПРЕДПРИЯТИЙ ПО ТЕРМИЧЕСКОЙ ПЕРЕРАБОТКЕ ТВЕРДЫХ КОММУНАЛЬНЫХ ОТХОДОВ
Ранее основным направлением исследований в области термической переработки ТКО было обеспечение экологической безопасности процесса. В настоящее время эта проблема решена: практически все сжигательные установки оснащены современным оборудованием для очистки дымовых газов, которое позволяет обеспечить требуемые нормативные показатели по выбросам вредных веществ. В [21] показано, что эти нормативы являются более жесткими, чем нормативы для котлов, сжигающих органическое топливо. Это дает возможность размещать предприятия по термической переработке ТКО в городской черте и даже, как будет показано далее, организовывать, например, горнолыжные склоны на крышах таких предприятий.
В последние годы после того, как экологическая проблема была решена, приоритетными становятся поиски путей повышения энергоэффективности ТЭС на ТКО, которая в соответствии с Европейской директивой [2] рассчитывается по формуле
Повысить энергоэффективность такой ТЭС можно путем увеличения ее мощности, повышения КПД процесса преобразования энергопотенциала ТКО в тепловую и электрическую энергию, а также организации ее работы в когенерационном цикле. Наибольший эффект достигается при интеграции установок для сжигания ТКО в тепловую схему ТЭС, сжигающей органическое топливо, и их совместной работе с парогазовыми установками (ПГУ).
В [3] говорится, что WTE должны иметь мощность более 100 тыс. т/год и сжигать отходы с теплотой сгорания более 7 МДж/кг. С точки зрения повышения энергоэффективности наиболее перспективными являются заводы мощностью более 260 тыс. т/год. Анализ существующих предприятий такой производительности, на которых установлены решетки ведущих фирм [Martin GmbH, Hitachi Zosen Inova (Von Roll), Babcock&Wilcox Volund A/S, Fisia Babcock Environment GmbH (Steinmuller) и Lentjes (Doosan)] и которые построены после 2000 г., показывает, что в основном на этих заводах установлены две (55%) или три (26%) технологические линии (ТЛ), а средняя производительность решеток, применяемых на таких заводах, составляет примерно 25 т/ч. В состав заводов производительностью 260–300 тыс. т/год входят в основном две или три установки (рис. 9). На заводах производительностью 300–400 тыс. т/год, как правило, применяются две технологические линии, а на предприятиях производительностью более 400 тыс. т/год могут использоваться две, три и более установок.
Рис. 9.
Зависимость числа заводов nз по термической утилизации ТКО от их производительности Qз. Количество линий: 1 – одна; 2 – две; 3 – три; 4 – более четырех
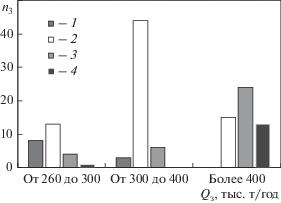
Коэффициент использования тепла при сжигании ТКО составляет 80–90%, электрический КПД – на уровне 20%. Относительно невысокий электрический КПД ТЭС на ТКО обусловлен, в первую очередь, низкими параметрами пара, повысить которые возможно путем применения коррозионно-стойких сталей при изготовлении пароперегревательных поверхностей и нанесения на них защитных покрытий. Кроме того, следует организовать перегрев пара на вынесенных из котла теплообменных поверхностях, обогреваемых продуктами сгорания органического топлива. Увеличить электрический КПД установок для энергетической утилизации ТКО можно также снижением температуры уходящих газов, уменьшением давления пара в конденсаторе, улучшением процесса горения, оптимизацией тепловой схемы. Зарубежный опыт показывает, что в результате реализации этих мероприятий и повышения параметров пара на некоторых ТЭС удается достичь КПД на уровне 27–30% [31].
Далее приводятся примеры WTE с повышенным электрическим КПД, на которых установлены решетки различных типов.
Завод Riverside (Великобритания), введенный в эксплуатацию в 2011 г., перерабатывает 670 тыс. т ТКО в год путем сжигания на трех технологических линиях с наклонной ПКР поставки HZI (конструкции VonRoll) (рис. 10). Ширина решетки 10.25 м, длина 10.4 м, производительность 31.8 т/ч [32]. Благодаря высоким параметрам пара (427°С, 7.2 МПа) электрический КПД превышает 27% [24]. На заводе установлен турбоагрегат мощностью 66 МВт.
Рис. 10.
