Теплоэнергетика, 2021, № 9, стр. 43-50
Применение Aspen plus для моделирования состава синтез-газа в процессе паровой бескислородной газификации биомассы
С. А. Шевырёв *
Кузбасский государственный технический университет им. Т.Ф. Горбачева
650000 Кемерово, Весенняя ул., д. 28, Россия
* E-mail: ssa.pmahp@kuzstu.ru
Поступила в редакцию 12.09.2020
После доработки 20.10.2020
Принята к публикации 23.12.2020
Аннотация
Процесс газификации – это один из способов получения водорода, все чаще используемых в мировой практике. При его промышленной реализации в качестве газифицирующего агента наибольшее распространение получила парокислородная смесь. Однако перегретый пар более перспективен в этой роли, так как вода служит донором водорода. Отсутствие кислорода в газифицирующем агенте крайне важно. Это не только позволяет экономить топливо, не окисляя его в процессе газификации, но и снижает стоимость синтез-газа вследствие отсутствия энергозатратных установок разделения воздуха для получения кислорода. Перегретый водяной пар для ведения процесса газификации можно получать на тепловых электрических станциях различной тепловой и электрической мощности. Это позволит производить перегретый пар в широком диапазоне температур, давлений и с больши́м расходом для газогенераторов с высокой удельной тепловой мощностью. Моделирование такого процесса осуществлено в программном комплексе Aspen Plus, широко используемом во многих странах для моделирования химико-технологических и энергетических систем. Процесс газификации моделируется в нем, как правило, с применением реакторов типа RYield или RGibbs. Показаны результаты влияния температуры (750–965°С) и давления (от 0.1 до 3.0 МПа) перегретого водяного пара на состав синтез-газа. В зависимости от давления и температуры перегретого водяного пара получаемый синтез-газ может быть использован в качестве топлива для энергоустановок (энергетическое направление) или в качестве исходного материала для получения разнообразных химических веществ, например водорода, синтетического жидкого топлива и др. Осуществлено сравнение результатов моделирования с литературными данными, которое показало расхождение не более 15%.
В связи со значительным изменением климата на планете, ростом выбросов CO2 и повышением средней температуры многие страны планируют существенное сокращение потребления ископаемого топлива и переход на возобновляемые источники энергии и биомассу для выработки тепловой и электрической энергии. Важная роль в этом процессе отводится освоению и развитию новых технологических процессов. Например, развиваются концепции Power-to-X, X-to-Liquid [1], согласно которым предполагается использовать в комбинации или раздельно электрическую энергию, углекислый газ, биомассу и продукты ее переработки в целях получения различных химических веществ, таких как водород, синтетические жидкие топлива, диметиловый эфир, метанол и др. [2]. Особое значение при этом уделяется получению водорода. Концепция развития водородной энергетики имеется, например, в Германии, где реализуется так называемый “энергетический поворот” с постепенным значительным увеличением доли возобновляемого топлива в энергетике [3]. При этом стоит отметить, что если ранее потребление твердого топлива (угля) для выработки электрической энергии в Германии составляло 50–60%, то в настоящее время оно снизилось до 20% [4].
Универсальной технологией, в которой могут успешно сочетаться выработка тепловой и электрической энергии, а также получение водорода и других химических веществ, является газификация. Реализация этой технологии должна осуществляться в полигенерирующих комплексах [5], так как это позволяет значительно повысить эффективность протекающих процессов и снизить стоимость получаемых продуктов. В качестве газифицирующего агента при газификации следует использовать перегретый водяной пар, что даст возможность получать максимальное количество синтез-газа оптимального состава для дальнейшего его нетопливного применения. Здесь речь идет о сравнении идеализированных процессов [6], потому что в неидеальных условиях все очень индивидуально и иногда паровая бескислородная газификация может проигрывать парокислородной технологии [7].
Перегретый пар может быть произведен в классическом цикле Ренкина с нетрадиционным перераспределением материальных (тепловых) потоков. Это позволит получать перегретый пар с требуемыми давлением и температурой, а также большим расходом для применения его в газогенераторах с высокой удельной тепловой мощностью. Моделирование такого процесса представляет собой очень интересную задачу. При этом необходимо определить влияние параметров перегретого пара на характеристики газовых продуктов, получаемых в процессе газификации.
