Теплоэнергетика, 2022, № 3, стр. 50-62
Расчетно-экспериментальное исследование работы контурной тепловой трубы в стационарном режиме
А. Е. Белов a, А. А. Великанов a, Д. Н. Ильмов a, *, О. А. Нагорнова a, В. В. Соболев a, Н. И. Филатов a
a Государственный научный центр “Центр Келдыша”
125438 Москва, Онежская ул., д. 8, Россия
* E-mail: ilmovdn@mail.ru
Поступила в редакцию 15.04.2021
После доработки 25.05.2021
Принята к публикации 26.05.2021
- EDN: DTWDBX
- DOI: 10.1134/S004036362203002X
Аннотация
Контурные тепловые трубы обладают всеми достоинствами классических тепловых труб, менее подвержены влиянию силы тяжести и имеют более высокие теплопередающие характеристики. Их удобно применять в стесненных условиях эксплуатации. В части поддержания температуры они обладают саморегулированием, предотвращая существенное снижение температуры посадочного места тепловыделяющего оборудования при уменьшении тепловой нагрузки. Миниатюрные контурные тепловые трубы способны заменить обычные тепловые трубы на перспективных космических аппаратах, заметно повысив при этом возможности по отводу тепловой мощности и понизив их массу. Для разработки эффективных методов проектирования контурных тепловых труб требуется создание физической и математической моделей сопряженных процессов переноса тепла и массы в устройстве. В настоящей работе предлагается методика математического расчета функционирования контурной тепловой трубы в стационарном режиме. По этой методике предполагается вести расчет гидравлических сопротивлений движению жидкости и пара в элементах устройства. Теплопередающая способность определяется возможностями капиллярной структуры проталкивать теплоноситель вопреки гидравлическим сопротивлениям. Во второй части задачи проводится расчет теплового состояния всех элементов, при этом используется подход, основанный на учете баланса тепловых потоков. Модель учитывает возможный перегрев пара в паропроводе. Теплофизические свойства теплоносителя вычисляются на каждом транспортном участке в зависимости от местной температуры. Расчеты достаточно точно моделируют работу устройства и совпадают с результатами испытаний экспериментальной контурной тепловой трубы в различных режимах при температуре испарителя от ‒35 до +25°С. Испытания проводились при комнатной температуре и в климатической камере, когда температура радиатора почти совпадала с температурой среды. Максимальная погрешность при расчете температуры испарителя по сравнению с экспериментально измеренной в различных режимах составила менее 5°С, средняя погрешность – менее 3°С.
Необходимость увеличения сроков активного функционирования космических аппаратов (КА) до 10 лет и более, уменьшения массы систем обеспечения теплового режима (СОТР), повышения надежности и экономической рентабельности потребовала использования новых принципов построения СОТР КА в негерметичном исполнении с применением тепловых труб (ТТ). Прокачка теплоносителя в них осуществляется благодаря капиллярным силам. Классические тепловые трубы не потребляют энергию, имеют значительный срок службы, обладают простой и технологичной конструкцией, но их теплопередающие характеристики относительно низки [1]. В наземных условиях их функционирование существенно зависит от ориентации в пространстве. Более перспективными для использования в системах теплового регулирования не только космических аппаратов, но и наземных устройств являются контурные тепловые трубы (КТТ), которые обладают всеми преимуществами обычных тепловых труб, но имеют более высокие теплопередающие характеристики, мало зависящие от пространственной ориентации в наземных условиях. Кроме того, данные устройства легко адаптировать к различным условиям эксплуатации благодаря следующим базовым конструктивным принципам [2]:
наличие мелкопористых капиллярных структур, расположенных непосредственно в зоне теплоподвода для прокачки теплоносителя;
организация зоны испарения и конденсации с учетом особенностей теплообмена в стесненных условиях;
соединение испарителя с конденсатором гибкими трубками, предназначенными для раздельного переноса теплоносителя в паровой и жидкой фазах.
В области поддержания температуры КТТ имеют способность саморегулирования. При снижении тепловой нагрузки происходит заполнение жидкостью трубопровода конденсатора и термическое сопротивление контура возрастает, предотвращая ощутимое снижение температуры посадочного места тепловыделяющего оборудования. При повышении тепловой нагрузки конденсатор освобождается от жидкости, обеспечивая эффективную теплопередачу. Таким образом, миниатюрные контурные тепловые трубы способны заменить обычные и газорегулируемые ТТ, при этом значительно повышаются возможности по отводимой мощности и снижается масса КА [3‒5].
К примеру, для обеспечения теплового режима малого КА “Юбилейный-2” были разработаны две дублирующие системы терморегулирования с газорегулируемой тепловой трубой и миниатюрной контурной тепловой трубой [6]. Масса обычной ТТ составляла 850 г, а масса КТТ ‒ около 450 г. При этом КТТ была способна передать намного бо́льшую тепловую нагрузку: более 60 Вт, тогда как газорегулируемая тепловая труба ‒ только 15 Вт. Летно-конструкторские испытания и эксплуатация изделий показали надежную работу этих элементов системы терморегулирования.
Характеристики различных КТТ существенно зависят от конструкции их частей, передаваемой мощности и др. Одной из наиболее важных задач проектирования является определение минимальных массогабаритных характеристик. Это подразумевает оптимизацию основных частей КТТ, соответствующую конкретному техническому заданию. Для разработки эффективных методов проектирования КТТ требуется создание физической и математической моделей сопряженных процессов переноса тепла и массы в устройстве.
На сегодняшний день широко представлены расчеты функционирования отдельных элементов КТТ, разработаны приближенные методы предсказания основных теплопередающих характеристик и работы КТТ в целом. Методика гидродинамического анализа разрабатывалась для оценки предельной мощности обычных тепловых труб и была адаптирована для КТТ [2, 7‒11]. Перепад давления в паровом тракте может значительно ограничить максимальную тепловую нагрузку КТТ. В работах [7, 8, 12‒15] представлен анализ гидродинамики парового потока, в [16] на основе анализа потерь давления на различных участках ‒ подробное исследование максимальной теплопередающей способности аммиачной контурной трубы.
В работах [17‒19] проводится численный расчет полей температур и скоростей в цилиндрическом испарителе. Для этого рассматривается замкнутая система уравнений переноса импульса, тепла и сохранения массы, которые затем решаются конечно-разностными методами. Выполненные исследования позволили оценить оптимальные размеры компенсационной полости и испарителя и качественно описать теплообмен в слое фитиля между испаряющей и впитывающей поверхностями. Однако из-за разнообразия конструкций испарителей требуется построение специальной конечно-разностной схемы для каждой задачи. Такая работа является весьма трудоемкой. Предложенные в [1] методики полезны для качественного понимания процессов тепло- и массопередачи в испарителе КТТ.