Завод Riverside (Великобритания) производительностью 670 тыс. т/год с НПР конструкции Von Roll. 1 – приемное помещение; 2 – приемный бункер; 3, 10 – грейферный кран ТКО и шлака; 4 – загрузочная воронка; 5 – питатель; 6 – ПКР конструкции Von Roll; 7 –шлаковыгружатель; 8 – шлаковый конвейер; 9 – шлаковый бункер; 11 – выгрузка шлака; 12, 15 – забор первичного и вторичного воздуха; 13 – вентилятор первичного воздуха; 14 – распределение первичного воздуха; 16 – вентилятор вторичного воздуха и дымосос рециркуляции дымовых газов; 17 – короба вторичного воздуха и дымовых газов рециркуляции; 18 – горелки; 19 – четырехходовой котел; 20 – система некаталитического восстановления; 21 – полусухой реактор; 22 – рукавный фильтр; 23 – дымосос; 24 – шумоглушитель; 25 – подогреватель конденсата; 26 – дымовая труба; 27 – система сбора и транспортировки золы из котла; 28 – система сбора и транспортировки отходов газоочистки
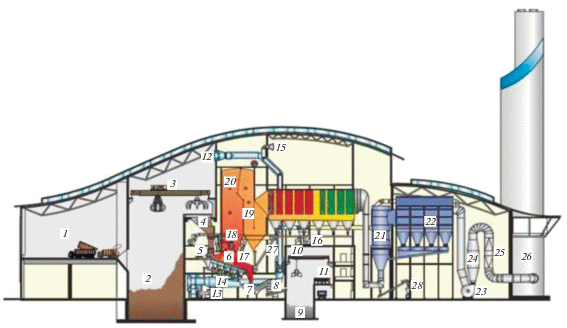
На технологических линиях 5, 6 завода Afval Energie Bedrijf (AEB) TKO сжигают на горизонтальной ПКР фирмы Martin (конструкции Widmer + Ernst), интегрированной в четырехходовой котел горизонтального типа (рис. 11) [33]. Ширина решетки 12.8 м, длина 9.3 м, номинальная производительность 33.6 т/ч, расчетная теплота сгорания отходов составляет 10 МДж/кг. Высокие параметры пара (440°С, 13 МПа) достигаются благодаря применению в пароперегревателе труб из хромоникелевого сплава. В котле используется промежуточный перегрев пара давлением 1.4 МПа с 195 до 320°С. Мощность турбоагрегата составляет 66 МВт, электрический КПД – 30.6% [34]. Котлы ТЛ 5, 6 завода AEB успешно эксплуатируются с 2007 г.
Рис. 11.
Котел завода Afval Energie Bedrijf (AEB) с горизонтальной решеткой Martin. 1 – ПКР; 2 – система подачи первичного воздуха; 3 – система подачи вторичного воздуха и газов рециркуляции; 4 – третичный воздух; 5–7 – первый, второй и третий газоход; 8 – пароперегреватель; 9 – экономайзер; 10 – выход дымовых газов из котла; 11 – барабан котла; 12 – бункер золы; 13 – шлакоудалитель
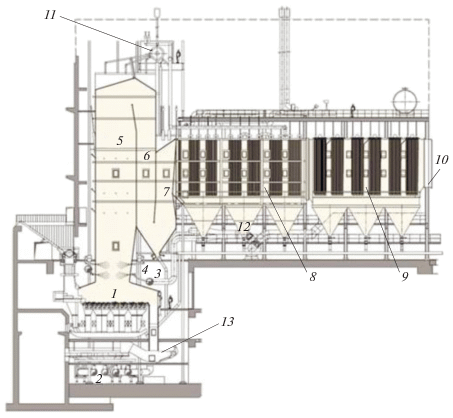
В 2015 г. был введен в эксплуатацию завод WTE West Palm Beach (Флорида, США) электрической мощностью 95.3 МВт, позволяющий перерабатывать примерно 960 тыс. т ТКО в год [10, 35]. На заводе установлены три ТЛ производительностью около 40 т/ч каждая, в состав которых входит котел с ПКР Babcock&Wilcox Volund Dyna Grate® (рис. 12). В котлах генерируется 386.2 т/ч пара температурой 443°С и давлением 6.3 МПа. Следует отметить оригинальную конструкцию котла, при проектировании которого были приняты решения, отличающиеся от традиционных, изложенных, например, в [21]. Для защиты от коррозии поверхностей нагрева, особенно пароперегревательных, применяется наплавка Inconel®. Для охлаждения пара после турбины, как и на большинстве современных WTE, используют воздушный конденсатор.
