Теплоэнергетика, 2022, № 3, стр. 92-99
Морфология и фазовый состав оксидных пленок и отложений продуктов коррозии в парогенераторе реакторной установки БН-800
Б. А. Гусев a, *, А. А. Ефимов a, А. М. Алешин a, В. Г. Семенов b, В. В. Панчук b, В. В. Мартынов a, А. Н. Максимова a
a Научно-исследовательский технологический институт им. А.П. Александрова
188540 Ленинградская обл., г. Сосновый Бор, Копорское шоссе, д. 72, Россия
b Институт химии Санкт-Петербургского государственного университета
198504 Санкт-Петербург, Университетский просп., д. 26, Россия
* E-mail: gusev@niti.ru
Поступила в редакцию 10.07.2021
После доработки 13.07.2021
Принята к публикации 25.08.2021
- EDN: CKVVEE
- DOI: 10.1134/S0040363622030055
Аннотация
Изложены результаты исследования морфологии, фазового и химического составов защитных оксидных пленок и отложений продуктов коррозии, самопроизвольно образующихся на поверхности стали при работе теплообменного оборудования в условиях окислительного водно-химического режима теплоносителя III контура реакторной установки БН-800. Проведено сравнение фазового состава защитных оксидных пленок на рабочих поверхностях III контура парогенераторов реакторных установок БН-600 и БН-800, эксплуатируемых в условиях различных водно-химических режимов. Показано, что, в отличие от горизонтальных парогенераторов типа ПГВ, используемых на энергоблоках с водо-водяными энергетическими реакторами, где оксидные пленки и отложения продуктов коррозии во II контуре определяются только магнетитом (Fe3O4), пленки и отложения в парогенераторе Н-272 содержат три фазы: магнетит (Fe3O4), гематит (α-Fe2O3) и лепидокрокит (γ‑FeOOH). Непосредственно на металле формируется защитная оксидная пленка магнетита (100%), на которой образуются прочно сцепленный с ней слой отложений, состоящий на 70% из магнетита, на 25‒30% из гематита, на 1‒5% из лепидокрокита, и поверхностные слабо фиксированные отложения продуктов коррозии. Фазовые составы плотного слоя (гематит) и слабо фиксированных отложений продуктов коррозии (гематит + лепидокрокит) на рабочих поверхностях теплообменных трубок парогенератора Н-272 отвечают слабощелочному окислительному водно-химическому режиму III контура реакторной установки БН-800. Установлено, что независимо от типа водно-химического режима (окислительного для реакторной установки БН-800 или восстановительного для реакторной установки БН-600) на поверхности перлитной стали в процессе эксплуатации самопроизвольно формируется оксидный слой магнетита, обладающий защитными свойствами.
При коррозии в контурах реакторных установок (РУ) на теплопередающих поверхностях образуются эксплуатационные отложения и происходит деградация свойств металла. Управление этими процессами осуществляется с помощью оптимального водно-химического режима (ВХР), своевременного проведения химических промывок и пассивации оборудования [1, 2]. На российских АЭС в условиях восстановительного ВХР в контур дозируется только гидразин, при окислительном ВХР ‒ кислород и аммиак.
К настоящему времени эти процессы подробно изучены для горизонтальных парогенераторов (ПГ) типа ПГВ [3] с трубной системой из аустенитной нержавеющей стали, используемых на энергоблоках с водо-водяными энергетическими реакторами. В условиях восстановительного ВХР на рабочих поверхностях теплообменных трубок (ТОТ) образуются структуры, состоящие из защитных оксидных пленок и отложений продуктов коррозии, содержащих только шпинели типа магнетита [2, 4]. Защитные оксидные пленки формируются на поверхности самопроизвольно в процессе эксплуатации и целенаправленно в результате применения технологий защитного оксидирования.