В ряде работ продемонстрированы модели КТТ, выполненные с помощью коммерческого программного пакета SINDA/FLUENT [20, 21], при моделировании с помощью которого реальное устройство заменяется взаимосвязанными тепловой и гидравлической схемами. Однако универсальность такого пакета снижает его гибкость, необходимую для решения задач, требующих более детального анализа процессов тепло- и массообмена [1].
Несмотря на довольно большое количество работ, посвященных контурным тепловым трубам, анализ литературных источников показывает, что универсальный инструмент для их расчета не существует. Это связано с многообразием конструкций устройства и отдельных его частей, а также со сложностью описания процессов испарения и конденсации.
Физико-математическая модель КТТ, представленная в данной работе, основана на учете баланса тепловых потоков аналогично работам [1, 22] и предназначена для расчета в стационарном режиме. Это упрощает вычисления и позволяет сразу получить параметры КТТ в установившемся режиме. Модель учитывает возможный перегрев пара в паропроводе. Теплофизические свойства теплоносителя вычисляются на каждом транспортном участке в зависимости от местной температуры.
ФИЗИКО-МАТЕМАТИЧЕСКАЯ МОДЕЛЬ КТТ
Задачу расчета КТТ можно разделить на две части. Одна часть, гидравлическая, представляет собой расчет гидравлических сопротивлений движению жидкости и пара в элементах КТТ. Теплопередающая способность определяется возможностями капиллярной структуры проталкивать теплоноситель вопреки гидравлическим сопротивлениям. Во второй части задачи проводится расчет теплового состояния всех элементов КТТ для конкретного режима работы, при этом используются результаты гидравлической части.
Капиллярный напор $\Delta {{р}_{{сap}}},$ создаваемый менисками пористой структуры испарителя, должен компенсировать потери давления при движении теплоносителя на каждом транспортном участке, а также гидростатическое давление столба жидкости в условиях гравитации. Контурная тепловая труба будет переносить тепло, если капиллярный напор будет больше суммы потерь давления $\sum\nolimits_i {\Delta {{р}_{i}}} $ на всех транспортных участках КТТ или равен ей. Этот физический принцип математически можно сформулировать в виде
В [7] рассматривается наглядный пример создания капиллярного напора в обычной тепловой трубе. При смачивании поверхности жидкостью образуется вогнутый мениск. Давление на вогнутой поверхности радиусом кривизны $R$ меньше, чем давление на плоской поверхности, на ${{2\sigma } \mathord{\left/ {\vphantom {{2\sigma } R}} \right. \kern-0em} R}$ (здесь σ ‒ поверхностное натяжение). В области испарения радиус кривизны мениска ${{R}_{{\,e}}}$ больше, чем в зоне конденсации ${{R}_{c}},$ и давление в зоне испарения будет меньше, чем в зоне конденсации, на
В предельном случае максимальный капиллярный напор будет достигаться, когда ${{R}_{{\,c}}} \to \infty ,$ а ${{R}_{{\,e}}} \to r$ [здесь r – радиус капилляра (характерный радиус капиллярной структуры)]. Следовательно, максимальный капиллярный напор определяется формулой
Приведенные выше рассуждения полностью справедливы для фитиля КТТ.
Гидравлические сопротивления зависят от расхода теплоносителя G, который, в свою очередь, связан с передаваемой тепловой мощностью Q соотношением
где $\psi $ – скрытая теплота парообразования теплоносителя.Выражение для суммарных потерь давления на всех транспортных участках в развернутой форме можно представить в виде
(4)
$\begin{gathered} \sum\limits_i {\Delta {{р}_{i}}} = \Delta {{р}_{{vc}}} + \Delta {{р}_{{vl}}} + \\ + \,\,\Delta {{р}_{{ll}}} + \Delta {{р}_{g}} + \Delta {{р}_{{wick}}} + \Delta {{р}_{{cond}}}, \\ \end{gathered} $Далее представлены формулы для расчета составляющих Δрi, рекомендованные в [23].
Потери давления в паропроводе, конденсатопроводе и конденсаторе Δр можно рассчитать как потери давления при движении среды в круглой трубе. Они имеют две составляющие: первая $\Delta {{р}^{\mu }}$ учитывает действие вязкостных сил, вторая – это локальные (инерционные) сопротивления на изгибах трубки $\Delta {{р}^{{iner}}}$;
Вязкостные потери давления зависят от режима течения среды, который, в свою очередь, определяется значением критерия Рейнольдса:
где d – диаметр канала; $\mu $ ‒ динамический коэффициент вязкости.При Re < 2300 течение ламинарное, в случае Re ≥ 5000 наблюдается развитое турбулентное течение, при 2300 < Re < 5000 – переходной режим течения в трубе.
Формула для вычисления вязкостных потерь давления имеет вид
где $\xi $(Re) – коэффициент трения; $\rho $ ‒ плотность; $u = \frac{G}{{\rho S}}$ ‒ среднерасходная скорость; S, l – площадь проходного сечения и длина канала.При Re $ \leqslant $ 2300
при Re > 5000
(8)
$\xi = {{0.3164} \mathord{\left/ {\vphantom {{0.3164} {{{{\operatorname{Re} }}^{{0.25}}}}}} \right. \kern-0em} {{{{\operatorname{Re} }}^{{0.25}}}}};$при 2300 ≤ Re ≤ 5000
Для локального сопротивления на изгибах трубки:
где R0 – радиус поворота трубки; δ0 – суммарный угол, град, всех поворотов паропровода [при различных радиусах поворота паропровода формулу (10) необходимо использовать для определения каждого поворота];(11)
$\begin{gathered} {{\xi }_{{tur}}} = \frac{{10.4}}{{{{{\operatorname{Re} }}^{{0.56}}}}}{{\left( {\frac{d}{{2{{R}_{0}}}}} \right)}^{{0.255}}}\,\,\, \\ {\text{при}}\,\,\,600 \leqslant \operatorname{Re} \sqrt {\frac{d}{{2{{R}_{0}}}}} \leqslant 1400; \\ \end{gathered} $Потери давления в пароотводных каналах зоны испарения Δpvc также складываются из двух составляющих: вязкостной (потери на трение) $\Delta р_{{vc}}^{\mu }$ и инерционной (потери на местных сопротивлениях) $\Delta р_{{vc}}^{{iner}}$:
В пароотводных каналах обычно реализуется ламинарный режим течения, при котором потери на трение принимают равными
(13)
$\Delta р_{{vc}}^{\mu } = \frac{{{{\mu }_{v}}G{{l}_{{vc}}}}}{{2{{n}_{{vc}}}d_{{evc}}^{2}{{\rho }_{v}}{{S}_{{vc}}}}},$Потери на местных сопротивлениях (с учетом того, что коэффициент гидравлического сопротивления выхода пароотводного канала равен 1.0) определяют по формуле
(14)
$\Delta р_{{vc}}^{{iner}} = \frac{{8{{G}^{2}}}}{{n_{{vc}}^{2}B_{{vc}}^{2}d_{{evc}}^{2}{{\rho }_{v}}}}.$Потери давления в капиллярной структуре рассчитывают в приближении Дарси, и формула для цилиндрических испарителей приобретает вид [7]
(15)
$\Delta {{р}_{{wick}}} = \frac{{{{\mu }_{l}}G\ln \left( {\frac{{{{d}_{{ext}}}}}{{{{d}_{{int}}}}}} \right)}}{{2\pi {{l}_{{wick}}}K{{\rho }_{l}}}},$Коэффициент проницаемости спеченных металлов хорошо аппроксимируется уравнением Блейка ‒ Козени [24] для плотно упакованных сферических тел:
где ${\text{П}}$ ‒ пористость материала (отношение объема пустого пространства в фитиле, к его полному объему).Если принять $r \approx 6.5 \times {{10}^{{ - 6}}}$ м, ${\text{П}} \approx 0.45,$ тогда $K \approx 75 \times {{10}^{{ - 14}}}$ м2.