Рис. 12.
Котел конструкции Babcock&Wilcox Stirling® для сжигания ТКО на WTE West Palm Beach (Флорида, США). 1 – пароперегреватель; 2 – система подачи вторичного воздуха; 3 – загрузочная воронка; 4 – барабан котла; 5 – испарительная ширма; 6 – экономайзер; 7 – уходящие дымовые газы; 8 – водоохлаждаемая зона; 9 – ПКР Dyna Grate®; 10 – выгрузка шлака
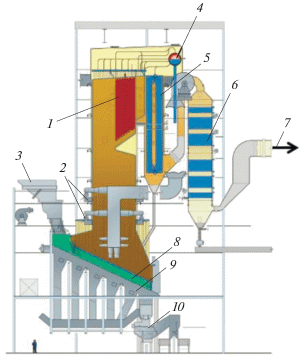
Еще одним примером современного предприятия по термической переработке ТКО с высокой энергоэффективностью, на котором используются также решетки Babcock&Wilcox Volund, может служить WTE Amager Bakke (Копенгаген, Дания) [36, 37]. Завод был пущен в эксплуатацию в 2017 г., имеет две ТЛ производительностью 35 т/ч каждая. В 2018 г. завод переработал около 451 тыс. т ТКО [36]. При сжигании в номинальном режиме отходов, имеющих теплоту сгорания 11.5 МДж/кг, в котле каждой ТЛ генерируется 141.1 т/ч пара температурой 440°С и давлением 7 МПа [37]. Электрический КПД составляет 28%. Помимо отпуска электроэнергии, завод обеспечивает теплом близлежащие районы города (примерно 120 тыс. домохозяйств). Благодаря системе газоочистки работа завода экологически безопасна, выбросы вредных веществ минимальны. Например, предельная концентрация NOх в дымовых газах не превышает 15 мг/м3. На крыше завода, выполненной с уклоном 45° и имеющей высоту 85 м, в 2019 г. был открыт круглогодичный искусственный горнолыжный склон длиной 450 м и разворотом на 180°, проложены пешеходные тропы с высаженными вокруг кустарниками и хвойными деревьями [36].
Завод WTE Bresia (Италия) с ОПР фирмы Martin перерабатывает 800 тыс. т ТКО в год. Пар давлением 7.2 МПа и температурой 450°С поступает в турбоагрегат мощностью 100 МВт (эл.). Электрический КПД составляет более 27% [34], отпуск электрической энергии – 570 ГВт · ч/год, тепловой – 568 ГВт · ч/год [24]. Коэффициент использования тепла топлива на WTE Bresia равен 65%. Данные эксплуатации завода WTE Bresia показывают, что наибольшая энергоэффективность, как уже говорилось ранее, достигается при работе WTE в когенерационном режиме.
В таком же режиме эксплуатируется завод WTE SILLA 2 (Милан, Италия) мощностью более 500 тыс. т/год, который успешно работает с 2001 г. и снабжает теплом почти треть города. В состав завода входят три ТЛ с ОПР системы Martin производительностью 26 т/ч каждая. Работа в теплофикационном цикле при давлении пара 5.2 МПа и температуре 425°С обеспечивают высокую энергоэффективность завода. Зимой при отпуске потребителю электрической [30.2 МВт (эл.)] и тепловой [140 МВт (т.)] энергии энергоэффективность составляет около 108%. Летом при работе завода в конденсационном режиме мощность турбогенератора достигает 63 МВт (эл.). В среднем энергоэффективность WTE SILLA 2 находится на уровне 84%.
Самый большой в Швейцарии завод Хагенхольц после модернизации в 2010 г. имеет мощность по сжиганию ТКО примерно 240 тыс. т/год и является лидером в области энергетического использования отходов в этой стране (эффективность составляет 92% [38]). На заводе установлены две ТЛ номинальной производительностью 115 тыс. т/год каждая с ОПР длиной 8.05 м и шириной 6.32 м. В зависимости от теплоты сгорания отходов производительность ТЛ может быть увеличена до 1200 тыс. т/год.
В топке дымовые газы нагреваются до температуры примерно 1100°C. В котлах генерируется пар давлением 4.0 МПа и температурой 400°C, вырабатываемая электроэнергия передается в сеть Цюриха (Elektrizitätswerkeder Stadt Zürich – EWZ), тепловая энергия – в теплосеть северной части Цюриха (Цюрих-Норд). В 2013 г. завод по сжиганию отходов в Хагенхольце произвел около 121 ГВт · ч электроэнергии и 638 ГВт · ч тепловой энергии. За вычетом собственного потребления в городские сети было направлено около 97 ГВт · ч электроэнергии и 404 ГВт · ч тепловой энергии.