Вертикальные парогенераторы Н-272 реакторной установки на быстрых нейтронах БН-800 с теплообменными трубками, изготовленными из перлитной стали 10Х2М-ВД, эксплуатируются в условиях окислительного ВХР. Перлитные стали обладают массой достоинств и высокотехнологичны. Однако у них есть один серьезный недостаток – высокая скорость общей коррозии, при этом на рабочих поверхностях ТОТ формируются структуры, состоящие из защитных оксидных пленок и отложений продуктов коррозии (ПК) сложного фазового состава. В основном это магнетит (Fe3O4), гематит (α-Fe2О3), магемит (γ-Fe2О3) и лепидокрокит (γ-FeOOH) в различных соотношениях с примесями оксидов легирующих элементов (Cr, Ni, Mn).
Вопрос соответствия фазового состава защитных оксидных пленок на поверхностях оборудования, выполненного из сталей перлитного класса, применяемому принятому ВХР вызывает неоднозначную реакцию. Имеющийся опыт химических промывок и пассивации оборудования ядерных энергетических установок [1, 2], эксплуатируемого в условиях восстановительного ВХР, не позволяет напрямую перенести его на оборудование, эксплуатируемое в условиях окислительного ВХР. Считается, что в этих условиях вследствие перестройки защитной оксидной пленки будет происходить усиленный вынос ПК с поверхностей конструкционных материалов в теплоноситель.
Коррозионные процессы в парогенераторах вертикального типа Н-272 с естественной циркуляцией пароводяной смеси в испарительных и пароперегревательных модулях практически не исследованы. Для оборудования ПГ Н-272, теплообменные трубки которого изготовлены из легированной перлитной стали 10Х2М-ВД, принят окислительный кислородно-аммиачный ВХР. Выбор слабощелочного окислительного режима определяется применением в составе оборудования III контура медного сплава типа МНЖ, при этом рН теплоносителя нормируется на уровне 9.0 ± 0.2. Химический состав, %, стали 10Х2М-ВД (10Х2М1А) приведен далее:
С ...............................................0.08‒0.112 |
Si ................................................0.17‒0.37 |
Mn .................................................0.4‒0.7 |
Ni ....................................................До 0.3 |
Cr ..................................................2.0‒2.5 |
Mo .................................................0.6‒0.8 |
Для перлитных сталей при их контакте с водным теплоносителем характерна общая коррозия [3], поэтому на рабочих поверхностях ТОТ можно обнаружить коррозионные отложения, морфология, фазовый и химический составы которых применительно к оборудованию с окислительным ВХР практически не изучены.
ИССЛЕДОВАНИЕ СВОЙСТВ ЗАЩИТНЫХ ОКСИДНЫХ ПЛЕНОК И ОТЛОЖЕНИЙ
Для исследования свойств оксидных пленок и отложений отбирали их пробы из теплообменных трубок длиной 15 м испарительного (ИМ) и пароперегревательного (ППМ) модулей парогенератора Н-272 ядерной энергетической установки БН-800. Вырезанные ТОТ делили на 15 фрагментов длиной по 1 м, каждый фрагмент разрезали на 4 образца длиной 250 мм. Дальнейшие исследования проводили на одном из образцов, отобранных из каждого фрагмента. С внутренних поверхностей образцов были отобраны просыпи рыхлых отложений ПК для определения удельной поверхностной загрязненности теплообменных трубок испарительного и пароперегревательного модулей и методом пластической деформации были удалены защитные оксидные пленки с плотными отложениями ПК. Полнота удаления иллюстрируется на рис. 1, на котором показан характерный внешний вид поперечного сечения поверхности в исходном состоянии и после удаления оксидной пленки вместе с плотными отложениями.
Рис. 1.