Потери давления в капиллярной структуре влияют на предельную проводимость КТТ, но не влияют на ее функциональные характеристики в режимах до достижения предельной проводимости.
В установившихся режимах сумма всех тепловых потоков равна нулю для каждого элемента КТТ. Уравнения теплового баланса для корпусов испарителя и компенсационной полости (КП), фитиля и жидкости в компенсационной полости имеют следующий вид (поясняются на рис. 1):
где $N$ ‒ тепловая нагрузка на испаритель от приборов; ${{Q}_{{ew}}}$ ‒ тепло, прошедшее через стенку испарителя; ${{Q}_{{ec}}}$ ‒ тепло, ушедшее от корпуса испарителя в корпус компенсационной полости теплопроводностью; ${{Q}_{{ea}}}$ ‒ тепловой поток в окружающую среду; $q$ ‒ управляющее тепловое воздействие; ${{Q}_{{cl}}}$ ‒ тепло, получаемое жидкостью от корпуса КП; ${{Q}_{{ca}}}$ ‒ тепло, сбрасываемое в окружающую среду; ${{Q}_{s}}$ ‒ тепло, затрачиваемое на испарение пара; ${{Q}_{{wick\,l}}}$ ‒ тепло, получаемое жидкостью от фитиля; ${{Q}_{{ov}}}$ ‒ тепло на нагрев жидкости, проходящей через фитиль; Qsub – тепло, необходимое для подогрева переохлажденной жидкости до температуры насыщения в компенсационной полости.Используемые в уравнениях (17)–(20) величины можно определить по приведенным далее формулам:
где $A = \frac{{2\pi \lambda {{L}_{{wick}}}}}{{\ln \left( {{{{{D}_{e}}} \mathord{\left/ {\vphantom {{{{D}_{e}}} {{{d}_{e}}}}} \right. \kern-0em} {{{d}_{e}}}}} \right)}};$ $\lambda $ = 15 Вт/(м ∙ K) ‒ теплопроводность материала испарителя, компенсационной полости, трубок паропровода, конденсатопровода и конденсатора (сталь 12Х18Н10Т); ${{L}_{{wick}}}$ ‒ длина фитиля (${{L}_{{wick}}}$ = 70 мм); ${{D}_{e}},$ ${{d}_{e}}$ ‒ наружный и внутренний диаметр испарителя (${{D}_{e}}$ = 10.0 мм, ${{d}_{e}}$ = = 9.4 мм); tе ‒ температура корпуса испарителя; twick ‒ температура поверхности фитиля; где $B = \lambda \frac{{{{S}_{{ec}}}}}{{{{L}_{{ec}}}}};$ ${{S}_{{ec}}} = \frac{\pi }{4}\left( {D_{{cc}}^{2} - d_{{ec}}^{2}} \right)$ ‒ площадь сечения “по металлу” между компенсационной полостью и испарителем; Dcc, dec ‒ диаметр компенсационной полости и испарителя ($D_{{cc}}^{{}}$ = 12.0 мм, ${{d}_{{ec}}}$ = 8.4 мм), соединение которых показано на рис. 2; ${{L}_{{ec}}}$ ‒ расстояние между компенсационной полостью и испарителем (${{L}_{{ec}}}$ = 4 мм); tсс ‒ температура корпуса КП; где $C = \frac{1}{{\frac{{{{\delta }_{{is}}}}}{{{{\lambda }_{{is}}}{{F}_{{ea}}}}} + \frac{1}{{{{\alpha }_{a}}{{F}_{{ae}}}}}}};$ ${{\delta }_{{is}}}$ – толщина слоя теплоизоляции (к-флекс); ${{\lambda }_{{is}}} = f\left( {\frac{{{{t}_{a}}}}{2} + \frac{{{{t}_{е}}}}{2}} \right)$ ‒ теплопроводность теплоизоляции [${{\lambda }_{{is}}} \approx $0.03 Вт/(м ∙ К)]; ${{F}_{{ea}}} = {{({{F}_{e}} + {{F}_{{ae}}})} \mathord{\left/ {\vphantom {{({{F}_{e}} + {{F}_{{ae}}})} 2}} \right. \kern-0em} 2};$ ${{F}_{e}},$ ${{F}_{{ae}}}$ ‒ площадь поверхности испарителя и наружной поверхности изолированного испарителя; ${{\alpha }_{a}}$ – коэффициент теплоотдачи в окружающую среду [подбирается в диапазоне 5‒15 Вт/(м2 ∙ K) как эмпирический коэффициент, отражающий “силу тепловой связи” с окружающей средой, в представленных далее расчетах ${{\alpha }_{a}}$ = 10 Вт/(м2 ∙ K)]; tа ‒ температура окружающей среды; где $E = 3.66{{\lambda }_{l}}\pi {{L}_{{cc}}};$ ${{\lambda }_{l}} = f\left( {{{t}_{l}}} \right)$ ‒ теплопроводность жидкости; ${{L}_{{cc}}}$ = 60 мм – длина КП; tl ‒ температура жидкости в КП; где D вычисляется аналогично С; tс ‒ температура конденсации; где ${{\alpha }_{e}}$ ‒ коэффициент теплоотдачи при испарении (зависит от возможностей распространения тепла от гранул пористой структуры фитиля к поверхностям менисков жидкости в порах); ${{F}_{{ew}}}$ ‒ площадь внутренней поверхности испарителя; tv1 ‒ температура пара; где ${{\lambda }_{l}} = f\left( {{{t}_{{wick}}}} \right)$ ‒ теплопроводность жидкости при температуре поверхности фитиля [${{\lambda }_{l}}$ = = 0.286 Вт/(м ∙ K) при 20°С, при $r \approx 6.5$ мкм ${{\alpha }_{e}}$ ≈ ≈ 39 600 Вт/(м2 ∙ K)]. В последующем расчете принята зависимость (27);(28)
${{Q}_{{wick\,l}}} = 2\pi {{\lambda }_{{wick}}}{{L}_{{wick}}}\frac{{{{t}_{{wick}}} - {{t}_{l}}}}{{{\text{ln}}\frac{{{{D}_{{ext}}}}}{{{{D}_{{int}}}}}}},$В пористых металлах основное термическое сопротивление теплопроводности сосредоточено в зоне контакта частиц, где наблюдаются наименьшая площадь поперечного сечения и наибольшая неоднородность в составе металла. Качество теплового контакта определяется многими практически невоспроизводимыми технологическими факторами – формой и размером исходных частиц, чистотой и составом материала, давлением прессования, температурой и временем спекания.