Наиболее радикальным способом повышения энергоэффективности WTE является их интеграция в тепловую схему обычной ТЭС, в том числе той, на которой реализован парогазовый цикл. Примером такой интеграции может служить предприятие для термической переработки ТКО в Vantaa (Финляндия), введенное в эксплуатацию в 2014 г., на котором на двух ТЛ с колосниковой решеткой HZI (конструкции Von Roll) ежегодно сжигаются 320 тыс. т ТКО [39]. Тепловая схема завода показана на рис. 13.
Рис. 13.
Тепловая схема ТЭС в Vantaa (Финляндия). 1 – природный газ; 2 – газовая турбина; 3 – электрогенератор мощностью 31 МВт; 4 – воздухоподогреватель; 5 – установка WTE; 6 – паровая турбина; 7 – электрогенератор мощностью 49.5 МВт; 8 – деаэратор; 9 – система теплоснабжения (тепловая мощность 119.3 МВт); 10 – сетевой подогреватель; 11 – котел-утилизатор
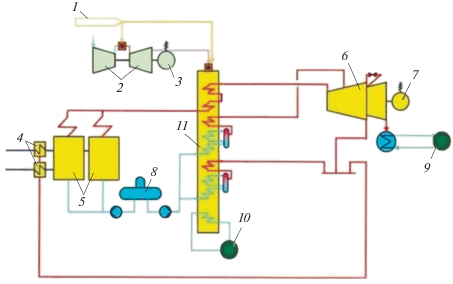
Генерируемый в котлах WTE пар давлением 9.0 МПа и температурой 400°С поступает в котел-утилизатор (КУ) ПГУ, перегревается до 535°С и направляется в паровую турбину мощностью 50 МВт (эл.). Греющей средой в трехконтурном КУ служат продукты сгорания природного газа после газовой турбины мощностью 31 МВт (эл.). В паровую турбину из КУ поступают также пар среднего давления (3.2 МПа, 370°С) и основной поток пара низкого давления (0.6 МПа, 157°С). Часть пара низкого давления направляется в паровые калориферы для нагрева дутьевого воздуха котлов WTE. После турбины пар поступает в сетевой подогреватель для отпуска потребителю тепловой энергии. Коэффициент использования тепла топлива ТЭС Vantaa приближается к 100%.
В [31] сообщается о других примерах совместной работы WTE и ПГУ: на ТЭС в Лингчепинге (Швеция), Моердийке (Нидерланды), Бильбао (Испания), а также на некоторых заводах в Японии. Еще одним примером совместной работы WTE и ПГУ может служить ТЭС в Майнце (Германия) производительностью 340 тыс. т/год, на которой первые две ТЛ были пущены в 2003 г., а третья – в 2008 г. Пар давлением 4.23 МПа и температурой 400°С, генерируемый на ТЛ 1, 2, направляется на близлежащую ТЭС с ПГУ мощностью 400 МВт (эл.). Пар, генерируемый на ТЛ 3 (4.23 МПа, 420°С), поступает в собственную конденсационную турбину мощностью 20 МВт(эл.), входящую в состав WTE. Электрический КПД ТЛ 3 довольно высок (до 27%), но наибольшая энергоэффективность достигается на ТЛ 1, 2.
Таким образом, в мире накоплен достаточно большой опыт по повышению энергоэффективности ТЭС на ТКО. Целесообразность внедрения тех или иных мероприятий на конкретных установках определяется на основании технико-экономических оценок и с учетом местных условий.