Внешний вид сечения поверхности теплообменной трубки до удаления отложений (а) и после удаления (б)
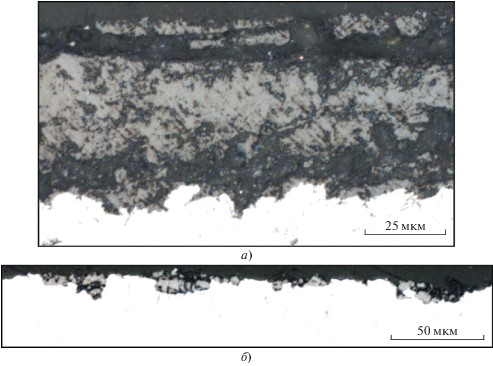
Пробы рыхлых отложений и просыпи защитных оксидных пленок с плотными отложениями были направлены на исследование фазового и химического составов ПК. Некоторые образцы ТОТ после удаления рыхлых отложений были использованы для металлографических исследований морфологии оксидных пленок и плотных отложений ПК на поверхности ТОТ. Визуальный осмотр и оценку исходного состояния рабочих поверхностей образцов проводили на оптическом микроскопе МПБ-2 при 24-кратном увеличении. Металлографические исследования выполняли на лазерном микроскопе OLYMPUSLEXTOLS-4000 при увеличении от 100 до 2000 крат.
По внешнему виду просыпи рыхлых отложений в ТОТ испарительного и пароперегревательного модулей парогенератора Н-272 представляют собой крупнодисперсные частицы темно-коричневого цвета размером более 15 мкм. На рис. 2 приведены данные определения плотности рыхлых отложений ρ по длине испарительного и пароперегревательного модулей ПГ Н-272, полученные по результатам весового анализа просыпей с фрагментов ТОТ. Обращают на себя внимание максимальные значения плотности отложений по длине ТОТ, которые, скорее всего, формируются на рабочих поверхностях вследствие “всплесков” твердофазных ПК в теплоносителе и затем нивелируются при движении рабочей среды. В пароперегревательном модуле отлагается до 95% ПК и лишь около 5% ‒ в испарительном.
Рис. 2.
Распределение плотности рыхлых отложений ПК по длине испарительного (а) и пароперегревательного (б) модулей ПГ Н-272
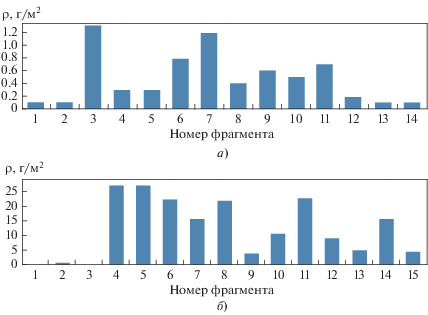
Внешний вид плотных отложений ПК на рабочих поверхностях ТОТ испарительного и пароперегревательного модулей после удаления рыхлых отложений показан на рис. 3.
Рис. 3.
Внешний вид рабочей поверхности образцов испарительной (а) и пароперегревательной (б) ТОТ после удаления рыхлых отложений
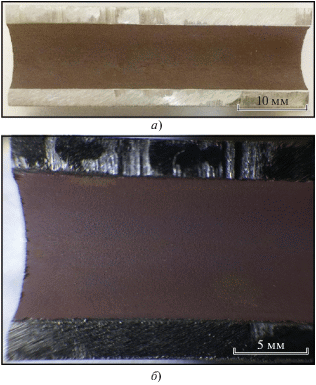
Плотность удаленной методом пластической деформации структуры, состоящей из защитной оксидной пленки и прочно сцепленных отложений ПК, на рабочих поверхностях ТОТ испарительного и пароперегревательного модулей составляет 20‒70 и 60‒190 г/м2 соответственно. Этот факт свидетельствует в пользу разных механизмов формирования фазы защитной оксидной пленки и фаз плотного и рыхлого слоев отложений ПК. Если фаза оксидной пленки на поверхности стали формируется путем взаимодействия “активных” поверхностных атомов железа с его растворенными в теплоносителе наноразмерными частицами продуктов гидролиза [2, 5], то образование фазы плотных и рыхлых отложений генетически не связано с образованием оксидной пленки и происходит по механизму осаждения сформировавшихся в теплоносителе твердофазных продуктов гидролиза железа (как основного элемента стали) с последующими термохимической дегидратацией, кристаллизацией и уплотнением со временем рыхлых слоев в плотные, прочно фиксированные на поверхности защитные пленки [2, 6].