В работе [25] представлены обзор моделей теплопроводности пористых металлов и экспериментальные данные разных авторов. На основе обработки данных по различным пористым материалам с различной структурой в широком диапазоне пористости 0.05 < П < 0.80 многими авторами рекомендована полуэмпирическая зависимость
(29)
${{\lambda }_{{wick}}} = {{\lambda }_{{\text{м}}}}\frac{{1 - {\text{П}}}}{{1 + 1{\kern 1pt} 1{{{\text{П}}}^{2}}}},$Тепло, необходимое для нагрева жидкости, проходящей через фитиль:
где ${{c}_{{wick\,l}}}$ ‒ теплоемкость жидкости при температуре $\frac{{{{t}_{{wick}}}}}{2} + \frac{{{{t}_{l}}}}{2}.$Тепло, необходимое для подогрева переохлажденной жидкости до температуры насыщения в компенсационной полости:
где ${{c}_{{in\,l}}}$ ‒ теплоемкость жидкости при температуре $\frac{{{{t}_{{in}}}}}{2} + \frac{{{{t}_{l}}}}{2};$ tin ‒ температура жидкости на входе в КП.Из формул (23), (24) можно исключить ${{t}_{e}}$ и ${{t}_{{cc}}},$ а из (26) ‒ ${{t}_{{wick}}}.$ Тогда уравнения теплового баланса будут выражать зависимость ${{t}_{l}}$ и ${{t}_{{v1}}}$ от $N$ и $q,$ а также от $Q$ и ${{t}_{{in}}}.$ Кроме того, температуры пара и жидкости связаны между собой через температуру конденсатора.
Далее приводится расчет конденсатора, который представляет собой змеевик из стальной трубки 2.0 × 0.25 мм, впаянный в алюминиевую пластину 165 × 96 × 3 мм (рис. 3). К пластине прикреплен прямоугольный П-образный жидкостный теплообменный аппарат, снаружи установлена теплоизоляция. Для охлаждения используется полиметилсиликоновая жидкость ПМС-1.5. В силу массивности конструкции, высокой теплопроводности алюминия и сложной формы всего конденсатора принимается, что температура его металлических частей однородна и равна ${{t}_{{\text{м}}}}.$
Рис. 3.
Расчетная схема конденсатора. Количество тепла: Qx ‒ отведенное охлаждающей жидкостью; QL ‒ на участке переохлаждения жидкости; Qмa ‒ отведенное от конденсатора в окружающую среду
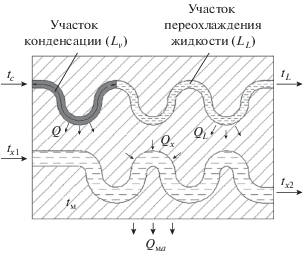
Тепловую эффективность теплообмена с охлаждающей жидкостью вычисляют по формуле
где NTU ‒ количество единиц теплопереноса.Выражение для NTU имеет вид
где αх ‒ коэффициент теплоотдачи; ${{F}_{x}}$ ‒ площадь поверхности теплообмена с охлаждающей жидкостью; ${{G}_{x}},$ ${{c}_{{рx}}}$ ‒ массовый расход и теплоемкость охлаждающей жидкости.Коэффициент теплоотдачи определяют следующим образом:
где ${{\lambda }_{x}}$ ‒ теплопроводность охлаждающей жидкости; dex ‒ эквивалентный диаметр канала теплообменника; Nux ‒ число Нуссельта, которое рассчитывается по формуле для турбулентного течения вязкой жидкости [26]:здесь Re ‒ число Рейнольдса; Pr ‒ число Прандтля.
Число Рейнольдса для охлаждающей жидкости вычисляют по формуле
где ${{S}_{x}}$ ‒ проходная площадь канала теплообменника; ${{\mu }_{x}}$ ‒ динамический коэффициент вязкости.Различием между вязкостью потока в его ядре и на стенке канала пренебрегают.
Аналогично вычисляют тепловую эффективность на участке переохлаждения жидкости ${{\eta }_{l}}$ при ${\text{Nu}} = 3.66,$ если $\operatorname{Re} < 2000,$ при Nu = = $0.023{{\operatorname{Re} }^{{0.8}}}{{\Pr }^{{0.4}}},$ если $\operatorname{Re} \geqslant 2000$ (в проведенных испытаниях образцов КТТ $\operatorname{Re} < < 2000$).
Предполагая, что пар не перегрет и не переохлажден, уравнение теплового баланса для конденсатора можно записать в виде
(33)
${{G}_{x}}{{c}_{x}}\left( {{{t}_{{\text{м}}}} - {{t}_{{x1}}}} \right){{\eta }_{x}} = Q + G{{c}_{l}}({{t}_{c}} - {{t}_{{\text{м}}}}){{\eta }_{l}} + \beta \left( {{{t}_{a}} - {{t}_{{\text{м}}}}} \right),$Из уравнения (33) вычисляют ${{t}_{{\text{м}}}},$ а затем температуру охлаждающей жидкости на выходе из конденсатора tх2 и температуру переохлажденной жидкости ${{t}_{L}},$ предполагая, что $Q$ и ${{t}_{c}}$ известны:
В свою очередь $Q$ и ${{t}_{c}}$ связаны между собой:
где ${{\alpha }_{c}}$ ‒ коэффициент теплоотдачи при конденсации; ${{d}_{{cond}}}$ ‒ диаметр трубки конденсатора; Lc ‒ длина участка конденсации.Согласно предварительным расчетам по методикам, представленным в [27], среднее значение ${{\alpha }_{c}}$ составляет примерно 5000 Вт/(м2 ∙ K); кроме того, изменения ${{\alpha }_{c}}$ в диапазоне от 2500 до 10 000 Вт/(м2 ∙ K) слабо влияют на функциональные параметры устройства, поэтому принято ${{\alpha }_{c}}$ = 5000 Вт/(м2 ∙ K).