ТЕРМИЧЕСКАЯ ПЕРЕРАБОТКА ТВЕРДЫХ КОММУНАЛЬНЫХ ОТХОДОВ В РОССИИ И ПЕРСПЕКТИВЫ РЕАЛИЗАЦИИ СОВРЕМЕННЫХ ТЕХНОЛОГИЙ
Для России безальтернативный путь цивилизованного решения проблемы с ТКО – сжигание (энергетическая утилизация). Здесь уместно сказать, что развитие энергетической утилизации ТКО во многом зависит от заинтересованности энергетических компаний использовать эти отходы в своей производственной деятельности. За рубежом строительством и эксплуатацией многих предприятий для термической переработки отходов часто занимаются именно энергетические компании и ТКО считают одним из доступных и экологически безопасных возобновляемых источников энергии (ВИЭ). В России только на трех предприятиях энергопотенциал ТКО преобразуется в электроэнергию: введенный в эксплуатацию в 2001 г. после реконструкции московский спецзавод завод № 2 (МСЗ № 2) мощностью 130 тыс. т/год, на котором установлены три турбоагрегата электрической мощностью 1.2 МВт каждый (сейчас законсервирован), МСЗ № 4 мощностью 250 тыс. т/год (год пуска 2005 г., установленная электрическая мощность 12 МВт) и МСЗ № 3 мощностью 360 тыс. т/год (введен в эксплуатацию в 2007 г., установленная электрическая мощность 11 МВт). На других российских относительно крупных (более 100 тыс. т/год) предприятиях по термической переработке ТКО: в Мурманске, Владивостоке (с 2019 г. закрыт) и Пятигорске – потребителю отпускается только тепло.
После принятия Правительством РФ Постановления от 28.02.2017 № 240 и Распоряжения от 28.02.2017 № 355-р намечено строительство объектов ВИЭ на основе ТКО общей электрической мощностью 280 МВт в Московской обл. и предприятия электрической мощностью 55 МВт в Республике Татарстан. Во исполнение указанных Постановления и Распоряжения в Свистягино (Воскресенский район Московской обл.) в августе 2018 г. начато строительство первого завода по термической переработке отходов мощностью 700 тыс. т/год. Изготовлены три котла Е-95.2-7.0-430 (П-152) для этого завода и начат монтаж оборудования котла на строительной площадке. На Уральском турбинном заводе завершено производство паровой турбины Кп-77-68 мощностью 77 МВт. Разработана и прошла государственную экспертизу проектная документация для трех других заводов: в Наро-Фоминском, Солнечногорском и Ногинском районах Московской обл. В 2021–2022 гг. планируется ввод всех четырех заводов в эксплуатацию. Однако у специалистов возникают некоторые вопросы к этим предприятиям:
выбранная единичная мощность 700 тыс. т/год не является базовой (масштабируемой) для внедрения по всей России;
не обоснован выбор их мощности с учетом логистики и ситуации с ТКО в Московском регионе;
установленная электрическая мощность заводов рассчитана для заведомо завышенной теплоты сгорания ТКО;
эксплуатация заводов по сжиганию ТКО в рамках договоров о предоставлении мощности (гарантийная выдача электрической мощности не менее 70 МВт) может приводить к “пережогу” природного газа (примерно 7600 м3/ч) и дополнительным ежегодным выбросам оксидов азота в количестве 255 т [40, 41].
Тем не менее выбор технологии и профессионализм отечественных производителей и поставщиков оборудования не вызывают сомнения и каких-либо опасений с точки зрения технологической надежности и экологической безопасности этих заводов. На них будет реализована технология японско-швейцарской компании HZI – одна из самых референтных в настоящее время в Европе с жесткими требованиями к экологическим параметрам работы оборудования. Основным поставщиком оборудования является ПАО “ЗиО-Подольск”, которое изготавливает котельное оборудование уже на протяжении 100 лет, в том числе и котлы для заводов по сжиганию ТКО. На этом машиностроительном предприятии были изготовлены котлы для московских заводов № 3, 4, завода в Зорбау (Германия).
После вступления в силу с 1 января 2020 г. Федерального закона от 27.12.2019 № 450-ФЗ, в котором использование ТКО в качестве возобновляемого источника энергии (вторичных энергетических ресурсов) приравнивается к утилизации (считается энергетической утилизацией), открываются еще более широкие перспективы для строительства ТЭС на ТКО в нашей стране. В этой связи на данном этапе необходимо прилагать максимум усилий, чтобы головные отечественные образцы ТЭС на ТКО, строительство которых предусматривается в ближайшее время, удовлетворяли по крайней мере современным мировым требованиям по экологической безопасности. Вряд ли можно ожидать, что головные образцы отечественных предприятий для энергетической утилизации ТКО будут иметь энергоэффективность выше 65%. Это, как показано ранее, подразумевает их работу только в теплофикационном режиме с гарантированным отпуском тепла потребителю, что в России в настоящее время весьма проблематично. Скорее всего, в большинстве случаев это будут конденсационные ТЭС с электрическим КПД на уровне 20%, на которых будут сжигать ТКО, имеющие теплоту сгорания 7–9 МДж/кг. Энергоэффективность таких ТЭС на ТКО не превысит 0.45.