ФАЗОВЫЙ СОСТАВ ОТЛОЖЕНИЙ ПРОДУКТОВ КОРРОЗИИ
Для определения фазового состава прочно сцепленных и рыхлых отложений продуктов коррозии методом мёссбауэровской спектроскопии [7] использовали просыпи ПК, полученные по описанной выше методике.
Мёссбауэровские спектры (МС) рыхлых и прочно сцепленных ПК представляют собой суперпозицию дублетов и секстетов квадрупольного и магнитного расщепления мёссбауэровских ядер 57Fe в исследуемых образцах (рис. 4) с различным долевым соотношением и параметрами компонентов в общем спектре образцов (табл. 1). На рис. 4 показана зависимость интенсивности излучения I (от источника), прошедшего через образец и зарегистрированного детектором, от скорости доплеровского модулятора v. Сопоставление этих параметров с параметрами МС стандартных образцов оксидов и гидроксидов железа [6] позволяет идентифицировать качественный фазовый состав просыпей коррозионных продуктов с образцов ТОТ парогенератора Н-272 следующим образом:
Рис. 4.
Мёссбауэровские спектры оксидных пленок и плотных отложений ПК на поверхности ТОТ испарительного (а) и пароперегревательного (б) модулей
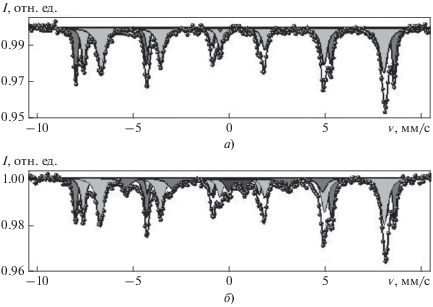
Таблица 1.
Качественный фазовый состав слабо фиксированных и прочно сцепленных продуктов коррозии на рабочих поверхностях ТОТ испарительного и пароперегревательного модулей парогенератора Н-272 реакторной установки БН-800 при 25°С
Модуль | Отложения | Компонент МС | Параметры МС | Фаза | ||
---|---|---|---|---|---|---|
ИСFe, мм/с | КР, м/с | Нэф, Т | ||||
ИМ | Рыхлые | Дублет I | 0.34 | 0.56 | 0 | γ-FeOOH |
Секстет I | 0.36 | 0.40 | 51.5 | α-Fe2O3 | ||
Секстет II (А) | 0.39 | 0.10 | 49.0 | Fe3O4 | ||
Секстет III (Б) | 0.65 | 0 | 45.3 | |||
Плотные | Дублет II | 0.15 | 1.27 | 0 | Наночастицы | |
Секстет IV | 0.37 | 0.19 | 51.7 | α-Fe2O3 | ||
Секстет V (А) | 0.28 | 0.01 | 48.9 | Fe3O4 | ||
Секстет VI (Б) | 0.67 | 0 | 45.8 | |||
ППМ | Рыхлые | Не анализировались | ||||
Плотные | Дублет III | 0.35 | 0.85 | 0 | γ-FeOOH | |
Секстет VII | 0.38 | 0.20 | 51.6 | α-Fe2O3 | ||
Секстет III (А) | 0.28 | 0.02 | 49.0 | Fe3O4 | ||
Секстет IX (Б) | 0.66 | 0.01 | 45.9 | |||
Секстет X | 0.15 | 0.25 | 31.3 | Металлические опилки |
параметры дублетов I и III отвечают фазе лепидокрокита (γ-FeOOH) или наноразмерным частицам гематита (α-Fe2O3);
параметры секстетов I, IV, VII относятся к фазе гематита (α-Fe2O3);
параметры секстетов (в совокупности) (II, III), (V, VI) и (VIII, IX) характеризуют два неэквивалентных структурных положения атомов железа в шпинельной структуре магнетита Fe3O4, Fe3+ в тетраэдрическом окружении и [Fe3+ + Fe2+] в октаэдрических пустотах [${\text{Fe}}_{{{\text{тетр}}}}^{{{\text{3 + }}}}$(Fe2+ + Fe3+)октО4];
параметры секстета X принадлежат металлической фазе (вкрапления α-Fe в оксидный слой) перлитной стали;
параметры дублета II (прочно сцепленный слой ПК образца испарительной ТОТ) по причинам, обоснованным в работе [7], относятся к фазе наноразмерных частиц гетита (α-FeOOH), т.е. прекурсоров формирования структуры α-Fe2O3.