Формула (34) показывает, что при уменьшении ${{L}_{c}}$ вследствие выдавливания жидкости из КП температура конденсации ${{t}_{c}}$ растет.
Длину участка переохлаждения жидкости вычисляют по формуле
где Lcond ‒ полная длина конденсатора.Выражение для количества единиц переноса тепла имеет вид
αL-in ‒ коэффициент теплоотдачи конденсата; ${{L}_{{ll}}},$ ${{d}_{{ll}}}$ ‒ длина и внутренний диаметр конденсатопровода; ${{D}_{{la}}}$ ‒ наружный диаметр теплоизоляции конденсатопровода; ${{c}_{{L - in}}}$ ‒ теплоемкость конденсата.
Эффективность теплообмена ηL-in и температура на входе в КП tin вычисляют по формулам
(36)
$\begin{gathered} {{\eta }_{{L - in}}} = 1 - \exp \left( { - NT{{U}_{{L - in}}}} \right); \\ {{t}_{{in}}} = {{t}_{L}} + \left( {{{t}_{a}} - {{t}_{L}}} \right){{\eta }_{{L - in}}}. \\ \end{gathered} $Как жидкость нагревается или остывает в конденсатопроводе, так и пар в паропроводе может нагреваться или остывать. Расчет теплообмена аналогичен представленному выше расчету.
Для увязки расчетной модели теплообмена в паропроводе с окружающей средой необходимо провести следующую корректировку уравнений. Если в паропроводе пар перегревается до температуры ${{t}_{{v2}}}$ и воспринимает тепло $\Delta Q,$ то при остывании в конденсаторе он это тепло отдает. Нужно скорректировать ${{t}_{{\text{м}}}},$ подставляя в (33) не $Q,$ а $Q + \Delta Q.$ Длина участка переохлаждения жидкости уменьшится на $\Delta L_{L}^{ - }$ (здесь $\Delta L_{L}^{ - }$ ‒ длина участка, на котором перегретый пар остынет от температуры ${{t}_{{v2}}}$ до температуры конденсации):
где $\theta = \frac{{{{t}_{{v2}}} - {{t}_{c}}}}{{\ln \left( {\frac{{{{t}_{{v2}}} - {{t}_{{\text{м}}}}}}{{{{t}_{c}} - {{t}_{{\text{м}}}}}}} \right)}}$ ‒ температурный напор; ${{\alpha }_{{ox}}}$ ‒ коэффициент теплоотдачи перегретого пара к стенке канала.Если пар охлаждается в паропроводе, то $\Delta Q < 0$ и длина участка переохлаждения жидкости увеличится на $\Delta L_{L}^{ + },$ причем
Итог предыдущих вычислений заключается в следующем:
в выражении (33) вместо $Q$ используют $Q + \Delta Q;$
длину участка переохлаждения жидкости вычисляют по формуле
длину участка движения пара в конденсаторе считают равной
Кроме уравнений (17)‒(38) в расчет теплового состояния КТТ дополнительно входят два условия:
(40)
${{p}_{{sat}}}\left( {{{t}_{c}}} \right) - {{p}_{{sat}}}\left( {{{t}_{l}}} \right) = \Delta {{р}_{{cl}}} + \Delta {{р}_{{ll}}},$СТРОЕНИЕ ВЫЧИСЛИТЕЛЬНОГО АЛГОРИТМА
Задают передаваемую тепловую мощность $Q$ в пределах от 0.5 N до 2.0 N.
Принимают температуру конденсации ${{t}_{c}}$ в пределах от ${{t}_{{х1}}} + \frac{Q}{{{{\alpha }_{c}}\pi {{d}_{c}}0.999{{L}_{{cond}}}}}$ до 60°С, после чего необходимо проверить выполнение уравнения (20) теплового баланса жидкости в КП. Для этого следует рассчитать значения показателей, которые входят в (20) с учетом принятой температуры tс.
Оценивают длину участка конденсации по приближенному соотношению (34), где вместо ${{t}_{{\text{м}}}}$ используют ${{t}_{{х1}}}{\text{:}}$
Оценивают температуру пара ${{t}_{{v1}}}$ и массовый расход теплоносителя $G$ по упрощенному условию (39):
Определяют ${{t}_{{\text{м}}}}$ из теплового баланса конденсатора (33). Для этого значения всех необходимых показателей ($Q,$ ${{t}_{c}},$ $G$) на данном этапе имеются.
Уточняют значение ${{L}_{c}}$ по выражению (34):
Уточняют значения ${{t}_{{v1}}}$ и $G$ по условию (39).
Учитывают перегрев или охлаждение пара, для чего:
определяют перегрев пара в паропроводе $\Delta Q$ и температуру пара на входе в конденсатор ${{t}_{{v2}}};$
выполняют коррекцию ${{t}_{{\text{м}}}},$ задавая в тепловой баланс (33) $Q + \Delta Q;$
вычисляют длину участка переохлаждения жидкости
гдеопределяют длину участка движения пара в конденсаторе ${{L}_{v}} = {{L}_{{cond}}} - {{L}_{L}}.$
Повторно уточняют значения ${{t}_{{v1}}}$ и $G,$ используя выражение (39):
Имея уточненные значения ${{t}_{c}},$ $G,$ ${{L}_{L}},$ определяют температуру переохлажденной жидкости на выходе из конденсатора ${{t}_{L}}.$
Определяют температуру жидкости на входе в КП ${{t}_{{in}}}.$
Вычисляют температуру жидкости в КП ${{t}_{l}}$ по условию (40):
Рассчитывают температуру поверхности фитиля ${{t}_{{wick}}}$ по (26):
Вычисляют температуру корпуса КП ${{t}_{{cc}}}$ и корпуса испарителя tе при совместном решении уравнений (17), (18):
Проверяют выполнение выражения (20) для теплового баланса жидкости в КП:
Если температура конденсации ${{t}_{c}}$ задана неправильно, то принимают другую температуру конденсации и повторяют цикл расчетов, пока не будет выполнено условие (20).
Проверяют выполнение выражения (19) для теплового баланса фитиля
Если передаваемая тепловая мощность $Q$ задана неправильно, то принимают другое значение Q и повторяют цикл расчетов, пока не будет выполнено условие (19).
Проверяют выполнение условия (1), и, если потери давления превышают капиллярный напор, значит решение выполнено некорректно. В этом случае для расчета режимов КТТ за пределами проводимости требуется изменение методики расчета.