Цель настоящей работы – осуществить моделирование процесса получения перегретого пара в условиях полигенерации и установить зависимость состава газовых продуктов после газогенератора от давления и температуры перегретого пара.
МЕТОДОЛОГИЯ ИССЛЕДОВАНИЯ
Подробное описание концепции полигенерации (энерготехнологическая схема – ЭНТЕС) представлено в [7, 8]. Ее основой являются способ получения перегретого пара и нетрадиционное перераспределение потоков между паровым котлом и паровой турбиной (рис. 1).
Рис. 1.
Принципиальные схемы получения перегретого водяного пара при использовании конденсационной турбины (a) и турбины с противодавлением (б). 1 – паровой котел; 2 – конденсационная или теплофикационная турбина; 3 – конденсатор; 4 – насос; 5 – регенеративный теплообменник; 6 – электрогенератор; 7 – турбина с противодавлением (значения давлений и температур показаны в качестве возможного варианта)
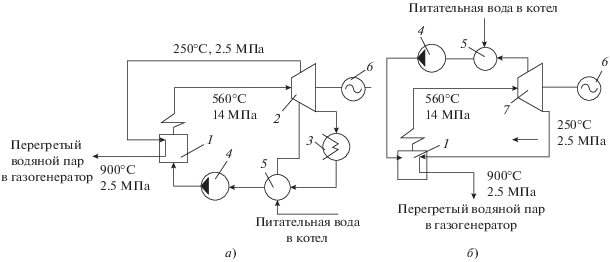
Из парового котла 1 перегретый пар подается в паровую турбину (может быть любого типа) 2 или 7. Из нее перегретый пар с пониженными давлением и температурой снова возвращается в котел, где в изобарном процессе повторно нагревается до более высокой температуры. Далее он направляется на газификацию. При этом температура пара, поступающего на газификацию, может составлять до 1000°С, а давление не должно превышать 3 МПа.
В России существует государственный стандарт [9], в котором описаны различные материалы и сплавы, предназначенные для применения при температуре менее 1000°С и давлении до 3 МПа. Срок службы этих материалов может составлять от 1 года и более в зависимости от температуры пара. Например, если в дополнительном парогенераторе температура пара будет около 850°С, то ожидаемый срок его службы может составить около 11 лет. Возможными материалами для изготовления такого дополнительного пароперегревателя может быть, например, сталь 40Х25Н20 или сплав 40Х20Н35.
Моделирование процессов полигенерации при использовании турбины с противодавлением выполнено в программном комплексе Aspen Plus. Он обладает большими функциональными возможностями и потому широко используется для моделирования химико-технологических систем [10].
МАТЕМАТИЧЕСКОЕ МОДЕЛИРОВАНИЕ
Для моделирования энерготехнологической схемы процесса горения в котле при производстве перегретого пара и газификации в ЭНТЕС использовали биомассу в виде буковых опилок.
Исходные данные для расчета
Биомасса (буковые опилки) имеет следующие характеристики (обозначения даны в соответствии с [11, 12]):
Влажность W ar, % ...........................................7.4 |
Зольность Ad, % ..............................................0.9 |
Выход летучих веществ V d, % ......................84.2 |
Связанный углерод, % ..................................14.9 |
Содержание, %: |
углерода Сd ............................................ 49.5 |
водорода Hd .............................................6.1 |
кислорода Od .........................................43.4 |
азота Nd .................................................. 0.13 |
серы Sd ...................................................0.01 |
Низшая теплота сгорания Qн, МДж/кг ........15.5 |
Расход биомассы для ведения процесса горения принимали равным 1 кг/с, для непосредственного процесса газификации – 3 кг/с. Соотношение биомасса : водяной пар для моделирования газификации составляло 0.55 (при учете суммарного расхода пара в обе камеры газогенератора, модель которого приведена на рис. 2).
Рис. 2.