На рис. 5 приведены мёссбауэровские спектры образцов рыхлых отложений, отобранных по высоте (верх, середина, низ) испарительного канала. Нумерация образцов слабо фиксированных отложений соответствует нумерации образцов ТОТ испарительного модуля. При анализе мёссбауэровских спектров интерпретации фазового состава образцов отложений учитывали изменение температуры теплоносителя по высоте испарительного канала (245°С на входе, 365°С на выходе).
Рис. 5.
Мёссбауэровские спектры образцов 1 (а), 7 (б), 15 (в) рыхлых отложений ТОТ по длине испарительного канала
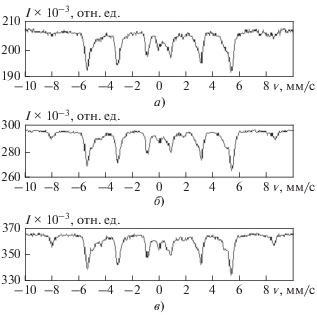
Центральная часть спектров ‒ аналоги секстетов V и VI (см. табл. 1) в диапазоне изменения v = = ±5.6 мм/с, в котором закреплен мёссбауэровский источник γ-квантов (см. рис. 5), остается неизменной для всех спектров, а изменения наблюдаются в области ±8 мм/с (аналог секстета I). Так, в образце 1 (самая низкая температура теплоносителя) сигналы в этой области не наблюдаются, при увеличении температуры появляются сигналы, отвечающие секстету (образец 7), доля которого растет с дальнейшим ростом температуры (образец 15). В результате обработки спектров исследуемых образцов помимо фазы материала ТОТ (pipe) идентифицированы еще две фазы: секстет, дающий сигналы в области ±8 мм/с, параметры которого отвечают α-Fe2O3 (corr1), и парамагнитный дублет (corr2) с параметрами изомерного сдвига 0.34 мм/с и квадрупольного расщепления 0.56 мм/с. Такие параметры могут соответствовать гидроксидам железа, например лепидокрокиту (γ-FeOOH), или наноразмерным частицам α-Fe2O3.
В результате обработки мёссбауэровских спектров проб рыхлых отложений ПК, отобранных с поверхности 15 образцов ТОТ испарительного модуля, была определена доля всех фаз ПК в измеренных пробах. Установлено, что содержание фазы α-Fe2O3 незначительно увеличивается с 1-го до 6-го образца, далее ее содержание резко увеличивается вплоть до 9-го образца, после которого перестает изменяться. Такое равномерное и монотонное изменение содержания продуктов коррозии вдоль трубки объясняется тем, что физико-химический состав теплоносителя по длине теплообменной трубки не изменяется, но растет его температура. Содержание второго продукта коррозии ‒ γ-FeOOH ‒ остается примерно постоянным от образца к образцу, поскольку лепидокрокит является продуктом стояночной коррозии конструкционных сталей на расхоложенном оборудовании.
В количественном отношении основу рыхлых ПК ТОТ испарительного модуля на 70‒90% составляет магнетит (Fe3O4). Содержание фазы гематита (α-Fe2O3) на входе в ТОТ испарительного модуля незначительно (5‒10%), в образцах с 6-го по 9-й содержание гематита возрастает до 20% и далее по ходу среды остается постоянным. Такое изменение объясняется ростом температуры теплоносителя (от 245°С на входе в ТОТ до 365°С на выходе из нее) при постоянстве его физико-химического состава. Содержание третьей составляющей фазового состава рыхлых ПК ‒ лепидокрокита (γ-FeOOH) ‒ остается постоянным по длине ТОТ, поскольку он является продуктом стояночной коррозии перлитной стали на расхоложенном оборудовании.