Дальнейшее развитие энергетической утилизации ТКО в России может быть только при условии учета зарубежного опыта и тесного взаимодействия энергетиков, экологов и специалистов в области управления отходами. В этой связи представляется, что наиболее перспективной для России является ТЭС для энергетической утилизации 360 тыс. т ТКО в год установленной электрической мощностью 24 МВт, которая ранее была предложена во исполнение реализации Постановления Правительства Москвы [42]. Эта ТЭС была разработана исходя из современных экологических требований Директивы 2000/76/ЕС Европейского парламента и совета от 04.12.2000 “О сжигании отходов” [43], Директивы 2008/98/ЕС Европейского парламента и совета от 19.11.2008 “Об отходах и отмене определенных директив” [2], а также с учетом мировой и отечественной практики использования наилучших доступных технологий в области термической утилизации отходов [20]. Кроме соблюдения современных требований к охране окружающей среды в комплекс заложен целый ряд других передовых тенденций в области энергетической утилизации ТКО. В соответствии с Постановлением [42] предполагалось, что по периметру столицы будет построено шесть таких ТЭС, что позволило бы решить проблему с ТКО в Москве уже к 2015 г. Близость потребителей тепла позволяла бы работать ТЭС как в теплофикационном, так и в конденсационном цикле со средней годовой энергоэффективностью на уровне 65%. Экспертные оценки показывают, что только в России востребованы, по крайней мере, 34 такие ТЭС в 22 городах.
ВЫВОДЫ
1. Энергетическая утилизация ТКО, т.е. термическая переработка отходов с выработкой электрической и тепловой энергии, является составной частью циркулярной экономики и будет в любом случае основным и завершающим этапом на пути комплексного решения проблемы санитарной очистки населенных пунктов от отходов. Именно поэтому в мире прослеживается устойчивая тенденция роста количества предприятий, перерабатывающих ТКО термическим способом.
2. Современные предприятия по термической переработке отходов – это по сути ТЭС, на которых основным топливом являются ТКО (ТЭС на ТКО) с комбинированным отпуском электроэнергии и тепла. Термическая переработка ТКО на таких ТЭС осуществляется главным образом путем слоевого сжигания отходов на механической колосниковой решетке. Эта технология наиболее отработана и освоена, затраты на собственные нужды, связанные с подготовкой отходов к сжиганию, существенно ниже расходов при реализации других технологий (сжигание в кипящем слое, газификация, пиролиз), а энергоэффективность – максимальная при сопоставимом воздействии на окружающую среду. Все современные ТЭС на ТКО оснащены многоступенчатой газоочисткой, поэтому проблемы их экологически безопасной эксплуатации полностью решены.
3. В настоящее время исследования направлены на повышение энергоэффективности ТЭС на ТКО путем увеличения их мощности, повышения КПД преобразования энергопотенциала ТКО в тепловую и электрическую энергию, а также на организацию работы такой ТЭС в когенерационном цикле (в режиме ТЭЦ). Наибольший энергетический эффект достигается при интеграции установок для сжигания ТКО в тепловую схему ТЭС, сжигающей органическое топливо, в том числе благодаря совместной работе с ПГУ.
4. В результате повышения параметров пара вследствие применения коррозионно-стойких сталей и защитных покрытий, организации промежуточного перегрева пара, снижения температуры уходящих газов, уменьшения давления пара в конденсаторе, улучшения процесса горения, оптимизации тепловой схемы путем интеграции в тепловую схему электростанции, сжигающей органическое топливо, и других мероприятий на некоторых ТЭС на ТКО удается достичь КПД на уровне 30%. На ТЭЦ, сжигающих ТКО, энергоэффективность может превышать 100%.
5. Россия делает только первые шаги в области энергетической утилизации ТКО. До настоящего времени построено всего три завода (все в Москве) суммарной установленной электрической мощностью 26.6 МВт. В Московской обл. предусматривается строительство четырех относительно крупных ТЭС каждая электрической мощностью 70 МВт и производительностью по сжигаемым ТКО 700 тыс. т/год.
6. В мире накоплен достаточно большой опыт по повышению энергоэффективности и экологически безопасной эксплуатации ТЭС на ТКО. На данном этапе необходимо прилагать максимум усилий, чтобы в России воспользовались этим опытом.