Модель двухстадийного газогенератора в Aspen Plus. 1 – первая камера двухстадийного газогенератора, предназначенная для предварительной газификации биомассы перегретым паром; 2 – вторая камера газогенератора для непосредственной газификации перегретым паром; линии 3 и 5 – коксовый остаток и зола соответственно; 4 – циклон для отделения твердых частиц от газовой смеси; 6 – парогазовая смесь, в которой содержатся синтез-газ и твердые частицы
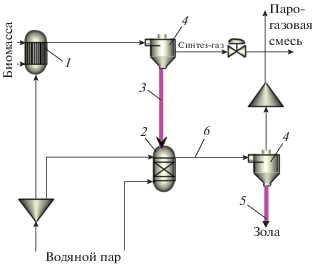
Для моделирования процесса паровой газификации принят двухстадийный газогенератор [13]. Газогенератор в моделировании имеет две камеры, и в модели каждая камера моделируется как отдельный реактор. В качестве модели для первой и второй камер газогенератора взяты реакторы RGibbs, которые обеспечивают моделирование равновесных реакций без необходимости ввода стехиометрических уравнений и количественного задания выходов продуктов реакций. Расчеты основываются на минимизации свободной энергии Гиббса ΔG всех возможных химических реакций в модели
где ΔH – изменение энтальпии химической реакции, кДж/кг; T – температура, К; ΔS – изменение энтропии химической реакции, кДж/(кг · К). При этом заранее определяются вещества-реагенты и возможные продукты, образующиеся в этих реакциях.Первый реактор RGibbs моделирует образование нелетучего углерода при недостатке перегретого пара для полного протекания газификации биомассы. В этом процессе происходит удаление из биомассы летучих веществ и влаги вследствие подвода тепловой энергии с перегретым паром. Параметры перегретого пара на входе в первый реактор варьировались следующим образом: температура от 750 до 965°С, давление от 0.1 до 3.0 МПа. Все горючие вещества, полученные при предварительной газификации биомассы (камера 1 на рис. 2), сжигались для производства тепловой и электрической энергии [7]. Снижение температуры и давления перегретого пара перед первой и второй камерами газогенератора моделировалось при использовании редукционно-охладительной установки путем дросселирования пара и добавления холодной воды.
Второй реактор RGibbs моделирует процесс непосредственной газификации в среде перегретого пара (камера 2 на рис. 2). Температура и давление перегретого пара во втором реакторе такие же, как и на входе в первый. Расход перегретого пара во второй реактор подобран с условием максимизации содержания водорода, CO и CH4 в получаемом синтез-газе.
Влияние давления на состав синтез-газа
Целевым продуктом в разработанной ЭНТЕС является синтез-газ (CO + H2), который формируется во второй камере газогенератора. Далее из него могут быть получены различные химические вещества, в том числе и водород. Результаты расчета состава синтез-газа при газификации перегретым паром при постоянной температуре (около 965°С) и различном давлении для второй камеры газогенератора показаны в табл. 1 и 2. Концентрации других газов (предельных и непредельных углеводородов) ввиду их относительно низкой концентрации приняты равными 0 и не учитывались в представленных данных.
Таблица 1.
Массовый расход G, кг/с (в числителе), и массовая доля Gx, % (в знаменателе), компонентов сухого синтез-газа после второй камеры газогенератора при постоянной температуре и различном давлении
Компонент | G/Gx при p, МПа | ||||||
---|---|---|---|---|---|---|---|
0.1 | 0.5 | 1.0 | 1.5 | 2.0 | 2.5 | 3.0 | |
CO2 | 1.94/82.7 | 1.84/80.6 | 1.63/79.7 | 1.58/79.1 | 1.54/78.7 | 1.52/78.4 | 1.50/78.1 |
H2 | 0.164/7.0 | 0.136/6.4 | 0.124/6.1 | 0.117/5.9 | 0.112/5.7 | 0.108/5.6 | 0.105/5.5 |
CO | 0.149/6.2 | 0.150/7.1 | 0.149/7.3 | 0.148/7.4 | 0.147/7.5 | 0.146/7.5 | 0.145/7.5 |
CH4 | 0.095/4.1 | 0.126/5.9 | 0.142/6.9 | 0.152/7.6 | 0.16/8.1 | 0.166/8.6 | 0.172/8.9 |
Таблица 2.