Подборы значений $Q,$ ${{t}_{c}},$ ${{t}_{{v1}}},$ ${{t}_{l}}$ проводятся методом “деления отрезка пополам”. За 50 итераций алгоритм позволяет добиться высокой машинной точности ‒ абсолютная погрешность составляет примерно 10‒14.
СОПОСТАВЛЕНИЕ ЭКСПЕРИМЕНТАЛЬНЫХ И РАСЧЕТНЫХ ДАННЫХ
Разработанную расчетную методику верифицировали по данным, полученным при экспериментах на контурной трубе, изготовленной из нержавеющей стали марки 12Х18Н10Т. Испаритель снабжен капилляроно-пористой структурой (фитилем) из титанового порошка марки ПТОМ. В качестве теплоносителя использовали аммиак особой чистоты содержанием 99.9999%. Его свойства принимали по данным [28]. Роль теплового стока выполняла “холодная” плита, контактирующая с теплообменником, по каналам которого прокачивалась охлаждающая жидкость ПМС-1.5. Для уменьшения влияния окружающей среды использовали теплоизоляцию к-флекс. Схема КТТ показана на рис. 4, ее основные характеристики приведены далее:
Размеры пароотводного канала, мм: |
высота ........................................................1.0 |
ширина ......................................................1.0 |
Радиус капилляра, мкм ..................................6.5 |
Пористость фитиля, % ....................................45 |
Внутренний диаметр паропровода, |
трубки конденсатора и конденсатопровода |
(трубка 2.0 × 0.25), мм ....................................1.5 |
Диаметр фитиля, мм: |
внутренний ...............................................3.0 |
внешний ....................................................9.4 |
Длина, м: |
пароотводного канала .............................0.06 |
паропровода ............................................1.45 |
конденсатопровода .................................1.47 |
фитиля .....................................................0.07 |
трубки конденсатора .............................0.592 |
Радиус поворота, мм: |
паропровода и конденсатопровода ............5 |
трубки конденсатора ..................................15 |
Суммарный угол всех поворотов, град: |
паропровода ...............................................90 |
конденсатопровода ..................................270 |
трубки конденсатора ...............................900 |
Рис. 4.
Экспериментальная контурная тепловая труба. 1 – паропровод; 2 – термоплата испарителя; 3 – корпус испарителя; 4 – компенсационная полость; 5 – конденсатопровод; 6 – радиатор. ⚫ ‒ размещение термопар в контрольных точках
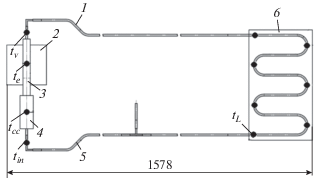
Первый эксперимент проводили при комнатной температуре. Задавали тепловую нагрузку 10‒60 Вт с шагом 10 Вт, изменяли температуру и расход охлаждающего теплоносителя (исходные данные). На рис. 5 показана зависимость тепловой нагрузки на испаритель и расхода охлаждающего теплоносителя от продолжительности эксперимента, на рис. 6 ‒ динамика изменения температур. Видно, что температуры испарителя и компенсационной полости очень близки. Температура tv оказалась существенно выше температуры испарителя. Здесь, по-видимому, сказываются влияние окружающей среды и перегрев пара. Сравнивая температуру переохлажденной жидкости на выходе из холодильника tL и на входе в компенсационную полость tin, также можно отметить, что жидкость значительно нагревается на своем пути по конденсатопроводу. В данном эксперименте окружающая среда оказывает сильное влияние на функционирование КТТ.
Рис. 5.
Зависимость тепловой нагрузки N (1) и расхода охлаждающего теплоносителя Gх (2) от продолжительности эксперимента τ
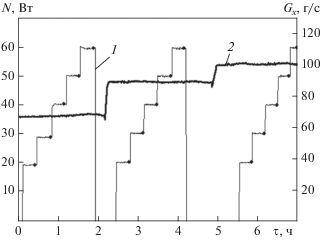
Рис. 6.
Температурно-временная зависимость при изменении тепловых нагрузок от 20 до 60 Вт. 1 ‒ ta; 2 ‒ tv; 3 ‒ tе; 4 ‒ tcc; 5 ‒ tin; 6 ‒ tL; 7 ‒ tx2; 8 ‒ tx1
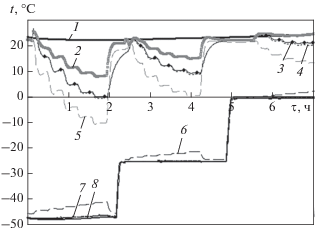
Экспериментальные и расчетные значения основных характеристик приведены в табл. 1 и показаны на рис. 7.
Таблица 1.
Экспериментальные и расчетные значения основных характеристик КТТ в испытаниях при комнатной температуре
Исходные данные | Температура экспериментальная/расчетная, °С | ||||||||
---|---|---|---|---|---|---|---|---|---|
N, Вт | ta, °С | Gx, г/с | tx1, °С | te | tcc | tL | tin | tv | tx2 |
19.6 | 23.0 | 66.7 | ‒48.0 | 15.7/15.0 | 15.6/15.5 | ‒44.4/‒43.1 | 9.5/7.5 | 15.7/18.5 | ‒47.6/‒47.6 |
29.1 | 22.6 | 67.1 | ‒48.0 | 10.7/7.5 | 10.4/8.5 | ‒43.8/‒41.8 | 2.6/‒1.2 | 10.7/13.8 | ‒47.5/‒47.4 |
40.4 | 22.4 | 67.3 | ‒47.9 | 4.9/1.9 | 4.7/3.2 | ‒43.0/‒40.2 | ‒4.0/‒7.7 | 4.9/9.4 | ‒47.3/‒47.2 |
50.1 | 22.3 | 67.9 | ‒47.6 | 1.8/‒0.9 | 1.5/0.5 | ‒42.1/‒38.8 | ‒7.8/‒11.2 | 1.8/6.7 | ‒46.9/‒46.8 |
59.6 | 22.2 | 68.3 | ‒47.2 | 0.1/‒2.5 | ‒0.5/‒1.1 | ‒41.2/‒37.4 | ‒10.3/‒13.5 | 0.1/4.9 | ‒46.4/‒46.3 |
20.5 | 22.4 | 89.0 | ‒25.5 | 19.9/17.8 | 19.5/18.0 | ‒23.5/‒22.8 | 13.2/11.4 | 19.9/19.7 | ‒25.4/‒25.2 |
30.5 | 22.6 | 89.1 | ‒25.5 | 15.2/12.9 | 14.9/13.5 | ‒23.0/‒22.0 | 8.2/5.5 | 15.2/16.7 | ‒25.4/‒25.1 |
40.4 | 22.7 | 88.7 | ‒25.5 | 12.2/9.6 | 12.0/10.3 | ‒22.5/‒21.2 | 4.5/1.6 | 12.2/14.2 | ‒25.3/‒25.1 |
50.1 | 22.8 | 88.7 | ‒25.5 | 10.4/7.5 | 10.1/8.3 | ‒22.1/‒20.4 | 2.1/‒1.0 | 10.4/12.3 | ‒25.3/‒25.0 |
59.5 | 23.0 | 88.8 | ‒25.5 | 9.5/6.4 | 8.9/7.2 | ‒21.5/‒19.7 | 0.5/‒2.7 | 9.5/11.0 | ‒25.2/‒24.9 |
20.5 | 23.6 | 100.0 | ‒0.7 | 23.9/23.3 | 23.4/23.2 | 0.3/0.8 | 18.9/18.0 | 23.9/23.2 | ‒0.6/‒0.5 |
30.3 | 23.8 | 99.7 | ‒0.7 | 22.3/21.1 | 21.8/21.1 | 0.8/1.3 | 16.6/15.2 | 22.3/21.9 | ‒0.5/‒0.5 |
40.2 | 24.0 | 100.2 | ‒0.7 | 21.4/19.7 | 20.9/19.7 | 1.1/1.9 | 15.0/13.3 | 21.4/20.9 | ‒0.5/‒0.4 |
50.0 | 24.1 | 100.3 | ‒0.7 | 21.1/18.8 | 20.4/18.8 | 1.6/2.4 | 14.0/12.0 | 21.1/20.0 | ‒0.4/‒0.3 |
59.8 | 24.2 | 99.9 | ‒0.7 | 21.2/18.4 | 20.2/18.3 | 2.2/3.0 | 13.5/11.2 | 21.2/19.5 | ‒0.4/‒0.3 |
Рис. 7.