Список литературы
Рынок производства энергии из отходов. Его состояние и прогноз развития. Режим доступа: https://zen.yandex.ru/media/w2e/energiia-iz-othodov-v-mire-5d91f4bee6cb9b00ad469efd
Directive 2008/98/EC of the European Parliament and of the Council of 19 November 2008 on waste and repealing certain Directives [Text with EEA relevance] // Official J. European Union. 22 Nov. 2008.
Waste to Energy: Considerations for Informed Decision-Making: 6 Aug. 2019. Режим доступа: https:// www.ctc-n.org/resources/waste-energy-considerations-informed-decision-making
Spoiler alert: Circular economy still needs residual waste treatment in 2035: June 2019. Режим доступа: https://www.cewep.eu/cewep-capacity-calculations/
Latest Eurostat Figures: Municipal Waste Treatment 2018. 29 Jan. 2020. Режим доступа: https://www.cewep.eu/municipal-waste-treatment-2018/
Waste-to-Energy 2018/2019: Technologies, plants, projects, players and backgrounds of the global thermal waste treatment business. 11th ed. Ecoprog GmbH, 2018.
Waste-to-Energy Plants in Europe in 2017. Режим доступа: https://www.cewep.eu/waste-to-energy-plants-in-europe-in-2017/
List of incinerators in the United Kingdom. Режим доступа: https://en.wikipedia.org/wiki/List_of_incinerators_in_the_United_Kingdom
Эстония как лидер в мусоросжигании // Твердые бытовые отходы. 2016. № 2. С. 6–7.
Kitto J.B., Fick M.D. Jr., Hiner L.A. World-Class Technology for the Newest Waste-to-Energy Plant in the United States – Palm Beach Renewable Energy Facility № 2 [Электрон. документ]: Technical Paper BR-1935. Renewable Energy World International, Orlando, Florida, U.S.A, 13–15 Deс. 2016. Режим доступа: https://yandex.ru/search/?text=World-Class-Technology-for-Waste-to-Energy-Plant—2016-Renewab-le-Energy-World-Article&lr=213
Трешлер Д.Р. Феникс из Флориды // Твердые бытовые отходы. 2008. № 6. С. 64–67.
Энергетическая утилизация ТБО // Энергетический бюл.: Аналитический центр при Правительстве РФ. 2017. Вып. № 48. С. 14–18. Режим доступа: https://ac.gov.ru/files/publication/a/13175.pdf
Чистые технологии и устойчивое развитие // Информ. бюл.: EY, Услуги в области чистых технологий и устойчивого развития. 2018. Вып. 5: Сжигание как способ решения проблемы коммунальных отходов. Уроки развитых стран. Режим доступа: https://www.ey.com/Publication/vwLUAssets/EY-cas-newsletter-march-2018/$File/EY-cas-newsletter-march-2018.pdf
Тугов А.Н., Родионов В.И. Термическая переработка ТКО в мире // Твердые бытовые отходы. 2016. № 8. С. 20–24.
Waste-to-Energy market continues strong growth: Press release of Еcoprog GmbH, 22 Nov. 2016. Press release Waste-to-Energy 2016–2017 ecoprog.rtf. Режим доступа: https://www.ecoprog.com/fileadmin/ user_upload/pressemitteilungen/pr_waste_to_energy_ ecoprog.pdf
Энергетическая утилизация отходов. Режим доступа: https://ru.wikipedia.org/wiki/
PCH201-127_Shenzhen_Plant Shenzhen East Waste-to-Energy Power Plant. Режим доступа: http://www. volund.dk/Waste_to_Energy/References/Shenzhen_ East_China
Lim Wen Bin, Yuen Edwin, Bhaskar Ananda Ram. Governments across the emerging markets are eager to tap into waste-to-energy (WTE) technologies, but many are learning that it takes more. Режим доступа: https:// home.kpmg/xx/en/home/insights/2019/10/waste-to-energy-green-solutions-for-emerging-markets.html
Globalization on Waste-to-Energy market continues: Press release of Ecoprog GmbH. 27 Nov. 2018. Press release Waste-to-Energy 2018–2019 ecoprog.rtf. Режим доступа: https://www.ecoprog.com/fileadmin/ user_upload/pressemitteilungen/ecoprog_press_release_ Waste_to_Energy_2018-2019.pdf
Integrated Pollution Prevention and Control. Reference Document on Best Available Techniques for Waste Incineration. European Commission, 2006.
Тугов А.Н. Энергетическая утилизация твердых коммунальных отходов на ТЭС. М.: ОАО ВТИ, 2016.
Тугов А.Н. Электростанции, сжигающие коммунальные отходы, в Китае // Энергохозяйство за рубежом. 2016. № 2. С. 11–14.