Мольный расход V, кмоль/с (в числителе), и мольная доля Vx, % (в знаменателе), компонентов сухого синтез-газа после второй камеры газогенератора при постоянной температуре и различном давлении
Компонент | V/Vx при p, МПа | ||||||
---|---|---|---|---|---|---|---|
0.1 | 0.5 | 1.0 | 1.5 | 2.0 | 2.5 | 3.0 | |
CO2 | 0.0440/32.2 | 0.0390/32.5 | 0.0370/32.8 | 0.0360/33.0 | 0.0350/33.2 | 0.0340/33.3 | 0.0340/33.4 |
H2 | 0.0810/59.6 | 0.0680/56.4 | 0.0620/54.6 | 0.0580/53.4 | 0.0560/52.5 | 0.0540/51.7 | 0.0520/51.0 |
CO | 0.0052/3.8 | 0.0054/4.5 | 0.0053/4.7 | 0.0053/4.9 | 0.0052/4.9 | 0.0052/5.0 | 0.0052/5.1 |
CH4 | 0.0059/4.3 | 0.0078/6.5 | 0.0088/7.8 | 0.0095/8.7 | 0.0100/9.4 | 0.0104/10.0 | 0.0107/10.5 |
Влияние температуры на состав синтез-газа
Так как при изменении давления перегретого водяного пара при постоянной температуре был найден оптимум (максимальное содержание CO + H2) по давлению, равный 0.5 МПа для конкретных условий моделирования, то именно это давление принято в качестве неизменного параметра при варьировании температуры перегретого водяного пара. Результаты влияния температуры пара на состав синтез-газа при постоянном давлении представлены в табл. 3 и 4.
Таблица 3.
Массовый расход G, кг/с (в числителе), и массовая доля Gx, % (в знаменателе), компонентов сухого синтез-газа после второй камеры газогенератора при постоянном давлении и различной температуре
Компонент | G/Gx при t, °С | ||||
---|---|---|---|---|---|
750 | 800 | 850 | 900 | 965 | |
CO2 | 1.570/81.91 | 1.620/81.97 | 1.660/81.81 | 1.690/81.43 | 1.710/80.62 |
H2 | 0.096/5.02 | 0.108/5.44 | 0.116/5.74 | 0.125/6.05 | 0.136/6.41 |
CO | 0.047/2.47 | 0.067/3.38 | 0.086/4.26 | 0.111/5.37 | 0.150/7.06 |
CH4 | 0.203/10.6 | 0.183/9.22 | 0.166/8.19 | 0.148/7.14 | 0.126/5.92 |
Таблица 4.
Мольный расход V, кмоль/с (в числителе), и мольная доля Vx, % (в знаменателе), компонентов сухого синтез-газа после второй камеры газогенератора при постоянном давлении и различной температуре
Компонент | V/Vx при t, °С | ||||
---|---|---|---|---|---|
750 | 800 | 850 | 900 | 965 | |
CO2 | 0.097/36.49 | 0.104/35.45 | 0.109/34.61 | 0.114/33.7 | 0.12/32.53 |
H2 | 0.048/48.82 | 0.053/51.32 | 0.058/53.06 | 0.062/54.69 | 0.068/56.45 |
CO | 0.0017/1.73 | 0.0024/2.29 | 0.0031/2.83 | 0.004/3.49 | 0.0054/4.48 |
CH4 | 0.0127/12.95 | 0.0114/10.94 | 0.0103/9.95 | 0.009/8.11 | 0.008/6.55 |
ВЕРИФИКАЦИЯ РЕЗУЛЬТАТОВ МОДЕЛИРОВАНИЯ
Для подтверждения достоверности результатов математического моделирования состава синтез-газа после второй камеры газогенератора (взаимодействие коксового остатка и перегретого водяного пара) их сравнивали с собственными экспериментальными данными, а также литературными данными других авторов.
В ранее проведенных экспериментальных исследованиях (методика приведена в [14]) получены результаты по паровой бескислородной газификации смеси древесных опилок при атмосферном давлении и температуре t2 в слое газифицируемого материала около 845°С (кривая 1 на рис. 3). Смесь древесных опилок имеет следующие характеристики, %:
Влажность W ar .............................................. 5.09 |
Зольность Ad ..................................................0.27 |
Выход летучих веществ V d ..........................77.79 |
Содержание, %: |
азота Nd ..................................................0.16 |
углерода Cd .......................................... 46.69 |
водорода Hd ...........................................5.76 |
Рис. 3.