Фазовый состав, %, оксидных пленок и плотных слоев ПК в ТОТ испарительного и пароперегревательного модулей практически одинаков: Fe3O4 ≈ 70, α-Fe2O3 ≈ 25‒30 и (γ-FeOOH + наночастицы) ≈ 1‒5 без учета металлических опилок, образовавшихся при фрагментации ТОТ. Фазовый состав рыхлых отложений в пароперегревательном модуле не исследовали, поскольку условия для его изменения по сравнению с испарительным модулем отсутствуют, а количественное распределение отложений носит случайный характер.
МОРФОЛОГИЯ ОКСИДНЫХ ПЛЕНОК И ОТЛОЖЕНИЙ ПРОДУКТОВ КОРРОЗИИ
Исследования морфологии оксидных пленок и плотных отложений ПК проводили путем анализа изображений микрошлифов на продольных и поперечных разрезах образцов ТОТ испарительного и пароперегревательного модулей (рис. 6). Полученные данные свидетельствуют о том, что на поверхности ТОТ как испарительного, так и пароперегревательного модуля в процессе эксплуатации самопроизвольно формируется защитная оксидная пленка магнетита, на которой расположены слой плотно сцепленных с ней отложений продуктов коррозии, фазовый состав которых определяется гематитом (α-Fe2O3), и слабо фиксированные отложения (гематит + лепидокрокит).
Рис. 6.
Внешний вид оксидной пленки на поверхности образца испарительного (а) и пароперегревательного (б) модулей
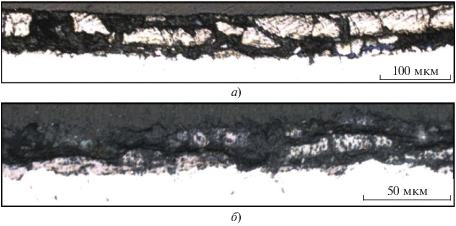
Таким образом, данные анализа фазового состава и морфологии ПК на поверхности ТОТ показывают, что проектному окислительному ВХР III контура ПГ Н-272 соответствует самопроизвольно образовавшаяся на рабочей поверхности ТОТ защитная оксидная пленка магнетита. Фазовый состав плотных отложений, сформировавшихся на рабочей поверхности ТОТ в процессе эксплуатации, также отвечает проектному окислительному ВХР.
Для определения плотности защитной оксидной пленки с отложениями ПК на рабочей поверхности образцов испарительных (ИТ) и пароперегревательных (ППТ) ТОТ был использован метод пластической деформации. В табл. 2 приведены полученные результаты.
Таблица 2.
Плотность оксидной пленки с отложениями ПК на рабочих поверхностях образцов ТОТ испарительного и пароперегревательного модулей
Образец | Место отбора пробы | Масса просыпи, г | Плотность пленки, г/м2 |
---|---|---|---|
ИТ | Вход | 0.1343 | 67.15 |
0.0425 | 21.25 | ||
Середина | ‒ | ‒ | |
Выход | 0.0513 | 25.65 | |
0.0738 | 36.90 | ||
ППТ | Вход | 0.0676 | 35.58 |
0.1372 | 72.21 | ||
Середина | 0.3621 | 190.58 | |
Выход | 0.1352 | 71.16 | |
0.1112 | 58.53 |
Плотность оксидной пленки с отложениями ПК, как и плотность рыхлых отложений, в ТОТ пароперегревательного модуля выше, чем в ТОТ испарительного. Реальная плотность оксидной пленки на 10‒20% меньше значений, приведенных в табл. 2, поскольку часть удаленной методом пластической деформации просыпи составляют продукты коррозии. Это подтверждается данными фазового состава оксидной пленки и отложений ПК, удаленных с поверхности образцов, которые на 80‒90% являются магнетитом, остальное – гематитом. Из данных табл. 2 следует, что плотность защитной пленки на рабочих поверхностях ТОТ изменяется в довольно широких пределах и, скорее всего, зависит от конкретных теплофизических и гидродинамических параметров теплоносителя для исследованных участков ТОТ.