Зависимости экспериментальной (1‒3) и расчетной (4‒6) температур корпуса испарителя от тепловой нагрузки при комнатной температуре. tx1, °С: ‒48.0 (1, 4); ‒25.5 (2, 5); ‒0.7 (3, 6)
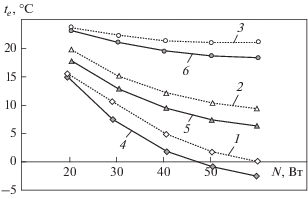
Последующие эксперименты проводили в климатической камере, когда температура среды была близка к температуре охладителя. Нагрузку варьировали от 10 до 60 Вт, изменялись температура среды, температура и расход охлаждающего теплоносителя. Экспериментальные и расчетные значения основных характеристик приведены в табл. 2 и показаны на рис. 8.
Таблица 2.
Экспериментальные и расчетные значения основных характеристик КТТ при испытаниях в климатической камере
Исходные данные | Температура экспериментальная/расчетная, °С | ||||||||
---|---|---|---|---|---|---|---|---|---|
N, Вт | ta, °С | Gx, г/с | tx1,°С | te | tcc | tL | tin | tv | tx2 |
31.3 | ‒50.0 | 64.1 | ‒50.1 | ‒35.3/‒31.0 | ‒36.7/‒33.0 | ‒48.8/‒46.5 | ‒47.1/‒48.8 | ‒39.1/‒39.6 | ‒49.8/‒49.8 |
41.7 | ‒50.0 | 64.0 | ‒49.8 | ‒33.4/‒28.2 | ‒35.1/‒30.7 | ‒47.9/‒45.0 | ‒46.6/‒47.7 | ‒37.3/‒37.3 | ‒49.5/‒49.4 |
53.9 | ‒50.0 | 63.5 | ‒50.1 | ‒30.5/‒24.9 | ‒33.1/‒28.0 | ‒47.5/‒43.8 | ‒46.6/‒46.6 | ‒35.3/‒34.5 | ‒49.7/‒49.5 |
58.5 | ‒50.0 | 63.2 | ‒50.1 | ‒28.9/‒23.8 | ‒32.3/‒27.0 | ‒46.7/‒43.2 | ‒45.6/‒46.1 | ‒34.0/‒33.4 | ‒49.6/‒49.5 |
20.0 | ‒25.0 | 89.3 | ‒25.0 | ‒21.5/‒17.1 | ‒22.0/‒18.0 | ‒23.5/‒23.6 | ‒23.5/‒24.7 | ‒22.0/‒21.0 | ‒24.8/‒24.9 |
29.8 | ‒25.0 | 89.2 | ‒25.0 | ‒19.0/‒16.0 | ‒19.7/‒17.0 | ‒22.8/‒22.9 | ‒22.8/‒24.3 | ‒19.9/‒20.3 | ‒24.8/‒24.8 |
39.2 | ‒25.0 | 88.8 | ‒25.0 | ‒17.1/‒14.6 | ‒18.0/‒15.9 | ‒21.8/‒22.2 | ‒21.9/‒23.7 | ‒18.3/‒19.2 | ‒24.8/‒24.7 |
49.0 | ‒25.0 | 89.7 | ‒25.0 | ‒15.2/‒12.8 | ‒16.8/‒14.4 | ‒20.9/‒21.5 | ‒21.3/‒23.2 | ‒17.1/‒17.9 | ‒24.7/‒24.6 |
58.1 | ‒25.0 | 89.0 | ‒25.0 | ‒13.3/‒11.2 | ‒15.3/‒13.1 | ‒20.0/‒20.9 | ‒20.4/‒22.6 | ‒15.7/‒16.6 | ‒24.7/‒24.6 |
19.3 | 0.3 | 99.9 | 0.2 | 3.3/5.4 | 2.4/4.8 | 1.5/1.2 | 0.3/0.5 | 2.9/2.8 | 0.3/0.3 |
28.9 | 0.1 | 99.4 | 0.2 | 4.5/6.0 | 3.5/5.3 | 2.3/1.7 | 0.8/0.7 | 3.9/3.2 | 0.3/0.4 |
38.0 | 0 | 99.6 | 0.1 | 5.8/6.8 | 4.6/5.9 | 3.3/2.0 | 1.4/0.9 | 5.0/3.6 | 0.3/0.3 |
49.5 | ‒0.1 | 99.2 | 0.2 | 7.7/8.0 | 6.1/6.8 | 4.3/2.7 | 2.4/1.4 | 6.5/4.4 | 0.4/0.5 |
59.2 | ‒0.1 | 99.8 | 0.2 | 9.5/9.0 | 7.5/7.6 | 4.9/3.3 | 3.3/1.9 | 7.9/5.2 | 0.4/0.6 |
Рис. 8.