Зависимости от времени и температуры объемной доли компонентов газовой смеси VV, измеренные поточным газоанализатором, при газификации коксового остатка смеси древесных опилок (1 –при t2 = 845°С)
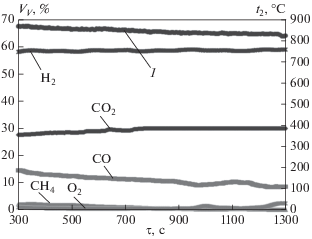
Полученные параметры удовлетворительно описывают содержание углекислого газа, метана, CO и водорода, что согласуется с результатами математического моделирования (интерполяция данных табл. 2 и 4). В итогах эксперимента, как и в результатах моделирования, можно отметить высокое содержание CO2 в объеме получаемого газа. Такое содержание CO2 в синтез-газе характерно в целом для биомассы [15].
Было проведено сравнение состава синтез-газа, полученного в результате математического моделирования, с литературными данными, в частности с [13]. В этой работе приведен обзор по паровой газификации биомассы в двухстадийных газификаторах и показаны типичные составы получаемого в них газа [13, рис. 11 ].
Также можно отметить, что результаты работы [13] удовлетворительно согласуются не только с экспериментальными данными автора (см. рис. 3), но и с итогами математического моделирования (см. табл. 2, 4) по определенным элементам. Различия в составе газа по отдельным компонентам связаны с тем, что в двухстадийных газогенераторах в первой камере для получения нелетучего углерода используется воздух, тогда как в предлагаемой концепции ЭНТЕС предварительная газификация осуществляется перегретым паром. Таким образом, имеется различие в способе подготовки газифицируемого материала.
В работе [16] на образцах белой бумаги и желтой сосновой щепы проведены исследования паровой бескислородной газификации не только с внутренним, но и с внешним подводом тепла. Состав синтез-газа, полученного при 900–950°С в результате этих экспериментов, представлен на рис. 4. Эти данные также удовлетворительно согласуются с результатами математического моделирования, особенно по содержанию H2 и CO2.
Таким образом, можно отметить, что результаты математического моделирования в Aspen Plus для буковых опилок при заданных условиях моделирования удовлетворительно согласуются с результатами экспериментальных исследований и могут быть использованы, например, для технико-экономической оценки стоимости синтез-газа и получаемых из него различных веществ. При сравнении результатов моделирования с собственными экспериментальными данными автора (по методике исследований, представленной в [14]), а также с литературными данными можно отметить расхождение по концентрации компонентов не более 15% (в собственных экспериментальных исследованиях автора погрешность измерения концентрации компонентов в составе синтез-газа составила не более 5%).
ОБСУЖДЕНИЕ РЕЗУЛЬТАТОВ
По данным табл. 1–4 можно сделать следующие выводы.
Повышение давления благоприятно сказывается на содержании метана в общем объеме газовой смеси. При этом суммарно уменьшается содержание в ней компонентов CO и H2, которые необходимы для производства, например, синтетических жидких топлив (СЖТ). По результатам моделирования для принятых условий существует некоторый оптимум по давлению, составляющий 0.5 МПа, при котором наблюдается максимальное содержание целевых компонентов в синтез-газе, а значит, и количество СЖТ, получаемых из него при таком давлении, будет максимальное. Повышение давления позволяет снизить общее содержание углекислого газа в составе синтез-газа, однако это снижение не будет значительным. Для использованного образца биомассы при повышении давления образование CO2 снижается примерно на 5.5%.
Концентрация метана при увеличении давления существенно возрастает – более чем в 2 раза в объеме получаемой смеси. Наличие большого количества метана при повышении давления в ЭНТЕС позволит значительно увеличить выработку электрической и тепловой энергии либо сэкономить исходное топливо. Достигнуть этого можно сжиганием горючей смеси, состоящей в основном из метана. Например, при давлении перегретого пара 3 МПа теплота сгорания метана при известном его расходе (см. табл. 1, 2) может составлять
где qm – удельная теплота сгорания метана, МДж/кг.При газификации биомассы в среде перегретого водяного пара и разделении процесса газификации на две зоны (предварительная и основная) в составе синтез-газа после второй зоны отмечается довольно высокое содержание CO2 и относительное низкое содержание CO. Так как в процессе синтеза химических веществ основные строительные элементы – это CO и Н2, то даже при условии большого количества водорода в газовой смеси (см. табл. 1–4) более значимую роль играет наличие CO в составе синтез-газа. При этом изменение давления перегретого водяного пара весьма незначительно влияет на изменение концентрации CO2 в составе синтез-газа. Поэтому употребление биомассы для генерации синтез-газа и использования его в нетопливной сфере может иметь существенные ограничения.