В табл. 3 приведен усредненный химический состав оксидной пленки с плотными отложениями ПК (в пересчете на металлы), далее ‒ химический состав, %, рыхлых отложений продуктов коррозии на рабочих поверхностях теплообменных трубок ПГ Н-272:
Fe ..........................................96.03 |
Ni ............................................0.58 |
Mn ..........................................0.76 |
Cr ............................................2.64 |
Таблица 3.
Химический состав, %, защитной оксидной пленки с плотными отложениями ПК на рабочих поверхностях теплообменных трубок парогенератора Н-272
Образец | Fe | Ni | Mn | Cr |
---|---|---|---|---|
ППТ | 97.90 | 0.19 | 0.47 | 1.44 |
ИТ | 97.90 | 0.17 | 0.48 | 1.45 |
Довольно хорошее совпадение элементных составов конструкционного материала ТОТ и слабо фиксированных отложений ПК укладывается в рамки представлений о механизме общей (равномерной) коррозии перлитных сталей с последующими гидролитическими и термохимическими процессами образования твердофазных продуктов коррозии железа с включением в их состав легирующих элементов [2].
ВЫВОДЫ
1. Независимо от типа водно-химического режима (окислительного для реакторной установки БН-800 или восстановительного для реакторной установки БН-600) на поверхности перлитной стали в процессе эксплуатации самопроизвольно формируется оксидный слой магнетита, обладающий защитными свойствами.
2. При слабощелочном окислительном водно-химическом режиме фазовый состав защитной оксидной пленки на поверхности перлитных сталей полностью определяется магнетитом, а фазовый состав плотного слоя (гематит) и рыхлых отложений продуктов коррозии (гематит + лепидокрокит) на рабочих поверхностях теплообменных трубок парогенератора Н-272 отвечает слабощелочному окислительному водно-химическому режиму III контура реакторной установки БН-800.
Список литературы
Трунов Н.Б., Логвинов С.А., Драгунов Е.Г. Гидродинамические и теплохимические процессы в парогенераторах АЭС с ВВЭР. М.: Энергоатомиздат, 2001.
Химические проблемы атомной энергетики. В 3 т. Т. 3: Химические технологии продления ресурса и повышения радиационной безопасности. Коррозионные процессы в контурах ЯЭУ / Л.Н. Москвин, А.А. Ефимов, О.Ю. Пыхтеев, Б.А. Гусев; под ред. Л.Н. Москвина. СПб.: Изд-во ВВМ, 2016.
Маргулова Т.Х., Мартынова О.И. Водные режимы тепловых и атомных электростанций. М.: Высшая школа, 1987.
Анализ фазового состава отложений продуктов коррозии на поверхности трубного пучка парогенератора ПГВ-440 методом мёссбауэровской спектроскопии / А.А. Ефимов, В.Г. Семенов, Б.А. Гусев, И.В. Мирошниченко, В.В. Панчук, В.С. Володин // Теплоэнергетика. 2009. № 2. С. 64‒65.
Методы химического и радиохимического контроля в ядерной энергетике / Л.Н. Москвин, М.Ф. Гумеров, А.А. Ефимов, В.М. Красноперов, Г.Г. Леонтьев, В.А. Мельников; под ред. Л.Н. Москвина. М.: Энергоатомиздат, 1989.
Образование гидролитических осадков в растворе нитрата Fe (III) / Г.Н. Белозерский, А.А. Ефимов, А.В. Калямин, М.Ю. Силин, С.Б. Томилов // Журн. общ. химии. 1980. № 6. С. 1209‒1213.
Расширение возможностей мессбауэровской спектроскопии в исследовании коррозии сталей на объектах атомной энергетики / А.А. Ефимов, В.Г. Семенов, Л.Н. Москвин, Б.А. Гусев // Радиохимия. 2011. Т. 53. № 1. С. 20‒25.
Дополнительные материалы отсутствуют.
Инструменты
Теплоэнергетика