Wang Tianyi. Waste-to-Energy in China. L., May 2018. Режим доступа: https://worldwastetoenergy.com/wp-content/uploads/2018/05/Wang-Tianyi-China-EverBright.pdf
Review of state-of-the-art waste-to-energy technologies: Stage Two – Case studies. WSP UK Limited, WSP House, L., Jan. 2013. Режим доступа: WSP Waste to Energy Technical Report Stage Two, http://www.epa.wa.gov.au/sites/default/files/Publications/WSP%20Waste%20to%20Energy%20Technical%20Report%20Stage%20Two.pdf
Direct Melting System Brochure.pdf. Режим доступа: https://www.eng.nipponsteel.com/english/whatwedo/wastetoenergy/wtoeplant/direct_melting_system/
Михайлов Н.В. Термическое обезвреживание отходов. В поиске осуществимых решений // Твердые бытовые отходы. 2009. № 3. С. 14–20.
Yamada S., Shimizo M., Mioshi F. Thermoselect waste gasification and reforming process // JFE Technical Report. 2004. № 3. P. 21–26.
ENERGOS. Режим доступа: http://www.energos.com/
This is what will happen to 3,500 tonnes of rubbish left at closed Derby рlant. Режим доступа: https://www.derbytelegraph.co.uk/news/derby-news/ what-happen-3500-tonnes-rubbish-3259542
Isle of White gasification facility. Режим доступа: https://en.m.wikipedia.org/wiki/Isle_of_Wight_gasification_facility
Тугов А.Н. Опыт использования твердых коммунальных отходов в энергетике (обзор) // Теплоэнергетика. 2015. № 12. С. 13–22. https://doi.org/10.1134/S0040363615120127
Riverside. UK Energy-from-Waste Plant: Hitachi Zosen Inova AGhzi_ref_riverside-en, Режим доступа: http://www.hz-inova.com/cms/wp-content/uploads/ 2014/11/hzi_ref_riverside-en.pdf
Value from Waste / Afval Energie Bedrijf, City of Amsterdam, March 2006. Режим доступа: https://www.aebamsterdam.com/media/1501/grote-hr-brochure-engels_v2006-small.pdf
Report and Recommendations of the Environmental Protection Authority and the Waste Authority. Report 1468 Waste to energy s16e, April 2013. Режим доступа: https://www.epa.wa.gov.au/sites/default/files/Publications/Rep%201468%20Waste%20to%20energy%20s16e%20040413.pdf
Solid Waste Authority. West Palm Beach, Florida, USA. Режим доступа: http://www.volund.dk/Waste_to_Energy/References/ West_Palm_Beach
Amager Bakke. Режим доступа: https://ru.wikipedia. org/wiki/
Waste-to-Energy Plant Amager Bakke / Copenhill Copenhagen, Denmark. Режим доступа: http://www.volund.dk/Waste_to_Energy/References/ARC_Amager_Bakke_Copenhagen
Stadt Zürich ERZ Entsorgung + Recycling. Thermische Verwertung von Abfall. Режим доступа: https://www.stadt-zuerich.ch/content/dam/stzh/ted/ Deutsch/erz/Zuerich_Waerme/Publikationen_und_ Broschueren/ZW_Thermische_Verwertung_Hagenholz_1708.pdf
Pöyry case summary: Vantaa Energy Finland. Waste-to-Energyplant. Режим доступа: https://www.poyry. com/sites/default/files/media/related_material/poyry_ vantaa_energy_technical_leaflet_2.pdf
Тугов А.Н., Родионов В.И. Энергетическая утилизация ТКО в России // Твердые бытовые отходы. 2017. № 8. С. 6–10.
Тугов А.Н., Смирнова О.А. К вопросу о строительстве в Московской области заводов по сжиганию ТКО // Твердые бытовые отходы. 2018. № 10. С. 6–12.
Постановление Правительства Москвы № 313-ПП от 22.04.2008 “О развитии технической базы городской системы обращения с коммунальными отходами в городе Москве”. Режим доступа: http://mosopen.ru/document/313_pp_2008-04-22
Directive 2000/76/ЕС of the European Parliament and of the Council of 4 December 2000 on incineration of waste // Official Journal of European Communities. 28.12.2000. Режим доступа: https://eur-lex.europa.eu/LexUriServ/LexUriServ.do?uri= CONSLEG:2000L0076:20001228:EN:PDF
Дополнительные материалы отсутствуют.
Инструменты
Теплоэнергетика