Температура перегретого водяного пара также оказывает существенное влияние на состав синтез-газа. Это особенно заметно для его горючих компонентов – CO, H2, CH4.
При повышении температуры в исследованном интервале наблюдается значительное возрастание количества целевых компонентов в объеме газовой смеси. Это позволяет, например, существенно увеличить либо образование СЖТ в процессе Фишера – Тропша, либо получение водорода.
Повышение температуры благоприятно сказывается на понижении концентрации CO2 в объеме газовой смеси (см. табл. 3, 4). При этом, как и при повышении давления, снижение образования CO2 не столь значительно.
Вследствие роста количества целевых компонентов в составе синтез-газа (CO + H2) снижается содержание метана. Это, в свою очередь, может сильно влиять на выработку тепловой и электрической энергии. При более низкой температуре и более высоком давлении в синтез-газе содержится большее количество метана, чем при высокой температуре, что может придать ЭНТЕС бо́льшую энергетическую эффективность при условии, что весь синтез-газ будет, например, сожжен в газовой турбине или котельном агрегате с получением перегретого пара для газификации. Тогда возможно достижение значительно более высоких показателей энергетического использования исходного газифицируемого материала и, соответственно, снижение выбросов вредных веществ в окружающую среду, в том числе количества CO2 на единицу вырабатываемой тепловой и электрической энергии.
В целом при изменении давления и температуры перегретого водяного пара, используемого для газификации нелетучего углерода с минеральной частью, можно условно выделить два режима газификации. Они могут определять целевое применение синтез-газа по энергетическому и химическому направлениям.
Энергетическое направление. В газогенераторе необходимо обеспечить повышенное давление и пониженную температуру для получения наиболее калорийного газа, в основном благодаря повышенному содержанию метана в объеме газовой смеси. В отдельных режимах (по результатам моделирования) после выделения водорода из синтез-газа концентрация метана в объеме газовой смеси может достигать почти 25% (табл. 5).
Таблица 5.
Состав сухого синтез-газа после выделения H2 при давлении 200 кПа и температуре 697°С в газогенераторе
Компонент | G, кг/с | Gx, % | V, кмоль/с | Vx, % |
---|---|---|---|---|
CO2 | 1.63 | 87.0 | 0.037 | 72.2 |
CO | 0.033 | 1.8 | 0.001 | 2.3 |
CH4 | 0.21 | 11.2 | 0.013 | 25.5 |
Химическое направление. В газогенераторе необходимо поддерживать давление близкое к атмосферному при максимально возможной температуре. Тогда в синтез-газе будет наибольшее содержание CO и H2.
При этом следует отметить как минимум два фактора, ограничивающих выработку синтез-газа как в том, так и в другом направлении. Во-первых, плавкостные характеристики золы, которые определяют максимальную температуру в газогенераторе. При этом температура перегретого пара зависит также от материала труб и условий теплообмена между дымовыми газами и перегретым паром. Во-вторых, давление перегретого водяного пара. По условиям прочности труб пароперегревателя оно не должно превышать 3 МПа, тогда как нижнее его значение должно быть таким, чтобы обеспечивалась возможность транспортировать синтез-газ по трубам в пределах ЭНТЕС и проводить с ним различные технологические операции. По объективным причинам давление синтез-газа не может быть равно атмосферному давлению, оно всегда должно его превышать, чтобы максимально снизить затраты на установку компрессорного оборудования, которое должно иметь взрывобезопасное исполнение из-за транспортируемой среды. Кроме того, повышение давления позволяет снизить стоимость синтез-газа благодаря сокращению капитальных и эксплуатационных издержек.
ВЫВОДЫ
1. Разработанная концепция полигенерации с реализацией паровой бескислородной газификации биомассы позволяет получать синтез-газ с различным содержанием CO, H2, CO2 и CH4. Чтобы синтез-газ имел требуемый состав, можно изменять температуру и давление перегретого водяного пара, используемого при его получении.
2. Изменяя температуру и давление перегретого водяного пара в процессе газификации, можно менять характеристики синтез-газа в зависимости от его целевого назначения. Можно выделить энергетическое и химическое направления использования синтез-газа, получаемого в процессе паровой бескислородной газификации в условиях полигенерации.