Зависимости экспериментальной (1‒3) и расчетной (4‒6) температур корпуса испарителя от тепловой нагрузки при испытаниях в климатической камере. ta, °С: ‒50.0 (1, 4); ‒25.0 (2, 5); 0 (3, 6)
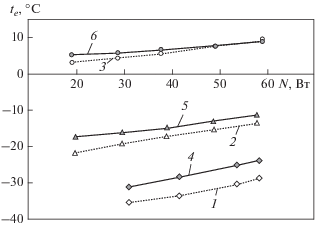
В испытаниях при комнатной температуре с увеличением нагрузки температура испарителя понижается, что свидетельствует о повышении тепловой проводимости КТТ. Результаты расчета качественно соответствуют экспериментальным данным. Однако при расчете несколько занижается температура испарителя. Средняя погрешность расчета (среднеквадратичная) по температуре испарителя составила 2.4°С, наибольшая погрешность ‒ 3.1°С.
В условиях пониженной температуры среды, близкой к температуре охлаждающей жидкости, зависимость температуры испарителя от нагрузки качественно меняется. С увеличением нагрузки температура испарителя возрастает. Качественное изменение характера процесса хорошо отслеживается расчетной моделью. В этих условиях расчетная модель несколько завышает температуру испарителя. Наибольшая погрешность составила 5.4°С, средняя погрешность ‒ 3.3°С.
ВЫВОДЫ
1. Разработанная авторами методика позволяет проводить математический расчет функционирования контурной тепловой трубы в стационарном режиме. Данные расчетов по этой методике довольно точно совпадают с результатами испытаний экспериментальной контурной тепловой трубы в различных режимах при температуре испарителя от ‒35 до +35°С.
2. Максимальная погрешность расчетного определения температуры испарителя составляет менее 6°С, средняя погрешность по всем расчетам ‒ 2.9°С.
Список литературы
Судаков Р.Г. Исследование нестационарных и колебательных режимов работы контурных тепловых труб: дис. … канд. физ.-мат. наук. Екатеринбург, 2004.
Майданик Ю.Ф., Ферштатер Ф.Г., Пастухов В.Г. Контурные тепловые трубы: разработка, исследование, элементы инженерного расчета. Свердловск: УрО АН СССР, 1989.
Романов А.В. Системы обеспечения тепловых режимов герметичных отсеков и ЯЭУ космических аппаратов. СПб.: АНО ЛА “Профессионал”, 2014.
Алексеев С.В., Прокопенко И.Ф., Рыбкин Б.И. Низкотемпературные тепловые трубы для космической техники. В 2 т. Т. 1: Проблемы обеспечения работоспособности. М.: Новости, 2006.
Проектирование и исследование прецизионных систем терморегулирования на базе контурных тепловых труб / В.А. Антонов, М.А. Балыкин, К.А. Гончаров, К.Н. Коржов // Решетневские чтения. 2016. Т. 1. С. 78‒80.
Ганенко С.А., Басынин В.В., Казанцев З.А. Особенности СТР малого космического аппарата “Юбилейный-2”. Красноярск: Сибирский гос. аэрокосм. ун-т им. акад. М.Ф. Решетнева, 2012.
Дан П., Рей Д. Тепловые трубы. М.: Энергия, 1979.
Чи С. Тепловые трубы: теория и практика. М.: Машиностроение, 1981.
Васильев Л.Л., Конев С.В., Хроленок В.В. Интенсификация теплообмена в тепловых трубах. М.: Наука и техника, 1983.
Ивановский М.Н., Сорокин В.П., Ягодкин И.В. Физические основы тепловых труб. М.: Атомиздат, 1987.
Перельман Т.Л., Левитан М.М. Основы теории тепловых труб // ИФЖ. 1973. Т. 25. № 5. С. 816‒826.
Каданер Я.С., Рассалкин Ю.П. Ламинарное течение пара в тепловой трубе // ИФЖ. 1975. Т. 28. № 2. С. 208‒216.
Rjhani A.R., Tien C.L. Analisis of effects of vapor pressure drop in heat pipes performance // Int. J. Heat Mass Transfer. 1974. V. 17. P. 61‒67. https://doi.org/10.1016/0017-9310(74)90038-6
Михаилов В.С., Крапивин А.И., Быстров П.И. Исследование гидродинамики парового потока в тепловых трубах при турбулентном режиме // ИФЖ. 1978. Т. 34. № 2. С. 197‒201.
Быстров П.И., Михаилов В.С., Покандюк Г.И. Экспериментальное исследование гидродинамики турбулентного потока в тепловых трубах // ТВТ. 1975. Т. 13. № 2. С. 379‒385.
Николаев Г.П., Изотеева О.Ю. Расчет рабочих характеристик контурных тепловых труб // Молодой ученый. 2012. Т. 1. № 3. С. 17‒25.
Gruzdova N.L., Kiseev V.M., Ostrovskii A.B. Models of the heat and mass transfer in LHP evaporator // 12th Intern. High Pipe Conf. Moscow, 2002. P. 108‒114.
Altman E.I., Mukminova M.I., Smirnov H.F. The loop heat pipe evaporators theoretical analysis // 12th Intern. High Pipe Conf. Moscow, 2002. P. 159‒164.
Ферштатер Ю.Г., Майданик Ю.Ф. Анализ температурного поля испарителя антигравитационной тепловой трубы // ИФЖ. 1986. Т. 51. № 2. С. 203‒207.
Pauken M., Rodriguez J.I. Performance characterization and model verification of a loop heat pipe // 30th ICES/European Symposium on Space Environmental Control Systems. France, 2000. https://doi.org/10.4271/2000-01-2317
Bauman J. Heat pipe, CPL and LHP analysis integrated with finite element and finite difference CAD-based thermal modeling // Intern. Two Thermal Control Technology Workshop. Mitcellville, Maryland, 2002.
Sudakov R.G., Maidanik Y.F. Development and investigation of an ammonia reversible loop heat pipe // 12th Intern. Heat Pipe Conf. Moscow, 2002. P. 177‒181.
Идельчик И.Е. Справочник по гидравлическим сопротивлениям. М.: Машиностроение, 1975.
Чи С. Тепловые трубы: теория и практика / пер. с англ. М.: Машиностроение, 1981.
Поляев В.М., Майоров В.А., Васильев Л.Л. Гидродинамика и теплообмен в пористых элементах конструкций летательных аппаратов. М.: Машиностроение, 1988.
Уонг Х. Основные формулы и данные по теплообмену для инженеров: справочник / пер. с англ. М.: Атомиздат, 1979.
Мартыненко О.Г. Справочник по теплообменникам. Т. 1. М.: Энергоатомиздат, 1987.
Варгафтик Н.Б. Справочник по теплофизическим свойствам газов и жидкостей. М.: Наука, 1972.
Дополнительные материалы отсутствуют.
Инструменты
Теплоэнергетика