Список литературы
Potential for hydrogen and power-to-liquid in a low-carbon EU energy system using cost optimization / H. Blanco, W. Nijs, J. Ruf, A. Faaij // Appl. Energy. 2018. V. 232. P. 617–639. https://doi.org/10.1016/j.apenergy.2018.09.216
Direct conversion of syngas to aromatics: A review of recent studies / X. Yang, X. Su, D. Chen, T. Zhang, Y. Huang // Chin. J. Catal. Sci. Press. 2020. V. 41. Is. 4. P. 561–573. https://doi.org/10.1016/S1872-2067(19)63346-2
Coal phase-out in Germany – implications and policies for affected regions / P.-Y. Oei, H. Hermann, P. Herpich, O. Holtemöller, B. Lünenbürger, C. Schult // Energy. 2020. V. 196. P. 117004. https://doi.org/10.1016/j.energy.2020.117004
Keles D., Yilmaz H.Ü. Decarbonisation through coal phase-out in Germany and Europe – impact on emissions, electricity prices and power production // Energy Policy. 2020. V. 141. P. 111472. https://doi.org/10.1016/j.enpol.2020.111472
Analysis of biomass polygeneration integrated energy system based on a mixed-integer nonlinear programming optimization method / N. Wu, X. Zhan, X. Zhu, Z. Zhang, J. Lin, S. Xie, C. Menga, L. Cao, X. Wang, N. Shah et al. // J. Clean. Prod. 2020. V. 271. P. 122761. https://doi.org/10.1016/j.jclepro.2020.122761
Мановян А.К. Технология переработки природных энергоносителей. М.: Химия; КолосС, 2004.
Паровая бескислородная газификация в условиях полигенерации / С.А. Шевырёв, П.А. Стрижак, Р.-Ю. Дитрих, А.Р. Богомолов // Изв. ТПУ. Инжиниринг георесурсов. 2021. Т. 332. № 2. С. 44–58. https://doi.org/10.18799/24131830/2021/2/3042
Shevyrev S.A., Bogomolov A.R. Production of superheated steam for oxygen-free steam gasification at thermal power plant // AIP Conf. Proc. American Institute of Physics Inc. 2019. V. 2135. Is. 1. P. 020053. https://doi.org/10.1063/1.5120690
ГОСТ 5632-2014. Нержавеющие стали и сплавы коррозионно-стойкие, жаростойкие и жаропрочные. Марки (с изменением № 1). Межгосударственный стандарт. Введ. 01.01.2015. М.: Стандартинформ, 2016.
Kartal F., Özveren U. A deep learning approach for prediction of syngas lower heating value from CFB gasifier in Aspen plus® // Energy. 2020. V. 209. P. 118457. https://doi.org/10.1016/j.energy.2020.118457
ГОСТ 27313-2015. Топливо твердое минеральное. Обозначение показателей качества и формулы пересчета результатов анализа на различные состояния топлива (переизд. с поправкой). Межгосударственный стандарт. Введ. 01.04.2017. М.: Стандартинформ, 2016.
ГОСТ 17070-87. Угли. Термины и определения (с поправкой). Межгосударственный стандарт. Введ. 01.07.1989. М.: Изд-во стандартов, 2003.
Karl J., Pröll T. Steam gasification of biomass in dual fluidized bed gasifiers: A review // Renewable and Sustainable Energy Rev. 2018. V. 98. P. 64–78. https://doi.org/10.1016/j.rser.2018.09.010
Богомолов А.Р., Шевырёв С.А., Алексеев М.В. Перспективы высокотемпературной газификации угля и шлама // Теплоэнергетика. 2013. № 2. С. 77–80.
Gasification of biowaste: a critical review and outlooks / J. Watson, Y. Zhang, B. Si, W.-T. Chen, R. de Souza // Renewable Sustainable Energy Rev. 2018. V. 83. P. 1–17. https://doi.org/10.1016 / j.rser.2017.10.003
Hydrogen production by high-temperature steam gasification of biomass and coal / S.N. Kriengsak, R. Buczynski, J. Gmurczyk, A. K. Gupta // J. Environ. Eng. Sci. 2009. V. 26. № 4. P. 739–744. https://doi.org/10.1089/ees.2008.0246
Дополнительные материалы отсутствуют.
Инструменты
Теплоэнергетика